Finding the Right PCB Sheet Suppliers: A Comprehensive Guide
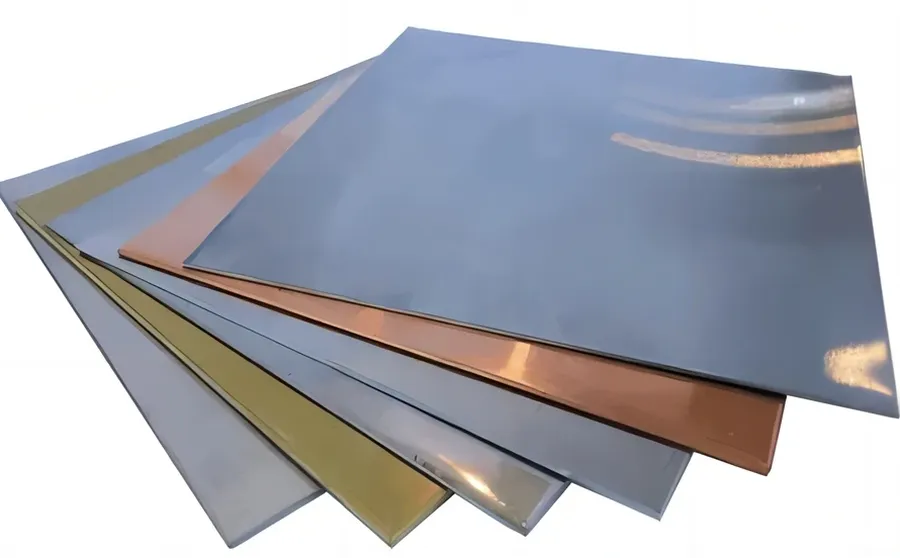
Printed circuit boards (PCBs) are the backbone of modern electronics, silently powering our smartphones, computers, and countless other devices. Selecting the right PCB sheet suppliers is crucial for ensuring the quality and reliability of these essential components. This article will guide you through the process, highlighting key considerations and offering practical advice for choosing the best supplier for your project, ultimately ensuring the smooth flow of your production cycle.
Understanding PCB Sheet Materials
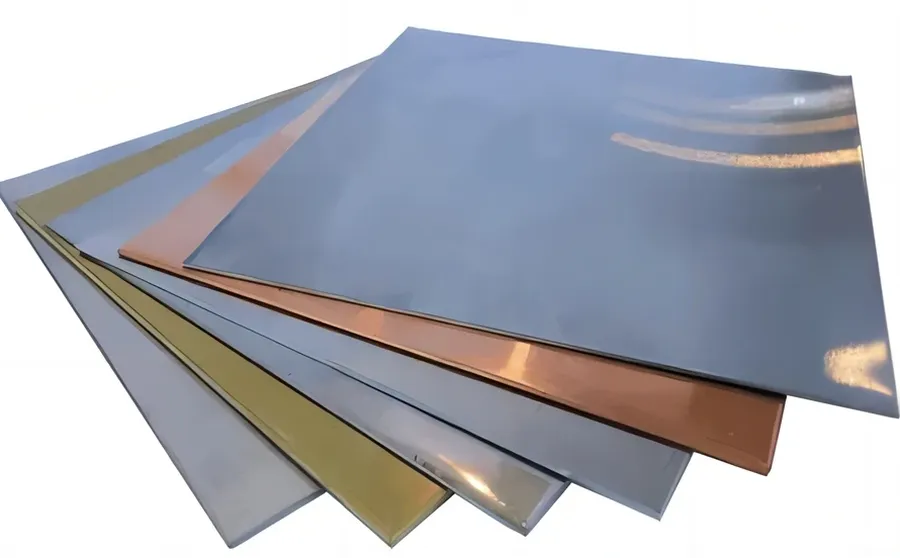
The selection of appropriate PCB sheet materials is paramount for the performance and longevity of electronic devices. Different materials offer varying electrical, thermal, and mechanical characteristics, making material selection a critical aspect of PCB design based on application requirements. A deep understanding of these materials is fundamental for engineers and designers.
