Shared Hair Washing Machine Solution
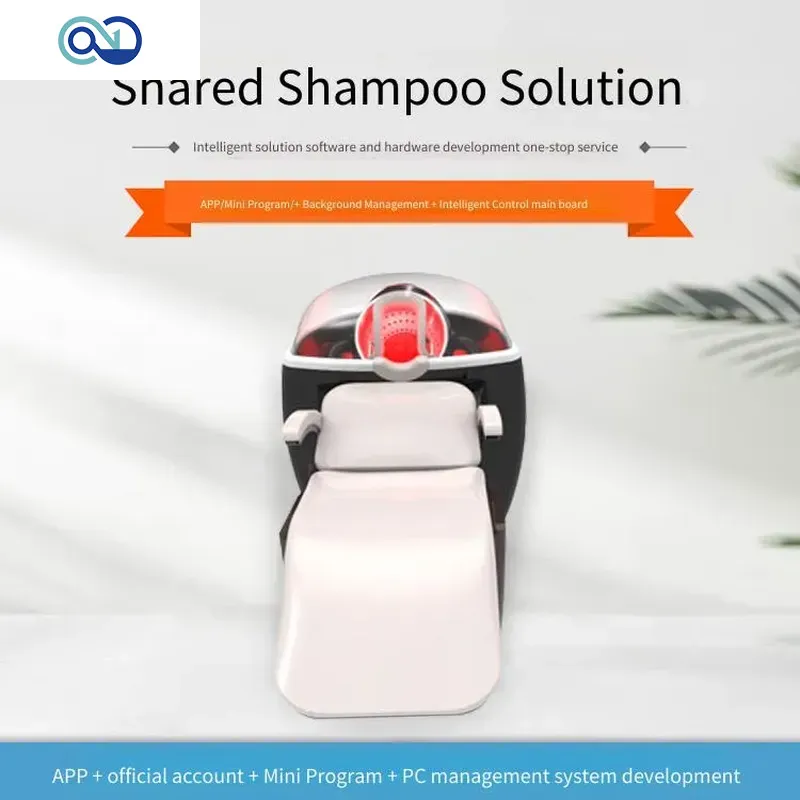
In today's fast-paced world, convenience and shared resources are increasingly important. Shared hair washing machines represent a fascinating intersection of technology and personal care, offering a convenient solution for individuals seeking efficient hair washing experiences, especially considering factors like limited mobility or optimizing personal time. But what powers these innovative devices? The answer lies in sophisticated PCB solutions. At Zero One Solution Limited, we specialize in providing cutting-edge PCB design, manufacturing, and assembly services that enable the functionality and reliability of shared hair washing machines. This article explores the critical role of PCB solutions in bringing these machines to life and how Zero One Solution Limited is at the forefront of this technological advancement.
Introduction to Shared Hair Washing Machines
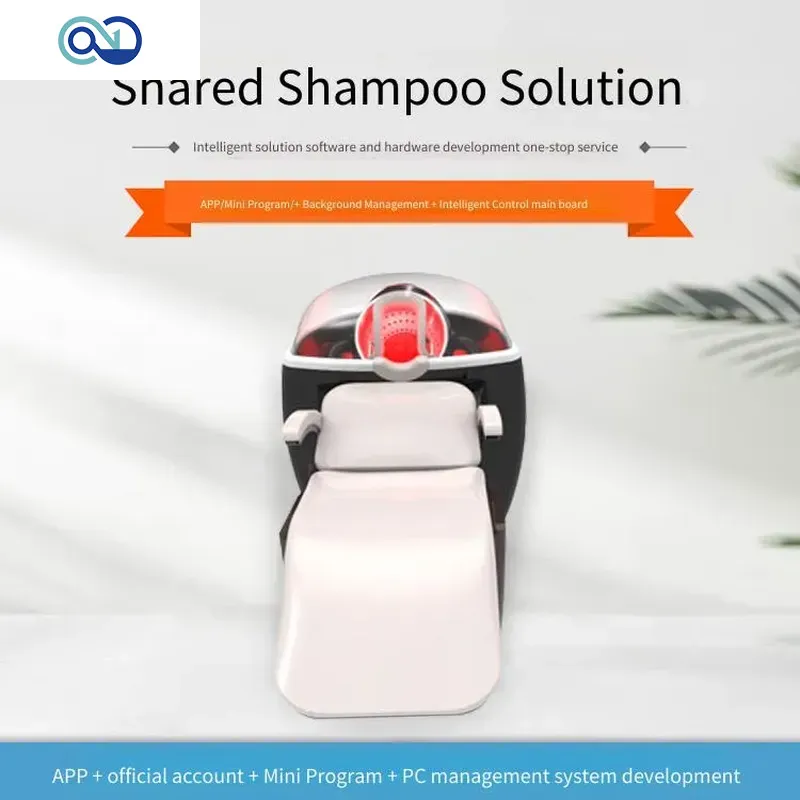
Shared hair washing machines are revolutionizing personal care, offering a blend of convenience, accessibility, and efficiency that caters to diverse needs. These innovative devices are gaining traction in various settings, from assisted living facilities enhancing the quality of life for residents, to modern homes and communal living spaces where convenience and resource sharing are valued. Their growing popularity stems from the ability to provide a consistent, hygienic, and user-friendly hair washing experience, particularly beneficial for individuals with mobility issues or those seeking a more efficient hair care routine.
