Affordable Flexible PCBs: Your Guide to Cheap Flexible PCB Solutions

In today's fast-paced world of electronics, flexible PCBs (printed circuit boards) are increasingly essential for innovative devices. From wearable tech to advanced medical equipment, these boards bend and flex, offering unprecedented design freedom. However, the cost can often be a barrier. This article explores how to navigate the market and secure cheap flexible PCBs without sacrificing quality, while also diving into the materials and manufacturing processes that impact the final price, ensuring that your project stays within budget. We will look at what makes a cheap flexible pcb, what to look for and how to get one.
Understanding Flexible PCBs and Their Applications

Flexible printed circuit boards (PCBs), often referred to as flex circuits, offer a significant departure from traditional rigid PCBs by utilizing a flexible substrate. This inherent flexibility enables these circuits to bend, fold, and conform to various shapes and spaces, making them indispensable in applications where mechanical flexibility and space optimization are paramount. Unlike rigid boards, flexible PCBs can dynamically adapt to their environment, making them particularly well-suited for high-stress or complex applications.
The key advantages of flexible PCBs include their capacity for dynamic movement, higher density connections, and enhanced reliability in high-stress environments. These properties enable innovative designs, reduced assembly costs, and improved system performance in a wide range of applications. Common applications include:
- Wearable Technology
Due to their compact size and adaptability, flex PCBs are integral in devices such as smartwatches, fitness trackers, and medical wearables, allowing these products to conform to the human body comfortably. - Automotive Industry
Flex PCBs are used in automotive displays, sensor integration, and complex wiring harnesses. Their ability to fit in tight spaces and withstand vibrations makes them ideal for automotive environments. - Consumer Electronics
They are found in smartphones, tablets, and digital cameras, enabling compact designs and connecting components that are not on the same plane. - Medical Devices
Flexible PCBs are critical in advanced medical devices, including pacemakers and implantable sensors, where reliability and biocompatibility are crucial. - Aerospace Applications
Due to their low weight, high flexibility and reliability in harsh environments, flex PCBs are commonly used in aerospace applications including satellites and avionic systems. - Industrial Equipment
In industrial control systems, robotics and machinery, flex PCBs provide solutions for complex connection needs where conventional boards are not viable.
Factors Influencing the Cost of Flexible PCBs
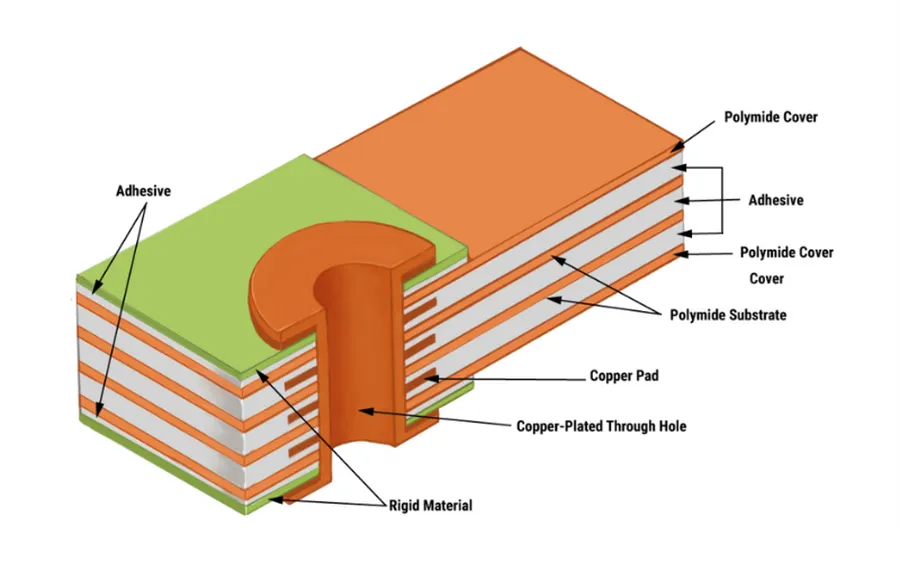
The cost of flexible PCBs is influenced by a variety of factors, spanning material choices, design complexity, and production scale. Understanding these elements is crucial for optimizing costs without sacrificing functionality.
