Decoding Custom Circuit Board Costs: A Comprehensive Guide
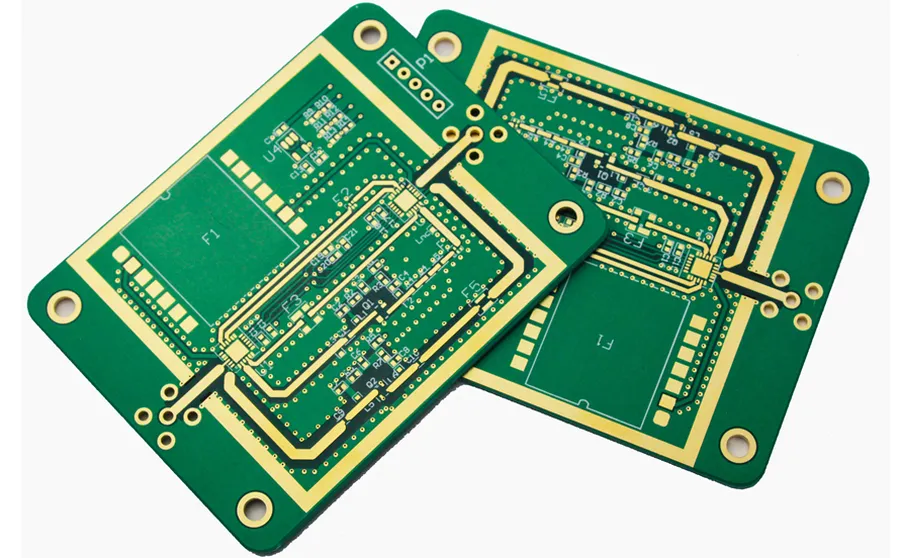
Custom circuit boards are the backbone of modern electronics, powering everything from smartphones to complex industrial equipment. But what exactly determines the custom circuit board cost? This article dives deep into the various factors that influence the price, guiding you through material choices, design complexity, production volume, and more. We’ll also explore practical tips to help you optimize costs and get the most value for your investment, making even the most complex electronic project financially accessible. Understanding these costs isn’t just about budgeting; it's about making informed decisions that can impact the success of your projects.
Key Factors Influencing Custom PCB Costs
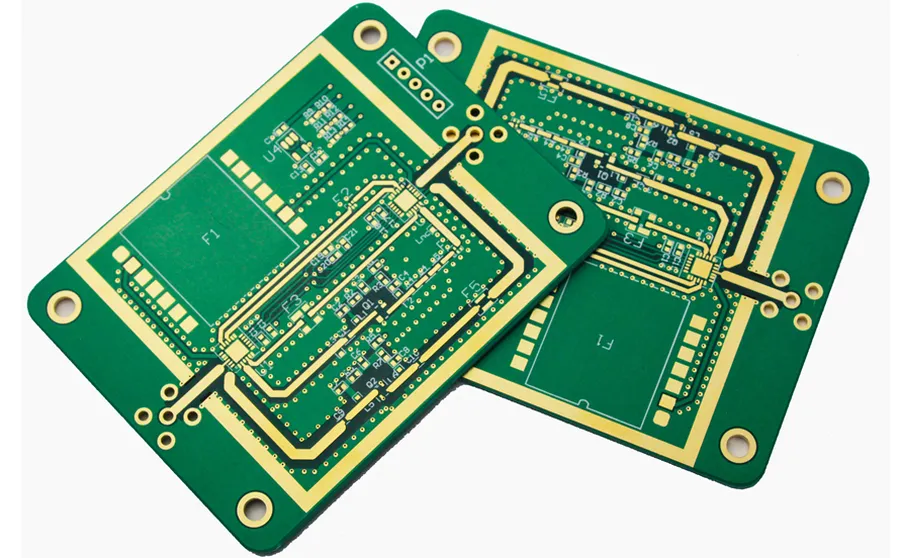
The cost of a custom circuit board is not a fixed figure; rather, it is a function of several interconnected variables. Understanding these key factors—namely, the physical dimensions of the board, the number of conductive layers it contains, the base materials employed, and the complexity of the circuit design—is crucial for accurate cost estimation and effective budget management. Each of these elements independently and collectively impacts the overall manufacturing expenses.
