Choosing the Right Microwave PCB Manufacturer: A Comprehensive Guide
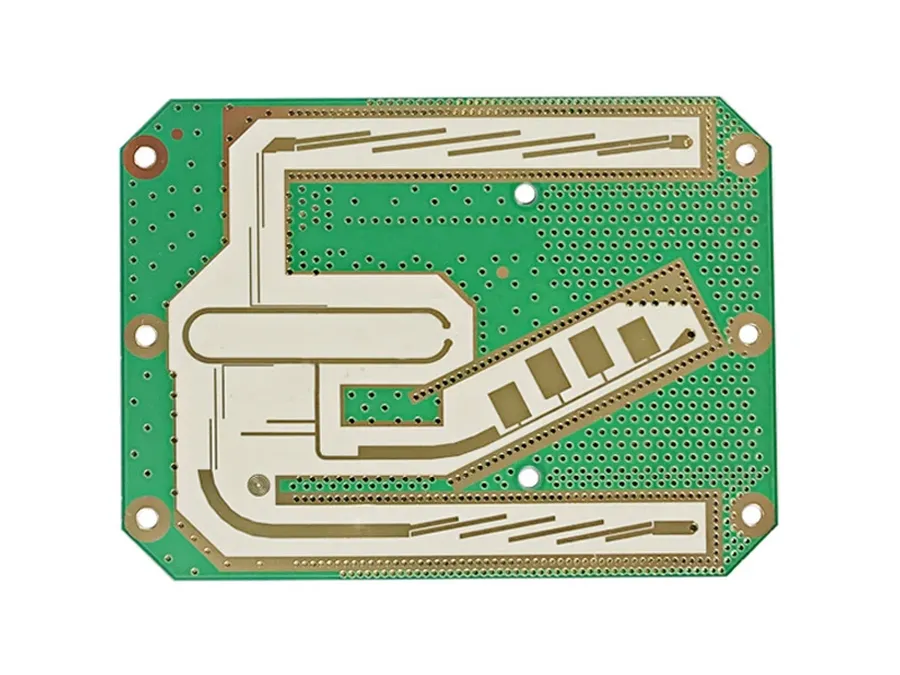
Microwave PCBs are the unsung heroes behind countless modern technologies, from advanced radar systems to sophisticated medical devices and communication networks. Selecting the right microwave pcb manufacturer is paramount to the success and reliability of these high-frequency applications. This guide will delve into the critical factors you should consider when choosing a manufacturer, ensuring that your project is not only well-supported but also achieves optimal performance. The complex materials and precision requirements demand an expert partner. We'll illuminate the best practices, common pitfalls, and essential questions to ask, enabling you to make an informed decision and secure a reliable supply chain.
Understanding Microwave PCBs: Key Characteristics
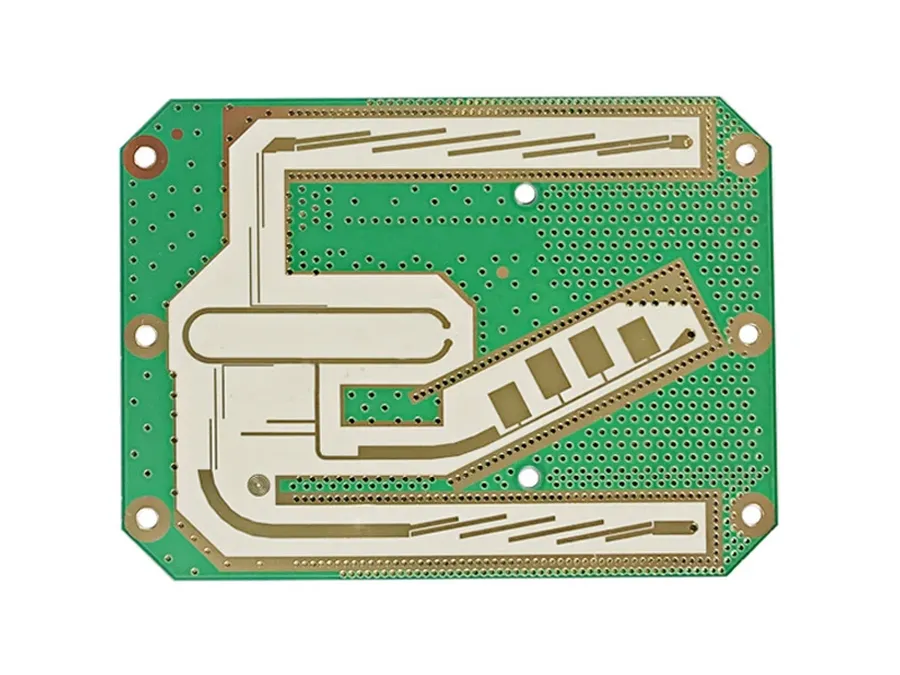
Microwave PCBs are distinct from standard PCBs due to their operation at high frequencies, typically ranging from 300 MHz to 300 GHz. This necessitates the use of specialized materials and manufacturing processes to minimize signal loss, maintain signal integrity, and ensure reliable performance. These boards are not just about connectivity; they are precision engineered components critical for high-frequency applications.
