Shared Juicer Software Solution
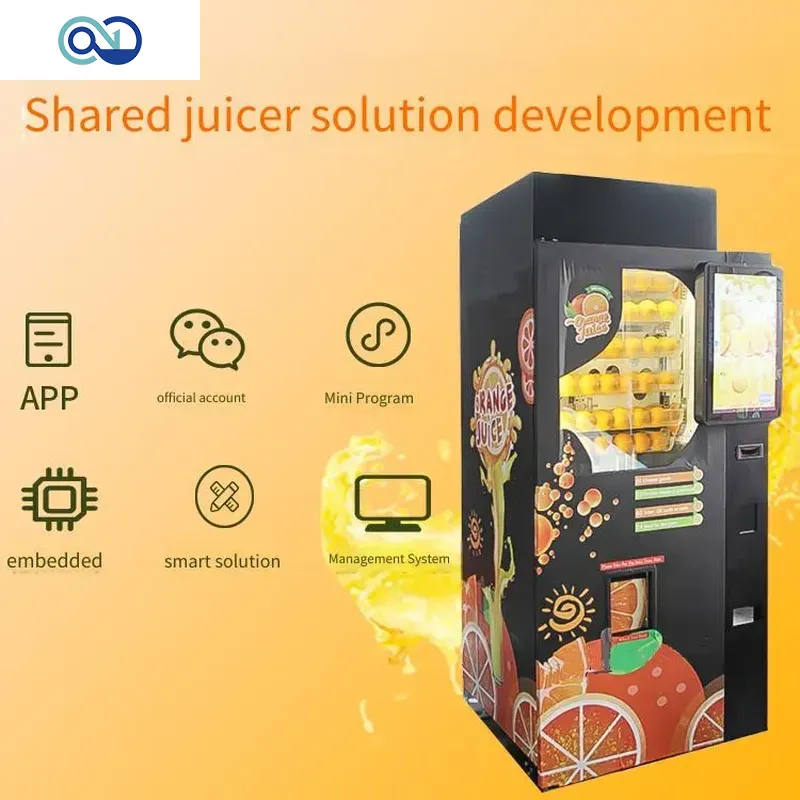
In today's fast-paced electronics industry, efficiency and collaboration are paramount. Imagine a world where PCB design and assembly processes are seamlessly integrated, eliminating bottlenecks and accelerating time-to-market. This vision is now a reality with Shared Juicer, a revolutionary software solution designed to streamline your entire PCB workflow. What if a software could harmonize design and manufacturing teams, reducing errors and optimizing resource allocation? Let's explore how Shared Juicer transforms PCB solutions through seamless collaboration and optimized processes.
Understanding the Challenges of Traditional PCB Design and Assembly
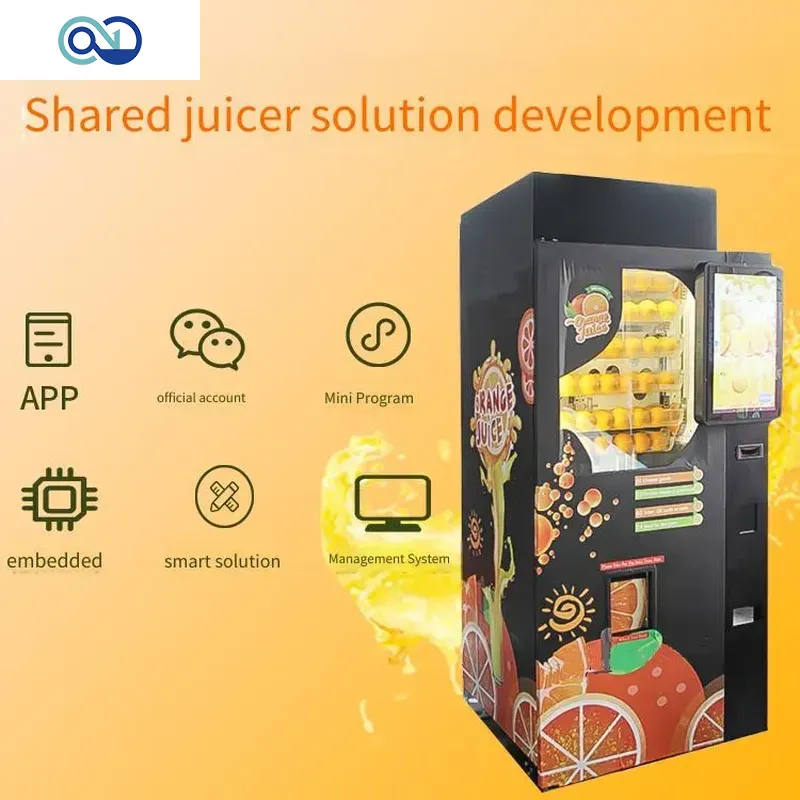
Traditional PCB design and assembly processes often grapple with significant hurdles. These challenges can stem from disjointed communication channels, leading to misunderstandings and errors, to the complexities of managing multiple design versions, which can result in costly rework and delays. Inefficient allocation of resources further compounds these issues, hindering productivity and extending project timelines. Understanding these pain points is crucial for recognizing the value of modern, collaborative solutions.