Factor | Description | Impact on Cost |
---|---|---|
Board Size | The overall area of the PCB. | Larger boards require more material, increasing cost. |
Number of Layers | The quantity of conductive layers (e.g., single, double, multi-layer). | More layers necessitate more complex fabrication, raising costs. |
Material Type | The base substrate material (e.g., FR-4, Rogers). | Specialized materials with superior properties command a higher price. |
Design Complexity | The intricacy of the circuit design, including trace widths, vias, and component density. | More complex designs demand greater manufacturing precision, increasing expenses. |
Material Choices and Their Impact on Cost
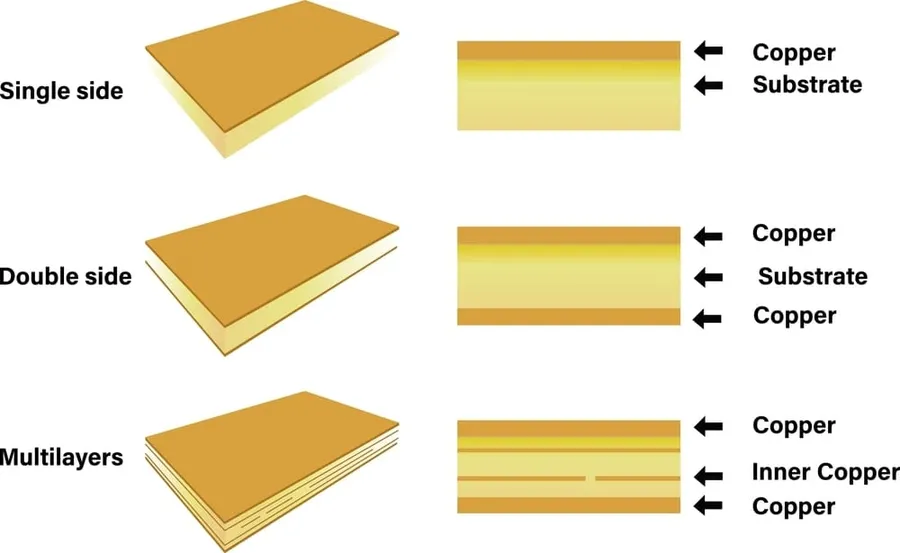
The selection of materials in printed circuit board (PCB) manufacturing is a critical determinant of both performance and cost. Different materials offer varying electrical, thermal, and mechanical properties, each with its own price point. Understanding these differences is crucial for optimizing cost and ensuring the PCB meets the application's specific demands.
Material | Properties | Typical Applications | Cost Implications |
---|---|---|---|
FR-4 | Good balance of electrical properties, mechanical strength, and cost. Flame retardant. Relatively easy to manufacture. | General purpose PCBs, consumer electronics, low-to-medium frequency applications. | Most cost-effective, widely available. |
Rogers | Superior electrical performance, lower signal loss, excellent thermal stability. Higher cost. | High-frequency applications, RF and microwave circuits, aerospace and defense systems. | Significantly more expensive than FR-4, requires specialized manufacturing. |
Metal Core PCB (MCPCB) | Excellent thermal dissipation capabilities, ideal for high-power applications. | LED lighting, power electronics, automotive applications where heat management is critical. | Moderately more expensive than FR-4, depends on the metal used. |
Polyimide | High temperature resistance, flexibility, good electrical properties. | Flexible circuits, high-temperature environments, aerospace. | Higher cost than FR-4, specialized manufacturing. |
CEM-1 | A composite material with paper and fiberglass, similar to FR-4 but lower in cost and performance | Less demanding applications, cost sensitive designs. | Lower cost alternative to FR-4 but with tradeoffs in performance. |
Beyond the primary substrate materials, other factors can influence cost, including the copper thickness, the type of surface finish, and specific treatments. For instance, heavier copper layers enhance current-carrying capacity but increase material usage and processing time, thus raising costs. Similarly, specialized surface finishes like ENIG (Electroless Nickel Immersion Gold) offer superior corrosion resistance and solderability compared to HASL (Hot Air Solder Leveling) but also come at a premium. When selecting materials, it's crucial to balance performance requirements with budgetary constraints. An engineer should consider material costs alongside factors such as the required reliability, lifespan, and environmental conditions to ensure that the optimal material choice is made.
