Shared Electric Bicycle/Scooter Solution
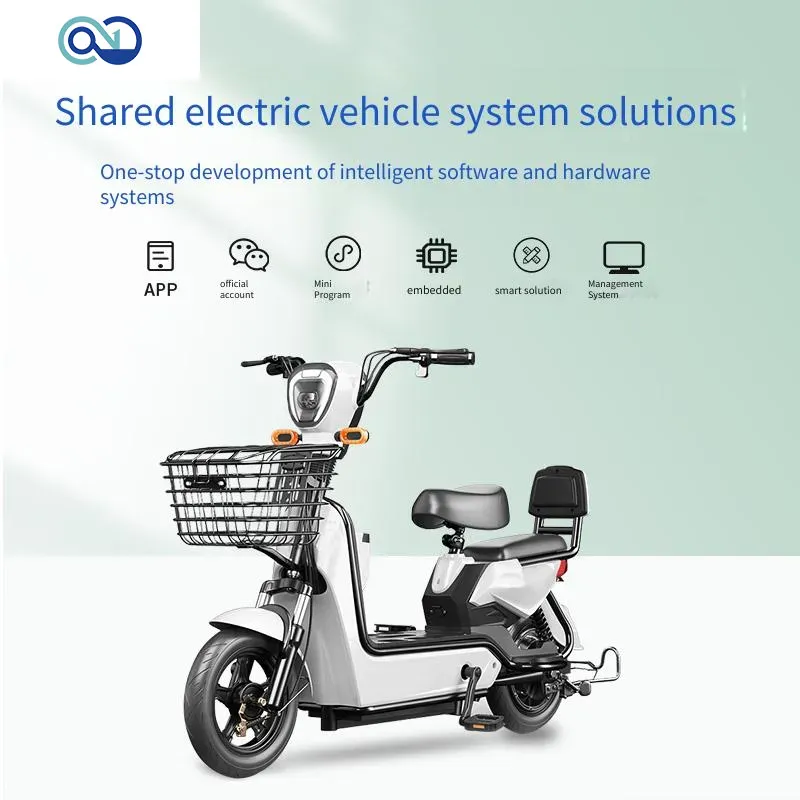
The urban landscape is rapidly evolving, with shared electric bicycles and scooters emerging as a cornerstone of sustainable and efficient last-mile transportation. This revolution in micromobility demands robust, reliable, and intelligent electronic solutions. At Zero One Solution Limited, we've been at the forefront of powering innovation since 2011, providing rapid-response R&D prototype manufacturing and one-stop PCB services from design to assembly. We understand the critical role high-performance PCBs play in the success of these complex shared vehicle systems. How can cutting-edge PCB technology drive the next generation of shared electric mobility?
The Rise of Shared Electric Mobility: Opportunities and Challenges
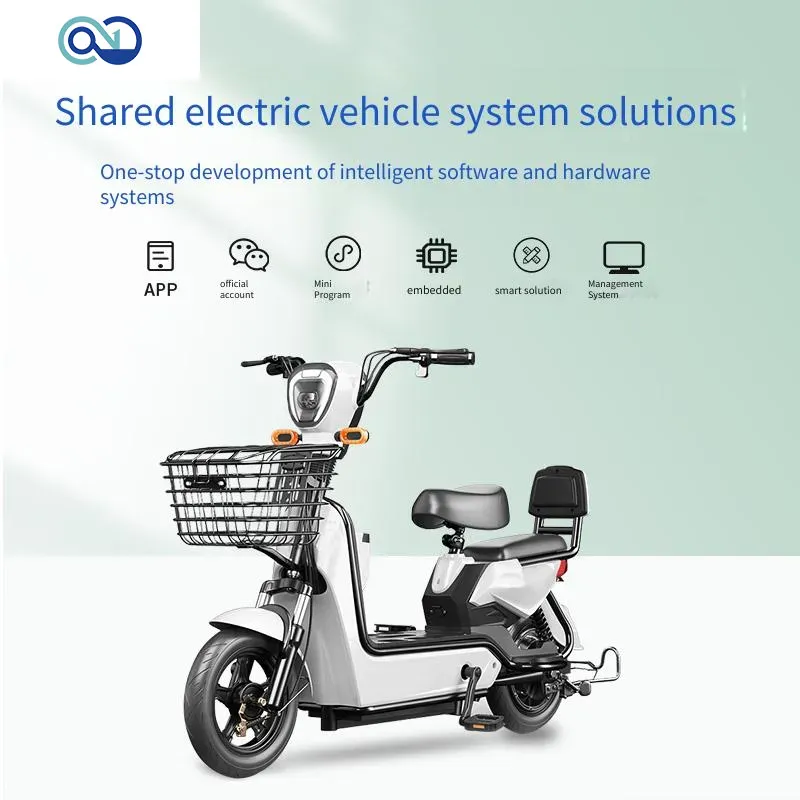
The shared electric mobility sector, encompassing e-bikes and e-scooters, is experiencing rapid growth, driven by increasing urbanization, environmental concerns, and the desire for convenient, affordable transportation options. This surge presents significant market opportunities for manufacturers and operators. However, the demanding public use environment poses considerable technical challenges, particularly in developing robust, connected, and durable vehicles. The reliability of electronics, especially within shared electric bicycle solutions, is paramount for ensuring uptime, safety, and user satisfaction.
