Finding Cheap Flex PCB Solutions: A Comprehensive Guide
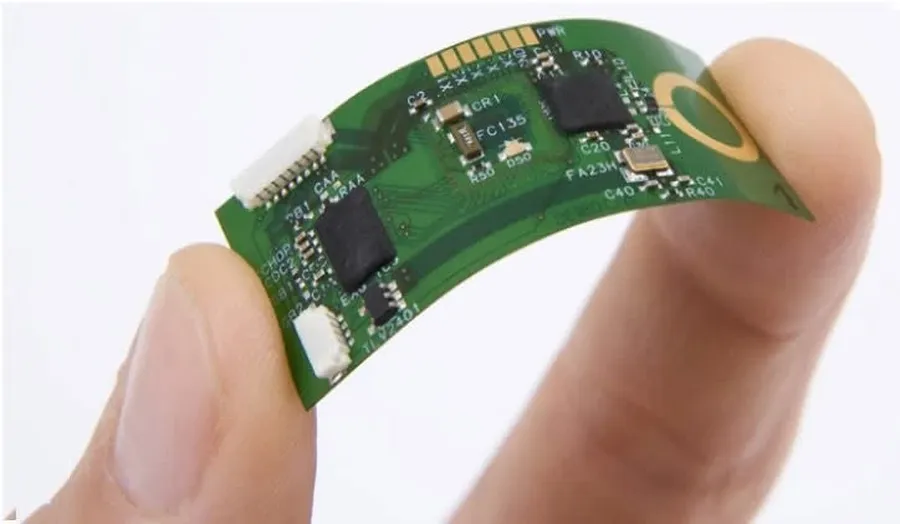
In today's world of ever-evolving electronics, flexible PCBs are becoming increasingly vital. These bendable circuit boards are the backbone of many modern devices. However, finding a balance between functionality and cost can be challenging. This article delves into how you can secure cheap flex PCB solutions without compromising quality, offering practical tips and insights to guide you through the process.
Understanding Flex PCB Basics and Cost Drivers
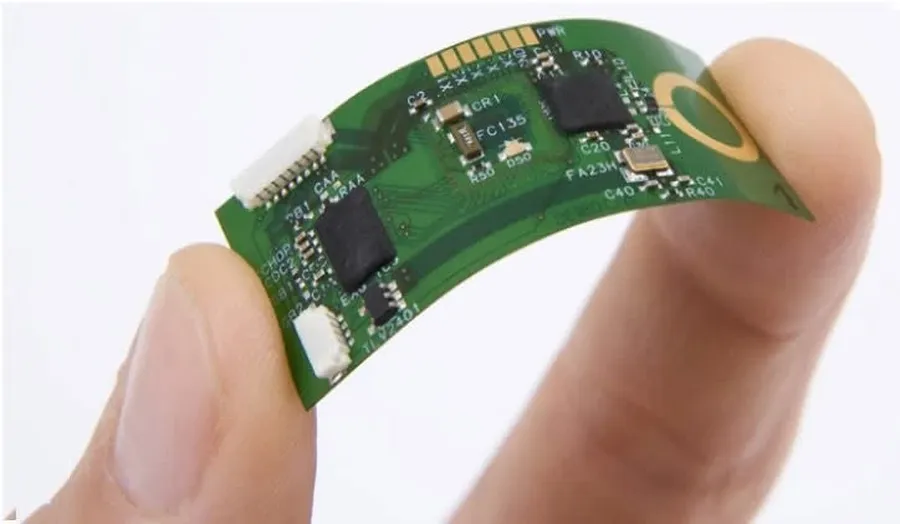
Flexible printed circuit boards (PCBs), or flex PCBs, are a specialized type of circuit board constructed from a flexible substrate, allowing them to bend and conform to various shapes and spaces. This adaptability distinguishes them from traditional rigid PCBs, but also introduces unique cost factors. Understanding the fundamental components and key cost drivers is crucial for anyone seeking cost-effective flex PCB solutions.
