Shared Forklift Solution
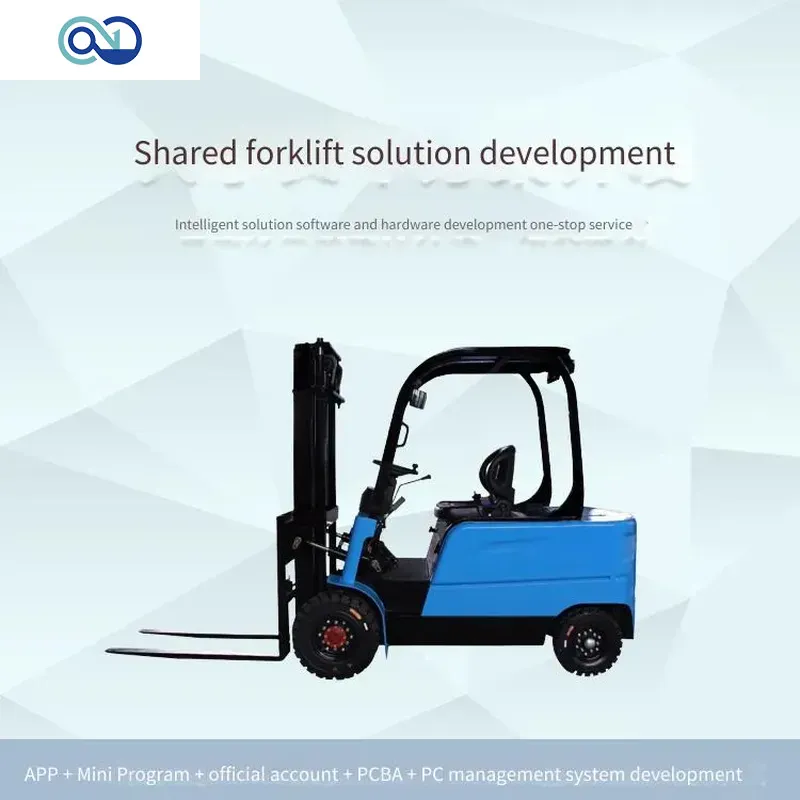
In today's dynamic industrial landscape, where efficiency and cost-effectiveness are paramount, businesses are continually seeking innovative ways to optimize their operations. Just as Zero One Solution Limited streamlines PCB design to assembly, enabling rapid prototyping and market acceleration, the concept of shared resources is transforming various sectors. This article delves into the transformative potential of a 'Shared Forklift Solution,' exploring how this collaborative approach to material handling can significantly enhance productivity and reduce overheads, mirroring the strategic advantages we bring to the PCBA supply chain. How can shared assets drive unprecedented gains in your logistics?
Understanding the Shared Forklift Solution Model
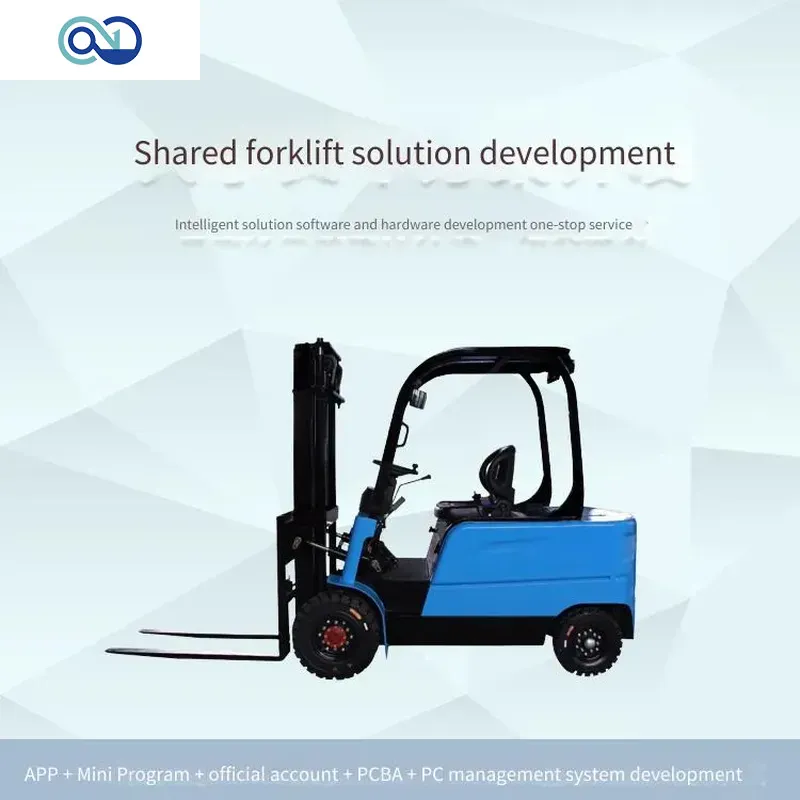
The Shared Forklift Solution model represents a paradigm shift in material handling, moving away from traditional, dedicated forklift ownership towards a collaborative, resource-optimized approach. At its core, this model involves multiple entities sharing a fleet of forklifts, enabling efficient utilization of equipment and resources. It's a strategic response to the evolving needs of modern warehouses and logistics operations, emphasizing flexibility, cost-effectiveness, and sustainability.
