Shared Portable Infusion Pump Solution
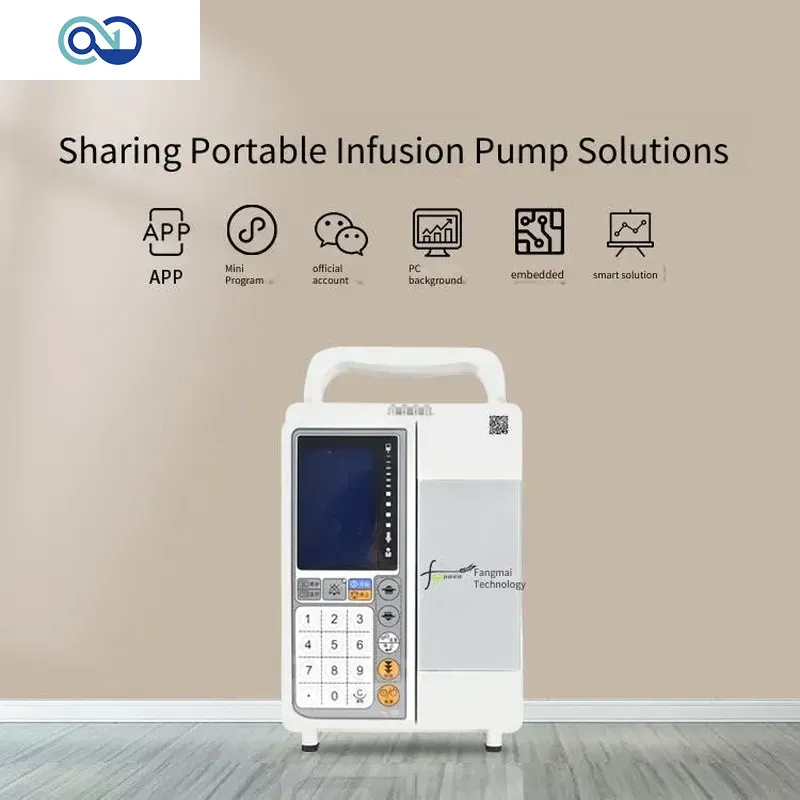
In the fast-evolving landscape of healthcare technology, the demand for innovative, reliable, and portable medical devices is paramount. Among these, shared portable infusion pumps stand out as critical tools for patient care, offering flexibility and precision in medication delivery. However, the complexity of these devices necessitates a robust and dependable electronic backbone. At Zero One Solution Limited, with our deep roots in Silicon Valley's innovation culture and over a decade of experience in rapid-response R&D prototype manufacturing, we understand the intricate challenges and opportunities in this sector. This article delves into how our specialized PCB solutions are revolutionizing the design, development, and deployment of shared portable infusion pumps, paving the way for enhanced patient outcomes and streamlined healthcare operations. How can advanced PCB manufacturing truly make a difference in such life-critical applications?
