Decoding PCB Circuit Price: A Comprehensive Guide
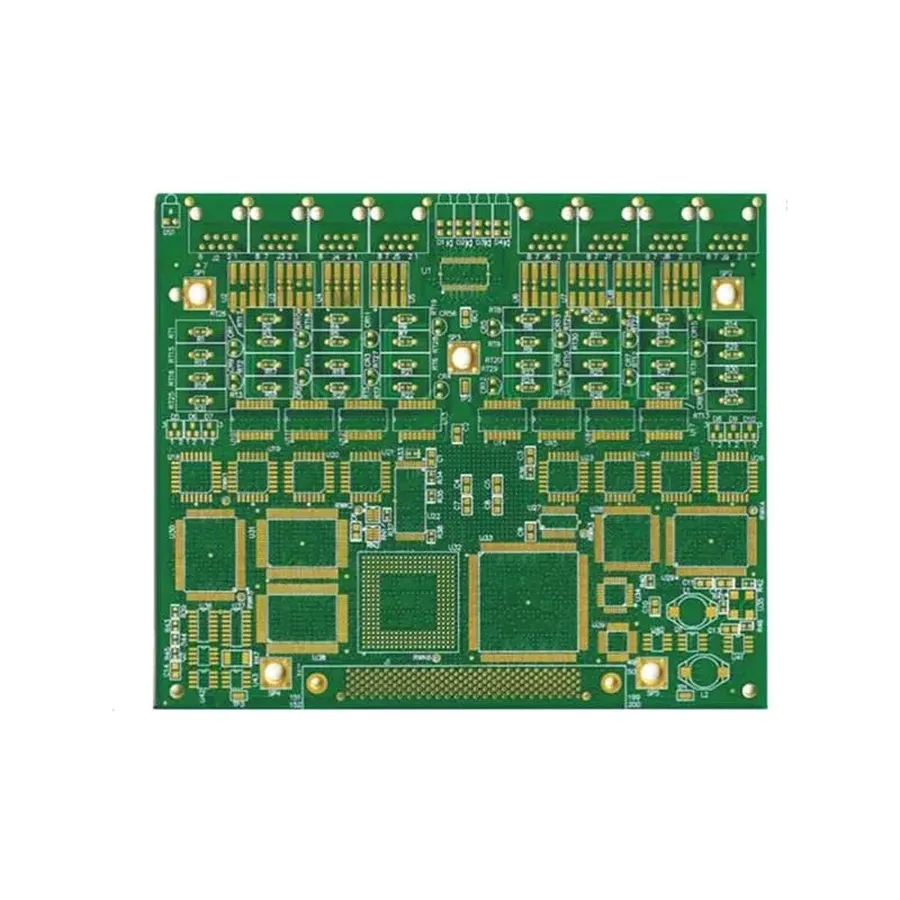
From powering our smartphones to controlling complex industrial machinery, printed circuit boards (PCBs) are the unsung heroes of modern electronics. But how is the price of these critical components determined? This article dives deep into the world of PCB circuit price, exploring the myriad factors that affect costs, guiding you to understand where your money goes when ordering PCBs, and how to get the best value.
