Finding the Right SMT PCB Assembly Supplier: A Comprehensive Guide
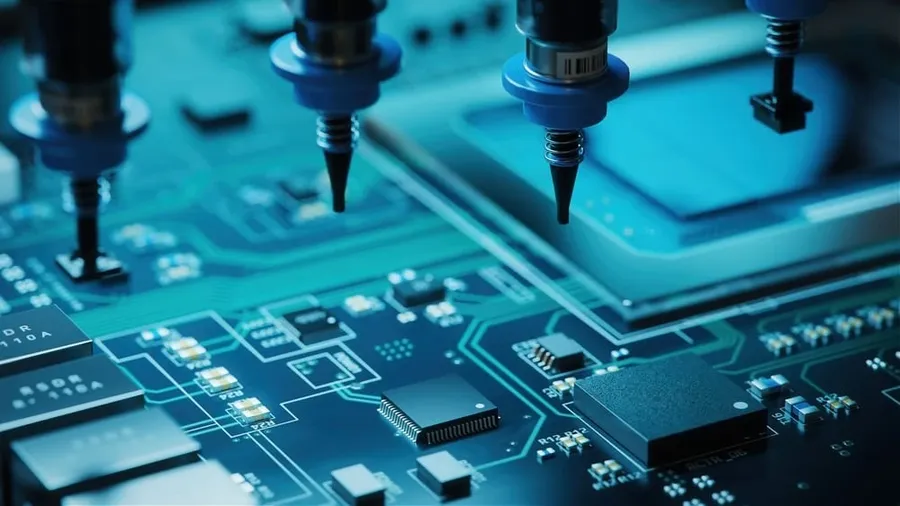
In today's technology-driven world, the reliability of electronic devices hinges heavily on the precision of their printed circuit boards (PCBs). Surface Mount Technology (SMT) has become the cornerstone of modern electronics manufacturing, with a reliable SMT PCB assembly supplier being crucial for success. This article explores the key considerations when choosing a supplier, delving into the nuances of SMT assembly processes to help you find the perfect partner. We'll bridge the gap between complex technical processes and real-world application, ensuring you are empowered to make informed decisions about your PCB assembly needs.
Understanding SMT PCB Assembly and Its Importance
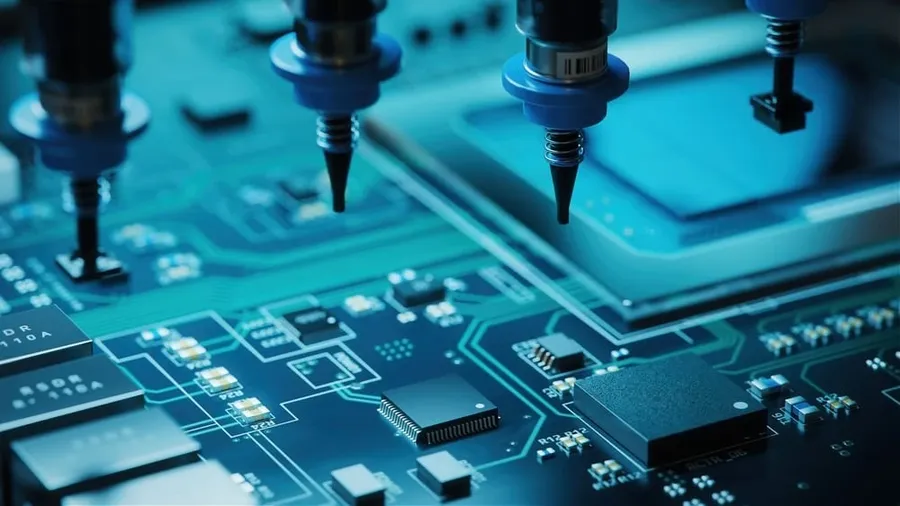
Surface Mount Technology (SMT) is the cornerstone of modern electronics manufacturing, enabling the efficient and precise assembly of electronic components onto printed circuit boards (PCBs). Its adoption has revolutionized the industry, offering significant advantages over traditional through-hole technology and underscoring the crucial role of a dependable SMT PCB assembly supplier in today’s electronics landscape. SMT's dominance stems from its ability to produce smaller, faster, and more feature-rich electronic devices.
The shift from through-hole to SMT assembly was driven by several factors. Firstly, the reduction in component size afforded by SMT allowed for greater circuit density, enabling more complex functionalities within a smaller space. Secondly, SMT lends itself better to automated assembly processes, greatly enhancing manufacturing speed and efficiency. Finally, the inherent design of SMT components results in lower electromagnetic interference, leading to more reliable and stable electronic products.
