Precision in Electronics: Understanding Drilled PCB Manufacturing
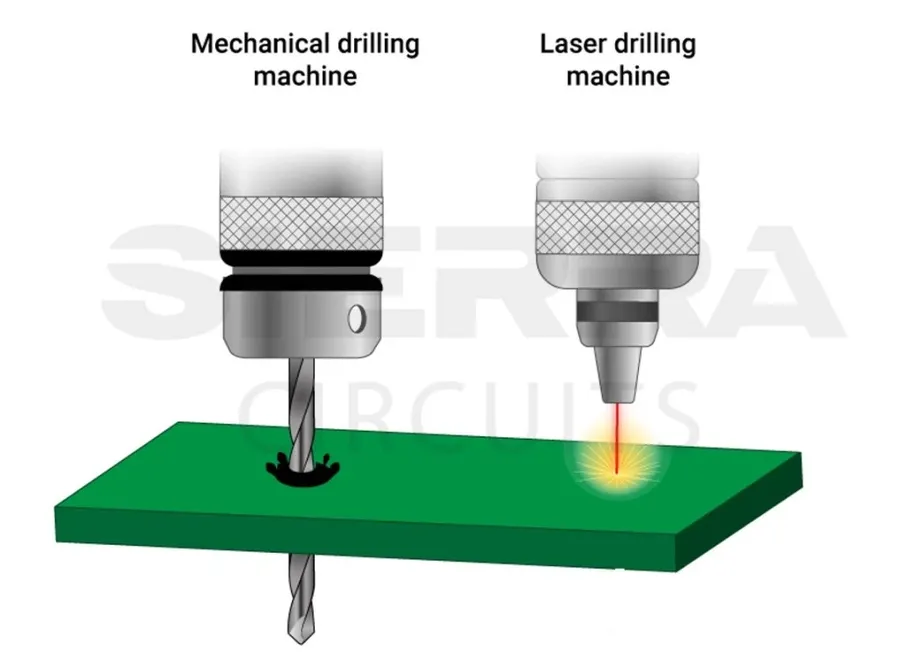
The intricate dance of electrons within electronic devices owes much to the precision of the drilled PCB. From smartphones to satellites, the foundation of every circuit board relies on accurately placed holes. These seemingly simple perforations are vital for component mounting, signal transmission, and the overall functionality of electronic systems. This article will dive deep into the world of drilled PCB, revealing the processes, challenges, and advancements that underpin modern electronics, connecting the engineering marvel to our daily lives.
The Fundamental Role of Drilled PCB
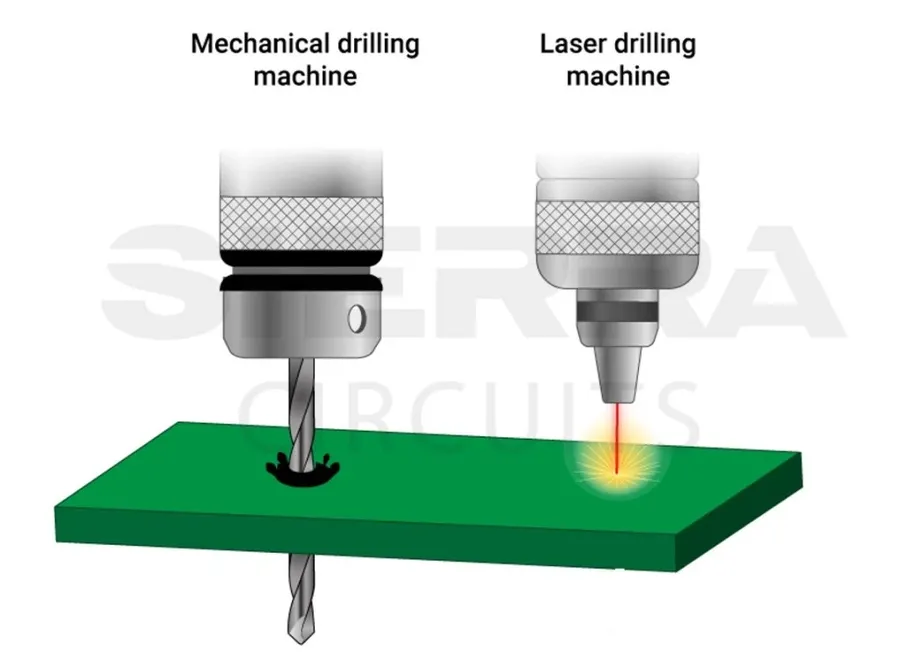
Drilled holes in Printed Circuit Boards (PCBs) are fundamental to their functionality, serving critical roles in component mounting, electrical interconnections, and mechanical stability. The precision of these drilled features is paramount, directly influencing the performance and reliability of the final electronic product. Deviations from specified hole parameters can lead to issues ranging from poor solder joints to catastrophic circuit failures.