The Evolution of Portable Infusion Pumps: A Technological Imperative
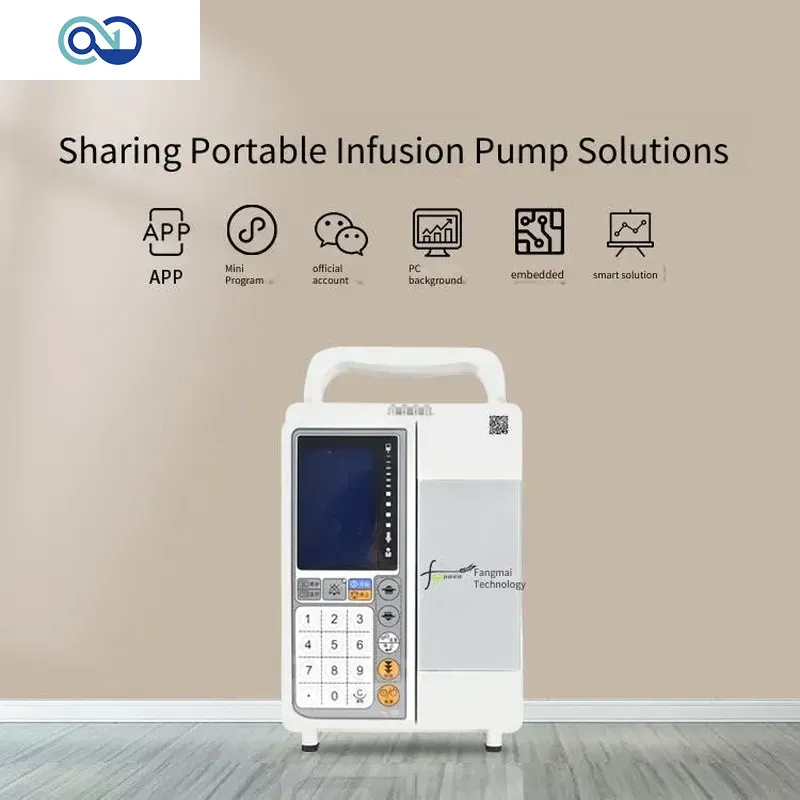
The rising demand for portable infusion pumps signifies a major shift in healthcare, prioritizing patient mobility, comfort, and efficient drug delivery. This evolution is propelled by technological advancements and the increasing need for shared models within modern healthcare systems. These pumps empower patients to maintain their daily routines while receiving necessary treatments, offering a significant improvement in their quality of life. The shift towards shared models further addresses the economic and logistical challenges faced by healthcare providers, optimizing resource utilization and reducing costs.
The evolution of portable infusion pumps can be attributed to several key factors:
- Enhanced Patient Mobility:
Traditional infusion methods often require patients to remain stationary, typically within a hospital setting. Portable pumps liberate patients, allowing them to move freely and continue many of their normal activities. - Improved Comfort and Quality of Life:
Smaller, lighter, and more user-friendly designs contribute to increased patient comfort. This leads to better treatment adherence and a higher overall quality of life. - Technological Advancements:
Miniaturization of components, improved battery technology, and sophisticated microelectronics have enabled the development of highly reliable and accurate portable pumps. - Growing Geriatric Population:
With an aging global population, the need for home healthcare solutions, including portable infusion, is steadily increasing. - Cost-Effectiveness:
Shared portable infusion pump programs can significantly reduce healthcare costs by optimizing resource utilization and minimizing hospital readmissions. - Need for Efficient Drug Delivery:
Portable infusion pumps allow for precise and controlled drug delivery, ensuring optimal therapeutic outcomes.
Shared models of portable infusion pumps are becoming increasingly important due to:
- Resource Optimization:
Sharing pumps across multiple patients reduces the total number of devices needed, optimizing resource allocation within healthcare facilities. - Cost Reduction:
The initial investment and maintenance costs are spread across a larger user base, making advanced infusion technology more accessible. - Improved Hygiene and Safety:
Modern shared pump designs incorporate features that facilitate thorough cleaning and sterilization, minimizing the risk of cross-contamination. - Enhanced Tracking and Management:
Connectivity features enable centralized monitoring and management of shared pump fleets, improving efficiency and patient safety.