- Core Principles of Shared Forklift Solutions
The core principles revolve around optimizing asset utilization, reducing capital expenditure, and fostering collaborative resource management. It promotes a shift from individual ownership to shared access, allowing multiple users or departments to benefit from a common pool of forklifts. - Key Characteristics of a Shared Forklift Model
The key characteristics include shared access among multiple users, flexible scheduling based on demand, a centralized management system, and data-driven insights for optimizing forklift allocation and maintenance. - Differentiating Shared Forklifts from Traditional Ownership
Unlike traditional ownership, where each entity owns and manages its forklifts, the shared model distributes costs and responsibilities across multiple users. This results in lower upfront investment, reduced maintenance overhead, and improved scalability. - Benefits of Collaborative Forklift Usage
Collaborative forklift usage yields numerous benefits, including reduced equipment redundancy, decreased idle time, and improved operational efficiency. It enables businesses to access a diverse fleet of forklifts without the burden of individual ownership. - Role of Technology in Shared Forklift Management
Technology plays a vital role in enabling seamless shared forklift operations. Telematics, IoT sensors, and cloud-based platforms facilitate real-time monitoring, predictive maintenance, and efficient allocation of forklifts, optimizing overall performance and minimizing downtime.
Key Benefits of Implementing Shared Forklifts
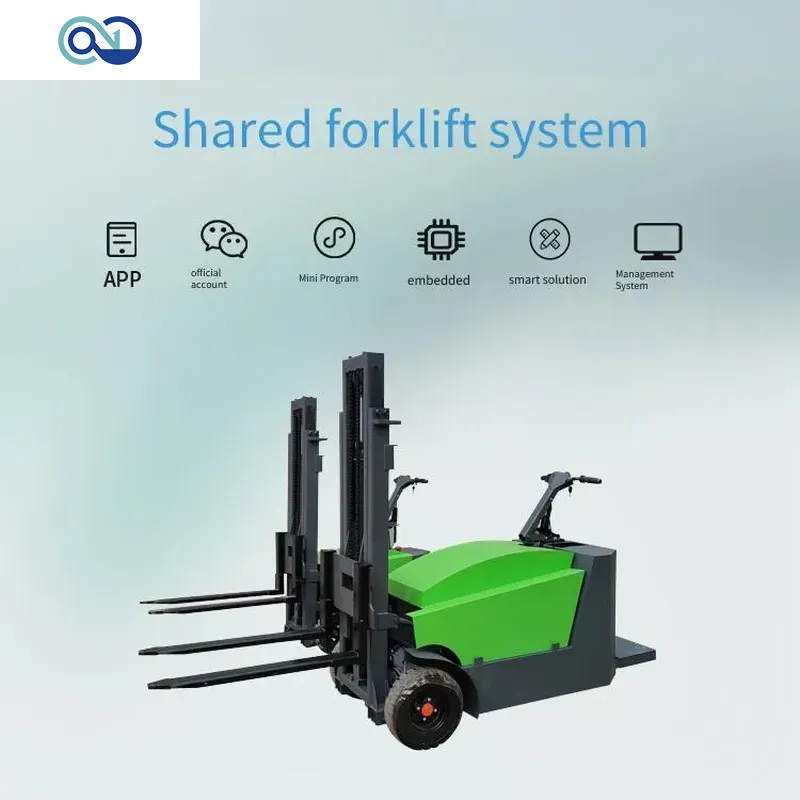
Implementing a shared forklift solution offers a multitude of advantages, transforming warehouse and logistics operations. The core benefits revolve around significant cost savings, enhanced operational flexibility, and a stronger commitment to environmental sustainability. By moving away from traditional ownership models, businesses can unlock considerable value and optimize resource allocation.