- Communication Breakdowns
Traditional methods often rely on email chains, phone calls, and in-person meetings for communication. This fragmented approach can lead to misinterpretations, delays in information sharing, and a lack of transparency across the project team. Without a centralized communication platform, critical design decisions and modifications can easily get lost in translation, resulting in costly errors and rework. - Version Control Issues
Managing different versions of PCB designs is a persistent challenge. Without a robust version control system, teams may struggle to track changes, identify the most current design, and revert to previous versions when necessary. This can lead to confusion, duplicated effort, and the risk of manufacturing PCBs based on outdated or incorrect designs. - Inefficient Resource Allocation
Traditional PCB design and assembly often involve manual processes and a lack of real-time visibility into resource availability. This can result in inefficient allocation of personnel, equipment, and materials, leading to delays, increased costs, and missed deadlines. Optimizing resource allocation is critical for maximizing productivity and minimizing waste in the PCB workflow. - Data Silos and Lack of Centralized Information
Design data, component information, and manufacturing specifications are often stored in disparate systems and formats. This lack of a centralized repository makes it difficult for team members to access the information they need, when they need it. Data silos hinder collaboration, increase the risk of errors, and make it challenging to track project progress. - Manual Processes and Automation Gaps
Many traditional PCB design and assembly processes still rely on manual methods, such as manual component placement, soldering, and inspection. These manual steps are time-consuming, prone to errors, and limit the ability to scale production. Automating key processes is essential for improving efficiency, reducing costs, and ensuring consistent quality. - Lack of Real-time Visibility and Reporting
Traditional PCB workflows often lack real-time visibility into project status, component availability, and manufacturing progress. This makes it difficult to identify potential bottlenecks, track key performance indicators (KPIs), and make informed decisions. Comprehensive reporting and analytics are essential for optimizing the PCB design and assembly process. - Challenges in Design for Manufacturability (DFM)
Ensuring that a PCB design is manufacturable is a critical step in the process. Traditional methods of DFM often involve manual reviews and communication between design and manufacturing teams, which can be time-consuming and prone to errors. Integrating DFM checks early in the design process is essential for avoiding costly rework and delays.
