Mobile PCB Boards: Design, Types, and Key Components Explained
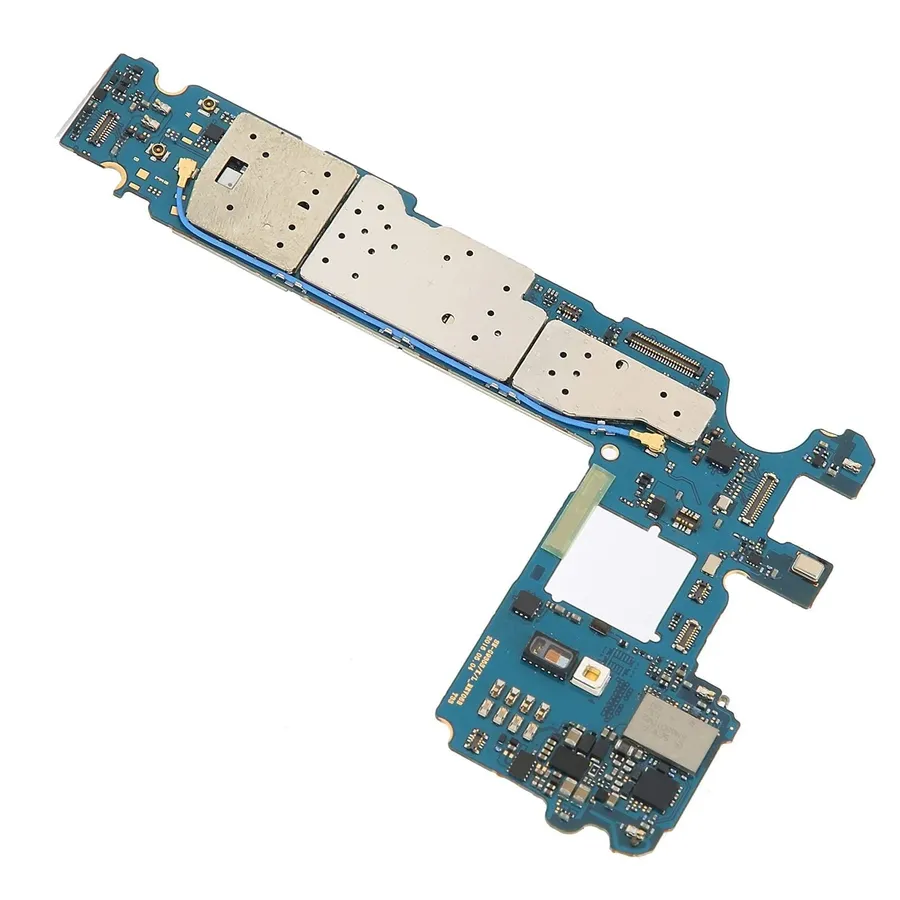
The mobile PCB board, a marvel of modern engineering, is the unsung hero powering our smartphones. These intricate circuit boards are the foundation upon which all mobile device functionality is built, interconnecting thousands of tiny components that enable us to communicate, access the internet, and so much more. This article dives deep into the world of mobile PCB boards, exploring their various types, designs, key components, and manufacturing processes to provide you with a complete understanding of this crucial element in mobile technology.
What is a Mobile PCB Board?
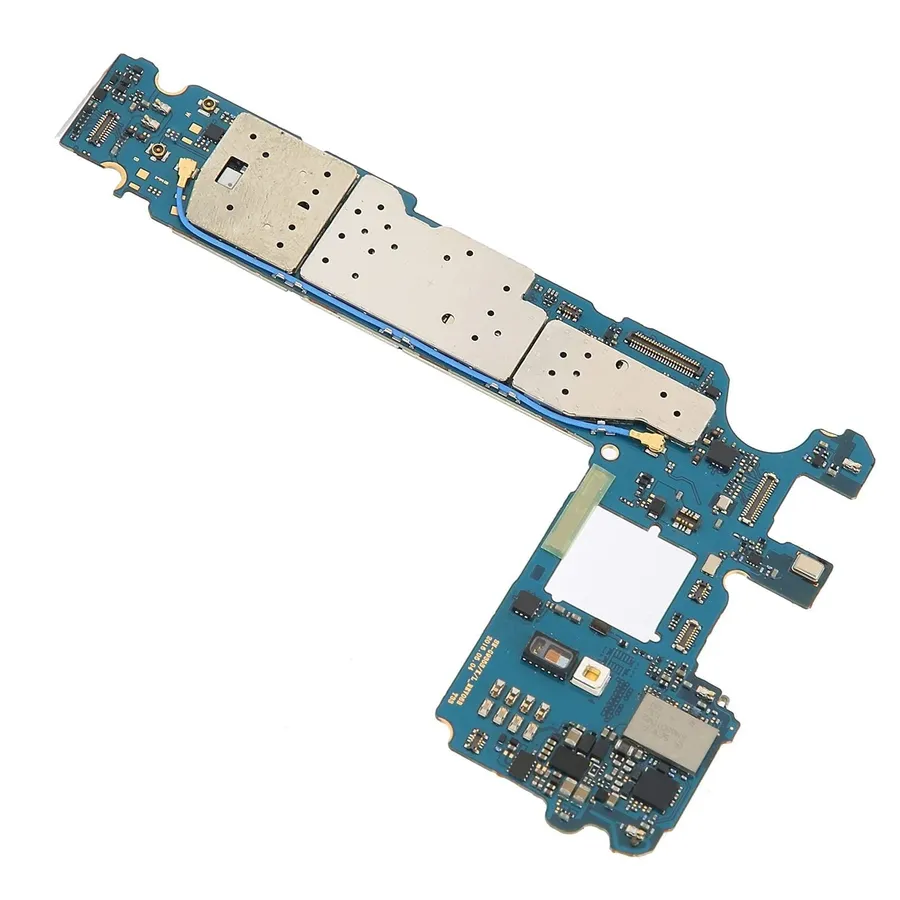
A mobile Printed Circuit Board (PCB) is the foundational component within a smartphone, serving as the central platform for mounting and electrically connecting all the electronic parts. This multi-layered board facilitates the intricate communication and power