- Cost Reduction
Sharing forklifts significantly lowers capital expenditure. Instead of purchasing equipment outright, companies can access forklifts on an as-needed basis, reducing upfront investment. Maintenance costs are also shared, leading to further savings. This model transforms fixed costs into variable expenses, aligning expenditure with actual usage. - Operational Flexibility
A shared forklift system allows businesses to scale their forklift fleet according to fluctuating demand. During peak seasons, additional forklifts can be easily accessed, while during slower periods, the fleet can be reduced, avoiding unnecessary expenses. This adaptability ensures that the right equipment is always available without the burden of owning excess capacity. - Enhanced Sustainability
Shared forklift solutions promote environmental responsibility by optimizing equipment utilization. Fewer forklifts are needed overall, reducing the resources required for manufacturing and disposal. Electrification of shared fleets is also more viable, decreasing carbon emissions and promoting greener operations. This aligns with corporate sustainability goals and contributes to a more environmentally friendly supply chain. - Improved Asset Utilization
Shared forklift arrangements lead to higher utilization rates for each forklift. This is because the equipment is actively used across multiple businesses or departments, minimizing idle time and maximizing the return on investment. Increased utilization also reduces the total number of forklifts needed in the market, promoting resource efficiency. - Access to Advanced Technology
Shared forklift providers often invest in advanced technologies such as telematics, IoT sensors, and data analytics platforms. This gives users access to real-time insights into forklift performance, location, and maintenance needs. These insights enable better decision-making, improved safety, and optimized operational efficiency. - Simplified Fleet Management
Outsourcing forklift management to a shared provider reduces the administrative burden on businesses. The provider handles maintenance, repairs, and compliance, freeing up internal resources to focus on core business activities. This streamlined approach improves overall efficiency and reduces operational complexity.
Optimizing Warehouse Efficiency with Forklift Sharing

Shared forklift solutions are revolutionizing warehouse operations by significantly enhancing efficiency through better equipment utilization, reduced idle times, and streamlined workflows. By moving away from dedicated forklift assignments, businesses can achieve greater productivity and responsiveness to fluctuating demands, ultimately optimizing their warehouse environment.
Here's how shared forklift systems drive warehouse efficiency:
- Enhanced Equipment Utilization
Shared forklift systems ensure that forklifts are in use more often, reducing the number of idle vehicles. This maximizes the return on investment for each forklift and minimizes the total number of forklifts needed. - Reduced Idle Time
By making forklifts available to multiple users or departments, shared systems minimize the time forklifts sit idle, waiting for a specific task. This leads to quicker task completion and improved overall workflow. - Streamlined Workflow
Shared forklift systems promote a more fluid and responsive workflow. Operators can quickly access the nearest available forklift, reducing delays and bottlenecks in material handling processes. This is facilitated by real-time location tracking and dispatch systems. - Optimized Resource Allocation
Shared systems allow warehouse managers to allocate resources more effectively. Forklifts can be dynamically assigned to tasks based on priority and location, ensuring that resources are deployed where they are needed most. - Data-Driven Insights
With integrated data collection and analytics, shared forklift systems provide valuable insights into equipment usage, operator performance, and workflow patterns. This data can be used to identify areas for improvement and optimize warehouse operations further. - Improved Throughput
The combined effect of increased utilization, reduced idle time, and streamlined workflows results in improved throughput. Warehouses can move more goods in less time, increasing overall productivity and profitability.