- What are the primary benefits of using a shared hair washing machine?
Shared hair washing machines offer numerous advantages, including enhanced convenience, particularly for individuals with limited mobility. They ensure consistent and hygienic hair washing, saving time and effort compared to traditional methods. Moreover, they promote accessibility in communal settings, making personal care more inclusive and efficient. - In what types of environments are shared hair washing machines commonly used?
These machines are increasingly found in assisted living facilities to improve residents' comfort and independence. They are also popular in modern homes for their convenience and efficiency. Additionally, communal living spaces, such as dormitories and co-housing communities, benefit from shared hair washing machines by providing accessible and hygienic hair care solutions for all residents. - How do shared hair washing machines improve accessibility for individuals with disabilities?
Shared hair washing machines are designed with accessibility in mind, featuring adjustable settings and ergonomic designs that accommodate users with mobility challenges. They reduce the physical strain associated with traditional hair washing, allowing individuals with disabilities to maintain personal hygiene with greater ease and dignity. - What makes shared hair washing machines more efficient than traditional hair washing methods?
Shared hair washing machines streamline the hair washing process by automating tasks such as shampoo dispensing, water temperature control, and rinsing. This automation reduces the time and effort required for hair washing, making it more efficient for all users, especially those with busy schedules or physical limitations. - Are shared hair washing machines hygienic, and what measures are in place to ensure cleanliness?
Yes, hygiene is a key consideration in the design of shared hair washing machines. Many models incorporate self-cleaning cycles and antimicrobial materials to prevent the growth of bacteria and fungi. Regular maintenance and cleaning further ensure a hygienic hair washing experience for all users. - Can shared hair washing machines be customized to meet individual user preferences?
Many shared hair washing machines offer customizable settings to accommodate individual user preferences. These settings may include adjustable water temperature, massage intensity, and shampoo dispensing levels, allowing users to tailor the hair washing experience to their specific needs and comfort levels. - What are the key features to look for when selecting a shared hair washing machine for a specific environment?
When selecting a shared hair washing machine, consider factors such as ease of use, adjustability, hygiene features, and durability. Look for models with intuitive controls, adjustable height and angle settings, self-cleaning functions, and robust construction to ensure long-lasting performance in a shared environment.
The Core Role of PCBs in Hair Washing Machine Functionality
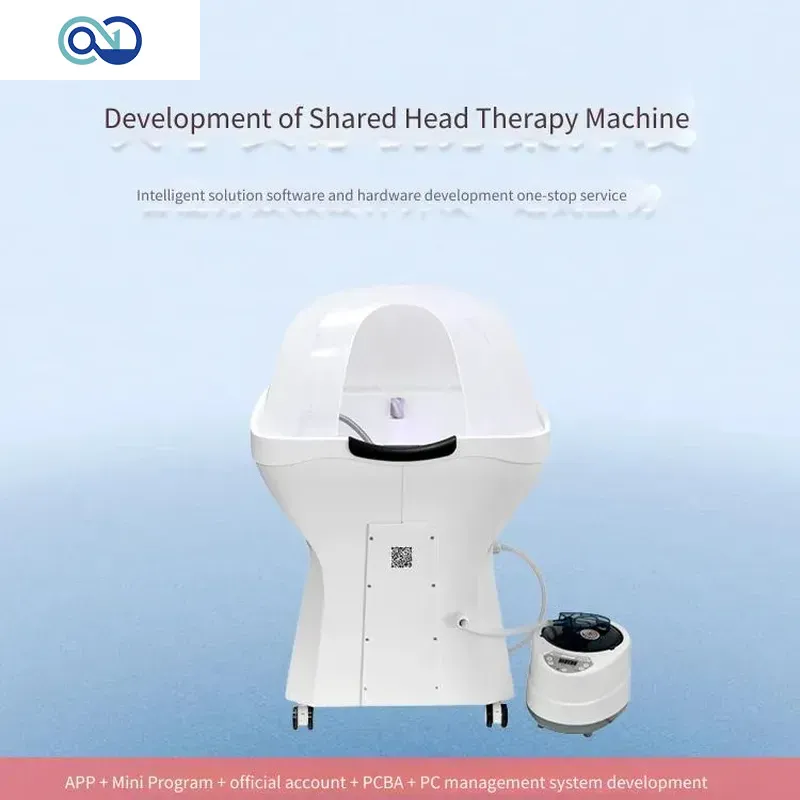
Printed Circuit Boards (PCBs) are the unsung heroes within shared hair washing machines, functioning as the central nervous system that orchestrates all automated processes. They are the backbone that enables these machines to deliver a consistent and user-friendly hair washing experience.
