Choosing the Right Soldering Board: A Comprehensive Guide
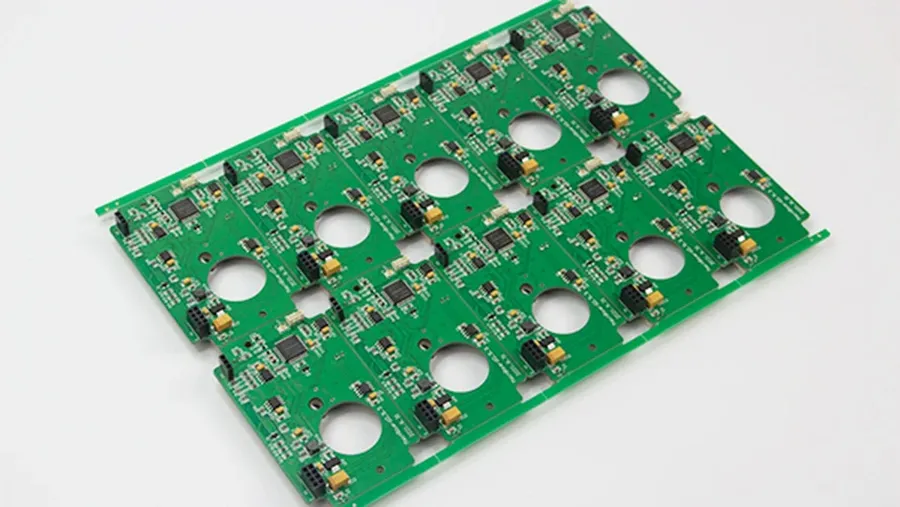
Soldering, a fundamental skill in electronics and jewelry making, relies heavily on a suitable soldering board. Just as an artist needs a canvas, a craftsman needs the right surface. A well-chosen soldering board not only provides a safe and stable platform but also significantly impacts the quality of the finished product. This article will guide you through the selection process, ensuring that your soldering projects are both precise and successful, focusing on the aspects of safety, material, and heat resistance relevant to various applications.
Understanding the Role of a Soldering Board
A soldering board is a critical component of any soldering setup, serving as a stable, heat-resistant surface that significantly enhances both safety and the quality of soldering work. Beyond simply protecting your workbench from the high temperatures involved in soldering, these boards contribute to the consistency and reliability of soldered joints by providing a secure and even platform for the work.
Types of Soldering Boards and Their Materials
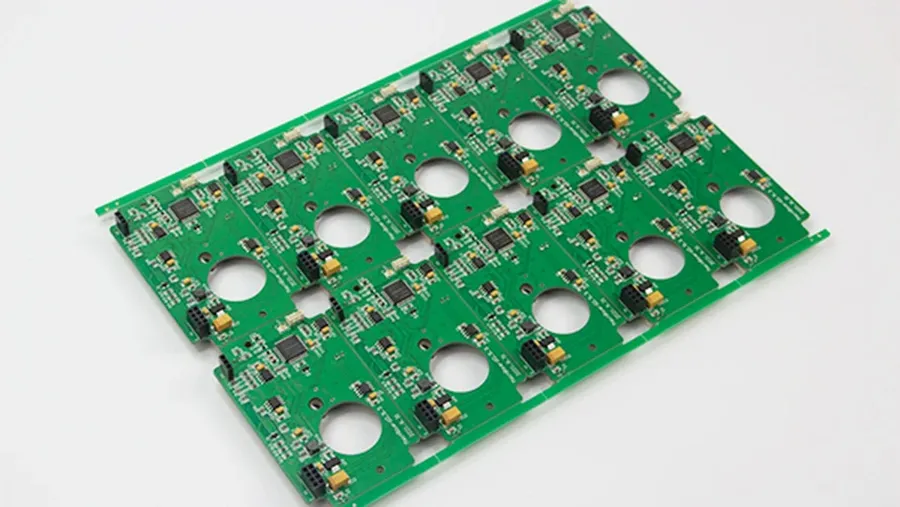
Selecting the correct soldering board is crucial for successful and safe soldering. Different materials offer varying degrees of heat resistance, durability, and suitability for specific applications. Understanding these differences allows for informed decisions, ensuring project success, safety, and efficiency.