Key characteristics of microwave PCBs include:
- Low Dielectric Loss
The dielectric material used in microwave PCBs must exhibit minimal loss at high frequencies. This is crucial to prevent signal attenuation and maintain signal strength. Materials like PTFE (Teflon) and specialized ceramics are common choices due to their low loss tangent. - Precise Impedance Control
Maintaining a consistent impedance across the board is essential to prevent signal reflections and ensure optimal signal transfer. This requires tight control over trace widths, dielectric thickness, and material properties. - Tight Dimensional Tolerances
Microwave circuits often require extremely precise dimensional control during fabrication to ensure the intended electrical performance. This is particularly important for components such as antennas and filters. - High Thermal Stability
The materials must also be able to withstand the thermal loads associated with high-frequency operation. This is important for preventing material degradation and maintaining the performance of the board in different thermal environments. - Consistent Material Properties
Variations in dielectric constant and loss tangent can significantly impact the signal behavior. Microwave PCB manufacturers must guarantee the consistency of material properties across the entire board. - Surface Finish
The surface finish of the PCB needs to be extremely smooth to ensure good solderability for high frequency components and to minimize any signal issues due to an irregular surface. Gold plating is a typical surface finish.
Characteristic | Description | Importance |
---|---|---|
Low Dielectric Loss | Minimizes signal attenuation at high frequencies. | Crucial for maintaining signal integrity and preventing signal loss. |
Precise Impedance Control | Ensures consistent signal impedance. | Prevents signal reflections and maximizes signal transfer. |
Tight Dimensional Tolerances | Requires precise control over trace widths and spacing. | Ensures correct functioning of microwave components and performance. |
High Thermal Stability | Materials must withstand the thermal stress. | Maintains board performance at various temperatures. |
Consistent Material Properties | Minimizes performance variability. | Ensures predictable and consistent signal behavior across boards. |
Smooth Surface Finish | Ensures good solderability. | Reduces signal issues caused by surface irregularities |
Essential Materials for Microwave PCBs
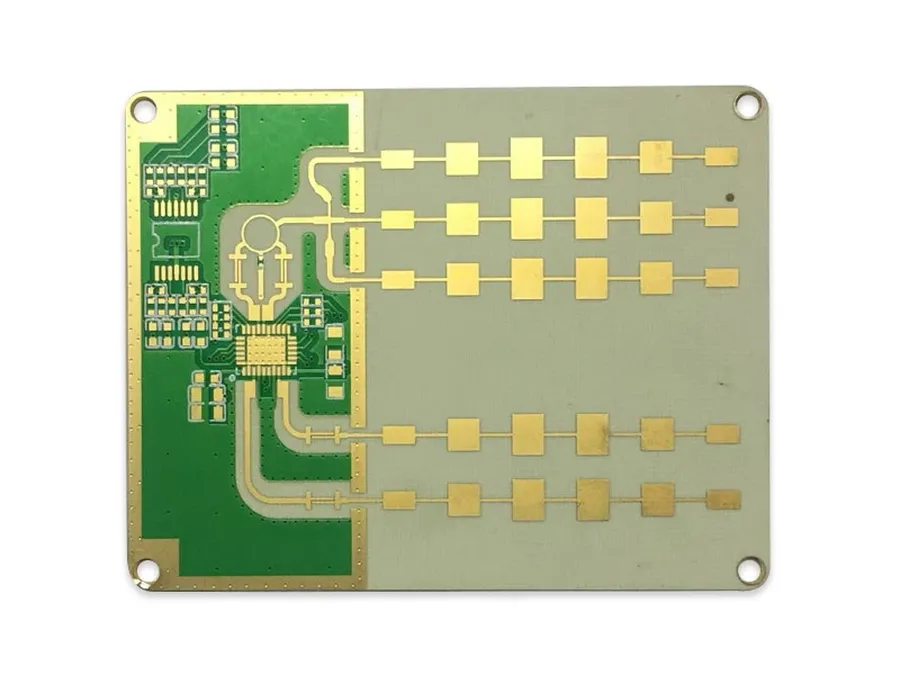
The performance of microwave PCBs hinges significantly on the materials used, as these boards operate at high frequencies where material properties can dramatically affect signal integrity and overall functionality. Selecting the right materials is crucial for achieving optimal performance in microwave applications.