Here's a detailed look at the core functionalities PCBs enable:
- Water Temperature Regulation:
PCBs precisely control heating elements to maintain the desired water temperature, ensuring a comfortable and safe experience, preventing scalding or ineffective cleaning. - Shampoo and Conditioner Dispensing:
PCBs manage the automated dispensing of shampoo and conditioner, controlling the amount and timing for optimal cleaning and conditioning. This ensures consistent dosage and reduces waste. - Massage Feature Control:
Many shared hair washing machines incorporate massage features to enhance relaxation. PCBs govern the intensity and patterns of these massage elements, offering users a customizable experience. - Drying Mechanisms:
PCBs manage the operation of drying fans or heating elements, controlling the temperature and duration of the drying cycle. This feature ensures efficient and safe hair drying. - Sensor Integration:
PCBs process data from various sensors, such as water level sensors, temperature sensors, and hair detection sensors, to optimize performance and safety. These sensors allow the machine to adapt to different hair types and conditions. - User Interface and Controls:
PCBs drive the user interface, allowing users to select desired settings, monitor progress, and receive feedback. This includes managing buttons, displays, and touchscreens. - Safety Mechanisms:
PCBs are integral to safety mechanisms, such as automatically shutting off the machine if temperatures exceed safe limits or if water levels are too low. This ensures user safety and prevents damage to the machine.
Key Considerations for PCB Design in Hair Washing Machines
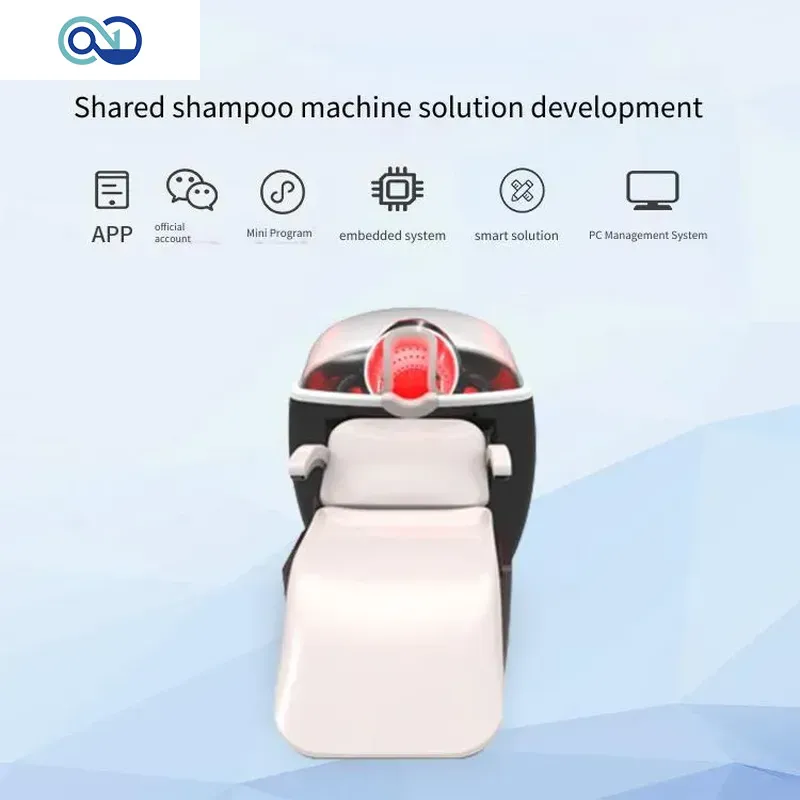
PCBs in shared hair washing machines demand careful design considerations to ensure reliable operation in challenging environments. Balancing performance with durability and safety is paramount. Key factors include moisture resistance to combat humidity, effective thermal management to dissipate heat from components, strict adherence to safety standards to protect users, and robust construction to withstand frequent use. Thoughtful component selection and strategic PCB layout are essential for achieving both longevity and consistent performance.