distribution necessary for a mobile device's functionality, essentially acting as its nervous system, and allowing all the individual components to work together seamlessly to deliver a functional product.
The mobile PCB is critical to the operation of a smartphone because it ensures both structural support for all electrical components and provides the electrical pathways required for signal transmission and power delivery. Without it, the mobile phone could not exist or function.
Types of Mobile PCB Boards
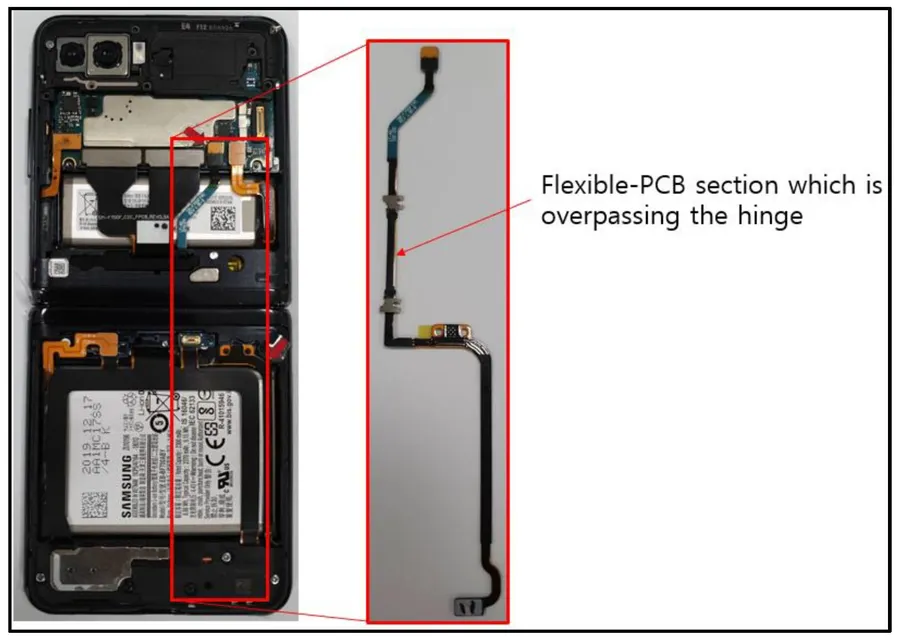
Mobile devices employ various types of Printed Circuit Boards (PCBs), each tailored to specific needs and design constraints. These PCBs primarily fall into three categories: rigid, flexible, and rigid-flex. The selection of PCB type is crucial for optimizing performance, space utilization, and overall device functionality. Understanding the characteristics of each type is essential for designing and manufacturing efficient mobile devices.
