Decoding PCB 2: A Comprehensive Guide to 2-Layer Printed Circuit Boards
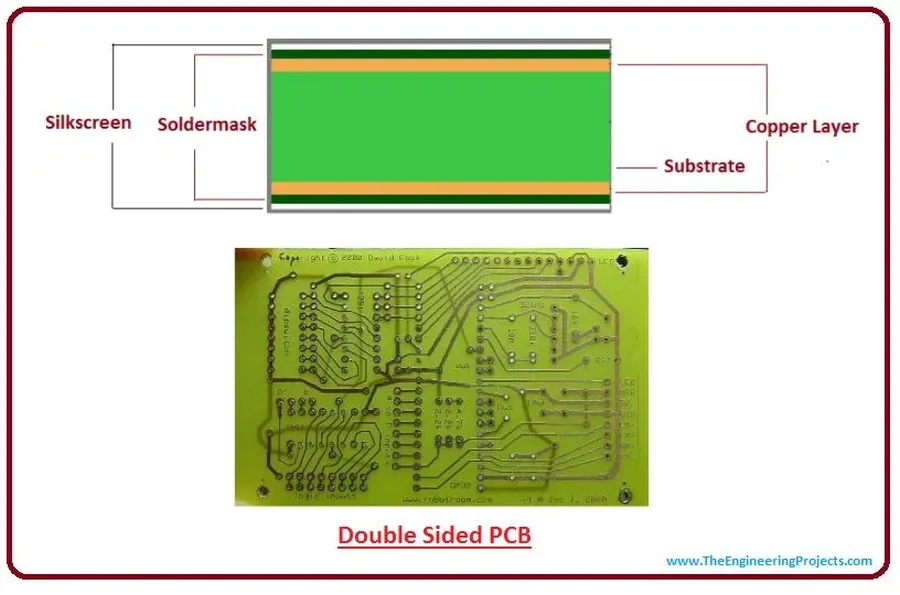
In our increasingly interconnected world, printed circuit boards (PCBs) form the backbone of nearly every electronic device. Among these, the PCB 2, or 2-layer PCB, stands out for its versatility and cost-effectiveness. This article delves into the intricacies of 2-layer PCBs, exploring their structure, design considerations, and applications, bridging the gap between technical complexity and everyday utility, and showing why they are still a mainstay of modern electronics.
What is a 2-Layer PCB?
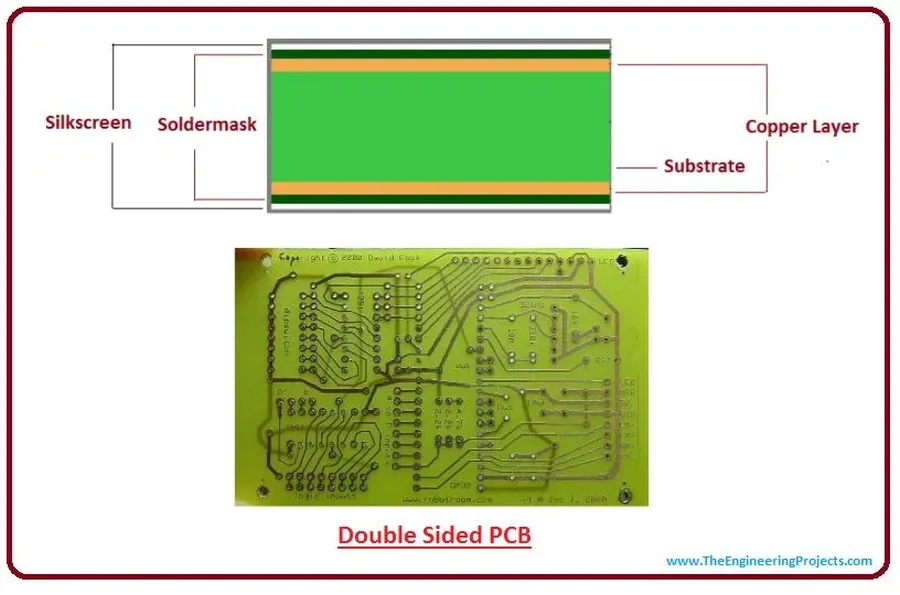
A 2-layer PCB, commonly known as a double-sided PCB, is a printed circuit board characterized by two conductive layers of copper, one on the top surface and another on the bottom, separated by a non-conductive substrate. This configuration enables the creation of relatively intricate electronic circuits while maintaining cost-effectiveness, making it a widely used choice in electronics manufacturing.