The primary cost drivers for flex PCBs can be categorized into several key areas:
- Material Costs
The type of flexible substrate used (e.g., polyimide, polyester), the copper thickness, and the adhesive all contribute significantly to the overall cost. Polyimide is the most common substrate and offers excellent thermal and electrical properties but tends to be more expensive than polyester. - Layer Count
Multilayer flex PCBs are considerably more expensive than single or double-layer designs due to increased complexity in manufacturing and higher material usage. Each additional layer requires more material, processing steps, and higher precision in alignment. - Complexity of Design
Intricate designs with fine lines, small vias, and complex geometries require tighter manufacturing tolerances, which increase both the fabrication time and the risk of defects. This leads to higher production costs. - Panel Size and Layout
The number of PCBs that can be efficiently placed on a manufacturing panel impacts material utilization. Optimizing the layout to minimize waste can reduce the cost per board. - Finishes and Special Requirements
Specific surface finishes (e.g., gold plating), impedance control, or specialized requirements can significantly increase the manufacturing cost of flex PCBs. These are often added due to performance or environmental concerns but come at a price premium. - Production Volume
The quantity of boards produced has a significant impact on price. Higher volumes allow manufacturers to amortize setup costs, resulting in lower per-unit prices. Prototype runs and smaller volumes will always be more expensive per board.
Design Strategies for Affordable Flex PCBs
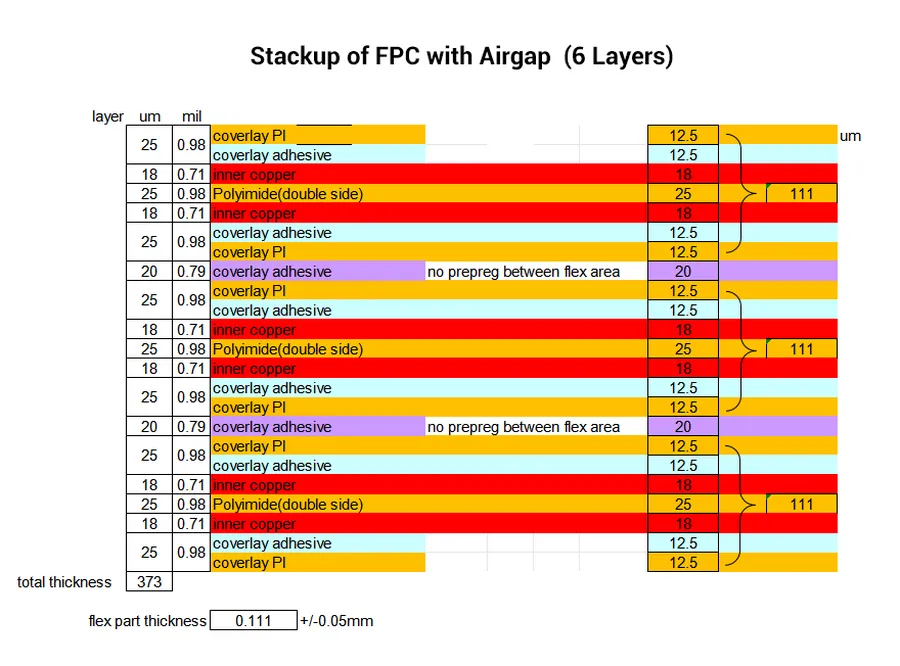
Optimizing the design of flexible PCBs is crucial for reducing fabrication costs without compromising functionality. By making smart choices during the design phase, significant savings can be realized. This section explores key design strategies that directly impact the affordability of flex PCBs.
