Decoding PCB Assembly Cost: A Deep Dive into Per-Component Pricing
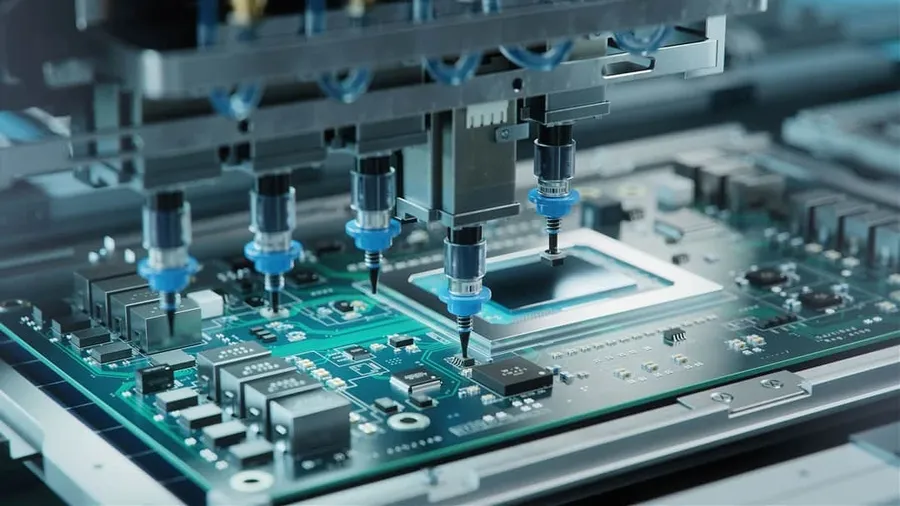
In today's electronics landscape, printed circuit boards (PCBs) are the backbone of every device, from the simplest toys to the most sophisticated medical equipment. But have you ever wondered about the costs associated with assembling these crucial components? The price of PCB assembly per component can feel like a mystery, impacting not just your budget but also the design choices you make. This article unravels the factors influencing PCB assembly costs per component, offering a detailed analysis to help you optimize your projects and gain cost-effective insights.
Understanding the Basics of PCB Assembly Cost
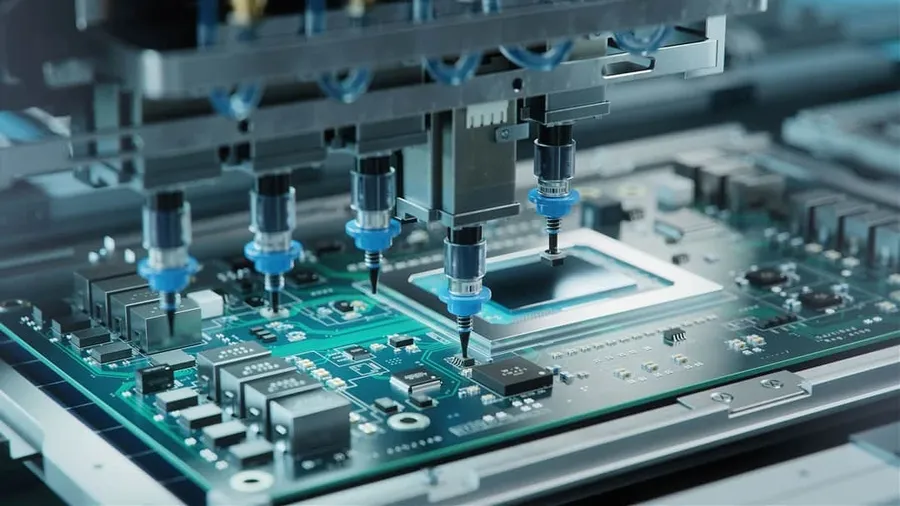
The cost of PCB assembly is not a monolithic figure; it's the result of several interconnected factors. Fundamentally, it encompasses the expenses related to materials, labor, and the depreciation of equipment involved in the manufacturing process. Understanding these underlying components is essential before analyzing per-component pricing.
