LED PCB: Design, Types, and Applications for Modern Lighting
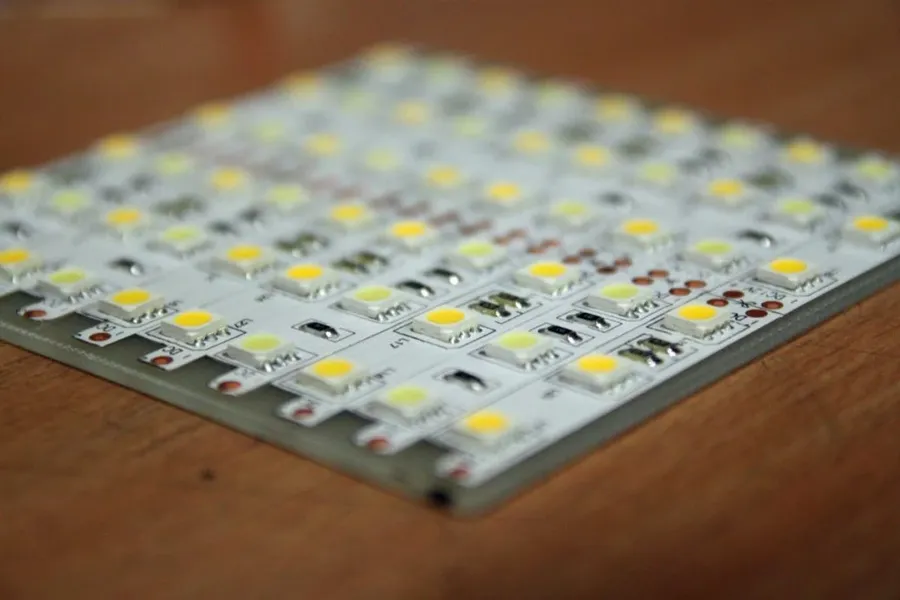
In our modern world, LEDs light up everything from our homes to our cities, and at the heart of this revolution is the LED PCB. This article will break down everything from its basic structure to advanced applications of LED PCBs, so read on to explore how this essential technology is powering our world and how to use it effectively.
What is an LED PCB?
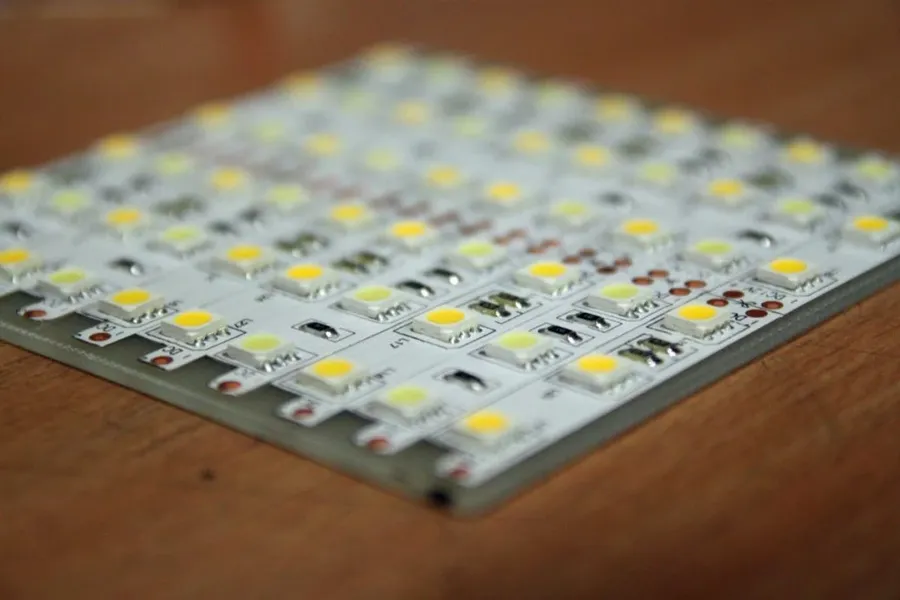
An LED PCB, or Light Emitting Diode Printed Circuit Board, is a foundational component in modern lighting technology. It serves as a specialized platform designed to physically support and electrically connect LEDs. Functionally, it provides the necessary conductive pathways and mounting points, ensuring that LEDs operate efficiently and reliably within a lighting system.