- Minimize Layer Count
Reducing the number of layers in a flex PCB is one of the most effective methods for cost reduction. Each additional layer increases material usage and processing complexity. Single or double-layer designs are inherently more affordable than multi-layer designs. Analyze the circuit requirements carefully; often, design efficiency can be achieved with fewer layers. - Avoid Complex Geometries
Complex shapes, intricate bends, and excessively small features on a flex PCB design increase fabrication costs. These designs require precision manufacturing, which is often more expensive. Streamline the shapes, use simpler bend radii, and use standard component sizes wherever possible. This simplification reduces manufacturing time and error rates, translating to lower prices. - Standardize Sizes and Shapes
Standardizing the sizes and shapes of your flex PCBs can enable manufacturers to optimize their processes, leading to lower unit costs. Using standard panel sizes can also result in better material utilization and reduced waste. When possible, design to fit within readily available material dimensions. - Optimize Via Placement and Size
The number, type, and size of vias directly impact the cost of manufacturing. Minimize the number of vias used in the design, as each via requires drilling and plating, which is a time and resource-intensive step. Use the largest allowable via size consistent with trace routing requirements to lower costs. - Efficient Panelization
Efficient panelization design is critical to reduce material waste. Strategically arrange multiple PCB designs within a single manufacturing panel, leaving enough space for routing and separation without wasting board material. This significantly reduces the cost per PCB. - Use Common Component Packages
Designing your flexible PCB to accommodate commonly used component packages can reduce assembly costs and lead times. Unique packages might require more specialized processes and thus add to the total cost of the project. Choose standard surface mount (SMD) packages whenever possible to take advantage of automated assembly processes.
Material Choices Impacting the Cost of Flexible Circuit Boards
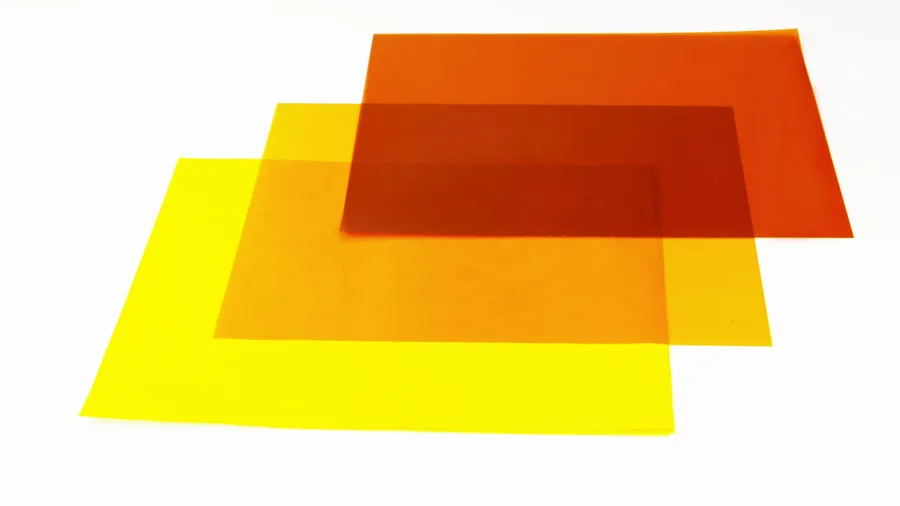
The selection of materials for flexible PCBs significantly influences both performance and cost. This section details the common materials used and how their properties and price points can impact the overall budget of your project. Moving beyond the commonly used polyimide to other substrates such as polyester can offer cost-saving opportunities.
Material | Cost | Temperature Resistance | Flexibility | Typical Applications |
---|---|---|---|---|
Polyimide (PI) | High | High (up to 400°C) | Excellent | High-reliability applications, aerospace, medical |
Polyester (PET) | Low | Moderate (up to 150°C) | Good | Consumer electronics, low-cost applications |
Liquid Crystal Polymer (LCP) | Moderate to High | High (up to 300°C) | Excellent | High-frequency applications, advanced electronics |
Polyethylene Naphthalate (PEN) | Moderate | Moderate (up to 180°C) | Good | Flexible displays, some electronics applications |
Other Modified Polymers | Variable | Variable | Variable | Specific applications based on modification |
Polyimide, while offering superior thermal and mechanical properties, comes at a premium. Exploring alternatives such as polyester (PET) can drastically reduce material costs, although it is essential to consider the trade-offs in temperature resistance and long term reliability. LCP (Liquid Crystal Polymer) is gaining traction in high frequency applications due to its superior electrical properties, but can also be a more expensive option. PEN (Polyethylene Naphthalate) is another alternative with moderate performance and cost. Other modified polymers are also emerging with varying price and performance trade offs.