Factor | Description | Impact on Cost |
---|---|---|
Material Choice | Selection of base materials such as Polyimide (PI) or Polyester (PET). | PI generally more expensive but offers better performance; PET is cheaper but has limitations. |
Layer Count | Number of conductive layers in the PCB (single, double, or multilayer). | Increased layers lead to higher complexity and cost due to additional materials and processing. |
Size | Physical dimensions of the PCB. | Larger PCBs require more materials and can have higher production costs. |
Design Complexity | Number of components, circuit trace complexity, and special features (e.g., impedance control). | More complex designs require more precise manufacturing and can increase costs. |
Production Volume | Number of PCBs produced in a single batch. | Larger volumes generally benefit from economies of scale, reducing per-unit cost. |
Manufacturing Process | Techniques used for fabrication, such as laser cutting, etching, lamination. | Advanced or specialized processes can increase costs. Standard processes are often cheaper. |
Finishes | Surface treatments applied to the PCB (e.g., ENIG, HASL). | Certain finishes offer better performance, but increase production costs. |
Material Choices for Cheap Flexible PCBs: Polyimide vs. Polyester
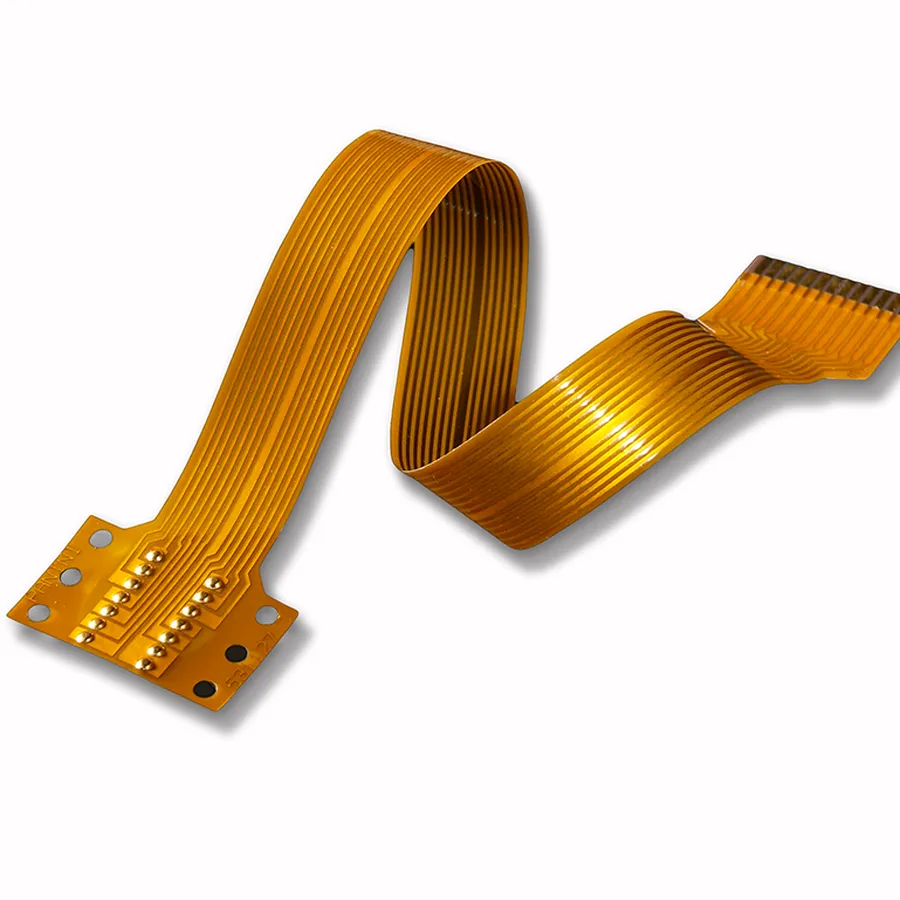
The selection of base material is a critical factor influencing both the cost and performance of flexible PCBs. Polyimide (PI) and Polyester (PET) are two common options, each with distinct advantages and disadvantages. Understanding their properties allows for informed decisions that can significantly reduce costs without compromising essential functionality. Polyimide generally offers superior performance but at a higher cost, while polyester presents a more economical solution for less demanding applications. The right choice depends heavily on the specific operational environment and performance criteria of the flexible PCB.