Fundamentally, drilled holes on PCBs facilitate the physical insertion and secure attachment of electronic components. Through-hole components, for example, rely on these precisely drilled apertures to establish a stable mechanical interface with the PCB substrate. Moreover, these holes provide the pathways for electrical signals to traverse between different layers of a multi-layered PCB, allowing for complex circuit designs to be realized. In addition to electrical and component mounting functionality, the drilled features also provide mechanical support that is crucial in preventing structural integrity issues with the assembled board.
Mechanical PCB Drilling: The Most Common Method
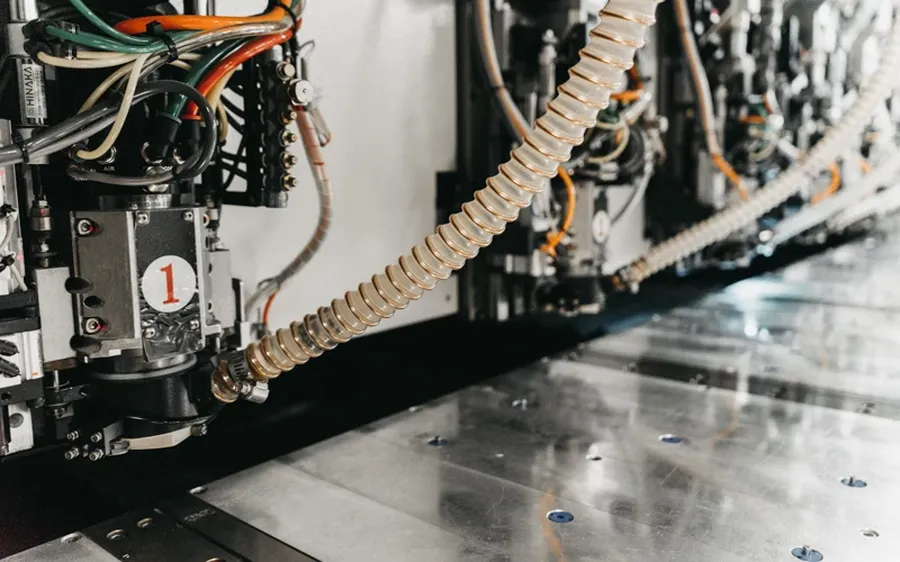
Mechanical drilling is the predominant method for creating holes in printed circuit boards (PCBs), essential for component mounting, electrical connections, and mechanical support. This process involves using precision drill bits, controlled spindle speeds, and accurate depth management to achieve high-quality and consistent hole fabrication. The selection of drill bit types directly influences the quality and precision of the drilled holes, making it a critical factor in PCB manufacturing.
Drill Bit Type | Material | Application | Advantages | Disadvantages |
---|---|---|---|---|
Solid Carbide | Tungsten Carbide | General PCB Drilling | High hardness, good wear resistance, suitable for high-speed drilling. | More expensive than HSS, can be brittle |
High-Speed Steel (HSS) | Steel Alloy | Less demanding applications, prototype PCBs | Lower cost, more flexible. | Lower hardness, lower wear resistance, not ideal for high-volume production |
Diamond Coated | Tungsten Carbide with Diamond Coating | Highly abrasive materials, FR-4 | High wear resistance, reduces burrs and rough hole walls | Expensive |
Cobalt Steel | Steel alloyed with Cobalt | Difficult materials, high heat applications | Heat resistance, suitable for materials that generate high heat during drilling | More expensive than HSS |
The mechanical drilling process involves several key stages. First, the PCB is securely positioned on the drilling machine. A drill bit, chosen based on the material and required hole size, is then mounted on the spindle. The machine then precisely controls the spindle speed and the feed rate as the drill penetrates the board, creating the hole. Accurate depth control is crucial to avoid damaging the underlying layers of the PCB. Post-drilling, the boards are cleaned to remove any debris from the drilling process. This mechanical process allows the creation of highly precise and repeatable holes, ensuring reliable connections and proper component alignment. Drill selection is crucial as it impacts hole wall quality, diameter accuracy, and the overall yield of the drilling process. Proper maintenance and replacement schedules for drill bits are also critical to maintain the necessary precision and quality.