Technological Enablers for Seamless Shared Forklift Operations
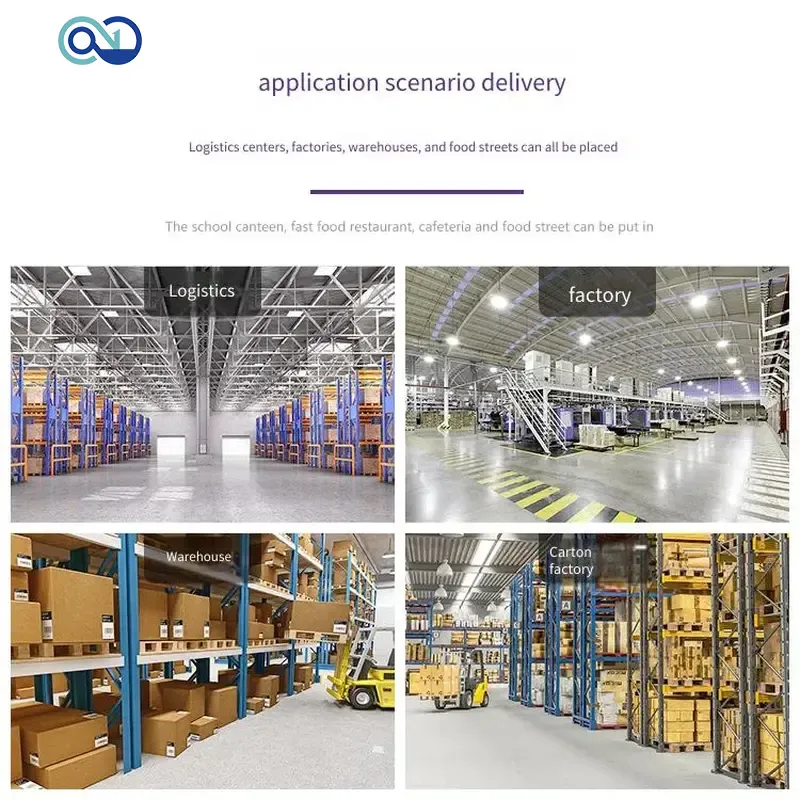
The seamless operation of shared forklift solutions hinges significantly on the integration of advanced technologies. These technologies facilitate efficient management, optimization, and accountability across shared forklift fleets. IoT devices provide real-time data on forklift location, usage, and condition, while telematics offer insights into operator behavior and equipment performance. Predictive analytics leverages this data to forecast maintenance needs, optimize deployment, and prevent downtime, ensuring that shared forklift operations are not only efficient but also highly reliable.
- How does IoT enhance shared forklift management?
IoT devices attached to forklifts transmit real-time data on location, operational status, and mechanical condition. This allows for precise tracking of each forklift, ensuring optimal deployment and preventing unauthorized use. Additionally, IoT data enables proactive maintenance by identifying potential mechanical issues before they lead to breakdowns, thereby minimizing downtime and repair costs. - What role does telematics play in optimizing shared forklift usage?
Telematics systems gather and analyze data on operator behavior, such as speed, load handling, and adherence to safety protocols. By monitoring these metrics, telematics helps identify areas for operator training and performance improvement, leading to safer and more efficient forklift operation. Moreover, telematics provides insights into usage patterns, allowing for better allocation of forklifts based on demand. - How do predictive analytics contribute to the efficiency of shared forklift fleets?
Predictive analytics uses historical and real-time data to forecast maintenance needs, optimize forklift deployment, and prevent equipment downtime. By analyzing data patterns, predictive analytics can identify forklifts at risk of mechanical failure, allowing for timely maintenance interventions. Furthermore, it helps optimize fleet size and allocation by predicting future demand, ensuring that the right number of forklifts are available at the right locations. - Can technology help prevent unauthorized use of shared forklifts?
