Inverter PCB Board Price Guide: Factors, Types & Cost Analysis
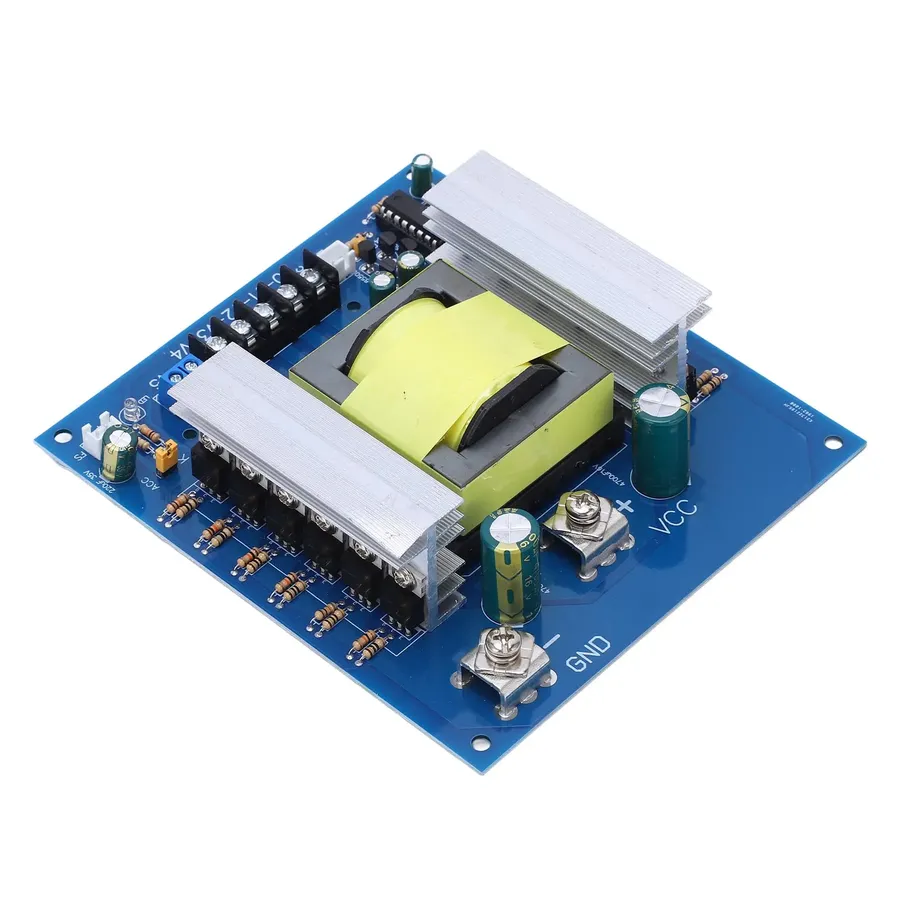
In our increasingly power-dependent world, inverter PCB boards play a pivotal role in converting DC power to AC, powering everything from our homes to industrial machinery. But, what factors influence the price of these vital components? In this article, we’ll dissect the intricacies of inverter PCB board pricing, guiding you to make informed decisions when purchasing this essential technology, highlighting the key elements that affect the cost of an inverter PCB board, and providing a clear understanding of what you should be paying, covering everything from raw material costs to manufacturing processes.