Challenges in Designing Robust Portable Infusion Pump PCBs
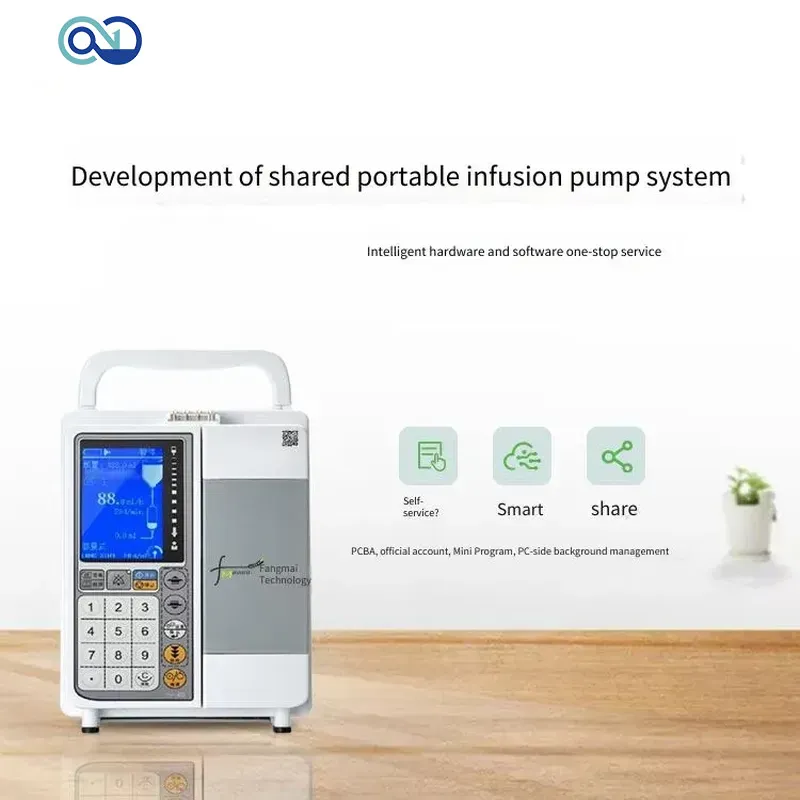
Designing Printed Circuit Boards (PCBs) for portable infusion pumps presents a unique set of engineering challenges, especially when these devices are intended for shared use. These challenges span miniaturization, power efficiency, electromagnetic compatibility (EMC), stringent reliability, and the complexities introduced by shared device environments. Overcoming these hurdles is crucial to ensure the safety, accuracy, and longevity of the infusion pumps.
- Miniaturization Challenges
Portable infusion pumps require compact PCBs to fit within small device housings. This necessitates high-density interconnect (HDI) designs, fine-pitch components, and creative layout strategies to maximize functionality within limited space. Effective thermal management in a small form factor is also critical to prevent overheating and ensure reliable operation. - Power Efficiency Demands
Battery life is paramount for portable devices. PCB design must minimize power consumption through efficient component selection, optimized power distribution networks (PDNs), and low-power routing techniques. Attention to detail in reducing parasitic capacitance and inductance is essential for maximizing energy efficiency. - Electromagnetic Compatibility (EMC) Concerns
Medical devices must operate reliably in the presence of electromagnetic interference (EMI). PCB designers must implement robust EMC mitigation strategies, including shielding, grounding, filtering, and careful signal routing, to prevent interference with other medical equipment and ensure accurate drug delivery. - Stringent Reliability Requirements
PCBs for medical devices must meet the highest reliability standards to guarantee patient safety. This requires rigorous component selection, robust manufacturing processes, and comprehensive testing to ensure long-term performance and prevent failures. Traceability and documentation are also crucial for regulatory compliance. - Shared Device Environment Complexities
Shared portable infusion pumps face additional challenges related to hygiene, durability, and security. PCB designs must withstand frequent cleaning and disinfection, resist physical damage from handling, and incorporate security features to prevent unauthorized access or tampering. The selection of materials resistant to harsh chemicals is also important. - Signal Integrity Considerations
Maintaining signal integrity is crucial for accurate data transmission and control within the infusion pump. PCB designers must carefully manage impedance, minimize signal reflections, and control crosstalk to ensure reliable communication between components. Simulation and testing are often used to validate signal integrity performance. - Component Selection and Obsolescence
Choosing the right components is vital for performance and longevity. Designers must consider factors such as accuracy, stability, and availability when selecting components. Managing component obsolescence is also important to ensure long-term product support and avoid costly redesigns.