Key Components of a 2-Layer PCB
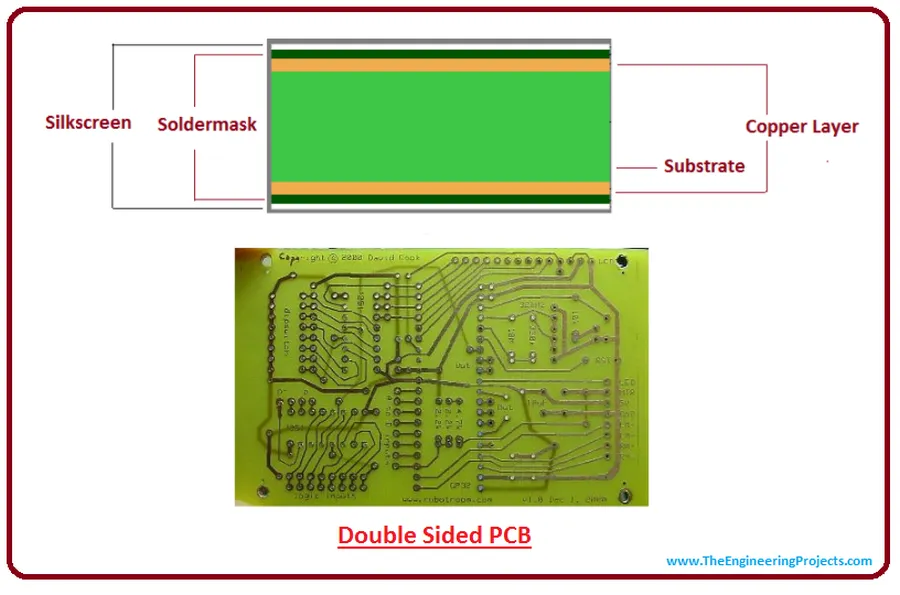
A 2-layer PCB's functionality is defined by its core components: the substrate, copper layers, vias, and solder mask. These components interact to form the structural and electrical basis of the circuit board, allowing for signal transmission and component mounting. Each element plays a crucial role in the overall performance and reliability of the PCB.
Component | Description | Function | Common Material |
---|---|---|---|
Substrate | The base material providing structural integrity. | Provides physical support, electrical insulation between layers. | FR4 (Flame Retardant 4) |
Copper Layers | Thin sheets of copper adhered to the substrate. | Conducts electrical signals and power. | Electrolytic Copper |
Vias | Plated holes connecting top and bottom copper layers. | Enables electrical connections between layers. | Copper-plated through-hole |
Solder Mask | A protective layer applied over the copper. | Prevents solder bridges and protects copper traces. | Epoxy or Liquid Photoimageable (LPI) Solder Mask |
2-Layer PCB Manufacturing Process

The manufacturing of a 2-layer PCB involves a series of precise steps, each critical to the final functionality and reliability of the board. This process transforms a digital design into a physical circuit capable of performing its intended purpose. Key stages include schematic creation, copper etching, via drilling, solder mask application, and silkscreen printing.
- Schematic Design and Layout
The process starts with creating a detailed schematic of the circuit. Once the schematic is finalized, the layout of the components and traces is designed. This includes determining the arrangement of components and the paths for electrical signals on the two copper layers. - Copper Layer Etching
Copper layers are selectively etched to form the traces that connect components. A photoresist process is used, where a UV-sensitive material is applied to the copper and exposed through a mask of the circuit design. The exposed areas are chemically etched away, leaving behind the desired circuit pattern. - Via Drilling
Vias, small holes that allow electrical connection between the top and bottom copper layers, are drilled using precision machinery. These vias are typically plated with copper to ensure good electrical conductivity between layers. - Solder Mask Application
A solder mask, usually green, is applied to the board. The solder mask prevents solder from bridging between pads during the soldering process and protects the copper traces from oxidation. - Silkscreen Printing
Finally, a silkscreen is printed on the PCB, which contains reference designators, component outlines, and other useful markings that assist in assembly and debugging.
Manufacturing Step | Purpose | Key Considerations |
---|---|---|
Schematic & Layout | Defines the circuit and arrangement of components and traces | Component placement, trace widths, signal integrity |
Copper Etching | Creates conductive paths on the board | Etch precision, trace dimensions, impedance control |
Via Drilling | Enables electrical connection between layers | Via diameter, plating quality, reliability |
Solder Masking | Prevents solder bridges and protects traces | Proper alignment, material type, coverage |
Silkscreen Printing | Adds component markings, and other references | Clarity, readability, position accuracy |
Advantages of Using 2-Layer PCBs
2-layer PCBs, characterized by conductive copper layers on both sides of an insulating substrate, offer distinct advantages, notably in cost-effectiveness and simplicity. These attributes make them a foundational choice for numerous electronic applications, especially where complexity is not paramount.