Soldering boards are crafted from several key materials, each with unique characteristics:
- Ceramic Boards
Known for their high heat resistance and even heat distribution, making them ideal for jewelry making and precision electronics work. They are durable but can be brittle. - Charcoal Blocks
Excellent for metalworking, these boards help prevent oxidation and provide support for soldering pieces. They are also used in casting, but care must be taken to avoid contamination with carbon. - Solderite Boards
A modern option with a smooth surface, good heat reflection, and rapid cool down capabilities, suitable for a variety of soldering tasks and especially convenient for repeated use.
The distinction between 'hard' and 'soft' soldering boards primarily refers to their density and material composition. Hard boards, like those made from ceramic, provide a rigid, stable surface and are preferable for high-heat applications. Soft boards, often charcoal, are more porous and may require more careful handling and maintenance, but offer unique benefits such as preventing oxidation. Ultimately, the optimal choice hinges on the type of soldering project, heat requirements, and user preference.
Material | Heat Resistance | Durability | Typical Applications | Hard/Soft |
---|---|---|---|---|
Ceramic | High | High, but brittle | Jewelry, small electronics | Hard |
Charcoal | High | Moderate, can crumble | Metalworking, casting | Soft |
Solderite | High | High | General soldering tasks | Hard |
Ceramic Soldering Boards: Benefits and Uses
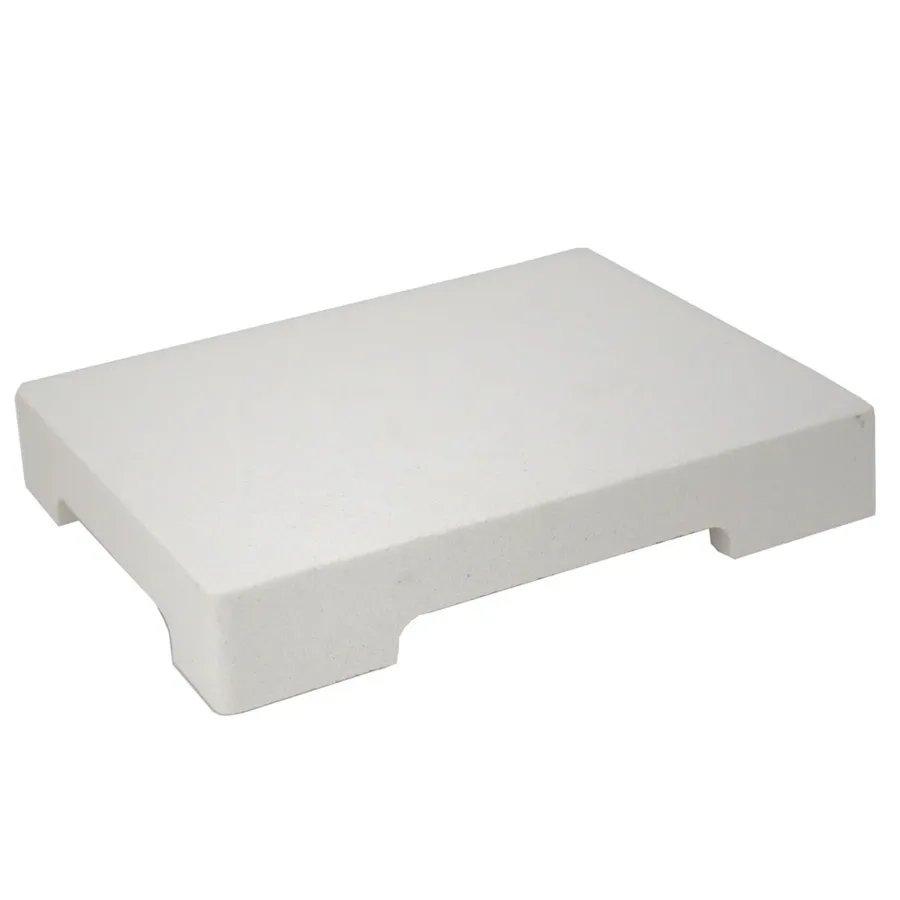
Ceramic soldering boards are a preferred choice for many soldering applications due to their exceptional heat resistance and ability to distribute heat evenly, which significantly enhances the soldering process. Their robustness at high temperatures makes them ideal for tasks requiring consistent heat without board degradation.