Feature | Through-Hole Technology | Surface Mount Technology (SMT) |
---|---|---|
Component Size | Larger | Smaller |
Circuit Density | Lower | Higher |
Assembly Method | Manual or Semi-Automated | Highly Automated |
Production Efficiency | Lower | Higher |
Electromagnetic Interference | Higher | Lower |
Manufacturing Cost | Higher | Lower |
Key Factors to Consider When Choosing an SMT PCB Assembly Supplier
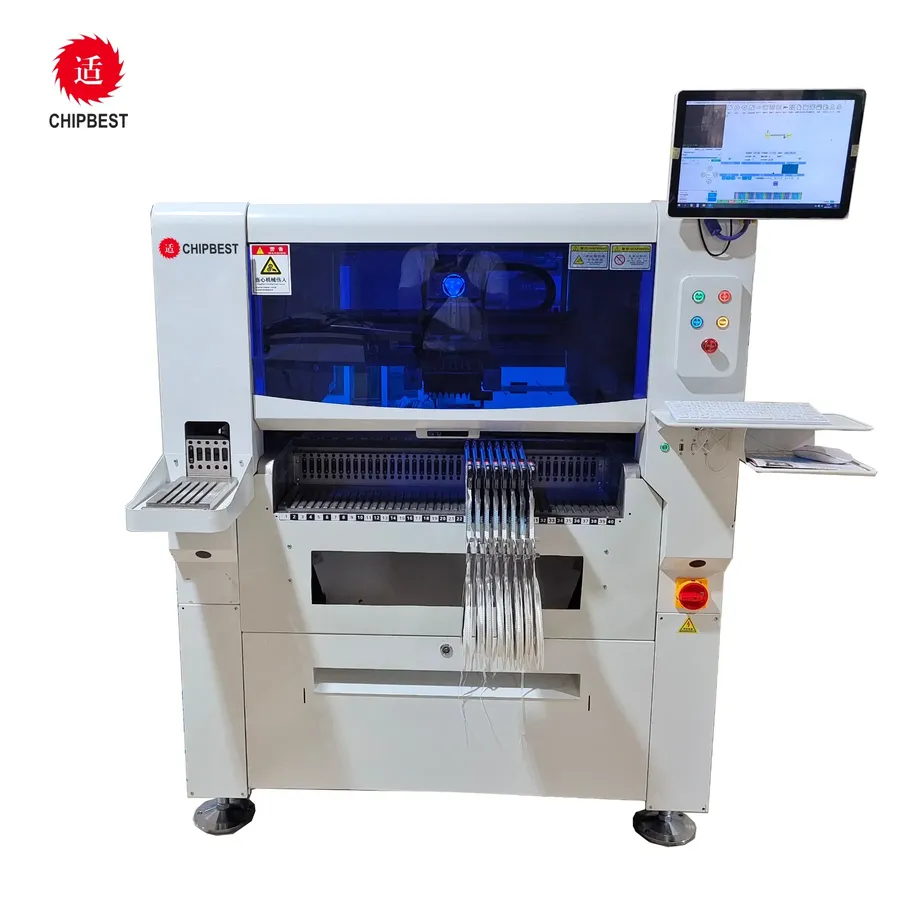
Selecting the right SMT PCB assembly supplier is critical for ensuring the quality and reliability of electronic products. This section details essential factors to evaluate when choosing a supplier, focusing on certifications, experience, capacity, technology, sourcing, and lead times, all of which directly impact the final product's quality and cost.