At its core, an LED PCB is a carefully engineered substrate upon which LEDs are mounted and interconnected. The board incorporates conductive tracks, typically made of copper, that facilitate the flow of electrical current to each LED. The substrate material, often fiberglass or composite, provides insulation between the conductive pathways, protecting against shorts and ensuring proper electrical function. These design aspects must be optimized to ensure proper thermal and electrical performance.
Different Types of LED PCBs
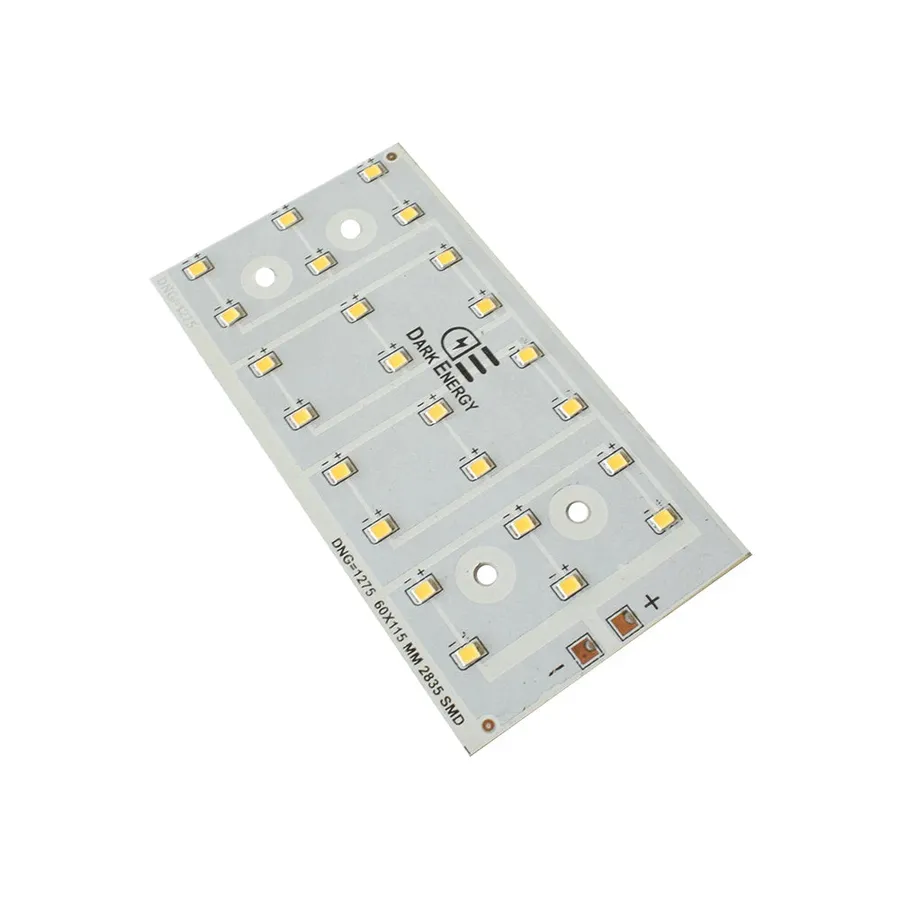
LED PCBs are not monolithic; they come in various types, each tailored for specific performance and application requirements. These variations primarily stem from the substrate material and intended use-case, affecting properties like thermal management, flexibility, and cost. Understanding these differences is crucial for selecting the most suitable PCB for a given LED lighting project.