- High Heat Resistance
Ceramic boards can withstand extremely high temperatures without warping or cracking, making them suitable for prolonged soldering sessions. - Even Heat Distribution
The uniform surface of ceramic ensures that heat is evenly dispersed across the board, preventing hot spots that could affect soldering quality. - Durability
Ceramic soldering boards are highly durable and resistant to chemical reactions, making them suitable for various soldering techniques. - Non-reactive Surface
The non-reactive surface of ceramic boards prevents contamination of the solder joint and ensures a clean and precise soldering process.
These properties make ceramic boards particularly well-suited for delicate work, such as jewelry making, and precision tasks, like small electronics repair. The controlled heat distribution is crucial when dealing with temperature-sensitive components. In jewelry making, the ability to withstand direct torch flame allows for complex soldering maneuvers without damaging the board, while in electronics, the even heat helps ensure that components are soldered correctly without overheating.
Feature | Benefit |
---|---|
High Temperature Resistance | Suitable for high-heat applications |
Even Heat Distribution | Prevents hot spots and ensures consistent soldering |
Durable | Resistant to wear and tear and chemical reactions, long lasting |
Non-reactive | Prevents contamination of solder joints |
Charcoal Soldering Blocks: When and Why to Use Them
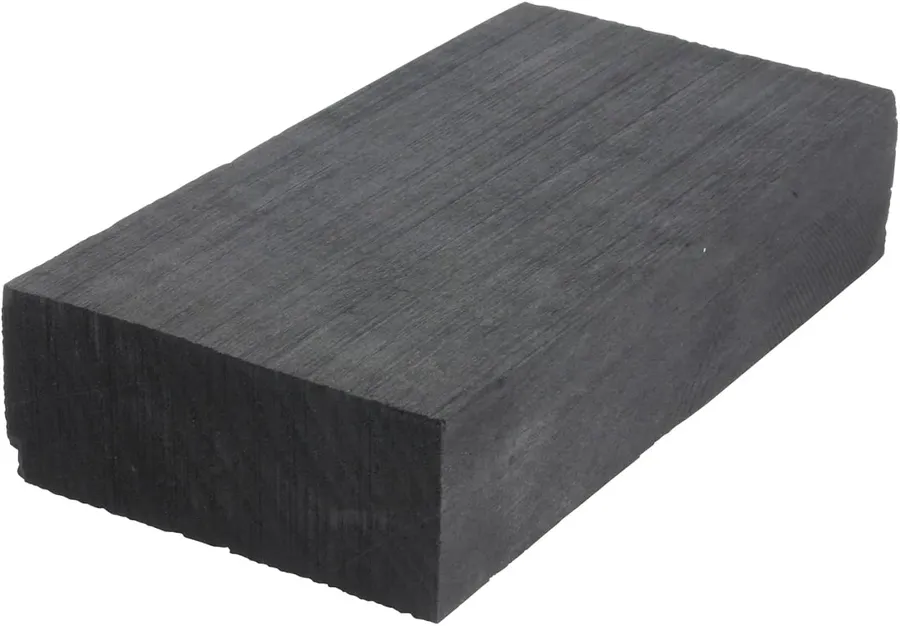
Charcoal soldering blocks are indispensable for specific metalworking applications, prized for their unique combination of heat resistance, anti-oxidation properties, and structural support capabilities. Unlike other soldering surfaces, charcoal blocks offer a reducing environment that minimizes scale formation during heating, crucial for maintaining the integrity of metals, especially during high-temperature processes.
The key advantage of using charcoal blocks lies in their porous structure. This allows for the dissipation of heat, reducing the risk of overheating localized spots on the work piece. Furthermore, they are not inert; the charcoal reacts with oxygen at high temperatures, creating a carbon monoxide atmosphere around the soldering area. This reduces the available oxygen, preventing oxidation of the metals being worked on, which would lead to brittle joints and a poor finish.
Charcoal blocks are not just for oxidation prevention. Their relative softness and ability to hold pins firmly make them ideal for supporting complex arrangements of metal components during soldering. This is particularly beneficial for intricate jewelry designs and larger metal pieces. In casting processes, charcoal blocks can be carved or shaped to create molds, which directly takes advantage of their capacity to withstand high temperatures.
Given these attributes, charcoal soldering blocks are primarily beneficial for tasks involving precious metals where preventing oxidation is paramount. They are also useful in casting processes where their mold-making capabilities are advantageous, and in scenarios that need a system of pins to hold complex geometries.