Understanding Inverter PCB Board Functionality
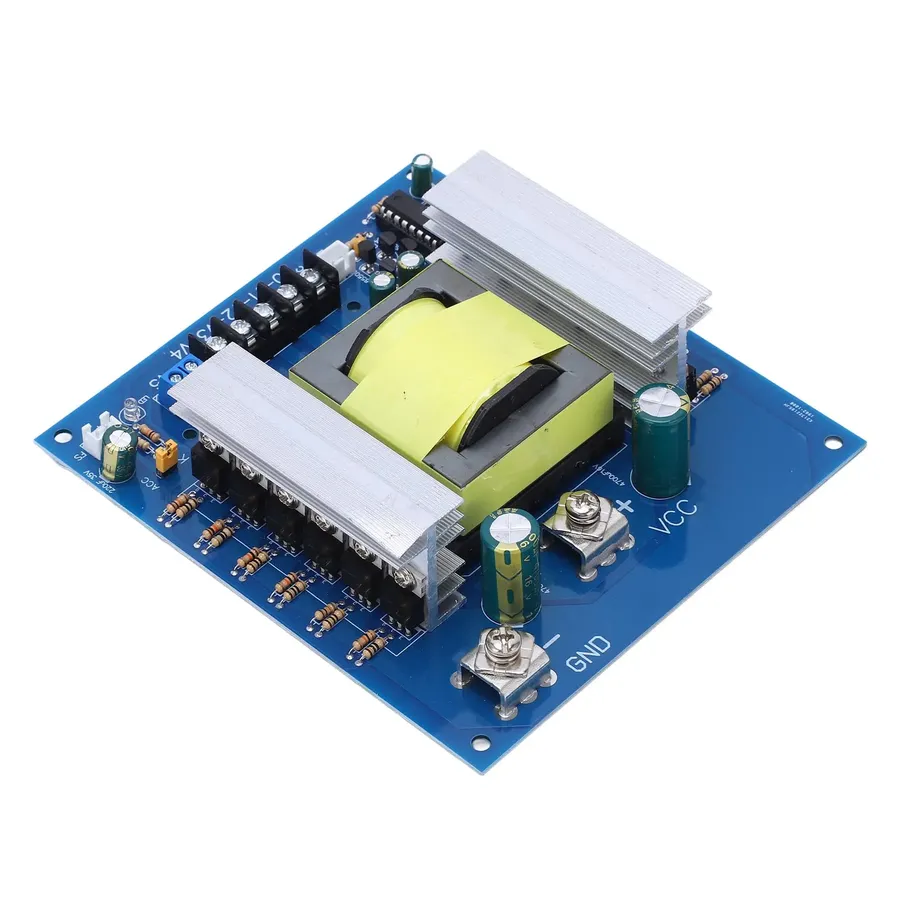
Inverter PCB (Printed Circuit Board) boards are fundamental components in electronic systems, primarily tasked with converting direct current (DC) power into alternating current (AC) power. This conversion is crucial for enabling various devices to operate from battery sources or DC power supplies, thus extending their utility and applicability.
At the heart of an inverter PCB board lies a sophisticated arrangement of electronic components such as semiconductors (transistors, MOSFETs, IGBTs), capacitors, inductors, and resistors. These components, precisely positioned on the PCB, work in concert to efficiently transform DC input into a usable AC output with controlled voltage and frequency characteristics.
- Power Conversion:
The core function of an inverter PCB is to convert DC power into AC power, which is essential for operating appliances, lighting systems, and other AC-powered devices from DC power sources such as batteries or solar panels. - Frequency Control:
Inverters not only convert power but also modulate the output frequency. This control is paramount for sensitive electronic equipment, ensuring stable and reliable operation. - Voltage Regulation:
A key feature of inverter PCBs is their ability to regulate the output voltage, ensuring a consistent supply regardless of fluctuations in the input DC voltage, which is vital for maintaining optimal performance and prolonging the lifespan of connected devices. - Protection Mechanisms:
Inverter PCB boards are designed with built-in protection circuits against overcurrent, overvoltage, short circuits and thermal overload, safeguarding the board and connected equipment from potential damage and increasing the overall reliability of the system.
The versatility of inverter PCBs extends across a wide array of applications, including renewable energy systems (solar inverters), uninterruptible power supplies (UPS), variable frequency drives (VFDs) for motors, and numerous portable electronic devices. The design and complexity of the inverter PCB are tailored to the specific requirements of its application, impacting its performance, size, and ultimately its price.
Key Factors Influencing Inverter PCB Board Prices
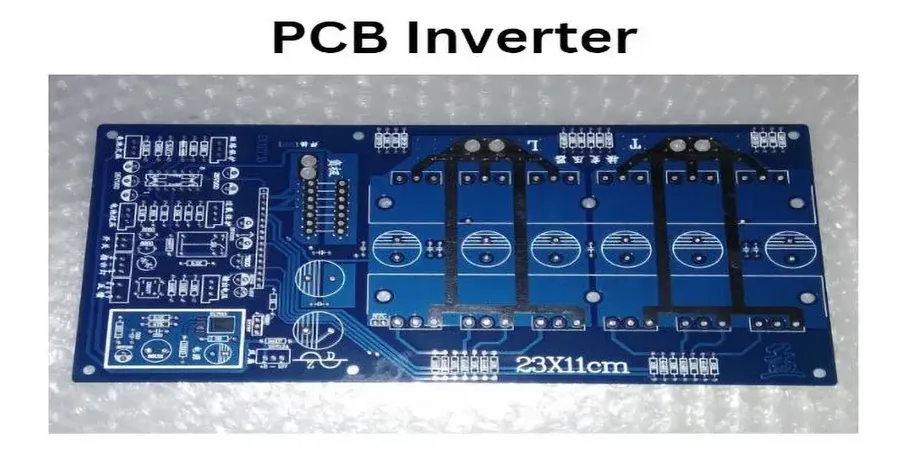
The price of an inverter PCB board is determined by a confluence of factors, primarily stemming from the materials used, the design complexity of the circuit, and the production scale. These elements interact to establish the final cost of the board.