- Why is moisture resistance so critical in hair washing machine PCBs?
Hair washing machines operate in humid environments, making PCBs susceptible to moisture-related failures. Moisture can lead to corrosion, short circuits, and decreased insulation resistance. Conformal coatings and sealed enclosures are crucial to protect the PCB from moisture ingress and ensure reliable long-term performance. - What thermal management strategies are essential for PCBs in this application?
The electronic components on PCBs generate heat during operation. Inadequate thermal management can lead to overheating, reduced component lifespan, and system failure. Heat sinks, thermal vias, and strategic component placement are necessary to dissipate heat effectively and maintain optimal operating temperatures. Consider using thermally conductive materials in the PCB construction to further enhance heat dissipation. - Which safety standards are relevant for hair washing machine PCBs?
Compliance with relevant safety standards is paramount to protect users from electrical hazards. Standards such as IEC 60335-1 (Household and similar electrical appliances - Safety) and related part 2 standards are crucial. PCB design must incorporate features such as reinforced insulation, proper grounding, and overcurrent protection to meet these safety requirements. - How does component selection impact the reliability of hair washing machine PCBs?
Selecting high-quality, reliable components is crucial for ensuring the longevity of PCBs in hair washing machines. Components should be rated for the operating temperature range, voltage levels, and environmental conditions they will experience. Derating components and choosing those with proven track records can significantly improve PCB reliability. - Why is PCB layout so important for optimal performance?
Strategic PCB layout minimizes signal interference, reduces noise, and optimizes power distribution. Careful placement of components, proper routing of traces, and effective grounding techniques are essential for achieving reliable performance. Consider impedance control for critical signal paths and use simulation tools to verify signal integrity. - What role does material selection play in the durability of hair washing machine PCBs?
The base material of the PCB significantly affects its durability and resistance to environmental factors. Materials with high glass transition temperatures (Tg) and good chemical resistance are preferred. Consider using materials that meet industry standards for flame retardancy and environmental compliance, such as RoHS. - How can Zero One Solution Limited assist with PCB design for shared hair washing machines?
Zero One Solution Limited offers comprehensive PCB design, manufacturing, and assembly services tailored to the specific requirements of hair washing machines. Our expertise in rapid prototyping allows for quick testing and refinement of designs, reducing time-to-market and development costs. We adhere to strict quality assurance procedures and industry standards to ensure the highest levels of reliability and performance.
Zero One Solution's Expertise in PCB Solutions for Hair Washing Machines
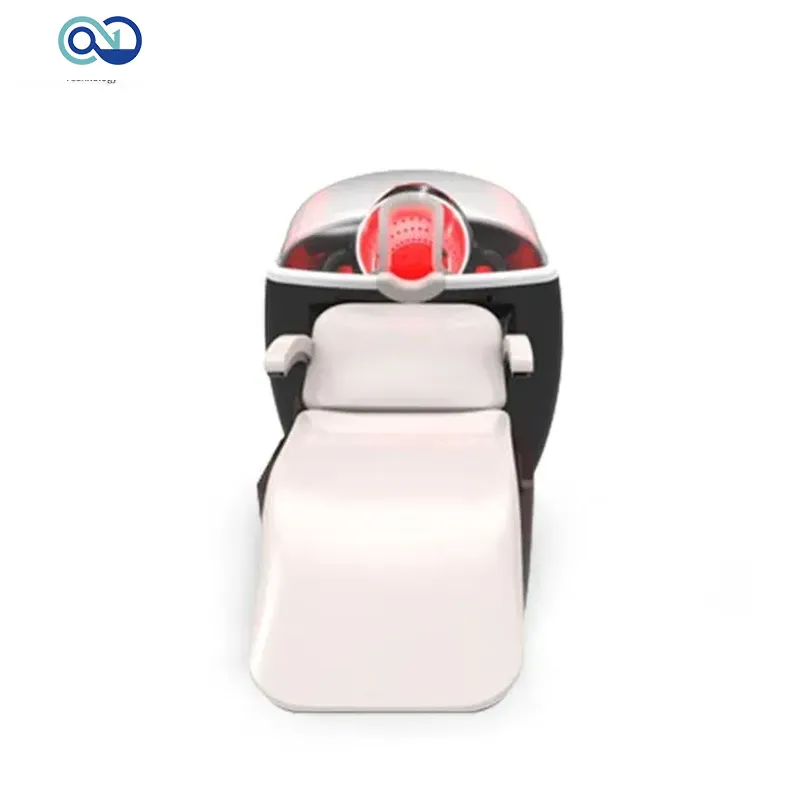
Zero One Solution Limited stands as a leading provider of PCB solutions, uniquely positioned to address the specialized needs of the hair washing machine industry. We excel in rapid prototyping and offer comprehensive, one-stop services encompassing PCB design, manufacturing, and assembly, enabling our clients to innovate and accelerate their product development cycles.
