Choosing the Right Quick Turn PCB Factory: A Comprehensive Guide
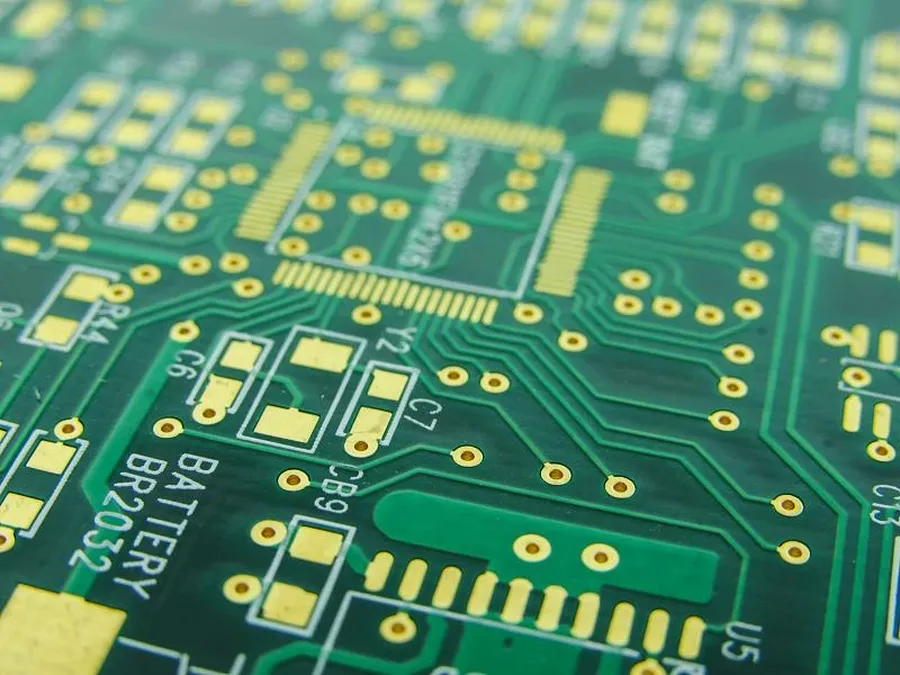
In today's fast-paced electronics industry, time is often of the essence. Quick turn PCB factories are vital for rapid prototyping and production, enabling engineers to test ideas and bring products to market faster. This article will delve into the crucial aspects of selecting a suitable quick turn PCB factory, drawing upon industry insights and technological advancements, connecting the essential need for speed with the precision required in modern electronic design. We will cover key considerations and provide actionable tips to ensure you choose the best partner for your PCB needs. Whether you're a seasoned engineer or a startup founder, understanding these nuances will pave the way for successful product development.
Understanding Quick Turn PCB Manufacturing
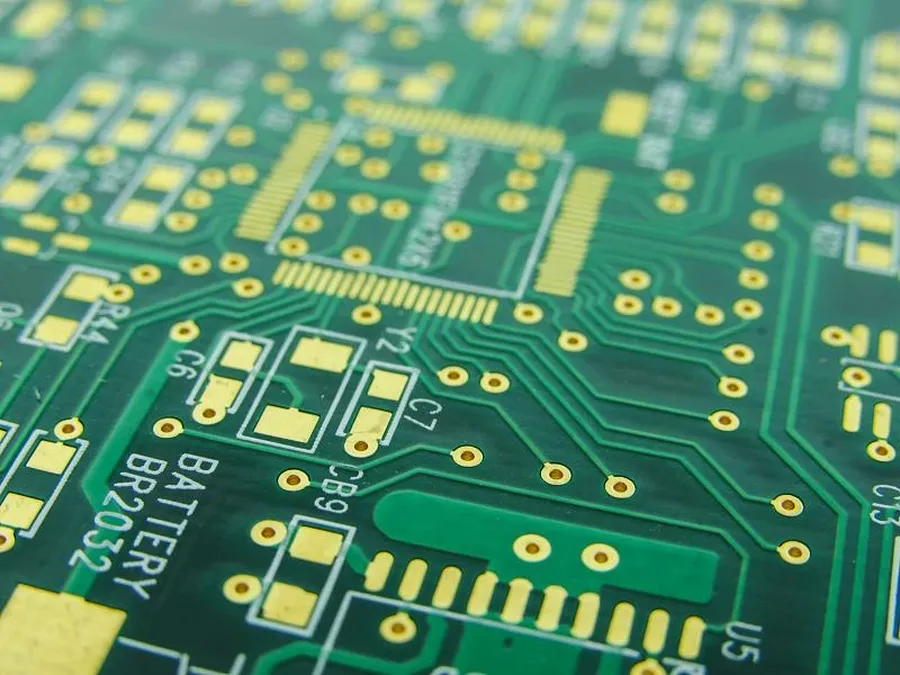
Quick turn PCB manufacturing is characterized by its accelerated production timelines, contrasting with standard PCB fabrication that typically involves longer lead times. This expedited service is designed to rapidly produce printed circuit boards, typically within 24 hours to a few days, enabling faster prototyping and time-sensitive project completions. The turnaround time varies depending on factors such as design complexity, material availability, and order volume.