- Material Composition
The type and quality of materials significantly impact the price. High-performance substrates like Rogers or Teflon are more expensive than standard FR-4 due to their superior electrical and thermal properties. Similarly, the grade of copper used for conductive traces affects the board's performance and cost. - Design Complexity
Inverter PCB design complexity plays a significant role in pricing. This includes the number of layers, the density of components, the presence of fine-pitch components, and the need for impedance matching. More complex designs necessitate more intricate fabrication processes, thereby increasing costs. For instance, a multi-layer board with blind and buried vias will cost more to manufacture than a single or double-sided board. - Component Sourcing
The cost of the components populated on the PCB, such as microcontrollers, power MOSFETs, and capacitors, can significantly affect the overall cost of the final product. Premium grade components with stricter tolerances and higher performance usually command a higher price. Furthermore, market dynamics of these components can cause fluctuating prices. - Production Volume
The scale of production is a major factor in price per unit, and follows the economic principle of economies of scale. Larger production runs will reduce the per-unit cost by spreading the initial setup and tooling costs over more units. Small batch production can cost significantly more due to fixed manufacturing costs. - Manufacturing Processes
The manufacturing processes used during production can also affect the price. Advanced fabrication processes such as fine line etching, controlled impedance, and specific surface finishes may add to the cost. The use of automated manufacturing vs. manual assembly will also affect costs. - Testing and Quality Control
Rigorous testing protocols and stringent quality control measures also contribute to the price of an inverter PCB. More comprehensive testing, including in-circuit testing and functional testing, increase manufacturing costs.
Factor | Impact on Price |
---|---|
High-Performance Materials | Higher |
Complex Multi-Layer Design | Higher |
Premium Components | Higher |
Large Production Volume | Lower per unit |
Advanced Manufacturing Processes | Higher |
Stringent Testing | Higher |
Types of Inverter PCB Boards and Their Price Ranges
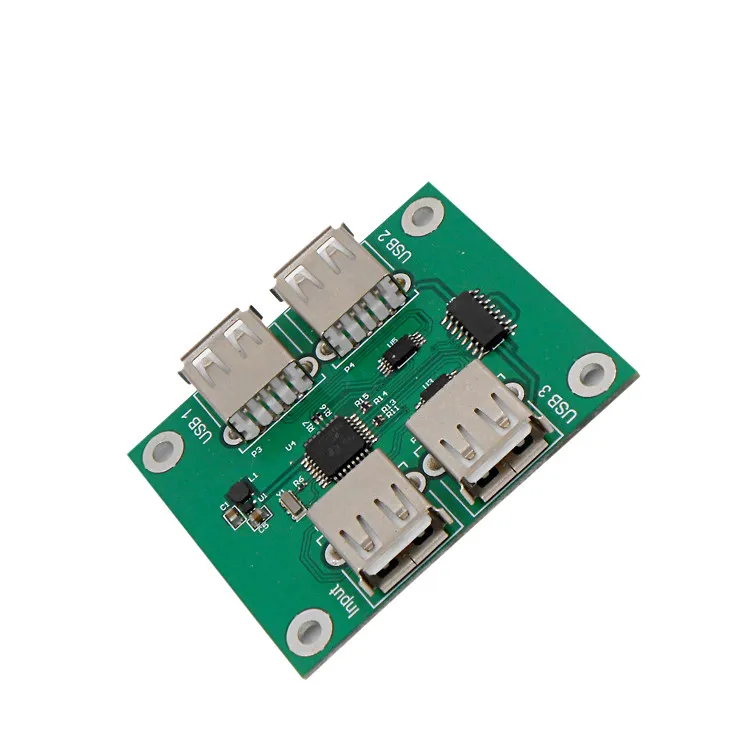
Inverter PCB boards are not monolithic; they vary significantly in design and function based on their intended application, directly influencing their price. This section categorizes these boards by application and provides an overview of typical price ranges.
