Shared Refueling Machine Solution

In today's fast-paced electronics manufacturing landscape, efficiency and cost-effectiveness are paramount. Just as a vehicle needs a quick and reliable refueling stop to continue its journey, modern PCB assembly lines demand seamless material replenishment to maintain peak performance. Zero One Solution Limited, a leader in rapid prototyping and one-stop PCB services, introduces its groundbreaking Shared Refueling Machine Solution. This innovative approach addresses critical bottlenecks in traditional manufacturing, promising to redefine operational fluidity and significantly enhance productivity.
The Evolution of PCB Assembly: Addressing Modern Challenges

Modern PCB assembly lines face increasing demands for efficiency and cost-effectiveness. Traditional material handling methods struggle to keep pace with high-volume, high-mix production, leading to inefficiencies and rising operational costs. The need for innovative solutions to streamline material replenishment and reduce downtime is more critical than ever.
The PCB assembly landscape is rapidly evolving, driven by factors such as increasing product complexity, shorter product lifecycles, and the growing demand for customized solutions. This evolution places significant strain on traditional assembly processes, particularly in the area of material handling. Here's a breakdown of the key challenges:
- Rising Operational Costs
Traditional material handling relies heavily on manual labor for tasks such as kitting, loading feeders, and transporting materials. These manual processes are not only labor-intensive but also prone to errors, leading to increased material waste and rework, which ultimately drive up operational costs. - Inefficiencies in Material Handling
Traditional material handling systems often involve decentralized storage locations and manual transportation of materials between these locations and the assembly line. This can result in significant delays and downtime, as operators spend valuable time searching for and retrieving materials. The lack of real-time inventory visibility further exacerbates these inefficiencies. - Limitations of Traditional Setups
Dedicated material replenishment setups for each production line or machine can be costly and inflexible. They require significant capital investment in equipment and infrastructure and may not be easily adaptable to changing production needs or new product introductions. This lack of scalability can hinder growth and innovation. - High-Mix Production Challenges
Modern PCB assembly often involves high-mix production, where a wide variety of different products are manufactured on the same line. This requires frequent changeovers and material replenishments, which can be time-consuming and error-prone with traditional material handling methods. The complexity of managing a diverse range of materials and components further adds to the challenge.
To overcome these challenges, innovative solutions are needed that can automate material handling, improve inventory visibility, and optimize material flow. The Shared Refueling Machine Solution represents a paradigm shift in PCB assembly, offering a centralized, intelligent material replenishment system that can address the limitations of traditional approaches and unlock significant improvements in efficiency, cost, and flexibility.
Introducing the Shared Refueling Machine Solution: A Paradigm Shift

The Shared Refueling Machine Solution represents a significant leap forward in PCB assembly, shifting from traditional, machine-centric material replenishment to a centralized and intelligent system. This innovative approach reimagines how components are managed and supplied, offering a more efficient and streamlined alternative to conventional methods.
At its core, the Shared Refueling Machine Solution operates as a centralized hub for material replenishment. Unlike dedicated setups where each machine has its own supply system, this solution serves multiple production lines or machines concurrently. This shared architecture allows for optimized resource allocation, reduced redundancy, and enhanced control over material flow throughout the assembly process.
Imagine a scenario where several SMT lines are running simultaneously, each requiring a steady stream of components. Instead of individual operators manually replenishing each machine, the Shared Refueling Machine Solution acts as a central warehouse, automatically delivering the right materials to the right machines at the right time. This is achieved through a combination of advanced technologies, including AI-powered predictive replenishment, automated material delivery systems, and real-time inventory tracking.
The 'paradigm shift' lies in its ability to break free from the limitations of isolated machine setups. By centralizing material management, the Shared Refueling Machine Solution unlocks new levels of efficiency, flexibility, and cost-effectiveness, paving the way for a more agile and responsive PCB assembly process.