Several key factors influence the speed of quick turn PCB production:
- Design Complexity
Intricate designs with numerous layers, fine traces, and vias require more processing time compared to simpler layouts. - Material Selection
The availability and processing requirements of specific materials, such as high-frequency laminates or specialized substrates, impact manufacturing speed. - Order Volume
Larger production runs often necessitate more time, although some facilities offer expedited services even for substantial orders.
Key Factors When Selecting a Quick Turn PCB Factory
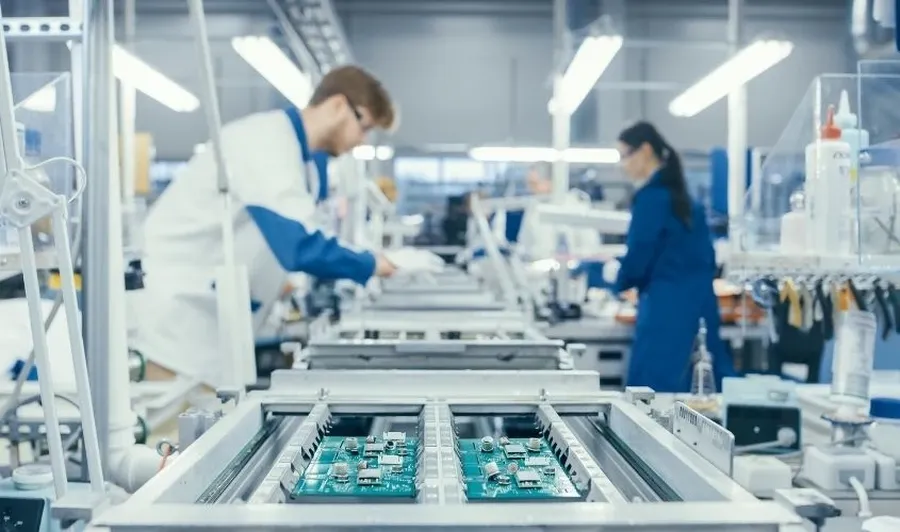
Selecting the right quick turn PCB factory hinges on several critical factors that directly impact the quality, functionality, and timely delivery of your printed circuit boards. These factors range from material capabilities and precision to testing services and certifications. A careful evaluation of these elements is essential to ensure that your chosen factory aligns perfectly with your project requirements, budget, and time constraints.