The cost of inverter PCB boards is influenced by factors such as the complexity of the circuit design, the quality of materials used, the manufacturing process, and the volume of production. Higher power ratings, specialized components, and intricate layouts typically command a higher price.
Inverter PCB Type | Typical Application | Power Range | Typical Price Range (USD) | Key Characteristics |
---|---|---|---|---|
Solar Inverter PCB | Solar Power Systems | 1kW - 1MW+ | $50 - $1000+ | High voltage, high power handling, grid synchronization |
UPS Inverter PCB | Uninterruptible Power Supplies | 500W - 10kW | $30 - $500+ | Battery backup, reliable power delivery, load protection |
Motor Drive Inverter PCB | Electric Motors, Appliances | 50W - 5kW | $20 - $300+ | Variable speed control, precise motor management |
HVAC Inverter PCB | Heating, Ventilation, Air Conditioning | 1kW - 10kW | $40 - $600+ | Compressor control, energy efficiency, temperature management |
Automotive Inverter PCB | Electric Vehicles, Hybrid Vehicles | 5kW - 200kW+ | $100 - $2000+ | High power, robust design, vehicle integration |
Appliance Inverter PCB | Refrigerators, Washing Machines | 100W - 1kW | $15 - $150+ | Energy efficient, precise control, compact |
It is essential to note that these price ranges are indicative and can vary based on specific design requirements, component selection, and order quantities. When sourcing inverter PCBs, always specify the required technical specifications to obtain the most accurate quotes.
Comparative Analysis of Inverter PCB Board Prices
This section provides a detailed comparative analysis of inverter PCB board prices across various applications. Prices are influenced by factors such as power rating, complexity, materials used, and production volume. Understanding these price variations is crucial for informed purchasing decisions.
The following table outlines typical price ranges, representing a broad spectrum of inverter PCB boards. Specific prices may vary considerably based on the supplier, custom requirements, and the current market conditions. It serves as a general guideline to aid in initial budgeting and planning.
Application | Typical Power Rating | Estimated Price Range (USD) | Complexity Level |
---|---|---|---|
Small Appliance Inverters (e.g., Kitchen Gadgets) | 50W - 200W | $5 - $25 | Low |
Portable Power Inverters (e.g., Car Inverters) | 100W - 500W | $15 - $60 | Low to Medium |
Solar Inverters (Residential) | 1kW - 10kW | $100 - $500 | Medium |
Uninterruptible Power Supplies (UPS) | 500W - 5kW | $80 - $400 | Medium to High |
Industrial Inverters (e.g., Motor Drives) | 10kW - 100kW+ | $400 - $2000+ | High |
HVAC Inverter Boards | Varies by Unit | $50 - $300 | Medium to High |
Refrigerator Inverter Boards | Varies by Refrigerator Size | $40 - $150 | Medium |
Note that these price ranges are estimates. For precise pricing, consult directly with PCB manufacturers or suppliers, providing detailed specifications for your specific requirements. Prices are subject to change due to market conditions and technological advancements in the field of electronic components and manufacturing.
Where to Buy Inverter PCB Boards: A Guide to Suppliers
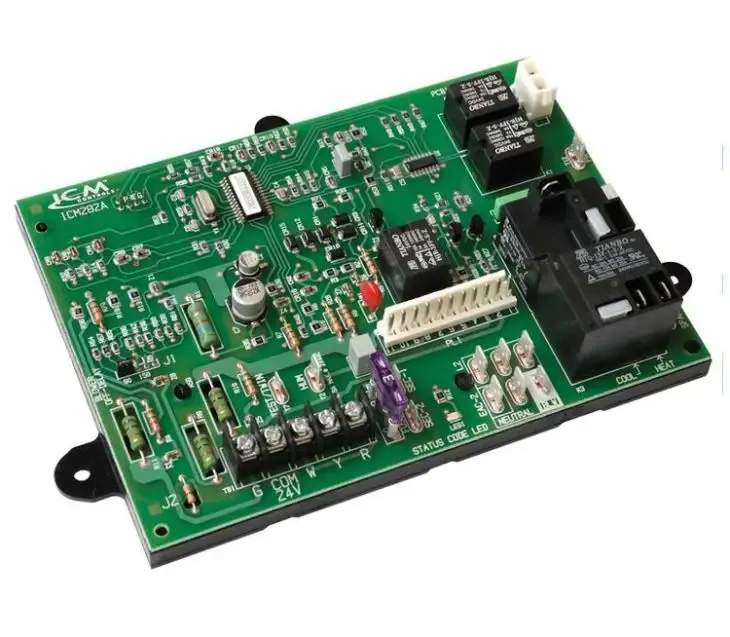
Securing the right supplier for inverter PCB boards is critical for both cost-effectiveness and quality assurance. This section explores the primary avenues for purchasing these essential components, evaluating the advantages and disadvantages of each to help you make informed decisions.