Material | Description | Typical Applications | Advantages | Disadvantages |
---|---|---|---|---|
FR-4 | Most common, fiberglass-reinforced epoxy laminate. It has good electrical properties, strength and moisture resistance. | General purpose PCBs, consumer electronics, computer hardware. | Cost-effective, widely available, good mechanical strength and electrical insulation. | Limited thermal conductivity, not suitable for high-frequency applications |
Metal Core (MCPCB) | Metal substrate (usually aluminum or copper) with a dielectric layer. High thermal conductivity. | LED lighting, power electronics, high-power circuits. | Excellent heat dissipation, improved thermal management. | More expensive than FR-4, heavier, can be electrically conductive, requires careful design |
Flexible Substrates | Polyimide or polyester based flexible materials for circuits that must bend or fold. | Flexible electronics, wearable devices, automotive electronics. | Flexibility, light weight, can fit into complex shapes. | Lower mechanical strength, more costly, more difficult to manufacture |
Rogers Materials | High-performance laminates, typically PTFE-based, offer excellent electrical properties at high frequencies. | RF applications, microwave circuits, aerospace. | Low dielectric loss, stable electrical properties at high frequencies. | Expensive, difficult to process and manufacture |
CEM-1 | Composite material of paper and epoxy. Lower performance compared to FR-4. | Low-end consumer electronics, single-sided boards. | Inexpensive, easy to machine. | Lower mechanical strength, moisture absorption, only single sided |
CEM-3 | Composite of woven glass and epoxy. Better performance than CEM-1 | Consumer electronics, double-sided PCBs. | Better mechanical and thermal properties than CEM-1, cost effective. | Lower performance than FR-4, limited thickness options |
Key Factors to Consider When Choosing PCB Sheet Suppliers

Selecting the right PCB sheet supplier is crucial for ensuring the quality and success of your electronic projects. This involves evaluating several critical factors that directly impact the manufacturing process, the final product, and overall project budget. A thorough assessment of these factors will help you identify a supplier that can consistently meet your specific needs and requirements.
Factor | Description | Importance |
---|---|---|
Manufacturing Capabilities | Assessment of the supplier's equipment, technology, and expertise to handle your specific PCB requirements, including layer count, size, and material types. | Crucial for complex designs and specialized applications. Ensures the supplier can actually produce what you need. |
Material Options | Availability and range of PCB materials offered (e.g., FR-4, metal core, flexible substrates), and their ability to source specialty materials, and meet specific performance and environmental requirements. | Essential to ensure the material matches the electrical, thermal, and mechanical demands of your project. |
Quality Control | Evaluation of the supplier’s quality management system, testing procedures, and adherence to industry standards (e.g., IPC, ISO). | Directly impacts the reliability and performance of the PCB. Essential to avoid failures. |