Factor | Description | Importance |
---|---|---|
Material Capabilities | The range of materials the factory can process, including FR-4, high-Tg, Rogers, and flexible substrates. | Critical for meeting specific application requirements and operating conditions; affects performance, durability and signal integrity. |
Layer Count | The number of conductive layers the PCB supports, influencing complexity and density. | Directly related to the design complexity and functionality of the PCB; important in multi-layered high performance applications. |
Surface Finishes | Options include HASL, ENIG, Immersion Silver, and others, which affect solderability and corrosion resistance. | Impacts the longevity and reliability of solder joints; choose according to environmental conditions and application. |
Precision and Tolerances | Minimum trace widths/spacing, via sizes, and overall dimensional accuracy. | Ensures proper functionality and compliance with design specifications; critical for high-density designs. |
Panelization Options | Capabilities of creating multiple boards on a single panel for efficient production. | Reduces manufacturing costs and accelerates turnaround times. |
Testing Services | Types of tests offered such as Electrical Testing, AOI, and X-ray inspection. | Verify the functional and quality standards of the PCB; reduces the likelihood of failures. |
Certifications | Quality and reliability certifications such as ISO 9001, AS9100, or IPC standards. | Indicate that the factory adheres to established quality control processes; important for reliability and compliance. |
Turnaround Time and Lead Times: What to Expect
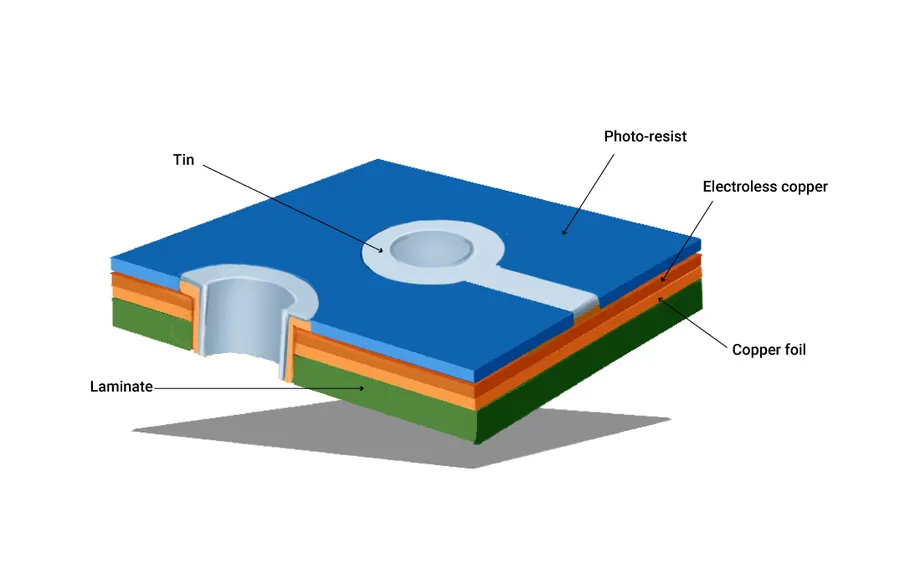
Quick-turn PCB manufacturing offers expedited services, but turnaround times can vary significantly based on several factors. Understanding these variations and their causes is crucial for effective project planning. While some factories may offer completion in as little as 24 hours, others might take several days, making it essential to align expectations with a given factory’s capabilities and your project’s requirements.
Factor | Impact on Lead Time | Mitigation Strategies |
---|---|---|
Design Complexity | More complex designs with multiple layers, intricate routing, or fine traces require more processing time. | Simplify design where possible; optimize for manufacturing; use standard components. |
Order Size | Larger orders typically take longer to produce than smaller ones due to increased production and quality control steps. | Accurately estimate needs; consider phased orders if possible. |
Material Availability | Lead times may be extended if specialized materials with longer lead times are needed. | Use common materials; verify material availability beforehand. |
Factory Workload | Factories experiencing high demand may have longer lead times even for standard orders. | Communicate early with your manufacturer; plan for potential delays. |
Surface Finishes | Certain finishes may require additional processing time. | Consider alternative, faster options when applicable; clarify finish requirements early on. |
To minimize delays, it is essential to establish clear and concise communication with your chosen PCB factory. Providing detailed specifications and design files up front, and maintaining open lines of communication throughout the process, can help to mitigate misunderstandings and ensure a smooth and timely production schedule. Planning your projects with potential lead time variability in mind is crucial to meeting deadlines.