Introducing Shared Juicer: A Collaborative Software Solution
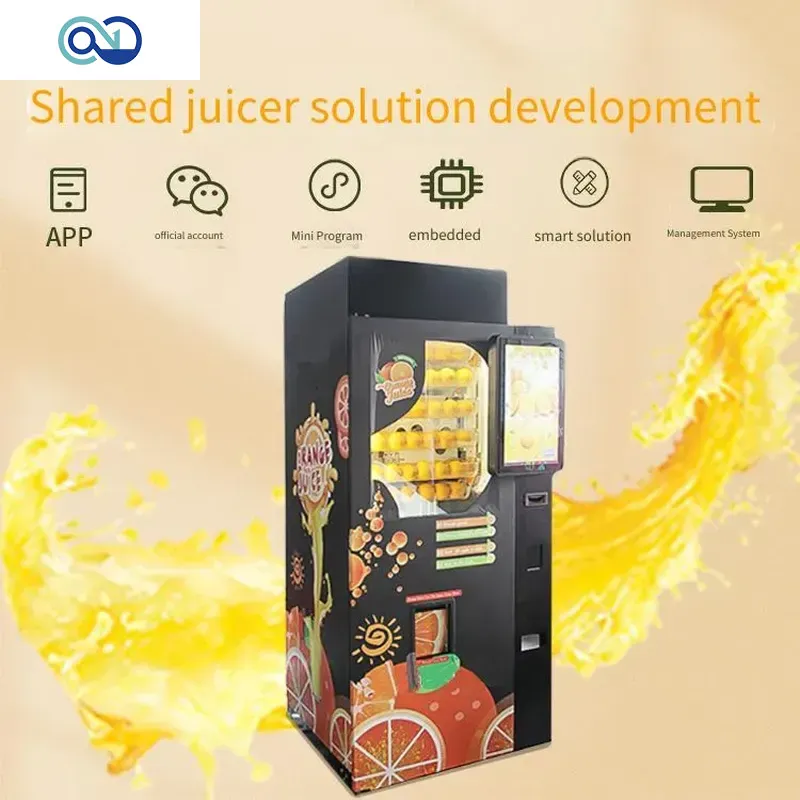
Shared Juicer is a cutting-edge software solution designed to revolutionize PCB design and assembly workflows through enhanced collaboration. It addresses the critical need for seamless communication and data management in complex PCB projects, offering a centralized platform that connects design, engineering, and manufacturing teams. By fostering real-time collaboration and providing a unified environment for all project stakeholders, Shared Juicer significantly reduces errors, accelerates development cycles, and streamlines the entire PCB production process.
At its core, Shared Juicer provides a suite of functionalities tailored to the specific challenges of PCB development. These functionalities include:
- Real-Time Collaboration
Enables multiple users to work on the same project simultaneously, with changes instantly visible to all collaborators. This eliminates version control issues and ensures everyone is always working with the latest design data. - Centralized Data Management
Provides a single, secure repository for all project-related files, including schematics, layouts, BOMs, and manufacturing data. This eliminates data silos and ensures easy access to information for all team members. - Automated Workflows
Streamlines repetitive tasks and reduces manual errors through automated workflows for design reviews, BOM generation, and manufacturing handoff. This frees up engineers to focus on more critical aspects of the design process. - Comprehensive Reporting
Offers detailed reporting and analytics on project progress, resource utilization, and potential bottlenecks. This provides valuable insights for optimizing workflows and improving overall efficiency.
The benefits of implementing Shared Juicer extend beyond just improved collaboration. By streamlining workflows, reducing errors, and accelerating time-to-market, Shared Juicer empowers PCB design and assembly teams to achieve significant improvements in efficiency, quality, and profitability. It is more than just software; it's a strategic enabler for innovation and competitive advantage in today's fast-paced electronics industry.