The expansion of shared electric mobility is fueled by several key factors:
- Urbanization:
Increasing population density in cities creates a need for efficient and space-saving transportation solutions. - Environmental Awareness:
Growing concerns about air pollution and carbon emissions drive demand for eco-friendly alternatives to traditional vehicles. - Cost-Effectiveness:
Shared e-bikes and e-scooters offer a relatively inexpensive mode of transport compared to owning a car or using ride-hailing services. - Convenience:
These vehicles provide a flexible and readily available option for short-distance travel, bypassing traffic congestion and parking challenges.
Despite the promising landscape, shared electric mobility faces significant technical hurdles:
- Durability:
Shared vehicles endure heavy usage and exposure to harsh weather conditions, requiring robust components and construction. - Connectivity:
Real-time tracking, remote diagnostics, and user authentication necessitate reliable IoT communication modules and secure data transmission. - Battery Management:
Extending battery life, ensuring safe charging, and preventing theft are critical for operational efficiency and profitability. - Vandalism and Theft:
Shared vehicles are susceptible to vandalism and theft, demanding robust security measures and tamper-proof designs. - Regulatory Compliance:
Meeting local regulations regarding speed limits, parking restrictions, and safety standards is essential for legal operation.
Addressing these challenges requires innovative engineering solutions, particularly in the design and manufacturing of printed circuit boards (PCBs) that form the backbone of these vehicles' electronic systems. High-quality, reliable PCBs are crucial for ensuring the safe, efficient, and sustainable operation of shared electric bicycles and scooters.
Core Electronic Components in Shared Electric Bicycles and Scooters
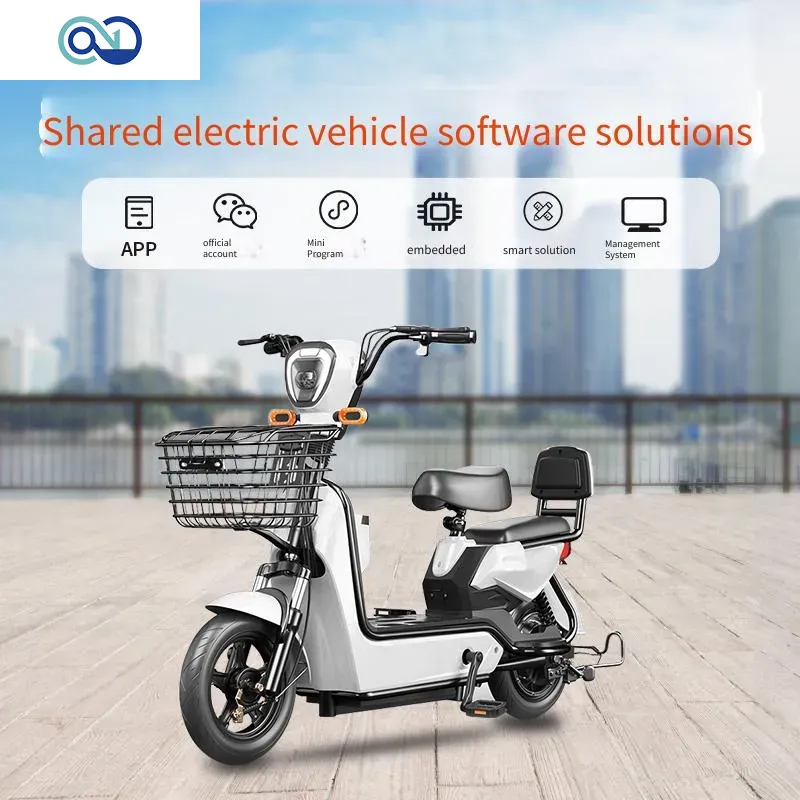
Shared electric bicycles and scooters rely on a suite of sophisticated electronic systems to deliver performance, safety, and connectivity. These core components, crucial for the operation of shared electric vehicles, include motor control units, battery management systems (BMS), GPS/IoT communication modules, and user interface displays. The integration and reliability of these systems are paramount, and robust PCB solutions are key to ensuring their effective operation in shared e-scooter solutions.