Zero One Solution Limited's Expertise in Medical Device PCB Solutions
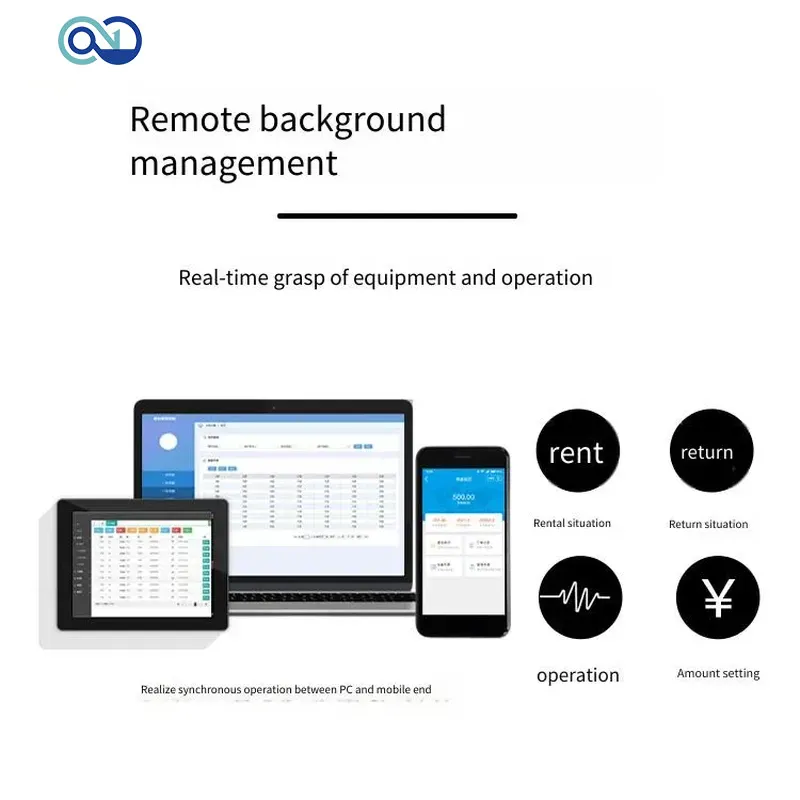
Zero One Solution Limited stands at the forefront of providing specialized PCB solutions for the medical device industry, particularly in the rapidly evolving sector of shared portable infusion pumps. With extensive experience and a proven track record, we offer a comprehensive suite of services encompassing PCB design, rapid prototyping, manufacturing, and assembly. Our commitment is to accelerate your product development cycle, ensuring innovative medical solutions reach the market faster and more efficiently.
- What specific PCB design expertise does Zero One Solution Limited offer for medical devices?
We specialize in high-density interconnect (HDI) PCBs, advanced material selection, power management circuits, and secure data transmission protocols, all crucial for shared portable infusion pumps. Our designs prioritize miniaturization, power efficiency, and electromagnetic compatibility (EMC) to meet the stringent requirements of medical devices. - How does Zero One Solution Limited's rapid prototyping service benefit medical device companies?
Our rapid prototyping capabilities significantly reduce development cycles, allowing for quicker iteration and testing of designs. This accelerated process helps medical device companies bring innovative solutions to market faster, gaining a competitive edge. - What manufacturing and assembly services does Zero One Solution Limited provide?
We offer a complete one-stop service from concept to assembly, ensuring seamless integration of PCB design, manufacturing, and assembly processes. Our state-of-the-art facilities and expertise in medical device manufacturing guarantee high-quality and reliable products. - How does Zero One Solution Limited ensure compliance with medical device regulations?
We adhere to stringent regulatory standards, including ISO 13485 and FDA guidelines, ensuring that our medical device PCBs meet all necessary compliance requirements. Our rigorous quality control processes guarantee the reliability and safety of our products. - Can Zero One Solution Limited handle the complexities of shared device environments for portable infusion pumps?
Yes, we have extensive experience in designing PCBs for shared device environments. We understand the unique challenges associated with these applications and tailor our solutions to meet the specific requirements of shared portable infusion pumps, ensuring robust performance and security. - What is Zero One Solution Limited's approach to Design for Manufacturability (DFM) and Design for Assembly (DFA)?
We prioritize DFM and DFA to ensure efficient and cost-effective production. Our design engineers work closely with manufacturing teams to optimize designs for manufacturability and assembly, reducing production costs and improving overall product quality. - How does Zero One Solution Limited stay updated with the latest trends in portable infusion technology?
We continuously monitor emerging trends in portable infusion technology, such as IoT integration and AI-driven dosage, to ensure our PCB solutions are at the forefront of innovation. Our ongoing research and development efforts allow us to provide cutting-edge solutions for the next generation of medical devices.