Key Features and Technological Innovations
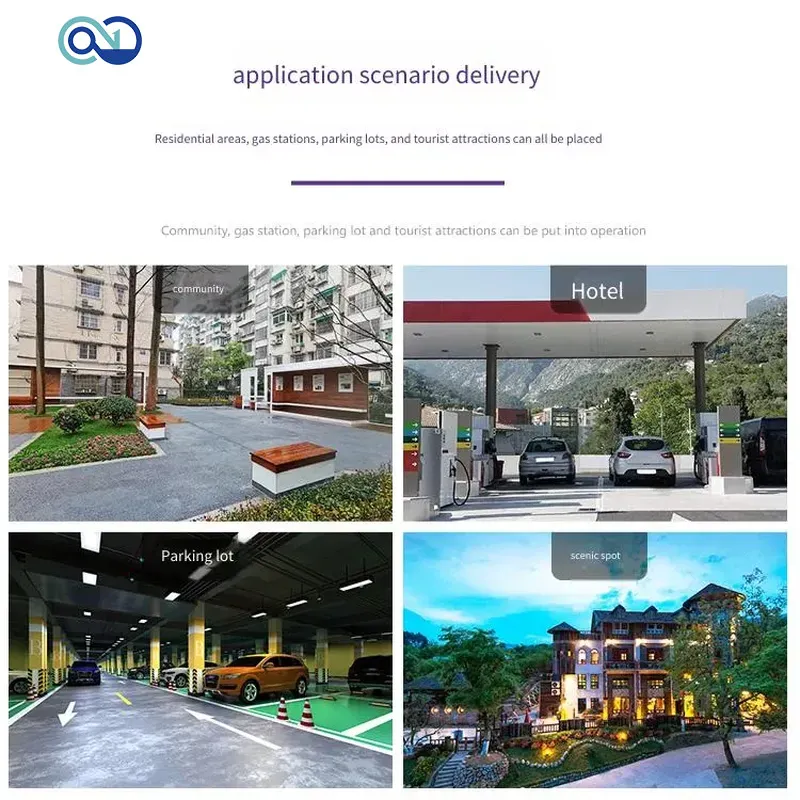
The Shared Refueling Machine Solution distinguishes itself through a suite of advanced features and technological innovations designed to optimize PCB assembly processes. This solution goes beyond simple material replenishment, offering a comprehensive system that leverages AI, automation, and real-time data to ensure seamless and efficient operations.
- AI-Driven Predictive Replenishment
The system utilizes artificial intelligence algorithms to analyze material consumption patterns and predict future needs. This proactive approach ensures that materials are replenished automatically before shortages occur, minimizing downtime and maximizing production throughput. By learning from historical data and adapting to real-time changes, the AI continuously refines its predictions, improving accuracy and efficiency over time. - Automated Material Delivery
Robotic systems or automated guided vehicles (AGVs) are employed to deliver materials directly to the point of use. This eliminates the need for manual material handling, reducing labor costs and the risk of human error. The automated delivery system is designed to navigate the production floor efficiently, ensuring that materials are delivered quickly and reliably. - Real-Time Inventory Tracking
The solution provides real-time visibility into inventory levels across all production lines. Sensors and tracking devices monitor material usage, providing accurate data on stock levels, consumption rates, and potential shortages. This information is accessible through a centralized dashboard, enabling managers to make informed decisions and optimize inventory management strategies. This also aids in minimizing waste by preventing overstocking and material expiration. - Seamless Integration with Existing MES/ERP Systems
The Shared Refueling Machine Solution is designed for seamless integration with existing Manufacturing Execution Systems (MES) and Enterprise Resource Planning (ERP) systems. This integration allows for the exchange of data between the refueling system and other enterprise systems, providing a holistic view of the production process. This ensures data consistency, reduces the need for manual data entry, and enables better coordination across different departments. - Centralized Control and Monitoring
A centralized control system allows for monitoring and management of the entire refueling process from a single location. This provides operators with a comprehensive view of material levels, delivery schedules, and system performance. The centralized system also enables remote diagnostics and troubleshooting, minimizing downtime and maximizing system uptime.