Inverter PCB boards are available through various channels, each offering a different balance of price, quality, and convenience. Understanding these differences is key to selecting the optimal purchasing strategy.
- Online Marketplaces
Platforms such as Amazon, Alibaba, and eBay offer a broad selection of inverter PCBs. These marketplaces typically feature a variety of suppliers, including manufacturers and distributors, providing a wide range of price points and specifications. - Direct from Manufacturers
Purchasing directly from PCB manufacturers can provide the opportunity for custom designs and larger order quantities at a lower per-unit cost. This is an ideal option for businesses requiring specific specifications or large volumes. - Specialized Distributors
Distributors specializing in electronic components often offer a selection of inverter PCBs, providing an intermediate option between online marketplaces and direct manufacturer purchases. These distributors typically ensure higher quality and better customer service. - Local Electronics Suppliers
Local suppliers can be a convenient source, especially for smaller quantities or urgent needs. However, their prices may be higher and their selection limited compared to larger online platforms or manufacturers.
Supplier Type | Pros | Cons |
---|---|---|
Online Marketplaces | Wide selection, competitive pricing, easy access | Variable quality, potential for counterfeit products, longer lead times for some suppliers |
Direct from Manufacturers | Customization options, lower per-unit cost for large orders, direct communication | Higher minimum order quantities, longer lead times, initial setup costs |
Specialized Distributors | Higher quality, better customer service, technical support | Potentially higher prices, may not offer custom designs |
Local Electronics Suppliers | Convenience, immediate availability, support local businesses | Higher prices, limited selection, may not offer specialized PCBs |
Choosing the right supplier depends on your specific needs. For low-volume or general-purpose requirements, online marketplaces might be sufficient. For custom designs or large-scale production, working directly with manufacturers is usually more advantageous. Specialized distributors strike a balance between quality, service, and cost, making them a good option for many.
Frequently Asked Questions About Inverter PCB Boards
This section addresses common questions regarding inverter PCB boards, focusing on their repairability, functionality, cost factors, and applications. Understanding these aspects is crucial for anyone dealing with power electronics.
- Is an inverter AC/PCB repairable?
Yes, inverter PCBs are often repairable, especially at the component level. Common issues such as blown capacitors, faulty MOSFETs, or damaged traces can be addressed by skilled technicians. However, the complexity of the repair depends on the extent of the damage and the availability of replacement parts. It’s often more cost-effective than replacing the entire board, especially in expensive equipment. Professional diagnosis is essential to determine if a repair is viable. - What is a PCB inverter board?
A PCB (Printed Circuit Board) inverter board is an electronic circuit board specifically designed to convert direct current (DC) power into alternating current (AC) power. It is a vital component in devices that require AC power from a DC source such as batteries or solar panels. The board includes transistors, capacitors, inductors, and control circuitry which work in concert to achieve this conversion efficiently. The board contains the electronics to control the switching, voltage and frequency of the alternating current. - Why are PCB boards so expensive?
The cost of PCB boards, including inverter PCBs, is influenced by several factors. These include the type of materials used (e.g., FR4, ceramic), the number of layers, the complexity of the circuit design, the precision of fabrication, and production volume. High-performance boards with stringent requirements, such as those used in inverters, necessitate more costly materials and processes. Furthermore, the cost of raw materials, especially copper, has a high impact on the final cost. - What is the purpose of an inverter board?
The primary purpose of an inverter board is to convert DC power, which is typically from a battery or DC power supply, into AC power suitable for use by various electrical appliances and electronic devices. This is achieved by rapidly switching the DC current on and off using semiconductors like MOSFETs or IGBTs. These switches are controlled in a precise sequence with specific pulse widths to create a sine wave that mimics household AC power. In essence, they serve as the ‘heart’ of any inverter system. - Can I replace my inverter board myself?