Characteristic | Polyimide (PI) | Polyester (PET) |
---|---|---|
Cost | Higher | Lower |
Temperature Resistance | High (up to 400°C) | Moderate (up to 150°C) |
Flexibility | Excellent, maintains flexibility over a wide temperature range | Good, can become brittle at higher temperatures |
Chemical Resistance | Very Good | Moderate |
Moisture Resistance | Excellent | Fair |
Durability | Excellent, high tensile strength and tear resistance | Good, lower tensile strength compared to PI |
Typical Applications | High-performance electronics, aerospace, medical devices | Consumer electronics, low-cost applications, disposable devices |
Cost-Optimization Use Case | When long-term reliability and high temperature performance are critical. | For applications where cost and moderate performance are acceptable. |
Finding Reliable & Cheap Flexible PCB Manufacturers
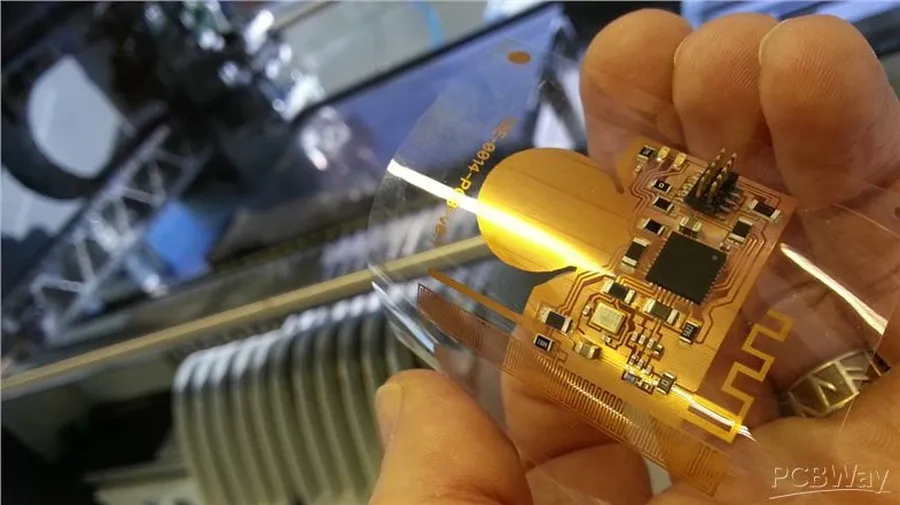
Identifying a reliable manufacturer is crucial for obtaining cost-effective flexible PCBs without compromising quality. This section outlines a strategic approach to researching and vetting potential partners, ensuring that you find a manufacturer capable of producing both prototypes and mass-produced flexible circuits at a budget-friendly price point.
- Researching Potential Manufacturers
Begin by compiling a list of manufacturers that specialize in flexible PCBs. Use online directories, industry publications, and recommendations from peers to identify potential partners. Look for manufacturers with experience in producing flexible circuits and those that are known for quality and reliability. - Vetting Process
After identifying potential manufacturers, vet them using the following methods: Check their certifications (ISO 9001, etc.), review customer testimonials, and assess sample quality. Request quotes from multiple manufacturers to benchmark costs. It's also wise to visit factories if possible to assess production capabilities firsthand. - Geographic Considerations
The location of the manufacturer can significantly impact costs and lead times. While overseas manufacturers may offer lower prices, factors like communication barriers, shipping costs, and longer lead times must be considered. Local manufacturers can be more expensive, but may provide faster turnaround and easier communication, particularly useful for prototyping and smaller projects. - Communication and Support
Effective communication is critical. Select manufacturers who offer clear communication channels, responsive customer service, and technical support. This ensures that your queries are addressed promptly, and any issues during production are resolved quickly. - Production Capabilities
Ensure the manufacturer has the equipment and expertise to handle your design requirements, including layer counts, material specifications, and tolerances. Assess their capabilities to produce prototypes and scale up production to meet future demands. - Pitfalls to Avoid
Be wary of manufacturers that offer prices that seem too good to be true. This can be indicative of subpar materials or production processes. Always ask for samples and production quality reports. Also, be aware of potential language and cultural barriers. Misunderstandings can lead to delays and errors.