- Cost-Effectiveness
The reduced complexity of 2-layer PCBs directly translates to lower manufacturing costs. Fewer layers mean less material usage, simpler fabrication processes, and reduced production time. - Design and Manufacturing Simplicity
Designing and manufacturing 2-layer PCBs involves fewer steps compared to their multilayer counterparts. This simplicity reduces the potential for errors and accelerates the overall production cycle, making them more accessible to manufacturers and designers. - Rapid Prototyping
The straightforward design and manufacturing of 2-layer PCBs allow for quicker prototyping. This is especially useful in early-stage product development when design iterations are frequent. - Shorter Lead Times
Due to simpler processes, 2-layer PCBs generally experience shorter lead times from design to production, which is critical for time-sensitive projects. Quicker turnaround facilitates faster product launches and reduced project development cycles. - Ideal for Low-Complexity Designs
For applications where high signal density and complex routing are not needed, 2-layer PCBs offer an ideal solution that is both cost-effective and technically adequate. Their suitability for simpler designs avoids unnecessary complications and costs.
Feature | 2-Layer PCB | Multilayer PCB |
---|---|---|
Cost | Lower | Higher |
Design Complexity | Simpler | More Complex |
Manufacturing Time | Shorter | Longer |
Signal Density | Lower | Higher |
Prototyping Speed | Faster | Slower |
Applications of PCB 2
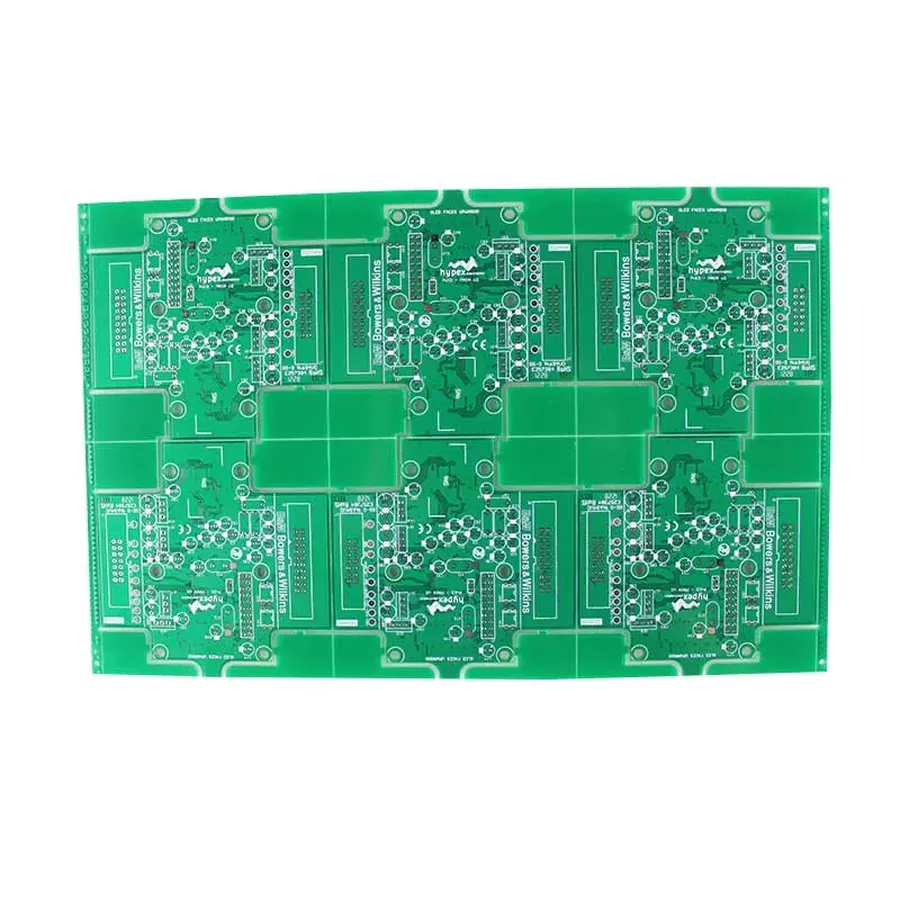
2-layer PCBs, owing to their balance of cost-effectiveness and design simplicity, are integral to a diverse range of electronic applications. Their versatility allows them to be employed in both basic consumer devices and more complex industrial control systems.