Key PCB Design Considerations for Shared Portable Infusion Pumps
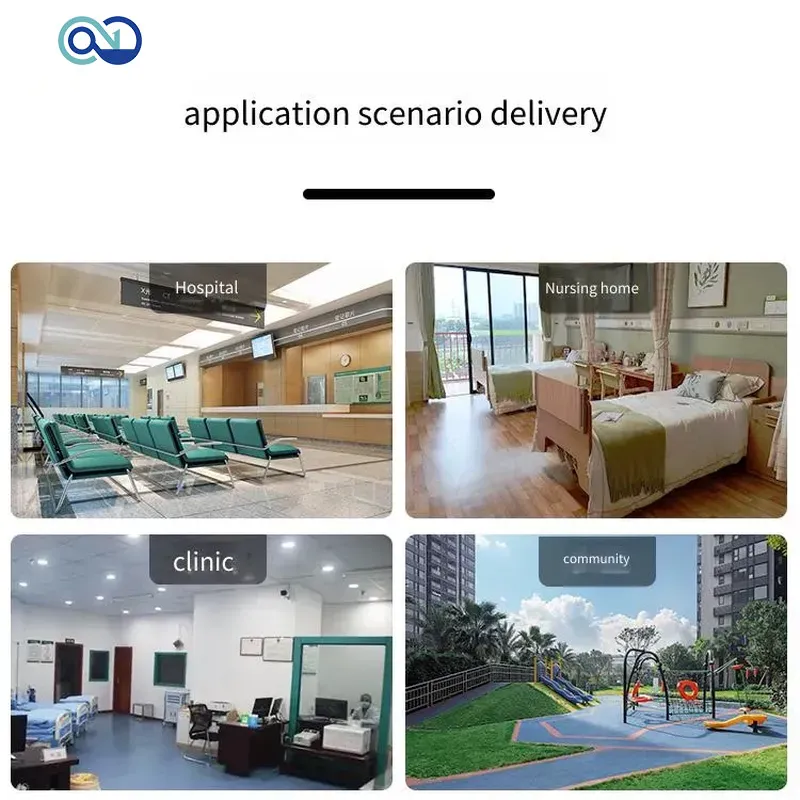
Designing Printed Circuit Boards (PCBs) for shared portable infusion pumps demands meticulous attention to detail, ensuring functionality, safety, and reliability. These devices operate in critical healthcare settings, often under demanding conditions, making robust PCB design paramount. Key considerations include high-density interconnect (HDI) technology for miniaturization, careful material selection for biocompatibility and durability, efficient power management to extend battery life, and secure data transmission protocols to safeguard patient information. Addressing these elements comprehensively is crucial for the successful deployment of shared portable infusion pumps.
Here's a breakdown of the critical PCB design considerations:
- High-Density Interconnect (HDI) PCBs
HDI PCBs are essential for miniaturizing infusion pumps while maintaining high performance. They allow for more components in a smaller area, utilizing microvias, blind vias, and buried vias to increase routing density. This is crucial for portable devices where space is a premium. - Advanced Material Selection
The choice of PCB materials significantly impacts the pump's performance and reliability. Materials must be biocompatible, capable of withstanding sterilization processes, and offer excellent thermal and electrical properties. Considerations include Rogers, FR-4, and polyimide, each offering a unique balance of characteristics. - Robust Power Management Circuits
Efficient power management is vital for extending the battery life of portable infusion pumps. The PCB design must incorporate low-power components, efficient DC-DC converters, and sophisticated power distribution networks to minimize energy consumption and heat generation. This ensures prolonged operation and reduces the frequency of battery changes. - Secure Data Transmission Protocols
Modern infusion pumps often incorporate wireless connectivity for remote monitoring and data logging. The PCB design must support secure data transmission protocols, such as AES encryption and secure boot mechanisms, to protect sensitive patient information from unauthorized access and cyber threats. This is crucial for maintaining patient privacy and data integrity. - Electromagnetic Compatibility (EMC)
Medical devices must comply with stringent EMC standards to prevent interference with other equipment and ensure reliable operation. PCB design techniques such as grounding, shielding, and filtering are crucial for minimizing electromagnetic emissions and susceptibility. Careful component placement and signal routing are also essential for achieving EMC compliance. - Design for Manufacturability (DFM)
DFM is a critical consideration to ensure the PCB can be manufactured efficiently and cost-effectively. This includes optimizing component placement, trace routing, and via placement to minimize manufacturing defects and improve yield. Early DFM analysis can identify potential issues and prevent costly rework. - Testing and Validation
Rigorous testing and validation are essential to ensure the PCB meets all performance and safety requirements. This includes functional testing, environmental testing (temperature, humidity, vibration), and EMC testing. Comprehensive testing helps identify and address potential issues before the device is deployed in the field.