Key Features and Benefits of Shared Juicer
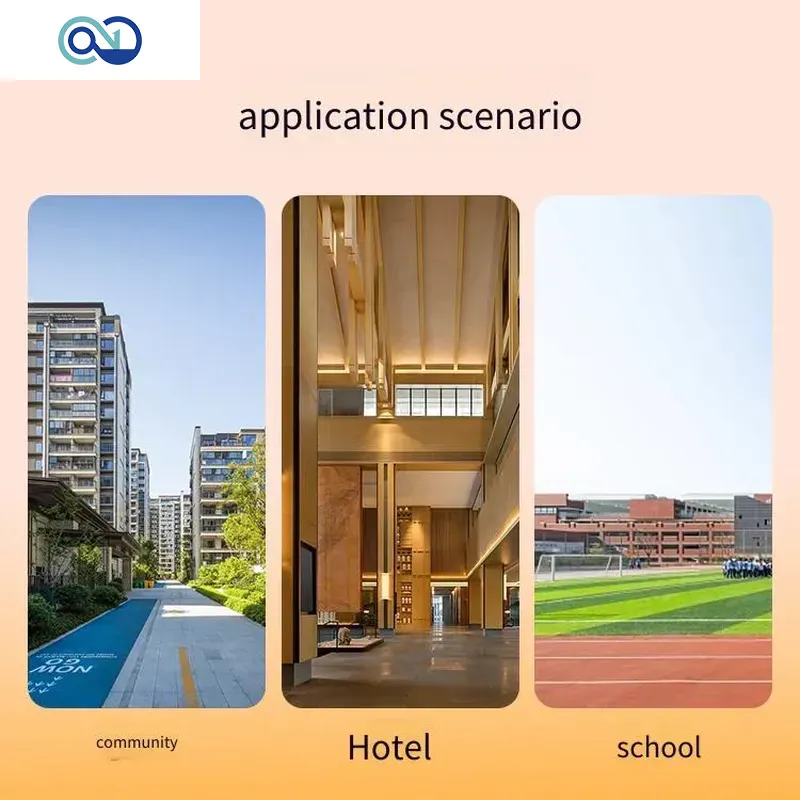
Shared Juicer is engineered to revolutionize PCB design and assembly through its comprehensive suite of features that foster real-time collaboration, ensure centralized data management, automate workflows, and provide in-depth reporting. These capabilities converge to offer significant benefits, including enhanced efficiency, minimized errors, and accelerated market entry for new products. It's not just about streamlining processes; it's about transforming how teams work together to bring innovative ideas to life faster and more reliably.
- Real-time Collaboration
Enables multiple team members to work on the same project simultaneously, regardless of their location. This reduces bottlenecks and ensures everyone is on the same page, leading to faster design cycles and fewer misunderstandings. - Centralized Data Management
Provides a single source of truth for all project-related data, eliminating the confusion and errors that can arise from using multiple, disparate systems. This ensures that everyone is working with the latest information, and that all data is properly backed up and secured. - Automated Workflows
Streamlines repetitive tasks, such as design rule checking and BOM generation, freeing up engineers to focus on more creative and strategic work. This not only increases efficiency but also reduces the risk of human error. - Comprehensive Reporting
Provides detailed insights into project progress, resource utilization, and potential bottlenecks. This enables project managers to make data-driven decisions, optimize workflows, and ensure that projects stay on track. - Increased Efficiency
By streamlining workflows and improving collaboration, Shared Juicer helps teams get more done in less time. This can lead to significant cost savings and a faster time-to-market for new products. - Reduced Errors
Centralized data management and automated workflows help to minimize the risk of human error, which can be costly and time-consuming to correct. This leads to higher quality designs and fewer manufacturing defects. - Faster Time-to-Market
By accelerating the design and assembly process, Shared Juicer helps companies get their products to market faster. This can provide a significant competitive advantage, allowing them to capture market share and generate revenue more quickly.
Shared Juicer in Action: Streamlining the PCB Design Process
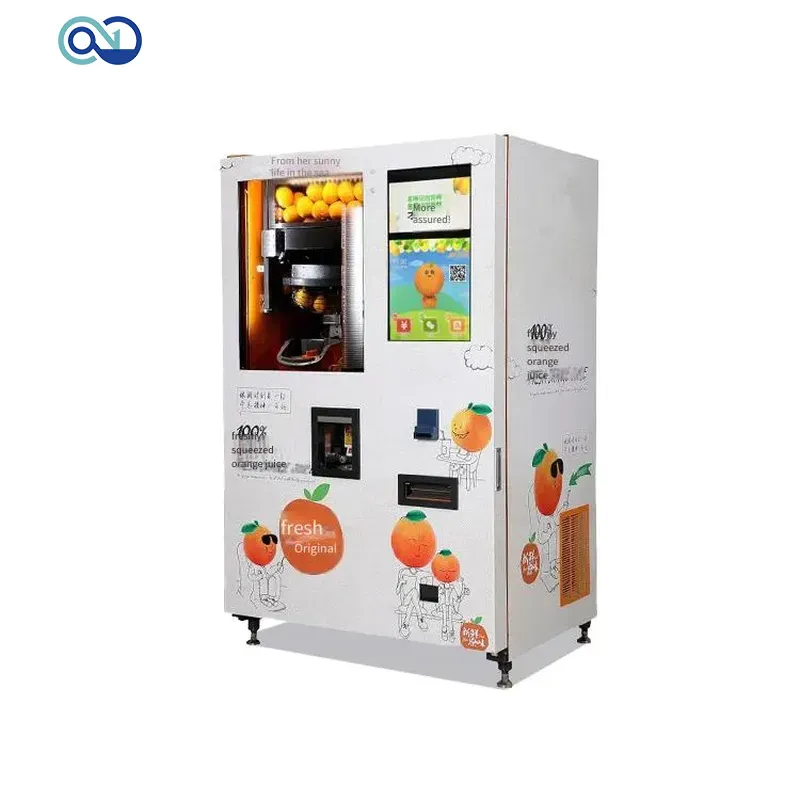
Shared Juicer revolutionizes the PCB design process by providing a seamless, collaborative environment from initial schematic capture to final layout and verification. It eliminates traditional bottlenecks and inefficiencies, resulting in faster design cycles and higher-quality PCBs. By centralizing data, automating workflows, and enabling real-time collaboration, Shared Juicer transforms the way design teams operate.
Consider a scenario where a design team is working on a complex, multi-layer PCB for a high-speed communication device. Traditionally, this would involve multiple iterations, with engineers passing design files back and forth, leading to version control issues and communication breakdowns. With Shared Juicer, however, all team members can access the latest design data in real-time, make simultaneous edits, and track changes effortlessly.
