Mastering Drone Circuit Boards: A Comprehensive Guide
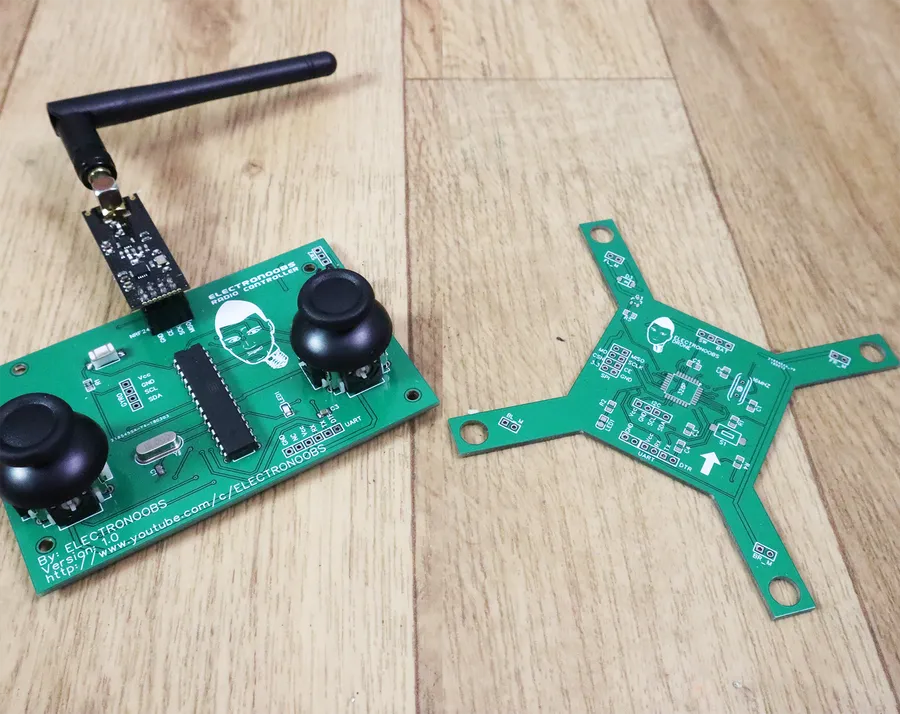
From high-speed aerial photography to package delivery, the unsung hero behind every drone's flight is its circuit board. This intricate piece of technology acts as the drone's central nervous system, dictating everything from motor speeds to communication protocols. This article will demystify drone circuit boards, providing a comprehensive guide to help you understand their function, selection criteria, and the cutting-edge advancements driving the drone industry forward.
Understanding the Role of a Drone Circuit Board
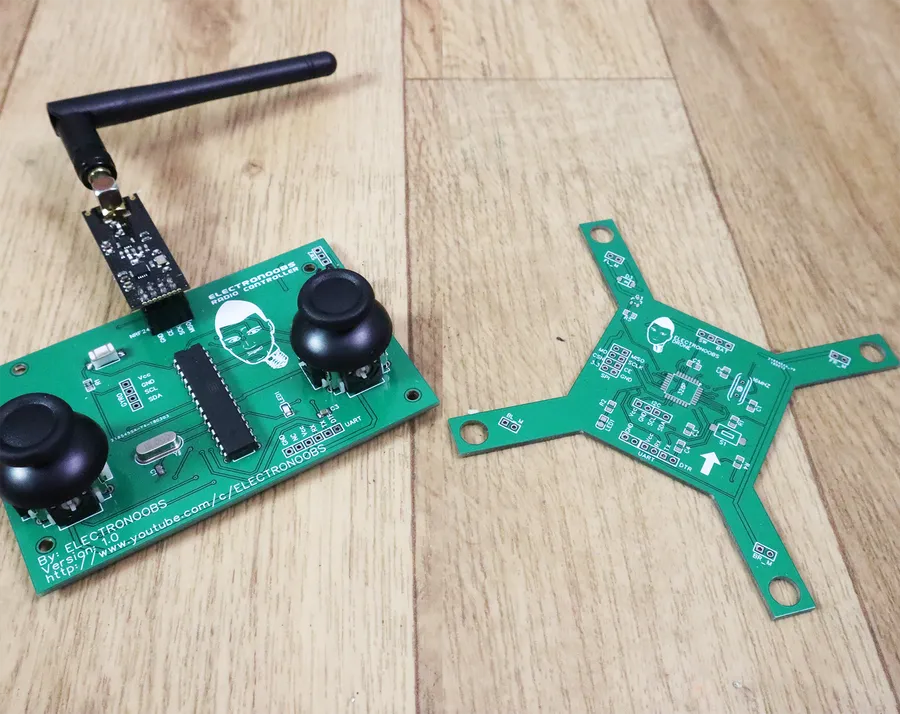
The drone circuit board serves as the central nervous system of the aircraft, orchestrating critical functions such as power distribution, flight control, sensor integration, and communication management, all essential for stable and reliable drone operation. Its intricate design facilitates seamless interaction between all electronic components, directly influencing a drone's overall performance and capability.