Design Strategies for Cost-Effective Flexible PCBs
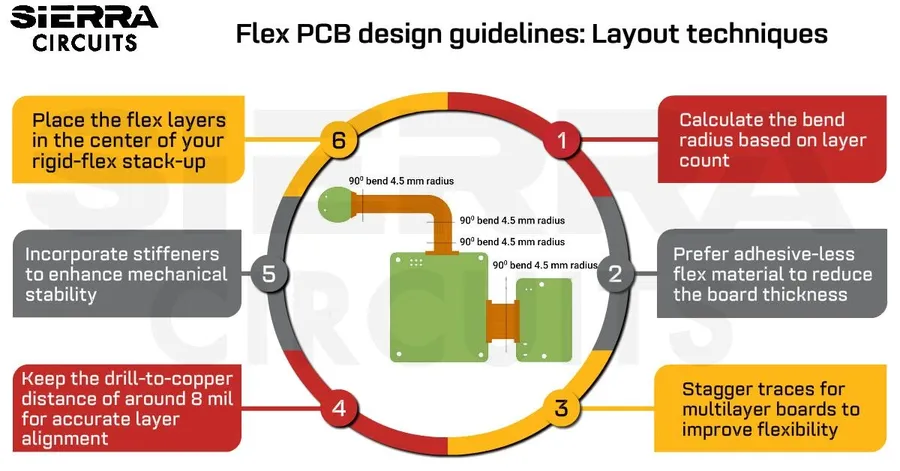
Optimizing the design of flexible PCBs is crucial for reducing manufacturing costs without compromising functionality. By carefully considering layout, material usage, and manufacturing constraints, significant cost savings can be achieved. These strategies focus on minimizing waste and streamlining the production process.
- Panelization for Efficient Material Use
Arranging multiple PCB designs on a single manufacturing panel allows for efficient material utilization. This minimizes waste by maximizing the useable area of the flexible substrate. - Standardized Component Selection
Using readily available, standard components reduces procurement costs. Opting for common sizes and values will lower prices and lead times compared to custom or specialized parts. - Simple Layouts and Routing
Minimize complex shapes, sharp angles and excessive routing. Simplify the design where possible, opting for straight traces and fewer vias. This can reduce manufacturing time and costs. - Minimize Layer Count
Stick to the minimum number of layers required for your application. Each additional layer significantly increases cost. Where possible, consolidate functionality to fewer layers to reduce material consumption and processing steps. - Adherence to Manufacturer's Design Rules
Strictly follow the design rules and guidelines provided by your chosen manufacturer. These guidelines are tailored to their specific equipment and capabilities and help avoid errors, rework, and potential cost overruns. - Consider the end-use environment.
Ensure the design meets the required bending radius, tensile strength, and other mechanical requirements of its operating environment. Failure to do so can cause failure of the PCB in the field, which could ultimately increase costs.
Flexible PCB Assembly Cost Reduction Techniques
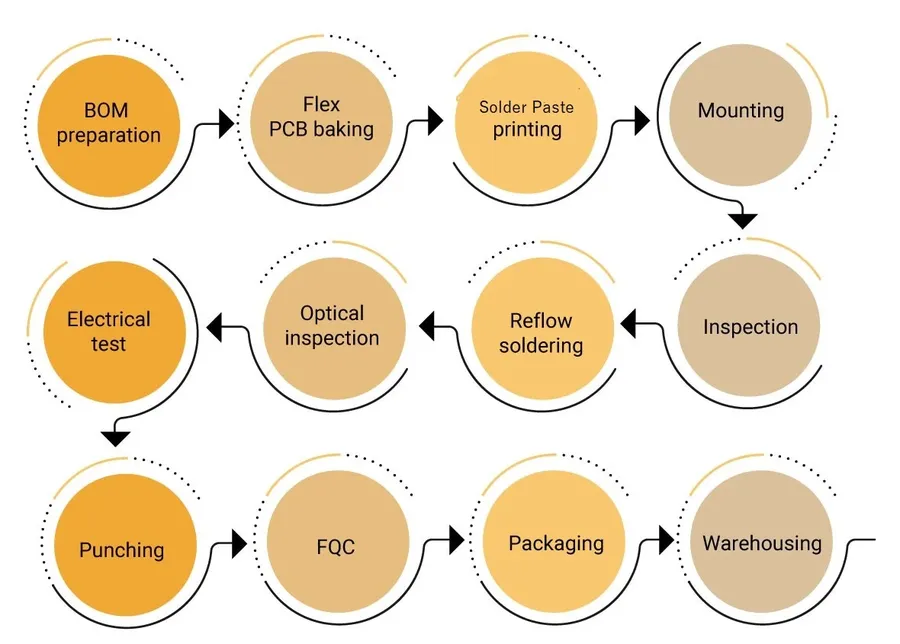
Reducing costs during the assembly of flexible PCBs is crucial for budget-conscious projects. Strategic decisions in design, component selection, and assembly methods can significantly lower overall expenses without compromising functionality. This section outlines key techniques for achieving cost-effective flex PCB assembly.