Accelerating Innovation with Rapid Prototyping and DFM
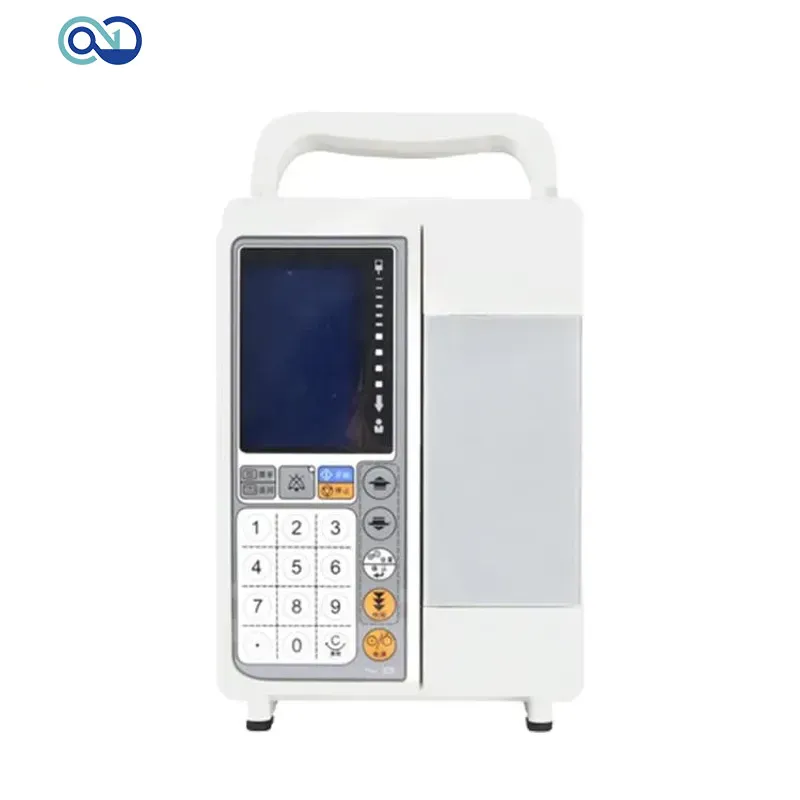
Zero One Solution Limited's rapid prototyping services are instrumental in accelerating the development of shared portable infusion pumps, significantly reducing the time from concept to deployment. By integrating Design for Manufacturability (DFM) and Design for Assembly (DFA) principles, we ensure that designs are not only innovative but also optimized for efficient, cost-effective mass production, addressing a critical need in the fast-paced medical device industry.
Here’s a breakdown of how rapid prototyping and DFM/DFA contribute to faster innovation:
- Reduced Development Cycles
Rapid prototyping allows for quick iterations and testing of design changes, compressing the overall development timeline. This is crucial for shared portable infusion pumps, where timely updates and improvements can directly impact patient care. - Early Issue Detection
DFM analysis identifies potential manufacturing bottlenecks and inefficiencies early in the design phase. Addressing these issues upfront prevents costly redesigns and delays later in the production process. - Optimized Assembly Processes
DFA focuses on simplifying the assembly process, reducing the number of parts, and improving ease of handling. This leads to faster assembly times, lower labor costs, and increased production throughput. - Cost-Effective Production
By optimizing designs for manufacturability and assembly, companies can significantly reduce production costs. This is particularly important for shared medical devices, where affordability can improve accessibility. - Improved Product Quality
DFM and DFA contribute to higher product quality by ensuring that designs are robust, reliable, and easily manufactured. This reduces the risk of defects and improves the overall performance of the shared portable infusion pumps.