The primary functions of a drone circuit board are multifaceted and critical to the drone’s operation:
- Power Distribution
The circuit board efficiently manages and distributes power from the battery to various components, such as motors, flight controller, and sensors, ensuring each receives the correct voltage and current required for optimal operation. - Flight Control
Acting as the brain, the flight controller on the circuit board processes data from sensors (IMU, GPS), interprets user commands, and adjusts motor speeds accordingly to achieve stable and precise flight maneuvers. - Sensor Integration
The circuit board serves as the central hub, integrating various sensors like the Inertial Measurement Unit (IMU), GPS, and barometer, which provide crucial data for navigation, altitude control, and position stabilization. - Communication Management
It facilitates communication between the drone and the remote controller, enabling the transmission of user inputs and telemetry data, as well as supporting data transfer for features like real-time video streaming.
Types of Drone Circuit Boards
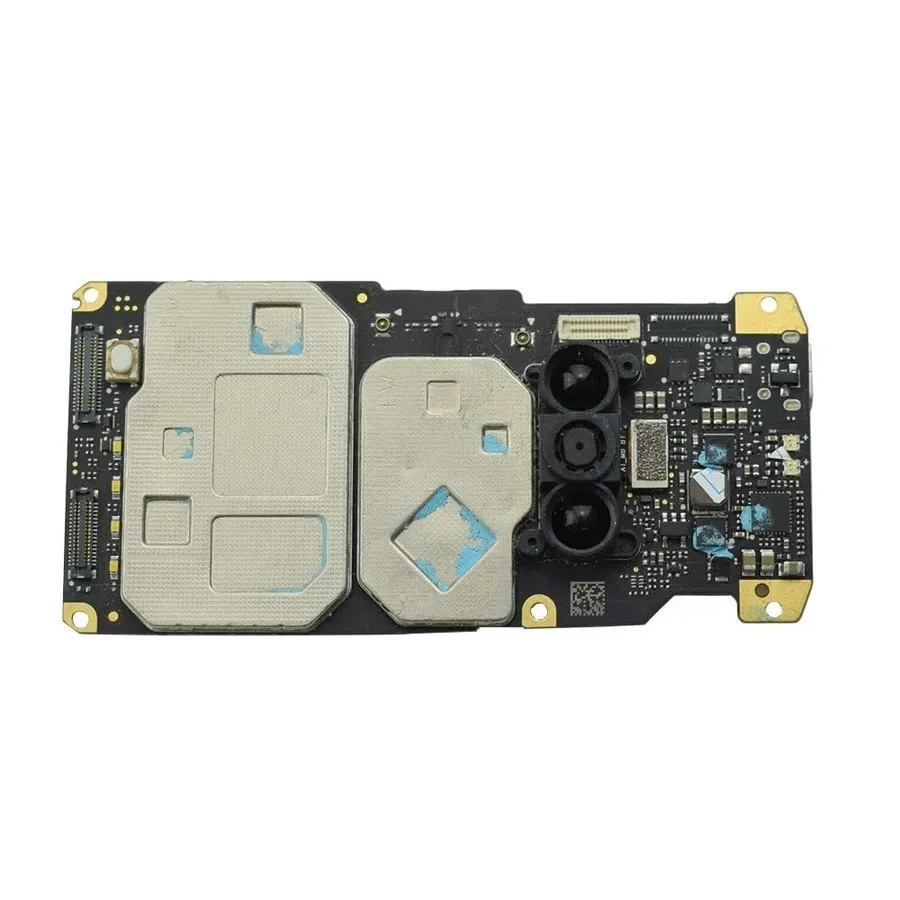
Drone circuit boards are the central nervous system of any unmanned aerial vehicle, and they are not monolithic; rather, they consist of several specialized types, each with distinct functions critical to the drone's operation. Understanding these different boards is essential for drone enthusiasts and professionals alike.
Board Type | Primary Function | Key Characteristics |
---|---|---|
Flight Controller Board | Manages flight stability and navigation. | Includes a microcontroller, IMU, and interfaces for other components. |
ESC (Electronic Speed Controller) Board | Regulates the speed of the drone's motors. | Receives signals from the flight controller to adjust motor speed. |
Power Distribution Board (PDB) | Distributes power from the battery to all drone components. | Features multiple power outputs with appropriate voltage and current ratings. |
Receiver Board | Receives control signals from the remote transmitter. | Demodulates radio signals and relays them to the flight controller. |
Specialized Boards | Provide specific functionality (e.g., camera control, video transmission). | Customized for a specific purpose, depending on the drone's design. |
The integration of these various circuit boards ensures the drone can operate effectively, responding to user commands, and maintaining stable flight. Each board contributes to the overall system, with specialized functions enabling a variety of drone applications. Below is a more detailed exploration of each type:
- Flight Controller Boards
These boards are the brains of the operation, housing the microcontroller that executes the flight control algorithm. They integrate data from the Inertial Measurement Unit (IMU) and other sensors to stabilize the drone and manage its flight path. Key considerations include processing power, sensor accuracy, and firmware support. - ESC (Electronic Speed Controller) Boards
ESCs are responsible for translating the throttle commands from the flight controller into motor speed adjustments. They must be capable of handling high current loads and precisely controlling the motor speed to achieve smooth, responsive flight. The ESCs specification must match the requirements of the motors they are connected to. - Power Distribution Boards (PDBs)
PDBs distribute the battery's power efficiently to various components within the drone. They often include protection circuitry, such as overcurrent and overvoltage protection, to safeguard the system. Good PDB design is crucial for the electrical system reliability. - Receiver Boards
These boards capture signals from the remote control transmitter and relay this information to the flight controller. They are responsible for decoding the signals which then control the drone's movement. The range and reliability of the receiver are essential to maintain a good connection between the pilot and drone. - Specialized Boards
These may include boards for camera stabilization, video processing, and telemetry. They add specific functionality to the drone, enabling it to accomplish specialized tasks such as photography, mapping, or package delivery. The requirements for these boards are very specific to the use case.