Type | Description | Typical Applications | Advantages | Disadvantages |
---|---|---|---|---|
Rigid PCBs | Traditional PCBs with a solid, inflexible substrate made of materials like FR-4. | General lighting, indoor fixtures, electronics. | Cost-effective, widely available, reliable. | Inflexible, not suitable for curved surfaces. |
Flexible PCBs | PCBs made from flexible substrates like polyimide, allowing bending and shaping. | Automotive lighting, wearable devices, curved lighting fixtures. | Lightweight, flexible, adaptable to various shapes. | More expensive than rigid PCBs, sensitive to damage |
Metal Core PCBs (MCPCBs) | PCBs with a metal base (often aluminum) that efficiently dissipates heat. | High-power LED lighting, automotive headlights, street lamps. | Excellent thermal management, improved lifespan of LEDs. | Higher cost, heavier than other types, reduced flexibility. |
Metal Core PCBs (MCPCBs) for LED Lighting
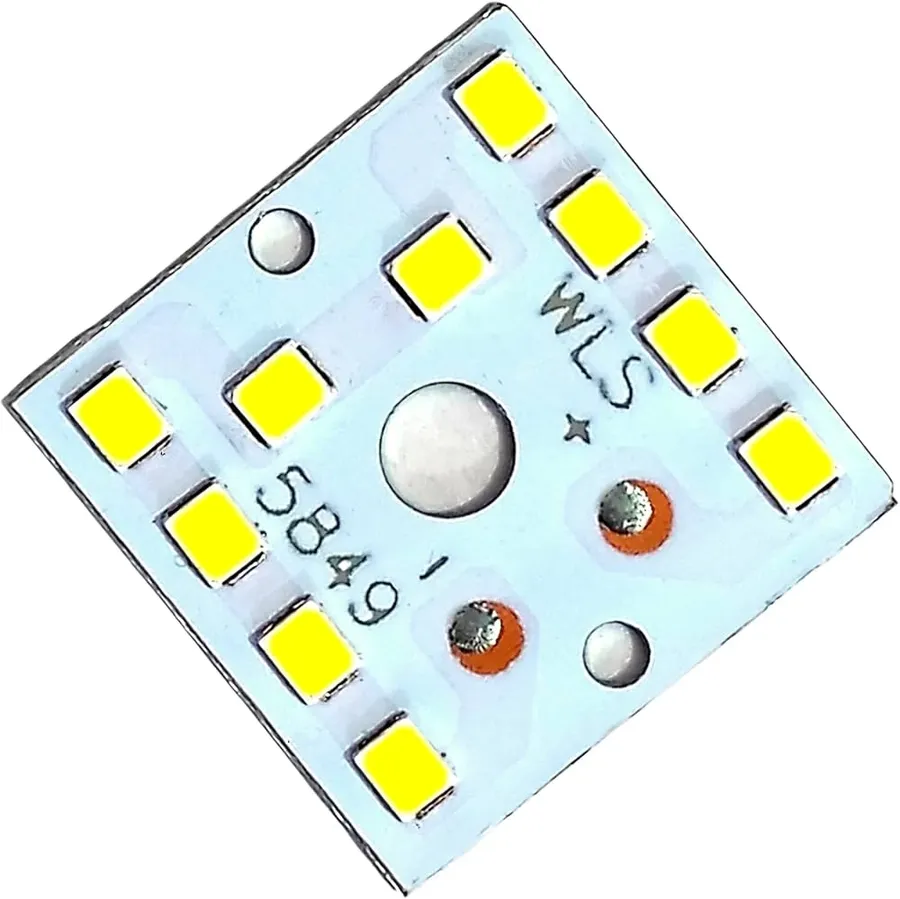
Metal Core PCBs (MCPCBs) are a specialized type of printed circuit board that incorporate a metal base, typically aluminum, copper, or steel, as a core material. This core provides superior thermal management capabilities, making MCPCBs ideal for high-power LED applications where efficient heat dissipation is crucial for performance and longevity. Unlike traditional PCBs that use FR-4 as the primary substrate, MCPCBs utilize the metal core to conduct heat away from the LEDs, preventing overheating and ensuring stable operation.
Feature | MCPCB | FR-4 PCB |
---|---|---|
Thermal Conductivity | High (e.g., Aluminum 237 W/m·K) | Low (0.2-0.3 W/m·K) |
Heat Dissipation | Excellent | Poor |
Typical Applications | High-power LEDs, Automotive lighting | General electronics, low-power LEDs |
Cost | Higher | Lower |
Mechanical Strength | Good | Moderate |
Longevity | Extended | Reduced at high heat |
The core material of MCPCBs greatly influences their thermal performance. Aluminum is the most common choice due to its cost-effectiveness, high thermal conductivity, and good strength. Copper, while more expensive, offers even higher thermal conductivity but may be heavier. Steel, though strong, is not as thermally conductive but can be used for structural applications in conjunction with thermal interface materials. The metal core is typically laminated with a dielectric layer to insulate the electrical traces and then covered with a copper foil layer where circuits are etched and components are soldered.