- Material Costs
This includes the raw cost of the PCB substrate (e.g., FR-4), solder paste, and the components themselves. Component costs can vary widely depending on type (resistors, capacitors, ICs), their specifications, and quantity purchased. This is a significant and highly variable factor in total cost. - Labor Costs
Labor costs are determined by the time spent in various stages of assembly, including stencil preparation, component placement (manual or automated), soldering, testing, and inspection. Highly automated assembly processes are used to reduce this expense, but some manual labor is frequently required for specific components or processes. - Equipment Depreciation
The cost of purchasing and maintaining assembly equipment such as pick-and-place machines, reflow ovens, and testing equipment is factored into the overall cost. This expense, often allocated across many projects, affects the final price. Higher-end machines can lead to more accurate placement, but at a greater amortized cost. - Overhead Costs
Factory overhead, including utilities, facility maintenance, and administrative costs, also contribute to the final assembly cost. These are necessary costs of production that need to be accounted for.
How Component Type Influences Assembly Cost Per Component

The selection of component types significantly impacts PCB assembly cost per component due to variations in assembly processes and handling requirements. Surface Mount Technology (SMT) components and Through-Hole Technology (THT) components each present unique challenges that affect assembly cost. Additionally, the complexity, size, and precision of a component play a critical role in determining the overall expenses.
Component Type | Assembly Process | Cost Implications | Typical Applications |
---|---|---|---|
Surface Mount (SMT) | Automated pick-and-place, reflow soldering | Generally lower cost for high-volume production; highly dependent on component size and pin density. Finer pitch components require higher precision machines and tooling, thus increasing costs. Smaller SMT components reduce board space and have lower material costs; but increase assembly complexity. | Most electronic devices, consumer electronics |
Through-Hole (THT) | Manual or wave soldering | Higher labor costs, especially for manual placement and soldering; Fewer automation opportunities for individual component placement, Increased cost due to manual placement requirements. Larger components with larger leads require more solder, which increases the per-component cost. | Power electronics, connectors, mechanical supports |