Key Components of a Drone Circuit Board
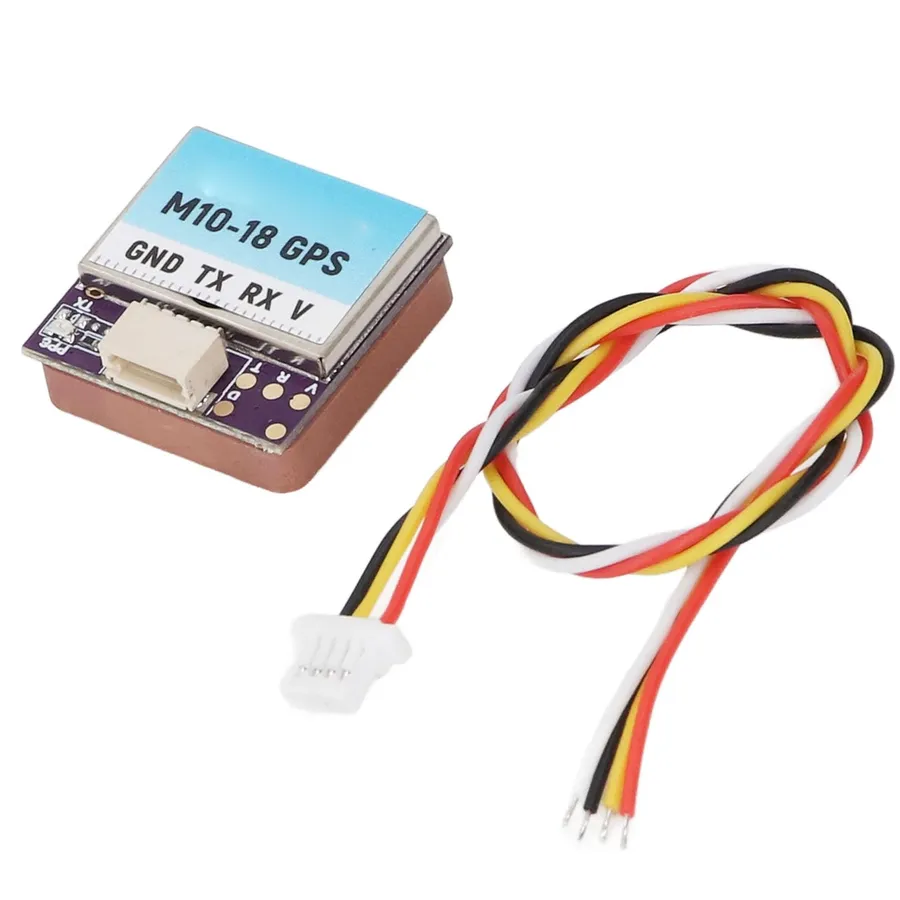
A drone's circuit board is a complex assembly of electronic components working in concert to enable flight and functionality. Understanding these key components is crucial for anyone looking to design, build, or repair drones. The primary components include microcontrollers, sensors, communication modules, power management integrated circuits (ICs), and connectors, each with a distinct role in the operation of the drone.