Solderite Boards: A Modern Alternative
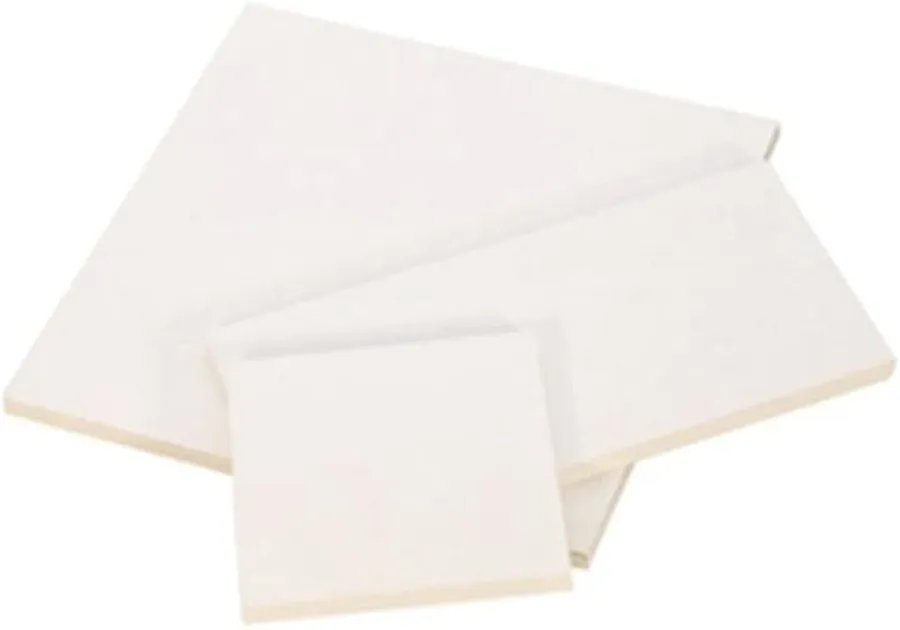
Solderite boards have emerged as a popular choice for soldering, particularly in contemporary applications, due to their unique combination of properties. Unlike traditional materials, Solderite offers a smooth, non-reactive surface coupled with excellent heat reflection and rapid cooling capabilities, thereby enhancing the efficiency and precision of soldering tasks. These characteristics make them a valuable asset in both hobbyist and professional settings.
- Smooth Surface
The smooth, non-porous surface of Solderite boards prevents solder from sticking, simplifying cleanup and ensuring the work-piece remains stable during soldering. This also minimizes the chances of contamination affecting the solder joint. - Superior Heat Reflection
Solderite material is designed to reflect heat effectively. This reflection ensures that the heat is directed back towards the work-piece, which in turn minimizes heat loss. Consequently, solder melts more quickly and evenly, resulting in stronger, more precise solder joints. - Rapid Cool Down
Unlike materials such as ceramic or charcoal, Solderite boards cool down rapidly after the heat source is removed. This rapid cooling not only improves workflow, but it also reduces the chances of accidental burns and enables faster manipulation of the soldered items. - Non-Reactive
Solderite boards are chemically inert and do not react with fluxes or metals commonly used in soldering. This characteristic prevents unwanted reactions that could compromise the strength or integrity of the soldered components. - Durability and Longevity
The composition of Solderite boards makes them highly durable and resistant to thermal shock. They can withstand repeated heating and cooling cycles without cracking or degrading, resulting in a long service life compared to other materials.