Founded in 2011, Zero One Solution Limited has rapidly become a trusted partner for companies developing cutting-edge hair washing machine technology. Our expertise is built on a foundation of rapid-response R&D prototype manufacturing, empowering our clients to bring innovative solutions to market with exceptional efficiency. Headquartered in Shenzhen, China's electronic manufacturing hub, and with a branch office in Dubai, we operate strategically within a global PCBA supply chain network, ensuring seamless access to worldwide resources and support.
- What specific PCB design considerations are crucial for hair washing machines?
Given the operating environment of hair washing machines, PCBs must be designed with a focus on moisture resistance, thermal management, and adherence to stringent safety standards. Component selection and layout are also critical to ensuring reliable performance and longevity. - How does Zero One Solution ensure the quality and reliability of PCBs for hair washing machines?
Zero One Solution is committed to quality assurance, employing rigorous testing procedures throughout the PCB manufacturing process. We adhere to industry standards and certifications to guarantee the highest levels of reliability and performance. - What PCB manufacturing and assembly services does Zero One Solution offer?
We provide comprehensive one-stop services that cover the entire PCB lifecycle, from initial design and rapid prototyping to full-scale manufacturing and assembly. This integrated approach ensures seamless transitions between stages and optimizes overall project efficiency. - How does Zero One Solution's rapid prototyping service benefit hair washing machine manufacturers?
Our rapid prototyping capabilities enable clients to quickly test and refine their hair washing machine designs. This reduces time-to-market and development costs through agile manufacturing and iterative design processes. - Can Zero One Solution provide custom PCB solutions tailored to the specific needs of hair washing machines?
Yes, we specialize in delivering custom PCB solutions designed to meet the unique requirements and challenges of each hair washing machine project. Our collaborative approach ensures that the final product aligns perfectly with the client's objectives. - What is Zero One Solution's experience in the hair washing machine industry?
We have extensive experience in catering to the hair washing machine industry's specific requirements. Our proven track record demonstrates our ability to deliver high-quality, reliable PCB solutions that enhance product performance and market success.
Rapid Prototyping for Accelerated Product Development
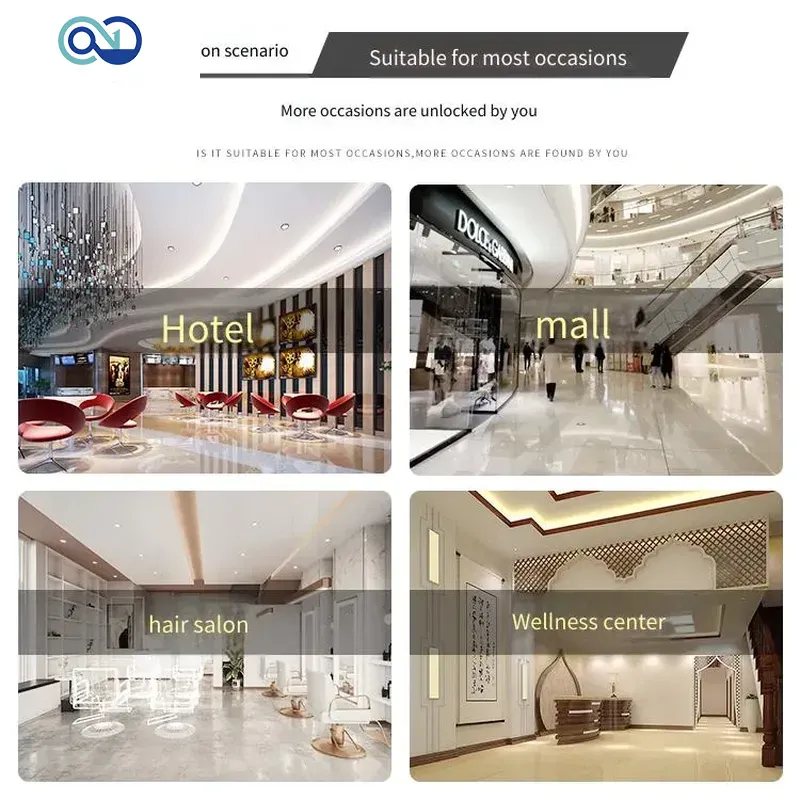
Zero One Solution's rapid prototyping services are designed to empower clients to swiftly test and refine their hair washing machine designs, significantly reducing time-to-market and overall development costs. By leveraging agile manufacturing and iterative design processes, we enable manufacturers to identify and address potential design flaws early on, leading to a more efficient and cost-effective product development lifecycle.