Key Parameters in PCB Drilling
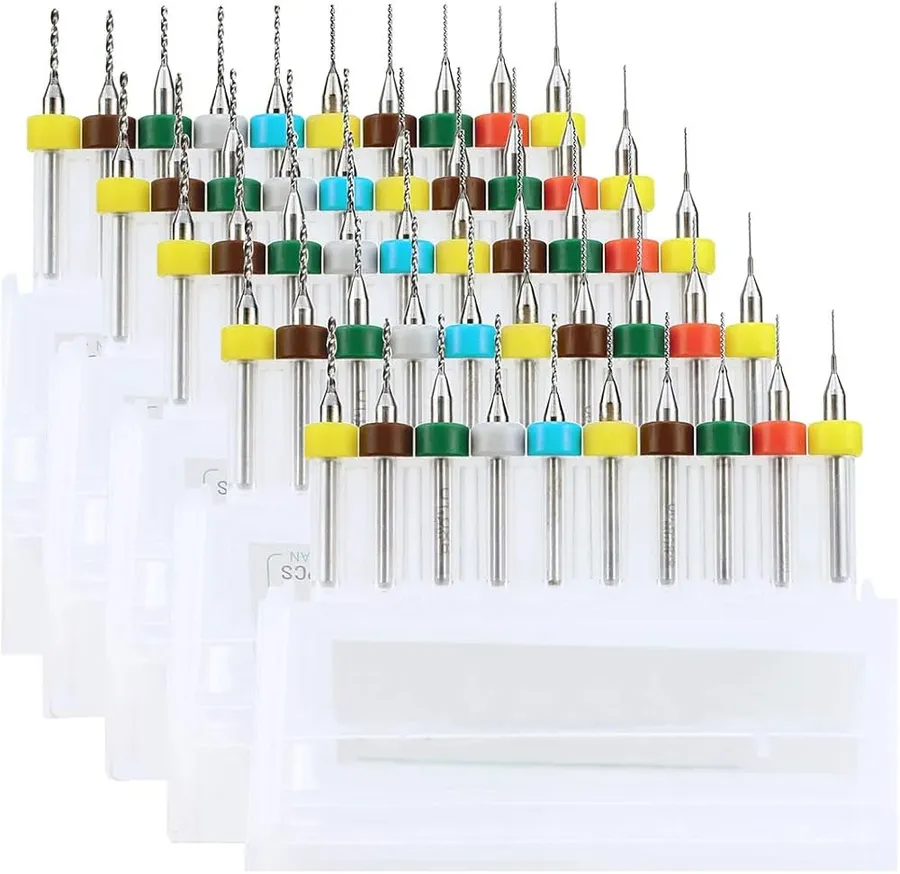
Precision in PCB drilling is governed by several critical parameters, each influencing the final board's functionality and reliability. These parameters include drill size, drilling depth, positional accuracy, and hole diameter tolerance, all of which must be carefully controlled to ensure optimal electrical and mechanical performance. Accurate control over these factors directly impacts the quality and yield of the PCB manufacturing process.