- Schematic Capture:
Designers can collaboratively create and modify schematics, ensuring accuracy and consistency across the design. Real-time feedback and commenting features facilitate immediate clarification and issue resolution. - Layout Design:
PCB layout engineers can work simultaneously on different sections of the board, optimizing component placement and routing while adhering to design rules and constraints. The software's intelligent routing tools and DRC (Design Rule Checking) capabilities ensure signal integrity and manufacturability. - Verification and Simulation:
Shared Juicer integrates with industry-standard simulation tools, allowing designers to verify the performance of their designs and identify potential issues before manufacturing. This reduces the risk of costly errors and rework. - Real-World Examples:
A leading aerospace company used Shared Juicer to design a complex avionics system, reducing the design cycle time by 40% and eliminating costly errors. A medical device manufacturer leveraged Shared Juicer to accelerate the development of a new diagnostic tool, bringing it to market months ahead of schedule. - Centralized Component Library:
Maintain a single source of truth for component data, ensuring consistency and accuracy across all designs. This eliminates the risk of using outdated or incorrect component information, which can lead to functional problems and delays. - Automated Design Reviews:
Automate the design review process with built-in checklists and approval workflows. This ensures that all designs meet the required standards and are thoroughly reviewed before being released for manufacturing.
Optimizing PCB Assembly with Shared Juicer
Shared Juicer revolutionizes PCB assembly by streamlining processes from bill of materials (BOM) management to production execution. It bridges the gap between design and manufacturing, ensuring seamless data flow and real-time collaboration, which significantly reduces errors and accelerates production cycles.
Here's how Shared Juicer optimizes various aspects of PCB assembly:
- BOM Management:
Centralizes and automates BOM creation and management, ensuring accuracy and consistency across all project stakeholders. Real-time updates reflect design changes instantly, minimizing discrepancies and preventing delays during assembly. - Production Planning:
Facilitates efficient production planning by providing a clear overview of project status, resource availability, and potential bottlenecks. This allows for optimized scheduling and resource allocation, maximizing throughput and minimizing downtime. - Execution and Tracking:
Provides real-time tracking of assembly progress, allowing for proactive identification and resolution of issues. Integrated communication tools enable seamless collaboration between design and assembly teams, ensuring smooth execution and timely completion. - Integration with Manufacturing Equipment:
Shared Juicer seamlessly integrates with various manufacturing equipment and automation systems, further streamlining the assembly process. Direct data transfer to pick-and-place machines, AOI systems, and other equipment minimizes manual data entry, reduces errors, and improves overall efficiency.