Key Components of an LED PCB
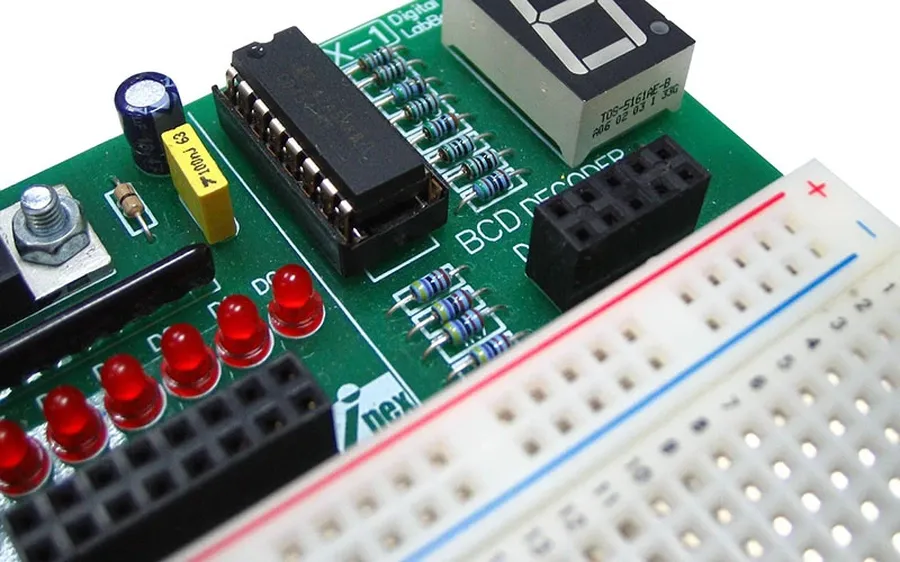
An LED PCB's functionality relies on several key components working in concert to provide electrical connection and mechanical support for LEDs. These components are crucial for ensuring the longevity, efficiency, and performance of the lighting system. A thorough understanding of each component is essential for effective LED PCB design and application.
Component | Description | Significance |
---|---|---|
Substrate Material | The base material of the PCB, typically made of FR-4, aluminum, or flexible materials like polyimide. | Provides mechanical support and insulation; material choice affects thermal performance and flexibility. |
Conductive Traces | Copper pathways etched onto the substrate, forming the electrical network. | Carry electrical current to LEDs and other components; trace width and routing affect current handling and signal integrity. |
LED Mounting Pads | Specially designed areas on the PCB to which LEDs are soldered. | Provide a stable and electrically conductive connection for LEDs; footprint design matches the specific LED package. |
Connectors | Points where the PCB connects to external power sources or other circuit boards. | Allow for electrical integration with other systems; type of connector depends on the application's power and signal requirements. |
Solder Mask | A protective layer covering most of the PCB surface, except for the pads to be soldered. | Prevents solder bridges and protects conductive traces from corrosion and environmental damage. |
Silkscreen | An ink layer used for component identification, polarity marks, and other helpful information. | Aids in assembly and maintenance; critical for preventing errors during component placement and troubleshooting |
Design Considerations for LED PCBs
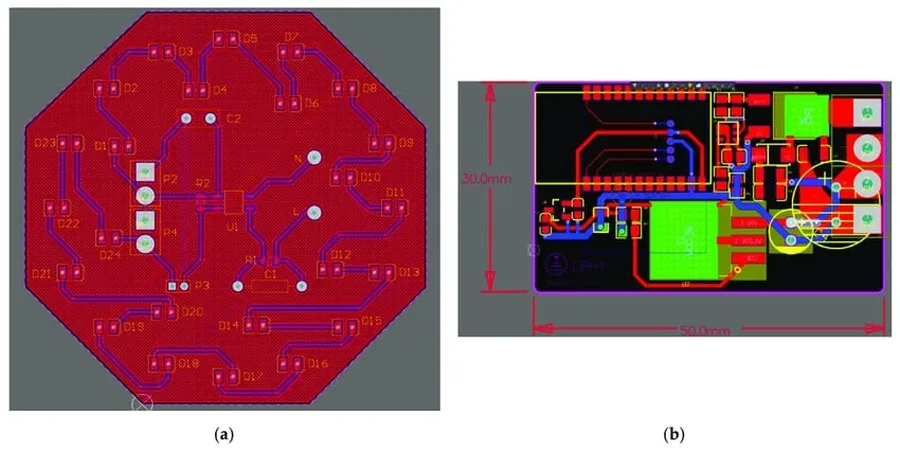
Effective LED PCB design hinges on several critical factors that directly impact performance, reliability, and longevity. These considerations encompass thermal management, electrical integrity, and compatibility with LED components. A well-designed LED PCB ensures optimal heat dissipation, efficient power delivery, and proper physical mounting of LEDs.