Soldering Board Sizes and Shapes: Finding Your Fit
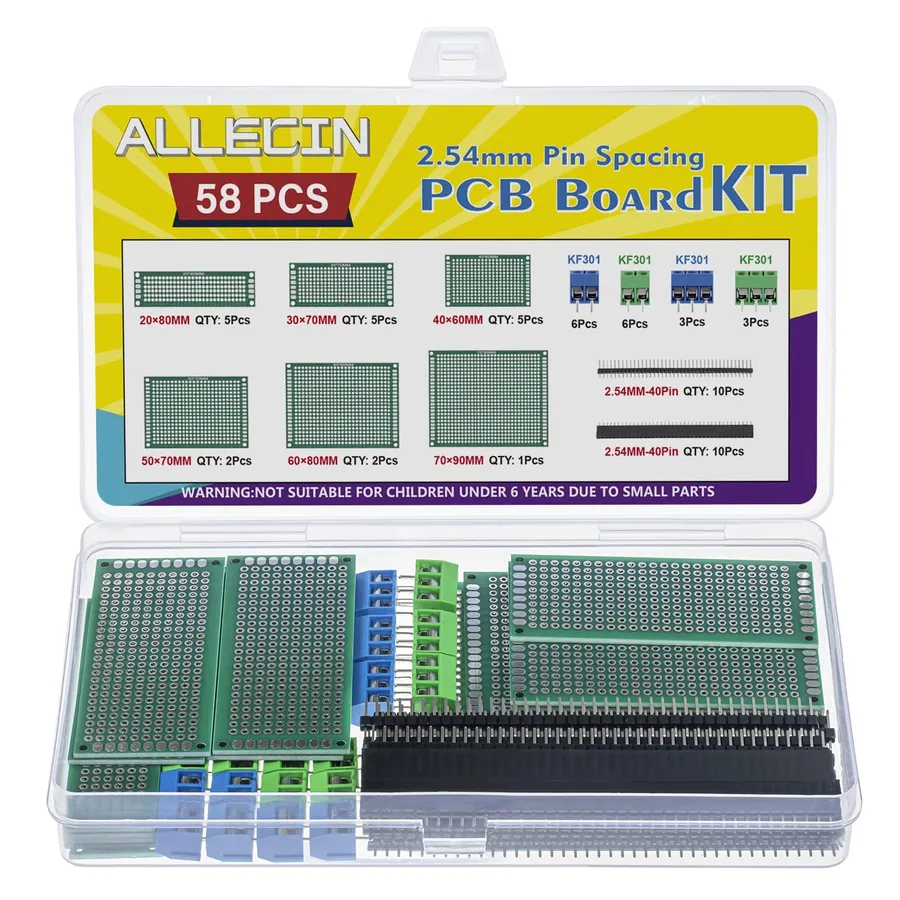
The dimensions and form of a soldering board significantly impact the efficiency and convenience of soldering operations. Selecting the appropriate size and shape tailored to the specific project requirements ensures optimal stability, accessibility, and workspace management. The right fit is crucial for consistent, high-quality solder joints.
Soldering boards come in a variety of sizes, typically ranging from small, handheld models suitable for intricate jewelry work to larger, more substantial boards designed for handling larger electronic assemblies or metalworking projects. The shape of a soldering board may be square, rectangular, circular or free-form to best support the type of work you do.
- Small Soldering Boards
Typically around 4"x6" and ideal for small electronic repairs, jewelry making or when working with small parts. - Medium Soldering Boards
Sizes around 6"x9" provide a good balance of space for most common soldering tasks, and allows space for a third hand tool to aid in assembly. - Large Soldering Boards
Board sizes of 9"x12" or larger offer ample workspace for larger projects or tasks involving multiple components.
When choosing a soldering board size, consider the following factors:
- Project Size
Match the board's dimensions to the size of the components or pieces being soldered. - Work Space
Ensure the board fits comfortably within the workspace without being too cumbersome. - Frequency of Use
A larger board may be beneficial if you frequently work with various projects. - Storage
Consider the ease of storage when not in use and ensure you have adequate space for the size of the board you choose.
In summary, the right size and shape of a soldering board greatly contribute to the comfort and effectiveness of the solderer. Thoughtful consideration of typical project dimensions and work environment will contribute to a more successful soldering workflow.