PCB Design Complexity and Cost Implications
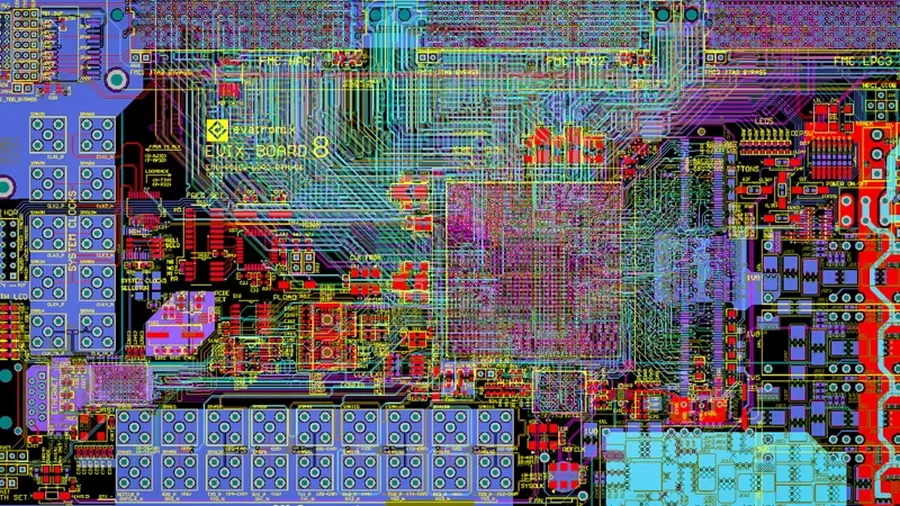
The complexity of a PCB design significantly influences its manufacturing cost. Intricate designs with a high density of components, multiple layers, and fine trace widths require more sophisticated manufacturing processes, leading to increased costs. Design choices directly impact the yield, time, and resources required, making it crucial to optimize for both functionality and cost-effectiveness.
Design Parameter | Cost Impact | Mitigation Strategies |
---|---|---|
Number of Layers | Increased cost with each additional layer due to material and processing needs. | Optimize layer count to meet required functionality, consider using blind and buried vias carefully. |
Trace Width and Spacing | Finer traces and spacing require more precision and can reduce yield, driving up costs. | Use wider traces and spacing where possible, optimize component placement to reduce trace density. |
Via Density | High via counts increase drilling time and complexity, impacting cost. | Minimize via usage by optimizing layer routing and using larger via sizes when possible. |
Component Density | Densely populated boards require more precise placement and soldering, increasing cost. | Use standard-sized components, avoid unnecessary complexity in component layout. |
Board Shape and Size | Complex or non-rectangular shapes add manufacturing complexity and increase material usage. | Use simpler board shapes, optimize board size for standard panel sizes of the manufacturer. |
Special Features (e.g., Impedance control, blind/buried vias) | These features require special manufacturing steps, increasing costs. | Only use these features if absolutely necessary for performance; consider less complex alternatives when possible. |
The Role of Production Volume in Pricing
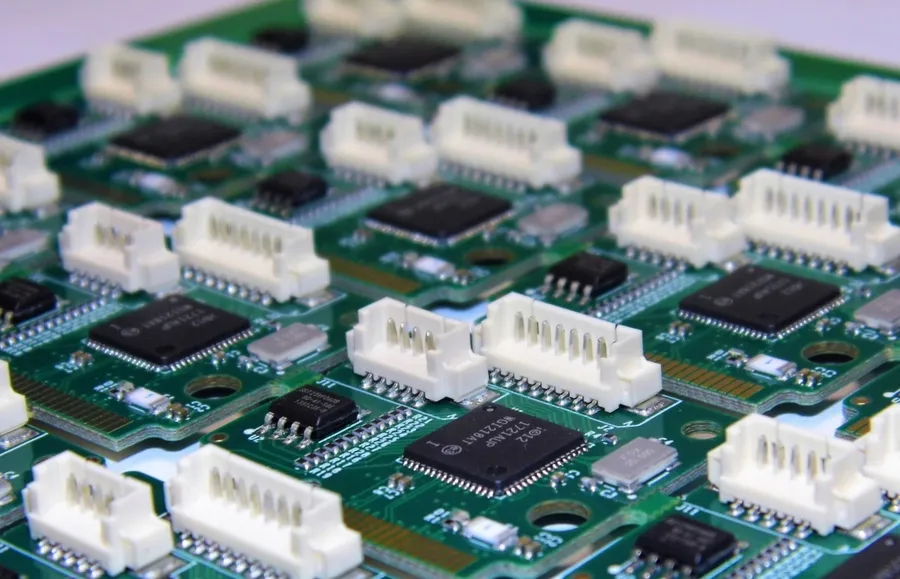
Production volume is a critical factor in determining the unit cost of custom circuit boards. The principle of economies of scale dictates that as the quantity of PCBs ordered increases, the per-unit price decreases significantly. This relationship is primarily due to the distribution of fixed costs, such as setup fees and tooling expenses, over a larger number of units.