Key Factors Influencing PCB Circuit Price
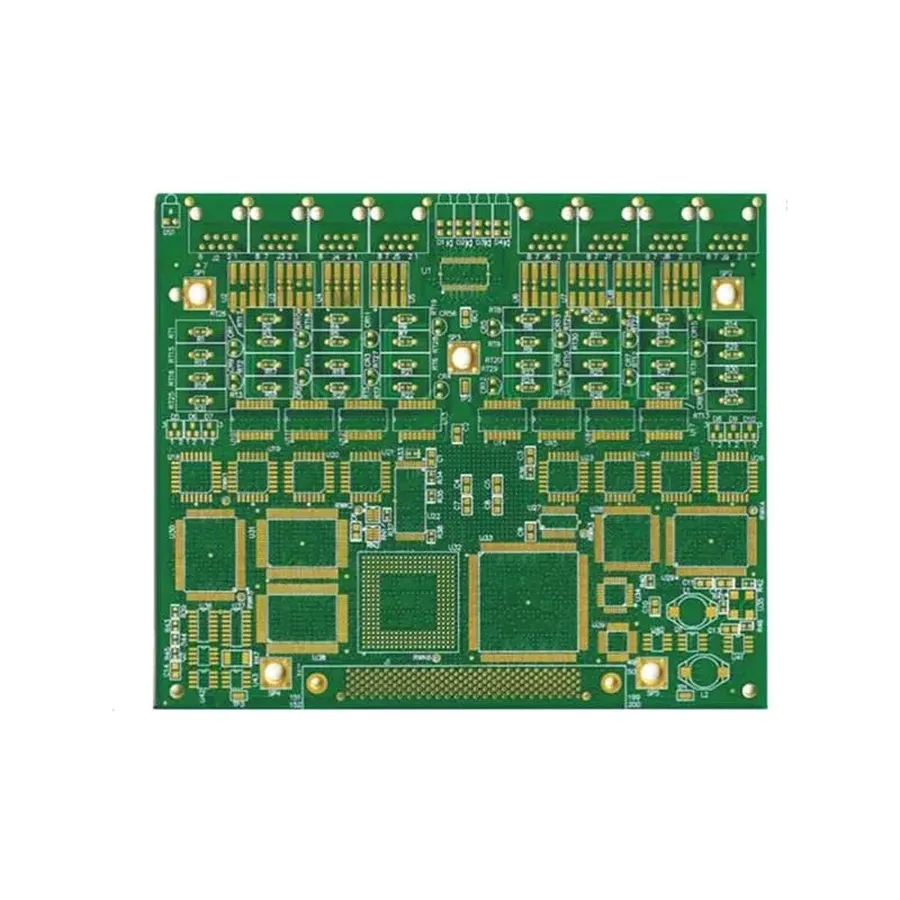
The final cost of a Printed Circuit Board (PCB) is not a fixed value, but rather a complex interplay of several factors. These factors, ranging from the fundamental materials used to the board's complexity and order volume, collectively determine the price. Understanding these core elements is essential for accurate budgeting and strategic cost management in electronic product development.
- Material Types
The base material, such as FR-4, aluminum, or flexible substrates, directly impacts the cost. Different materials have varying performance characteristics and price points. - Board Size
The dimensions of the PCB directly affect the amount of material used and the manufacturing effort required. Larger boards generally cost more than smaller ones. - Layer Count
The number of conductive layers in the PCB significantly influences its complexity and cost. Single-layer boards are the least expensive, while multi-layer boards are more complex and therefore pricier. - Surface Finish
The type of surface finish applied to the PCB, such as HASL, ENIG, or OSP, affects both the board's functionality and its price. - Order Quantity
The number of PCBs ordered significantly impacts the cost per unit. Larger orders typically benefit from economies of scale, resulting in lower per-unit prices. - Manufacturing Complexity
Factors such as the complexity of the design, the size of vias and traces, and special routing requirements affect the price of manufacturing - Assembly and Testing
The process of assembling components on the PCB and conducting quality testing add to the overall cost of the final product.
Material Selection and its Impact on PCB Price
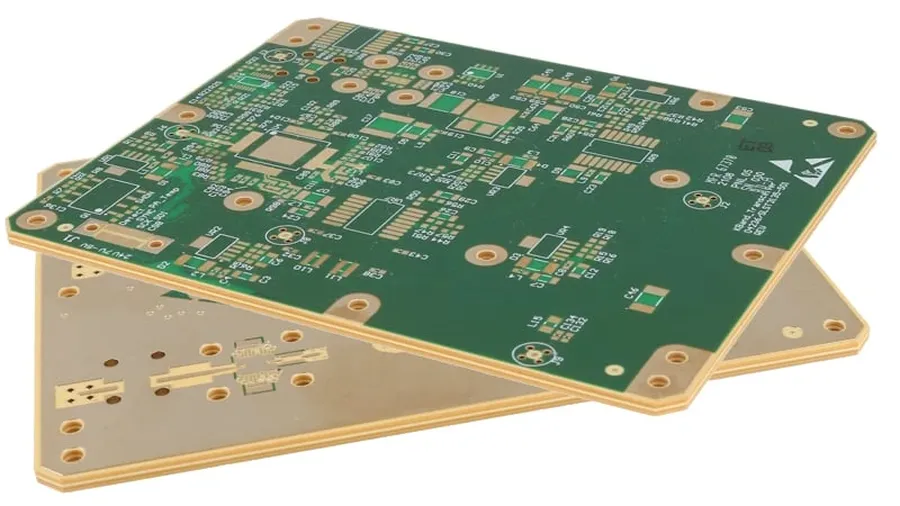
The choice of materials in PCB manufacturing is a critical determinant of the final cost, performance, and application suitability of the circuit board. Different materials offer varying electrical, mechanical, and thermal properties, which directly influence their price points and usability in specific applications. Selecting the right material involves carefully considering these attributes against the project’s needs and budget.