High-Precision Components | Precise placement and soldering | Higher costs due to specialized equipment and trained personnel; Stringent quality control measures further increase costs; Specialized pick-and-place machines are required, which have higher depreciation. Highly specialized equipment increases per-component cost, especially if component counts are low. | Sensors, medical devices, high-frequency circuits |
Components with High Pin Count | Complex placement and soldering | Increased cost due to the potential for solder bridging and alignment errors; Requires skilled operators or specialized automated placement and soldering equipment. Higher pin-count leads to more rework, which increases cost; Complex solder masks, stencils, and reflow profiles are required. | Microprocessors, FPGAs, complex ICs |
The Impact of Assembly Volume on Per-Component Cost
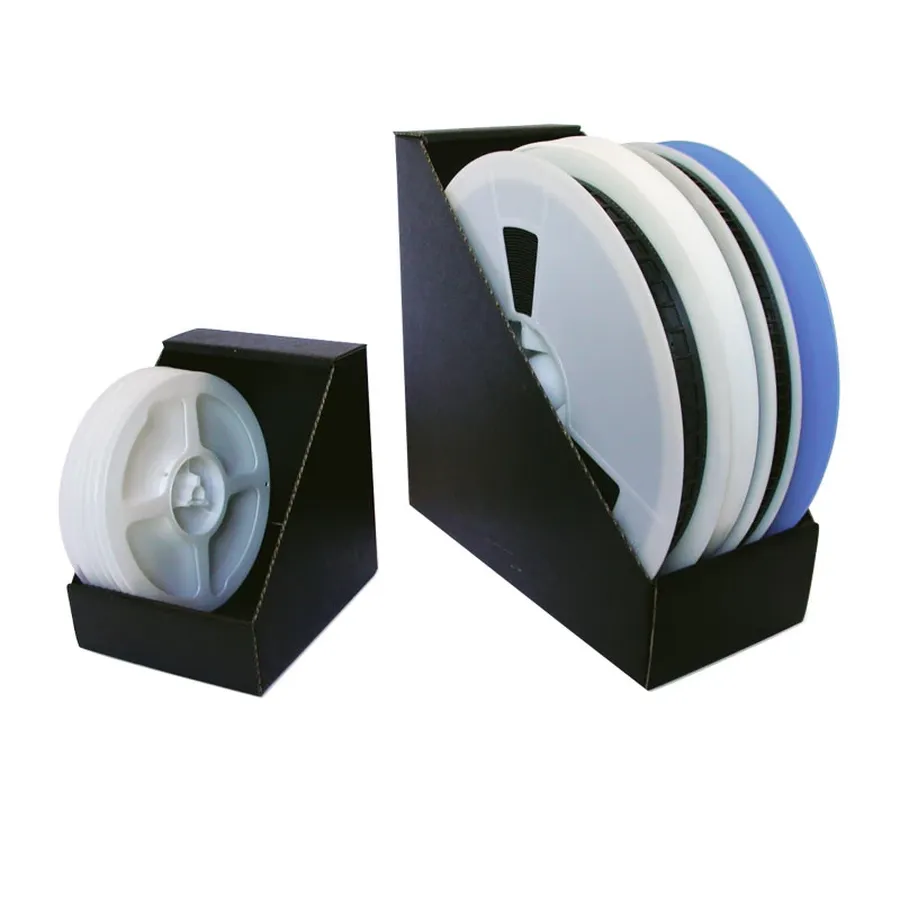
The quantity of PCBs manufactured significantly influences the assembly cost per component. Larger production volumes typically result in lower per-unit costs due to economies of scale. This is a critical consideration for any project involving PCB assembly, where understanding the impact of volume can drastically affect project budgets.
When assessing assembly costs, it's crucial to differentiate between fixed costs and variable costs. Fixed costs, such as setup fees for stencil creation and programming of pick-and-place machines, are incurred regardless of the quantity of PCBs produced. However, variable costs, such as component costs, labor, and machine runtime, are directly proportional to the production volume. As volume increases, fixed costs are spread across more units, reducing the per-unit cost. This is the fundamental concept behind volume discounts.
Production Volume | Per-Component Cost | Total Cost | Cost Distribution |
---|---|---|---|
Small (1-100) | High | Relatively High | Higher proportion of fixed costs |
Medium (100-1000) | Moderate | Moderate | More balanced fixed and variable costs |
Large (1000+) | Low | Relatively Low | Lower proportion of fixed costs |
Key Cost Factors: Board Complexity and Density
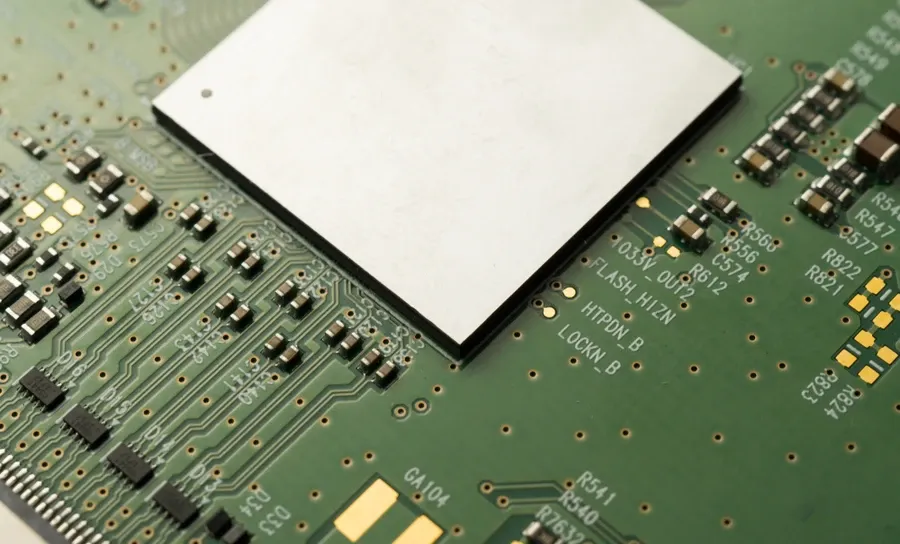
The complexity and density of a printed circuit board (PCB) significantly impact the assembly cost per component. These factors directly influence the manufacturing process, necessitating more sophisticated equipment, higher precision, and longer assembly times, thereby increasing costs.