Cost Considerations: Balancing Speed and Budget
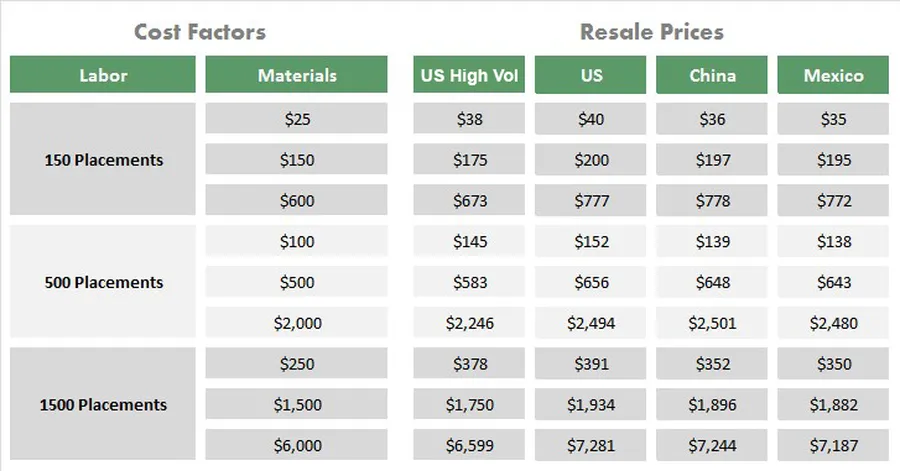
Selecting a quick-turn PCB factory necessitates a careful balance between speed and cost. Faster turnaround times often come with increased expenses. A thorough understanding of pricing structures and cost optimization strategies is essential for achieving both project objectives and budgetary goals.
The cost of quick-turn PCB fabrication is not static and is influenced by multiple variables, primarily the required turnaround time. Expedited services demand additional resources and incur a premium over standard lead times. Furthermore, costs can fluctuate based on factors such as design complexity, material requirements, order volume, and chosen surface finishes.
Cost Factor | Impact on Price | Optimization Strategies |
---|---|---|
Turnaround Time | Faster turnarounds generally increase costs significantly due to expedited processes. | Plan ahead, clearly define deadlines, and avoid unnecessary rush orders. |
Design Complexity | Intricate designs with tight tolerances and numerous layers require more specialized manufacturing, increasing costs. | Implement Design for Manufacturability (DFM) to simplify designs. Design reviews can help catch and fix issues before fabrication. |
Material Selection | Specialized and high-performance materials will always lead to higher costs | Consider using standard materials if they meet performance requirements to reduce the price. |
Order Volume | Small orders often have higher per-unit costs due to set-up expenses. | Consolidate orders when possible and use panelization to reduce costs per PCB. |
Surface Finish | Premium surface finishes (e.g., ENIG) are more costly than standard options (e.g., HASL). | Choose the appropriate finish for the application. Consider lower-cost options if performance is not compromised. |
Effective cost optimization involves adopting Design for Manufacturability (DFM) practices. DFM reduces production costs by ensuring the PCB design is optimized for efficient manufacturing. This includes using standard components, designing with consideration for manufacturing limitations, and avoiding overly complex layouts when possible. DFM can help reduce re-spins and therefore save time and money.
Price structures for quick-turn PCB services can vary significantly. Some factories might implement a tiered pricing system based on turnaround time, order size, or design complexity. For example, a 24-hour turnaround may cost significantly more per unit than a 3-day turnaround for an identical design. Understanding these structures is important to choose the right production schedule. Furthermore, negotiating and communicating clear needs can help secure more advantageous rates. It is also important to ensure that the factory has all the correct tooling to avoid delays and unnecessary cost increases.
Geographic Considerations: Domestic vs. Offshore Quick Turn PCB Factories
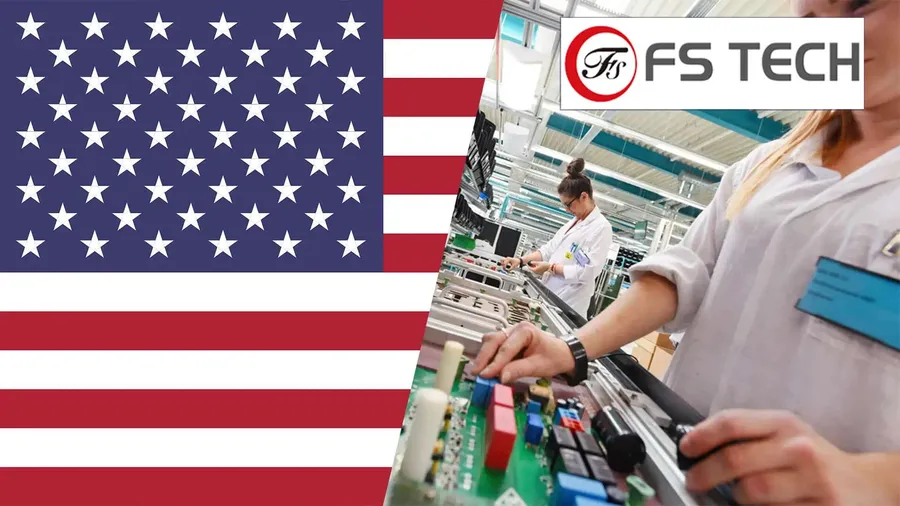
The decision between domestic and offshore quick-turn PCB factories is pivotal, significantly impacting project timelines, costs, and quality. This choice necessitates a careful evaluation of several factors, including manufacturing standards, communication ease, turnaround times, and overall costs. Understanding these aspects is crucial for making an informed decision aligned with project needs and constraints.
