Aluminum PCB: The Ultimate Guide for Superior Thermal Performance
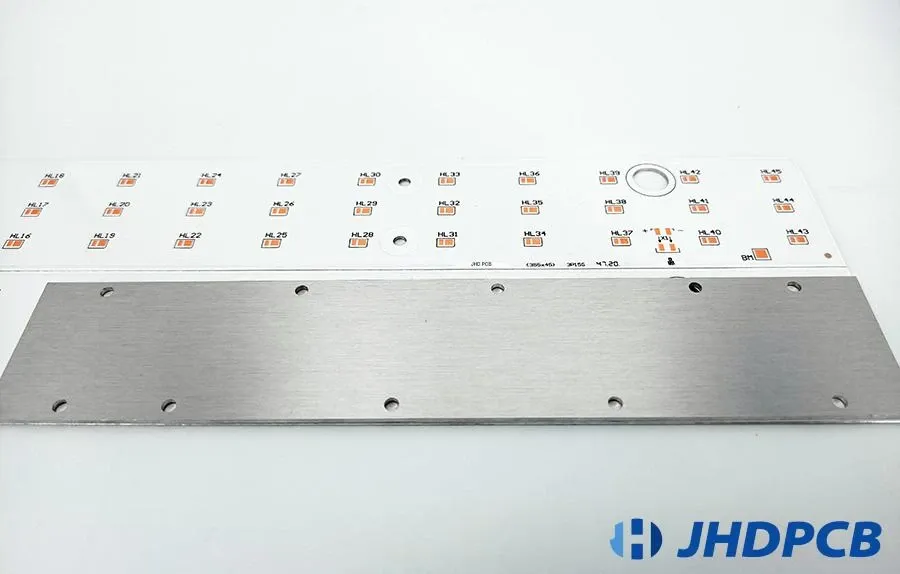
In the realm of modern electronics, where miniaturization and power density are constantly increasing, thermal management has become a critical challenge. Traditional FR4 PCBs often struggle to dissipate heat effectively, leading to performance degradation and reliability issues. This is where Aluminum PCBs step in, offering superior thermal performance and reliability. This article will delve deep into the world of aluminum PCBs, exploring their construction, advantages, applications, and how they're shaping the future of electronics.
What is an Aluminum PCB?
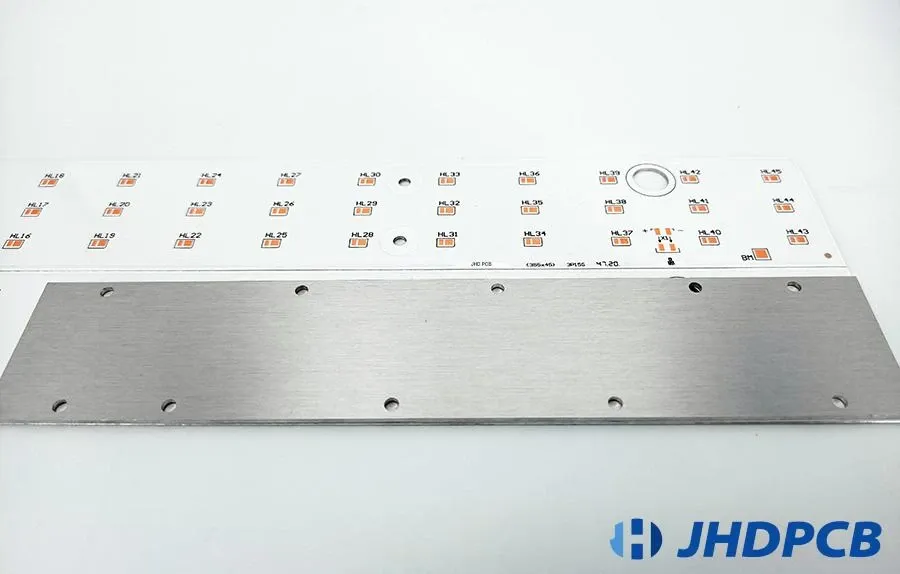
An Aluminum Printed Circuit Board (PCB) distinguishes itself from traditional FR4 PCBs through its core material: a layer of aluminum. This aluminum base is then overlaid with a dielectric layer and a copper conductive layer, a configuration specifically designed to facilitate superior heat dissipation, making aluminum PCBs exceptionally well-suited for high-power applications where thermal management is critical.