Design Aspect | Description | Importance |
---|---|---|
Thermal Management | Effective heat dissipation from LEDs to prevent overheating and ensure long-term performance. | Crucial for maintaining LED efficiency, lifespan, and overall system reliability. |
Electrical Routing | Designing conductive traces for minimal resistance and impedance to ensure efficient power delivery. | Minimizes power loss, voltage drop, and ensures even light output across all LEDs. |
LED Package Compatibility | Ensuring the PCB design is appropriate for specific LED packages (e.g., 5050, 3528, COB). | Guarantees proper mounting, alignment, and electrical contact with the chosen LEDs. |
Substrate Material | Choosing the right material (e.g., FR-4, Aluminum) based on thermal requirements and environmental conditions. | Impacts thermal performance, structural integrity, and cost of the PCB. |
Layout and Component Placement | Strategically positioning LEDs and other components for optimal thermal and electrical performance. | Prevents hotspots, ensures balanced lighting, and simplifies assembly. |
Layer Stackup | Selecting the number and arrangement of copper layers for heat dissipation, current carrying capacity, and signal integrity. | Optimizes thermal and electrical performance, especially in complex multi-layer designs. |
LED PCB Applications Across Industries
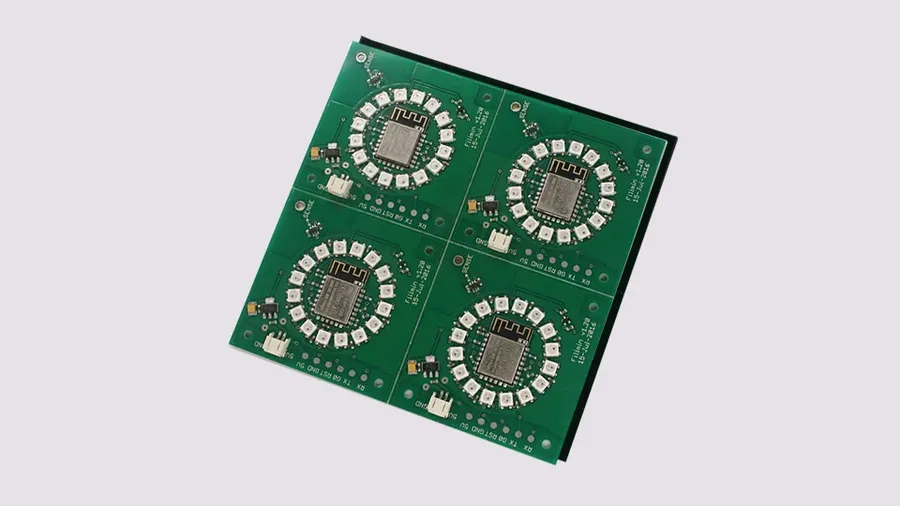
LED PCBs are foundational components enabling a wide array of lighting and display technologies across diverse sectors. Their ability to efficiently manage heat and provide reliable electrical connections makes them indispensable in modern electronic applications. This section explores the key industries and applications where LED PCBs are prominently featured.