Production Volume | Unit Cost Impact | Key Considerations |
---|---|---|
Prototyping (1-10 boards) | High per-unit cost | Initial setup costs dominate, used for testing and design validation. |
Small Batch (10-100 boards) | Moderate per-unit cost | Some cost reduction due to increased volume, suitable for early production runs. |
Medium Volume (100-1000 boards) | Decreasing per-unit cost | Economies of scale begin to impact, ideal for small to mid sized product launches. |
Large Scale (1000+ boards) | Lowest per-unit cost | Fixed costs are spread over many units, optimal for mass production. |
The following points will discuss the relationship between production volume and pricing:
- Initial Setup Costs:
These costs, including tooling, programming, and machine setup, are generally fixed and do not change significantly with order size. Therefore, spreading these costs over a larger production run significantly reduces the unit cost. - Material Procurement:
Purchasing materials in bulk often leads to discounts from suppliers. Manufacturers can secure lower material costs per PCB when dealing with larger orders. - Manufacturing Efficiency:
Larger production volumes allow manufacturers to optimize their processes. This increased efficiency leads to shorter production times and reduced labor costs per unit. - Reduced Handling and Shipping:
Handling and shipping are often more cost-effective when done in larger quantities. This can lower logistics costs per board. - Negotiating with Manufacturers:
Higher volume orders provide more leverage when negotiating with PCB manufacturers, which can lead to more favorable pricing.
Surface Finish Options and Cost Differences
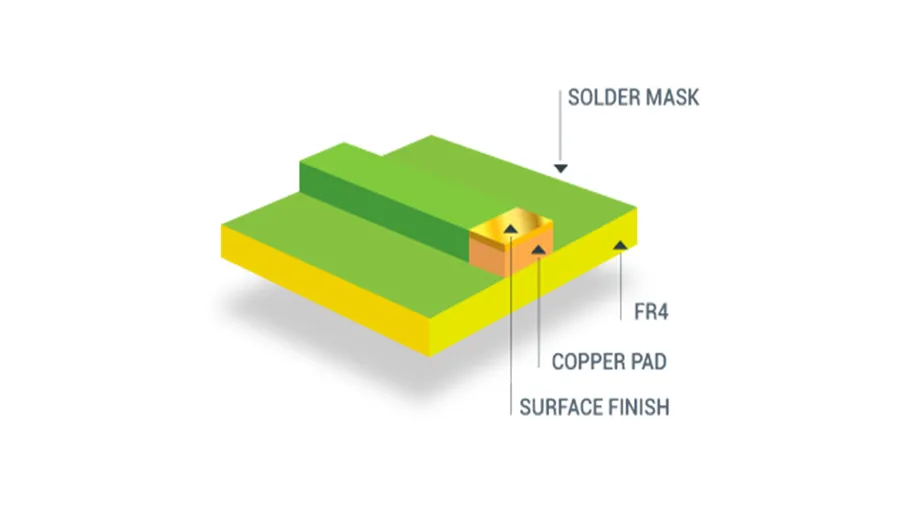
The surface finish of a printed circuit board (PCB) is a crucial factor impacting both its performance and cost. Different finishes offer varying levels of solderability, corrosion resistance, and overall reliability, directly influencing the final product's lifespan and effectiveness. This section details common surface finish options, their associated costs, and their performance characteristics.