Material | Description | Typical Applications | Cost (Relative) | Key Properties | Advantages | Disadvantages |
---|---|---|---|---|---|---|
FR-4 | Fiberglass-reinforced epoxy laminate; most common PCB material. | General-purpose electronics, consumer products. | Low to Medium | Good electrical insulation, moderate mechanical strength, temperature resistance. | Widely available, cost-effective, easy to fabricate. | Limited thermal performance, not suitable for high-frequency applications. |
Aluminum | Aluminum substrate for metal-core PCBs (MCPCBs). | LED lighting, power electronics, high-power applications. | Medium to High | Excellent thermal conductivity, good mechanical strength. | Superior heat dissipation, durable. | More expensive than FR-4, more complex fabrication. |
Flexible Substrates (e.g., Polyimide) | Flexible polymer substrates. | Wearable electronics, flexible displays, automotive applications. | High | High flexibility, good thermal and chemical resistance. | Excellent for complex shapes and dynamic bending applications, lightweight. | More expensive, may have more manufacturing challenges. |
Rogers Materials | High-performance laminates for high-frequency and RF applications. | RF circuits, high-speed digital designs, aerospace. | Very High | Excellent electrical properties, low signal loss, precise impedance control. | Superior electrical performance at high frequencies. | Expensive, requires specialized fabrication. |
CEM-1/CEM-3 | Composite material; paper substrate with fiberglass and epoxy resin. | Single-sided or simple double-sided boards in cost-sensitive applications. | Low | Acceptable mechanical and electrical properties, low cost. | Inexpensive, easy to process, good for non-critical applications. | Limited electrical performance, less robust than FR-4. |
Layer Count and its Effect on PCB Circuit Price
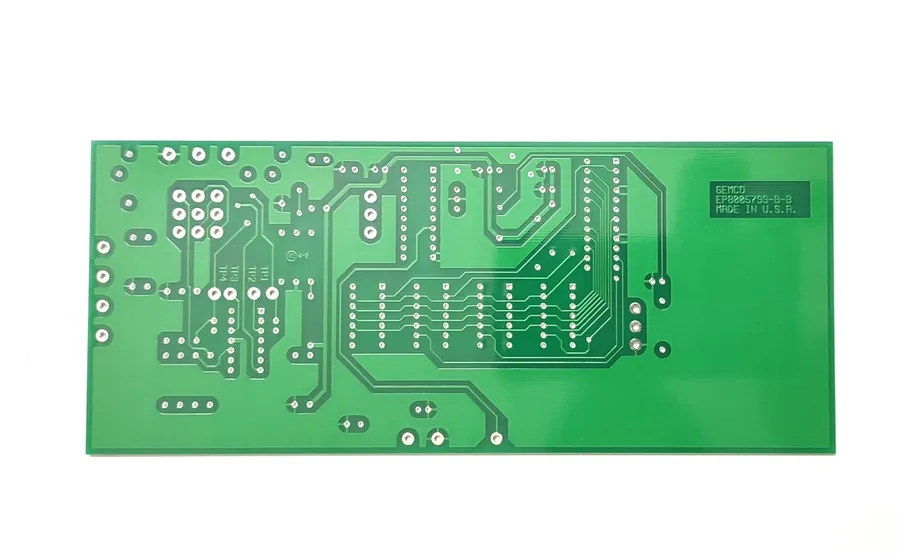
The number of layers in a Printed Circuit Board (PCB) is a primary cost driver, directly impacting both the complexity of the manufacturing process and the subsequent price. Layer count dictates the number of conductive copper layers separated by insulating dielectric material within the PCB. Increasing layer count elevates the fabrication cost due to the additional processing steps and material requirements, including lamination and drilling.