The table below compares traditional development approaches with those enhanced by rapid prototyping and DFM/DFA:
Feature | Traditional Development | Rapid Prototyping & DFM/DFA |
---|---|---|
Development Cycle Time | Longer, due to multiple iterations and redesigns | Significantly shorter, with faster feedback loops |
Issue Detection | Late detection, leading to costly fixes | Early detection, minimizing redesign costs |
Production Costs | Higher, due to inefficiencies and rework | Lower, through optimized designs and assembly |
Product Quality | Potentially lower, due to manufacturing challenges | Higher, ensuring robust and reliable designs |
Ensuring Compliance and Quality in Medical PCB Manufacturing
In medical PCB manufacturing, regulatory compliance and stringent quality control are not merely procedural; they are paramount for patient safety and device reliability, especially for shared portable infusion pumps. Adherence to standards like ISO 13485 and FDA regulations is critical. Zero One Solution Limited prioritizes these aspects, ensuring every PCB meets the highest industry benchmarks.
- What are the key regulatory standards for medical device PCBs?
Key standards include ISO 13485 for quality management systems, FDA 21 CFR Part 820 for quality system regulation, and IEC 60601 series for electrical safety. Compliance ensures the PCB manufacturing process meets rigorous quality and safety requirements. - How does Zero One Solution Limited ensure PCB quality?
Zero One Solution Limited employs a multi-faceted approach, including rigorous material inspection, automated optical inspection (AOI), in-circuit testing (ICT), and functional testing. These measures guarantee that each PCB performs reliably and meets specified performance criteria. - What is ISO 13485, and why is it important for medical PCBs?
ISO 13485 is an internationally recognized standard that specifies requirements for a quality management system specific to the medical device industry. It's crucial because it demonstrates a manufacturer's ability to consistently meet customer and regulatory requirements applicable to medical devices and related services. - How does FDA compliance impact medical PCB manufacturing?
FDA compliance mandates adherence to strict guidelines for design, manufacturing, testing, and documentation. It ensures traceability and accountability throughout the PCB lifecycle, minimizing risks associated with device malfunction or failure. - What documentation is required for medical PCB manufacturing to ensure compliance?
Comprehensive documentation is essential, including design specifications, material certifications, manufacturing process records, inspection reports, and test results. This documentation provides evidence of compliance with regulatory requirements and facilitates audits. - How does Zero One Solution Limited handle material traceability for medical PCBs?
Zero One Solution Limited maintains strict material traceability through a robust tracking system. Each component and material used in PCB manufacturing is tracked from its origin to the finished product, ensuring accountability and facilitating swift identification of potential issues. - What testing procedures are used to validate the reliability of medical PCBs?
Reliability testing encompasses a range of procedures, including thermal cycling, vibration testing, and humidity testing. These tests simulate real-world operating conditions, identifying potential failure points and ensuring the PCB can withstand harsh environments.
The Future of Shared Portable Infusion Pumps and Zero One Solution Limited's Role
The future of shared portable infusion pumps is being shaped by advancements in IoT integration, AI-driven dosage precision, and enhanced connectivity, promising to revolutionize patient care and device management. Zero One Solution Limited is committed to pioneering these advancements, driving the next generation of medical devices through innovative PCB solutions and comprehensive support.