- Motor Control Units (MCU)
The MCU is the brain behind the electric motor, precisely controlling the power delivered to the motor to manage speed, acceleration, and braking. Advanced MCUs also incorporate regenerative braking features, enhancing energy efficiency. High-performance PCBs are essential in MCUs to handle the power switching and control signals effectively. - Battery Management Systems (BMS)
The BMS monitors and manages the battery pack, ensuring safe charging and discharging, preventing overvoltage, undervoltage, and overcurrent conditions, and balancing cell voltages for optimal battery life. A reliable PCB is crucial for accurate voltage and current sensing, as well as for implementing protection circuitry. - GPS/IoT Communication Modules
GPS modules provide location tracking for fleet management and theft prevention, while IoT modules enable communication with a central server for remote monitoring, diagnostics, and over-the-air (OTA) updates. PCBs for these modules must support reliable wireless communication in urban environments, often requiring impedance control and signal integrity optimization. - Display Interfaces
User interface displays provide riders with essential information such as speed, battery level, and trip distance. These displays require robust PCBs to ensure clear visibility and reliable operation in various lighting conditions. Touchscreen functionality may also be integrated, adding complexity to the PCB design. - Lighting Systems
Front and rear lights are critical for safety, especially during nighttime operation. LED lighting systems require efficient power delivery and thermal management, making PCB design crucial for longevity and brightness. - Braking Systems Control
Electronic braking systems, including ABS (Anti-lock Braking System), enhance rider safety. The control systems require reliable PCBs to ensure quick response times and accurate braking force modulation. - Security Systems
Alarm systems and immobilizers deter theft and unauthorized use. These systems rely on robust PCBs for reliable operation and tamper resistance.
Zero One Solution Limited's Expertise in PCB Solutions for Micromobility

Zero One Solution Limited stands at the forefront of providing specialized PCB solutions for the rapidly evolving micromobility sector. With over a decade of experience, we have honed our expertise in PCB design, rapid prototyping, manufacturing, and assembly services tailored specifically for shared electric bicycles and scooters. Our comprehensive, one-stop service streamlines the PCB development process for shared e-bike projects, accelerating innovation and time-to-market for our clients.
Our capabilities encompass the entire PCB lifecycle, ensuring seamless integration and optimal performance of electronic components in shared electric vehicles. We understand the unique demands of this industry and deliver solutions that meet the highest standards of reliability, durability, and efficiency.
- What specific PCB design services does Zero One Solution Limited offer for shared electric bicycles and scooters?
Zero One Solution Limited provides a full suite of PCB design services tailored for shared electric bicycles and scooters, including schematic capture, layout design, signal integrity analysis, thermal management, and design for manufacturability (DFM). We ensure that every design meets the unique requirements of micromobility applications, such as durability, power efficiency, and compact size. - Can Zero One Solution Limited handle rapid prototyping for shared e-bike PCB development?