Factor | Description | Importance |
---|---|---|
Certifications (ISO, AS9100) | Compliance with international quality standards such as ISO 9001, ISO 13485 (for medical devices), and AS9100 (for aerospace). | Indicates the supplier's commitment to quality management and process control, crucial for consistent output and reliability. |
Experience | Years of operation and specific experience with the type of assembly required (e.g., complex boards, fine-pitch components). | Experienced suppliers are more adept at handling complex projects and are less likely to encounter unforeseen manufacturing issues. |
Manufacturing Capacity | The volume of boards that the supplier can produce within a given timeframe. | Ensures the supplier can meet current and future demand without causing delays. Look for scalability for growth. |
Technology Capabilities | The range of SMT equipment and processes available, such as pick-and-place machines, reflow ovens, AOI, and X-ray inspection systems. | Ensures the supplier can handle the technological requirements of the PCB design, including fine-pitch components, BGAs, and advanced assembly techniques. |
Component Sourcing | The supplier's ability to source high-quality components from reputable suppliers, ideally with established relationships and robust supply chain management. | Ensures the use of genuine, high-quality components, reducing the risk of failures due to counterfeit or substandard parts. |
Lead Times | The time required from placing an order to receiving the assembled PCBs. | Critical for timely project completion. Shorter lead times can result in faster time-to-market. |
Quality Control | The implementation of robust quality control procedures at each stage of the assembly process. | Guarantees the final product meets specifications and performs reliably, reducing the risk of defects and failures. |
Prototype, Low-Volume, and High-Volume SMT Assembly Services
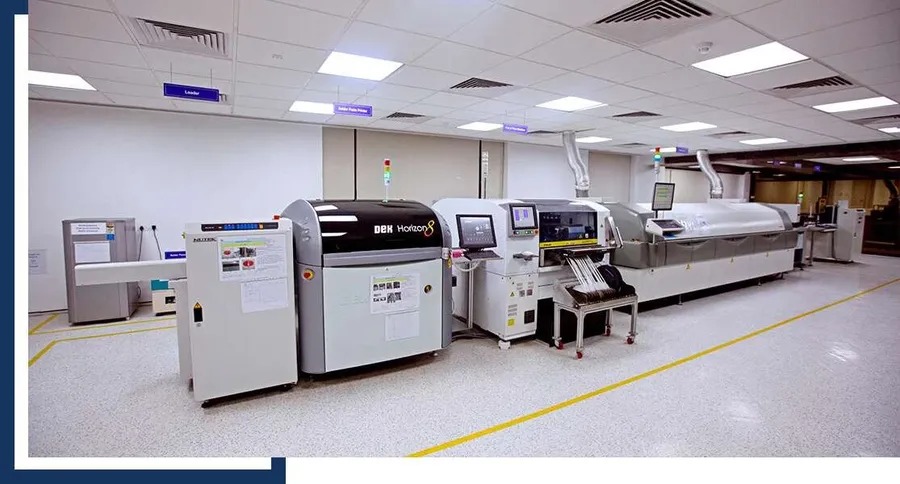
The scale of SMT PCB assembly requirements varies significantly, ranging from initial prototypes to mass production. Understanding these distinct needs is crucial for selecting the right supplier. Each production volume—prototype, low-volume, and high-volume—demands specific capabilities and resources from an assembly partner. Matching your project's scale with a supplier’s specialization is essential for both cost-effectiveness and quality.
Production Volume | Typical Quantity | Purpose | Supplier Focus | Cost Considerations | Turnaround Time |
---|---|---|---|---|---|
Prototype | 1-100 Units | Proof of concept, testing, design validation | Flexibility, quick turnaround, design for manufacturability (DFM) support | Higher per-unit cost due to setup, engineering, and material handling | Fastest, often within days or weeks |
Low-Volume | 100-1000 Units | Small production runs, market testing, niche products | Adaptability, process optimization, material management | Moderate per-unit cost, with some economies of scale | Moderate, typically within weeks |
High-Volume | 1000+ Units | Mass production, large-scale product manufacturing | Automation, efficiency, supply chain management, capacity | Lowest per-unit cost due to optimized processes and volume discounts | Longer lead times may be necessary for large orders |
Selecting the right assembly service is not only about the quantity. It is about ensuring the supplier can efficiently manage specific demands while maintaining quality. For example, prototype runs require a high degree of flexibility and design support, while high-volume runs necessitate robust supply chain and automated manufacturing. Different suppliers have different strengths, and this should be a key factor to consider when evaluating potential partners.