Soldering Board Accessories and Add-ons
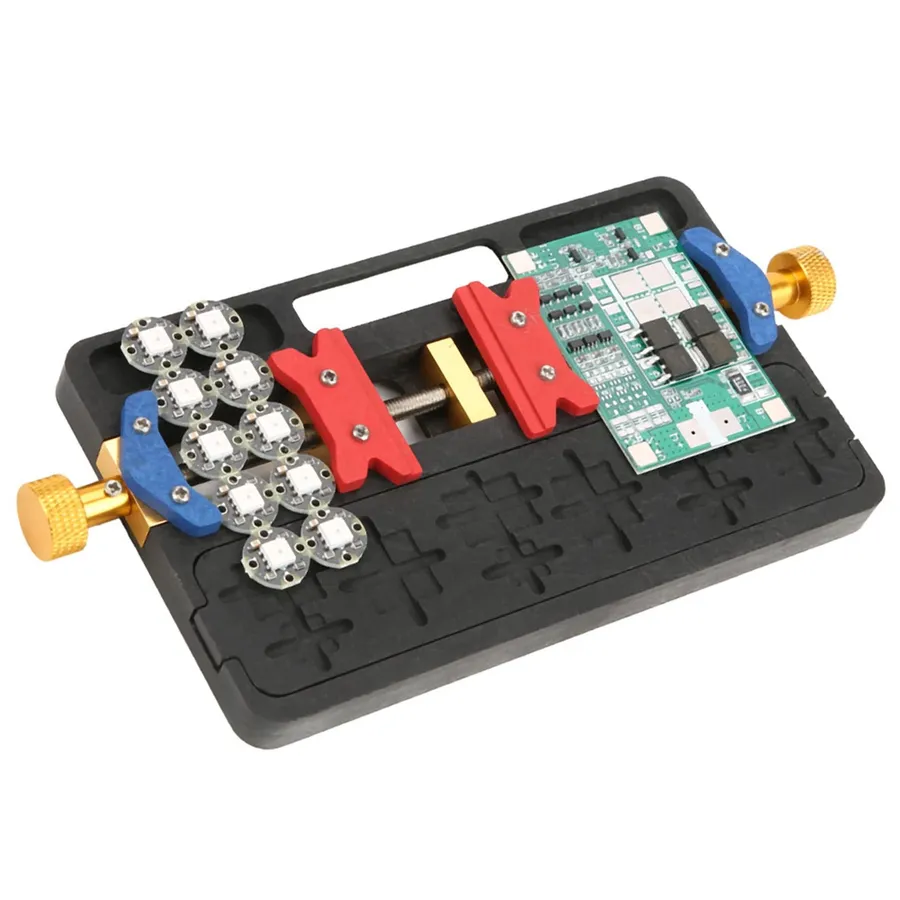
Enhancing the soldering process often involves more than just the board itself. The right accessories can significantly improve precision, stability, and overall workflow, transforming a basic setup into a professional soldering station. These add-ons are designed to address specific challenges, making intricate tasks easier and more consistent.
- Tripods
Tripods provide a stable, elevated platform for the soldering board, allowing for easier access and better visibility. They are particularly useful when working on complex projects or when multiple angles of access are required. Adjustable height tripods offer further flexibility, accommodating different working heights and preferences. Using a tripod will also prevent accidental contact between the heated board and the workbench. - Turntables
Turntables enable 360-degree rotation of the soldering board, allowing for easy manipulation of the workpiece without having to physically move the entire setup. This is invaluable for projects that require soldering from multiple angles or when working with circular components. Turntables are available in various sizes and materials, allowing one to choose according to the size of the work. - Pins
Pins, typically made from heat-resistant materials, are used to hold workpieces securely on the soldering board, preventing movement during the soldering process. They are extremely helpful with intricate solder jobs and where precision is key. Pins are available in various shapes and sizes and are sometimes used in conjunction with charcoal blocks to provide localized heat treatment. - Clamps
Clamps are used to secure larger workpieces to the soldering board, or to secure the board to the table. They can be a good alternative to pins in situations that require more robust holding force. They can also be used in combination with pins to ensure that the solder job does not move during the process. - Heat Shields
Heat shields are used to protect adjacent components or materials from excessive heat during soldering, preventing damage or melting. These shields can be made from metal, ceramics, or other heat resistant materials and are important for intricate soldering tasks in tight spaces.
Frequently Asked Questions About Soldering Boards
This section addresses common queries regarding soldering boards, focusing on alternative materials, safety measures, and the necessity of protective equipment. These answers are designed to provide practical guidance for users.
- What can I use as an alternative to a dedicated soldering board?
While a dedicated soldering board is recommended for optimal safety and performance, alternatives include firebricks, ceramic tiles, or even a thick piece of hardwood. However, it's crucial to consider the material's heat resistance to avoid damage or fire hazards. Ensure the alternative is stable, non-flammable, and can withstand the temperatures involved in soldering. - What surface is best to solder on?
The optimal soldering surface should be heat-resistant, stable, and provide good support. Dedicated soldering boards made of ceramic, charcoal, or Solderite are ideal. Avoid surfaces that are flammable, easily damaged by heat, or can reflect heat poorly. A stable, flat surface is critical for consistent solder joints. - Is it necessary to wear a mask while soldering?
Yes, wearing a mask during soldering is highly recommended, especially for tasks involving lead-based solder. Soldering can release harmful fumes that, upon inhalation, can pose significant health risks. A respirator or a mask with appropriate filters is essential to protect your respiratory system. - Can a regular brick be used as a soldering block?