Yes, we specialize in rapid prototyping services that significantly reduce time-to-market for shared electric vehicle manufacturers. Our quick-turn PCB assembly allows for iterative design and testing, enabling clients to refine their products efficiently. We can deliver prototypes in as little as 24 hours. - What manufacturing and assembly capabilities does Zero One Solution Limited offer for micromobility PCB solutions?
We offer comprehensive manufacturing and assembly services, including SMT (Surface Mount Technology), through-hole assembly, and mixed technology assembly. Our state-of-the-art facilities and experienced technicians ensure high-quality PCB production. We also provide conformal coating and potting services to protect PCBs from harsh environmental conditions. - How does Zero One Solution Limited ensure the quality and reliability of PCBs for shared electric bicycles and scooters?
Quality and reliability are paramount. We implement rigorous quality control processes at every stage, from design review to final inspection. Our testing capabilities include automated optical inspection (AOI), in-circuit testing (ICT), and functional testing. We also conduct environmental testing to ensure PCBs can withstand the demanding conditions of shared mobility environments. - Does Zero One Solution Limited offer one-stop service for shared e-bike PCB development?
Yes, we offer a complete one-stop service that covers everything from initial design to final assembly and testing. This integrated approach streamlines the development process, reduces lead times, and ensures seamless communication between different teams. Our clients benefit from a single point of contact and a cohesive, efficient workflow. - What are the key benefits of choosing Zero One Solution Limited for PCB solutions in the shared electric bicycle/scooter market?
Choosing Zero One Solution Limited offers several key benefits, including our extensive experience in the micromobility sector, our rapid prototyping capabilities, our comprehensive manufacturing and assembly services, our rigorous quality control processes, and our commitment to customer satisfaction. We provide tailored solutions that meet the specific needs of each client, helping them to accelerate innovation and achieve their business goals. - Can Zero One Solution Limited assist with cost optimization for PCB solutions in shared electric mobility?
Yes, we understand the importance of cost optimization in the competitive shared electric mobility market. Our experienced engineers can analyze designs and identify opportunities to reduce costs without compromising performance or reliability. We offer value engineering services, including component selection, design simplification, and process optimization, to help clients achieve their target cost objectives.
Key PCB Design Considerations for Shared Mobility Solutions
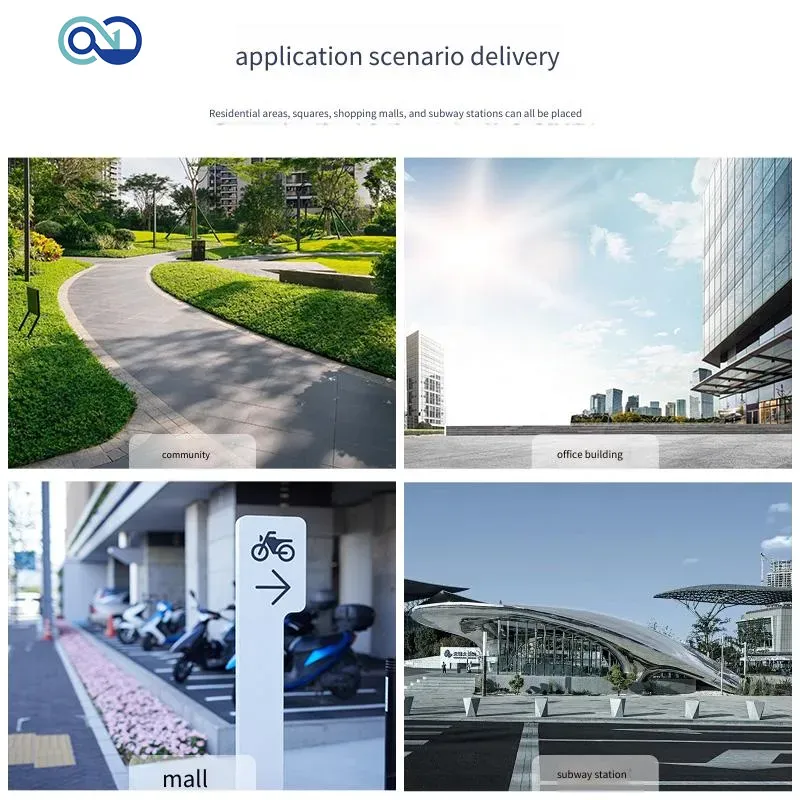
Designing PCBs for shared mobility solutions, such as electric bicycles and scooters, demands a meticulous approach, focusing on durability, power efficiency, size, and signal integrity. These vehicles face harsh outdoor conditions and continuous usage, necessitating robust electronic designs. The PCB is the backbone of these systems, and its design directly impacts the performance and reliability of the entire vehicle. This section delves into the critical considerations for PCB design in shared mobility applications, ensuring optimal performance and longevity.