This integration not only speeds up the assembly process but also enhances the quality and reliability of the final product by minimizing human error and ensuring consistent execution.
Here are some frequently asked questions (FAQs) about optimizing PCB assembly with Shared Juicer:
- How does Shared Juicer handle BOM revisions during the assembly process?
Shared Juicer features robust version control, ensuring that all stakeholders are working with the most up-to-date BOM. Changes are tracked in real-time, and notifications are automatically sent to relevant personnel, minimizing the risk of using outdated information during assembly. - Can Shared Juicer integrate with our existing ERP system for production planning?
Yes, Shared Juicer offers flexible integration options with various ERP systems. This allows for seamless data exchange between design, manufacturing, and business operations, enabling streamlined production planning and resource allocation. - What types of manufacturing equipment does Shared Juicer integrate with?
Shared Juicer is designed to integrate with a wide range of manufacturing equipment, including pick-and-place machines, AOI systems, soldering equipment, and testing equipment. Our team can provide custom integration solutions to meet your specific needs. - How does Shared Juicer improve communication between design and assembly teams?
Shared Juicer provides integrated communication tools, such as real-time chat, video conferencing, and document sharing, enabling seamless collaboration between design and assembly teams. This facilitates quick resolution of issues and prevents misunderstandings that can lead to errors and delays. - Is Shared Juicer suitable for high-volume PCB assembly?
Yes, Shared Juicer is designed to handle high-volume PCB assembly with ease. Its automated workflows, real-time tracking, and integration with manufacturing equipment ensure efficient and reliable production, even at large scales. - Can Shared Juicer help reduce material waste during PCB assembly?
By optimizing BOM management and production planning, Shared Juicer helps to minimize material waste during PCB assembly. Accurate inventory tracking and real-time monitoring of material consumption enable proactive identification and resolution of potential shortages or surpluses, reducing the risk of waste and minimizing costs.
Zero One Solution Limited and Shared Juicer: A Powerful Partnership
Zero One Solution Limited, a leading PCB solution provider specializing in rapid prototyping and one-stop services from PCB design to manufacturing and assembly, has forged a powerful partnership with Shared Juicer to revolutionize its service offerings. By integrating Shared Juicer into its workflow, Zero One Solution Limited is able to provide its clients with faster turnaround times, higher quality PCBs, and reduced costs, solidifying its position as a leader in the PCB assembly solutions industry.
This collaboration allows Zero One Solution Limited to leverage Shared Juicer's robust features to enhance various aspects of its operations. Key benefits include:
- Rapid Prototyping:
Shared Juicer's real-time collaboration and centralized data management capabilities enable faster design iterations and quicker prototyping cycles. This is crucial for clients who need to rapidly test and refine their product designs. - One-Stop PCB Solutions:
By streamlining the entire PCB design and assembly process, Shared Juicer allows Zero One Solution Limited to offer comprehensive, end-to-end solutions to its clients. From initial design to final assembly, clients benefit from a seamless and efficient workflow. - Faster Turnaround Times:
Automated workflows and efficient communication channels within Shared Juicer significantly reduce the time required to complete PCB projects. Clients can expect faster delivery of their prototypes and finished products. - Higher Quality:
Shared Juicer's centralized data management and version control features minimize errors and ensure design integrity. This results in higher quality PCBs that meet the most stringent requirements. - Reduced Costs:
By optimizing resource allocation and minimizing errors, Shared Juicer helps Zero One Solution Limited reduce overall project costs. These savings are passed on to clients, making high-quality PCB solutions more accessible.
The partnership between Zero One Solution Limited and Shared Juicer exemplifies a commitment to innovation and customer satisfaction. By embracing cutting-edge technology, Zero One Solution Limited is able to deliver exceptional value to its clients and maintain its competitive edge in the dynamic PCB market.
Implementation and Integration of Shared Juicer
Implementing and integrating Shared Juicer into your existing PCB design and assembly workflows is a strategic process designed to enhance collaboration and efficiency. This section provides a structured outline of the key steps involved, along with guidance on training, customization, and ongoing support to ensure a seamless transition and optimal utilization of the software's capabilities.