Factor | Impact on Assembly Cost per Component | Explanation |
---|---|---|
Board Size | Positive Correlation | Larger boards generally require more materials and time for assembly, leading to increased costs. |
Number of Layers | Positive Correlation | Multi-layer boards are more complex to manufacture and assemble. Each additional layer requires precise alignment and specialized processing, driving up costs. |
Component Density | Positive Correlation | Higher component density increases assembly difficulty and risk of errors. It requires precise placement and handling, thus increasing time and cost. |
Component Package Size | Negative Correlation (for larger, standard sizes) & Positive Correlation (for smaller, complex sizes) | Larger standard packages are easier to handle and place during assembly, reducing cost. However, smaller packages (e.g., 0201, 01005) can increase cost due to increased precision and specialized equipment needs. |
Component Pitch | Positive Correlation | Finer pitch components require more accurate and precise placement, increasing complexity and assembly costs. Very small pitch components require special process controls and higher equipment capabilities. |
Specifically, complex board designs with high component densities lead to several cost escalations. For instance, densely populated boards demand finer pitch components, requiring expensive, high-precision assembly equipment such as advanced pick-and-place machines and reflow ovens with accurate temperature control. Moreover, the more complex a PCB, the greater the likelihood of assembly defects. This means more stringent testing protocols, adding further to the cost. Ultimately, manufacturers need to ensure a lower defect rate for complex boards to maintain yield, which impacts the overall per component cost.
When designing a board, it's critical to consider these trade-offs between cost and complexity. While advanced functionality may require higher component densities or multi-layer boards, understanding the cost implications can help in optimizing the design for cost efficiency. For example, choosing slightly larger component packages, where feasible, can reduce assembly costs without significantly affecting functionality. Therefore, a good balance between board complexity and cost must be carefully considered.
SMT Assembly Cost Breakdown
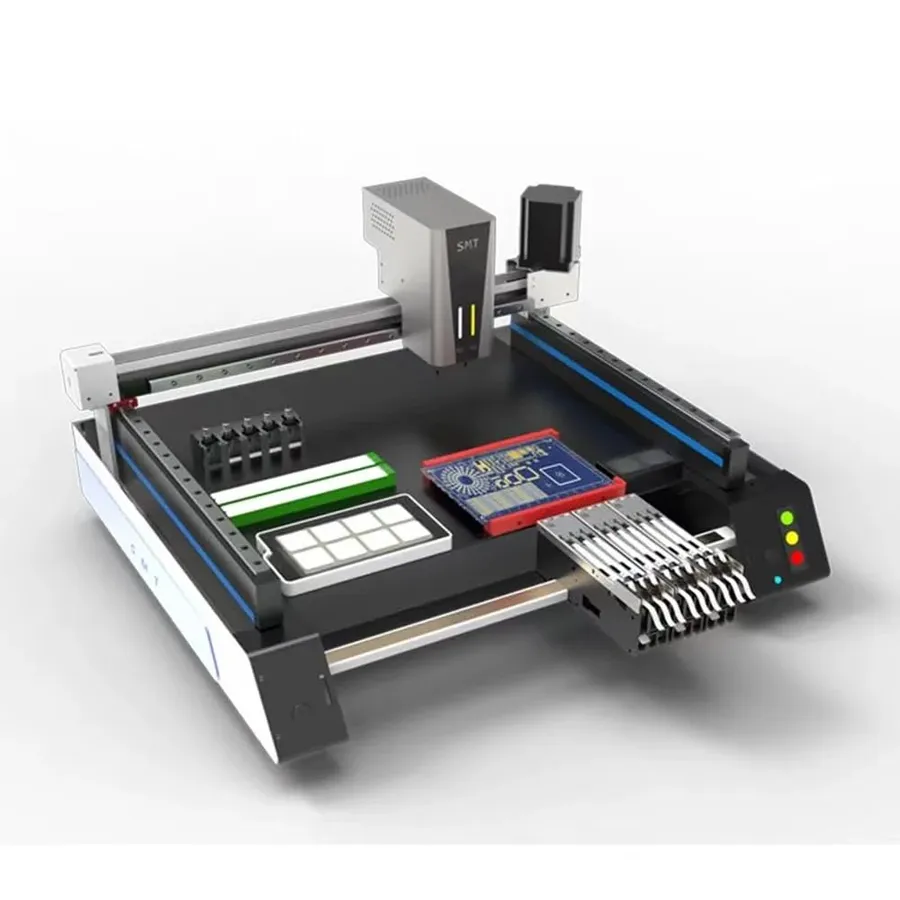
Surface Mount Technology (SMT) assembly cost is a significant factor in the overall PCB production expense. Understanding its breakdown is crucial for cost optimization. SMT assembly involves several key processes, each contributing to the final cost per component.
Process Step | Description | Cost Drivers | Optimization Strategies |
---|---|---|---|
Stencil Cost | Creation of a stencil used to apply solder paste onto the PCB. | Material, precision, size of PCB and stencil. | Optimize layout to reduce stencil size, use existing stencils if possible. |