Surface Finish | Description | Cost | Advantages | Disadvantages | Typical Applications |
---|---|---|---|---|---|
HASL (Hot Air Solder Leveling) | A process where the PCB is dipped in molten solder, and excess solder is removed by air knives. | Low | Cost-effective, good solderability, readily available. | Uneven surface, not suitable for fine-pitch components, contains lead (in leaded HASL). | General-purpose PCBs, through-hole components, prototype boards. |
Lead-Free HASL | Similar to HASL but uses lead-free solder. | Low-Medium | Better for the environment, good solderability. | Uneven surface, not suitable for fine-pitch components. | General-purpose PCBs, complying with RoHS. |
ENIG (Electroless Nickel Immersion Gold) | A two-layer coating of nickel followed by a thin layer of gold. | High | Excellent solderability, flat surface, good for fine-pitch components, good corrosion resistance. | Higher cost, can suffer from 'black pad' issue. | Fine-pitch components, wire bonding, high reliability applications. |
Immersion Tin | A thin layer of tin deposited chemically. | Medium | Good solderability, flat surface, good for fine-pitch components. | Tin whiskers can be an issue, requires careful handling. | Fine-pitch components, high-speed circuits. |
Immersion Silver | A thin layer of silver deposited chemically. | Medium-High | Excellent solderability, good for fine-pitch components and wire bonding. | Prone to tarnishing, requires careful storage, can migrate under moisture conditions. | High-frequency applications, components with specific performance demands |
OSP (Organic Solderability Preservative) | An organic coating that protects copper pads before soldering. | Low-Medium | Flat surface, good solderability, cost-effective, environmentally friendly. | Short shelf life, susceptible to damage and oxidation before soldering. | General-purpose PCBs, reflow soldering, cost-sensitive applications. |
When selecting a surface finish, it's essential to balance cost considerations with performance requirements. While cost-effective options like HASL may suffice for simple through-hole boards, more advanced finishes such as ENIG are necessary for complex designs that demand high reliability, fine-pitch components, and long-term performance. Understanding these trade-offs is critical for effective PCB design and manufacturing. Additionally, considerations such as environmental regulations (e.g., RoHS) can also influence the selection.
Comparing Costs: Prototype vs. Production
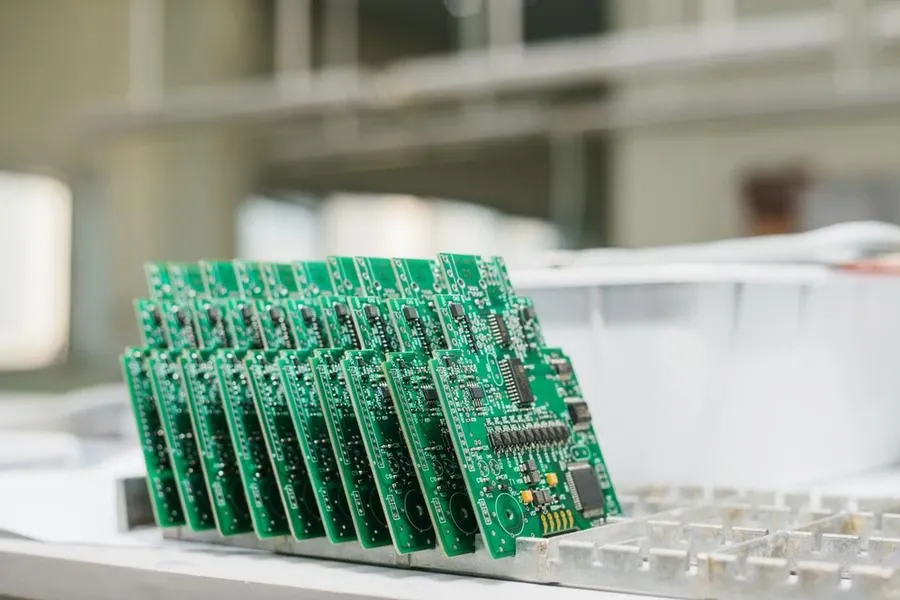
Understanding the cost variations between prototype and production runs is crucial for effective budgeting and project planning in custom circuit board manufacturing. Prototype runs incur higher per-unit costs due to initial setup expenses, while production runs benefit from economies of scale, significantly reducing the per-unit price.