Supplier Selection: Finding the Right Partner for Cheap Flex PCBs
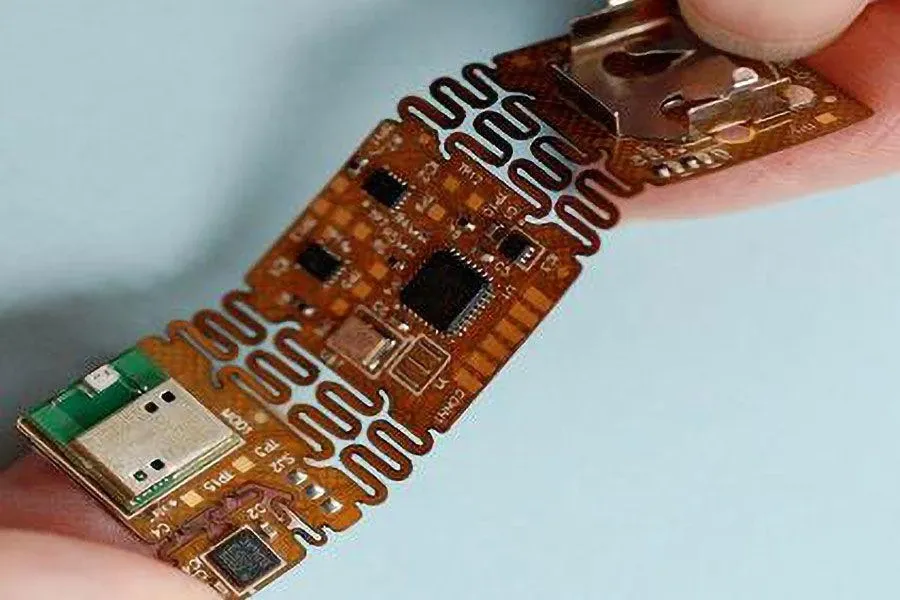
Selecting the appropriate supplier is crucial for obtaining cost-effective flex PCBs without sacrificing quality or reliability. This involves a strategic approach to evaluating potential manufacturers, understanding their capabilities, and effectively comparing quotes to ensure your project's requirements are met within budget.
- Assess Manufacturing Capabilities
Evaluate if the supplier possesses the necessary equipment, technology, and expertise to handle your specific flex PCB design. This includes layer count, material compatibility, and tolerance requirements. - Request and Compare Quotes
Obtain detailed quotes from multiple suppliers. Ensure each quote includes all project costs, such as tooling, setup, and any additional charges, to accurately compare pricing. Scrutinize not just the unit price but also the total project cost. - Evaluate Material Expertise
Inquire about the types of flexible materials the supplier commonly uses and their proficiency with each. Confirm they have experience with your selected materials, or are able to provide viable cost-effective alternatives with comparable performance. - Review Turnaround Time
Consider the lead time required by each supplier. Balance project deadlines with potential cost savings from suppliers that may have longer lead times. - Check Quality Certifications
Verify that the supplier has relevant certifications (e.g., ISO 9001, IPC standards) to ensure they adhere to quality control standards. This helps in minimizing defects and maintaining high product quality. - Examine Sample Boards
Whenever feasible, request a sample of a flex PCB from the supplier to evaluate the manufacturing quality, tolerances and overall workmanship. A quality inspection will minimize the risk of mass-produced faulty products. - Communication and Support
Consider the supplier's communication style, responsiveness, and technical support. Clear communication channels are essential for addressing design changes, questions, and any potential issues during production.