The SMT Assembly Process: From Stencil Printing to Reflow Soldering
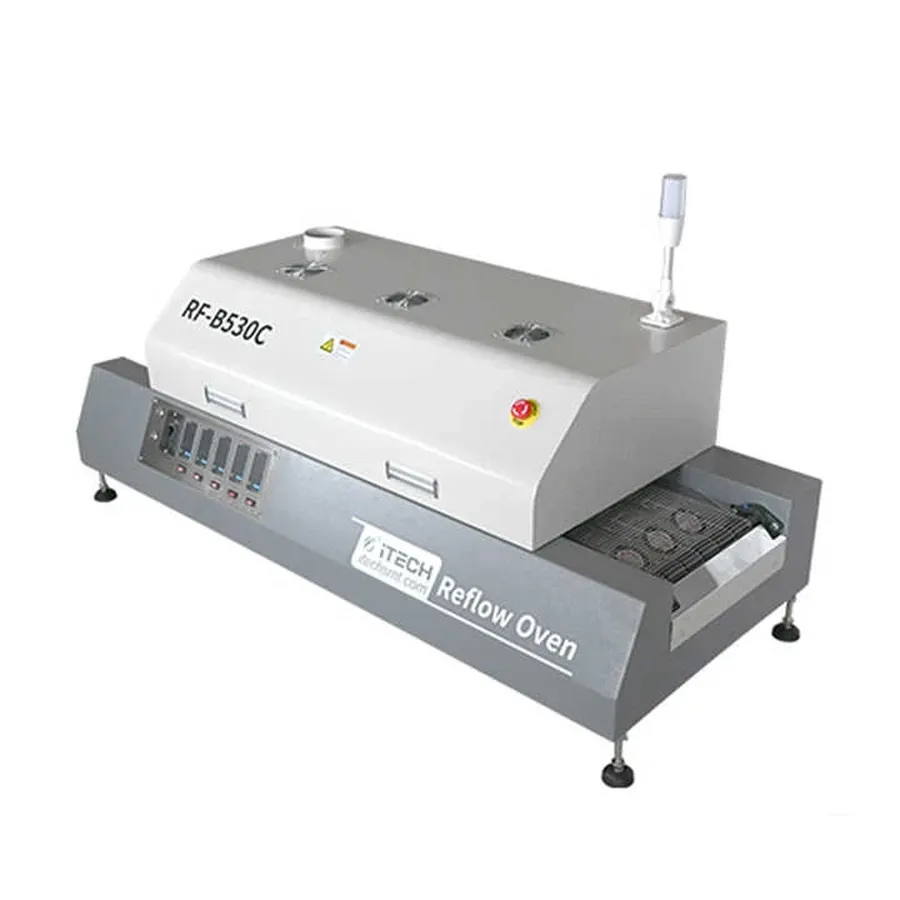
The Surface Mount Technology (SMT) assembly process is a sophisticated sequence of steps crucial for manufacturing modern electronic devices. It encompasses a precise workflow from solder paste application to final testing, with a strong emphasis on precision and quality control at every stage to ensure the reliability of the final product.
Below is a detailed breakdown of each key step involved in the SMT assembly process:
- Solder Paste Application (Stencil Printing)
The process begins with applying solder paste onto the PCB pads using a stencil. This stencil, custom-made for each board design, ensures accurate solder deposition. The quality of the solder paste and printing process is vital for reliable solder joints. - Component Placement
Automated pick-and-place machines then accurately position surface mount components onto the PCB. These machines use CAD data from the PCB design, placing components at precise locations. Correct orientation and placement are essential to prevent assembly defects. - Reflow Soldering
The PCB then passes through a reflow oven, which uses a controlled temperature profile to melt the solder paste, creating reliable solder joints between components and the board. The reflow profile is customized for each design to avoid overheating components and ensure the correct solder flow. This stage requires precise thermal control to ensure good connections without damaging components. - Inspection
After reflow soldering, various inspection methods are used to verify the quality of solder joints and component placement. Automated Optical Inspection (AOI) and X-ray inspection are used to detect common defects like misaligned components, shorts, and open circuits. The inspection methods must be able to identify various types of defects. - Testing
Finally, the assembled PCBs undergo electrical testing to confirm they meet the required performance specifications. In-circuit testing (ICT) and functional testing are common methods used to ensure that the product works as intended. These steps are to make sure the assembled PCBs are fully functional and reliable.