Factor | Domestic Quick Turn PCB Factories | Offshore Quick Turn PCB Factories |
---|---|---|
Manufacturing Standards | Typically adhere to stringent international standards (e.g., IPC, ISO) often enforced with greater oversight. | Standards vary widely; some adhere to high standards, while others may have less stringent practices. |
Communication | Direct, often real-time communication due to proximity and similar time zones, facilitating quicker issue resolution. | Communication may be challenging due to time zone differences and language barriers; requires clear and detailed specifications. |
Turnaround Times | Potentially faster shipping and logistics due to domestic locations, which can reduce total project lead time. | Shipping times can be significantly longer, affecting overall project turnaround time; customs and logistics add complexity. |
Costs | Generally higher manufacturing costs due to labor and overhead expenses; may have reduced shipping and logistics costs. | Generally lower manufacturing costs due to lower labor and operational costs; may involve higher shipping and import duties. |
Quality Control | Easier to oversee and verify quality due to proximity and often, established trust in manufacturing practices. | Quality control can be more challenging to oversee remotely; needs thorough vetting and may require on-site visits. |
Intellectual Property | IP protection can be more reliable due to domestic legal frameworks. | IP protection is a significant concern; requires careful contracts and risk assessment. |
Selecting a factory requires a comprehensive understanding of the project needs and the implications of each choice. Domestic factories offer advantages in communication, quality oversight, and IP protection, often at a higher cost. Offshore options can provide cost savings but may introduce challenges in communication, quality control, and lead times. The optimal choice hinges on balancing these competing factors in alignment with project-specific requirements and constraints.
Quality Assurance and Certifications
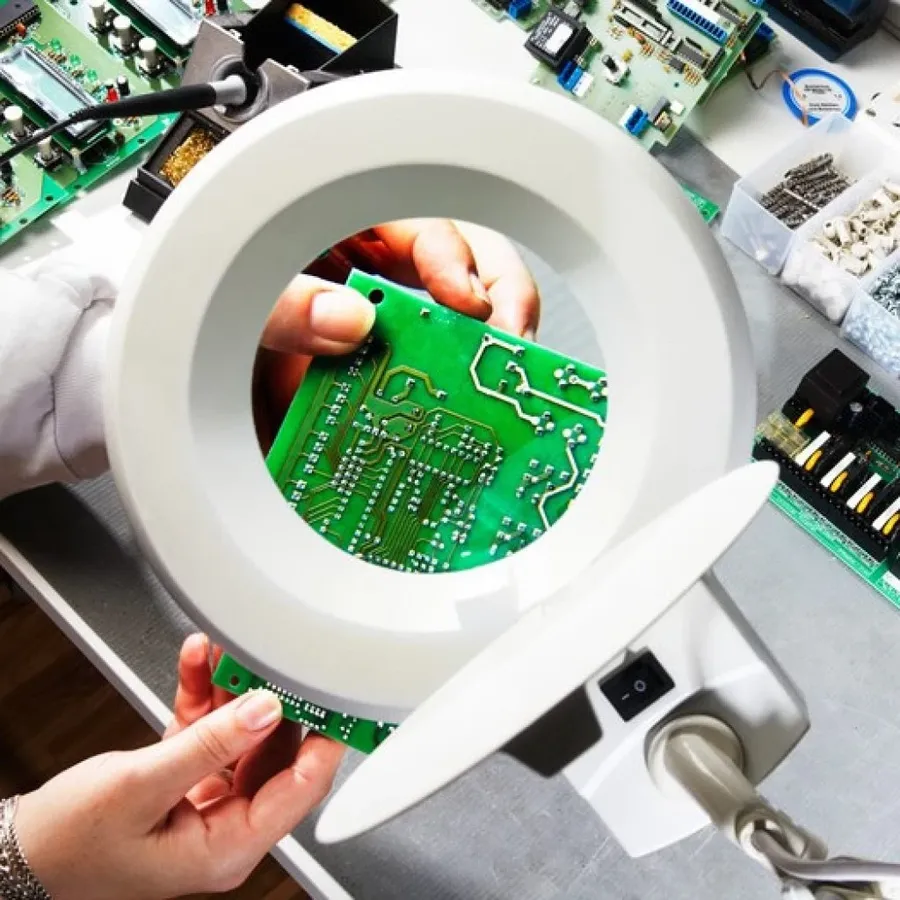
Rigorous quality assurance and relevant certifications are paramount when selecting a quick turn PCB factory. These measures ensure the reliability and performance of your printed circuit boards. Verifying a manufacturer's commitment to quality control is crucial for avoiding costly defects and delays.