Yes, technologies like RFID (Radio-Frequency Identification) and access control systems can ensure that only authorized personnel operate the forklifts. These systems require operators to use a unique ID or card to start the forklift, preventing unauthorized use and enhancing security. Additionally, geofencing technology can be used to restrict forklift operation to designated areas, preventing theft and misuse. - How does technology aid in scheduling and coordinating shared forklift usage?
Advanced scheduling software integrated with real-time tracking systems allows for efficient coordination of forklift usage. These systems enable warehouse managers to schedule forklift assignments based on demand, availability, and proximity to tasks. Operators can receive assignments directly through mobile devices, ensuring timely task completion and minimizing idle time. Furthermore, automated alerts can notify managers of any scheduling conflicts or delays, allowing for quick resolution and maintaining operational efficiency. - What is the impact of data analytics on improving the ROI of shared forklift solutions?
Data analytics provides actionable insights that drive continuous improvement in shared forklift operations, thereby enhancing the return on investment (ROI). By analyzing data on usage, maintenance, and operational efficiency, businesses can identify areas for cost reduction, performance optimization, and resource allocation. For example, data analytics can reveal underutilized forklifts, allowing for reallocation or reduction of fleet size. Additionally, it can highlight inefficiencies in workflows, leading to process improvements that boost productivity and reduce operational costs. - How can AI be integrated into shared forklift solutions?
AI can optimize shared forklift operations through route optimization, predictive maintenance, and automated decision-making. AI algorithms can analyze real-time data to determine the most efficient routes for forklifts, reducing travel time and energy consumption. Additionally, AI can predict equipment failures based on historical data and usage patterns, enabling proactive maintenance and minimizing downtime. Furthermore, AI can automate decision-making processes, such as task assignment and resource allocation, improving overall operational efficiency and reducing the need for manual intervention.
Addressing Challenges and Mitigating Risks in Shared Forklift Solutions
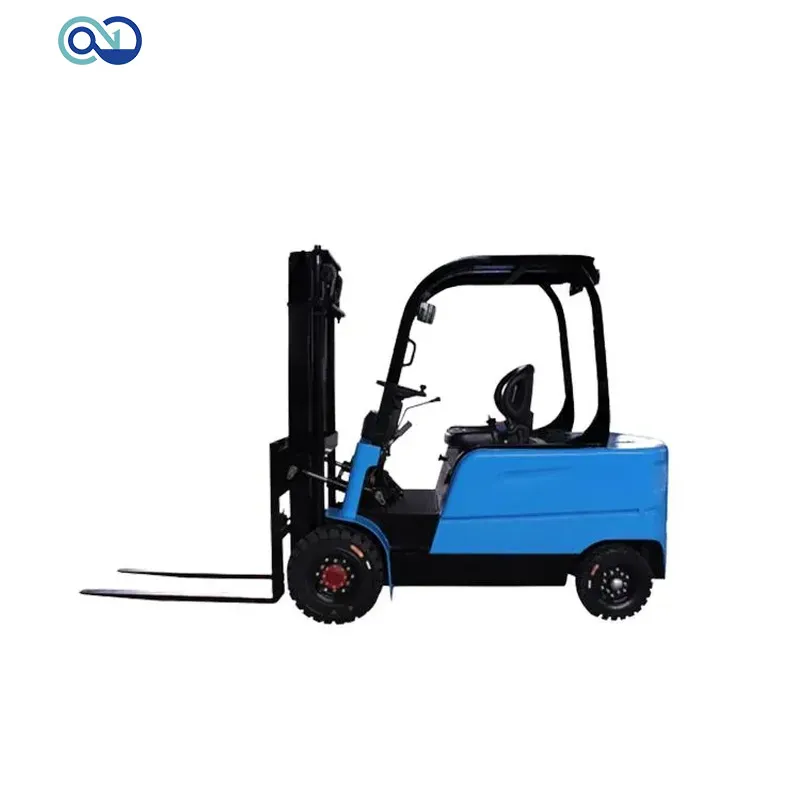
While shared forklift solutions offer numerous advantages, it's crucial to acknowledge and address the inherent challenges and risks to ensure successful implementation and sustained operational efficiency. These hurdles range from logistical complications like scheduling conflicts and maintenance coordination to issues of operator accountability and potential equipment misuse. Proactive identification and mitigation strategies are essential for smooth and effective shared forklift operations.