Layer Type | Complexity | Cost | Typical Applications |
---|---|---|---|
Single-Layer | Simplest design, all components on one side. | Lowest cost. | Basic electronic circuits, simple sensors, LED lighting. |
Double-Layer | Components can be placed on both sides, more routing flexibility. | Moderate cost. | Widely used in various consumer electronics, power supplies, simple controllers. |
Multi-Layer (4-8 Layers) | Complex interconnections and routing with multiple signal and power planes. | Higher cost. | More complex electronics, computer motherboards, network devices. |
Multi-Layer (8+ Layers) | Highly complex designs, high-density interconnects, advanced features. | Highest cost. | High-speed computing, advanced networking hardware, high-performance computing. |
Each increase in the number of layers necessitates more precise registration processes to ensure all layers are accurately aligned. This complexity is reflected in the final cost. Additionally, multi-layer PCBs often require vias (small plated through-holes) to establish electrical connections between the layers which adds further to the manufacturing expense.
Board Size and Its Impact on PCB Cost
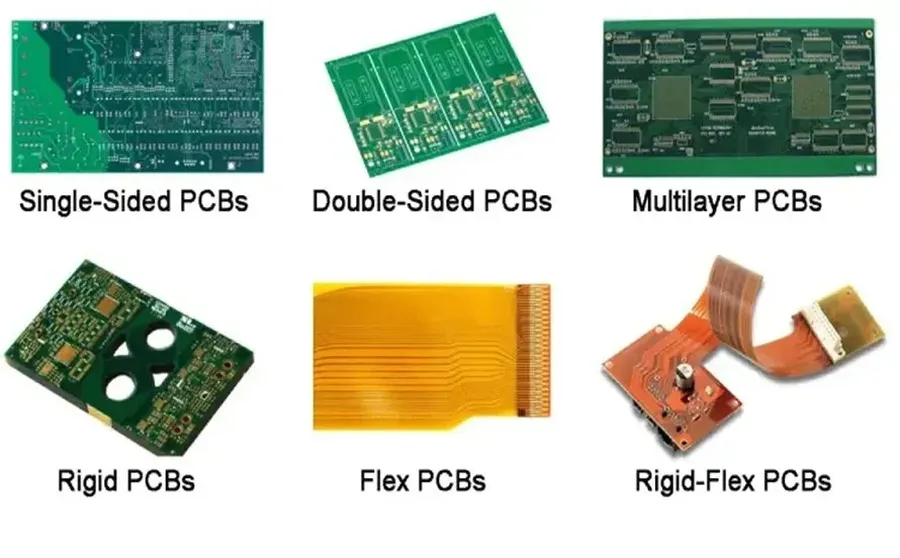
The physical dimensions of a Printed Circuit Board (PCB) significantly influence its manufacturing cost, with larger boards generally commanding higher prices due to increased material consumption and processing time. This relationship is not always linear, as other factors interact with board size to determine final cost.
Pricing models often incorporate a 'per square inch' calculation, particularly for standard rectangular boards. However, this metric can be a starting point rather than a precise determinant of final cost as it doesn't account for complexity or other manufacturing constraints.
Board Size Category | Typical Area (square inches) | Impact on Cost |
---|---|---|
Small | < 10 | Lower material cost, potentially higher per-unit costs for small quantities. |
Medium | 10-50 | Moderate material cost, with economies of scale becoming more apparent. |
Large | > 50 | Higher material cost, increased handling and processing complexity may impact final price. |
It's crucial to remember that the 'per square inch' price can fluctuate depending on the factors such as board layer count and materials as well as quantity of the order.