Type | Description | Advantages | Disadvantages | Typical Applications |
---|---|---|---|---|
Rigid PCBs | Made from solid, inflexible materials like FR-4. Commonly multi-layered for complex circuitry. | Cost-effective, durable, high component density possible, well-established technology. | Limited flexibility, prone to damage from bending, can be bulky. | Main logic board, power management sections, areas with minimal movement. |
Flexible PCBs | Constructed from thin, flexible substrates like polyimide. Capable of bending and flexing without damage. | Lightweight, compact, excellent bending capabilities, high design freedom, good for high-density interconnects. | More expensive than rigid PCBs, less durable, complex assembly required. | Connecting cameras to main board, display connections, buttons, areas requiring flexibility. |
Rigid-Flex PCBs | Combines rigid and flexible sections in one PCB. Integrates the benefits of both types. | Integrates rigid and flexible sections which reduces the need for connectors, offers design flexibility, reliable connection, space-saving. | High cost, complex manufacturing process, design challenges. | Complex interconnections between multiple sections, devices with multiple moving parts. |
Key Components on a Mobile PCB Board
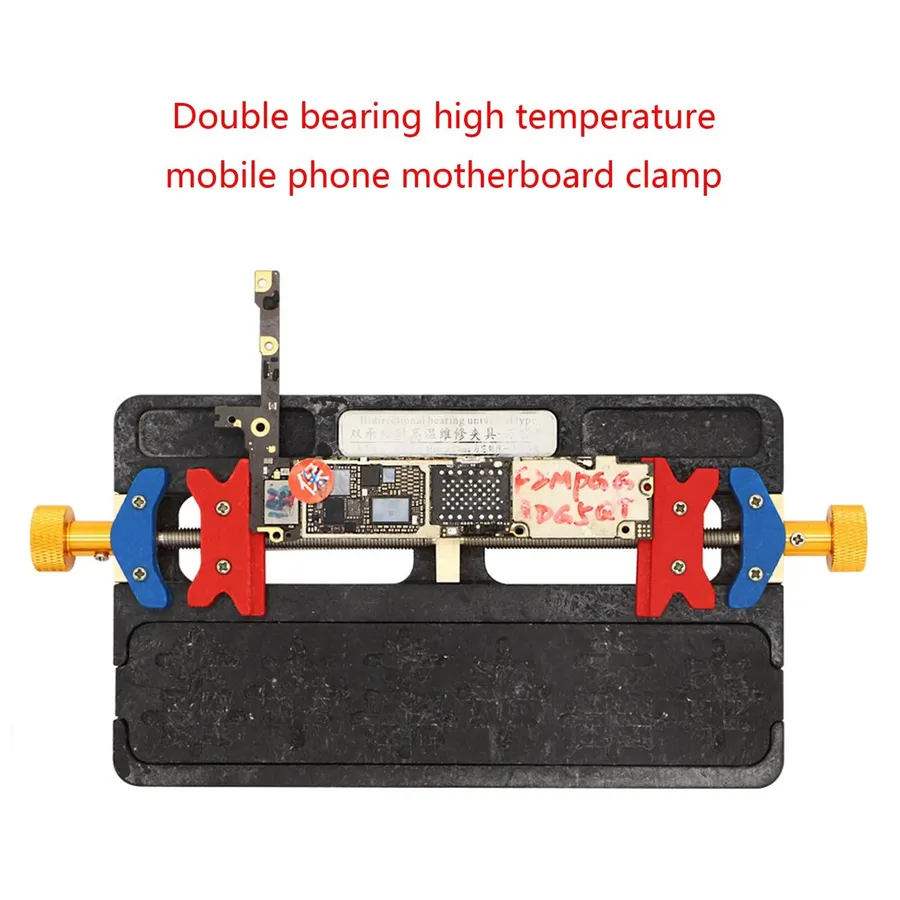
The mobile PCB (Printed Circuit Board) is the central hub of a smartphone, housing numerous critical components that dictate its functionality. These components work synergistically to enable communication, processing, storage, and user interaction. Understanding these key elements and their arrangement is essential for comprehending the overall operation and performance of a mobile device.