Here’s how our rapid prototyping process benefits your project:
- Accelerated Time-to-Market:
Quickly iterate through design revisions, allowing for faster product launches. - Reduced Development Costs:
Early detection of design issues minimizes costly rework and redesigns. - Enhanced Design Validation:
Thoroughly test and validate design concepts before committing to mass production. - Increased Innovation:
Experiment with new features and functionalities without significant financial risk. - Agile Manufacturing:
Adapt to changing market demands and customer feedback with ease.
The iterative design process is central to our rapid prototyping approach. This involves:
- Design:
Creating initial PCB designs based on client specifications. - Prototyping:
Fabricating quick-turn prototypes using advanced manufacturing techniques. - Testing:
Conducting comprehensive testing to identify areas for improvement. - Refinement:
Incorporating feedback from testing to optimize the design. - Iteration:
Repeating the process until the design meets all performance and reliability requirements.
By embracing rapid prototyping, Zero One Solution empowers hair washing machine manufacturers to stay ahead of the competition, delivering innovative and reliable products to market faster and more efficiently.
Ensuring Quality and Reliability in PCB Manufacturing

At Zero One Solution Limited, quality and reliability are not just buzzwords; they are the cornerstones of our PCB manufacturing process for shared hair washing machines. We understand that the performance and longevity of these devices hinge on the robustness of their PCBs. Therefore, we implement stringent quality assurance measures and rigorous testing procedures at every stage of production.
Our commitment to quality is reflected in our adherence to industry standards and certifications, ensuring that our PCB solutions meet the highest levels of performance and reliability. Here’s how we ensure the quality and reliability of our PCBs:
- Comprehensive Design Review
Before manufacturing begins, our experienced engineers conduct thorough design reviews to identify potential issues related to manufacturability, signal integrity, thermal management, and component placement. This proactive approach helps prevent defects and ensures optimal performance. - Stringent Material Selection
We use only high-quality materials from trusted suppliers who meet our strict quality standards. This includes selecting appropriate laminates, copper foils, and surface finishes that can withstand the demanding operating conditions of hair washing machines, such as high humidity and temperature variations. - Advanced Manufacturing Processes
Our state-of-the-art manufacturing facilities are equipped with advanced equipment and technologies to ensure precise and consistent PCB fabrication. We employ automated optical inspection (AOI) and X-ray inspection to detect any defects, such as shorts, opens, and misalignments, during the manufacturing process. - Rigorous Testing Procedures
We conduct a comprehensive suite of tests to verify the functionality, performance, and reliability of our PCBs. These tests include:
- Electrical Testing
Ensures that all electrical connections are correct and that the PCB meets specified electrical parameters. - In-Circuit Testing (ICT)
Verifies the functionality of individual components and circuits on the PCB. - Functional Testing
Simulates the actual operating conditions of the hair washing machine to ensure that the PCB performs as expected. - Environmental Testing
Subjects the PCB to extreme temperatures, humidity levels, and vibration to assess its durability and resistance to environmental factors.
By adhering to these rigorous quality assurance and testing procedures, Zero One Solution Limited ensures that our PCB solutions for shared hair washing machines meet the highest standards of quality, reliability, and performance. Our commitment to excellence enables our clients to deliver innovative and dependable products to the market.
The Future of Shared Hair Washing Machines and PCB Innovation
The shared hair washing machine industry is poised for significant advancements, driven by technological innovation and evolving consumer expectations. Printed circuit boards (PCBs) will be at the heart of these future developments, enabling more sophisticated functionalities, enhanced user experiences, and greater connectivity. Zero One Solution is committed to staying at the forefront of PCB innovation to support the next generation of shared hair washing machines.