Material | Dielectric Constant (εr) | Loss Tangent (tan δ) | Typical Applications | Advantages | Disadvantages |
---|---|---|---|---|---|
PTFE (Polytetrafluoroethylene) | 2.1-2.3 | 0.0001-0.0003 | High-frequency circuits, antennas, aerospace | Excellent electrical properties, low loss, temperature stability | Expensive, mechanically soft, difficult to process |
Ceramic-filled PTFE | 2.5-10+ | 0.0003-0.002 | Microwave circuits, high-power applications | Improved mechanical strength, tunable dielectric constant | More expensive than standard PTFE, processing can be complex |
Hydrocarbon-based laminates | 3.0-4.0 | 0.002-0.008 | General RF applications, cost-sensitive designs | Good balance of cost and performance, good mechanical properties | Higher loss than PTFE, less temperature stable |
Modified epoxy resins | 4.0-4.8 | 0.010-0.025 | Lower frequency RF, mixed signal boards | Low cost, good availability, easy to process | High loss tangent, limited high frequency performance |
The choice of material is a complex balancing act, dependent on required electrical performance, environmental operating conditions, mechanical stresses, and of course, cost targets. For instance, while PTFE offers superior electrical performance for high-frequency applications, ceramic-filled PTFE can be selected if both the mechanical and high electrical performance are critical, albeit at higher cost.
Critical Manufacturing Capabilities of a Microwave PCB Manufacturer
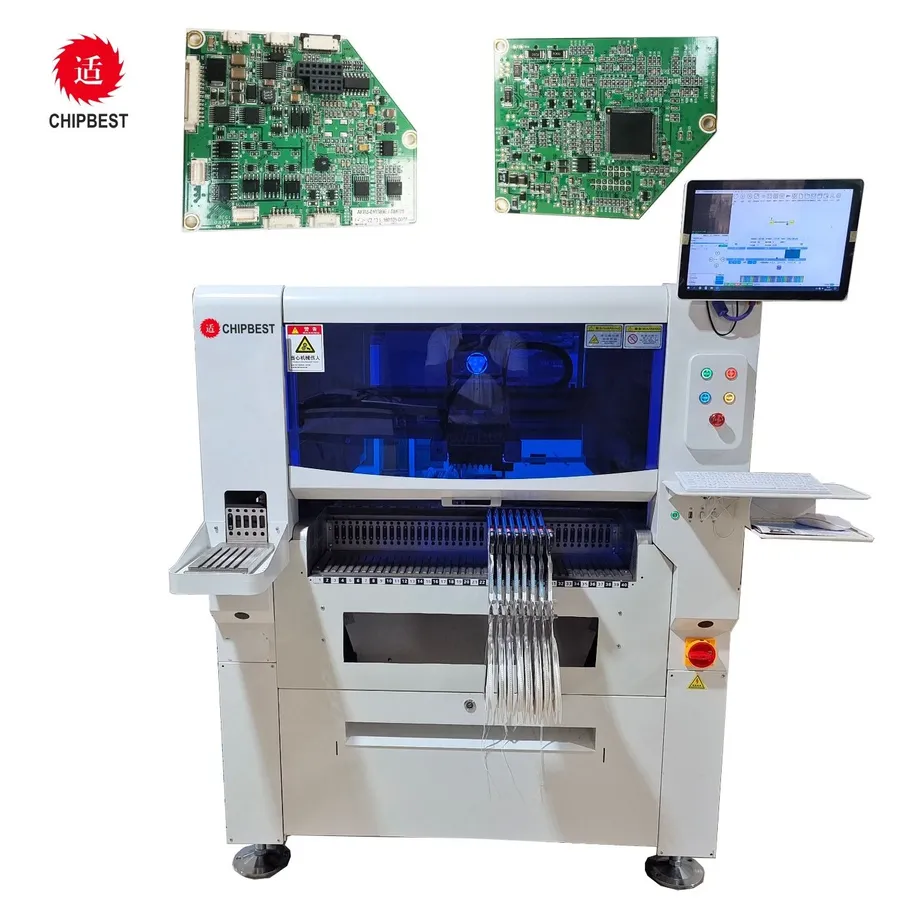
Microwave PCB manufacturing demands a specialized skillset and advanced equipment due to the high frequencies involved. Precision in manufacturing is paramount to ensure signal integrity, minimize signal loss, and maintain performance across various applications. Critical capabilities encompass precision etching for fine lines and spaces, tight impedance control for reliable signal transmission, and the ability to fabricate advanced layer stack-ups.