Prototyping Strategies to Minimize Initial Expenses
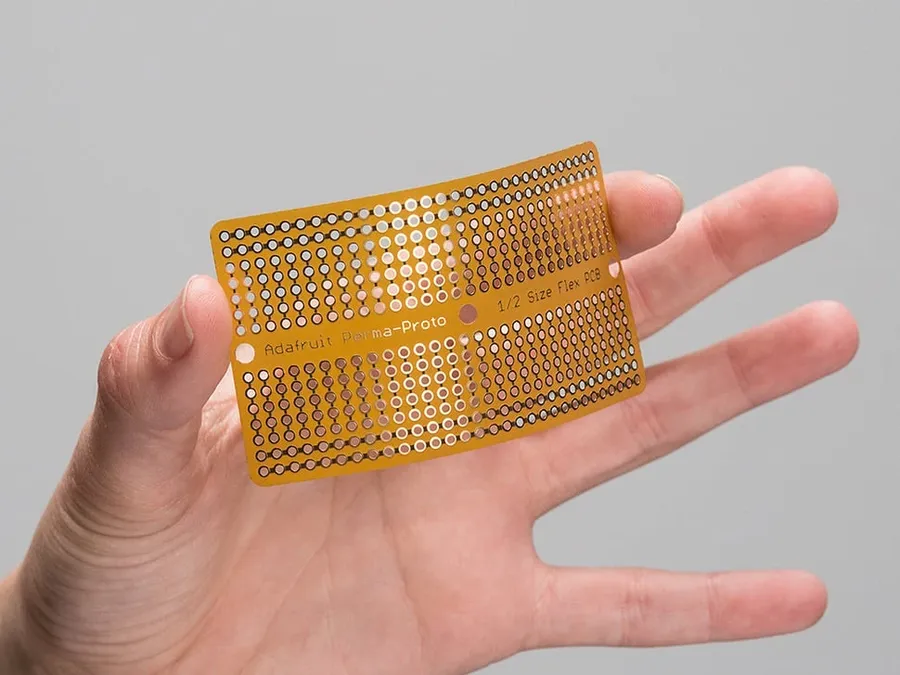
Prototyping flexible PCBs (Flex PCBs) cost-effectively is crucial for validating designs and minimizing financial risks before full-scale production. Efficient prototyping not only reduces initial expenses but also helps refine the product, ensuring better performance and reliability.
- Small Batch Production
Opting for small production runs for prototyping reduces the initial financial outlay. This allows you to test the design with a limited quantity before committing to mass production, thereby decreasing the risk of significant financial losses if any modifications are needed. - Utilize PCB Design Software Simulations
Leveraging sophisticated PCB design software for simulations allows for a comprehensive evaluation of the flex PCB’s performance prior to fabrication. This method uncovers potential design flaws and optimizes performance before production, reducing expenses associated with multiple iterations. - Partial Prototyping
Instead of fully fabricating the entire flex PCB, you can opt for partial prototypes. Focus on critical sections of the flex circuit, and test these areas separately. This approach can significantly reduce prototyping costs, and allows for targeted modifications. - Standardized Components
Using common, readily available components simplifies procurement and reduces cost. Avoiding specialized parts, unless absolutely necessary, will contribute to decreased expenses. - Cost-effective Materials for Testing
For prototyping, using a less expensive substrate material, if possible, can reduce the overall cost. Ensure it is suitable for testing purposes. For instance, polyester-based substrates can be a cost-effective alternative to polyimide for initial testing and validation.
Frequently Asked Questions About Cheap Flex PCBs
Navigating the world of flexible printed circuit boards (PCBs) can raise numerous questions, especially when cost is a significant factor. This section addresses common queries related to finding affordable flex PCB solutions, providing clarity on pricing, cost-effective design choices, and reliability.
- How much does a flex PCB typically cost?
The cost of a flex PCB varies widely depending on several factors, including the complexity of the design, the materials used, the number of layers, the quantity ordered, and the manufacturer. Small, simple designs in low quantities can cost a few dollars each, while complex, multilayer designs in large quantities can be significantly more expensive. It's crucial to get custom quotes based on your project's specific requirements. - What are the most cost-effective PCB finishes for flex PCBs?