Cost Factor | Prototype Run | Production Run |
---|---|---|
Setup Costs | High | Low (Amortized) |
Per-Unit Cost | High | Low |
Tooling Costs | High | Minimal |
Volume | Low | High |
Lead Time | Shorter | Longer |
Purpose | Testing and Validation | Mass Production |
The primary cost driver in prototype runs is the initial setup and tooling expenses. These costs include creating the necessary files, configuring machinery for a small batch, and potentially incurring extra charges for rapid turnaround. In production runs, these setup costs are spread over a larger number of units, drastically lowering the per-unit price. The tooling costs, which might be high for prototype runs, are minimal for production runs due to the use of existing and refined manufacturing processes.
Production runs benefit from economies of scale. As the number of boards increases, manufacturers can optimize their processes, leading to lower material costs and more efficient production methods. This efficiency translates to a significantly reduced per-unit price. However, production runs usually have longer lead times due to the large quantity being manufactured, whereas prototype runs prioritize quick turnaround for testing and validation.
The optimal choice between prototype and production runs hinges on the project's phase. Prototypes are critical for validating design and functionality before mass production. Production runs are the next step to mass produce and scale the project. Understanding the financial implication of each approach helps make well-informed decisions.
Frequently Asked Questions About Custom Circuit Board Costs
Understanding the cost of custom circuit boards can be complex, given the various factors at play. This section addresses common questions to clarify the pricing process and help you make informed decisions.
- How much does it cost to build a circuit board?
The cost to build a circuit board is highly variable, depending on factors such as the complexity of the design, the number of layers, the materials used, the board size, and the quantity produced. A simple, single-layer PCB in small quantities might cost a few dollars, while complex, multi-layer boards in larger production runs could cost hundreds of dollars each, even with economies of scale. The most accurate way to determine cost is to obtain a quote from a manufacturer, providing them with all the specific design and production requirements. - Why are custom PCBs so expensive?
Custom PCBs often appear expensive due to several underlying costs associated with their production. These include: the initial setup costs for tooling and design verification; the cost of specialized materials such as FR-4 or Rogers; the labor costs associated with complex design requirements; the precision manufacturing processes required to create fine circuit traces and vias; and the overhead associated with small production runs, which lack economies of scale. These factors, combined with quality assurance and testing, contribute to the overall cost of custom PCB production. - How much should a PCB cost?
Determining the “right” cost for a PCB is difficult, as it varies with the project specifications. For a simple prototype, costs may be higher on a per-unit basis because of setup fees. As the quantity increases for production runs, the per-unit cost typically decreases significantly, due to the amortization of the initial costs. To determine if you're receiving a fair quote, obtain several quotes from different manufacturers, and analyze them in terms of the board's complexity, the materials used, the production volume, and the turnaround time. Online PCB cost calculators can also provide a preliminary estimate. - Can I make my own circuit board?
Yes, it is possible to make your own circuit board, especially for simpler designs or prototype purposes. Common methods include using chemical etching or a CNC mill, as well as using transfer paper with a laser printer. However, DIY circuit board fabrication is typically limited in terms of precision, layer count, and materials. Complex designs or mass-production would be nearly impossible to achieve without specialized equipment and processes. For projects requiring high reliability and mass manufacturing, it's generally more efficient and cost-effective to use a professional manufacturer. - How does PCB size affect the cost?
The size of the PCB directly impacts the cost, as larger boards consume more materials and require more processing time. The cost of materials such as FR-4 or other substrates is directly proportional to the board size. Larger boards may also have a higher probability of defects, increasing the number of boards that have to be scrapped. For optimized cost, it is crucial to use only the necessary space on the PCB while considering design rules and the spacing of components, and also consider standard panel sizes. - Do more layers increase PCB costs?
Yes, increasing the number of layers on a PCB significantly increases the cost, since multilayer PCBs require more materials and more complex production processes. Additional layers also require alignment processes, electrical testing, and lamination, all adding to the overall cost. While multilayer PCBs provide higher density and better electromagnetic compatibility (EMC), the additional costs should always be justified by performance requirements. - What is the difference in cost between prototype and production PCBs?
Prototype PCBs often have higher per-unit costs than production PCBs, because the initial set-up costs like tooling and programming are amortized over a smaller number of boards. Production runs take advantage of these costs being divided over a large quantity of boards, resulting in lower per-unit costs. It's often advisable to start with a prototype run to debug and optimize a design before committing to a larger production run. This approach can lead to savings, because it allows you to correct any issues before significant money is invested.