Parameter | Description | Impact on PCB | Typical Values | Challenges |
---|---|---|---|---|
Drill Size | The diameter of the drill bit used to create a hole. | Determines the size of the mounting hole for components, via size, or mechanical attachments. Incorrect size can result in poor component fit or compromised electrical connections. | 0.1 mm to 6.35 mm (0.004" to 0.250"), varies widely based on component needs. | Maintaining the precise drill bit diameter, especially with wear and tear; selecting an appropriate drill bit size based on the pad size of the component. |
Drill Depth | The depth to which the drill penetrates the PCB material. | Crucial for creating through-holes, blind vias, or back-drilled holes. Improper depth can lead to incomplete connections or damage to underlying layers. | Varies based on PCB layer structure and via type. Controlled by drilling machine settings. | Achieving consistent depth, especially in multi-layer PCBs; managing drill bit wear to ensure consistent hole depth. |
Positional Accuracy | The precision with which the drill bit is positioned before drilling each hole. Measured by the variance between the planned hole location and the actual location | Affects alignment between different layers of the PCB, as well as the proper positioning of components. Misalignment can result in short circuits, open circuits or component misplacement. | Typically within ±25µm (±0.001"), though can be more precise for advanced boards. Controlled by drill machine and optical registration. | Maintaining precision with high-volume production and tool wear; ensuring accurate registration of each layer in multi-layer PCBs. |
Hole Diameter Tolerance | The allowed variation in the diameter of the drilled hole from the intended size. | Ensures that components fit correctly, and vias make reliable connections. Too much deviation can cause poor fit or connectivity issues. | Typically ±0.05 mm (±0.002") for through holes, tighter for vias and controlled depth holes. | Controlling hole diameter across different materials and PCB thicknesses; maintaining consistent hole diameter throughout the production run. |
The challenge of small hole drilling is particularly noteworthy. Smaller holes, typically those used for vias, require higher precision and often lead to increased drill bit wear and breakage. Achieving precise hole diameters and positional accuracy becomes increasingly difficult as hole size decreases. In addition, small holes are more susceptible to burrs and wall roughness, which can impact signal integrity.
PCB Back Drilling: Removing Via Stubs
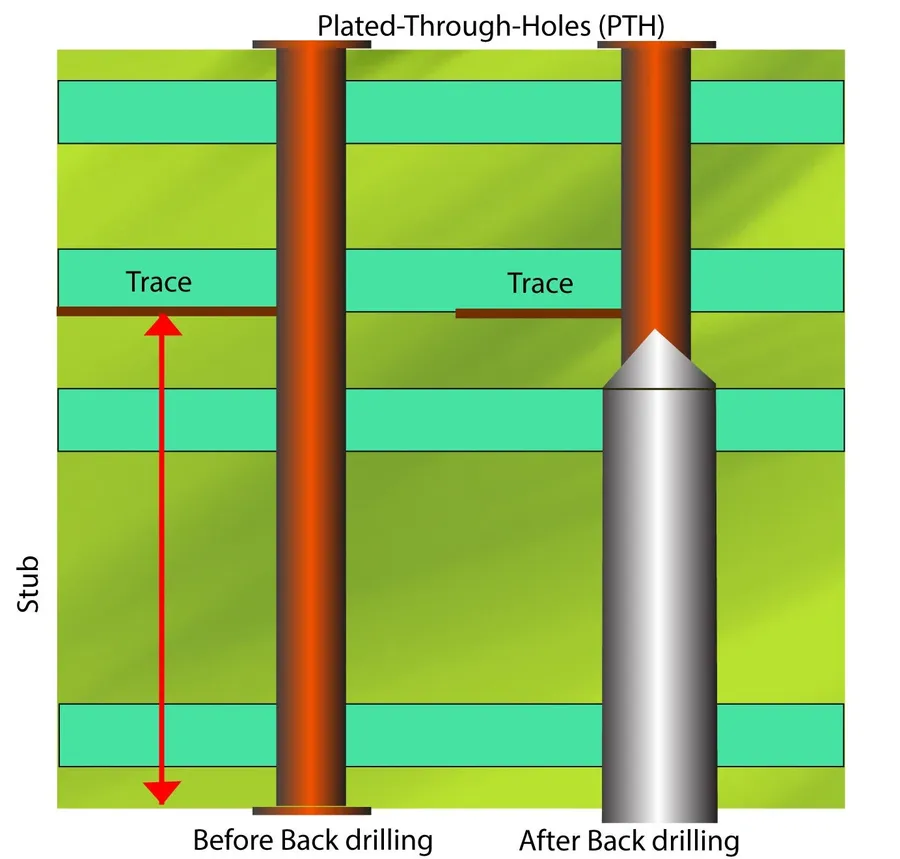
Back drilling, also known as controlled-depth drilling, is a specialized technique used in printed circuit board (PCB) fabrication to remove the unused portion, or 'stub', of a via. This process is critical for improving signal integrity, particularly in high-speed and high-frequency applications, by minimizing signal reflections and distortions that can arise from these stubs.