While a regular brick might seem like a suitable alternative, it's generally not recommended. Bricks are not designed for soldering; they may not have consistent heat distribution, and can also crumble or crack under high heat conditions. Firebricks, specifically designed for high-temperature applications, are a safer choice if a dedicated soldering board isn't available. - Do I need to use a soldering board for every soldering project?
While not absolutely mandatory for all projects, using a soldering board is highly advisable. It ensures safety, provides a stable base, and helps achieve cleaner results. Especially for projects requiring consistent heat or involving heat-sensitive materials, a soldering board is essential. It protects your work area and improves precision. - What type of safety precautions should I take while soldering?
Safety precautions during soldering include wearing appropriate protective gear such as safety glasses, a respirator, and heat-resistant gloves. Work in a well-ventilated area to minimize fume inhalation, and keep flammable materials away from the soldering area. Proper grounding is also important when working with electrical soldering equipment. Having a fire extinguisher on hand is a prudent safety measure. - How do I prevent solder from sticking to the soldering board?
Most soldering boards are designed to prevent solder from adhering directly, especially ceramic and Solderite boards. For charcoal boards, using a dedicated flux can minimize the solder’s tendency to stick. Ensure your board is clean and free of debris to avoid any issues. If solder does stick, a gentle scraping motion with a tool can help remove it.
Comparing Soldering Board Types: A Practical Table
Selecting the appropriate soldering board is crucial for achieving optimal results and ensuring safety. This section provides a comparative analysis of different soldering board types, materials, and their respective applications, presented in a table format for easy reference. This comparison will assist users in making an informed decision based on their specific soldering requirements.
Board Type | Material | Heat Resistance | Durability | Surface Properties | Typical Use Cases | Advantages | Disadvantages |
---|---|---|---|---|---|---|---|
Ceramic | Ceramic Compounds | High (Up to 1300°C) | High | Smooth, Even | Jewelry Making, Small Electronics, High-Temperature Soldering | Excellent heat distribution, inert, resistant to thermal shock | Can be brittle, prone to cracking with impact |
Charcoal | Compressed Charcoal | High (Up to 1000°C) | Moderate | Porous, Heat Reflective | Metal Casting, Larger Soldering Pieces, Oxidation Prevention | Prevents oxidation, helps maintain even heat distribution , suitable for use with pins | Can be brittle, needs careful handling, produces dust, and not ideal for fine work |
Solderite | Proprietary Composite | High (Up to 1000°C) | Moderate | Smooth, Reflective | General Soldering, Electronics, Jewelry Making | Excellent heat reflection, smooth surface, rapid cool-down, lightweight | Less durable compared to ceramic and charcoal, can be sensitive to thermal shock |
Choosing the correct soldering board is vital for success in any soldering project, be it electronics or jewelry. By understanding the differences in materials like ceramic, charcoal, and Solderite, and considering factors like size, shape, and additional accessories, you can create a safer, more efficient, and precise soldering environment. Investing in the proper soldering board is an investment in the quality and outcome of your projects. Whether you’re a beginner or an experienced professional, having the right equipment, including a high-quality soldering board, can significantly enhance your soldering experience and results, ensuring your creations are not only well-made but also safe to produce.
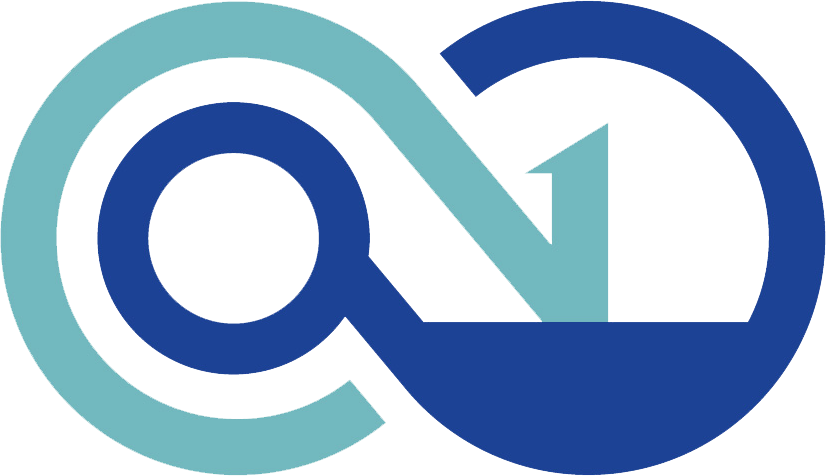