Practical Tips for Reducing Custom Circuit Board Cost
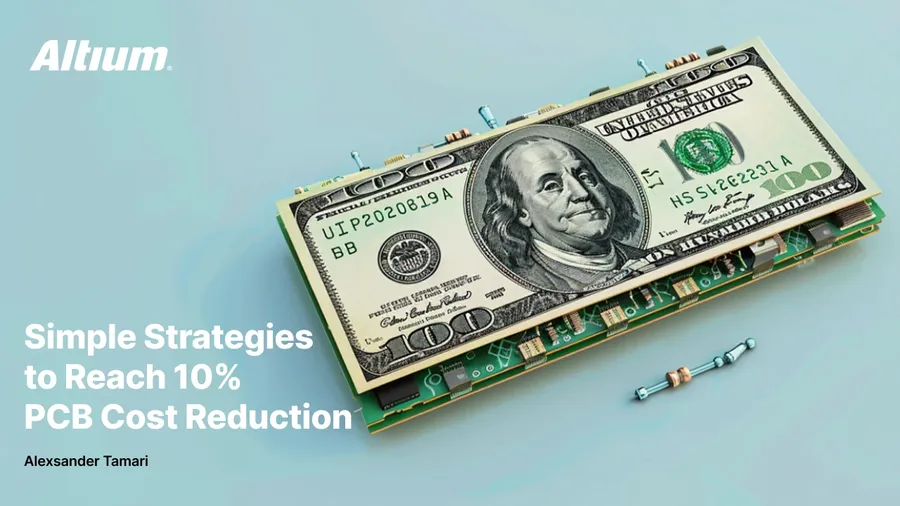
Reducing the cost of custom circuit boards requires a strategic approach that considers design, materials, and manufacturing processes. By optimizing these areas, you can significantly lower your expenses without sacrificing functionality or quality. This section provides actionable tips to achieve cost-effective PCB fabrication.
- Optimize Your PCB Design
Simplify your design by minimizing the number of layers, trace width, and vias. Every unnecessary feature adds to the cost. Use design rule checks (DRC) to identify potential issues before manufacturing. - Choose Cost-Effective Materials
FR-4 is often the most economical choice for many standard applications. While advanced materials like Rogers offer superior performance, they come at a higher price. Select materials that meet your project's performance requirements without overspending. - Panelize Your Design
If you are ordering multiple boards, panelize your design to maximize the usage of the manufacturing panel. This reduces the number of setup runs and can substantially reduce cost, especially for larger orders. - Standardize Component Selection
Opt for common, readily available components. Avoid custom or hard-to-source parts, which can increase procurement and manufacturing costs. Using common packages can help reduce manufacturing costs through streamlined processes. - Use Online PCB Cost Calculators
Before finalizing your design, utilize online cost calculators from various PCB manufacturers. These tools provide instant estimates based on your design specifications, allowing you to compare options and make informed decisions. These tools can also highlight design features that are driving up costs. - Plan for Production Volume
Consider your needs for production. Economies of scale apply here. Ordering in larger quantities can significantly reduce the per-unit cost. If your project allows, plan for future needs so that you can benefit from these cost reductions. - Consider Alternative Surface Finishes
While ENIG (Electroless Nickel Immersion Gold) provides excellent performance and durability, HASL (Hot Air Solder Leveling) is more economical and suitable for many applications. Consider HASL if your application does not require the superior finish or wire bond capability of ENIG.