The back drilling process involves precisely drilling a hole from the back side of the PCB to remove the portion of the via that extends beyond the layer where the signal is being routed. This requires accurate depth control to avoid damaging the active signal layers and ensure the proper connection of the remaining via portion.
Key considerations in back drilling include: drill bit selection, to match the via diameter and material, the drilling depth to precisely remove via stubs, and the process control to maintain positional accuracy and avoid over drilling.
Drilled PCB Materials and Their Impact
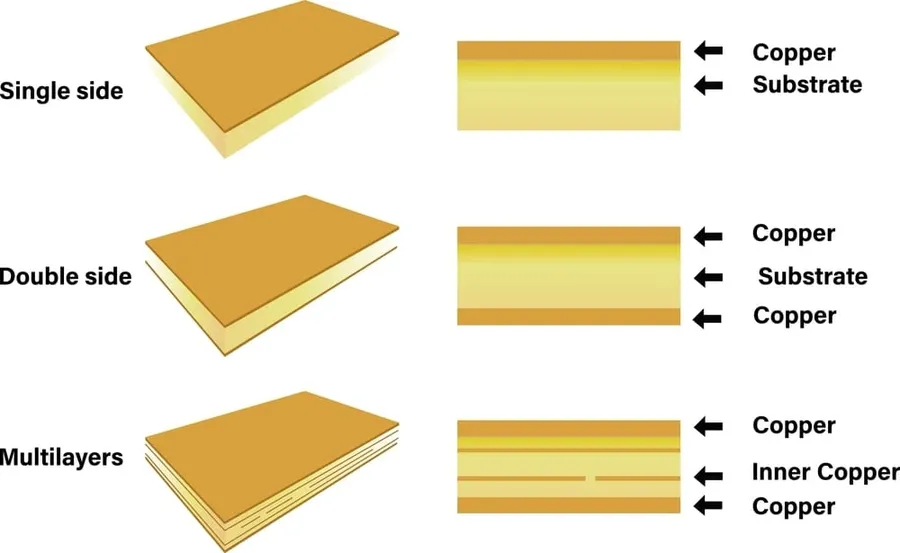
The selection of materials in PCB fabrication significantly dictates the drilling process parameters, tool requirements, and potential issues encountered during production. Different materials exhibit varying mechanical and thermal properties, which necessitate tailored drilling strategies to achieve precise and high-quality hole formation.
Material Type | Drilling Considerations | Tooling Implications | Common Issues |
---|---|---|---|
FR-4 (Fiberglass Epoxy) | Moderate drilling speeds, standard feed rates. Good machinability. | Carbide drill bits are typical. Standard geometry is sufficient. | Fiber pullout, burring |
High Tg FR-4 | Requires precise control of temperatures due to higher glass transition temperature, Moderate drilling speeds and feed rates. | Carbide drill bits with enhanced wear resistance, optimized geometry. | Increased wear, thermal stress |
Flexible PCB (e.g., Polyimide) | Lower drilling speeds and feeds are required due to soft material, Precise depth control is crucial. | Specialized drill bits with sharp cutting edges. Micro-drilling tools are common. | Tearing, material deformation |
Metal Core PCB (MCPCB) | Lower drilling speed, special cooling solutions and high feed rate to reduce the heat generation during drilling is important. | Diamond coated drills, or specialized drills | Tool wear, hole quality issues due to harder material. |
Teflon/PTFE | Careful management of drilling speed and feed rates because of its soft nature | Specialized sharp carbide drill bits to prevent material build up | Hole deformation, material tear-out |
The drilling process is influenced by the specific material properties. For example, harder materials like FR-4 require robust tools and optimized speeds and feeds to prevent premature tool wear. Conversely, softer materials like flexible polyimide require slower speeds and specific drill geometries to avoid tearing and deformation. Selecting the appropriate drill bit type, such as carbide for standard materials or diamond-coated for abrasive materials, is essential to maintaining hole quality and preventing damage to the PCB.