Construction and Materials of Aluminum PCBs
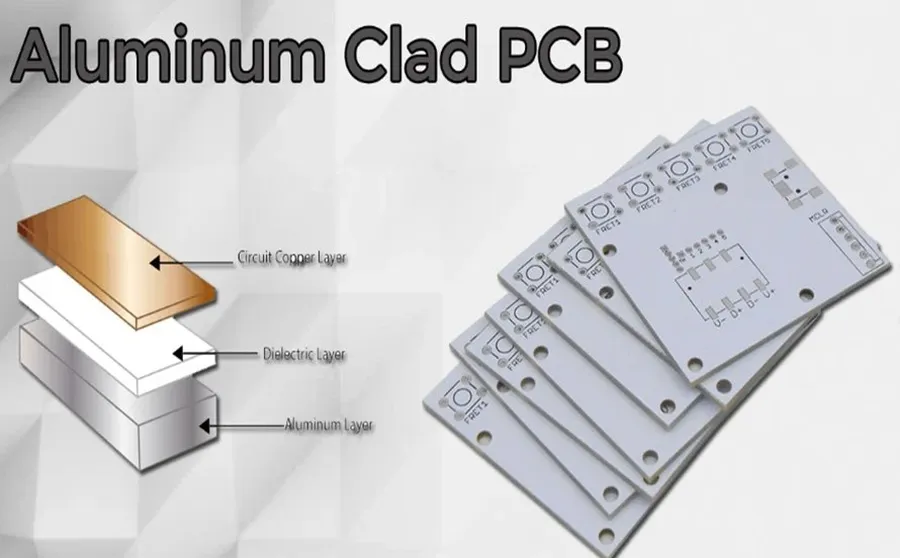
Aluminum PCBs are distinguished by their layered construction, primarily composed of an aluminum base, a thermally conductive dielectric layer, and a copper foil layer. The specific materials and thicknesses of these layers are crucial for determining the performance and application of the PCB.
Layer | Material | Function | Typical Thickness |
---|---|---|---|
Aluminum Base (Core) | Aluminum alloy (e.g., 5052, 6061) | Provides structural support and primary heat dissipation path | 0.5 mm - 3 mm |
Dielectric Layer | Thermally conductive epoxy or ceramic filled polymer | Electrical insulation between copper and aluminum, facilitates heat transfer | 50 μm - 200 μm |
Copper Foil Layer | Copper | Conductive layer for electrical signal transmission | 18 μm - 105 μm |
The aluminum base typically employs alloys like 5052 or 6061, chosen for their thermal conductivity and mechanical strength. The dielectric layer is critical in providing electrical isolation while allowing efficient heat transfer. Materials like epoxy resins filled with thermally conductive ceramics are common. The copper layer, essential for electrical connections, is typically formed using electrolytic deposition.
Key parameters that influence the performance of aluminum PCBs include the dielectric material's thermal conductivity, the thickness of the aluminum core, and the copper layer thickness. These parameters are carefully tuned to achieve the specific thermal and electrical requirements of the target application.