Component | Function | Impact of Placement |
---|---|---|
Application Processor (AP) | The 'brain' of the phone; executes instructions, handles calculations, and manages overall device operations. | Central placement on the PCB to optimize thermal dissipation and minimize signal delays to connected peripherals. |
RAM (Random Access Memory) | Provides temporary data storage for active applications and processes, enabling quick access for the AP. | Proximity to the AP is vital to maximize data transfer speed and minimize latency, often directly connected. |
ROM (Read Only Memory) | Stores the device's firmware, operating system, and other essential data, retaining information even when the power is off. | Usually placed to minimize interference with active circuits, but close enough for efficient booting. |
Power Management IC (PMIC) | Regulates power distribution to all components, managing charging, battery health and optimizing battery life. | Strategically located near the battery connector and other power-hungry components to minimize loss and maintain voltage integrity. |
Connectivity Modules (Wi-Fi, Bluetooth, Cellular) | Enable wireless communication via various protocols for network access and data exchange. | Positioned to avoid interference between modules and with other high-frequency signals, often near the antenna feeds. |
Sensors (Accelerometer, Gyroscope, Magnetometer) | Detect device orientation, motion, and environmental conditions, enabling user-interface and application functionality. | Placed at locations to enable accurate data collection, often situated at the edges or corners of the board for spatial sensitivity. |
Mobile PCB Board Layers and Materials
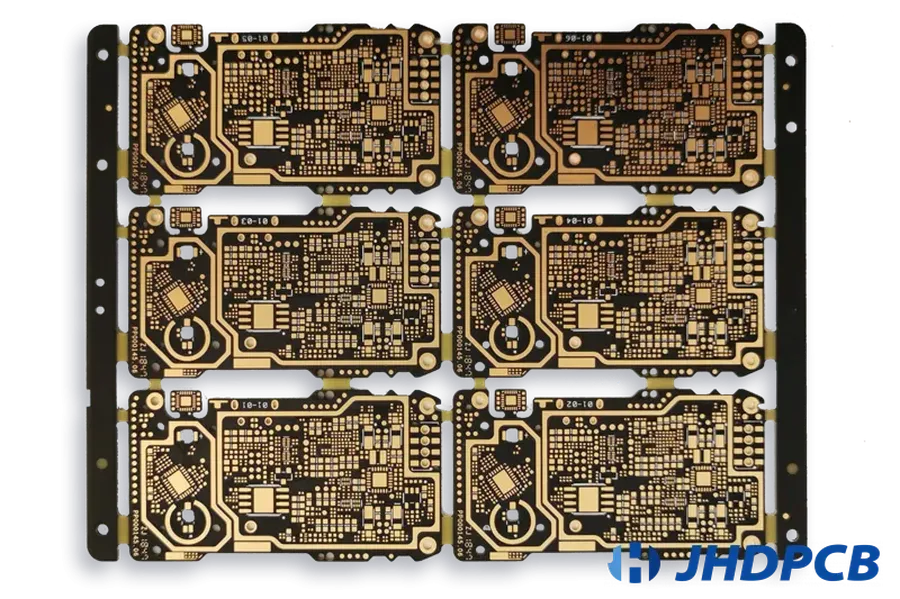
Mobile printed circuit boards (PCBs) are typically multi-layered structures, designed to optimize space and performance within compact mobile devices. The selection of materials and the number of layers are critical factors influencing the overall functionality and reliability of the mobile phone.
Layer Type | Typical Material | Function | Thickness Range |
---|---|---|---|
Core Layer(s) | FR-4 (Fiberglass Reinforced Epoxy) or Polyimide | Provides structural support and insulation between conductive layers. | 50 μm - 200 μm |
Copper Layer(s) | Copper | Forms the conductive traces, pads, and planes for signal and power distribution. | 10 μm - 35 μm |
Prepreg Layer(s) | Epoxy resin with fiberglass or other reinforcing material | Bonds core and copper layers together and provides insulation. | 25 μm - 100 μm |
Solder Mask Layer(s) | Epoxy-based polymer | Protects conductive traces from oxidation, corrosion, and short circuits and facilitates solderability. | 10 μm - 25 μm |
Silkscreen Layer(s) | Epoxy ink | Provides component identification, polarity markings, and test points on the PCB. | 5 μm - 10 μm |
The number of layers in a mobile PCB can range from 4 to 12 or more, depending on the complexity of the device and its required functionality. Higher layer counts allow for more intricate routing, improved signal integrity, and better power distribution. Common layer configurations include 4-layer, 6-layer, and 8-layer PCBs. The materials are carefully selected to provide a balance between mechanical strength, electrical properties, thermal performance, and cost.
Copper traces are essential for electrical connectivity within mobile PCBs. These thin conductive lines, formed by etching a copper layer, facilitate the flow of electrical signals and power between components. Trace width and spacing are carefully designed to ensure signal integrity, minimize interference, and handle the required current load. The thickness of the copper layer impacts current carrying capacity, with thicker copper being used for power traces and thinner copper being used for signal traces.
Material selection is paramount for performance and reliability. FR-4 is widely used because of its cost-effectiveness, good mechanical strength, and electrical properties. Polyimide is a premium material used in high-performance mobile devices because of its superior thermal stability, flexibility, and high electrical resistance. The performance of the board can be affected by the material and layer selection, especially the high-frequency signal propagation and thermal management.