Capability | Description | Importance for Microwave PCBs |
---|---|---|
Precision Etching | The ability to accurately create fine lines and spaces on the PCB. | Critical for high-frequency circuits where even small variations can affect performance. It ensures that the circuit paths match the design specifications, preventing signal reflections and losses. |
Impedance Control | Maintaining specific impedance values throughout the PCB. | Ensures that signal reflections are minimized, maintaining signal integrity and preventing signal degradation, crucial for accurate signal transmission in microwave applications. |
Advanced Layer Stack-ups | The ability to create complex multilayer PCBs with specific material properties and layer thicknesses. | Enables the creation of PCBs with multiple signal layers, ground planes, and power planes, optimizing for signal performance, minimizing crosstalk, and ensuring efficient power distribution. |
Controlled Drilling | Precise and accurate drilling of vias and holes. | Accurate drilling is vital for precise layer connections and component mounting. Misalignment of vias can create signal discontinuities and impact performance, especially at high frequencies. |
Surface Finish | The surface finish of pads and plated through holes, is crucial for solderability and resistance to environmental conditions. | The surface finish of the PCB impacts the reliability of solder joints, which affects overall performance. A good surface finish ensures that the solder joints are strong and conductive. |
Material Handling | Handling of the specialized materials like PTFE and other high frequency laminates to avoid damage or contamination. | The specialized materials required for microwave PCBs are often delicate. Careful handling and processing is crucial to maintain their properties and prevent issues during fabrication. |
Evaluating a Microwave PCB Manufacturer's Experience
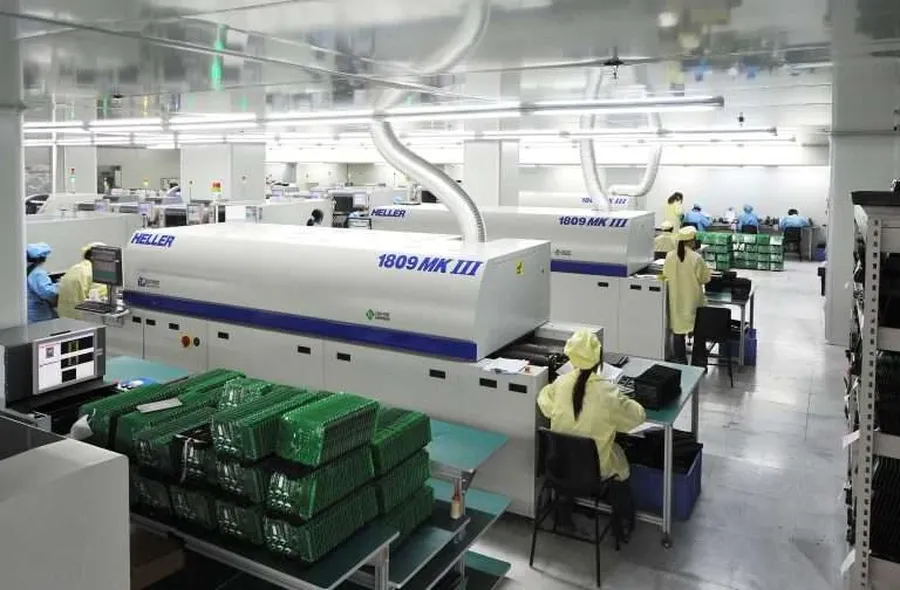
Selecting a microwave PCB manufacturer requires careful consideration of their experience, as it directly impacts the quality and reliability of the final product. A manufacturer's proven track record in handling high-frequency designs and complex fabrication is paramount, as these boards operate under stringent electrical and mechanical specifications. Experience not only ensures adherence to industry best practices but also indicates a deeper understanding of the nuances involved in microwave PCB manufacturing.