Advantages of Using Aluminum PCBs
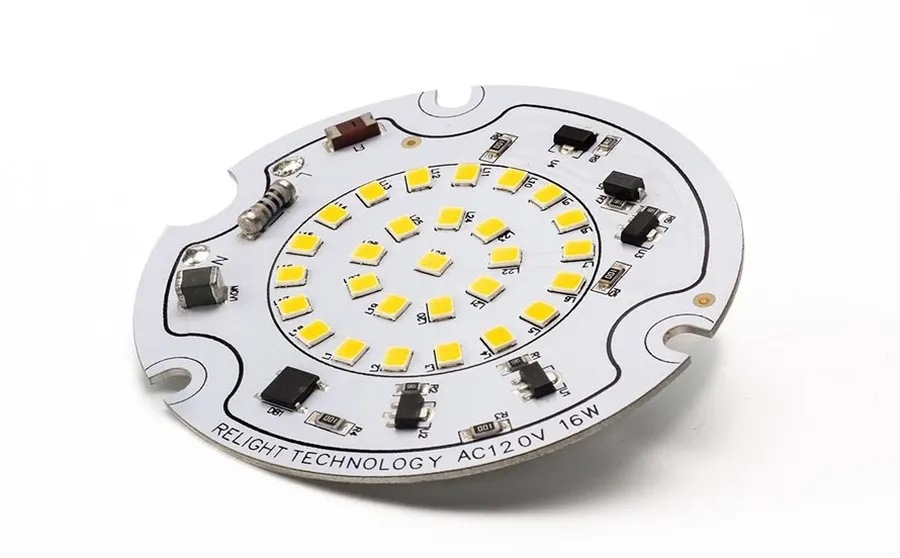
Aluminum PCBs provide several key advantages over traditional FR4 PCBs, primarily due to the superior thermal properties of aluminum. These benefits directly address common challenges in electronic design, particularly in high-power and thermally demanding applications, leading to enhanced performance, reliability, and longevity of electronic devices.
- Superior Heat Dissipation
The primary advantage of aluminum PCBs is their excellent thermal conductivity, typically ranging from 1 to 2 W/mK but can reach 200+ W/mK, depending on the alloy. This allows heat to be transferred away from heat-generating components far more efficiently than with FR4 PCBs, which are thermal insulators. Effective heat dissipation prevents components from overheating, thereby enhancing performance and extending the lifespan of the PCB and the devices it powers. This is particularly critical for high-power applications like LEDs, power supplies and automotive electronics. - Enhanced Durability
Aluminum PCBs have a rigid metal core that offers improved mechanical stability and durability compared to FR4 boards. This makes them more resistant to physical stress, warping, and damage from mechanical impact or vibration. This durability is particularly beneficial in harsh environments or applications where the PCB might be subjected to physical stress. - Longer Lifespan
Due to the superior thermal management and enhanced mechanical stability, aluminum PCBs tend to have a longer operational lifespan. By preventing overheating and reducing stress on components, the likelihood of failures due to thermal fatigue or physical damage is reduced. This results in improved reliability, reduced maintenance and replacement costs. - Environmental Friendliness
Aluminum is a recyclable material, making aluminum PCBs more environmentally friendly than some other types of PCBs. The recyclability of the material and its potential for re-use in the manufacturing process further contributes to sustainable manufacturing practices. Additionally, effective heat dissipation can lead to energy efficiency by reducing the need for additional cooling components. - Improved Component Performance
By maintaining lower operating temperatures, aluminum PCBs help ensure components such as processors, power devices, and LEDs operate within their designed specifications. This enhances the accuracy and efficiency of electronic devices. The stable thermal environment allows components to operate more reliably and deliver their intended performance output consistently.