Process Step | Description | Key Consideration |
---|---|---|
Solder Paste Application | Application of solder paste to PCB pads via stencil. | Stencil precision, paste quality, alignment accuracy |
Component Placement | Accurate positioning of surface mount components on PCB. | CAD data accuracy, machine calibration, component handling |
Reflow Soldering | Melting solder paste in a controlled temperature environment. | Temperature profile, reflow oven performance, solder alloy |
Inspection | Verification of solder joint quality and component placement. | Automated optical inspection, X-ray capabilities, defect analysis |
Testing | Electrical testing to confirm performance and function. | In-circuit testing, functional testing, test procedure |
Cost Considerations for SMT PCB Assembly
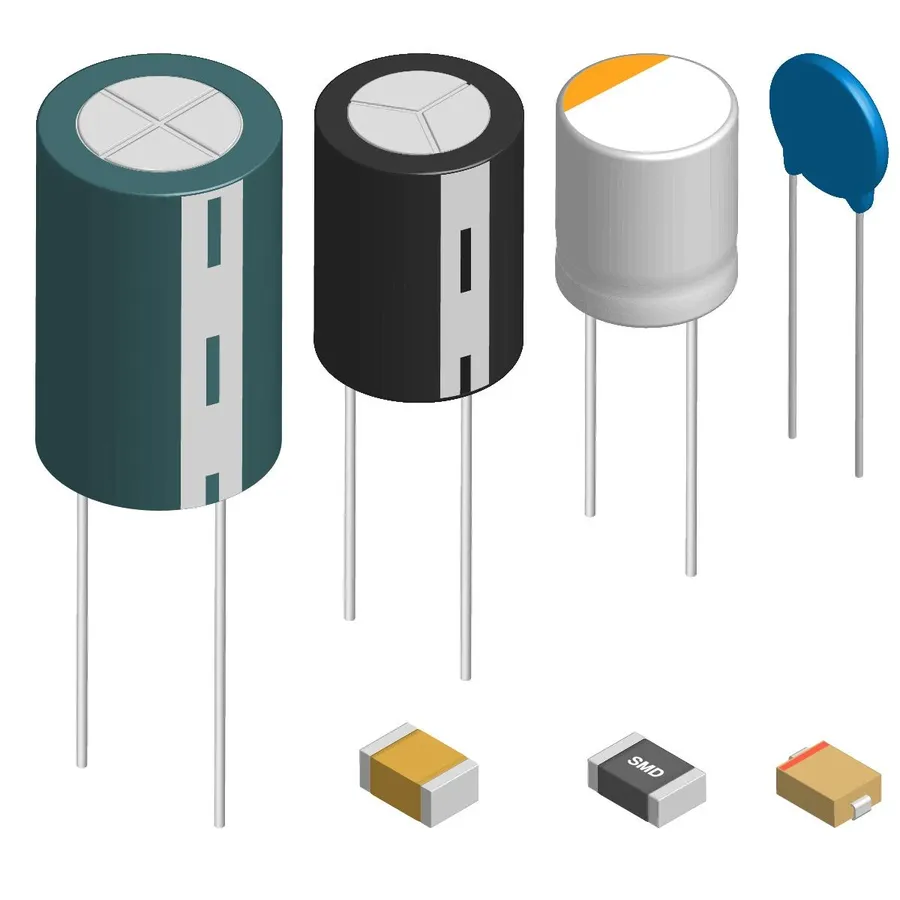
Understanding the cost drivers in SMT PCB assembly is crucial for effective budgeting and maintaining profitability. These costs are influenced by a multitude of factors, including component prices, labor expenses, production volume, and the inherent complexity of the PCB design. Optimizing these factors is key to achieving cost-effective assembly without sacrificing quality and reliability.
Cost Factor | Description | Impact on Cost |
---|---|---|
Component Prices | Cost of electronic components like resistors, capacitors, ICs. | Significant, varies based on part type and quantity. Higher for rare or specialized components. |
Labor Costs | Expenses for skilled labor involved in assembly process. | Varies by region and expertise. Highly automated processes can reduce labor costs. |
Production Volume | Number of PCBs to be assembled. | Economies of scale apply. Cost per unit decreases with higher volumes. |
PCB Complexity | The intricacy of the board design (e.g., number of layers, component density, fine pitch components). | More complex designs necessitate specialized equipment, skills, and may increase rework, leading to higher costs. |
Setup Costs | Initial costs for setting up the assembly line, including stencil creation and machine programming. | More significant for low-volume runs; amortized over the total number of assembled PCBs in high-volume production. |
Testing and Inspection | Costs associated with in-circuit testing, automated optical inspection (AOI), and functional testing. | Essential for quality, but can increase costs. Strategic testing reduces overall costs by finding defects early. |
Lead Time | The time required to complete the assembly process. | Express assembly or quick turnarounds typically cost more than standard lead times. |
To achieve cost-effective SMT PCB assembly, consider these strategies: component standardization to leverage volume discounts and streamlined logistics; design optimization for manufacturability (DFM) to reduce assembly complexity; strategic negotiation with suppliers for better pricing; and implementing robust quality control processes to minimize costly rework and wastage.
Frequently Asked Questions About SMT PCB Assembly
This section addresses common queries regarding SMT PCB assembly, providing concise and authoritative answers to help you make informed decisions. Understanding these frequently asked questions is crucial for anyone involved in electronics manufacturing.