Key aspects of quality assurance and certifications include:
- ISO 9001 Certification
ISO 9001 is a globally recognized standard for quality management systems (QMS). A factory with ISO 9001 certification demonstrates a commitment to consistently providing products that meet customer and regulatory requirements. This certification indicates a robust system for process control, documentation, and continuous improvement. - AS9100 Certification
AS9100 is the quality management system standard specific to the aerospace industry. This certification is crucial for manufacturers supplying PCBs to the aerospace, defense, and space sectors, signifying compliance with stringent requirements for product safety and reliability. This standard includes specific clauses relating to risk and product traceability, necessary for these high-reliability applications. - IPC Standards Compliance
IPC standards (e.g., IPC-A-600, IPC-A-610) set the industry-wide benchmarks for acceptability of printed boards. Look for manufacturers that adhere to these standards in both fabrication and assembly processes. Compliance with IPC standards ensures consistent quality and reduces the risk of product failure. - Equipment and Technology
A reputable quick-turn PCB factory will invest in modern, high-end equipment to ensure precision and repeatability in manufacturing. This includes automated pick-and-place machines, advanced etching and plating systems, and high-resolution testing equipment. Confirm that the factory has the necessary technology to produce PCBs according to the required tolerances and specifications. - Technical Staff Qualifications
The expertise of the factory’s technical staff is essential for maintaining quality. Qualified engineers and technicians with experience in PCB fabrication and assembly are vital. Inquire about the factory's training programs and the qualifications of its key personnel. Continuous training and certification of staff are indicators of a proactive approach to quality. - Testing Procedures
A comprehensive testing regime is essential to confirm PCB performance and reliability. This includes Electrical Testing (ET), Impedance Testing, Flying Probe Testing and Automated Optical Inspection (AOI) where appropriate. Ensure the factory has rigorous testing protocols in place, and that they match the requirements of your project.
To assess a manufacturer's quality control measures, consider the following:
- Documented Processes
Look for a factory that uses documented process controls with clear procedures for each production step. This is a hallmark of a robust quality management system. Request access to these documents if necessary. - Inspection Reports
Reliable manufacturers should provide detailed inspection reports for each production run. These reports should include testing data and visual inspection results that confirm the quality of the boards. - Corrective Actions
Inquire about the manufacturer's process for addressing nonconformities. A structured process for corrective and preventative actions is indicative of their ability to learn and improve from any issues identified during production.
Frequently Asked Questions About Quick Turn PCB Manufacturing
This section addresses common questions about quick turn PCB manufacturing, offering concise and practical answers to guide you further.
- What is quick turn manufacturing, and how does it apply to PCBs?
Quick turn manufacturing refers to an expedited production process that significantly reduces the time between design and delivery. In the context of PCBs, it involves a faster fabrication and assembly process, enabling rapid prototyping or addressing urgent production needs. This is achieved through streamlined workflows, prioritizing fast turnaround times over standard lead times, while maintaining quality and precision. - What exactly is a quick turn PCB?