Applications of Aluminum PCBs
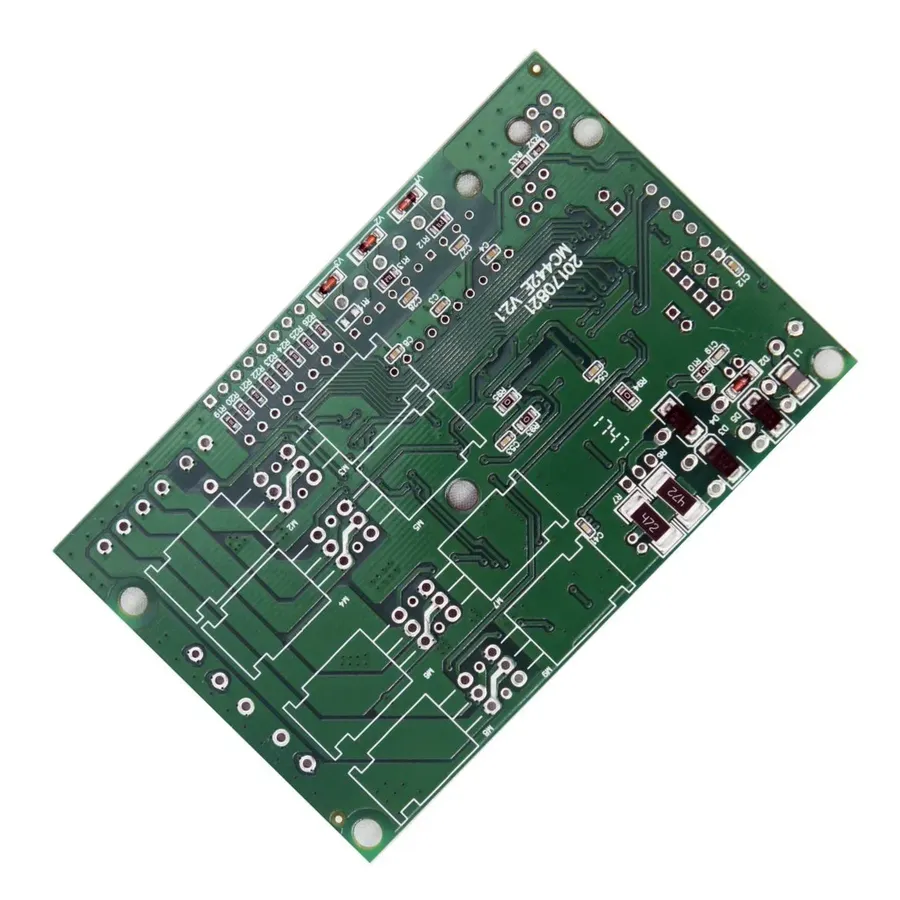
Aluminum PCBs are integral in applications demanding robust thermal management due to their superior heat dissipation capabilities. Their ability to efficiently transfer heat away from critical components makes them ideal for use in demanding environments across various industries. They ensure the reliability and longevity of electronic devices operating under high-power and high-temperature conditions.
- LED Lighting
Aluminum PCBs are extensively used in LED lighting applications, including high-power LED modules, streetlights, and architectural lighting. The substrate acts as a heatsink, preventing LEDs from overheating and ensuring consistent performance and longer life. Effective thermal management is critical for LED efficiency and longevity. - Power Electronics
In power electronics, aluminum PCBs are essential for handling high currents and voltages in devices like power supplies, inverters, and converters. The aluminum base provides efficient heat dissipation from power semiconductors, improving efficiency and device reliability. These applications benefit significantly from the high thermal conductivity of aluminum. - Automotive Electronics
The automotive sector utilizes aluminum PCBs in various applications, such as engine control units (ECUs), LED headlights, and power control systems. Their durability and thermal management capabilities are crucial for reliable performance in harsh automotive environments, withstanding high temperatures and vibrations common in vehicles. - High-Power Audio Amplifiers
High-power audio amplifiers use aluminum PCBs to dissipate heat generated by power transistors and other active components. The effective heat management provided by the aluminum substrate ensures audio signal fidelity and prevents thermal failures. This is particularly important for high-fidelity audio systems that operate at significant power levels. - Other Applications
Aluminum PCBs are also utilized in other niche applications such as, solar panel systems, industrial control systems, and medical devices. They can be considered in any environment where effective heat dissipation is crucial for reliable operation, including aerospace electronics and telecommunication equipment.