- Who are the major players in the PCB supply market?
While pinpointing the absolute 'biggest' supplier is complex due to varying metrics (revenue, volume, product range), several companies are recognized as leaders in the PCB manufacturing industry. These include global manufacturers like TTM Technologies, Unimicron, and Shennan Circuits. Regional leaders often dominate specific markets. It's crucial to evaluate suppliers based on their ability to meet your specific production needs rather than solely on size. - What is the typical cost range for SMT PCB assembly?
The cost of SMT PCB assembly is highly variable, depending on factors like production volume, PCB complexity, component costs, and chosen supplier. For small prototype runs, costs can range from a few hundred to a few thousand dollars. Larger production runs will experience a lower per-unit cost. To get an accurate estimate, provide your supplier with detailed design files and volume requirements. Component costs and complexity are major cost drivers. - What are some of the most popular SMT machine brands?
Several reputable brands manufacture SMT equipment. Top contenders known for their reliability and advanced technology include Panasonic, Fuji, ASM (formerly Siemens), and Yamaha. These companies offer a wide range of pick-and-place machines, screen printers, and reflow ovens. The optimal choice depends on the specific application, production volume, and budget. - What is the approximate cost of setting up an SMT assembly line?
An SMT assembly line requires significant capital investment. The cost can range from $100,000 for a basic setup to several million dollars for a high-volume, fully automated line. Key costs include pick-and-place machines, screen printers, reflow ovens, inspection equipment, and conveyors. Additional costs may include software, training, and facility upgrades. A staged approach to investment, scaling up as demand increases, is often recommended. - How do I choose the right SMT PCB assembly supplier for my needs?
Selecting an SMT PCB assembly supplier requires careful consideration of several factors. Evaluate their certifications (ISO 9001, AS9100), experience, technology capabilities (fine pitch, BGA), component sourcing, lead times, and quality control. Request sample assemblies and thoroughly vet their processes before making a final decision. Don't solely prioritize the lowest cost, focus on suppliers that offer a balance of quality and cost efficiency. - What are common challenges faced in SMT PCB assembly?
Common challenges in SMT PCB assembly include component placement accuracy, solder joint quality, managing thermal profiles during reflow, and preventing electrostatic discharge. Additionally, maintaining traceability, managing material inventories, and dealing with supply chain disruptions can pose significant issues. Effective process control, rigorous quality inspections, and skilled operators are essential for minimizing these challenges. - How does SMT assembly compare to through-hole assembly?
SMT assembly offers higher component density, smaller footprints, and greater automation potential compared to through-hole assembly. While through-hole provides stronger mechanical connections, SMT is generally faster, more cost-effective for mass production, and facilitates more complex circuit designs. SMT is the dominant technology for surface mount components, while through-hole remains relevant for larger components and connectors requiring greater mechanical strength.
Benefits of Partnering with a Local SMT PCB Assembly Supplier vs. Offshore Options
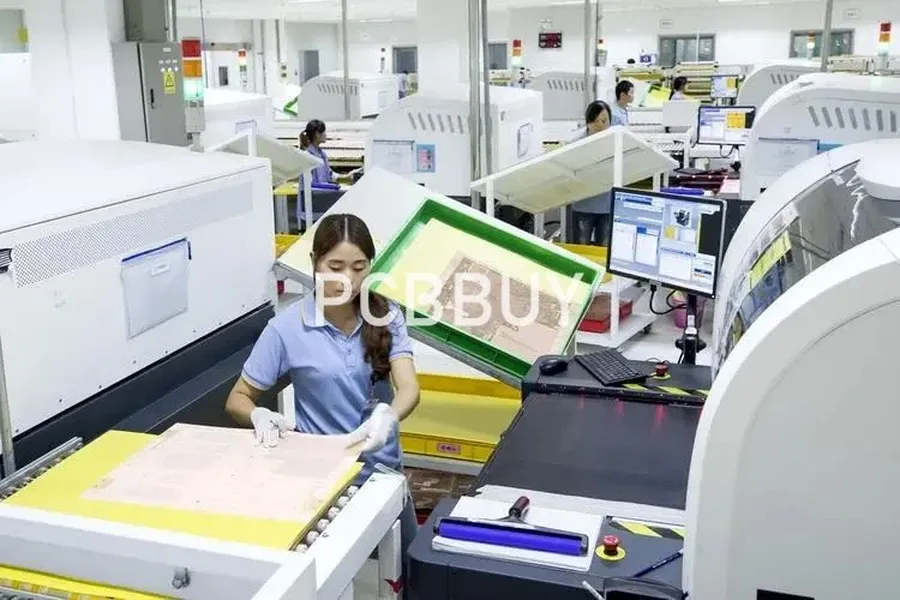
Selecting an SMT PCB assembly supplier involves weighing the advantages of local versus offshore options, each presenting distinct benefits regarding communication, lead times, costs, and quality control. A thorough evaluation of these factors is essential to align with project needs and priorities.