Drilled PCB Precision Challenges and Solutions
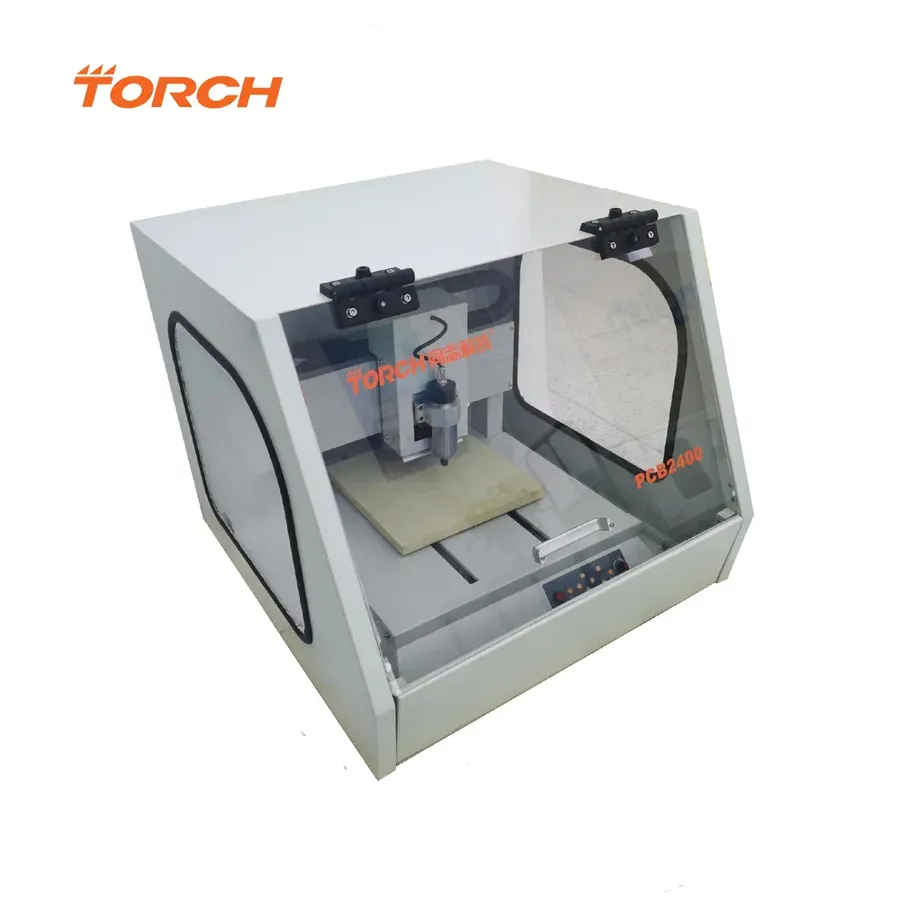
Achieving high precision in PCB drilling is paramount for functionality and reliability; however, the process is fraught with challenges. These challenges encompass issues from the physical integrity of the drilling tools to the accuracy of the drilled holes, each potentially impacting the performance of the final electronic product.
- Drill Bit Breakage
Fragile drill bits, especially those used for micro-vias, are susceptible to breakage due to factors like excessive feed rates, inappropriate spindle speeds, or material inconsistencies. Breakage can lead to defects, production delays, and increased costs. For instance, inadequate lubrication can cause friction that leads to bit failure during high-speed drilling. This is particularly challenging when working with tougher materials such as high-Tg FR-4 or ceramic filled substrates. - Hole Wall Roughness
Rough hole walls can hinder plating adhesion and cause electrical performance issues. Factors such as drill bit wear, inappropriate drilling parameters, or the inherent characteristics of the PCB material can cause this issue. For example, when the drill bit is dull, it can tear the laminate fibers rather than cut cleanly, resulting in rough and uneven hole walls. This is especially critical for vias where poor plating can lead to higher resistance or open circuits. - Positional Inaccuracies
Inaccurate hole placement can cause component misalignment and circuit failures. This is typically caused by mechanical inaccuracies in the drilling machine, errors in the design file data, or issues with the workholding of the PCB panels. For instance, a slight shift in the panel during drilling can cause vias to miss their intended target pads, causing shorts or open circuits in the final product. This is particularly relevant for high-density interconnect PCBs.