Lead Times | Analysis of the supplier's typical turnaround time from order placement to delivery, as well as their ability to accommodate rush orders. | Critical for project timelines. Delays can lead to cascading problems. |
Pricing | Comparison of cost structures, including unit price, tooling fees, shipping costs, payment terms, and payment method. | Impacts overall project budget and profitability. Need to balance cost with quality. |
Customer Support | Accessibility and responsiveness of the supplier's customer service team, including communication channels and support during the entire process. | Important for smooth project execution and quick resolution of any issues. |
Local vs. Overseas PCB Sheet Suppliers: Weighing the Pros and Cons
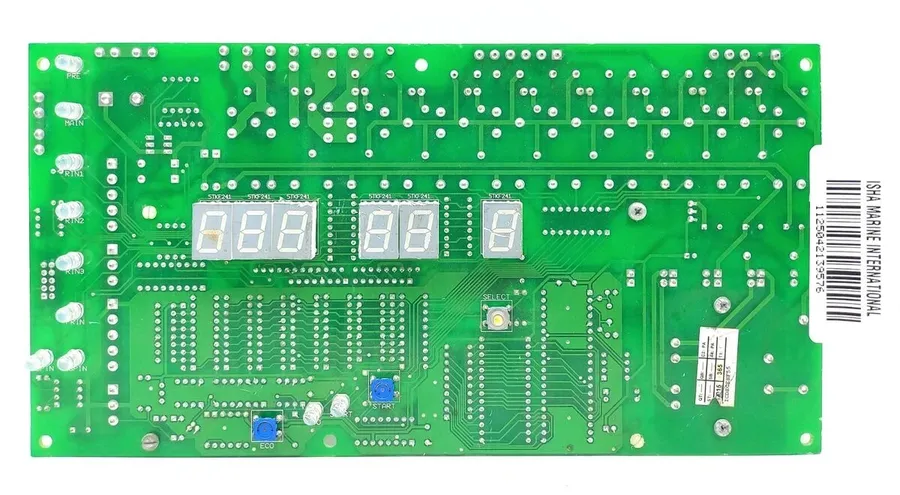
Selecting a PCB sheet supplier involves a critical decision between local and overseas options, each presenting a unique set of advantages and disadvantages. This choice significantly impacts cost, lead times, communication, and overall project risk. A thorough evaluation based on project specifics is paramount.
Factor | Local Suppliers | Overseas Suppliers |
---|---|---|
Cost | Generally higher unit costs due to higher labor and overhead expenses. | Typically lower unit costs, especially for large volume orders, due to lower labor and operational costs. |
Lead Time | Shorter lead times due to proximity and reduced shipping times, facilitating faster turnaround. | Longer lead times due to longer shipping times and potential customs delays, necessitating careful planning. |
Communication | Easier communication due to minimal time zone differences, linguistic and cultural similarities. | More challenging communication due to time zone differences and possible language barriers. |
Quality Control | Potentially easier to monitor and audit processes with closer physical proximity. Direct visits are often easier to arrange. | Quality control may be more difficult to manage due to geographical distance. Requires strong documentation and clear process management. |
Intellectual Property Protection | Potentially stronger IP protection due to legal systems and ease of recourse. | IP protection might be more challenging due to varying legal systems and enforcement practices. |
Flexibility and Customization | Potentially higher flexibility in design changes and customizations, with the opportunity for close collaboration. | Potentially less flexibility in design changes and customizations due to logistical hurdles. |
Shipping and Logistics | Lower shipping costs and simplified logistics due to shorter distances. | Higher shipping costs and complex logistics, with longer transit times and customs clearance procedures. |
Minimum Order Quantity | May be more flexible with smaller order quantities. | Often requires larger minimum order quantities to achieve cost benefits. |
In conclusion, the decision to choose a local or overseas PCB sheet supplier should be driven by your project's specific needs. If speed, quality oversight, and easy communication are paramount, local suppliers may be preferred. If budget constraints are critical and larger production volumes are involved, overseas suppliers could be more suitable. Carefully considering these trade-offs is critical for project success.