- Consumer Electronics
Found in numerous household gadgets such as remote controls, simple audio devices, and LED lighting systems. - Power Supplies
Frequently used in power adapters and chargers for a variety of electronic devices. - Sensor Interfaces
Utilized as sensor interface boards for temperature, pressure, and other environmental monitoring devices. - Basic Electronic Modules
Used for basic modules in electronic circuits, such as amplifiers, simple logic circuits, and small control boards. - Automotive
Employed in basic automotive electronics, such as indicators and simple control modules. - Industrial Controls
Used in less complex industrial control units where high density and signal integrity aren't critical factors.
Design Considerations for PCB 2
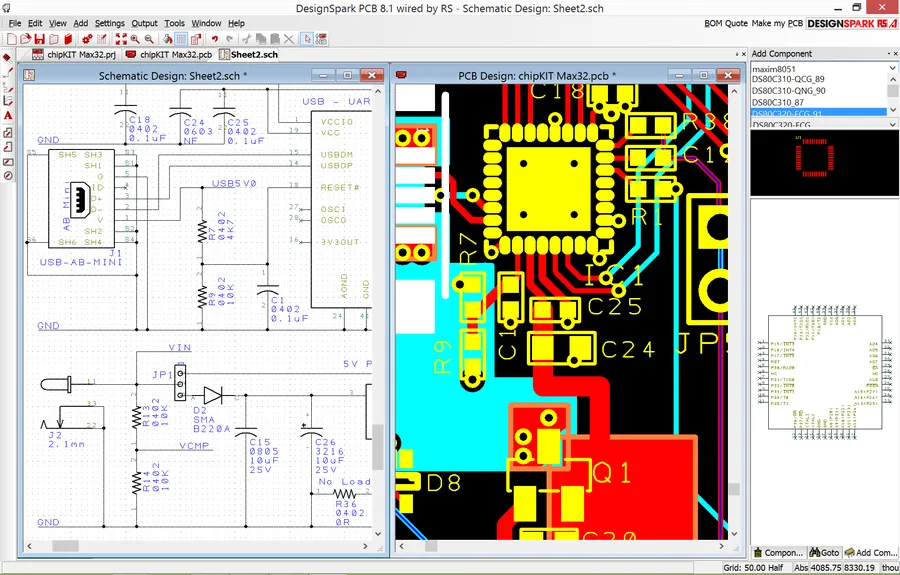
Effective design of 2-layer PCBs requires careful attention to several interconnected factors. These considerations are paramount to ensure the manufactured board operates reliably, avoids signal integrity issues, and fulfills its intended function. Key aspects involve trace geometry, layer stack-up, via implementation, thermal considerations, and adherence to established design guidelines.
Design Parameter | Description | Impact | Design Rule Best Practices |
---|---|---|---|
Trace Width and Spacing | Width and spacing of copper traces on the board. | Affects current carrying capacity, impedance, and crosstalk. | Use appropriate width for current needs and maintain adequate spacing between traces |
Layer Stack-up | The arrangement of the substrate and copper layers. | Determines impedance control and signal routing. | Select proper layer order to achieve controlled impedance. |
Via Placement | The location of vias (holes that connect layers). | Impacts signal routing and can cause signal integrity problems. | Place vias strategically and minimize their number |
Thermal Management | How heat is dissipated by components on the board. | Critical for board longevity and performance. | Provide adequate copper area around heat-generating components. |
Design Rules & Best Practices | Established guidelines for PCB design. | Ensures reliable manufacturing and function. | Adhere to industry standards and manufacturer recommendations. |
Layout Planning | The physical organization of components and routing. | Prevents interference and crosstalk. | Strategically position components to minimize signal interference. |
2-Layer PCB vs. Multilayer PCB
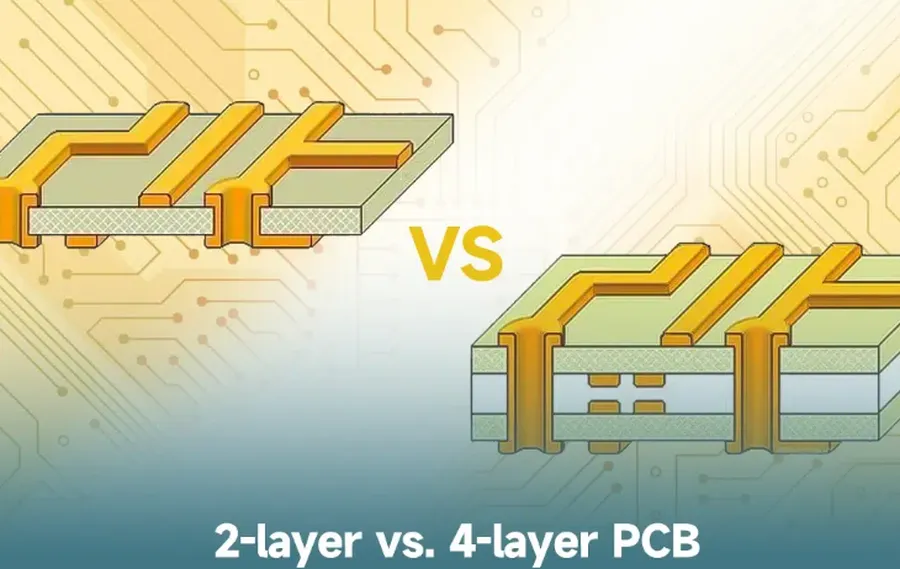
The selection between a 2-layer PCB and a multilayer PCB is a critical decision in electronic design, dictated by the complexity and performance needs of the project. While 2-layer PCBs excel in cost-effectiveness and simplicity, multilayer PCBs offer enhanced density and signal integrity required for more sophisticated applications.
Feature | 2-Layer PCB | Multilayer PCB |
---|---|---|
Complexity | Suitable for simpler designs | Handles complex designs |
Density | Lower component density | Higher component density |
Signal Integrity | More susceptible to noise and interference | Better signal integrity due to internal layers |
Cost | Lower manufacturing cost | Higher manufacturing cost |
Layer Count | Fixed at two conductive layers | More than two conductive layers |
Design Time | Faster and simpler design process | Longer and more complex design process |