Component | Function | Importance |
---|---|---|
Microcontrollers (MCU) | Execute code to manage flight control, sensor data processing, and communication. | The brain of the drone, essential for all operations. |
Inertial Measurement Unit (IMU) Sensors | Measures the drone's angular rate (gyroscope) and acceleration (accelerometer) for flight stabilization. | Enables accurate control and prevents erratic flight behavior. |
Global Positioning System (GPS) Sensors | Provides positional information for navigation and autonomous flight. | Essential for precise location tracking and waypoint navigation. |
Communication Modules (Wi-Fi, Bluetooth) | Enables wireless communication with a remote controller and other devices. | Allows for user control and data transmission. |
Power Management Integrated Circuits (ICs) | Regulate power distribution from the battery to the other components. | Ensures stable power delivery to prevent damage and optimize battery life. |
Connectors | Physical interfaces that allow for the connection of various parts, like the battery, motors, and external sensors. | Provide secure and reliable connections within the drone system. |
Selecting the Right Drone Circuit Board
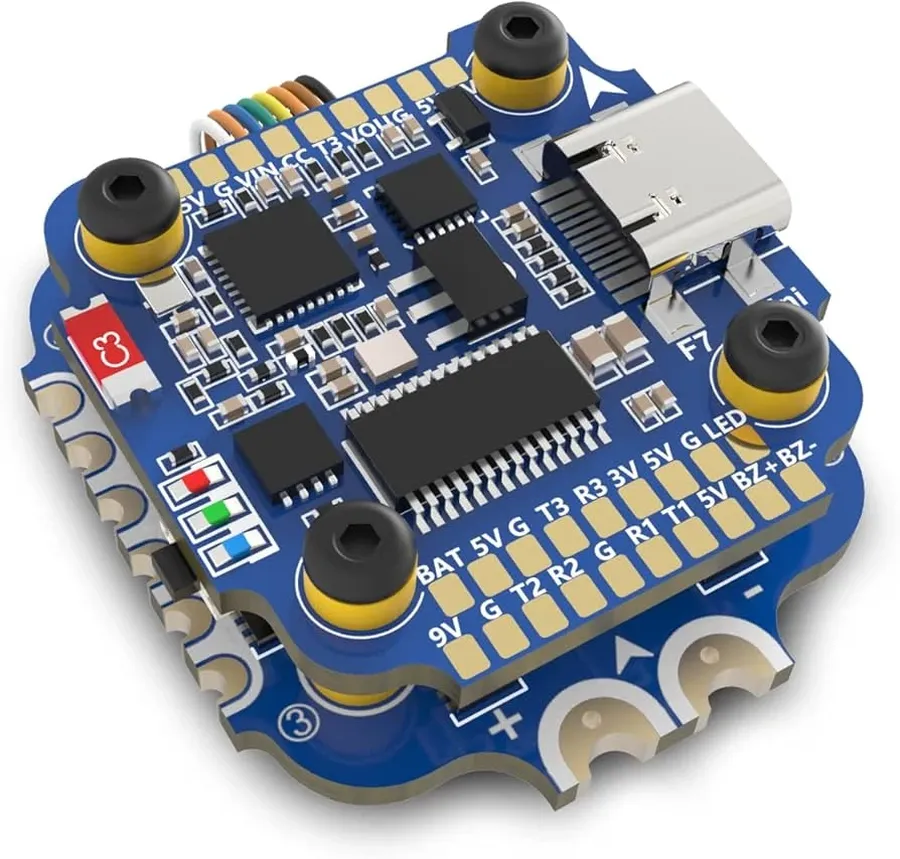
Choosing the appropriate drone circuit board is crucial for optimal performance, reliability, and compatibility. This selection process requires a detailed understanding of your drone's specific needs, considering factors such as its intended use (racing, photography, etc.), desired features, size and weight limitations, and performance expectations, while also ensuring that all components can function in harmony.
Factor | Considerations | Impact on Selection |
---|---|---|
Drone Type | Racing, Photography, Mapping, etc. | Different applications require different processing power, sensor compatibility, and power distribution capabilities. |
Required Features | GPS, IMU, Barometer, Wi-Fi, Bluetooth, etc. | Ensure the board supports the necessary communication and navigation modules. |
Size and Weight | Compact designs for smaller drones, heavier duty boards for larger ones. | Board's physical dimensions and mass must fit the drone frame and meet payload requirements. |
Performance Specifications | Flight time, speed, stability, etc. | The circuit board’s design must support the desired operational parameters, including power efficiency. |
Component Compatibility | Motor ESCs, cameras, sensors, etc. | Choose a board that is fully compatible with all other electronic components used in your build. |
Firmware and Software Support | Open source like ArduPilot, or manufacturer specific. | Ensure that the circuit board’s firmware is well supported by your choice of drone control software, and is regularly updated. |
Cost | Budget limits. | Balance the features needed for your application with budget constraints. |
When making a decision, it is also important to consider the board's power management capabilities. An inefficient power distribution board can drastically reduce flight time and cause overheating, which can harm the drone’s electronics. The integration of the electronic speed controllers (ESCs) into the main board or separate modules needs to be considered in the selection process. A well-integrated ESC solution can improve the efficiency and performance of the system.