Experience in microwave PCB manufacturing offers several key benefits: Familiarity with high-frequency materials, proficiency in precision etching and impedance control and the ability to handle advanced layer stack-ups. A seasoned manufacturer will have a portfolio of successfully completed projects and will be better equipped to address potential challenges that may arise during the manufacturing process.
Here's what to look for when evaluating a potential manufacturer's experience:
- Years of Operation
The number of years a manufacturer has been in business can be a good indicator of their accumulated knowledge and stability. - Project Portfolio
Review their project portfolio for relevant experience in manufacturing microwave PCBs and the types of applications they have supported. - Case Studies
Look for case studies or testimonials that provide evidence of successful projects involving complex designs and high-frequency applications. - Technical Expertise
Inquire about the qualifications and experience of their technical staff, including engineers and fabrication specialists.
Quality Control and Certifications
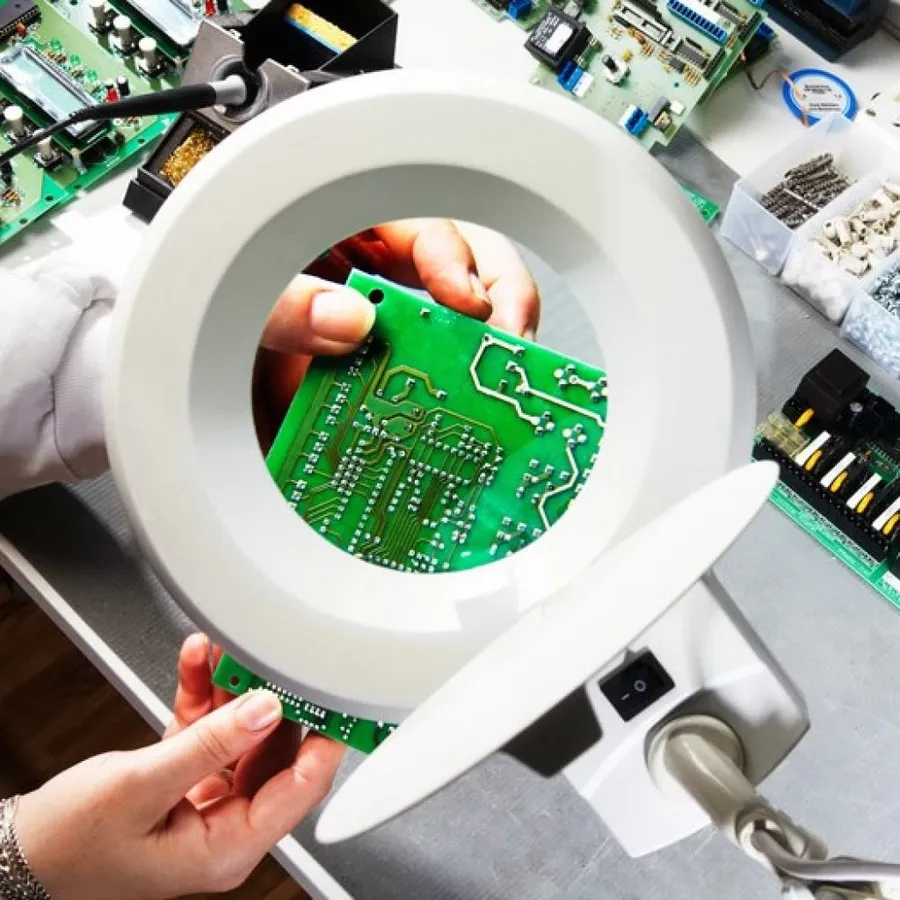
Rigorous quality control and adherence to industry certifications are paramount in microwave PCB manufacturing to guarantee the reliability and performance of these high-frequency boards. These processes ensure that the manufactured PCBs meet the stringent requirements of microwave applications and provide consistent performance.