- Durability for Outdoor Environments
Shared e-bikes and e-scooters are exposed to diverse weather conditions, including rain, humidity, extreme temperatures, and UV radiation. PCBs must withstand these environmental stressors to prevent corrosion, degradation, and eventual failure. This is achieved through: - Conformal Coating
Applying a protective layer to shield the PCB from moisture and contaminants. - Material Selection
Choosing PCB materials with high thermal and chemical resistance. - Robust Component Mounting
Ensuring components are securely attached to withstand vibrations and mechanical stress. - Power Efficiency for Extended Battery Life
Power consumption is a critical factor in shared mobility, as it directly affects the range and operational uptime of the vehicles. Efficient PCB design minimizes energy waste and maximizes battery life. Strategies include: - Low-Power Components
Selecting components with minimal power requirements. - Optimized Routing
Designing PCB layouts to minimize trace lengths and impedance, reducing power losses. - Efficient Power Management Circuits
Implementing circuits that regulate voltage and current efficiently. - Compact Size for Integration
Space is often limited in shared electric vehicles, requiring PCBs to be compact and efficiently packaged. Considerations include: - High-Density Interconnect (HDI) Technology
Utilizing HDI techniques to pack more components into a smaller area. - Multi-Layer PCBs
Employing multiple layers to increase circuit density without increasing the overall PCB size. - Strategic Component Placement
Optimizing the placement of components to minimize space requirements and improve signal integrity. - Signal Integrity for Reliable Data Transmission
Shared electric vehicles rely on reliable data transmission between various electronic modules, such as GPS, motor controllers, and display units. Maintaining signal integrity is crucial for accurate and timely communication. Key considerations are: - Controlled Impedance Traces
Designing traces with consistent impedance to minimize signal reflections. - Proper Grounding
Implementing a robust grounding scheme to reduce noise and interference. - Signal Isolation
Separating sensitive signals from noise sources to prevent signal corruption.
Accelerating Development with Rapid Prototyping and Assembly
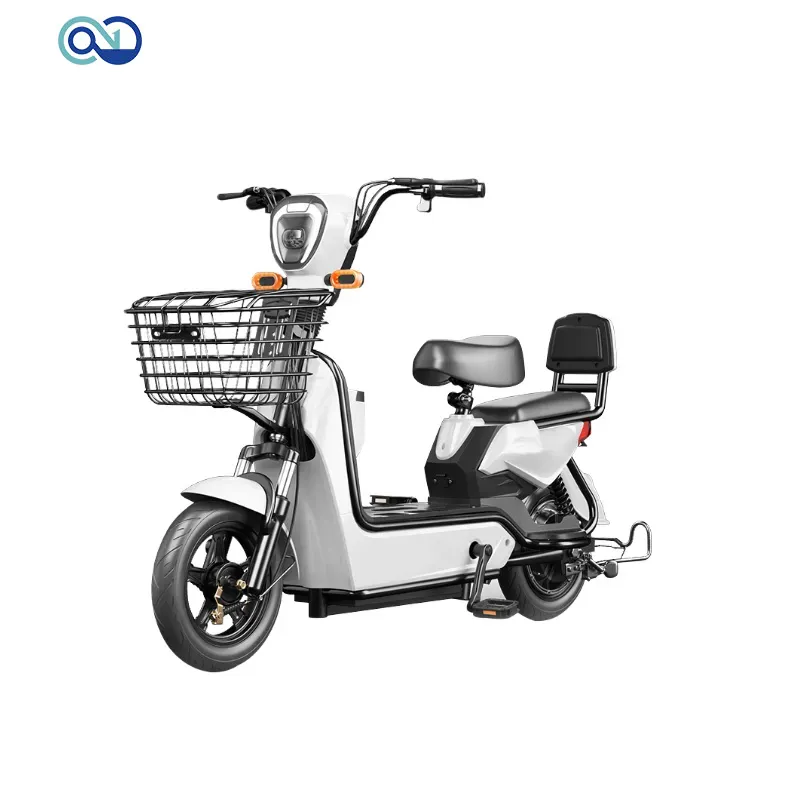
In the fast-paced market of shared electric vehicles, time is of the essence. Zero One Solution Limited specializes in rapid prototyping and quick-turn PCB assembly, crucial for manufacturers aiming to swiftly introduce shared electric bicycles and scooters. Our capabilities significantly compress the development cycle, allowing for faster innovation and quicker market entry. This acceleration is achieved through streamlined processes and advanced manufacturing techniques, specifically designed to meet the urgent demands of the micromobility sector.