Several emerging trends are shaping the future of shared hair washing machines:
- Integration with IoT Devices
Future hair washing machines will likely be integrated with the Internet of Things (IoT), allowing users to control and monitor the devices remotely via smartphones or other smart devices. This connectivity enables features such as remote scheduling, usage tracking, and personalized settings stored in the cloud. PCBs will play a vital role in facilitating this connectivity, ensuring seamless communication between the hair washing machine and other IoT devices. - AI-Powered Personalization
Artificial intelligence (AI) can be used to personalize the hair washing experience based on individual user preferences and hair types. AI algorithms can analyze data from sensors to optimize water temperature, shampoo dosage, and massage intensity, delivering customized treatments that cater to specific needs. Advanced PCBs will be needed to process the complex data and control the various machine functions in real-time. - Advanced Sensor Technology
Future hair washing machines will incorporate advanced sensor technology to monitor various parameters, such as water quality, hair condition, and skin sensitivity. These sensors can provide valuable feedback to optimize the washing process and ensure a safe and effective treatment. PCBs will be responsible for collecting and processing the sensor data, enabling intelligent control and feedback mechanisms. - Eco-Friendly Designs
Sustainability is becoming increasingly important, and future hair washing machines will likely incorporate eco-friendly designs that minimize water and energy consumption. This includes features such as water recycling systems, energy-efficient heating elements, and biodegradable materials. PCBs can contribute to sustainability by optimizing power consumption and reducing electronic waste. - Enhanced Safety Features
Safety is paramount, and future hair washing machines will include enhanced safety features to prevent accidents and injuries. This includes features such as automatic shut-off mechanisms, temperature sensors, and water leak detection systems. PCBs will be crucial in implementing these safety features, ensuring reliable operation and preventing hazardous situations.
Zero One Solution is actively developing innovative PCB solutions to enable these future advancements. We are investing in research and development to create PCBs that are more powerful, efficient, and reliable. Our expertise in rapid prototyping and agile manufacturing allows us to quickly adapt to emerging trends and deliver cutting-edge solutions that meet the evolving needs of the shared hair washing machine industry.
Case Studies: Zero One Solution's Successful Hair Washing Machine Projects
Zero One Solution Limited has consistently delivered tailored PCB solutions that significantly enhance the performance, efficiency, and market success of hair washing machines. The following case studies illustrate our commitment to addressing specific client needs and challenges within this innovative sector. These examples demonstrate our expertise in rapid prototyping, quality manufacturing, and collaborative problem-solving, ultimately enabling our partners to achieve their product development and business goals.
Case Study 1: Enhanced Thermal Management for a Leading Hair Washing Machine Manufacturer
Client: A top-tier manufacturer of shared hair washing machines renowned for their innovative features and sleek designs.
Challenge: The client faced issues with overheating in their high-end hair washing machine model due to the complex integration of heating elements, massage motors, and drying fans. This overheating led to performance degradation and potential safety concerns.
Solution: Zero One Solution conducted a thorough thermal analysis of the existing PCB design. We then developed a custom PCB solution incorporating advanced thermal management techniques, including:
- Optimized Copper Traces:
Strategically widened and thickened copper traces to improve heat dissipation. - Thermal Vias:
Implemented an array of thermal vias to conduct heat away from critical components and spread it across the PCB. - High Thermal Conductivity Substrate:
Utilized a specialized PCB substrate material with enhanced thermal conductivity properties.
Results: The redesigned PCB, implemented by Zero One Solution, resulted in a 30% reduction in operating temperature, significantly improving the reliability and lifespan of the hair washing machine. The client reported a decrease in field failures related to overheating and enhanced customer satisfaction.
Case Study 2: Cost-Effective PCB Design for a Startup
Client: An innovative startup company developing a low-cost, shared hair washing machine for use in budget-conscious salons.
Challenge: The startup needed a reliable and functional PCB solution while adhering to a strict budget. They required a cost-optimized design without compromising on performance or safety.
Solution: Zero One Solution collaborated closely with the startup to identify opportunities for cost reduction without sacrificing essential functionality. Our approach included:
- Component Selection:
Carefully selected cost-effective components with proven reliability and performance. - Simplified PCB Layout:
Optimized the PCB layout to reduce the number of layers and minimize material usage. - DFM Optimization:
Implemented Design for Manufacturing (DFM) principles to streamline the manufacturing process and reduce production costs.
Results: Zero One Solution delivered a PCB solution that met the startup's performance requirements while reducing PCB costs by 20%. This enabled the client to launch their product successfully within their target budget and gain a competitive edge in the market.
FAQs About PCB Solutions for Shared Hair Washing Machines
This section addresses frequently asked questions concerning PCB (Printed Circuit Board) solutions for shared hair washing machines. We aim to provide clarity on crucial aspects such as cost optimization, material selection, regulatory compliance, design considerations, manufacturing processes, and ensuring the reliability of PCBs in these specialized devices. Our goal is to equip you with the knowledge needed to make informed decisions about your PCB requirements.
- What are the key PCB design considerations for shared hair washing machines?