- Importance of Quality Control
Quality control encompasses a range of activities, from incoming material inspection to final product testing. It's not simply about catching defects; it's about preventing them by implementing robust manufacturing processes that minimize variability. This includes process monitoring, statistical process control (SPC), and regular equipment calibration. By implementing a comprehensive quality control system, manufacturers can consistently produce PCBs that adhere to design specifications and performance requirements, reducing the risk of field failures and ensuring customer satisfaction. - Certifications
Industry certifications validate a manufacturer’s capability to meet specific standards of quality and reliability. Some key certifications in microwave PCB manufacturing include ISO 9001 (Quality Management Systems), AS9100 (Aerospace Quality Management), and IATF 16949 (Automotive Quality Management). Certifications provide an objective assessment of the manufacturer’s processes and demonstrate its commitment to quality. These certifications also often involve third-party audits that provide an additional layer of verification. Furthermore, specific certifications for environmental management (e.g., ISO 14001) can also demonstrate the manufacturer's commitment to sustainability. Manufacturers may also carry IPC certifications, demonstrating their adherence to the industry's standards. - Key Quality Control Processes
Key processes include: * **Incoming material inspection**: Ensuring that raw materials meet specifications is the first step in ensuring a quality product. * **In-process inspections**: Regular checks at various stages of manufacturing to identify and address any issues early. * **Automated Optical Inspection (AOI)**: Using sophisticated equipment to scan PCBs for defects and verify correct assembly. * **Electrical testing**: Testing the electrical performance of the boards to ensure they meet design specifications, including impedance testing, signal integrity analysis, and other critical parameters for microwave frequency operation. * **Final product testing**: Conducting a final inspection and testing to verify that the finished PCBs meet all required specifications before shipping. - Material Traceability
A robust quality control system also requires material traceability. The ability to trace back the origin of raw materials is crucial in identifying and rectifying any potential issues. Traceability involves using lot numbers and other identifiers to track materials from the supplier through the manufacturing process to the final product.
Cost Factors in Microwave PCB Manufacturing
The cost of microwave PCBs is influenced by a complex interplay of factors, predominantly material selection, design complexity, and production volume. Understanding these cost drivers is crucial for effective budgeting and project management. Optimized cost strategies can be implemented by balancing design requirements, performance expectations, and financial constraints.
Cost Factor | Impact on Cost | Mitigation Strategies |
---|---|---|
Material Selection | High-performance materials like PTFE laminates significantly increase cost compared to standard FR-4. | Consider alternative materials with acceptable performance, optimize layer stack-up for material efficiency. |
Design Complexity | Higher layer counts, fine-line traces, complex geometries, and specialized features (e.g., blind/buried vias) increase manufacturing difficulty and cost. | Simplify the design where possible, using standard component footprints and minimizing the number of unique features. |
Production Volume | Low-volume production incurs higher per-unit costs due to setup fees and inefficiencies; high volumes offer economies of scale. | Plan production volumes strategically to leverage price breaks and minimize waste, consider panelization for volume efficiencies. |
Surface Finish | High-performance surface finishes, such as ENIG (Electroless Nickel Immersion Gold) are more costly than HASL. | Choose surface finishes based on application requirements. ENIG is preferred for demanding applications, while HASL may suffice for simpler ones. |
Tolerances and Precision | Tighter tolerances for impedance control and via registration elevate manufacturing precision demands and associated costs. | Balance performance needs with cost by setting realistic tolerance values. |
Testing Requirements | Extensive electrical testing and specialized RF testing will increase the overall cost. | Focus testing on the critical parameters, choose automated testing where possible to minimize manual testing costs. |
The Importance of Prototyping and Testing
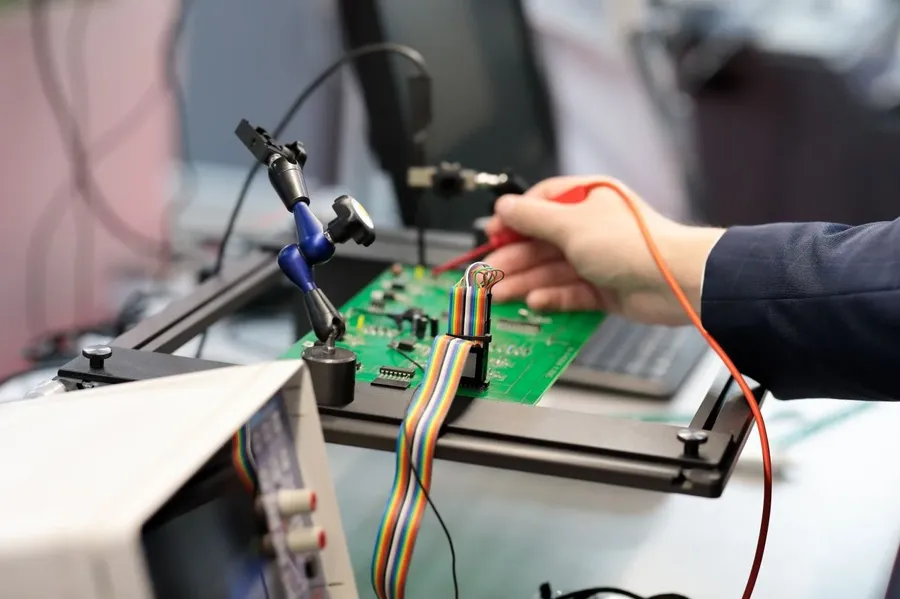
Prototyping and rigorous testing are paramount in microwave PCB manufacturing, serving as critical steps to validate the design and performance of boards before commencing full-scale production. These processes help identify potential issues early, ensuring the final product meets the stringent requirements of high-frequency applications, avoiding costly errors and delays in mass production.