The most cost-effective PCB finish options for flex PCBs include ENIG (Electroless Nickel Immersion Gold) and HASL (Hot Air Solder Leveling). ENIG provides excellent solderability and corrosion resistance but can be more expensive than HASL. HASL, while less flat, is a robust and less costly alternative. The best choice for your project will depend on the performance needs and budget. - How can I reduce the cost of manufacturing flex PCBs?
Several strategies can help reduce flex PCB manufacturing costs, including: minimizing the number of layers, simplifying the design and avoiding complex geometries, opting for standard sizes and shapes, choosing less expensive materials (e.g., polyester instead of polyimide for certain applications), negotiating with manufacturers for bulk orders, and ensuring your design is optimized for manufacturability. Working closely with your manufacturer during the design phase can also help you identify areas where costs can be reduced without compromising functionality. - Are flex PCBs reliable, and what factors affect their reliability?
Flex PCBs are generally very reliable when designed and manufactured correctly. Key factors affecting their reliability include: material selection (polyimide is generally very robust but other materials may be more suitable depending on the application), proper stress analysis, appropriate design for dynamic flexing if required, and ensuring the manufacturer follows stringent quality control standards. It's important to consider the application environment (temperature, humidity, etc.) when choosing flex PCB materials and design. For applications that require high reliability, conducting thorough testing is critical to identify potential failures before mass production. - Are there cost-effective alternatives to polyimide for flex PCBs?
While polyimide is a popular choice for flex PCBs due to its excellent thermal and mechanical properties, other cost-effective alternatives such as polyester (PET) are available. Polyester can be a good option for applications that require less demanding performance characteristics and are not exposed to high temperatures. However, it's crucial to evaluate the specific application and environmental conditions when selecting materials to ensure performance and reliability. - How does the quantity of flex PCBs affect the unit cost?
The quantity of flex PCBs ordered has a significant impact on the unit cost. Larger production runs generally result in a lower per-unit cost due to economies of scale. Set-up costs, such as tooling and design preparation, are often distributed across a larger number of units, which reduces the cost per PCB. Consider consolidating orders or planning for future needs to leverage quantity discounts. - What are some common mistakes that increase flex PCB costs?
Common mistakes that can increase flex PCB costs include: overly complex designs with unnecessary features, tight tolerances that are not necessary, specifying expensive materials when cheaper alternatives would suffice, and choosing a manufacturer with high setup costs or limited experience with flex PCBs. It's also important to avoid making significant design changes after fabrication has started, as this can increase time and production cost. Thorough design reviews and choosing the right manufacturer can prevent these costly mistakes.
Comparing Flex PCB Manufacturing Options
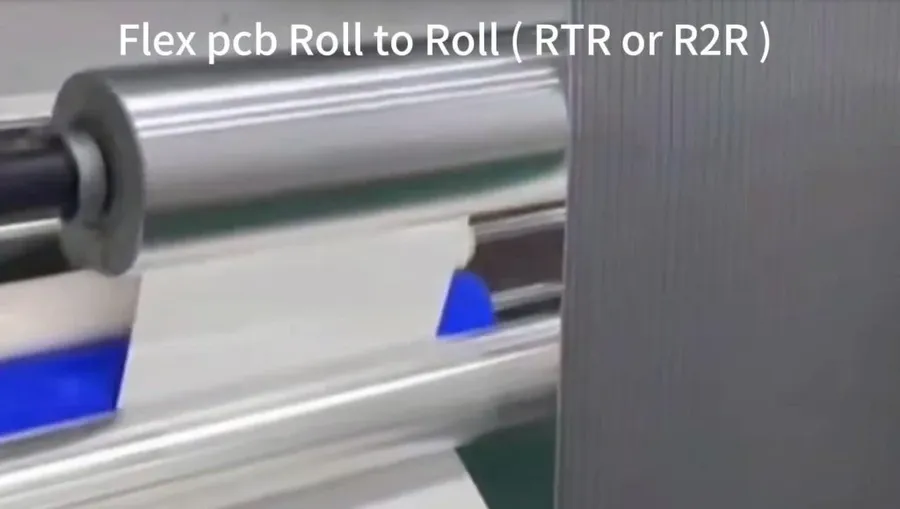
Selecting the optimal manufacturing approach for flexible printed circuit boards (PCBs) is crucial for balancing cost, quality, and project requirements. This section provides a comparative analysis of different manufacturing options, enabling informed decision-making for cost-effective flex PCB production.