Aluminum PCB vs. FR4 PCB: Key Differences
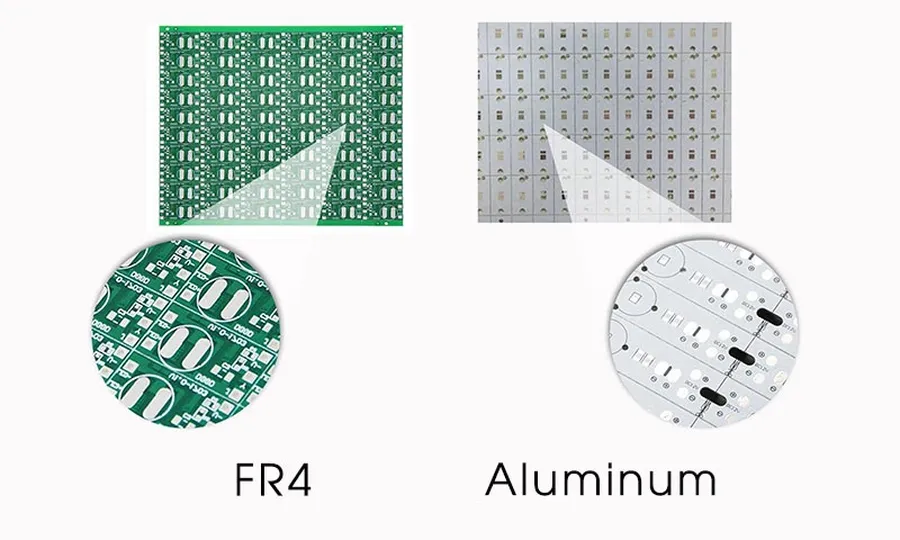
Aluminum PCBs distinguish themselves from FR4 PCBs primarily through their superior thermal conductivity. While FR4, a common insulator, is used in standard PCBs, aluminum acts as a heat-dissipating substrate, critical for preventing overheating in high-power applications, and ensuring optimal device performance. The following comparison outlines the core distinctions between these two PCB types.
Feature | Aluminum PCB | FR4 PCB |
---|---|---|
Thermal Conductivity | High | Low |
Heat Dissipation | Excellent | Poor |
Mechanical Strength | Good | Moderate |
Cost | Higher | Lower |
Applications | High-power, LED lighting | General purpose, low-power |
Design Considerations for Aluminum PCBs
Designing with aluminum PCBs requires a comprehensive approach that balances electrical and thermal performance. Key considerations include trace geometry, layer stack-up, material selection and component placement, all of which significantly influence the PCB's overall functionality and reliability. Understanding the thermal behavior of each layer and material is paramount to leveraging the heat dissipation capabilities of the aluminum core.
Design Aspect | Considerations | Impact |
---|---|---|
Trace Width and Spacing | Wider traces for high-current paths; adequate spacing to prevent shorts. | Controls current carrying capacity and reduces the risk of shorts and electrical failures. |
Layer Stack-Up | Optimize for thermal path; position heat-generating components close to the aluminum core. | Maximizes heat transfer to the aluminum base and ensures efficient cooling of heat sources. |
Dielectric Material | Choose materials with high thermal conductivity and good electrical insulation properties. | Ensures both effective thermal transfer and reliable electrical isolation between layers. |
Impedance Control | Match trace impedance to signal requirements, accounting for the dielectric properties and trace geometry. | Ensures signal integrity and minimizes signal reflections and losses. |
Solder Mask Selection | Use solder masks with appropriate thermal resistance and adhesion properties. | Protects the PCB from environmental factors and provides a solderable surface for components. |
Component Placement | Place heat-generating components strategically to facilitate efficient heat dissipation. | Optimizes the thermal management and prevents localized overheating issues. |
Manufacturing Process of Aluminum PCBs
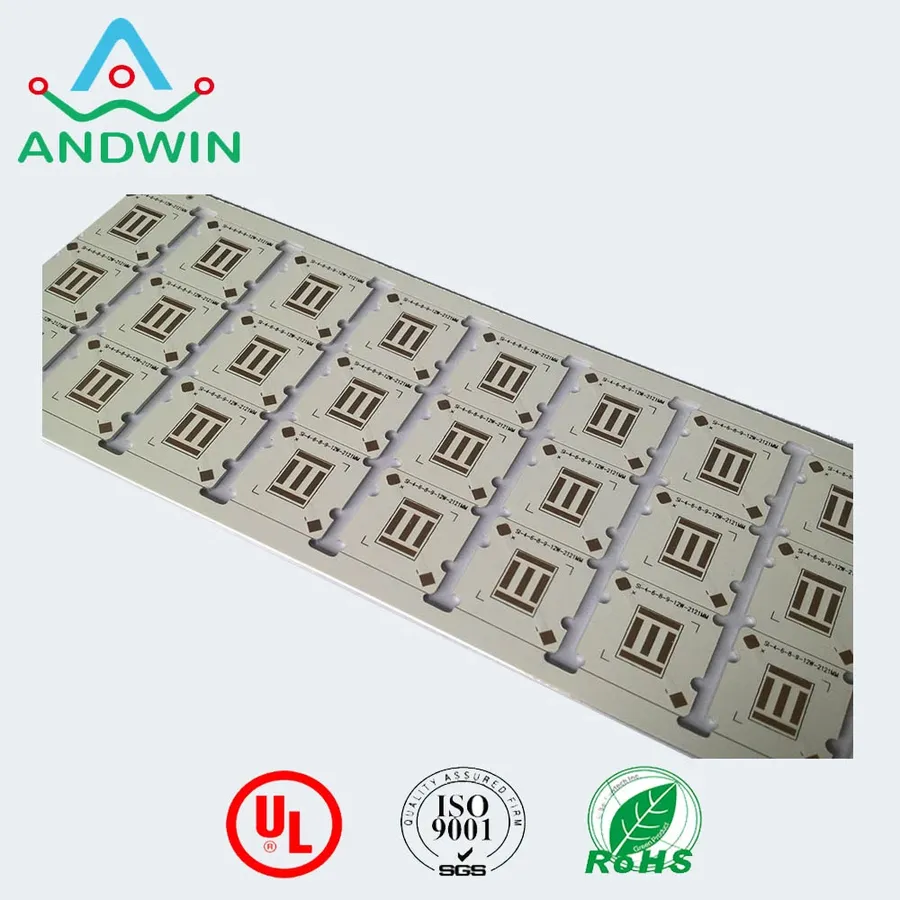