Solder Paste Application | Precisely applying solder paste onto the PCB pads using the stencil. | Solder paste type, amount applied, equipment operation time. | Optimize paste application settings, select cost-effective solder paste. |
Component Placement | Placing components onto the solder paste-covered PCB pads using pick-and-place machines. | Machine time, component type, component density, placement precision, machine setup time. | Optimize component layout for efficient pick-and-place, use standard component packages, accurate placement data. |
Reflow Soldering | Passing the PCB through a reflow oven to melt the solder paste and permanently connect components to the PCB. | Reflow profile, energy consumption, equipment operation time. | Optimize reflow profile, monitor and control reflow process |
Inspection | Visual and automated inspection of solder joints and component placement. | Inspection method (manual/automated), inspection time | Optimize inspection process, use automated inspection equipment to reduce errors. |
Testing and Quality Assurance Costs Per Component

Testing and quality assurance are critical phases in PCB assembly, significantly impacting the final product's reliability and performance. These processes, while essential, contribute to the overall PCB assembly cost per component. These costs are not always fixed, and they vary greatly based on the complexity of the board, the required level of quality, and the testing methods employed.
Each test has its own cost drivers and the aggregate of these drive the cost per component, therefore, understanding the breakdown of these processes is key to cost optimization.
- Visual Inspection Costs
Visual inspection involves manually or automatically examining the assembled PCB for defects such as misaligned components, solder bridges, and insufficient solder joints. The cost is driven by the labor costs (manual inspection) or the cost of automated optical inspection (AOI) equipment and setup. The complexity of the board and the number of components increase inspection time and cost. - In-Circuit Testing (ICT) Costs
ICT uses specialized equipment to check the electrical connections and values of components on the board, looking for shorts, opens, and incorrect component values. The primary cost drivers here are the cost of the ICT equipment itself, the design of a custom test fixture or bed-of-nails adapter for each unique PCB design, and the labor costs associated with programming and executing the tests. The fixture cost increases with the number of test points and board size. - Functional Testing Costs
Functional testing involves running the assembled PCB through a series of tests to ensure it operates as designed and the test scenarios have the required fidelity to reflect real-world usage of the assembly. The cost of functional testing is influenced by the complexity of the testing procedure, the design and development cost of the test setup (which may require specialized hardware/software), the labor cost to perform the tests, and the time needed to conduct testing (often on a per unit basis). The more features and modes of operation the higher the associated cost.