Here’s how Zero One Solution’s rapid prototyping and assembly services benefit shared electric vehicle development:
- Reduced Time-to-Market
Our rapid prototyping services enable manufacturers to quickly validate designs and iterate improvements, drastically reducing the time it takes to bring a product from concept to market-ready. This speed is essential in capturing early market share and staying ahead of competitors. - Iterative Design and Testing
With quick-turn PCB assembly, design teams can receive assembled boards in a matter of days. This allows for continuous testing and refinement of prototypes, ensuring that the final product is thoroughly optimized for performance and reliability. - Cost-Effective Prototyping
By accelerating the prototyping phase, we help minimize development costs. Early detection of design flaws and quick iterations prevent costly mistakes in mass production, ensuring efficient use of resources. - Advanced Technology Integration
Our expertise supports the integration of cutting-edge technologies, such as IoT modules and advanced battery management systems, into shared electric vehicles. Rapid prototyping allows for experimentation with these technologies to optimize performance and functionality. - Customized Solutions
We provide tailored PCB solutions that meet the specific needs of shared mobility applications. Whether it's a compact design for space-constrained scooters or a rugged board for all-weather bicycles, our services are customized to fit each unique project.
Zero One Solution Limited is committed to providing the rapid prototyping and assembly services necessary for shared electric vehicle manufacturers to innovate quickly and efficiently. Our streamlined processes and technological expertise ensure that your product development cycle is optimized for speed and success.
Ensuring Reliability and Performance: Quality Control and Testing
At Zero One Solution Limited, we recognize that the reliability and longevity of PCBs are paramount in the demanding environments where shared electric bicycles and scooters operate. To ensure our PCBs meet these stringent requirements, we implement rigorous quality control and testing processes at every stage of production, from design validation to final product inspection. Our commitment to quality translates into dependable performance for shared mobility solutions.
Our comprehensive quality control and testing protocols encompass the following key aspects:
- Design Verification
Prior to manufacturing, our design verification process meticulously checks the PCB layout against design specifications and industry standards. This includes signal integrity analysis, thermal simulation, and manufacturability assessments to identify and address potential issues early on. - Material Inspection
We source high-quality materials from trusted suppliers and conduct thorough inspections upon arrival. This ensures that all materials meet our stringent requirements for electrical performance, thermal stability, and environmental resistance. - In-Process Quality Control
Throughout the manufacturing process, our skilled technicians perform continuous monitoring and inspection. This includes automated optical inspection (AOI) to detect defects such as shorts, opens, and misaligned components, as well as X-ray inspection to verify solder joint integrity. - Environmental Testing
Our PCBs undergo rigorous environmental testing to simulate the harsh conditions encountered in shared mobility applications. This includes temperature cycling, humidity testing, vibration testing, and shock testing to ensure reliable performance in extreme environments. - Functional Verification
Each PCB is subjected to functional testing to verify that it performs according to its intended design. This includes testing critical parameters such as voltage levels, current consumption, and signal timing. We utilize customized test fixtures and automated test equipment (ATE) to ensure accurate and repeatable results. - Reliability Testing
To assess the long-term reliability of our PCBs, we conduct accelerated life testing (ALT) and highly accelerated stress screening (HASS). These tests simulate years of real-world operation in a compressed timeframe, allowing us to identify potential failure modes and improve product robustness. - Final Inspection
Before shipment, all PCBs undergo a final inspection to ensure that they meet our stringent quality standards. This includes visual inspection, dimensional checks, and packaging verification.