Factor | Local Supplier | Offshore Supplier |
---|---|---|
Communication | Direct, often in-person, easier to resolve issues quickly, same or similar time zones. | Potential language barriers, reliance on email/digital communication, time zone differences may slow down response times. |
Lead Times | Shorter shipping times, faster turnaround for prototypes, better control over production schedule, faster response to changes. | Longer shipping times, potential delays due to customs/international shipping, increased difficulty in managing timelines. |
Costs | Potentially higher per unit cost, but reduced shipping costs and possible lower overall costs for lower volumes and prototypes, lower tariffs and taxes. | Lower per unit cost, but increased shipping costs, tariffs and taxes, potential costs related to communication delays, may be more cost-effective for large volumes. |
Quality Control | Easier to visit the facility for audits, local regulations may ensure better standards, direct access to production team, faster issue identification and resolution. | More challenging to verify quality, may require third-party inspection, greater risk of inconsistencies in production, greater difficulty in resolving issues. |
Intellectual Property Protection | Greater protection due to local laws and regulations, easier legal recourse if needed. | Risk of IP theft is higher, legal recourse may be more complex and costly, cultural and legal norms may differ. |
Supply Chain Flexibility | More flexible to adjust production and make changes, more responsive to changes in product design, easier to adjust delivery schedules. | Less flexible to adapt to changes, may require longer lead time to adjust the production, less control over supply chain issues. |
Comparing SMT PCB Assembly Technologies
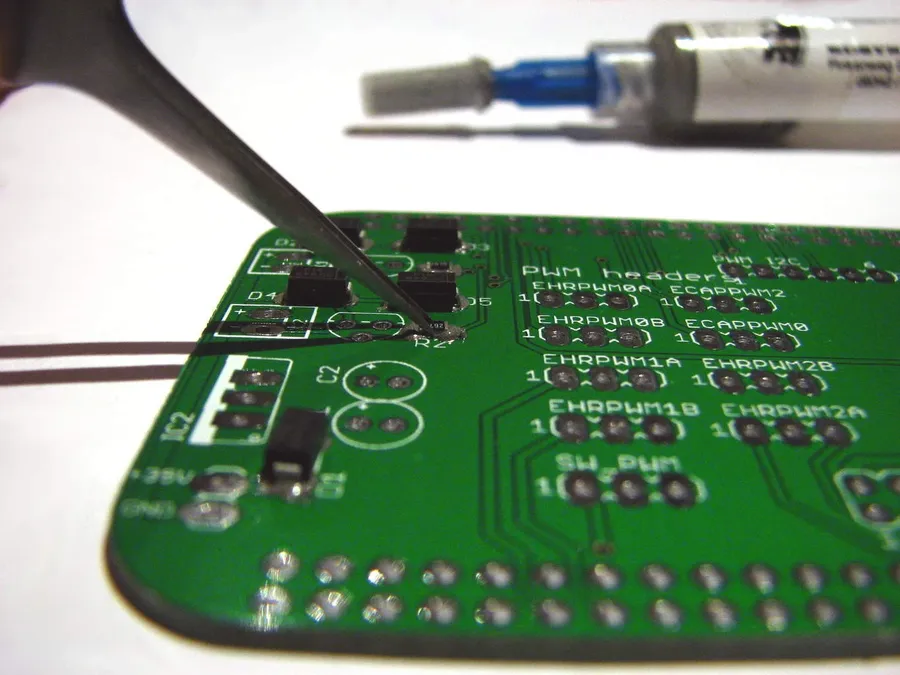
Modern SMT PCB assembly encompasses a range of advanced technologies, each presenting unique capabilities and challenges. Understanding these technologies—such as fine-pitch, Ball Grid Array (BGA), and lead-free assembly—is crucial for selecting the appropriate supplier and ensuring the reliability and performance of the final product.