Testing Method | Cost Drivers | Impact on Per-Component Cost |
---|---|---|
Visual Inspection | Labor costs (manual or automated), equipment cost, inspection time | Increases with board complexity and component count. |
In-Circuit Testing (ICT) | Equipment cost, test fixture design, programming cost, labor cost, number of test points | Significant for complex designs and high component count. |
Functional Testing | Test procedure complexity, test setup design, labor cost, testing time per unit, specialized hardware/software cost | Higher for complex functional testing requirements. |
Frequently Asked Questions About PCB Assembly Cost Per Component
This section addresses common inquiries regarding PCB assembly costs, providing clear, concise answers based on the preceding analysis to aid in understanding and estimation.
- How much does it generally cost to get a PCB assembled?
The cost to assemble a PCB varies greatly depending on factors like the number of components, board complexity, component types (SMT vs. through-hole), and the assembly volume. There isn't a single fixed price; instead, costs are calculated based on these variables and market conditions. For a small batch or simple board it may be a few dollars per board, but can increase to 10s or 100s for more complex boards at small quantities. Volume production drastically reduces the per unit cost. - How can I accurately estimate PCB assembly costs?
To estimate assembly costs, begin by identifying all components in your design and their type (SMT, through-hole, etc.). Then estimate the total number of components. Next, determine the board's size, complexity (number of layers), and the required production quantity. Request quotes from multiple assembly houses for this data. Using a PCB assembly cost calculator (often available online) can help generate preliminary estimates. Keep in mind that most calculators do not take into consideration the cost impact of testing or quality assurance, and should be included in the final estimation. - Why is PCB assembly perceived as being expensive?
PCB assembly involves multiple complex steps and various associated costs which drive up cost. The process requires specialized equipment for component placement, soldering, and testing. The cost of skilled labor, high precision equipment, and material handling can significantly increase prices. Additionally, small order quantities result in higher per-unit costs due to setup fees and smaller economies of scale. High precision or complex boards increase costs further. - What is a reasonable cost to expect for a PCB assembly?
There is no universal price. Low-complexity PCBs with standard components and larger production volumes can be manufactured at a lower per-unit cost. High-complexity, low-volume builds tend to be more costly due to setup costs and higher component placement times. Component cost can also play a major role. If using high end or high precision components then overall costs will be driven higher. A reasonable cost can range from a few dollars per board for simple designs at volume to hundreds or even thousands for complex or custom low volume builds. A cost breakdown and quote analysis will provide the most accurate pricing. - How does the type of components affect the assembly cost?
Surface Mount Technology (SMT) components are generally more cost-effective for automated assembly than Through-Hole components because they can be placed and soldered more efficiently. Fine-pitch components or those with a large number of pins require higher precision and special handling, which raises the per-component cost. The quantity and complexity of the components have a major impact. Simple resistor and capacitor based designs cost less than designs with many ICs and complex components. Component cost also adds directly to the assembly cost. - How does assembly volume influence the per-component cost?
Higher production volumes drastically reduce the per-component assembly cost. Setup costs, including stencil creation and machine programming, are distributed across a larger number of boards, leading to economies of scale. Volume discounts from component suppliers also reduce costs at higher volumes. Ordering larger batches will always result in a lower per unit cost. - What are the main cost drivers in PCB assembly?
The primary cost drivers in PCB assembly include material costs (the PCB itself, solder paste, and components), labor, and equipment depreciation. In addition, design and component complexity, the type of components used (SMT vs. through-hole), assembly volume, and testing requirements all play a significant role in the total cost. Optimizing for board size, layer count, and component placement can reduce costs.