Mobile PCB Design Considerations
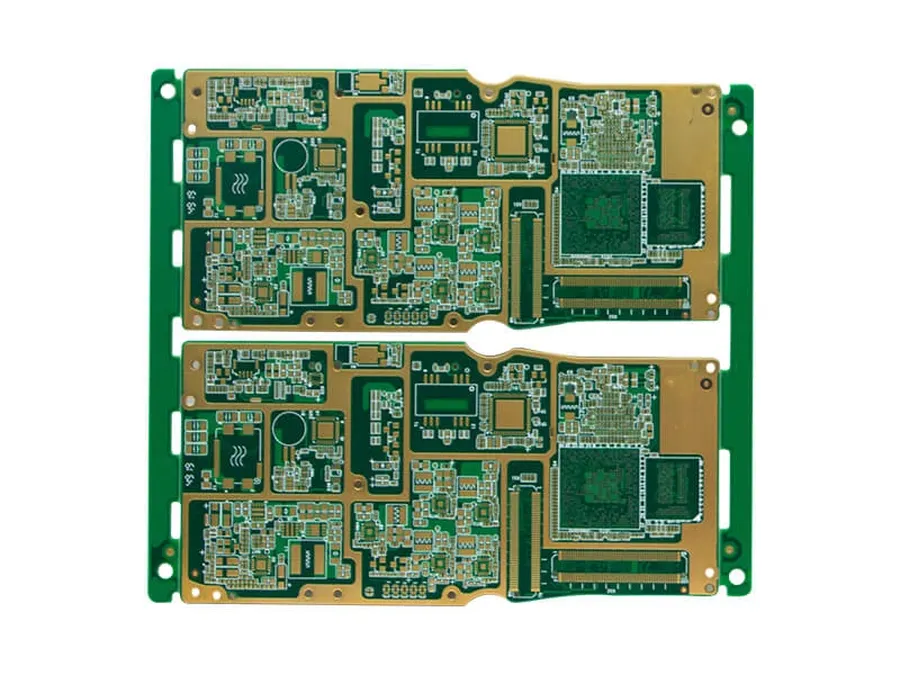
Effective mobile PCB design hinges on several critical factors that directly influence the performance and reliability of the final product. These considerations include miniaturization, signal integrity, thermal management, and power consumption, each demanding careful attention to achieve optimal device functionality within the constraints of a compact mobile form factor.
- Miniaturization
The relentless push for smaller and lighter mobile devices necessitates highly compact PCB designs. This involves utilizing advanced technologies such as high-density interconnect (HDI) techniques, fine-pitch components, and multi-layer boards to maximize component density while minimizing the overall board footprint. Successful miniaturization directly translates to more compact and user-friendly devices. - Signal Integrity
Maintaining signal integrity is crucial for ensuring reliable data transmission across the PCB. Factors such as trace impedance, signal reflections, crosstalk, and electromagnetic interference (EMI) can severely degrade signal quality. Therefore, careful design practices are necessary to minimize these effects, such as controlled impedance routing, proper trace spacing, and the strategic placement of decoupling capacitors. Inadequate signal integrity can lead to performance issues, including data loss, instability, and reduced data rates. - Thermal Management
Mobile devices generate significant heat during operation, and effective thermal management is essential to prevent component overheating and ensure long-term reliability. This involves employing techniques such as thermal vias, heat sinks, and careful component placement to distribute heat efficiently. Proper thermal management not only prevents component failure but also minimizes performance throttling that can occur when devices overheat. - Power Consumption
Power efficiency is critical for extending battery life in mobile devices. Minimizing power consumption in PCB design involves using low-power components, optimizing power delivery networks, and incorporating power management ICs (PMICs). In addition, optimizing clocking and controlling sleep states can greatly improve battery performance. Reducing energy demand is essential for delivering enhanced user experience and extended device usability.
Manufacturing Process of Mobile PCB Boards
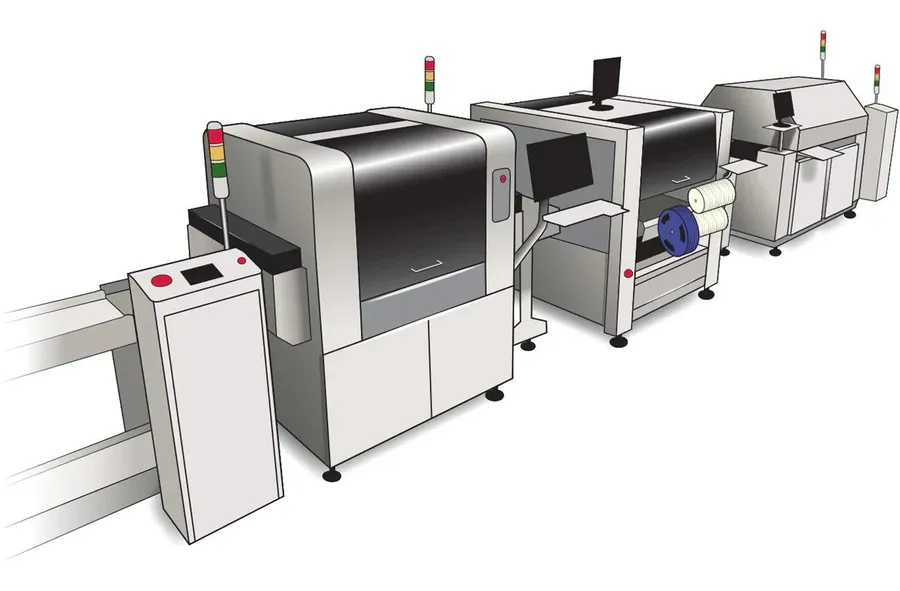
The fabrication of mobile PCB boards is a complex, multi-stage process requiring high precision and adherence to strict quality controls. This process transforms raw materials into the intricate circuit boards that are the heart of mobile devices. Each step is crucial to ensure the performance and reliability of the final product.