A quick turn PCB is a printed circuit board manufactured using accelerated processes to meet tight deadlines. The key differentiator is the reduced manufacturing time, often measured in days instead of weeks, allowing for rapid iteration and validation. This speed comes from using streamlined processes, often with a higher associated cost, in comparison to standard production cycles. - How do quick turn PCB factories handle complex PCB designs?
Quick turn PCB factories address complex designs using specialized equipment, advanced software, and experienced staff. They use sophisticated CAM (Computer-Aided Manufacturing) software to prepare intricate layouts, high-precision machinery for drilling and etching, and highly skilled technicians to navigate the nuances of complex designs, while still prioritizing a fast turnaround. - Is a quick turn PCB suitable for all project types?
While quick turn PCBs are beneficial for many projects, they might not be optimal for all. Quick-turn services are best suited for prototypes, urgent design validations, or short-run production needs where time is of the essence. Large-scale projects with less time pressure, or that require special materials and intricate designs, might be better suited to a standard, or longer, lead time. - What is the process for setting up a PCB manufacturing factory?
Setting up a PCB manufacturing factory involves a complex process including securing funding, selecting an appropriate facility, investing in advanced equipment (such as etching, drilling, and plating machines), hiring skilled staff, establishing supply chains, and implementing rigorous quality control measures. Compliance with environmental regulations and securing certifications are also vital. A thorough business plan and feasibility study are indispensable for a successful launch. - Who are some of the leading PCB manufacturers globally?
The global PCB manufacturing landscape includes both large international players and specialized regional manufacturers. Some of the globally recognized leading manufacturers include companies like TTM Technologies, Unimicron, and Nippon Mektron. However, many smaller, more specialized PCB manufacturers excel in specific niches or technologies. The best choice will depend on your project requirements and the location of your supply chain. - Beyond time and cost, what other factors should be considered when choosing a quick turn PCB factory?
Beyond time and cost, critical factors to consider include the factory's material capabilities, layer count limits, precision standards, available surface finishes, testing procedures, and certifications (ISO 9001, AS9100, IPC standards). You should also evaluate their communication responsiveness, design for manufacturability (DFM) support, and the availability of engineering support. All of these factors impact the quality and reliability of the final product. - What are common errors to avoid when selecting a quick turn PCB factory?
Common errors include failing to verify certifications, not clearly communicating project specifications, neglecting DFM checks, focusing only on price without considering quality, overlooking the factory's capacity to handle the project's design complexity, and assuming that all quick-turn services are equal. A due diligence approach and clear communication with the factory is essential to avoid these issues.
Case Studies: Success Stories with Quick Turn PCB Factories
Real-world examples of successful projects utilizing quick turn PCB services demonstrate the tangible benefits of selecting an appropriate factory. These case studies span various industries and applications, showcasing how the right choice can significantly impact project timelines and product quality, often providing a competitive edge through rapid prototyping and time-to-market.
The following case studies illustrate the benefits of leveraging quick turn PCB factories across diverse sectors:
- Aerospace Startup: Rapid Prototyping for Flight Control Systems
A new aerospace startup needed to rapidly prototype and test a new flight control system. By using a quick-turn PCB factory they were able to create prototypes in 48 hours. This rapid iteration enabled them to quickly identify and fix design flaws and accelerate their product development cycle, reducing time to market by three months. The boards produced had stringent requirements and the factory was able to meet the required specifications. This success led to them securing Series A funding. - Medical Device Company: Fast Turnaround for Patient Monitoring Equipment
A medical device company required a small number of high-precision PCBs for patient monitoring equipment. The quick turn PCB factory provided the required parts in 24 hours. This greatly reduced the time that the company needed for prototyping and testing for regulatory compliance. The quick turn around allowed the company to get their device to market and start helping patients a lot quicker than their competition. - Consumer Electronics Manufacturer: Agile Production of Wearable Devices
A consumer electronics company producing wearable fitness trackers required a quick turnaround on a new batch of circuit boards. By using a quick turn factory they were able to ensure consistent quality, while still meeting tight deadlines. This ability to quickly pivot and respond to market needs allowed the company to stay ahead of the competition and meet the demand for their product. - Industrial Automation: Custom Solutions for Manufacturing Lines
An industrial automation company needed specialized PCBs for a new robotic arm used on an assembly line. By using a quick-turn PCB factory, they were able to quickly and cost-effectively produce boards with the specific dimensions, material, and high-performance requirements they needed. The customized boards ensured reliable operation within the harsh factory conditions, leading to increased production efficiency and decreased downtime.