Quality Control and Certifications in PCB Manufacturing
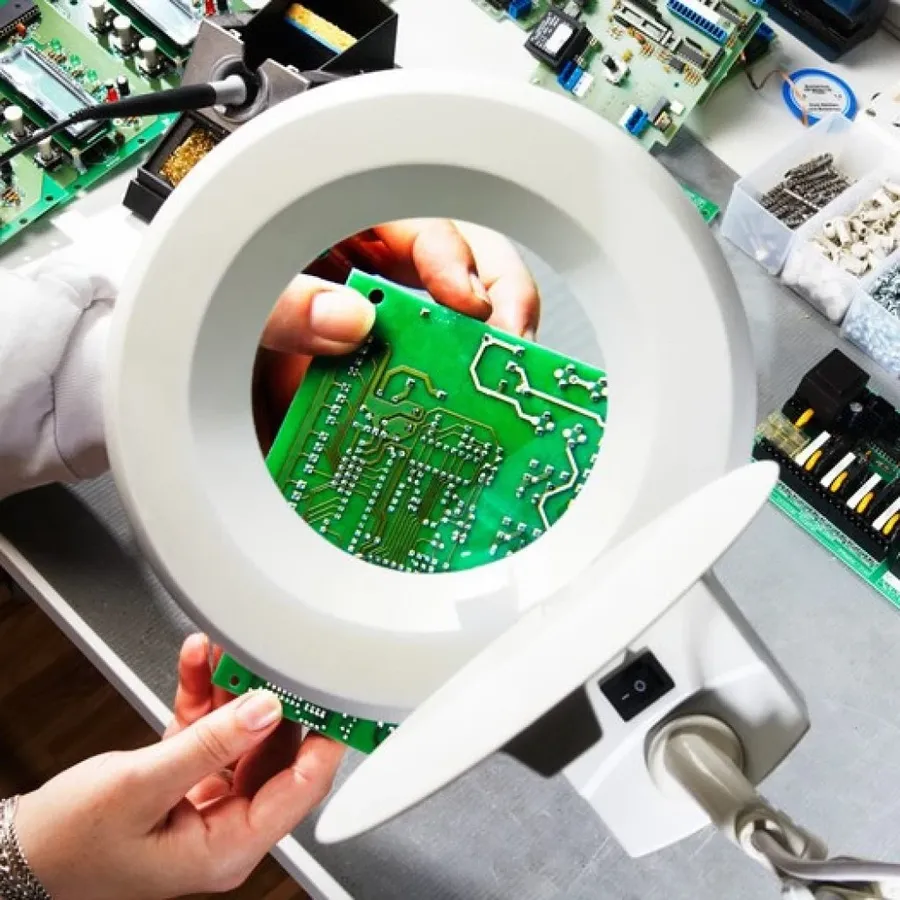
Rigorous quality control and adherence to industry certifications are paramount in PCB manufacturing to ensure the reliability and performance of printed circuit boards. These processes and standards provide assurance that the PCBs meet specific performance criteria and will function as designed.
Several key certifications and standards are relevant to PCB manufacturing, each addressing different aspects of quality and safety:
- ISO 9001
A globally recognized standard for quality management systems. It focuses on ensuring consistent product quality through well-defined processes and continuous improvement. Compliance with ISO 9001 indicates a supplier's commitment to quality management and can be a good indicator of process robustness. - UL Certification
Underwriters Laboratories (UL) certification is a safety certification, particularly important for electronic products. UL standards cover aspects like flammability, electrical safety, and material performance. UL certification is crucial if your PCBs are used in a device sold to consumers. - IPC Standards
The IPC, formerly known as the Institute for Printed Circuits, develops industry standards for printed circuit boards. IPC standards cover everything from design to manufacture and assembly. IPC standards define acceptable criteria for all levels of PCB manufacturing. Adhering to these standards can greatly enhance quality and reliability of the finished product. Common standards include IPC-A-600 for PCB acceptability and IPC-6012 for PCB qualification and performance. - RoHS Compliance
The Restriction of Hazardous Substances (RoHS) directive restricts the use of hazardous materials in electronics. RoHS compliance is not just a matter of quality, but also of regulatory compliance. The directive restricts the use of certain hazardous materials, most notably lead, mercury, cadmium and hexavalent chromium. Suppliers must be RoHS compliant to sell PCB based products to the EU and various other countries. - Other Standards and Certifications
Depending on the application of the PCB there might be other industry-specific standards and certifications relevant. For example, the automotive industry has very strict standards on quality, reliability and traceability of components.
When selecting a PCB sheet supplier, it is crucial to verify if they hold the appropriate certifications and adhere to relevant standards. Suppliers should be able to provide documentation and proof of compliance. Additionally, ask potential suppliers about their internal quality control measures which include in-process inspections, testing procedures, and corrective action processes.
By prioritising quality control and certifications you ensure the reliability, durability and safety of PCBs. Therefore choosing a PCB supplier with a strong quality commitment is critical for your project's success.