Replacing an inverter board yourself is possible, but it requires a strong understanding of electronics, safe handling of electrical components, and the proper tools. It is imperative to identify the correct replacement part and follow the equipment manufacturer's instructions. Improper installation can lead to further damage or pose a safety hazard. If you're not comfortable with these steps, it's best to seek professional assistance. Furthermore, it may be necessary to reset the unit software after replacement for the device to work correctly. - How does an inverter board affect the performance of the device?
The quality and efficiency of the inverter board significantly impact the overall performance and longevity of the device it powers. A well-designed inverter board minimizes energy losses during the conversion process, leading to reduced heat generation and improved energy efficiency. It also ensures a stable AC output with correct voltage and frequency, which protects the connected equipment. Poor quality boards can cause lower efficiency, high energy losses, or in the worst case, malfunction of the device it powers. - What are common failures of an Inverter board?
Common failures of an inverter board include capacitor degradation due to heat, MOSFET or IGBT failures from overcurrent or voltage spikes, fuse issues, relay failures, and issues with the gate drivers that turn the switches on and off. Environmental factors, like moisture and extreme temperatures, can also contribute to failures by corrosion or mechanical stress. Additionally, poor design and manufacturing can cause failures due to inadequate heat sinking or improper component selection.
Practical Tips for Getting the Best Inverter PCB Board Price
Securing the most favorable price for inverter PCB boards involves strategic planning and informed purchasing practices. This section outlines practical methods to minimize costs without compromising quality, focusing on leveraging volume and negotiation.
- Bulk Purchasing
Significant cost reductions are often achievable through bulk purchases. Manufacturers typically offer lower per-unit prices for larger orders due to economies of scale, allowing them to optimize production runs and reduce overhead costs. - Direct Negotiation
Engage directly with suppliers and manufacturers to negotiate pricing, especially for larger orders or long-term partnerships. Demonstrating a commitment to a sustained relationship can often lead to more favorable terms. - Standardization of Design
Opting for standardized PCB designs, whenever possible, can lower costs. Using common components and fewer unique layouts reduces manufacturing complexity and facilitates streamlined production. - Component Sourcing
Consider sourcing components directly rather than relying on the PCB manufacturer to procure them, especially if you have established supply chains or can secure better pricing on specific components. This can be particularly effective for high-cost or frequently used parts. - Early Planning and Forecasting
Accurate forecasting of your PCB requirements and early planning of your procurement schedule allows manufacturers to plan their production more effectively, potentially leading to better pricing. Last-minute requests often incur higher costs. - Alternative Materials
Explore alternative materials and finishes that meet your performance requirements while being more cost-effective. Consult with your manufacturer to identify lower-cost alternatives that can be used without compromising functionality. - Avoid Customization if Possible
While unique designs are sometimes necessary, limiting unnecessary customization can reduce costs. Custom work typically requires additional design and manufacturing resources which may lead to increased prices. - Payment Terms
Negotiate favorable payment terms with suppliers. Options such as extended payment periods or milestone-based payments can provide financial flexibility, helping to manage cash flow more effectively.
By implementing these strategies, businesses can effectively manage costs associated with inverter PCB board acquisition and secure a competitive price point in the market. The key is to combine strategic planning, proactive supplier engagement, and a thorough understanding of your project's technical requirements.
Future Trends in Inverter PCB Board Technology and Pricing
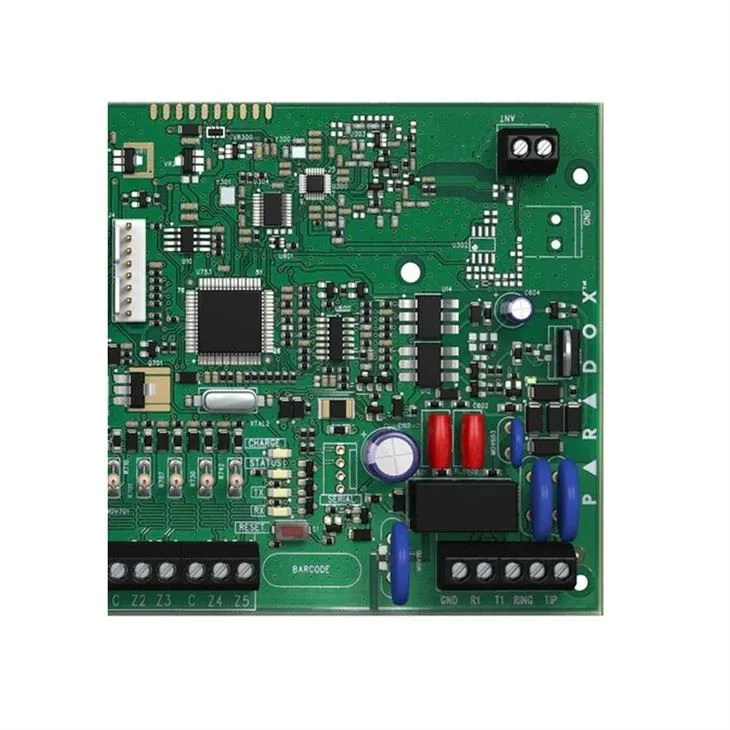
The inverter PCB board market is poised for significant transformation, driven by advancements in materials science, manufacturing processes, and the increasing demand for more efficient and compact power conversion solutions. These emerging trends are expected to influence both the technology and pricing of inverter PCBs.