- Scheduling Conflicts
Challenge: Multiple users needing the same forklift at the same time can lead to delays and operational bottlenecks. Mitigation: Implement a robust scheduling system, potentially leveraging digital platforms, that allows for transparent booking and prioritizes tasks based on urgency and operational needs. Consider using a real-time tracking system to optimize allocation. - Maintenance Coordination
Challenge: Ensuring timely and consistent maintenance across a shared fleet can be complex, leading to potential downtime and increased repair costs. Mitigation: Establish a clear maintenance schedule with predefined intervals and responsibilities. Utilize IoT sensors and predictive analytics to anticipate maintenance needs and minimize disruptions. Implement a centralized maintenance management system accessible to all stakeholders. - Operator Responsibility and Training
Challenge: Determining responsibility for damage or misuse in a shared environment can be difficult. Inconsistent training levels among operators can also pose safety risks. Mitigation: Implement a comprehensive operator training program with certification requirements. Utilize telematics to monitor operator behavior and identify areas for improvement. Clearly define responsibility protocols for equipment damage and ensure accountability. - Equipment Misuse and Abuse
Challenge: Shared equipment is potentially subject to misuse or rough handling, especially when individual accountability is unclear. Mitigation: Incorporate usage monitoring systems, such as impact sensors and operational checklists, to track equipment handling. Implement a reward or penalty system based on equipment condition reports to encourage responsible use. - Security and Access Control
Challenge: Preventing unauthorized use of forklifts within a shared environment. Mitigation: Integrate access control systems, such as keycard or biometric authentication, to restrict forklift operation to authorized and trained personnel only. Implement geofencing to prevent equipment removal from designated areas. - Data Security and Privacy
Challenge: Ensuring the security and privacy of data collected by telematics and other monitoring systems. Mitigation: Implement robust data encryption and access control measures. Comply with relevant data privacy regulations and ensure transparency with operators regarding data collection practices.
Case Studies: Real-World Impact of Shared Forklift Implementation
Shared forklift solutions are revolutionizing material handling across various industries, offering compelling advantages over traditional ownership models. By examining real-world case studies, we can uncover tangible benefits and valuable lessons learned from companies that have successfully implemented shared forklift programs, showcasing the practical impact and strategic value of this innovative approach.
Below are examples demonstrating the transformative power of shared forklift solutions in diverse sectors:
- Case Study 1: Manufacturing Plant – Enhanced Efficiency and Reduced Costs
A large manufacturing plant implemented a shared forklift solution across its multiple warehouses. By utilizing a fleet management system with real-time tracking and automated scheduling, the plant reduced its forklift fleet size by 30% while simultaneously increasing throughput by 15%. This resulted in significant cost savings in equipment purchases, maintenance, and energy consumption. Operator training and accountability were also improved, leading to fewer accidents and equipment damage. - Case Study 2: Retail Distribution Center – Streamlined Operations and Improved Flexibility
A retail distribution center adopted a shared forklift model to manage its fluctuating inventory levels and seasonal demands. The center implemented a cloud-based platform that allowed them to dynamically allocate forklifts to different zones based on real-time needs. This flexibility enabled them to handle peak seasons without investing in additional equipment. They also saw a reduction in idle time and improved operator productivity, leading to faster order fulfillment and increased customer satisfaction. - Case Study 3: Food and Beverage Company – Optimized Warehouse Space and Enhanced Sustainability
A food and beverage company transitioned to a shared electric forklift fleet, which not only reduced their carbon footprint but also optimized warehouse space. The company installed strategically located charging stations and implemented a battery management system to ensure continuous operation. By sharing forklifts among different departments, they reduced the number of forklifts required and freed up valuable floor space for storage. This also resulted in lower energy costs and reduced reliance on fossil fuels, aligning with the company's sustainability goals. - Case Study 4: Logistics Provider – Scalable Solution and Improved Asset Utilization
A third-party logistics provider implemented a shared forklift solution across its network of warehouses, enabling them to scale their operations efficiently and improve asset utilization. The provider utilized telematics and data analytics to monitor forklift usage, identify bottlenecks, and optimize fleet allocation. This resulted in reduced equipment downtime, improved operator performance, and increased profitability. The shared model also allowed them to easily integrate new warehouses and adapt to changing customer demands. - Case Study 5: Cold Storage Facility – Robust Fleet Management and Reduced Maintenance
A cold storage facility implemented a shared forklift program with ruggedized equipment designed to withstand harsh conditions. By utilizing a comprehensive maintenance management system, the facility reduced equipment breakdowns and extended the lifespan of their forklifts. The shared model also enabled them to optimize battery charging schedules and minimize energy consumption. This resulted in lower maintenance costs, improved operational reliability, and enhanced safety for workers operating in cold environments.