Quantity and its Effect on PCB Pricing
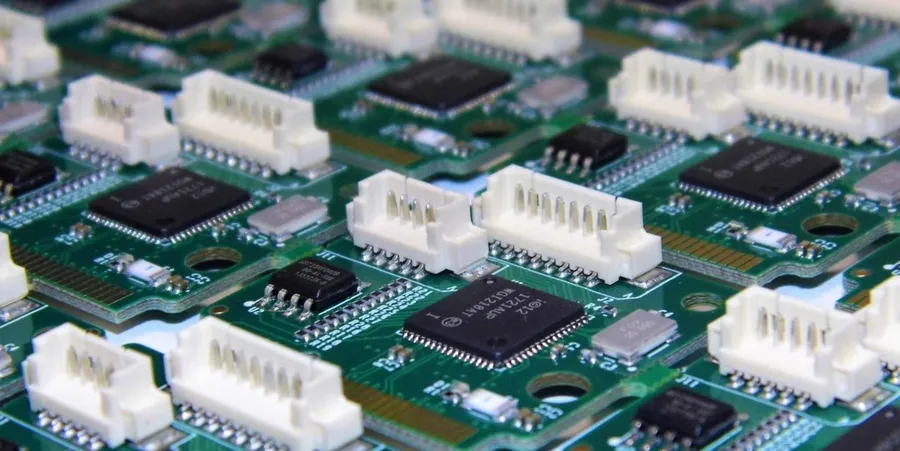
The quantity of PCBs ordered has a significant impact on the per-unit cost. This is due to economies of scale in manufacturing. Generally, as the order volume increases, the price per PCB decreases substantially.
This relationship stems from the fixed costs associated with PCB production, which include tooling, setup, and initial processing. These costs are distributed across all units in the production run. When more units are produced, the impact of these initial fixed costs is diluted, resulting in lower per-unit expenses.
Order Quantity | Unit Price (Example) | Price Notes |
---|---|---|
1-10 (Prototypes) | $50 - $150 | High per unit cost due to setup and tooling, suitable for design verification |
10-100 (Small Batch) | $15 - $50 | Moderate per unit cost. Useful for pilot production runs or specialized projects |
100-1000 (Medium Volume) | $5 - $15 | Significant reduction in unit cost. A good compromise for mass production |
1000+ (High Volume) | $1 - $5 | Lowest per unit cost. Ideal for very high-volume consumer and industrial products |
It's crucial to consider this pricing dynamic when planning your PCB order. Prototypes, which involve very small production runs, often come with a higher per-unit price. Conversely, high-volume orders unlock significant cost savings, making larger runs advantageous for mass production or projects with long lifespans.
Surface Finish Options and Their Associated Costs
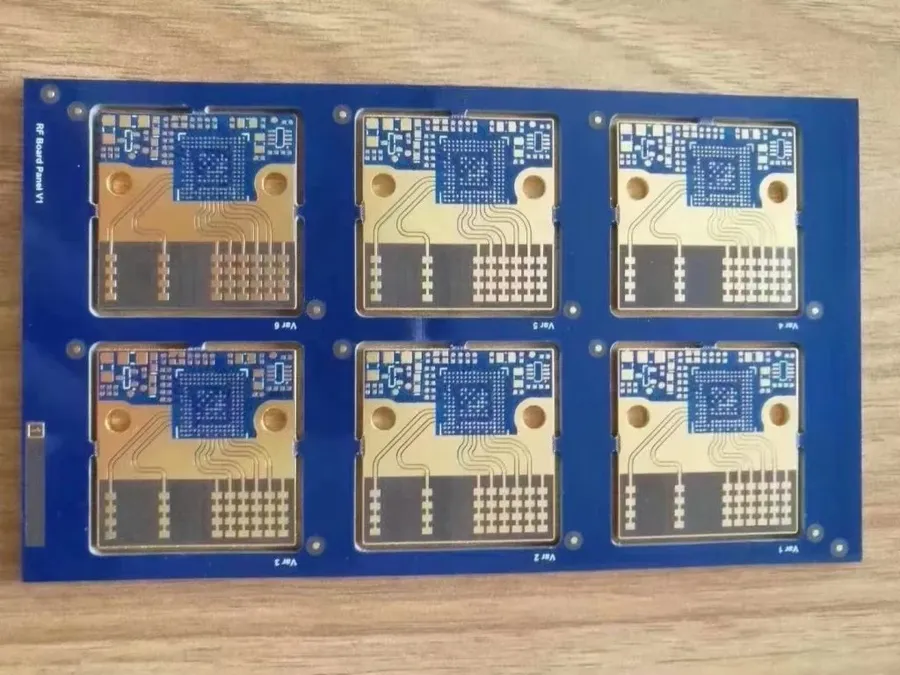
The surface finish of a Printed Circuit Board (PCB) is a critical aspect of its manufacturability, solderability, and long-term reliability, significantly impacting the final cost. Different finishes offer varying levels of performance, durability, and cost, making selection a crucial step in PCB design and manufacturing.