- Design and Layout
The manufacturing process begins with the design phase, where engineers create detailed schematics of the PCB using specialized CAD software. This includes defining the board's dimensions, component placement, and the intricate network of conductive traces. Precise layouts are critical for optimizing signal integrity and component functionality. - Material Selection
Based on the design specifications, the appropriate base materials are chosen. Common materials for mobile PCBs include FR-4 and polyimide, each offering different electrical and thermal properties. Copper foil is also selected for the conductive layers, usually in a controlled thickness. - Image Transfer (Etching)
The PCB layout is transferred onto the copper-clad base material using photolithography. The copper surface is coated with a photoresist material, exposed to UV light through a mask of the circuit pattern, and then the exposed photoresist is removed. The uncovered copper is then etched away using chemical solutions. - Layer Lamination
In multi-layer PCBs, multiple etched layers are stacked together using heat and pressure. Insulating materials like prepreg are used between the layers to create a cohesive board structure. This process bonds the layers together permanently. - Drilling
Precise holes for component mounting and through-hole vias are drilled using automated drilling machines. These holes connect different layers of the PCB, facilitating electrical connections between components and circuits. - Plating
After drilling, the holes and other conductive surfaces are plated with copper. This process enhances the electrical conductivity of vias and ensures reliable connections between layers. Additional plating, such as gold or nickel, may be applied to protect against corrosion and improve solderability. - Solder Mask Application
A protective solder mask is applied to the PCB, leaving only the component pads exposed. This prevents solder bridges during component assembly and protects the traces from environmental damage. The solder mask is usually green, but other colors are also available. - Silkscreen Printing
A silkscreen layer is applied to the board, which provides essential information, such as component references, logos, and test points. This is vital for both manual and automated assembly, helping in the correct identification and placement of components. - Final Testing and Inspection
The completed PCBs undergo rigorous testing, including electrical tests, dimensional checks, and visual inspections to identify any defects. These quality control measures ensure that each board meets the required specifications before being used in mobile devices. - Panelization
Often, multiple individual PCBs are manufactured together on a larger panel to improve manufacturing efficiency. After all processes, these individual PCB will be separated, and ready for component assembly.
Mobile PCB Board Testing and Quality Control
Rigorous testing and quality control are paramount in ensuring the reliability and performance of mobile PCB boards. These processes verify that the manufactured boards meet stringent specifications and operate correctly under various conditions, guaranteeing the overall quality of mobile devices. Comprehensive testing procedures prevent defects, ensuring that the PCB will support the intended lifespan of the mobile phone.
The following table details common testing procedures for mobile PCB boards:
Test Type | Description | Purpose |
---|---|---|
Electrical Testing | Includes continuity testing, impedance testing, and shorts testing. | Verifies electrical connections, ensuring that signals flow correctly and that there are no unintended shorts or opens. |
Functional Testing | Simulates real-world operating conditions using specialized testing fixtures and software. | Confirms that all components on the PCB function correctly and interact as designed under realistic operational conditions. |
Visual Inspection | Detailed examination of the PCB using microscopes and cameras. | Checks for physical defects such as cracks, solder joint issues, misaligned components, and any surface contamination. |
X-Ray Inspection | Uses X-ray technology to examine internal layers and components | Identifies hidden defects within the PCB structure or under BGA components that are not visible with standard visual inspection. |
Environmental Testing | Subjects PCBs to extreme temperature, humidity, and vibration conditions. | Determines the boards' ability to withstand challenging environmental conditions over their expected lifespan. |
Mobile PCB boards must conform to specific industry standards to ensure safety and reliability. These standards provide guidelines for material selection, manufacturing processes, and performance criteria. Adherence to these standards is a prerequisite for the boards to be used in consumer electronics. Common Standards include IPC-A-600 which defines acceptable quality for PCBs and is the industry standard used by most manufacturers and PCB designers.