These case studies illustrate the diverse benefits of shared forklift solutions, including cost savings, improved efficiency, enhanced flexibility, and increased sustainability. By carefully analyzing these real-world examples, companies can gain valuable insights into how to successfully implement and optimize shared forklift programs to achieve their specific operational goals.
Future Trends in Material Handling and Shared Logistics
The material handling and shared logistics sectors are on the cusp of significant transformation, driven by the relentless pursuit of efficiency, sustainability, and adaptability. As businesses navigate increasingly complex supply chains and heightened customer expectations, the integration of shared models, automation technologies, and digitalization strategies is poised to revolutionize warehouse management and overall logistics operations. This section explores the key trends shaping the future of material handling, offering insights into how companies can prepare for and leverage these advancements.
Here's a closer look at some of the most impactful trends:
- Increased Adoption of Automation
Automation is moving beyond basic tasks to encompass more complex processes within the warehouse. Expect to see greater use of autonomous forklifts, robotic picking systems, and automated guided vehicles (AGVs). These technologies enhance throughput, reduce labor costs, and improve safety by minimizing human error. The integration of AI and machine learning further optimizes automated systems, enabling them to adapt to changing conditions and make data-driven decisions. - Expansion of Shared Logistics Models
The shared forklift solution is just one facet of a broader trend towards shared logistics. Companies are increasingly exploring collaborative models for warehousing, transportation, and distribution. This includes sharing resources, infrastructure, and data to achieve economies of scale, improve asset utilization, and enhance supply chain resilience. Blockchain technology can play a crucial role in ensuring transparency and security within these shared networks. - Rise of Digital Twins and Simulation
Digital twin technology creates virtual replicas of physical warehouse environments, allowing companies to simulate different scenarios and optimize their operations without disrupting real-world processes. This enables proactive identification of bottlenecks, validation of new strategies, and fine-tuning of workflows. Simulation tools, powered by advanced analytics, provide valuable insights for improving efficiency and reducing costs. - Emphasis on Sustainable Practices
Sustainability is becoming a central focus in material handling and logistics. Companies are actively seeking ways to reduce their environmental footprint through initiatives such as using electric forklifts, optimizing transportation routes, and minimizing waste. Shared forklift solutions contribute to sustainability by promoting efficient use of resources and reducing the overall number of vehicles required. Furthermore, the adoption of circular economy principles, such as remanufacturing and recycling, is gaining traction. - Data-Driven Decision Making
The proliferation of IoT sensors and data analytics tools is transforming material handling into a data-rich environment. Companies are leveraging real-time data on equipment performance, inventory levels, and operational efficiency to make informed decisions. Predictive analytics algorithms can forecast maintenance needs, optimize inventory levels, and identify potential disruptions in the supply chain. This data-driven approach enables proactive problem-solving and continuous improvement. - Integration of Wearable Technology
Wearable devices, such as smart glasses and exoskeletons, are enhancing the capabilities of warehouse workers. Smart glasses provide hands-free access to information, improving picking accuracy and reducing errors. Exoskeletons reduce physical strain, improving worker comfort and productivity. These technologies empower workers to perform their tasks more efficiently and safely.