- Design for Assembly (DFA)
Implementing DFA principles during the PCB design phase is fundamental to cost reduction. This includes optimizing component placement, using standard footprint sizes, and minimizing the number of unique components. Simpler layouts with fewer assembly steps translate directly to lower costs. - Component Selection and Standardization
Choosing readily available, standardized components reduces procurement costs and shortens lead times. Favoring common component packages and sizes will reduce the amount of time and cost involved in assembly. - Panelization Strategy
Panelizing multiple PCBs together allows for more efficient and faster assembly through automated pick-and-place machines. Optimized panel layouts can also reduce material waste, further reducing costs. - Automation and Manual Assembly
Selecting the appropriate method of assembly (automated or manual) is important. While automation is highly efficient for large-scale production, manual assembly may be more cost-effective for smaller runs or more complex layouts. The decision should be based on the production quantity and complexity of the design. - Minimize Rework and Rejection
Reducing the amount of rework necessary or number of rejected boards is key to reducing costs and improving efficiency. Careful planning and following standard procedures are key to reducing assembly errors. - Test Strategy Optimization
Optimizing the test procedures, can reduce overall costs. Developing test strategies that catch potential defects early in the assembly process can help reduce rework costs and ensure higher reliability.
Frequently Asked Questions About Cheap Flexible PCBs
This section addresses common inquiries regarding the affordability and manufacturing of flexible PCBs, providing clear and concise answers to help guide your decision-making process.
- How much does a flexible PCB typically cost?
The cost of a flexible PCB varies widely based on several factors, including the material used (polyimide, polyester), the number of layers, the complexity of the design, and the production volume. Simple single-layer designs in polyester can be very affordable, whereas complex multi-layer designs in polyimide will be significantly more expensive. Prices can range from a few cents for very basic layouts to upwards of hundreds of dollars for highly intricate boards. It's best to obtain quotes from several manufacturers for your specific design to get an accurate estimate. - What is the most cost-effective PCB finish for flexible PCBs?
The cheapest PCB finish typically is HASL (Hot Air Solder Leveling), but it's not ideal for all flexible PCB applications due to its uneven surface. ENIG (Electroless Nickel Immersion Gold) offers better performance and is more suitable for flexible boards requiring fine pitch components and higher durability, but is more costly. Consider cost vs application needs when choosing your finish. OSP (Organic Solderability Preservative) is another cost-effective option, offering good solderability while being more affordable than ENIG. - Is it possible to manufacture flexible PCBs at a low cost?
Yes, it is absolutely possible to manufacture flexible PCBs at a low cost. The key is to optimize the design, select cost-effective materials, and utilize efficient manufacturing processes. For example, opting for a single-layer design, using polyester as the base material instead of polyimide, and choosing a standard production method can dramatically reduce the cost. Furthermore, working with a manufacturer that specializes in economical production will also help in controlling costs without sacrificing necessary functionality. - How can I make my flexible PCB design more affordable?
Several design strategies can significantly reduce the cost of a flexible PCB. Simplifying the circuit layout, minimizing the number of layers, using standard component sizes, and avoiding complex shapes all help. Also, adhering to the manufacturer's design rules for minimum trace widths and spacing, using larger vias, and avoiding unnecessary features will reduce production costs. Choose the appropriate material and finish for the application to balance cost and required performance. - Can using Polyester (PET) instead of Polyimide (PI) significantly reduce the cost of flexible PCBs?