Cost-Effective PCB Sheet Procurement Strategies
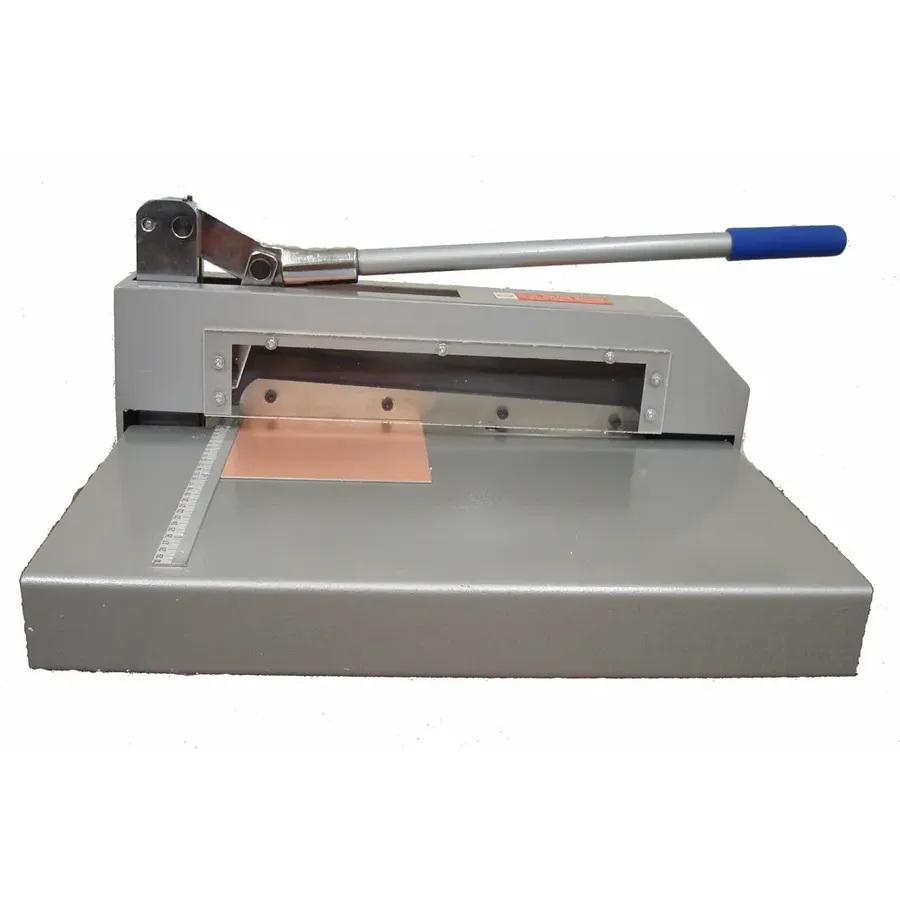
Optimizing PCB sheet procurement costs while maintaining quality is crucial for project success. Strategies involve strategic purchasing, material selection, and proactive supplier engagement, all while aligning with project specifications.
- Bulk Ordering
Purchasing larger quantities of PCB sheets can lead to significant per-unit cost reductions. This is often due to suppliers offering volume discounts, which can result in substantial savings, especially for projects with recurring needs or large-scale production. However, carefully assess your storage capacity and anticipated usage to prevent material waste from over-ordering. - Negotiate Payment Terms
Engage with suppliers to negotiate favorable payment terms such as extended payment periods, milestone-based payments, or early payment discounts. Securing better terms can significantly reduce immediate cash outlay and improve cash flow, giving your company financial flexibility. Building a robust relationship with your supplier often aids in securing favorable payment terms. - Explore Alternative Material Options
Consider using alternative materials that offer comparable performance but at lower costs, such as composite materials or different grades of FR-4. Conduct a comprehensive analysis of material properties and project requirements to ensure that performance is not compromised. Alternative material analysis should involve comprehensive material testing to ensure the design's integrity. - Standardization of Designs
Using standard board sizes and stack-ups in design will help reduce costs by leveraging the efficiency of volume production and economies of scale. In general, it's best to stick with popular stack-ups as this will allow for more competition between manufacturers, which helps reduce costs. - Efficient Panelization
Efficient panelization will allow the manufacturer to produce more boards per panel which will reduce production costs. Always design panels with manufacturability in mind so the designs can be produced efficiently. - Optimize Design for Manufacturing (DFM)
Design your PCB to reduce the complexity of the manufacturing processes to reduce costs. DFM considers manufacturability from the outset which helps reduce cost, turnaround time, and improve the overall reliability of the design.