- Assessment and Planning
Begin by evaluating your current PCB design and assembly processes to identify specific pain points and areas for improvement. Define clear objectives for implementing Shared Juicer, such as reducing design cycle time, minimizing errors, or improving team collaboration. Develop a detailed implementation plan with timelines, resource allocation, and key performance indicators (KPIs). - System Requirements and Setup
Ensure that your hardware and software infrastructure meets the system requirements for Shared Juicer. Install the software on designated servers or cloud platforms, following the vendor's installation guide. Configure user accounts, access permissions, and security settings to protect sensitive design data. - Data Migration and Integration
Migrate existing PCB design data, component libraries, and bill of materials (BOMs) into Shared Juicer. Integrate the software with other relevant systems, such as CAD tools, PLM systems, and ERP software, using APIs or connectors. Verify data integrity and consistency during the migration and integration process. - Customization and Configuration
Customize Shared Juicer to align with your specific PCB design and assembly workflows. Configure templates, rules, and automated tasks to streamline repetitive processes. Tailor the user interface, reports, and dashboards to meet the needs of different user groups. - Training and Onboarding
Provide comprehensive training to all users on how to use Shared Juicer effectively. Conduct hands-on workshops, webinars, and one-on-one coaching sessions to ensure that users understand the software's features and functionalities. Create user guides, tutorials, and FAQs to support ongoing learning. - Testing and Validation
Conduct thorough testing of Shared Juicer to ensure that it meets your requirements and performs as expected. Validate the software's functionality, performance, and security. Identify and resolve any issues or bugs before deploying the software to production. - Deployment and Go-Live
Deploy Shared Juicer to production environments, following a phased approach to minimize disruption. Monitor the software's performance and usage after deployment. Provide ongoing support and maintenance to address any issues or user questions. - Ongoing Support and Improvement
Establish a process for providing ongoing support to Shared Juicer users. Collect user feedback and track software usage metrics to identify areas for improvement. Regularly update the software with new features, bug fixes, and security patches. Continuously optimize your PCB design and assembly workflows to maximize the benefits of Shared Juicer.
The Future of PCB Solutions: Shared Juicer and Beyond
The PCB industry is on the cusp of a technological revolution, driven by trends like increased automation, the integration of artificial intelligence (AI), and the shift towards cloud-based collaboration. Shared Juicer is strategically designed to not only adapt to these changes but to spearhead innovation, offering a forward-looking solution for PCB design and assembly.
Here's how Shared Juicer is poised to lead the way:
- Enhanced Automation:
Shared Juicer is built to support increasing levels of automation in PCB design and assembly. By automating repetitive tasks and streamlining workflows, Shared Juicer reduces manual intervention, minimizes errors, and accelerates the overall production cycle. - Artificial Intelligence Integration:
The future of PCB solutions lies in the intelligent application of AI. Shared Juicer is designed to integrate AI-powered features such as intelligent routing, automated component placement, and predictive maintenance, enabling users to optimize designs, improve performance, and reduce downtime. - Cloud-Based Collaboration:
Cloud technology is transforming the way PCB design teams collaborate. Shared Juicer embraces cloud-based collaboration, providing a centralized platform for sharing data, managing projects, and communicating in real-time, regardless of location. - Data-Driven Insights:
Shared Juicer provides comprehensive reporting and analytics capabilities, enabling users to track key performance indicators (KPIs), identify bottlenecks, and make data-driven decisions to improve efficiency and quality. - Seamless Integration:
Shared Juicer is designed to integrate seamlessly with existing PCB design and assembly tools, providing a unified platform for managing the entire PCB lifecycle. This integration eliminates data silos, improves communication, and streamlines workflows. - Scalability and Flexibility:
As PCB designs become more complex and production volumes increase, Shared Juicer offers the scalability and flexibility to adapt to changing needs. Whether you're a small startup or a large enterprise, Shared Juicer can be customized to fit your specific requirements.