Comparing PCB Assembly Pricing Models
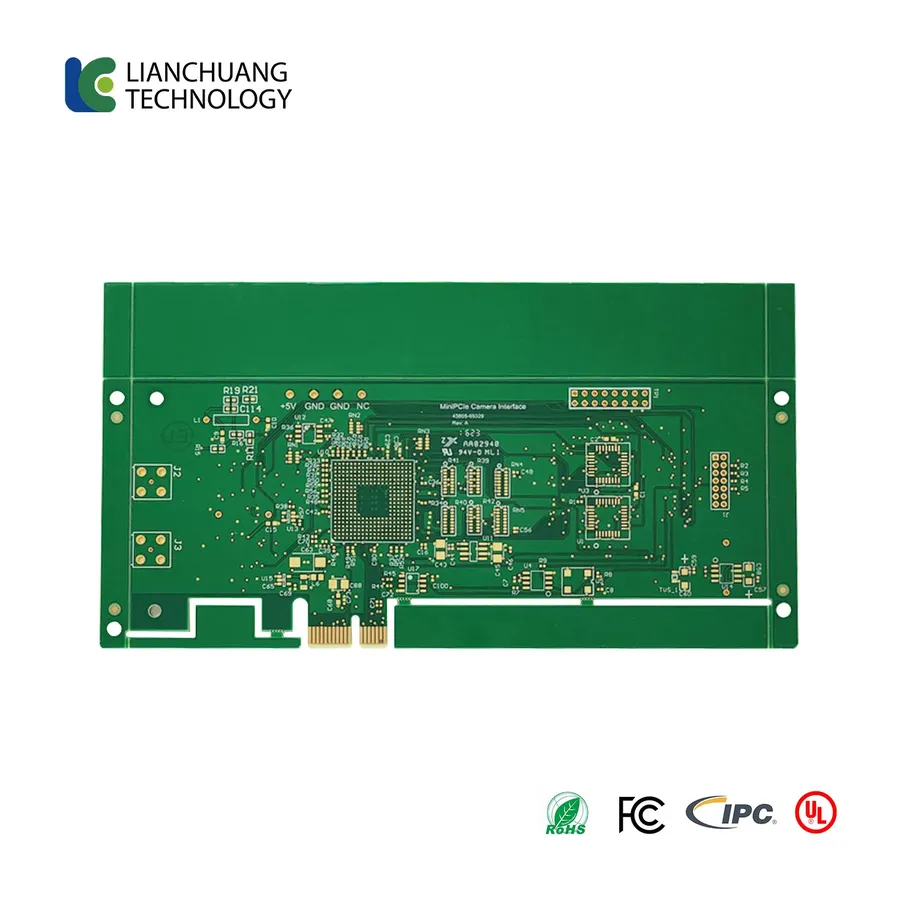
Understanding the nuances of PCB assembly pricing models is crucial for accurately estimating project costs and selecting the most suitable manufacturing partner. The cost of PCB assembly per component can vary significantly based on the pricing model used, thus affecting the overall project budget. This section provides an overview of several common pricing structures including per-pin, per-square-inch, and flat-fee models, and their implications for your project.
Pricing Model | Description | Advantages | Disadvantages | Best Use Cases |
---|---|---|---|---|
Per-Pin Pricing | Cost is determined by the number of pins on the components. | Accurate representation of component complexity, Suitable for boards with many complex ICs. | Can be more expensive for boards with many simple components, complexity in predicting total costs beforehand. | Designs with a high density of integrated circuits (ICs) and complex components. |
Per-Square-Inch Pricing | Cost is based on the total area of the PCB. | Easy to calculate, predictable, good for standard and rectangular layouts. | Less accurate for unusual board shapes, does not factor in component complexity. | Simple boards with standard layouts and relatively uniform component density. |
Flat-Fee Model | A fixed cost for a specific assembly job, irrespective of the number of components. | Cost is known up front and straightforward, good for simple and repetitive jobs. | Not cost-effective for boards with high component counts, does not account for board complexity | Very simple PCB designs or low-volume, prototyping runs, fixed and easily defined project. |
The selection of a pricing model can drastically impact the total assembly cost, hence evaluating the options against the project’s specific needs is critical. Each of the pricing models has unique strengths and weaknesses that suit different types of PCB assemblies.