Building a Strong Relationship with Your PCB Sheet Supplier
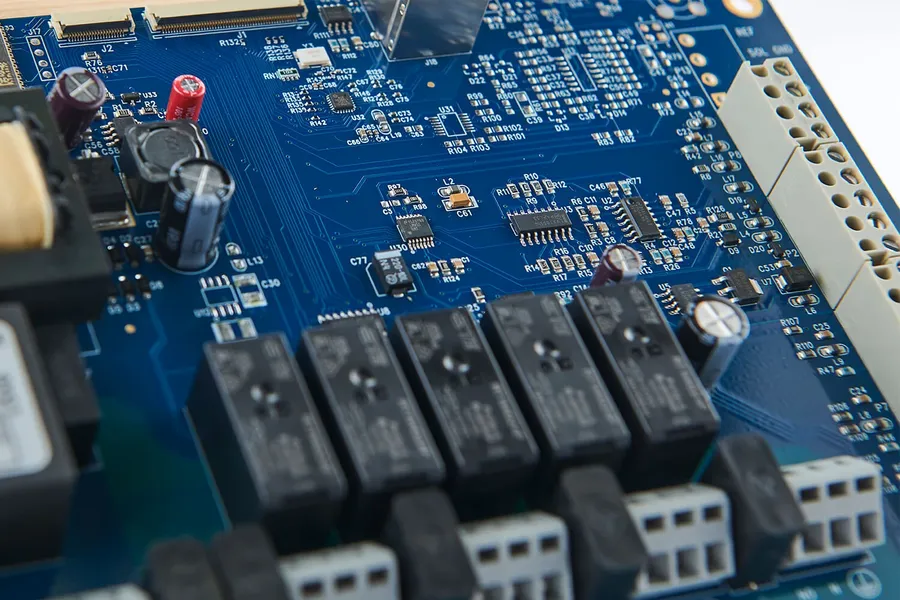
A robust and reliable supply chain is crucial for the success of any electronics project, and the foundation of a strong supply chain is a positive and collaborative relationship with your PCB sheet supplier. This involves more than just transactional interactions; it necessitates open communication, mutual understanding, and a commitment to long-term partnership to ensure consistent quality, on-time delivery, and effective problem-solving.
- Establish Clear Communication Channels
Define preferred methods of communication and establish regular check-ins to discuss project progress and any potential issues. - Foster Mutual Understanding
Take time to understand your supplier’s processes and limitations, and proactively provide all necessary information upfront to avoid misunderstandings and delays. - Commit to Long-Term Collaboration
Look for suppliers willing to invest in a long-term relationship by working to understand your evolving needs, adapting to your unique requirements, and contributing to the overall success of your projects. - Focus on Consistent Quality
Regular communication and collaboration with the supplier will increase the likelihood of getting consistent quality, which helps to reduce failure rates and improves efficiency. - Ensure Timely Delivery
Building a strong relationship with your supplier will increase the likelihood of meeting deadlines, which reduces delays and ensures smooth project execution. - Enhance Problem Solving
A strong relationship with your supplier ensures open communication channels which facilitates a quicker and more effective way to resolve issues, which will reduce downtime and minimizes potential losses.
Frequently Asked Questions About PCB Sheet Suppliers
Navigating the PCB supply chain can be complex, and many questions arise when selecting a suitable PCB sheet supplier. This section addresses those common inquiries, providing concise and authoritative answers to ensure you have a clear understanding of the process.
- What are the typical minimum order quantities (MOQs) for PCB sheets?