Drone Circuit Board Design Considerations
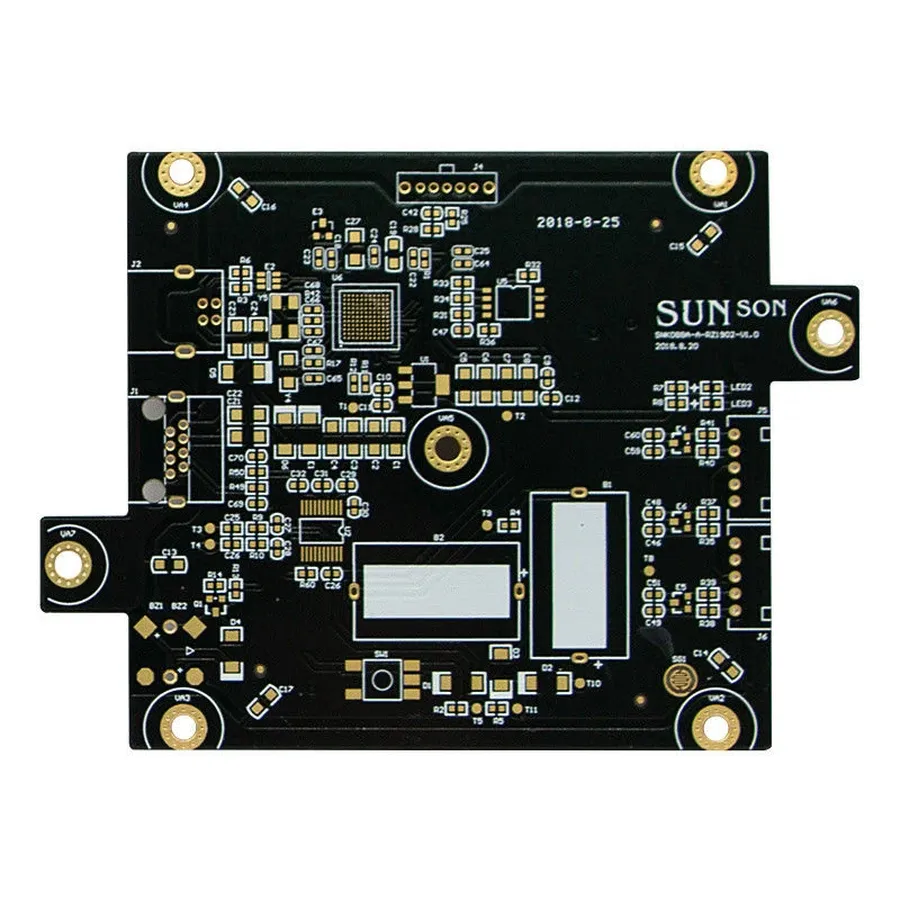
Effective drone circuit board design is paramount for ensuring optimal performance, reliability, and compliance with regulatory standards. This involves meticulous planning of PCB layout, strategic component placement, efficient heat management, robust signal integrity, and adherence to drone regulations.
Below are key considerations that should be taken into account during the design phase of a drone circuit board:
- PCB Layout
The layout of the printed circuit board (PCB) significantly impacts signal paths, noise levels, and overall circuit performance. Careful routing of traces, proper grounding techniques, and appropriate layer stackup are crucial. Trace width must be calculated to handle the expected current, and impedance matching is critical for high-frequency signals. Utilizing software like Altium Designer or Eagle for PCB layout is common. - Component Placement
The placement of components affects thermal management, signal integrity, and manufacturability. High-power components should be positioned to facilitate heat dissipation, while sensitive components should be isolated from noise sources. Grouping related components and placing them strategically can minimize trace lengths and reduce signal degradation. - Heat Management
Effective heat management is essential for preventing component damage and ensuring reliable operation. This may involve using heat sinks, thermal vias, or strategically placed copper pours. Proper consideration of the power dissipation of components is necessary to design for the thermal envelope of the device. - Signal Integrity
Signal integrity refers to the quality of the electrical signals transmitted through the circuit. Maintaining signal integrity involves minimizing signal reflections, crosstalk, and electromagnetic interference (EMI). This can be achieved through careful trace routing, impedance matching, and shielding of sensitive components. - Compliance with Drone Regulations and Standards
Drone circuit boards must comply with all applicable regulations and standards, which vary by region. These may include requirements related to radio emissions, electrical safety, and component certifications. Design must accommodate compliance testing requirements from entities such as the FCC or CE. - Material Selection
The materials used in the PCB have an impact on thermal properties, electrical insulation, and mechanical strength. FR-4 is commonly used for standard PCBs, but higher-performance materials may be required for more demanding applications, such as thermal clad for improved heat dissipation. - Testability and Maintainability
The design should include test points for verifying the proper operation of the circuit, and should make it easy to replace components during maintenance or repair. Test points can be strategically placed and easy to access. Modularity is an important factor for both testability and maintainability.
Adhering to these design considerations ensures that a drone circuit board operates safely, reliably, and within regulatory guidelines. A design checklist can help to ensure all considerations have been addressed.