Choosing the Right PCB Manufacturer
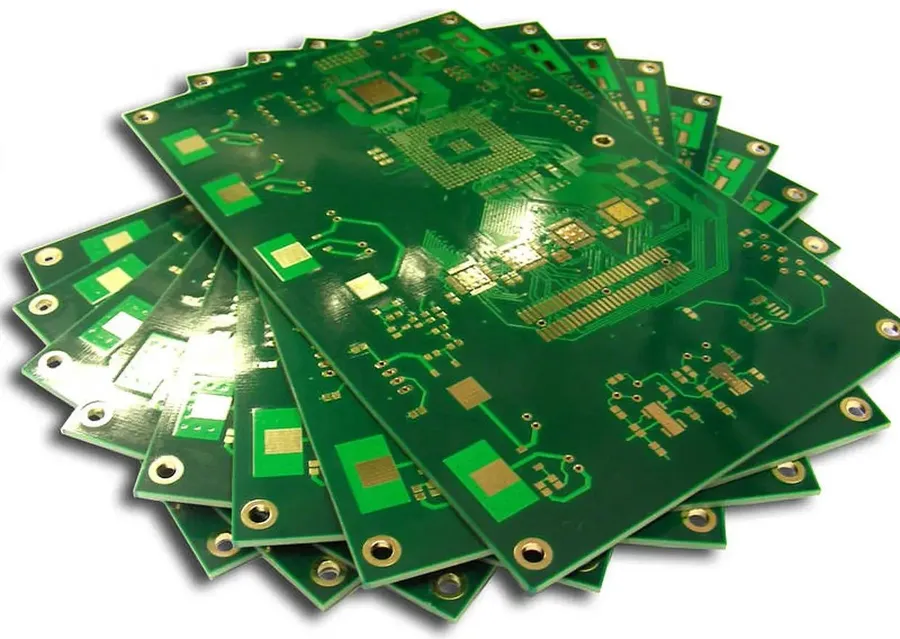
Selecting the appropriate PCB manufacturer is a critical step in ensuring the success of your project, balancing cost, quality, and timeliness. A dependable manufacturer not only provides competitive pricing but also offers the necessary support and expertise to handle the intricacies of your custom circuit board production.
When evaluating potential manufacturers, consider the following key criteria:
- Pricing
Assess cost structures, paying attention to hidden fees and shipping costs, and understand the impact of volume on pricing. - Turnaround Time
Ensure the manufacturer can meet project deadlines. Confirm their typical lead times for both prototype and production runs. - Quality Standards
Verify their certifications and adherence to industry standards such as IPC standards. Review samples and previous customer reviews to gauge the quality of their output. - Customer Support
Evaluate the responsiveness and technical capabilities of the manufacturer's support team to address any questions or issues that may arise during your project. - Manufacturing Capabilities
Confirm they can produce boards that meet the required specifications, including layers, materials, and surface finishes.
Leveraging online PCB cost calculators can provide a valuable starting point in assessing the cost of your custom circuit board. These tools allow you to input project-specific parameters and quickly generate an estimate. However, understand that these are estimates; contacting manufacturers directly for a tailored quote, especially for complex designs or large orders, is recommended.
By carefully evaluating manufacturer capabilities, comparing pricing, and utilizing estimation tools, you can make an informed decision, ensuring a cost-effective and high-quality outcome for your custom circuit board project.
Understanding the nuances of custom circuit board cost is essential for any electronics project. By carefully considering factors like materials, design complexity, and production volume, you can effectively manage expenses. Custom circuit board cost can range from a few dollars to hundreds, depending on your specific needs. By utilizing the tips and information provided in this guide, you can navigate these costs effectively, ensuring that your projects are both innovative and budget-conscious. Remember to leverage online PCB calculators for accurate estimates and to select a manufacturer that aligns with your project requirements, thus balancing quality and cost.
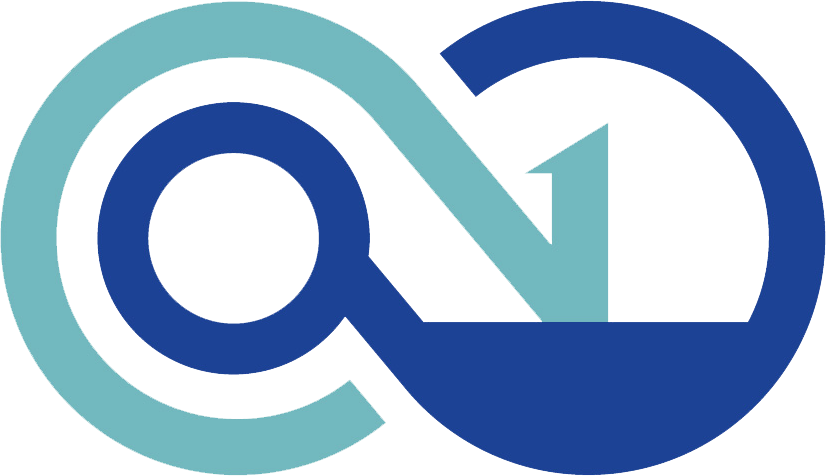