Applications | Suitable for basic electronics and low-speed circuits | Suitable for high-speed, high-density, and complex circuits |
The key differentiation lies in the number of conductive layers, with multilayer PCBs utilizing three or more layers. This increased layer count enables designers to route more signals, accommodate higher component densities, and achieve better impedance control, critical for high-speed applications.
Ultimately, the choice depends on a careful evaluation of project requirements, balancing performance needs, cost constraints, and design complexity. If a straightforward circuit design is needed without high density needs or complex signal requirements, then a 2-layer board is sufficient, but if more complex needs exist, then a multilayer is necessary.
Frequently Asked Questions About 2-Layer PCBs
This section addresses common questions regarding 2-layer printed circuit boards (PCBs), providing clear and concise answers to assist in your understanding and application of this technology. These FAQs are designed to cover key aspects from basic definitions to design considerations.
- What does a 2-layer PCB mean?
A 2-layer PCB, or double-sided PCB, features conductive copper layers on both the top and bottom surfaces of an insulating substrate. This allows for routing of electrical signals on both sides, increasing design flexibility and component density compared to single-layer PCBs. These are cost-effective and widely utilized in various electronic applications. - Why is PCB testing important?
PCB testing is critical to ensure the reliability and functionality of electronic devices. Testing verifies that the PCB's design matches the intended circuit, that components are correctly mounted, and that there are no manufacturing defects. Common tests include visual inspections, electrical tests and functional tests that guarantee proper operation and longevity of the product. - How can I ensure a proper design for a 2-layer PCB circuit?
Ensuring a proper design involves adhering to design rules and best practices, such as appropriate trace width and spacing for the current load and signal integrity, impedance matching and controlling, proper thermal management and via design to minimize interference and cross talk. Additionally, meticulous attention to the schematic, component placement and careful routing are essential to a functional design. It is also advisable to have a design rule check (DRC) performed by your PCB CAD software. - What are some common errors in 2-layer PCB design?
Common errors include inadequate trace width and spacing leading to overheating or signal issues, improper via placement resulting in connection problems, insufficient thermal management, incorrect component footprint selection, and ignoring design rules. Lack of ground plane or improper component placement can create interference and noise and improper layer stack up can result in the circuit not working at all. - What are typical applications for 2-layer PCBs?
2-layer PCBs are commonly used in applications where the complexity and density requirements are moderate. Examples include consumer electronics, power supplies, sensor interfaces, simple control systems and basic electronic modules. Their cost effectiveness makes them suitable for many mass production applications where cost is a primary consideration. - What are the limitations of 2-layer PCBs compared to multilayer PCBs?