These challenges can have significant impacts on the functionality of the PCB.
- Component Misalignment
Positional inaccuracies can prevent components from being properly soldered onto the board, leading to open or short circuits. For instance, if a hole for a surface mount component is not positioned correctly, the solder joint will be unreliable or may not form at all. - Signal Integrity Issues
Rough hole walls and inconsistent plating can lead to signal degradation, particularly in high-speed circuits. This can cause signal reflections and reduced transmission quality, severely hampering performance. For example, in a high-frequency RF PCB, poor hole quality can impact impedance, causing signal distortion and loss. - Reduced Reliability
Defects introduced by drilling, such as micro-cracks or uneven plating, can reduce the long-term reliability of the PCB. This can lead to premature failures in the field due to thermal stress, vibration, or other environmental factors. For example, a poorly drilled via may crack under stress, leading to an intermittent failure or complete open circuit.
To mitigate these challenges, various solutions are implemented in PCB manufacturing:
- Drill Bit Maintenance
Regular inspection and replacement of drill bits, along with sharpening, are essential. Tool management systems track the usage and wear of each drill bit. High-performance coatings on drill bits, such as diamond-like carbon (DLC), extend their lifespan and improve hole quality. Proper bit storage and handling are also important to minimize damage. - Advanced Drilling Techniques
Employing optimized drilling parameters (feed rates, spindle speeds), pre-drilling, and step-drilling techniques, help reduce the stress on the drill bit and minimize hole defects. Careful selection of drilling parameters based on material thickness and composition can greatly reduce material damage and improve hole wall quality. Using controlled depth drilling helps mitigate the issue of back drilling. - Automated Inspection Processes
Automated optical inspection (AOI) and X-ray inspection are used to identify defects such as positional errors and hole wall irregularities. Such systems ensure the holes meet required specifications before further PCB manufacturing steps. AOI detects surface defects and dimensional errors, while X-ray inspection can reveal internal defects and misalignments in multilayer PCBs.
Frequently Asked Questions about Drilled PCBs
This section addresses common inquiries regarding drilled PCBs, offering clarity on various aspects from hole types to drilling impacts on design and performance. These insights will assist in understanding the critical role drilling plays in PCB fabrication.
- What is the primary purpose of drilling holes in a PCB?
Drilled holes in PCBs serve multiple critical functions. They are essential for mounting components, creating electrical connections between different layers of the board using vias, and providing mechanical support. Each hole must be precisely placed and sized to ensure the functionality and reliability of the final product. - What is the difference between vias and through-holes in PCBs?
Through-holes extend through the entire thickness of the PCB, allowing for component leads and connections to be soldered on both sides. Vias, on the other hand, are designed to create electrical connections between different layers of the PCB, and may not extend all the way through the board. They are essential for multilayer PCBs to allow signals to travel between layers. Blind vias and buried vias are types of vias that do not go through all layers, they connect to only some layers. - How does the selection of drill bits impact PCB hole quality?
The drill bit's material, size, geometry, and condition are paramount to achieving high-quality holes. Using the wrong bit can result in poor hole wall quality, such as roughness or tearing, which could affect solderability and signal integrity. For example, carbide drill bits are often used due to their durability and high precision, while specific geometries are chosen based on the material and desired hole characteristics. - What are the critical parameters to consider when drilling holes in PCBs?
Critical drilling parameters include drill size, depth, precision, and tolerance. Drill size must match the design specifications for component mounting or via creation. Drilling depth needs to be accurately controlled, especially in back drilling. Precision and tolerance refer to the allowable deviation from the specified hole size and position, which affects the overall PCB quality and reliability. - How does the drilling process affect the overall performance of a PCB?
The drilling process significantly affects the electrical and mechanical performance of the PCB. Inaccurate drilling can lead to impedance mismatches, signal reflections, and component mounting issues. Proper drilling ensures consistent conductivity between layers and secure mechanical assembly, which are vital for optimal performance. Poor hole quality and positional inaccuracies can drastically reduce the board's efficiency and reliability. - What are some common problems encountered during the PCB drilling process, and how can they be resolved?