DIY Drone PCB: From Concept to Creation
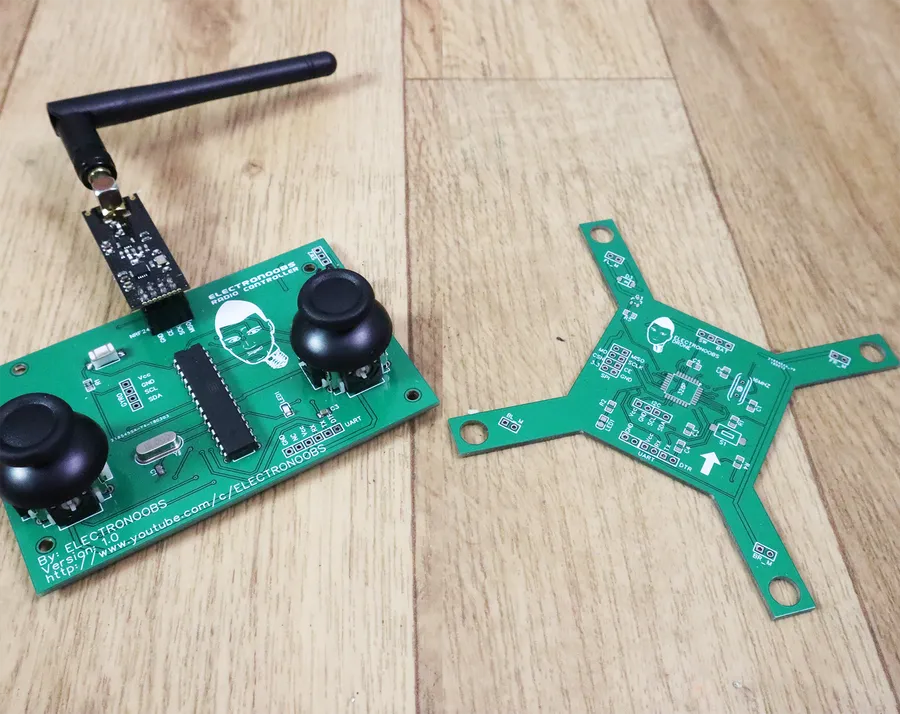
Creating a custom drone PCB is a challenging yet rewarding endeavor, allowing for tailored performance and features. This section outlines the process, from initial concept to a fully functional board, encompassing schematic design, PCB layout, fabrication, component assembly, and thorough testing. The information provided herein will help guide users in building their own drone circuit board.
- Schematic Capture
Begin by designing the electronic schematic using software such as KiCad, Eagle, or Altium Designer. This stage involves selecting the required components (microcontrollers, sensors, communication modules, etc.) and creating their electrical interconnections as per the drone's functionality. Ensure all components are compatible and their connections are properly defined for signal integrity. - PCB Layout
Translate the schematic into a physical PCB layout, determining component placement and trace routing. Consider factors like signal integrity, thermal management, and ease of assembly. The PCB layout software will allow you to place components, draw traces, create vias, and define board dimensions and layers. Efficient layout will minimize noise and signal interference. - Fabrication
Once the PCB layout is complete, generate the necessary Gerber files (industry-standard format) and send them to a PCB fabrication service, such as JLCPCB, PCBWay or similar. These manufacturers will use the Gerber files to produce the physical PCB with the copper traces and component pads as designed. Verify the design rules with the manufacturer’s capabilities to avoid any production errors. Ensure the board material and thickness meet your requirements. - Component Assembly
Assemble the electronic components onto the fabricated PCB. This includes soldering components (SMD or through-hole) at their designated locations. Depending on the complexity, this might require a reflow oven, soldering station, and careful handling of components. Inspect the joints for quality and any shorts or opens. - Testing
Test the assembled board for continuity and correct operation using a multimeter and logic analyzer. Initially, test the power rails followed by each functional block. Program the microcontroller and verify the functionality of each integrated system. Thorough testing is essential to guarantee a functional and reliable circuit.
Stage | Description | Tools/Software | Considerations |
---|---|---|---|
Schematic Capture | Define the electronic interconnections of the components | KiCad, Eagle, Altium Designer | Component compatibility, signal integrity |
PCB Layout | Translate schematic into physical layout | KiCad, Eagle, Altium Designer | Signal integrity, thermal management, assembly feasibility |
Fabrication | Physical production of the PCB | PCB Fabrication Service (JLCPCB, PCBWay) | Design rule check (DRC), material and layer specifications |
Component Assembly | Soldering of electronic components onto the PCB | Soldering station, reflow oven, tweezers | Soldering quality, proper component placement |
Testing | Verifying the functionality of the assembled board | Multimeter, logic analyzer | Power rail integrity, each functional block |
For building your own drone PCB, several resources are available. Software like KiCad is free and open source, ideal for hobbyists. Online communities and forums provide guidance and design tips. The component datasheets must be read carefully to ensure the application circuit design meets the component requirements. Additionally, many online vendors offer PCB prototyping services at affordable costs.
Drone Circuit Board Maintenance and Troubleshooting
Maintaining and troubleshooting drone circuit boards is essential for ensuring the longevity and reliability of your drone. This section provides guidance on diagnosing common issues, performing component replacements, and adopting preventative maintenance strategies.