The fabrication of aluminum PCBs shares similarities with standard PCB manufacturing but incorporates specific procedures tailored to the aluminum substrate. These specialized processes ensure the integrity of the board while leveraging aluminum's thermal properties. The critical steps include preparing the aluminum base, applying the dielectric layer, and etching the conductive copper layer, culminating in surface finishing. These steps require precise control to ensure reliable insulation and efficient heat dissipation.
Below is a detailed look at the typical stages involved in aluminum PCB fabrication:
- Aluminum Base Preparation:
The process begins with the preparation of the aluminum base, which serves as the core of the PCB. This involves cleaning and surface treatment to ensure proper adhesion of the subsequent layers. The aluminum base thickness can vary to accommodate different application requirements, typically ranging from 0.5 mm to 3.0 mm. - Dielectric Layer Application:
A thermally conductive but electrically insulating dielectric material is applied onto the aluminum base. This layer facilitates efficient heat transfer from the copper layer to the aluminum core while maintaining electrical isolation. The thickness of this dielectric layer ranges from 50μm to 200μm and is selected based on the voltage requirements, a higher voltage requirement would require thicker dielectric. - Copper Layer Lamination:
A thin layer of copper foil is laminated onto the dielectric layer. This copper foil is the foundation for the conductive traces. Typical copper foil thicknesses range from 18um to 35um. This layer will form the conductive pattern of the PCB. - Circuit Patterning (Etching):
Using photolithography and etching, the desired circuit pattern is transferred onto the copper layer. This involves applying a photoresist material, exposing it to UV light through a photomask, and then chemically etching away the unwanted copper, leaving the circuit traces. - Solder Mask Application:
A solder mask is applied to the board to protect the traces from oxidation and to ensure precise soldering during component assembly. This protective layer prevents solder bridging and provides a surface for component placement. - Surface Finishing:
Finally, a surface finish is applied to enhance solderability and prevent corrosion. Common finishes include HASL, ENIG, and Immersion Tin. The selection of surface finish depends on the requirements of the application such as reliability and cost. - Quality Control and Testing:
The completed aluminum PCBs undergo rigorous quality control and testing to ensure they meet the required electrical and thermal performance specifications.