By implementing these rigorous quality control and testing processes, Zero One Solution Limited ensures that our PCBs deliver exceptional reliability and performance in demanding shared mobility environments. This commitment to quality minimizes downtime, reduces maintenance costs, and enhances the overall user experience for shared electric bicycle and scooter operators.
The Future of Shared Electric Mobility and PCB Innovation
The shared electric mobility sector is on the cusp of transformative advancements, driven by technological innovation and evolving user expectations. As shared electric bicycles and scooters become increasingly integrated into urban transportation networks, PCB innovation will play a pivotal role in shaping their future capabilities and performance. This section explores emerging trends and how Zero One Solution Limited is positioned to drive these advancements.
Here are some key areas of development:
- Enhanced IoT Integration
Future shared electric vehicles will feature more sophisticated IoT solutions for real-time data collection, predictive maintenance, and improved user experience. PCB design will need to accommodate a greater density of sensors and communication modules, ensuring seamless connectivity and efficient data processing. - AI-Powered Fleet Management
Artificial intelligence will optimize fleet distribution, predict demand patterns, and enhance security features. PCBs will be integral in supporting the AI processing power required for these advanced functionalities, demanding high-speed data transmission and robust computing capabilities. - Advanced Safety Features
Next-generation e-bikes and e-scooters will incorporate advanced safety systems, such as collision avoidance, smart braking, and rider monitoring. PCB innovation will be critical in integrating these features reliably and efficiently, ensuring rider safety and regulatory compliance. - Sustainable Materials and Manufacturing
As environmental concerns grow, the shared mobility industry will prioritize sustainable materials and manufacturing processes. Zero One Solution Limited is committed to exploring eco-friendly PCB materials and production techniques to minimize the environmental impact of shared electric vehicles. - Wireless Charging Capabilities
Integrating wireless charging will streamline operations and reduce maintenance needs. PCB design will support the integration of wireless charging components, ensuring efficient power transfer and robust performance in diverse environmental conditions.
Zero One Solution Limited is dedicated to staying at the forefront of these advancements, providing cutting-edge PCB solutions that empower shared electric bicycle and scooter manufacturers to innovate and excel in this dynamic market. Our expertise in rapid prototyping, advanced materials, and rigorous testing ensures that our clients can confidently develop and deploy the next generation of shared mobility solutions.
Frequently Asked Questions about Shared Electric Bicycle/Scooter PCB Solutions
This section addresses common questions and concerns regarding PCB solutions for shared electric bicycles and scooters. We aim to provide clear, concise answers to help you understand the critical aspects of PCB design, durability, cost, and Zero One Solution's capabilities in this rapidly evolving industry.
- What makes a PCB durable enough for shared electric bicycle/scooter applications?
Durability in shared mobility PCBs stems from several factors. These include the selection of high-quality materials resistant to environmental factors like moisture, temperature variations, and vibrations. Robust design practices, such as adding conformal coatings and ensuring proper component mounting, also contribute significantly. Furthermore, rigorous testing, including environmental stress testing and accelerated life testing, verifies the PCB's ability to withstand the harsh conditions of public use. - How can PCB cost be optimized for shared electric bicycle/scooter projects without sacrificing quality?
Cost optimization involves a multifaceted approach. Efficient PCB layout design minimizes material usage and manufacturing complexity. Strategic component selection, balancing performance requirements with cost-effectiveness, is crucial. Utilizing rapid prototyping services allows for early detection and correction of design flaws, preventing costly revisions later in the production cycle. Partnering with an experienced PCB manufacturer like Zero One Solution Limited can further optimize costs through streamlined manufacturing processes and supply chain management. - What are the main design challenges specific to PCBs used in shared electric vehicles?
Designing PCBs for shared electric vehicles presents unique challenges. Space constraints often require compact and high-density designs. The need for efficient power management to maximize battery life is paramount. Ensuring reliable communication between various electronic components, such as motor controllers, BMS, and IoT modules, demands careful signal integrity analysis and design. Furthermore, designing for harsh environmental conditions, including vibration, moisture, and extreme temperatures, necessitates robust materials and construction techniques. - How does Zero One Solution Limited support shared electric bicycle and scooter PCB needs?