Surface Finish | Description | Cost | Advantages | Disadvantages |
---|---|---|---|---|
HASL (Hot Air Solder Leveling) | A process where molten solder is applied to exposed copper pads and then leveled using hot air. | Low | Cost-effective, good solderability, widely available. | Not suitable for fine pitch components, uneven surface, contains lead (lead-free options are available but more expensive). |
ENIG (Electroless Nickel Immersion Gold) | A two-layer metallic finish with a thin layer of gold over a layer of nickel. | High | Excellent solderability, good corrosion resistance, suitable for fine pitch components. | More expensive than HASL, can suffer from 'black pad' issues if not applied correctly. |
OSP (Organic Solderability Preservative) | A thin, water-based organic coating that protects the copper pads from oxidation. | Low-Medium | Flat surface, good solderability, lead-free. | Short shelf life, susceptible to damage during handling, not suitable for multiple reflow cycles. |
Immersion Tin | A thin layer of tin applied to the copper pads. | Medium | Good solderability, flat surface, lead-free. | Susceptible to whisker growth, can tarnish over time, not as robust as ENIG. |
Immersion Silver | A thin layer of silver applied to the copper pads. | Medium-High | Good solderability, flat surface, lead-free. | Susceptible to tarnishing, can migrate under certain conditions, more expensive than OSP. |
PCB Assembly and Testing Costs
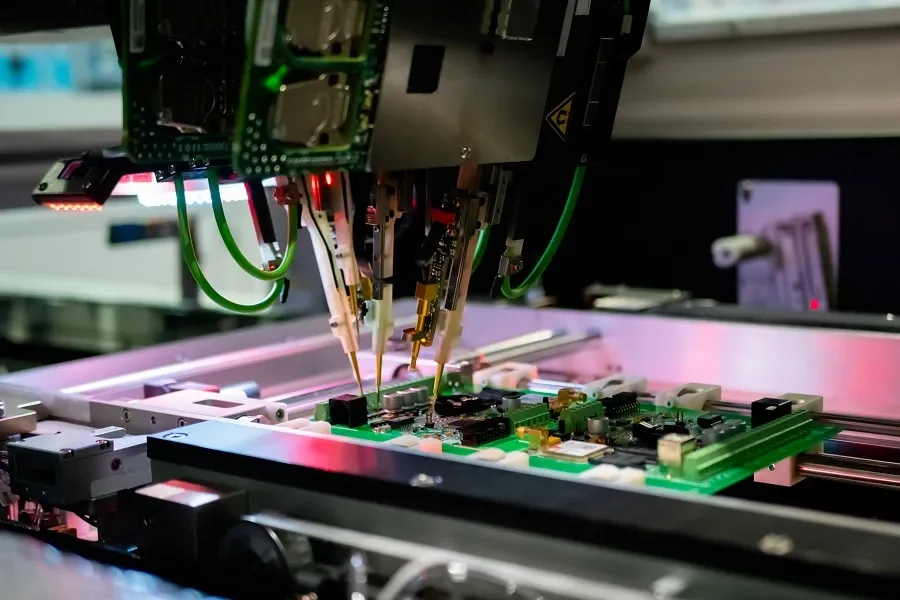
The final price of a printed circuit board (PCB) extends beyond the bare board fabrication to encompass assembly, component sourcing, and testing. These downstream processes are integral to delivering a functional PCB and can significantly impact the overall cost. Understanding these aspects is crucial for accurate budgeting and cost control, especially for turnkey solutions.
PCB assembly costs are influenced by several factors, including component count, the complexity of assembly (surface mount vs. through-hole), and the use of automated or manual processes. Component sourcing adds another layer, as prices can fluctuate depending on market conditions, supplier, and volume. Finally, testing, while essential to ensuring functionality, incurs costs based on the type and number of tests performed.