Strategies for Reducing PCB Assembly Cost Per Component
Reducing PCB assembly cost per component requires a multifaceted approach, encompassing design optimization, component selection, and efficient procurement strategies. By strategically addressing these areas, significant cost savings can be realized without compromising the quality or functionality of the final product.
- Optimize Board Design
Simplifying the board layout can directly reduce assembly time and cost. Techniques such as minimizing the number of layers, using standard component footprints, and reducing the overall board area contribute significantly to cost savings. Efficient routing and avoiding complex geometries that require high precision placement will lead to lower assembly costs. - Choose Cost-Effective Components
Selecting components with similar performance specifications but lower cost can greatly influence the overall price. Evaluating alternate component packages that have better cost efficiency, especially for high-volume manufacturing, is a useful method. Consider using passives in larger footprints as these tend to be cheaper to assemble than very small passives (e.g. 0201, 01005). - Component Standardization
Reducing the number of unique part types on a board can streamline the pick-and-place process and decrease assembly errors. This reduces set-up costs and simplifies component management. Using parts that are common, readily available in stock, and from multiple vendors will also reduce cost. - Consolidate Orders
Ordering PCBs and components in larger batches leverages volume discounts from both suppliers and assembly houses. Planning production runs to minimize order frequency can reduce per-unit cost and may make sense even if you must hold a buffer of inventory. - Panelization Strategy
Panelizing the PCB designs, i.e., combining multiple boards onto a single larger panel, is a very effective method of reducing manufacturing and assembly costs as it reduces the per-board cost. This will generally reduce the amount of raw material, handling and set up time required. - Consider Alternate Component Packages
In addition to reducing the number of different types of parts on your bill of materials, also evaluate alternative package styles that provide similar functionality. Some component package styles may cost more to place and solder. For example, very fine-pitch BGA parts typically cost much more to assemble than a similar part in a QFP package. - Optimize Solder Paste and Stencil
Ensure that the stencil design optimizes solder paste application for reduced waste and improved reliability. Reducing stencil thickness and considering step stencils (for different pad sizes) can also reduce costs.
Understanding the nuances of PCB assembly costs per component is crucial for effective project management and budgeting in electronics manufacturing. Factors ranging from component complexity and assembly volume to testing processes and quality checks all impact the final price. By implementing strategies to optimize design choices and streamline assembly processes, it's possible to achieve significant cost reductions and improve the overall efficiency of production, keeping per-component costs under control while maintaining high-quality manufacturing standards. As technology advances, keep abreast of new innovations to further enhance cost-effectiveness and improve assembly processes to remain competitive in the market.
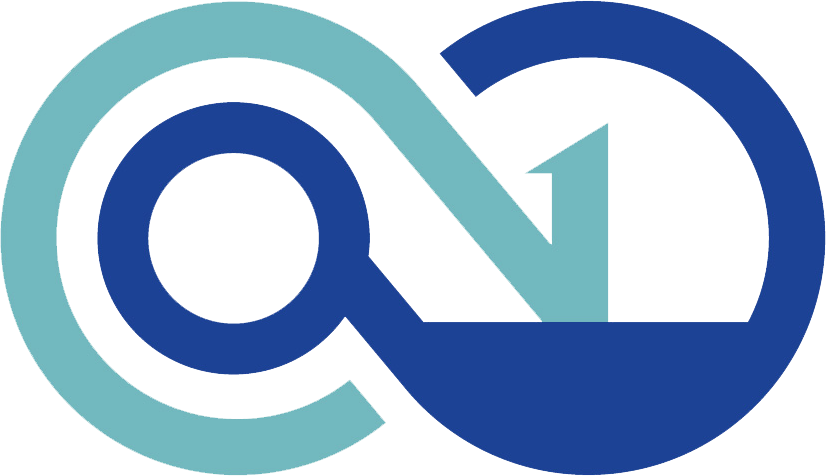