- Visual Inspection
Begin with a thorough visual inspection of the circuit board for signs of physical damage such as cracks, burnt components, or loose connections. Use a magnifying glass for a detailed examination. - Power Supply Check
Verify the power supply to the board, checking the voltage with a multimeter against the specified rating. A faulty power supply is a common cause of circuit board malfunction. - Component Testing
Test individual components such as resistors, capacitors, and integrated circuits (ICs) using a multimeter or component tester. Identify components that have failed or are outside their specifications. - Connection Issues
Check all solder joints, connectors, and wiring for continuity using a multimeter. Ensure secure connections as loose or corroded contacts can disrupt signals. - Sensor Calibration
Calibrate sensors such as the IMU (Inertial Measurement Unit) and GPS if experiencing issues with stability or location accuracy. Follow the manufacturer's instructions for calibration procedures. - Firmware Updates
Ensure that the firmware for the flight controller and other components is up-to-date. Outdated firmware can cause compatibility issues or operational errors. - Heat Management
Monitor the operating temperature of the board, especially during and after prolonged use. Overheating can damage components and lead to erratic behavior. Employ heat sinks or cooling fans if necessary.
When replacing components, ensure the new components match the specifications of the original parts. Use proper soldering techniques to ensure secure and reliable connections. Avoid static discharge which can damage sensitive components. Regular cleaning with a soft brush and isopropyl alcohol can help prevent build-up of dust and debris.
Frequently Asked Questions About Drone Circuit Boards
This section addresses common questions and concerns regarding drone circuit boards, providing clear and concise answers to enhance understanding and guide decision-making for drone enthusiasts and professionals.
- What exactly is a drone PCB (Printed Circuit Board)?
A drone PCB is the foundational board within a drone that mechanically supports and electrically connects electronic components. It's the central hub for power distribution, flight control, sensor data processing, and communication, forming the 'brain' of the drone. - How do I choose the right power distribution board (PDB) for my drone?
Selecting the correct PDB requires careful consideration of your drone's power requirements. Ensure the PDB's current rating meets or exceeds the combined demands of all connected components, like motors and ESCs. Additionally, match the PDB's input voltage with your battery and verify that it has the necessary output connectors. - What kind of circuits are typically used in drones?
Drones utilize a variety of circuit types. These include: 1. Power circuits for battery management and voltage regulation. 2. Control circuits for processing signals from the remote controller and sensors. 3. Communication circuits for data transmission, and 4. Motor control circuits, specifically the Electronic Speed Controllers (ESCs). - What are the essential components needed to build my own drone?
Building a drone necessitates a flight controller, ESCs, motors, propellers, a battery, a receiver, and a transmitter (remote controller). Additionally, a frame, a suitable power distribution system, and wiring are crucial. Depending on your goal, you may also need sensors and cameras. - Can I repair a damaged drone circuit board myself?
Simple repairs such as replacing a capacitor or connector may be feasible for experienced individuals. However, more complex repairs, especially involving microcontrollers or complex integrated circuits, usually require specialized tools and technical expertise best left to a professional repair service. - What are the key factors to consider when designing a custom drone PCB?
When designing a custom PCB, crucial considerations include proper component placement to minimize interference, effective heat management for reliable operation, and a layout that ensures signal integrity. Compliance with drone regulations and standards is also paramount to ensure safety and operational legality. Additionally, choosing robust materials and surface finishes is essential for withstanding operational conditions. - How can I extend the life of my drone’s circuit board?
To extend the lifespan of your drone's circuit board, ensure proper heat dissipation during use to prevent thermal stress, shield it from physical impacts, moisture, and electrostatic discharge (ESD). Regular cleaning to prevent corrosion and adhering to the drone’s operating voltage and current limits is essential. Proper storage and handling practices are equally vital.
Future Trends in Drone Circuit Boards
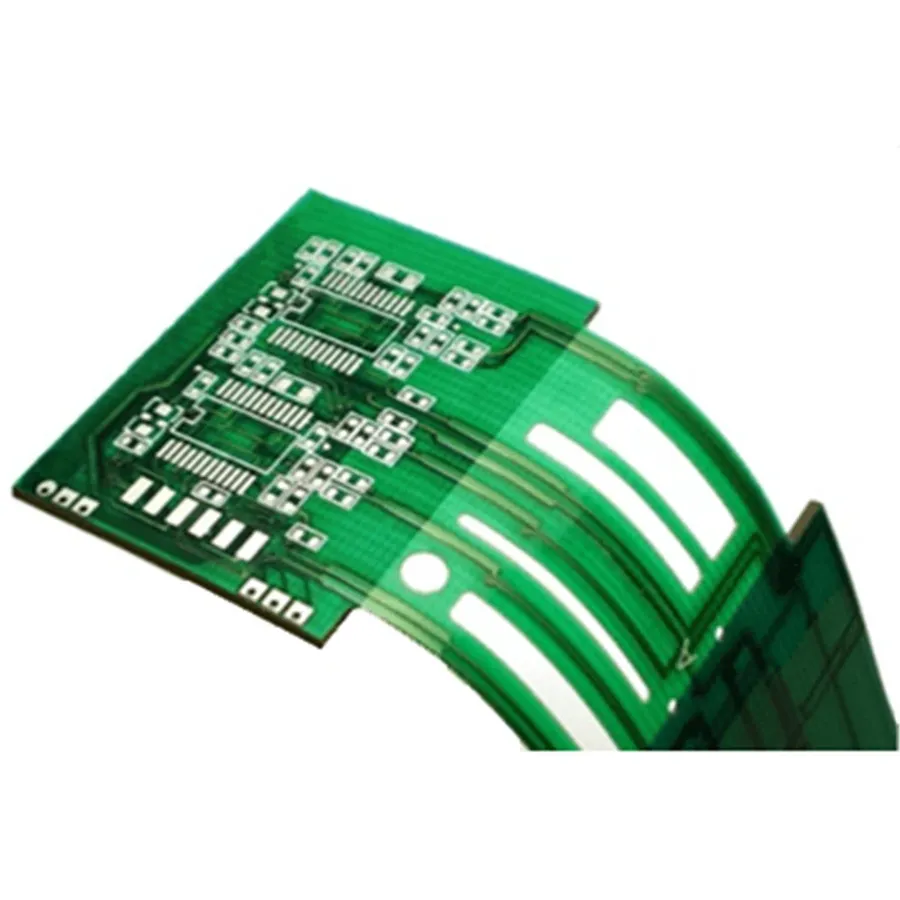
The landscape of drone circuit boards is rapidly evolving, driven by demands for enhanced performance, efficiency, and integration. These future trends are poised to significantly impact drone capabilities and applications, pushing the boundaries of what’s currently achievable.