Frequently Asked Questions About Shared Forklift Solutions
This section addresses common inquiries about shared forklift solutions, offering clear, concise answers to help you understand the practical aspects and benefits of this innovative approach to material handling.
- What exactly is a Shared Forklift Solution?
A Shared Forklift Solution involves multiple users or departments within a facility, or even multiple companies within a shared space, accessing a common pool of forklifts. This eliminates the need for each entity to own and maintain its own fleet, leading to cost savings and increased efficiency. - What are the primary benefits of adopting a shared forklift model?
The key benefits include reduced capital expenditure, lower maintenance costs, improved equipment utilization, increased operational flexibility, and a smaller environmental footprint. It also minimizes downtime and streamlines warehouse operations. - How does a Shared Forklift Solution improve warehouse efficiency?
By optimizing equipment usage and reducing idle times, a shared forklift system ensures that forklifts are always in service when needed. This streamlined workflow enhances productivity and reduces bottlenecks within the warehouse. - What technologies are essential for managing a shared forklift fleet?
Essential technologies include IoT devices for real-time tracking, telematics for performance monitoring, and predictive analytics for maintenance scheduling. These tools enable efficient management, accountability, and proactive maintenance to minimize downtime. - What are the common challenges in implementing a Shared Forklift Solution, and how can they be addressed?
Common challenges include scheduling conflicts, maintenance coordination, and operator responsibility. These can be mitigated through the use of a robust management platform, clear communication protocols, and comprehensive training programs. Establishing clear guidelines and responsibilities is crucial for success. - Can you provide examples of industries that have successfully implemented Shared Forklift Solutions?
Industries such as logistics, warehousing, manufacturing, and retail have successfully adopted shared forklift models. These implementations have demonstrated significant cost savings, improved operational efficiency, and enhanced sustainability. - How does the Shared Forklift Solution contribute to sustainability?
By reducing the overall number of forklifts needed and optimizing equipment usage, a shared forklift solution minimizes energy consumption, reduces emissions, and promotes a more sustainable approach to material handling. It also decreases the demand for new forklift production, further reducing environmental impact.
The Shared Forklift Solution stands as a testament to modern industrial ingenuity, offering a scalable, cost-effective, and environmentally conscious approach to material handling. By embracing shared resources, businesses can unlock significant operational efficiencies, reduce their carbon footprint, and reallocate capital towards core strategic initiatives, much like how Zero One Solution Limited's one-stop PCB services empower clients to focus on innovation. This paradigm shift in logistics is not just about sharing equipment; it's about fostering a collaborative ecosystem that drives mutual growth and sustainable progress. Are you ready to optimize your material handling and join the future of shared logistics? Contact us today to explore how a Shared Forklift Solution can revolutionize your operations.
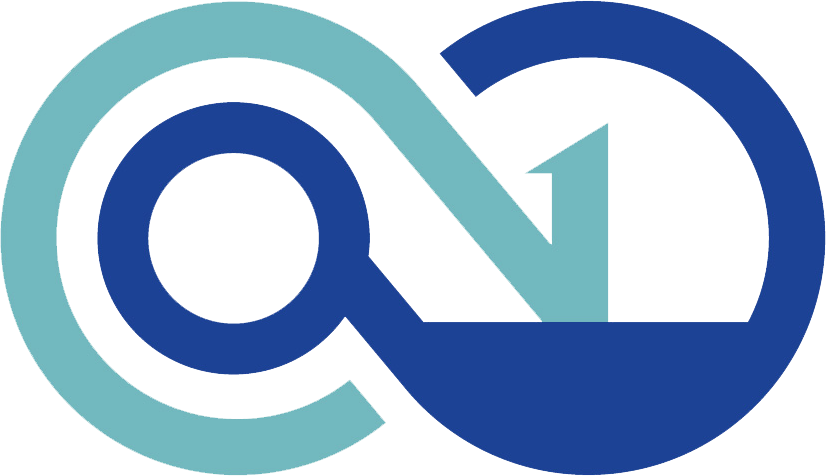