- Design Validation
Prototyping allows for the empirical validation of the PCB design. It confirms whether the theoretical design translates into practical functionality, particularly concerning signal integrity and impedance matching at microwave frequencies. - Performance Verification
Testing of prototypes is essential to verify the electrical performance of the PCB, including parameters like insertion loss, return loss, and isolation. These tests ensure the PCB will function correctly in its intended high-frequency applications. - Material Evaluation
Prototyping enables testing of the chosen materials under actual operating conditions, ensuring their suitability for high-frequency applications. It assesses the material’s dielectric constant and loss tangent at microwave frequencies. - Process Optimization
The prototyping phase offers an opportunity to fine-tune the manufacturing processes, identify potential bottlenecks, and optimize parameters for mass production. This can prevent problems in large-scale fabrication. - Cost Reduction
By identifying and correcting design or manufacturing flaws early on, prototyping and testing mitigate the risk of costly errors in the final production, thus lowering the overall cost of manufacturing. - Risk Mitigation
Rigorous testing at the prototyping phase helps in identifying any possible manufacturing defect or design vulnerability that can lead to product failure, reducing the risk of producing faulty end-products.
Frequently Asked Questions about Microwave PCB Manufacturing
This section addresses common inquiries regarding microwave PCB manufacturing, providing clarity on aspects from material selection to quality control, and the critical design considerations involved in producing high-performance microwave PCBs.
- What are the key differences between standard PCBs and microwave PCBs?
Microwave PCBs operate at much higher frequencies (typically above 1 GHz) than standard PCBs. This requires the use of specialized materials with low dielectric loss and tight impedance control, as well as manufacturing processes optimized for precision and minimal signal degradation. Standard PCBs, in contrast, often utilize FR-4 material and less stringent manufacturing tolerances. - How does material selection affect microwave PCB performance?
The choice of materials is paramount for microwave PCB performance. Materials with low dielectric constant and loss tangent, like PTFE, are crucial for minimizing signal attenuation and maintaining signal integrity at high frequencies. The material's thermal properties and mechanical stability are also important considerations. - What are the most important design considerations for microwave PCBs?
Critical design considerations include precise impedance matching, careful trace routing to minimize signal reflections, and the use of appropriate ground planes to reduce noise. Component placement and the design of discontinuities such as vias also play a significant role in overall performance. It is essential to use design software specifically for high frequency applications. - What manufacturing capabilities should I look for in a microwave PCB manufacturer?
A capable microwave PCB manufacturer should have expertise in precision etching for fine-line traces and tight impedance control. They should also possess the ability to handle advanced multilayer stack-ups using the specialized materials needed for microwave applications and possess robust quality control measures, including electrical testing. - What kind of quality certifications should a microwave PCB manufacturer have?
Manufacturers should hold certifications like ISO 9001 for quality management, and preferably industry-specific certifications like AS9100 for aerospace or IATF 16949 for automotive applications. Compliance with IPC standards for PCB fabrication is also crucial. Such certifications demonstrate the manufacturer's commitment to quality and consistency. - Can any PCB manufacturer produce microwave PCBs?