Key advancements are focused on several critical areas:
- Enhanced Integration
Future drone circuit boards will feature higher levels of integration, combining multiple functionalities onto a single chip or board. This consolidation reduces size, weight, and complexity, leading to more compact and efficient drone designs. For example, combining the flight controller, ESC and power distribution onto a single board reduces failure points and simplifies assembly. - Efficient Energy Management
Energy management is a crucial focus in drone technology. Future boards will employ more sophisticated power management ICs and techniques to maximize flight time and minimize energy loss. This includes optimized voltage regulation, battery management systems, and wireless power transfer technologies. - Increased Processing Power
Drones are becoming more intelligent, requiring enhanced processing capabilities for complex tasks such as real-time image processing, autonomous navigation, and AI-driven flight control. Future circuit boards will incorporate more powerful microcontrollers and AI accelerators to meet these demands. This includes leveraging edge computing capabilities directly on the drone. - Innovative Designs for Increased Performance
Beyond traditional designs, innovations such as flexible PCBs, 3D-printed circuit boards, and advanced materials will become more prevalent. These designs enable new drone forms, improved thermal management, and increased mechanical resilience. For instance, flexible boards can accommodate curved surfaces within the drone frame, and 3D-printed boards can be highly customized. - Improved Sensor Integration
Future drones will integrate a wider range of advanced sensors on their circuit boards. This includes higher-resolution IMUs, more accurate GPS modules, and environmental sensors for obstacle avoidance and data collection, further expanding their operational versatility. The move to more integrated sensor modules will reduce the total board space required and further improve the drones capabilities.
These advancements will collectively drive the next generation of drones, making them more capable, efficient, and versatile across various applications, from recreational use to industrial and commercial deployment. The incorporation of AI and edge computing is anticipated to be a major shift in the sector. These advancements are underpinned by progress in materials science, microelectronics, and software engineering.
In conclusion, the drone circuit board is the nerve center of any drone, dictating its functionality and performance. Whether you are a hobbyist building your first drone or a professional utilizing drones for complex tasks, understanding the nuances of drone PCB technology is crucial. This comprehensive guide aims to empower you with the information you need to select, design, and maintain drone circuit boards, ensuring that your aerial endeavors are not just successful but cutting-edge. By staying abreast of these developments, you'll unlock the full potential of drone technology, pushing the boundaries of what's possible.
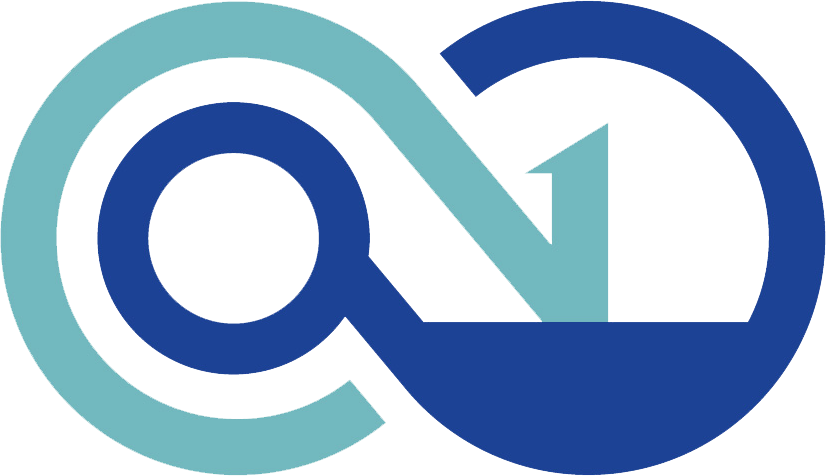