Feature | Prototype Manufacturing | Small Batch Production | Large Scale Production |
---|---|---|---|
Typical Order Quantity | 1 - 100 Units | 100-1000 Units | 1000+ Units |
Cost Per Unit | High | Medium | Low |
Lead Time | Fast (1-2 weeks) | Moderate (2-4 weeks) | Longer (4+ weeks) |
Process Optimization | Limited | Some | Extensive |
Best Use Case | Initial Design Testing, Quick Iteration | Pilot Production, Medium Size Projects | Mass Market Products, Cost-Critical Applications |
Tooling Costs | Lower | Moderate | Higher |
Supplier Flexibility | High | Medium | Low |
Design Complexity | Suitable for simple to moderately complex designs | Suitable for most design complexities | May require more stringent design rules to improve manufacturability and reduce cost |
Key considerations when evaluating flex PCB manufacturers include their technological capabilities, quality control procedures, and pricing structures. Factors such as material options, layer count, and the intricacy of design can also impact cost and production feasibility. It's advisable to obtain quotes from multiple suppliers and analyze them based on these parameters.
Future Trends in Affordable Flex PCB Technology
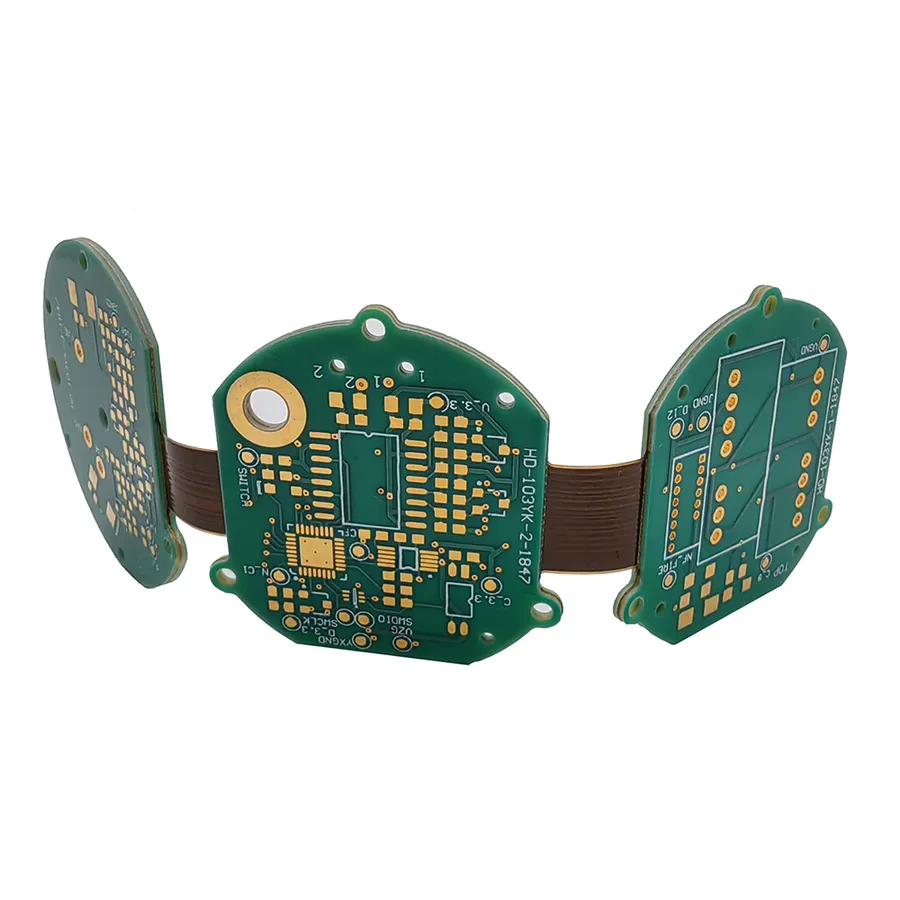
The future of flexible PCB technology is poised for significant advancements, driven by the continuous demand for smaller, more efficient, and cost-effective electronics. Innovations in materials, manufacturing processes, and design tools are expected to play key roles in reducing the cost of flex PCBs while improving their performance and reliability.