Cost Factor | Description | Impact on Overall Cost |
---|---|---|
Assembly Method | Surface Mount (SMT), Through-hole (THT), Mixed | SMT is generally more cost-effective for high-volume production; THT can be more expensive due to manual labor. |
Component Sourcing | Procurement of components (resistors, capacitors, ICs) | Component prices vary with market demand, lead times, and manufacturer. |
Assembly Volume | Number of boards being assembled | Higher volumes typically result in lower per-unit assembly costs due to economies of scale. |
Testing | Functional testing, In-Circuit Testing (ICT), Automated Optical Inspection (AOI) | Testing costs increase with the complexity of tests required. |
Turnkey Services | Full-service assembly, sourcing, and testing by one vendor | Turnkey solutions can be more expensive but save time and resources by streamlining the process. |
For turnkey solutions, expect a premium for the convenience of having all stages managed by a single provider, with assembly, component procurement, and testing being included. This often means higher costs compared to managing each step individually, but also minimizes the time and logistical burden. The cost advantage of such solutions depends largely on your internal capabilities, resources, and volume of production. Understanding the costs associated with each phase can help in making informed decisions that align with both budget constraints and technical requirements.
Frequently Asked Questions About PCB Circuit Price
Understanding the cost drivers for Printed Circuit Boards (PCBs) is crucial for effective project budgeting. This section addresses common queries regarding PCB pricing, offering clear answers based on established principles of manufacturing and supply chain economics.
- What is the average cost of a circuit board?
The average cost of a circuit board varies significantly depending on complexity, materials, and order volume. Simple single-layer boards may cost a few dollars, while complex multi-layer boards with specialized materials and finishes can cost significantly more. It's best to get quotes based on your specific requirements. - How much does a basic PCB cost?
A basic PCB, typically a single or double-layer FR-4 board, can range from a few dollars for small prototypes to less than a dollar per board for high-volume orders. The exact price depends heavily on dimensions, complexity, and production quantities. - What factors most significantly impact PCB price?
Key factors influencing PCB price include: material type (e.g., FR-4, aluminum, flexible substrates), board dimensions, the number of layers, surface finish (e.g., HASL, ENIG, OSP), quantity, and the level of testing required. More complex designs and higher standards will always incur higher costs. - What are the typical price ranges for PCB prototypes?
PCB prototype costs are typically higher per unit due to the setup costs for small production runs. Expect to pay a premium per board when ordering small quantities compared to larger mass production runs. Prices can range from tens to hundreds of dollars for a small batch, depending on the complexity. - How can I reduce my PCB cost?
To reduce costs, consider using standard materials (like FR-4), simplifying your board design, optimizing the board size, panelizing multiple designs, ordering larger quantities, using a standard surface finish, and selecting suppliers with competitive pricing. Avoid unnecessary complexity or tight specifications where possible. - Is it cheaper to order PCBs in bulk?
Yes, ordering PCBs in larger quantities significantly reduces the per-unit cost due to economies of scale. Manufacturers spread their setup and tooling costs across a larger number of boards, resulting in lower individual board prices. Therefore, consider carefully the total number of boards you will need during the product life cycle. - How does surface finish affect PCB cost?
The surface finish directly impacts the final cost of the PCB. Basic finishes like HASL (Hot Air Solder Leveling) are more cost-effective, while more advanced finishes like ENIG (Electroless Nickel Immersion Gold) offer better performance and longer shelf life but come at a premium.