These case studies showcase the importance of choosing the right quick turn PCB factory to suit the project's needs. They clearly highlight how a fast, reliable manufacturer can contribute significantly to success in diverse industries by improving production timelines and delivering high quality circuit boards.
Future Trends in Quick Turn PCB Manufacturing
The quick turn PCB manufacturing landscape is rapidly evolving, driven by technological advancements and increasing demands for faster, more efficient production. This section explores key trends that are poised to shape the future of the industry, focusing on innovations that enhance speed, sustainability, and performance.
- Advanced Materials
The incorporation of new materials with superior thermal, electrical, and mechanical properties will enable higher performance and more reliable PCBs. These include advanced polymers, ceramics, and composites, designed to withstand extreme conditions and enhance signal integrity. - Automation and AI
Increased automation in PCB manufacturing processes, driven by artificial intelligence and machine learning, will enhance production speed, reduce human errors, and optimize resource utilization. AI-powered tools are being used for predictive maintenance, defect detection, and process optimization, leading to improved efficiency and yield. - Digital Twins
The use of digital twins is allowing manufactures to create a virtual representation of the physical factory and processes. This enables manufactures to monitor, analyze and optimize operations in real time, and to simulate changes and upgrades before implementing them physically, which is leading to faster iteration and improvements in efficiency. - Sustainable Practices
The drive toward environmentally friendly manufacturing is pushing the industry to adopt sustainable practices, like the use of eco-friendly materials, closed-loop water systems and waste reduction processes. Regulations are also driving manufacturers to reduce emissions and their overall environmental impact. - Additive Manufacturing
Additive manufacturing techniques, such as 3D printing, are becoming more relevant in PCB prototyping and potentially in the production of specialized PCBs, offering greater flexibility, faster turnaround, and the ability to create complex geometries.
Staying at the forefront of these trends requires a proactive approach. Partnering with forward-thinking PCB factories that embrace innovation and are ready to invest in cutting-edge technologies is a strategic advantage for companies seeking to leverage the latest advances in quick turn PCB manufacturing.
Choosing the right quick turn PCB factory is crucial for the success of your project. By understanding the nuances of quick turn PCB manufacturing, you can make an informed decision that balances cost, time, and quality. This guide has highlighted critical factors, including the different types of quick-turn PCB factories, turnaround times, material options, quality assurance, and cost optimization. By leveraging the best practices and insights discussed here, engineers, entrepreneurs and everyone in between can navigate the quick turn PCB industry efficiently. Remember that the best outcome involves thoroughly evaluating options, communicating effectively with your chosen manufacturer, and leveraging the capabilities of the modern quick turn PCB factory to achieve the optimum results.
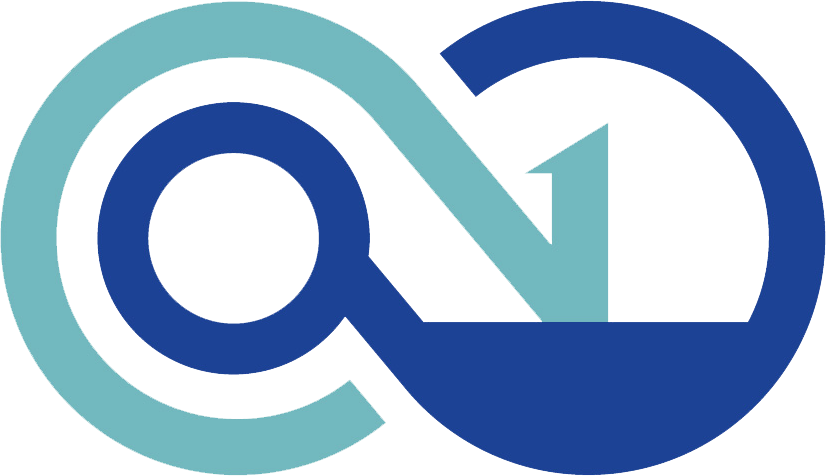