No, the fabrication of microwave PCBs requires specialized equipment, materials, and expertise. General-purpose PCB manufacturers often lack the technology and knowledge required to produce high-performance boards. It's crucial to choose a manufacturer that is experienced in microwave and high-frequency applications. - What is the typical prototyping and testing process for microwave PCBs?
Prototyping involves creating a small batch of boards to validate the design. Testing is a critical part of the process, that includes, impedance measurements, S-parameter analysis, and thermal tests as well. The manufacturer should be capable of using test equipment like vector network analyzers to characterize the performance of the PCB across the intended frequency range, to ensure the design meets specified performance parameters.
Future Trends in Microwave PCB Manufacturing
The microwave PCB manufacturing landscape is continually evolving, driven by the demand for higher frequencies, improved performance, and greater miniaturization. This section explores the emerging trends and cutting-edge technologies that are poised to shape the future of microwave PCB fabrication.
- Advanced Materials
Beyond traditional PTFE, research is focused on new materials with lower loss tangents, higher dielectric constants, and improved thermal management capabilities. These include novel ceramic composites, liquid crystal polymers (LCPs), and modified epoxies, enabling higher performance and improved reliability for microwave applications. - 3D Printing and Additive Manufacturing
Additive manufacturing technologies are gaining traction in PCB production, allowing for the creation of complex 3D structures, embedded components, and conformal circuits. This approach offers design freedom, faster prototyping, and the potential for customized solutions in microwave applications. - Integrated Passives
The integration of passive components such as resistors, capacitors, and inductors directly into the PCB substrate reduces overall size and improves performance by minimizing parasitic effects. This trend is critical for compact, high-frequency microwave designs, offering improved impedance matching and signal integrity. - Miniaturization and High-Density Interconnect (HDI)
As devices become smaller and more feature-rich, the need for miniaturized PCBs increases. HDI technology, with its finer lines, spaces, and microvias, is essential for meeting the demands of high-frequency, compact microwave modules, enabling more complex circuitry in a reduced footprint. - Artificial Intelligence (AI) and Machine Learning (ML) in Manufacturing
AI and ML are being implemented for process optimization, predictive maintenance, and quality control in PCB manufacturing. These technologies enable manufacturers to improve yields, reduce defects, and ensure consistent performance of microwave PCBs through data analysis and adaptive process adjustments. - Sustainable Manufacturing Practices
There's an increasing emphasis on environmentally responsible manufacturing. This includes the use of eco-friendly materials, reduced chemical usage, and improved energy efficiency during PCB fabrication. These efforts help minimize the environmental impact while maintaining high-performance standards.
Selecting a microwave PCB manufacturer is a crucial step in any high-frequency project. By understanding the unique requirements, considering manufacturer experience, and prioritizing rigorous testing, you can find a partner that aligns with your needs. Remember, choosing the right microwave pcb manufacturer can significantly impact the performance and reliability of your final product, making it worth the investment in due diligence. With ongoing advancements in technology, the future of microwave PCBs holds great potential, emphasizing the need to stay informed and work with expert partners in the field.
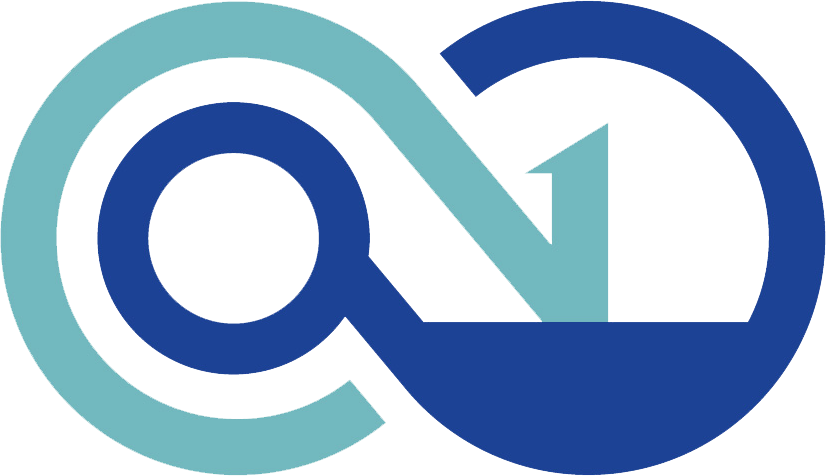