Zero One Solution Limited provides comprehensive support for shared electric bicycle and scooter PCB needs, from initial design and rapid prototyping to manufacturing and assembly. Our expertise in power electronics, IoT integration, and ruggedized PCB design makes us an ideal partner for shared mobility companies. We offer rapid prototyping services to accelerate development cycles, and our rigorous quality control processes ensure the reliability and longevity of our PCBs in demanding shared mobility environments. Furthermore, our global supply chain network allows us to provide cost-effective solutions without compromising quality. - Can Zero One Solution Limited handle both small prototype runs and large-scale production of shared e-bike PCBs?
Yes, Zero One Solution Limited is equipped to handle both small prototype runs and large-scale production. Our rapid prototyping services are ideal for initial design validation and iterative development. We utilize advanced manufacturing technologies and processes to ensure consistent quality and scalability for large-scale production runs. Whether you need a few prototype boards or thousands of PCBs for mass deployment, we have the capabilities to meet your needs. - What types of testing does Zero One Solution Limited perform to ensure PCB reliability for shared mobility applications?
Zero One Solution Limited implements a comprehensive suite of testing procedures to ensure PCB reliability. These include Automated Optical Inspection (AOI) to detect manufacturing defects, In-Circuit Testing (ICT) to verify component placement and functionality, and functional testing to validate overall system performance. We also conduct environmental stress testing, including thermal cycling, humidity testing, and vibration testing, to simulate the harsh conditions experienced in shared mobility environments. These rigorous testing processes ensure that our PCBs meet the highest standards of quality and reliability. - What are the key considerations for integrating IoT modules into shared electric bicycle/scooter PCBs?
Integrating IoT modules into shared electric bicycle/scooter PCBs requires careful consideration of several factors. Antenna placement is crucial for ensuring reliable connectivity. Power consumption must be minimized to maximize battery life. The PCB design must accommodate the specific requirements of the IoT module, including its pinout, voltage levels, and communication protocols. Furthermore, security considerations are paramount to protect against unauthorized access and data breaches. Zero One Solution Limited has extensive experience in IoT integration and can provide expert guidance on these critical design aspects.
The shared electric bicycle and scooter market is dynamic and full of promise, demanding advanced, reliable, and efficient electronic solutions. Zero One Solution Limited stands as your premier partner, delivering the high-quality PCB design, rapid prototyping, manufacturing, and assembly services essential for your shared mobility innovations. Our strategic global presence and unwavering commitment to excellence ensure that your vision translates into market-leading products. Don't let complex electronics slow down your progress. Partner with Zero One Solution Limited to accelerate your shared electric vehicle project. Contact us today to discuss your specific PCB requirements and discover how we can help you power the future of urban mobility.
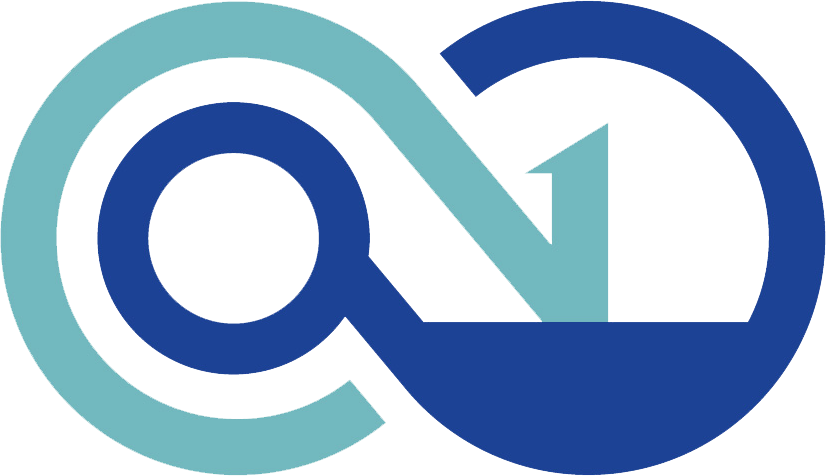