Yes, choosing Polyester (PET) as the base material instead of Polyimide (PI) can greatly reduce the cost of your flexible PCB. Polyester is typically much less expensive than Polyimide. However, it’s essential to consider the application requirements. PET has lower temperature resistance and is not as durable or flexible as PI. Thus, it may be a suitable option for less demanding or static applications, whereas PI is more appropriate for applications that require high heat resistance, superior durability, or repeated flexing. - What role does production volume play in the cost of flexible PCBs?
Production volume is a major factor in determining the cost of flexible PCBs. Higher volumes often lead to lower per-unit costs. This is because manufacturers can amortize tooling, setup costs, and material waste over a larger number of units. Furthermore, bulk material purchasing typically results in discounts. However, small quantities like prototypes will usually come at a higher per unit cost due to the tooling cost.
Case Studies: Real-World Examples of Cost-Effective Flex PCB Projects
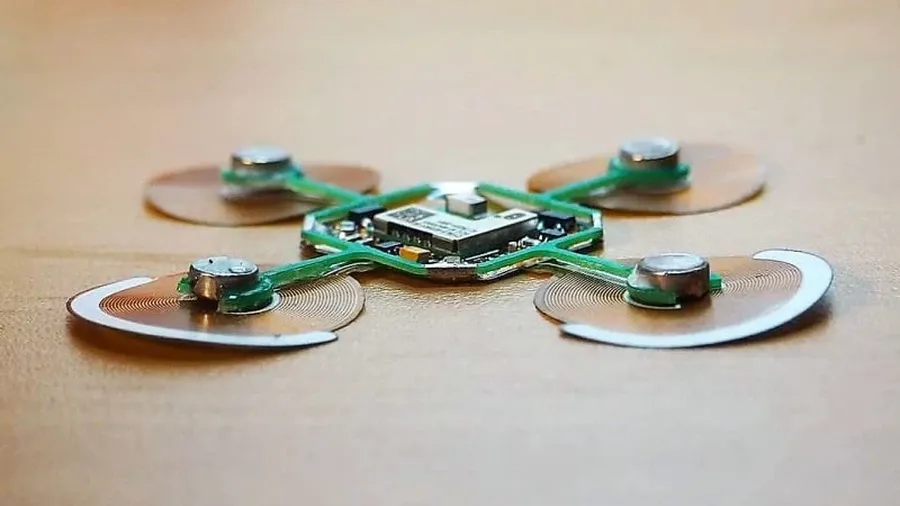
Examining real-world applications of flexible PCBs reveals the practical cost-saving advantages and design flexibility they offer. These case studies span various industries, demonstrating how strategic material choices, efficient design, and optimized manufacturing processes contribute to significant cost reductions without sacrificing functionality or reliability.
Below are a few examples of how flexible PCBs have been implemented to achieve cost effectiveness.
- Consumer Electronics: Wearable Fitness Tracker
A wearable fitness tracker uses a single-layer polyester-based flex PCB to connect the display, sensors, and battery. The design is optimized to fit the curved shape of the device, significantly reducing the need for multiple rigid PCBs and connectors, resulting in a 20% cost reduction. The use of PET instead of PI also contributed to lower material costs, while still meeting the application's performance requirements. A key learning here is that simplicity in design coupled with material optimization can lead to substantial savings in mass-produced consumer electronics. - Automotive: Dashboard Display Interconnect
In an automotive dashboard, a multi-layer flex PCB made with polyimide is used for interconnecting the main display with various control modules. This design replaced a complex network of wires and rigid PCBs. The flex circuit not only reduced the assembly time by 30% but also improved the reliability of the connection by eliminating multiple potential failure points. Although the initial material cost is higher, the reduction in labor and increase in system reliability and service life lead to a decrease in the total cost of ownership by 15%. Furthermore, the flexible nature of the PCB makes it easy to assemble in the curved contours of the dashboard. - Medical Devices: Portable Diagnostic Equipment
A portable diagnostic device uses a double-sided flex PCB for its sensor arrays and display. By designing the circuit with smaller features and higher component density, the board size was minimized, therefore reducing the amount of material used and the total manufacturing cost by approximately 18%. The choice of a high-density via structure allowed for more complex routing in a smaller area, which further helped to shrink the PCB footprint and reduce material waste. Lessons from this project show that intelligent design can have a significant impact on material utilization. - Industrial Control: Flexible Sensor Integration
In industrial environments, a sensor network deployed in machinery used a single-layer polyimide flex PCB that is conformable to different surfaces. This eliminated the need for multiple connectors and rigid PCBs, reducing material cost and improving the reliability of the sensor system by 25% . The ruggedness of the polyimide material ensured that the sensors could withstand harsh conditions, leading to an increase in the overall life cycle of the equipment. From this it can be seen that, in demanding environments, the material choice can be important to ensure reliable performance and cost effectiveness.