Compared to multilayer PCBs, 2-layer PCBs have limitations in terms of routing complexity, component density, and signal integrity due to the limited number of layers and thus routing tracks. High-speed signal routing and applications requiring multiple power and ground layers are generally better suited to multilayer designs. However for basic and cost sensitive designs 2-Layer PCBs are adequate. - How does the cost of 2-layer PCBs compare to multilayer PCBs?
Generally, 2-layer PCBs are more cost-effective than multilayer PCBs because of their simpler manufacturing process and lower material usage. The cost difference can be significant, particularly for large volume production. However, the choice between 2-layer and multilayer should be based on design requirements and performance needs rather than cost alone.
Cost of 2-Layer PCBs and Sourcing
The cost of 2-layer PCBs is influenced by several factors, including material selection, board size, complexity of the design, production volume, and the chosen manufacturer. Balancing these factors is essential to achieve a cost-effective solution without compromising quality and desired lead times.
Cost Factor | Description | Impact on Cost |
---|---|---|
Material | Type of substrate (e.g., FR4, CEM-1), copper thickness | Higher-grade materials or thicker copper increase cost |
Board Size | Physical dimensions of the PCB | Larger boards require more material and processing, thus higher cost |
Design Complexity | Number of vias, trace density, and board outline shape | More complex designs increase fabrication time and cost |
Production Volume | Number of PCBs to be manufactured in a single batch | Higher volumes typically result in a lower per-unit cost due to economies of scale |
Manufacturer Location | Labor costs, facility overheads, and shipping costs | Manufacturers in certain regions might offer lower prices, but this could affect lead times or quality |
Surface Finish | Type of coating applied to the copper pads (e.g., HASL, ENIG) | Certain finishes provide enhanced performance or corrosion resistance but may add cost |
Sourcing the right PCB manufacturer is as important as design considerations. Consider the following:
- Quality Standards
Ensure the manufacturer complies with industry standards such as IPC (Association Connecting Electronics Industries). Certifications like ISO 9001 are indicators of a commitment to quality. - Capabilities
Assess whether the manufacturer can handle your PCB's specifications, including layer count, via types, and impedance control requirements, as well as minimum track widths. - Cost Transparency
A detailed quotation that breaks down the cost of materials, labor, and any other charges. Avoid manufacturers who give unclear quotations that can lead to hidden fees. - Lead Times
Understand the production and delivery schedule. Quick turnarounds may come at a premium. Confirm they have the capacity to deliver the required quantity within your timeline. - Communication and Support
A responsive customer support team is crucial for addressing any questions or concerns during the manufacturing process. Do they offer engineering support for DFM (Design for Manufacturability)? - Customer Reviews and Reputation
Seek feedback from other customers, and evaluate the manufacturer's standing within the industry to assess reliability and quality.
PCB 2, the 2-layer PCB, remains a fundamental element in the electronics industry due to its balance of simplicity, cost-effectiveness, and reliability. Understanding their design, fabrication, and applications enables both seasoned and novice engineers to create efficient and robust electronic systems. By considering all factors, PCB 2 can serve as the foundation for diverse electronic devices. This guide provides a roadmap for successfully implementing 2-layer PCBs in your next project and emphasizes their continued importance in modern electronics.
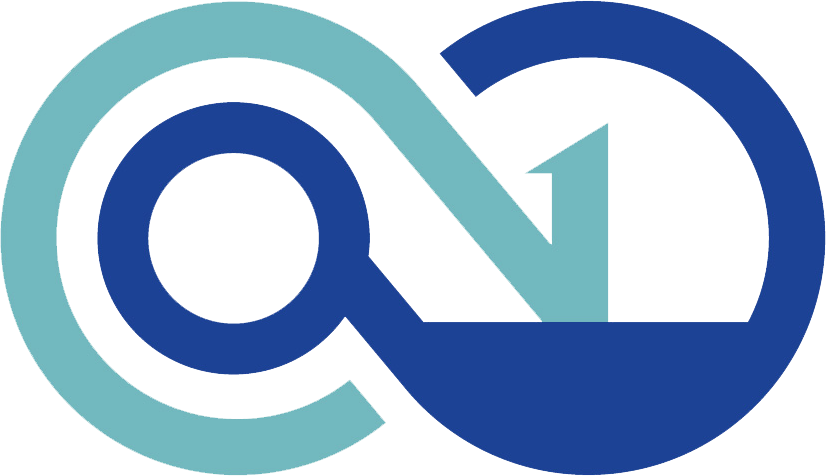