Here's a look at some emerging trends and how Zero One Solution Limited is contributing:
- IoT Integration for Remote Monitoring
Integrating IoT technology into shared portable infusion pumps allows for real-time remote monitoring of device performance, patient compliance, and drug delivery accuracy. This enables healthcare providers to proactively manage patient care, adjust dosages as needed, and ensure optimal treatment outcomes. Zero One Solution Limited is developing PCB solutions that support seamless IoT connectivity, robust data transmission, and secure communication protocols. - AI-Driven Dosage Optimization
Artificial intelligence (AI) algorithms are being used to personalize drug dosages based on individual patient needs, physiological parameters, and treatment responses. AI-driven dosage optimization can improve therapeutic efficacy, reduce adverse effects, and enhance patient safety. Zero One Solution Limited is designing PCBs with the processing power and memory capacity required to support complex AI algorithms and real-time data analysis. - Enhanced Connectivity for Data Sharing
Enhanced connectivity options, such as Bluetooth, Wi-Fi, and cellular, enable seamless data sharing between shared portable infusion pumps, electronic health records (EHRs), and other medical devices. This facilitates improved communication, collaboration, and coordination among healthcare providers, leading to better patient care. Zero One Solution Limited is developing PCB solutions that support a variety of connectivity protocols, ensuring interoperability and data security. - Miniaturization and Portability
The trend towards smaller, more portable infusion pumps continues to drive innovation in PCB design. High-density interconnect (HDI) PCBs allow for increased component density and reduced device size, making shared portable infusion pumps more convenient and user-friendly. Zero One Solution Limited specializes in HDI PCB manufacturing, providing miniaturized solutions without compromising performance or reliability. - Advanced Power Management
Efficient power management is crucial for extending the battery life of shared portable infusion pumps and ensuring uninterrupted drug delivery. Advanced power management circuits and low-power components minimize energy consumption and maximize device uptime. Zero One Solution Limited offers PCB solutions with optimized power distribution networks and energy-efficient designs. - Improved Security Features
As shared portable infusion pumps become more connected, security features are becoming increasingly important to protect patient data and prevent unauthorized access. Robust encryption, authentication, and access control mechanisms are essential for ensuring the confidentiality, integrity, and availability of sensitive information. Zero One Solution Limited is committed to designing PCBs with advanced security features to safeguard patient data and maintain regulatory compliance.
Zero One Solution Limited is dedicated to pushing the boundaries of what's possible in shared portable infusion pump technology, collaborating closely with medical device manufacturers to create innovative solutions that improve patient outcomes and enhance the quality of healthcare. Our expertise in PCB design, rapid prototyping, and manufacturing makes us a valuable partner in bringing the next generation of these vital medical devices to market.
In conclusion, Zero One Solution Limited is not just a PCB solution provider; we are a strategic partner in advancing medical technology. Our comprehensive expertise in PCB design, rapid prototyping, and manufacturing ensures that shared portable infusion pump solutions are not only innovative but also reliable, efficient, and compliant with the highest industry standards. By choosing Zero One Solution Limited, you are leveraging over a decade of Silicon Valley-inspired engineering excellence, a global supply chain network, and an unwavering commitment to quality. Elevate your medical device development and bring life-changing solutions to market faster. Contact us today to explore how our tailored PCB solutions can power your next-generation portable infusion pump project and contribute to a healthier future.
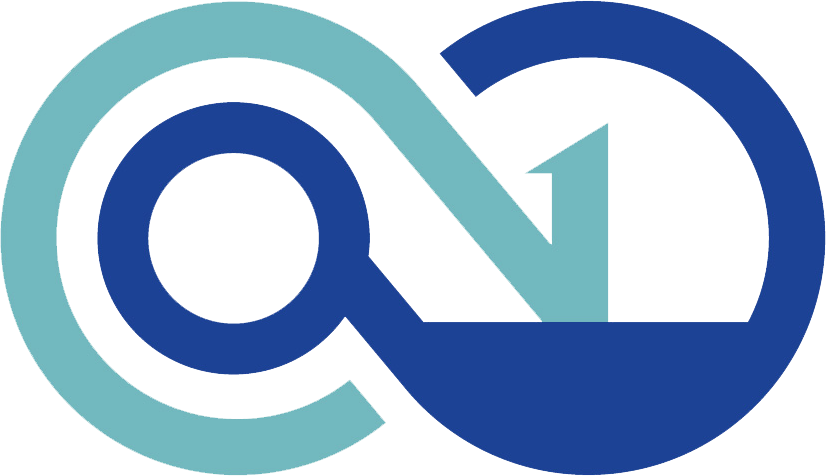