Technology | Description | Key Requirements | Challenges | Applications |
---|---|---|---|---|
Fine-Pitch Assembly | Involves components with very small lead spacing, often less than 0.5mm. | High-precision placement equipment, solder paste control, and expertise. | Requires precise alignment and solder application to prevent shorts or opens. | High-density electronics, smartphones, and wearable devices. |
BGA Assembly | Uses components with solder balls underneath the package instead of leads. | Advanced reflow profiling, X-ray inspection for solder joint integrity. | Inspection is difficult due to hidden solder joints; requires specialized techniques. | High-performance computing, networking equipment, and automotive electronics. |
Lead-Free Assembly | Uses lead-free solder alloys to comply with environmental regulations. | Careful reflow profile optimization, selection of compatible components, and rework expertise. | Lead-free solders have different melting points and require process adjustments. | Almost all modern electronics, including medical devices and consumer products. |
Selecting the right SMT assembly partner requires careful consideration of their capabilities in these specific technologies. The supplier should demonstrate proficiency in the required areas and have robust process controls for optimal assembly outcomes.
Future Trends in SMT PCB Assembly
The SMT PCB assembly landscape is rapidly evolving, driven by advancements in technology, increasing demands for miniaturization, and the push for higher efficiency. Future trends point towards greater automation, the integration of artificial intelligence, and the adoption of advanced materials and methodologies to meet the challenges of next-generation electronics.
- Automation and Robotics
Increased use of robotic systems for component placement, soldering, and inspection to enhance throughput, reduce human error, and improve overall production speed. This includes advanced pick-and-place machines with higher precision and speed capabilities, as well as automated optical inspection (AOI) systems for faster and more accurate quality control. - Artificial Intelligence (AI) and Machine Learning (ML)
Integration of AI and ML for predictive maintenance, process optimization, and defect detection. These technologies can analyze data from production processes in real-time to identify anomalies, adjust parameters, and predict potential failures, leading to improved yields and reduced downtime. For example, AI algorithms can optimize reflow oven profiles based on real-time temperature data. - Advanced Materials
Exploration of new substrate materials (e.g., flexible substrates, ceramic-based materials) and solder alloys to meet specific performance requirements like increased thermal conductivity or improved mechanical reliability. These materials cater to the needs of high-frequency applications and harsh operating environments. - Miniaturization and High-Density Interconnects
Continued push for smaller component sizes and increased component density on PCBs. This trend requires the use of advanced placement techniques (such as fine-pitch placement) and specialized materials to handle the smaller feature sizes and higher density connections while ensuring reliable electrical performance. - Digital Twins
Creation of digital replicas of physical assembly lines. This allows simulations, testing and optimizations to be done without disrupting the physical production process. This can lead to faster time-to-market, higher reliability and lower cost.
Choosing the right SMT PCB assembly supplier is a pivotal decision for any electronics manufacturer. By understanding the nuances of SMT technology, considering key factors in supplier selection, and staying informed about industry trends, you can secure a partnership that enhances product quality, streamlines production, and reduces costs. Remember to assess the technical capabilities of your potential SMT PCB assembly supplier, their capacity to handle your specific project requirements, and their ability to adapt to future technology demands. Partnering with the right SMT PCB assembly supplier will pave the way for your success in the dynamic world of electronics.
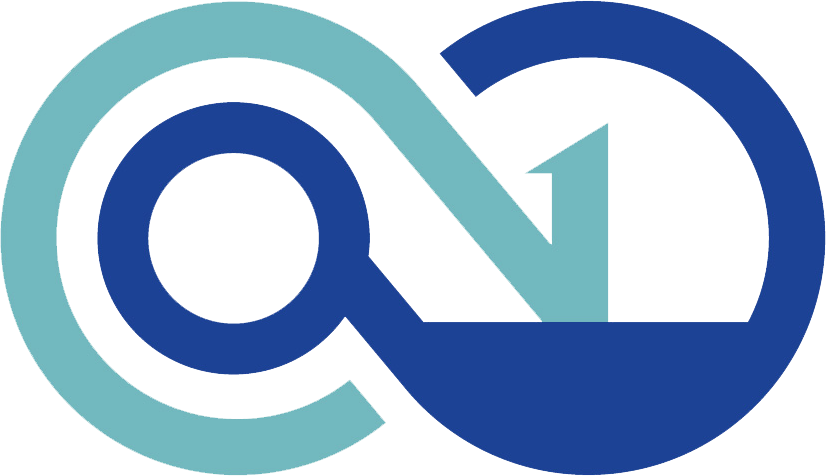