MOQs vary widely among suppliers and depend on factors such as material type, board thickness, and complexity. Some suppliers cater to prototyping with low MOQs, while others, often large manufacturers, have higher volume requirements. It's crucial to inquire about the supplier's specific MOQ policy early in your selection process. Generally, MOQs are influenced by the supplier's production efficiency and the need to cover setup costs. - What design file formats do PCB sheet suppliers typically require?
Suppliers commonly accept Gerber files, which are industry-standard vector files for PCB manufacturing. In addition, they might support other formats like ODB++ or IPC-2581, which contain richer information. It is paramount to consult with your chosen supplier to ensure compatibility of your design files to avert any delays and potential rework. Gerber RS-274X is the most widely used format. - What are the typical turnaround times for PCB sheet fabrication and delivery?
Turnaround times are contingent on the complexity of the PCB, the supplier's current workload, and the selected shipping method. Simple, single-layer PCBs may have a turnaround as short as a few days, while intricate multi-layer boards can take several weeks. Expedited services are often available but usually come with higher prices. It's advisable to discuss lead times with your supplier before placing an order, and consider these times when planning the entire product development cycle. Always factor in shipping times. - Can PCB sheet suppliers provide design assistance or DFM (Design for Manufacturing) feedback?
Many PCB sheet suppliers offer design support and DFM analysis. DFM aims to optimize a PCB's design for manufacturability, identifying and resolving potential issues such as trace widths, spacing, and via placements. This service minimizes manufacturing errors, improves reliability, and reduces overall costs. Always request a DFM check before production. - What certifications should I look for in a PCB sheet supplier?
Essential certifications include ISO 9001 for quality management, UL certifications for product safety, and industry-specific standards like IATF 16949 for automotive applications. These certifications ensure that the supplier adheres to rigorous quality control and manufacturing processes, producing dependable PCBs. Request certificates and perform due diligence prior to engaging any supplier. - What are the standard PCB sheet material options provided by suppliers?
Standard PCB sheet materials offered include FR-4 (the most common), high-frequency materials (like Rogers), metal core (for heat dissipation), flexible substrates (like polyimide), and others. The selection depends on the application's performance requirements, environmental conditions, and cost constraints. Ensure to consult with your supplier about what material will provide you the best cost and performance outcome. FR-4 is highly cost effective and versatile. - What is the best way to ensure the supplier meets my PCB quality standards?
Establish clear communication with the supplier regarding quality expectations, implementing regular inspections during production and final QC. Request sample boards for testing, and maintain detailed documentation of all quality control checks. It's important to build a relationship based on quality and trust with any supplier, especially a PCB supplier. Ensure you have a documented QC process.
The Future of PCB Sheet Materials and Manufacturing
The printed circuit board (PCB) industry is undergoing rapid transformation, driven by advancements in materials science, manufacturing technologies, and the ever-increasing demand for smaller, faster, and more versatile electronic devices. Understanding these trends is crucial for selecting suppliers that can meet future project requirements.
Key emerging trends in PCB sheet materials and manufacturing include:
- Flexible PCBs
Flexible PCBs are gaining traction due to their ability to conform to various shapes and sizes, making them ideal for applications in wearables, medical devices, and automotive electronics. Polyimide and other flexible materials are at the forefront of this development, pushing the boundaries of traditional PCB designs. - Advanced Materials
The industry is moving beyond FR-4 to explore high-performance materials with improved electrical, thermal, and mechanical properties. These materials include ceramic substrates, liquid crystal polymers (LCPs), and various composites. The selection of these materials depends highly on the application's specific requirements, including temperature, frequency, and mechanical stress. - Embedded Components
Embedding passive components (resistors, capacitors) directly into the PCB substrate is becoming more common. This technique allows for greater miniaturization, reduces assembly costs, and improves the overall performance of electronic circuits. Suppliers who can offer such embedding technologies will be in higher demand. - Additive Manufacturing (3D Printing)
3D printing is revolutionizing PCB manufacturing by enabling the rapid prototyping of complex designs and customized boards without the need for traditional tooling. This technology offers a more sustainable method of manufacturing as well, reducing waste by printing only the necessary material. - Eco-Friendly Materials
Environmental regulations and sustainability concerns are driving the adoption of eco-friendly materials in PCB production. Suppliers are exploring bio-based resins, recycled materials, and processes that reduce chemical consumption and waste generation. - High-Density Interconnect (HDI)
The demand for smaller and more functional devices has led to an increased usage of HDI PCB technologies. HDI boards feature thinner lines and spaces, enabling denser component mounting. Suppliers who offer HDI manufacturing capabilities will be highly valuable for advanced electronics. - Thermal Management Solutions
As electronic devices get more powerful and compact, efficient thermal management is critical. PCB materials and designs are being optimized to dissipate heat more effectively, ensuring performance and reliability. Metal core PCBs (MCPCBs) are increasingly used for high-power applications.