Frequently Asked Questions About Mobile PCB Boards
This section addresses common queries regarding mobile PCB boards, offering clear and concise answers to enhance understanding of their role and function in mobile devices.
- What exactly is a PCB board in a mobile phone?
A PCB (Printed Circuit Board) in a mobile phone is a foundational component that serves as a base for mounting and electrically connecting all the electronic parts, such as the processor, memory, and communication modules. It provides the necessary pathways for signals and power to flow between these components, enabling the device to operate. - How can I identify the different components on a mobile PCB board?
Identifying components on a mobile PCB requires careful observation. The largest chip is often the Application Processor (AP). Memory chips (RAM and ROM) are also typically rectangular and are often in close proximity to the AP. Power Management ICs (PMIC) are involved in power distribution and can be identified by their specific markings and location. Connectivity modules, sensors and other components vary in size and shape and are labelled with manufacturer part numbers. Datasheets can be referenced to identify components. - How many layers are typically present in a mobile PCB board?
Mobile PCBs are typically multi-layered, with common layer counts ranging from 6 to 12 layers or more. These layers are essential for creating complex routing paths and separating power, ground, and signal planes. The multi-layer structure allows for higher component density and improved signal integrity, critical for the compact designs of mobile devices. - What are the main steps involved in manufacturing mobile PCB boards?
The manufacturing process starts with design and layout, followed by etching to define the copper traces, plating to enhance conductivity and mechanical robustness, lamination to stack the layers, and finally assembly where electronic components are mounted and soldered onto the board. These processes require precision and advanced technology. - Are mobile PCB boards repairable, and what does mobile pcb board replacement entail?
Mobile PCB board repair is complex due to the miniaturization of components, and typically requires specialist equipment and expertise. Mobile PCB board replacement involves removing the damaged board and installing a new one, this is a delicate procedure and can be a costly process, sometimes even more expensive than replacing the entire device. - What materials are typically used to construct a mobile PCB board?
Common materials for mobile PCBs include FR-4 (a fiberglass-reinforced epoxy laminate), and polyimide, chosen for its flexibility and thermal stability. Copper is used for the conductive traces. Material selection is based on performance, durability and reliability requirements, as well as cost. - What is the difference between rigid, flexible, and rigid-flex PCB boards, and which is used in mobile phones?
Rigid PCBs, such as FR-4, offer structural support, while flexible PCBs use materials such as polyimide which allows for bending and flexing. Rigid-flex PCBs combine both characteristics. Mobile phones often use a combination of rigid and flexible PCBs to connect different sections of the phone, and to accommodate small and complex form factors.
Future Trends in Mobile PCB Technology
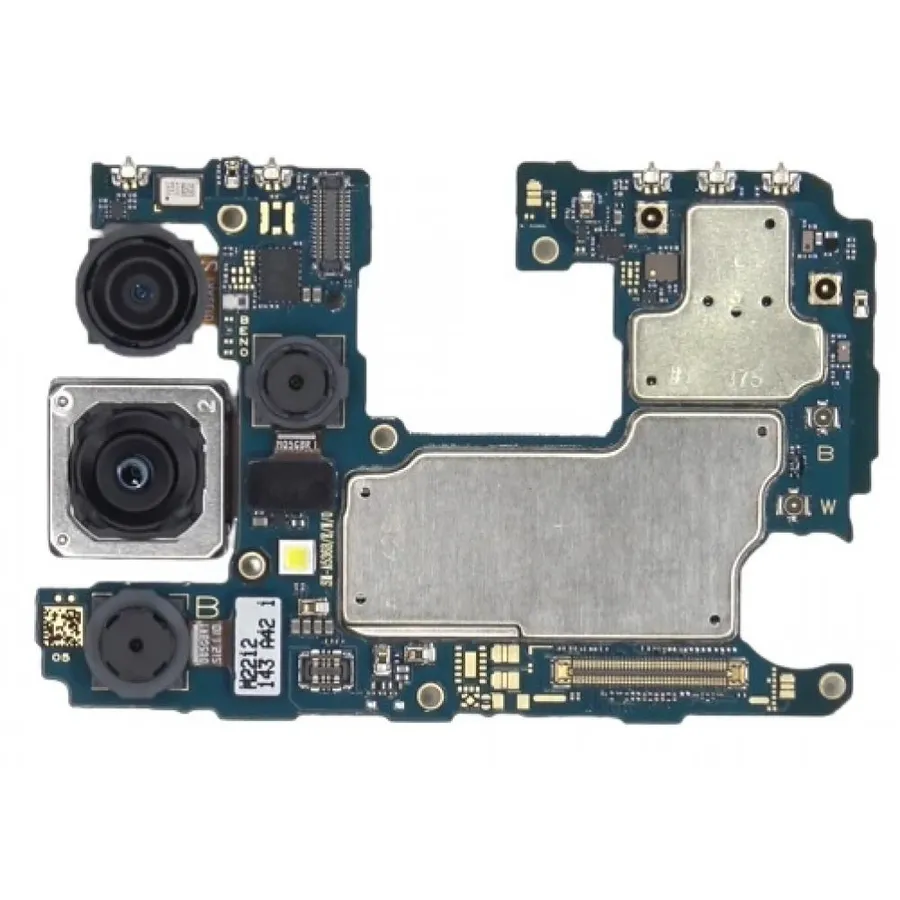
The mobile PCB industry is in constant evolution, driven by the relentless demand for smaller, faster, and more efficient devices. Future trends in mobile PCB technology are focused on addressing these demands through advanced materials, innovative interconnect solutions, and enhanced compatibility with emerging communication standards.