Here's an overview of key areas shaping the future:
- Advanced Materials
The adoption of new materials with superior thermal and electrical properties, such as silicon carbide (SiC) and gallium nitride (GaN), will enable higher switching frequencies and improved efficiency. These materials are more expensive initially but can reduce system costs by lowering cooling requirements and boosting performance. - Miniaturization and Integration
Trend toward integrating multiple components onto a single PCB, reducing size and improving reliability. This includes System-in-Package (SiP) and chip-on-board (COB) technologies. - Smart PCB Technology
The integration of smart features into inverter PCBs, such as temperature and current monitoring, enables predictive maintenance and performance optimization. - Additive Manufacturing
3D printing or additive manufacturing techniques for PCB production will allow for more complex designs, faster prototyping, and customized solutions. This could disrupt traditional manufacturing methods and reduce production costs for specialized applications. - Sustainable PCB Production
Focus on eco-friendly materials and processes, driven by environmental regulations and corporate sustainability goals. This might involve bio-based materials and low-energy manufacturing techniques.
The impact on pricing will likely be complex. Initially, the costs of SiC and GaN-based boards and other innovative technologies are expected to be high, leading to increased prices for high-performance applications. However, as these technologies mature and manufacturing scales, costs should decrease, making them more competitive. Additive manufacturing and advanced integration techniques should also help to reduce overall costs in the long run, offering more affordable solutions. Furthermore, the competition in PCB manufacturing and component supply chain will play a role in reducing the inverter PCB board price.
This ongoing evolution presents both challenges and opportunities for manufacturers and consumers. Staying abreast of these trends will be critical for making informed decisions about the selection and application of inverter PCBs.
Understanding the intricacies of inverter PCB board price is critical for making cost-effective decisions for your needs, ranging from simple household appliances to sophisticated industrial setups. This guide has armed you with the knowledge of the various factors influencing pricing, and practical tips to ensure you secure the best [inverter pcb board price] available. Remember to consider the quality, application, and supplier when purchasing your next inverter PCB board, ensuring a balance between price and performance as technology and market dynamics continue to evolve.
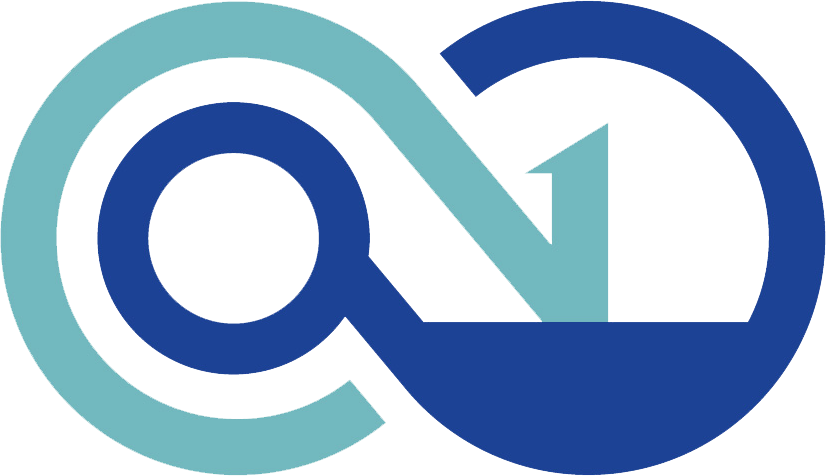