Future Trends in Cheap Flexible PCB Technology
The landscape of flexible printed circuit board (PCB) technology is continuously evolving, with future trends poised to significantly impact both cost and capabilities. These advancements are driven by the need for more compact, efficient, and adaptable electronic devices across various industries, from consumer electronics to medical devices and aerospace.
Several key technological areas are expected to shape the future of flexible PCBs:
- Advanced Materials
Research into novel substrate materials beyond traditional polyimide and polyester is underway. This includes the exploration of bio-based polymers, thin glass, and nanomaterials. These materials promise improved performance characteristics such as higher thermal stability, better mechanical flexibility, and enhanced electrical conductivity, potentially at reduced costs through economies of scale and simplified processing. - Additive Manufacturing Techniques
The application of additive manufacturing (3D printing) to flexible PCB fabrication is a rapidly developing field. This approach enables the creation of complex, custom designs with greater precision and reduced material waste, potentially lowering overall manufacturing costs. Furthermore, it could enable rapid prototyping and on-demand production. - Enhanced Integration and Miniaturization
Future flexible PCBs will see an increased level of component integration, including embedded passives and microchips directly within the substrate. This enhances miniaturization, improves system performance, reduces the need for discrete components, and could lead to cost savings by reducing the number of parts and assembly steps. - Roll-to-Roll Processing
Continuous manufacturing processes, like roll-to-roll (R2R) processing, are being refined for flexible PCB production. R2R offers significant advantages in mass production, reducing per-unit costs while increasing throughput compared to batch processes. This involves high-speed printing and deposition techniques on flexible substrates. - Smart and Multifunctional Flex PCBs
Integrating sensors, actuators, and energy harvesting capabilities directly into flexible PCBs is a key area of development. These "smart" flex circuits will enable new applications in wearables, IoT devices, and healthcare, by creating products that perform more than basic signal transfer.
Securing a cheap flexible pcb doesn't need to mean settling for less. By carefully considering materials, design, and manufacturing options, you can source affordable solutions to meet your needs and stay within budget. As technology advances, the availability of cheap flexible PCBs is set to increase, making them a viable option for even more applications. Knowing your requirements, researching options, and considering design strategies will be important as you move to develop with cheap flexible PCBs, allowing you to capitalize on the benefits of flexible circuits in your future projects.
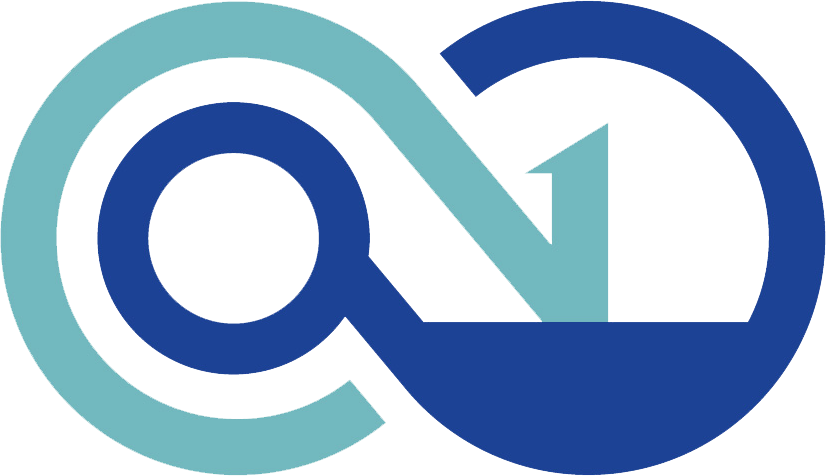