Key considerations include moisture resistance to prevent corrosion and electrical shorts, thermal management to dissipate heat generated by components, compliance with safety standards (e.g., UL, CE) to ensure user safety, durability to withstand frequent use and vibrations, and efficient power distribution to support various functionalities like water heating, massage, and drying. - How can I optimize PCB costs for shared hair washing machines without compromising quality?
Cost optimization strategies involve selecting appropriate materials based on performance requirements rather than over-specifying, optimizing PCB layer count and size to minimize material usage, utilizing efficient manufacturing processes, negotiating pricing with PCB suppliers, and implementing design for manufacturability (DFM) principles to reduce manufacturing defects and rework. - What materials are commonly used for PCBs in shared hair washing machines?
Common PCB materials include FR-4 (a fiberglass epoxy laminate), which offers a good balance of cost, performance, and processability. High-temperature FR-4 variants may be used for components generating significant heat. For applications requiring enhanced thermal performance, metal core PCBs (MCPCBs) with aluminum or copper cores can be employed to efficiently dissipate heat. - What regulatory compliance standards apply to PCBs used in hair washing machines?
Relevant regulatory compliance standards include UL (Underwriters Laboratories) standards for safety, CE (Conformité Européenne) marking for European market access, RoHS (Restriction of Hazardous Substances) directive to limit the use of hazardous materials, and REACH (Registration, Evaluation, Authorisation and Restriction of Chemicals) regulation to ensure the safe use of chemicals in PCB manufacturing. Compliance with these standards ensures product safety and environmental responsibility. - How does Zero One Solution ensure the reliability of PCBs for shared hair washing machines?
Zero One Solution employs rigorous quality control measures throughout the PCB manufacturing process, including incoming material inspection, automated optical inspection (AOI) for defect detection, in-circuit testing (ICT) to verify component functionality, functional testing to simulate real-world operating conditions, and environmental stress testing (e.g., temperature cycling, humidity testing) to assess long-term reliability. We also adhere to industry best practices and certifications, such as ISO 9001, to ensure consistent quality. - What PCB manufacturing capabilities does Zero One Solution offer for hair washing machines?
Zero One Solution offers a comprehensive range of PCB manufacturing capabilities, including rapid prototyping for quick design iterations, multi-layer PCB fabrication, surface mount technology (SMT) assembly, through-hole assembly, mixed technology assembly, and box build assembly. We also provide value-added services such as conformal coating, potting, and encapsulation to protect PCBs from harsh environments. - How can Zero One Solution help with PCB design for shared hair washing machines?
Zero One Solution provides expert PCB design services, including schematic capture, PCB layout, signal integrity analysis, thermal analysis, and design for manufacturability (DFM) optimization. Our experienced engineers work closely with clients to understand their specific requirements and develop custom PCB designs that meet their performance, cost, and reliability goals.
Shared hair washing machines represent a significant advancement in personal care technology, offering convenience and accessibility to a wide range of users. The reliable and efficient operation of these machines hinges on the quality and performance of their PCB solutions. Zero One Solution Limited is dedicated to providing cutting-edge PCB design, manufacturing, and assembly services that empower hair washing machine manufacturers to create innovative and reliable products. As the demand for shared hair washing machines continues to grow, Zero One Solution remains committed to staying at the forefront of PCB innovation, enabling the future of personal care technology. Contact us today to discuss your PCB needs and discover how we can help you bring your hair washing machine vision to life. Visit our website or call us to learn more.
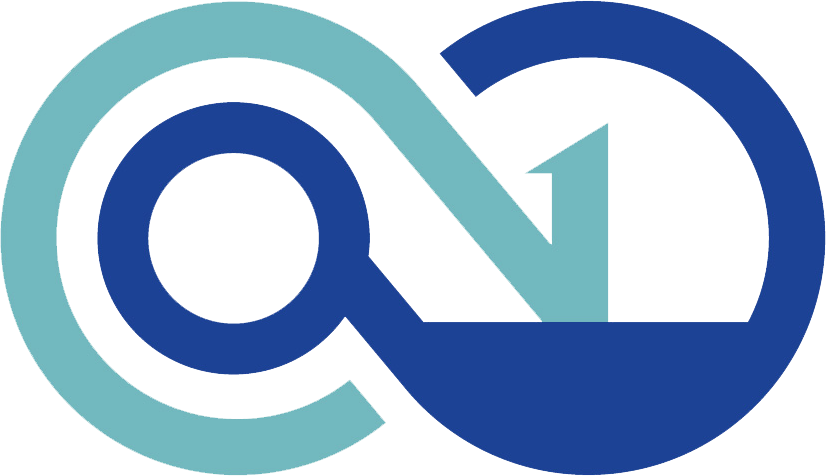