Frequently Asked Questions About Aluminum PCBs
This section addresses common inquiries about aluminum PCBs, providing concise answers to help you understand their characteristics, benefits, and limitations.
- What are the primary disadvantages of using aluminum PCBs?
While aluminum PCBs excel in thermal management, they typically come with a higher cost compared to FR4 PCBs. Their manufacturing process can be more complex, potentially requiring specialized equipment and expertise. Additionally, their rigid metal core makes them less flexible than FR4 boards. - What advantages do aluminum PCBs offer over traditional FR4 PCBs?
Aluminum PCBs provide superior heat dissipation, leading to enhanced reliability and performance, especially in high-power applications. They also exhibit increased durability, longer lifespans, and a more environmentally friendly profile compared to FR4 alternatives. - What is the typical operating temperature range for aluminum PCBs?
Aluminum PCBs can generally withstand high temperatures, withstanding up to 200°C. However, the precise temperature tolerance is contingent on the specific materials used in construction and the demands of the application. It's essential to consult the specific datasheet for the selected board material. - What is the typical thermal conductivity range of aluminum PCBs?
The thermal conductivity of aluminum PCBs varies based on the alloy, and dielectric materials, generally ranging from 1 to 2 W/mK. However, specific aluminum metal cores can exhibit much higher thermal conductivities in the range of 200+ W/mK, greatly enhancing the heat dissipation capabilities of the board. For more precise figures, refer to the product specifications. - Are aluminum PCBs suitable for flexible applications?
Due to the inherent rigidity of the aluminum core, aluminum PCBs are not designed for flexible applications. If flexibility is required, other PCB materials and designs should be considered. - How does the dielectric layer contribute to the performance of an aluminum PCB?
The dielectric layer in aluminum PCBs serves a dual purpose: it provides electrical isolation between the conductive copper layer and the aluminum base, and it also facilitates efficient heat transfer from the copper layer to the heat-dissipating aluminum core. The dielectric material's thermal properties significantly affect the overall thermal performance of the PCB. - Can aluminum PCBs be used for high-frequency applications?
While aluminum PCBs are predominantly chosen for their thermal properties, they can still be used in high-frequency applications, when properly designed for such purposes. However, considerations such as impedance matching, dielectric properties, and signal integrity should be carefully evaluated in the design phase.
In conclusion, aluminum PCBs offer a robust solution for modern electronics by addressing the critical need for effective thermal management. With superior heat dissipation, increased durability, and versatile applications, aluminum PCBs are poised to become essential components in an increasing number of devices. Understanding their construction, advantages, and design considerations will enable engineers and designers to fully leverage their potential and create more reliable, high-performing products. As technology advances, the role of aluminum PCBs in ensuring efficient operation, long-term reliability and superior performance will only increase.
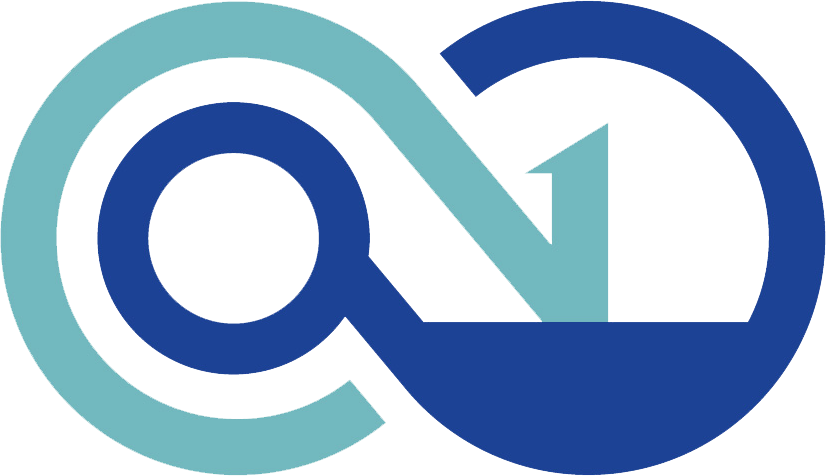