Common issues include drill bit breakage, which can be caused by excessive speed or worn bits; hole wall roughness, often due to improper drill bit geometry or wear; and positional inaccuracies, usually related to machine calibration or errors in the drill program. These problems can be addressed by regularly inspecting and replacing drill bits, optimizing drilling parameters, and ensuring accurate machine calibration. - What is back drilling in PCBs and when is it used?
Back drilling, also known as controlled depth drilling, is a process used to remove via stubs from high-speed PCBs. Via stubs can cause signal reflections and degrade signal integrity. Back drilling is applied in very specific applications, it does not affect component mounting or through hole connections, its goal is to optimize the signal quality through minimizing signal reflections. This process improves the electrical performance of the board.
Future Trends and Innovations in Drilled PCB Technology
The evolution of drilled PCB technology is being shaped by the increasing demand for miniaturization, higher performance, and improved manufacturing efficiency. Emerging trends are focused on enhancing drilling precision, speed, and cost-effectiveness, leading to advanced techniques and automation that will be pivotal in the future of electronics manufacturing.
- Laser Drilling
Laser drilling is increasingly being adopted for creating microvias and other small features on PCBs. This non-contact method offers high precision and is especially suited for complex designs, eliminating the need for physical drill bits and reducing wear and tear. UV lasers, for instance, are capable of ablating materials with high precision. - Advanced Control Systems
The integration of sophisticated control systems, including closed-loop feedback mechanisms, is leading to significantly improved accuracy in drilling processes. These systems monitor parameters such as drill speed, depth, and alignment in real-time, automatically adjusting to maintain consistent quality, reducing errors and enhancing yield. - Automated Drilling Processes
Robotic automation is transforming PCB drilling by enabling higher throughput, greater consistency, and more precise control. Automated systems can handle the loading, drilling, and unloading of boards with minimal human intervention. This reduces the potential for human error, increases the speed of production, and lowers manufacturing costs. - Direct Imaging for Drilling
Direct imaging technologies are being developed to replace traditional mechanical drilling for specific applications. This allows for more precise and faster fabrication of via holes, eliminating the potential for drill wandering. This approach aligns with a trend toward digitalized manufacturing methods. - AI-Powered Process Optimization
Artificial intelligence and machine learning algorithms are being integrated to analyze data from drilling processes in real-time. These systems can identify patterns, optimize drilling parameters, and predict potential issues. This leads to optimized performance, better quality control, and reduction in downtime.
The precision of drilled PCB is an unseen but vital aspect of modern technology. From the initial drilling to advanced techniques like back drilling, every step significantly impacts the performance and reliability of electronic devices. As technology continues to evolve, so will the methods used to create these essential components. The continued advancement of drilled PCB technologies guarantees more efficient, reliable and advanced electronic products.
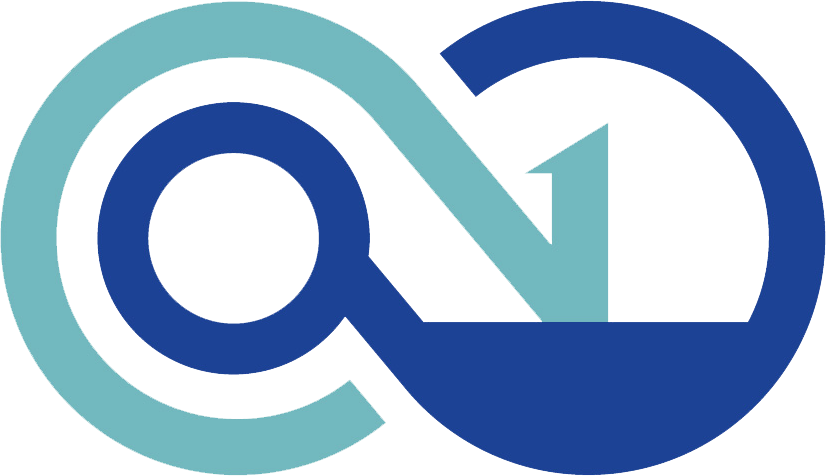