Practical Tips for Cost Optimization When Ordering PCBs
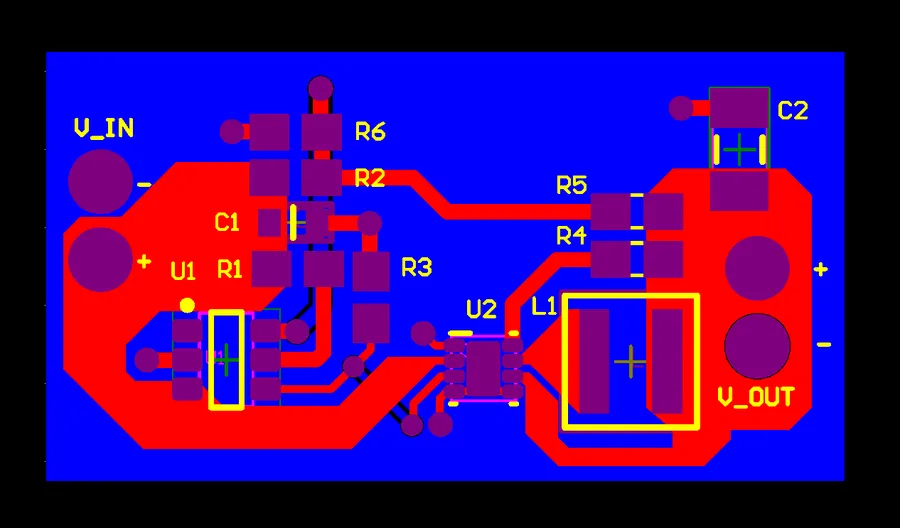
Optimizing PCB costs requires a multi-faceted approach, encompassing design choices, efficient panelization, and strategic supplier selection. By carefully considering these factors, significant cost reductions can be achieved without compromising quality or functionality.
- Design for Manufacturability (DFM)
Prioritize design choices that simplify the manufacturing process. This includes using standard component footprints, minimizing vias, and adhering to manufacturer's recommended clearances and trace widths. Avoiding overly complex designs reduces fabrication costs and improves yields. - Efficient Panelization
Panelization involves arranging multiple PCB designs onto a single panel for fabrication. Optimized panel layouts maximize board utilization, reducing material waste and overall production costs. Collaborate with your manufacturer to ensure your panelization strategy is cost-effective. - Standard Materials and Finishes
Opting for commonly available materials, such as FR-4, and standard surface finishes like HASL can significantly reduce costs compared to specialized materials and finishes. Consider the specific application requirements and choose materials and finishes that balance performance and cost. - Component Selection and Procurement
Carefully select components that are readily available and competitively priced. Avoid rare or specialized parts that can drive up costs and lead times. Consider purchasing components in bulk and negotiate pricing with suppliers. - Strategic Supplier Selection
Research and compare quotes from multiple PCB manufacturers and assemblers. Consider factors beyond just the initial quote, such as quality, lead time, and customer service. Building a long-term relationship with a reliable supplier can lead to preferential pricing and better communication. - Minimize Layer Count
Evaluate the necessity of multiple layers. While multi-layer PCBs offer greater design flexibility, they also increase production costs. If your application allows, design a simpler single or double-layer board to reduce manufacturing complexity and expense. - Avoid Unnecessary Specifications
Specify only the necessary tolerances and requirements for your PCB. Overly stringent specifications can increase costs without providing any meaningful benefit. Focus on the essential parameters and relax the less critical requirements.
Understanding the intricacies of PCB circuit price is crucial for effective project budgeting and design choices. By considering materials, layer counts, quantity and assembly costs, engineers and makers can effectively manage costs and optimize the value of PCBs in their projects. Keeping track of market trends and comparing multiple suppliers will ensure you get the best price for your PCB circuit needs.
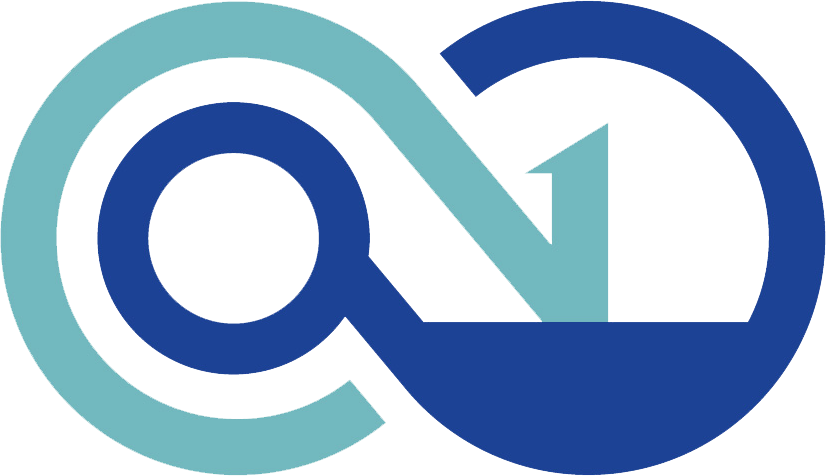