- Automotive Lighting
LED PCBs are used extensively in automotive lighting, including headlights, taillights, turn signals, and interior lighting. Their compact size, durability, and energy efficiency make them ideal for vehicle applications. - Street Lighting
LED PCBs form the core of modern street lighting systems. Their high brightness, long lifespan, and low energy consumption are critical for efficient and cost-effective public lighting. - Indoor Lighting
LED PCBs are found in numerous indoor lighting solutions, such as LED bulbs, tube lights, panel lights, and decorative lighting. Their versatility allows for various color temperatures and dimming options, enhancing the ambiance and functionality of indoor spaces. - 3D Printers
LED PCBs are used to provide illumination within 3D printers, allowing users to clearly observe the printing process and ensuring proper printing layer visualization, especially in enclosed printer designs. - Display Technology
LED PCBs are fundamental to various display technologies including LED video walls, backlights for LCD screens, and digital signage. Their capacity to deliver consistent brightness and color reproduction is vital for high-quality displays. - Consumer Electronics
From smartphones to televisions, LED PCBs enable backlighting in various displays. They also play a crucial role in indicator lights, flashlights, and other small electronic devices, offering energy efficient and compact illumination solutions. - Medical Equipment
LED PCBs are increasingly used in medical devices where precise illumination is required, such as surgical lights, dental equipment, and diagnostic tools, offering stable, high-intensity light with minimal heat generation.
Application Area | Specific Use Cases | Key Advantages of Using LED PCBs |
---|---|---|
Automotive | Headlights, taillights, interior lighting | Compact size, durability, energy efficiency |
Street Lighting | Outdoor lighting systems | High brightness, long lifespan, low energy consumption |
Indoor Lighting | Bulbs, tubes, panel lights, decorative lighting | Versatile color temperatures, dimming options |
3D Printers | Illumination within the printing chamber | Allows clear visualization during printing |
Display Technology | LED video walls, LCD backlights, digital signage | Consistent brightness, accurate color reproduction |
Consumer Electronics | Smartphones, televisions, indicator lights | Energy efficient, compact illumination |
Medical Equipment | Surgical lights, dental tools | Precise illumination, minimal heat generation |
LED PCB Manufacturing and Assembly
The production of LED PCBs involves a complex interplay of precision manufacturing and careful assembly to ensure optimal performance and reliability. This process encompasses PCB fabrication, component placement, soldering, and rigorous quality control.
LED PCB manufacturing is a multi-stage process that transforms raw materials into functional circuit boards, ready for population with LEDs and other electronic components. The primary steps are outlined below:
- PCB Fabrication
This stage begins with a substrate material, which forms the base of the PCB. Common materials include FR-4 (a fiberglass composite), aluminum, or flexible substrates like polyimide. The substrate is then layered with copper, which is then chemically etched to form the circuit traces. This process may include multiple layers, depending on design complexity. Other steps include drilling vias for electrical connections between layers, and applying a solder mask to protect copper traces and to define soldering areas. A silkscreen layer is also often applied to aid in component placement and identification. - Solder Paste Application
Solder paste, a mixture of solder powder and flux, is applied precisely to the pads where components will be placed. This application is often done through a stencil that matches the PCB's pad layout. Solder paste is essential for creating reliable solder joints in the next step. - Component Placement
Automated pick-and-place machines accurately position LEDs and other components onto the solder paste. The precision in this step is critical to the functionality of the final product. Various components such as resistors, capacitors, and integrated circuits may be placed depending on specific LED PCB application. - Reflow Soldering
The populated PCB is then passed through a reflow oven. The solder paste melts, and forms a secure electrical and mechanical connection with the components. The temperature profile is precisely controlled to achieve optimum soldering quality, and to avoid damaging the components. - Quality Control and Inspection
After soldering, the PCB undergoes rigorous inspection. This process includes both visual inspection and automated testing such as x-ray inspection to check the integrity of solder joints. Functional tests may be used to ensure that the LED PCB is functioning as designed, ensuring electrical connectivity and correct LED operation. - Separation and Testing
If the PCBs were part of a larger array (panelization), they are separated at this step. Individual PCBs then undergo final testing to ensure full functionality.
Each of these steps is carefully monitored to maintain high production standards. Parameters such as solder paste viscosity, reflow oven temperature profiles, and component placement accuracy are crucial for producing reliable and effective LED PCBs.