In conclusion, Shared Juicer is not just a software solution; it's a strategic investment in the future of PCB design and assembly. By embracing automation, AI, and cloud-based collaboration, Shared Juicer empowers users to stay ahead of the curve and achieve unparalleled levels of efficiency, quality, and innovation.
FAQs About Shared Juicer: Pricing, Licensing, System Requirements, and Support
This section addresses frequently asked questions concerning Shared Juicer, providing clarity on aspects such as pricing models, licensing options, system prerequisites, and available support channels. These FAQs are designed to offer quick and comprehensive answers to common inquiries, ensuring users have the necessary information to make informed decisions and effectively utilize Shared Juicer.
- What are the pricing options for Shared Juicer?
Shared Juicer offers flexible pricing plans tailored to meet various needs, including subscription-based models (monthly/annual) and enterprise licenses. Contact our sales team for detailed pricing information and custom solutions. - What types of licenses are available for Shared Juicer?
We offer individual, team, and enterprise licenses. The appropriate license type depends on the number of users and the intended scope of usage. Individual licenses are suitable for single users, while team and enterprise licenses are designed for collaborative environments with multiple users and advanced features. - What are the system requirements for running Shared Juicer?
Shared Juicer is compatible with Windows and macOS operating systems. Specific system requirements include a minimum of 8GB RAM, a multi-core processor, and a dedicated graphics card. Detailed specifications can be found on our website's download page to ensure optimal performance. - What kind of support options do you offer for Shared Juicer?
We provide comprehensive support options, including online documentation, video tutorials, a knowledge base, and direct support via email and phone. Premium support packages are also available for enterprise clients, offering prioritized assistance and dedicated account management. - Can Shared Juicer integrate with other PCB design software?
Yes, Shared Juicer is designed to integrate seamlessly with popular PCB design software such as Altium Designer, Eagle, and KiCad. We offer APIs and plugins to facilitate smooth data exchange and interoperability, streamlining your existing workflows. - How secure is my data when using Shared Juicer?
Data security is a top priority. Shared Juicer employs advanced encryption protocols to protect your sensitive data both in transit and at rest. We adhere to industry best practices and regularly undergo security audits to ensure the highest level of protection. - Is training available for Shared Juicer?
Yes, we offer comprehensive training programs for individuals and teams. Training options include online courses, webinars, and on-site workshops. Our training materials cover all aspects of Shared Juicer, from basic usage to advanced features, ensuring users can maximize the software's potential.
Shared Juicer represents a paradigm shift in PCB design and assembly, offering a collaborative and efficient solution for today's demanding electronics industry. By streamlining workflows, reducing errors, and accelerating time-to-market, Shared Juicer empowers companies to innovate faster and stay ahead of the competition. As Zero One Solution Limited continues to leverage Shared Juicer to provide cutting-edge PCB solutions, we invite you to explore the possibilities and transform your own PCB processes. Contact us today to learn more and schedule a demo!
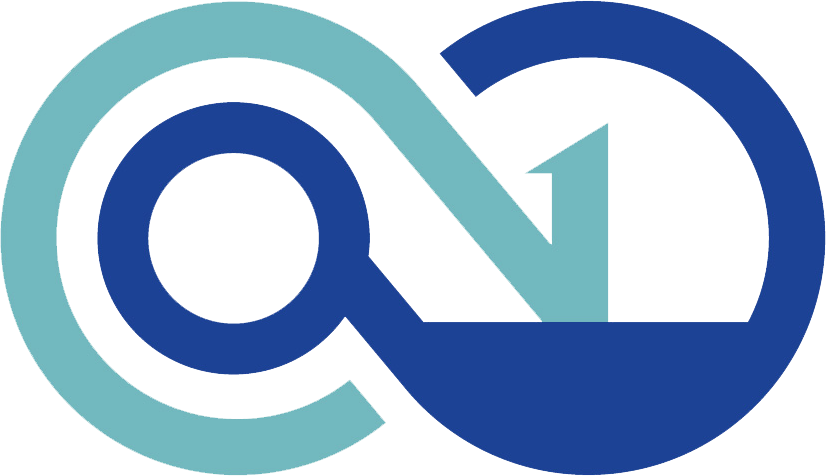