- Advanced Materials
The quest for improved performance and miniaturization is pushing the boundaries of materials science. Future mobile PCBs will likely incorporate materials with superior dielectric properties, enhanced thermal conductivity, and increased mechanical flexibility. Examples include advanced ceramics, liquid crystal polymers (LCP), and modified epoxies, which enable higher signal speeds, better heat dissipation, and greater design freedom. - Higher Density Interconnects (HDI)
HDI technology will continue to play a pivotal role in achieving smaller and more powerful mobile devices. Future trends point towards finer lines and spaces, microvias, and stacked vias, enabling a higher density of components on the PCB. These advancements will improve electrical performance and reduce the overall size of the board. This also includes the increased use of via-in-pad technology which maximizes routing density. - Integration of Embedded Components
Embedding passive components such as resistors, capacitors, and inductors directly within the PCB substrate is an emerging trend. This approach will significantly reduce the space required for discrete components on the surface, allowing for more compact and efficient circuit designs. Embedding will also help minimize parasitic effects by shortening the interconnections, thus improving signal integrity. - 5G and Beyond Compatibility
The proliferation of 5G and future generations of communication technologies necessitates the development of PCBs capable of handling higher frequencies and data rates. This requires materials with low signal losses at high frequencies, novel interconnects, and improved shielding techniques to minimize electromagnetic interference. Mobile pcb boards will be designed to be compatible with evolving technologies, ensuring seamless integration and performance. - Thermal Management Innovations
As mobile devices become more powerful, effective thermal management strategies are critical. Future PCBs will likely incorporate innovative cooling solutions, such as embedded heat spreaders, microfluidic cooling channels, and materials with higher thermal conductivity. These measures will help maintain optimal operating temperatures and enhance the reliability of mobile pcb boards. - Sustainability and Eco-Friendly Practices
Increased focus on sustainability and environmental responsibility is driving the adoption of eco-friendly manufacturing processes and materials in the mobile PCB industry. This includes the use of recycled materials, lead-free solders, and water-based processes to reduce environmental impact.
The mobile PCB board is a complex and integral part of any mobile device. Understanding its design, components, and manufacturing is crucial for appreciating the technological marvel that fits in our pockets. From supporting critical components and enabling electrical connections to managing power and performance, the mobile pcb board is a vital foundation. As technology continues to evolve, mobile PCB boards will undoubtedly continue to push the boundaries of what’s possible in the palm of our hands. With advancements in materials, design and manufacturing, we can expect even smaller, more powerful, and more efficient mobile devices in the future, all anchored by the humble, yet essential, mobile pcb board.
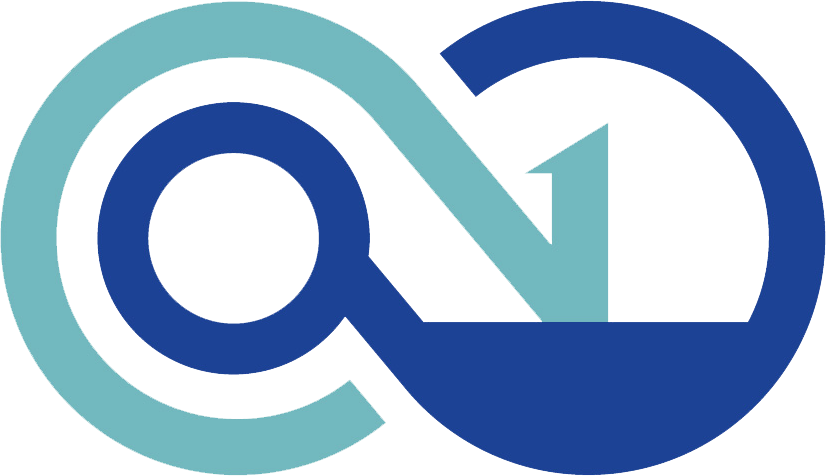