Parameter | Description | Importance |
---|---|---|
Solder Paste Viscosity | Thickness and flow properties of solder paste | Ensures proper deposition on pads and avoids bridging |
Reflow Oven Temperature Profile | Temperature variations during reflow soldering | Critical for successful solder joints without component damage |
Component Placement Accuracy | Precision in placing components on PCB | Ensures functional circuit connections and alignment |
Inspection Methods | Visual, x-ray, and functional tests | Guarantees quality and reliability of final product |
Frequently Asked Questions about LED PCBs
This section addresses common inquiries regarding LED PCBs, providing clear and concise answers to enhance your understanding of their function, design, and applications.
- What does PCB stand for in the context of LED lighting?
In the context of LED lighting, PCB stands for Printed Circuit Board. It serves as the foundational platform where LEDs and other electronic components are mounted and interconnected via conductive traces. These traces provide the necessary pathways for electrical current to power the LEDs. - How are LED PCBs manufactured?
The manufacturing process for LED PCBs involves several key steps. Initially, a substrate material (such as FR-4, aluminum, or polyimide) is selected. Next, a conductive layer of copper is etched to form the circuit traces. Following this, the LEDs and other surface mount components are placed on the board using automated pick-and-place machines. Finally, the components are soldered in place through reflow or wave soldering. Quality control measures are implemented throughout each stage. - What are the key differences between LED PCBs and standard PCBs?
While both LED PCBs and standard PCBs share the fundamental function of providing electrical connections, LED PCBs often require enhanced thermal management capabilities due to the heat generated by LEDs. This frequently leads to the use of metal core substrates (MCPCBs) instead of traditional FR-4. LED PCBs also often feature specialized mounting pads and heat dissipation features not commonly found in standard PCBs. - Why can LED PCBs sometimes be more expensive than other types of PCBs?
The cost of LED PCBs can be higher than standard PCBs due to several factors. These include the use of higher-cost substrate materials like aluminum or copper for enhanced thermal dissipation, more intricate trace routing requirements to handle higher current, and the inclusion of thermal vias or other heat management features. Additionally, the specialized assembly process for mounting LEDs and the higher precision manufacturing demands can contribute to increased overall cost. - Can LED PCBs be designed for different LED packages, such as 5050 LEDs?
Yes, LED PCBs are designed to accommodate different LED package sizes and types. The PCB design specifies the footprint, mounting pad dimensions, and trace layouts that are precisely tailored to the specific LED packages being used, such as 5050 LEDs or others. This allows for a versatile and adaptable design that can accommodate various LED configurations. - What role does thermal management play in LED PCB design?
Thermal management is a crucial aspect of LED PCB design. LEDs generate heat during operation, which if not properly managed, can lead to reduced performance, reduced lifespan, or even failure. Design considerations include the use of metal-core PCBs, thermal vias to conduct heat away from the LEDs, and proper layout to ensure even heat distribution. Efficient heat dissipation is essential to maintaining optimal LED performance and reliability. - Are there different types of LED PCBs?
Yes, there are several types of LED PCBs, each designed for different applications and performance requirements. Common types include rigid PCBs (typically FR-4 based), flexible PCBs (using flexible materials like polyimide), and metal core PCBs (MCPCBs) which are used for high-power LEDs that generate a lot of heat. Each type offers unique advantages regarding cost, flexibility, and heat dissipation capabilities.