Choosing a PCB sheet supplier with capabilities in these emerging trends is essential for future-proofing your designs and ensuring access to cutting-edge technology.
Comparative Analysis: Top PCB Sheet Suppliers
Selecting the right PCB sheet supplier is a critical decision that can significantly impact the cost, quality, and timeline of your electronics project. This section provides a comparative analysis of several top PCB sheet suppliers, highlighting their key strengths and capabilities. The information is synthesized from various SERP results to provide a concise and informative overview, empowering you to make well-informed decisions.
Supplier | Strengths | Capabilities | Target Customer | Notes |
---|---|---|---|---|
JLCPCB | Low cost, fast turnaround, good for prototyping | PCB fabrication, assembly, SMT, stencil | Hobbyists, small to medium-sized businesses | Popular for quick-turn and low-cost needs. |
PCBWay | Wide range of materials, advanced technologies, customer support | PCB fabrication, assembly, CNC machining | Medium to large businesses, engineers | Good for complex projects and specific material requirements. |
Local/Regional Suppliers | Stronger communication, faster lead times, better quality control | Varies depending on the specific supplier | Businesses requiring strict quality control, faster lead times, or special materials. | May come at a premium price. |
Overseas Suppliers (excluding JLCPCB and PCBWay) | Potentially lower costs, higher volumes | Wide range, depends on supplier. | Large-scale manufacturing | Requires careful vetting for quality control. |
Choosing the right PCB sheet suppliers is a critical step in the product development process that can influence both the quality and cost-effectiveness of your electronics projects. By understanding the nuances of materials, quality standards, and supplier relationships, and by looking at potential PCB sheet suppliers, you can secure a reliable source of PCBs, enabling smooth production and successful deployment of your products. Remember to continually evaluate and adapt your strategies to remain ahead of the curve in this constantly evolving field.
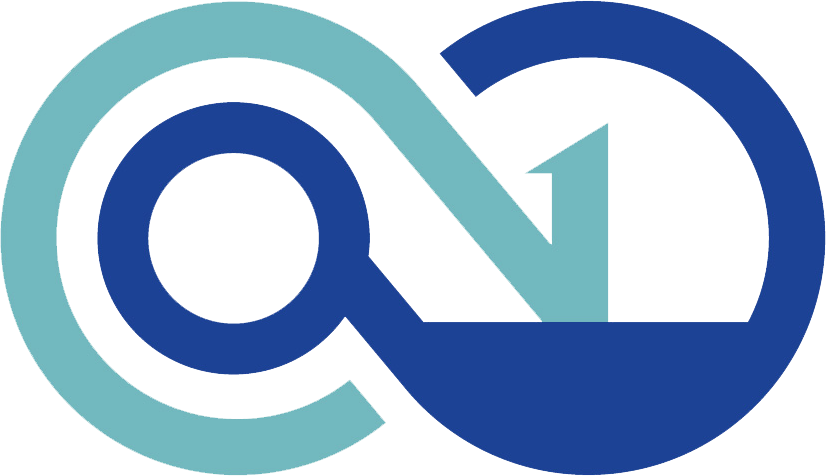