- Advanced Materials
The development of new flexible substrates beyond traditional polyimide, such as low-cost polymers, bio-based materials, and flexible glass, promises to lower material costs. These materials are explored for their potential to provide comparable performance with reduced manufacturing expenses and enhanced sustainability. For example, research into the use of nano-materials to create conductive inks and pastes that can be printed onto low cost substrates holds promise. - Innovative Manufacturing Processes
Additive manufacturing techniques, such as inkjet printing and 3D printing, are being explored to produce flex PCBs with minimal material waste and at lower production costs. These methods allow for the creation of complex designs with greater precision, and scalability, reducing the reliance on traditional subtractive methods involving chemical etching and waste. This also allows for greater material utilization and customized production. - Automation and AI
Automation of flex PCB manufacturing processes through robotics and AI-driven optimization is expected to improve production efficiency, increase yield rates, and reduce human labor costs, subsequently decreasing the price of flexible PCBs. AI algorithms can also help optimize design rules and material selection for cost-effectiveness. In addition, the application of AI in quality control will improve precision and reduce error rates, resulting in higher-quality, lower-cost PCBs. - Standardization and Design Optimization
Increased standardization in flex PCB design and manufacturing will enable economies of scale, leading to reduced costs. In addition, the development of more sophisticated design tools and libraries will improve the efficient use of resources and reduce the overall design time. This includes design for manufacturing (DFM) analysis tools that optimize layouts for cost-effective production, and software that allows engineers to optimize layer count, material use, and trace routing, reducing production costs. - Integrated Components
The integration of components directly into the flexible substrate, such as embedded passives and chip-on-flex technology, reduces the number of assembly steps and the overall cost of flex PCB manufacturing. Such advancements reduce the need for discrete components and additional assembly steps, leading to a more streamlined and cost-effective process.
Finding cheap flex PCB solutions is achievable with strategic planning and the right choices. By understanding cost drivers, optimizing your design, selecting appropriate materials, and choosing the right supplier, you can create high-quality, affordable flexible circuit boards for your next project. Remember to consider prototyping methods and stay updated on technological advancements to further reduce expenses and ensure your long-term cost savings for cheap flex PCB.
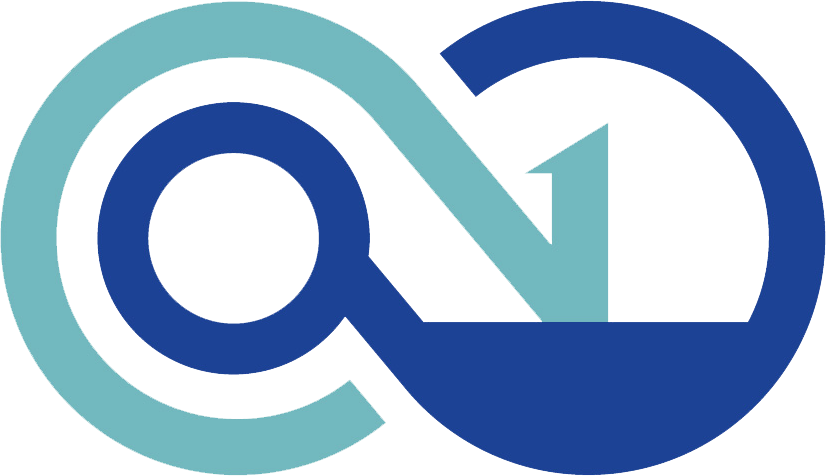