DIY LED PCB Projects and Resources
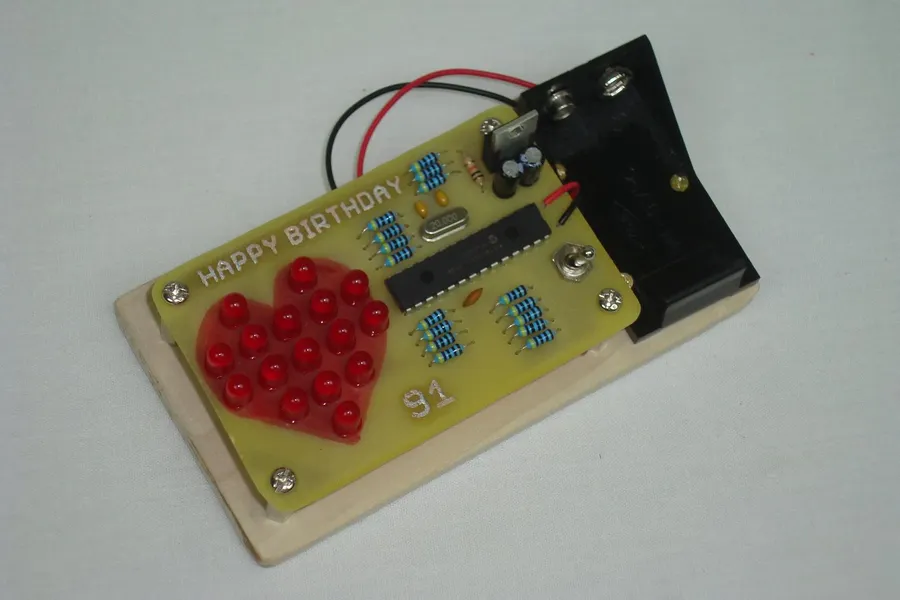
For hobbyists and small-scale projects, creating your own LED PCBs can be a rewarding experience. This section explores options for embarking on DIY LED PCB projects, including resources for kits, individual components, and custom design services.
- LED PCB Kits
These kits provide a streamlined way to get started with LED PCB projects. They typically include a pre-designed PCB, LEDs, resistors, and other necessary components. Kits are available for various project types, from simple lighting to more complex circuits, often accompanied with tutorials and instructions. - Individual LED Components
For those wanting full design control, sourcing individual components is essential. This includes selecting specific LEDs (e.g., 5050, 3528), resistors, capacitors, and connectors. Understanding component specifications is critical for successful projects, ensuring proper electrical and thermal performance. - Custom LED PCB Design Services
When a kit or pre-designed boards don't quite meet your requirements, custom PCB design services are available. These services typically provide the tools and expertise to develop unique PCBs tailored to your project needs. The process generally involves providing a schematic or layout, then working with the service to generate the final PCB design. - Where to find these resources
Various online retailers and specialized electronics suppliers offer LED PCB kits, individual components, and custom design services. Popular platforms include Adafruit, SparkFun, Amazon, and PCB fabrication services such as JLCPCB and PCBWay. Evaluate the costs, reviews, and delivery times before making a purchase. - Software Tools for DIY PCB Design
For those designing their own boards, open-source and free software are available, such as KiCad and Eagle. These tools enable users to create schematics, PCB layouts, and gerber files for manufacturing.
LED PCBs are integral to the advancement of lighting solutions. Their versatility, thermal efficiency and design flexibility make them a core component in diverse applications. By understanding the design and application of LED PCBs, both professionals and hobbyists can fully harness the potential of this exciting technology to create powerful lighting solutions.
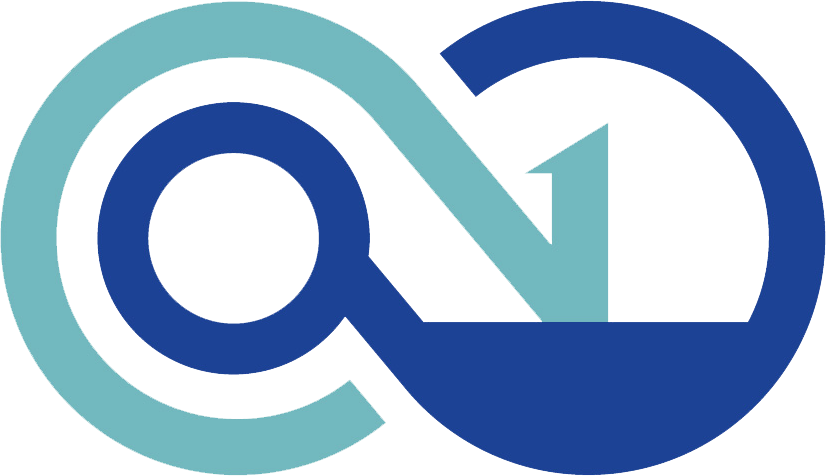