Optimizing Operational Efficiency and Throughput
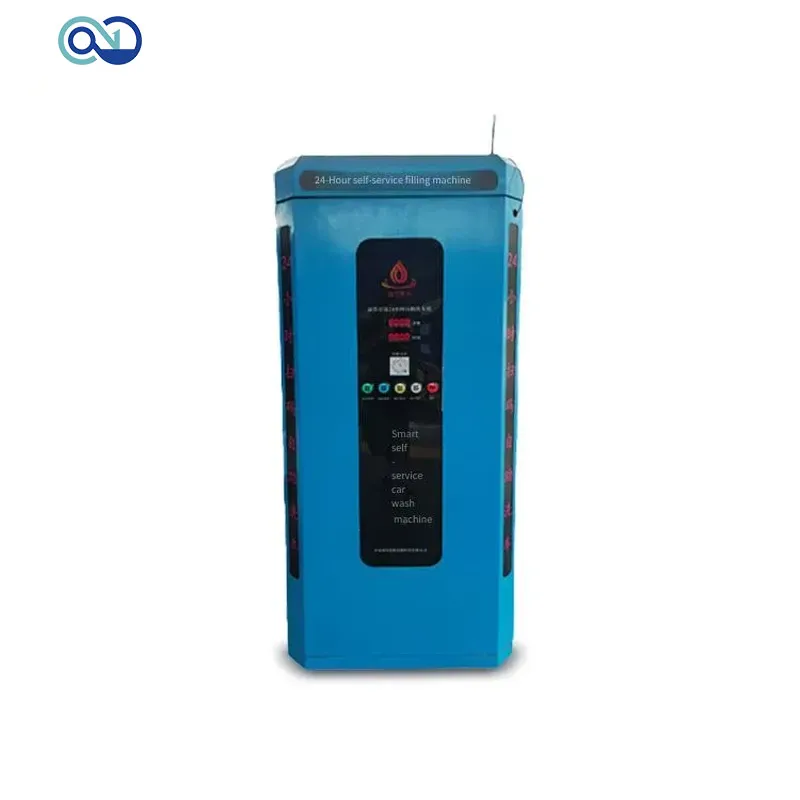
The Shared Refueling Machine Solution is engineered to significantly enhance operational efficiency and throughput in PCB assembly lines. By minimizing downtime, reducing manual intervention, and ensuring a consistent material flow, this system directly addresses key bottlenecks that traditionally impede production. The result is a streamlined process that not only accelerates production cycles but also improves Overall Equipment Effectiveness (OEE).
Here's how the Shared Refueling Machine Solution optimizes operational efficiency and throughput:
- Reduced Downtime
The system's proactive replenishment strategy ensures that materials are always available when needed. AI-driven predictive replenishment anticipates material needs, eliminating stockouts and the associated downtime for manual restocking. - Minimized Manual Intervention
Automated material delivery reduces the need for manual handling of components. This not only frees up human resources for more critical tasks but also minimizes the risk of errors and material damage associated with manual handling. - Continuous Material Flow
By maintaining a constant supply of materials to multiple production lines or machines simultaneously, the Shared Refueling Machine Solution ensures a continuous material flow. This is crucial for maintaining consistent production speeds and avoiding disruptions. - Improved OEE
The combined effect of reduced downtime, minimized manual intervention, and continuous material flow directly contributes to improved OEE. OEE is a key metric for measuring manufacturing productivity, and improvements in this area translate directly to increased profitability. - Enhanced Traceability
Real-time inventory tracking provides complete visibility into material usage and availability. This allows for better planning and forecasting, further optimizing material flow and reducing waste.
The following table illustrates the potential impact of the Shared Refueling Machine Solution on throughput and OEE:
Metric | Traditional Method | Shared Refueling Machine Solution | Improvement |
---|---|---|---|
Throughput (Units/Hour) | 100 | 120 | 20% |
OEE | 70% | 85% | 15% |
Downtime | 15% | 5% | 66.7% |
These figures demonstrate the significant potential for improvement in operational efficiency and throughput through the adoption of a Shared Refueling Machine Solution. The actual results may vary depending on the specific production environment and the extent of implementation.
Significant Cost Reduction Opportunities
The Shared Refueling Machine Solution offers a compelling pathway to significant cost reductions in PCB assembly operations. By centralizing material replenishment and automating key processes, this system directly tackles several major cost drivers, delivering substantial savings compared to traditional, machine-by-machine refueling approaches. These savings stem from lower labor expenses, optimized inventory management, reduced material waste, and minimized capital expenditure.
- Reduced Labor Expenses
The Shared Refueling Machine Solution reduces the need for manual intervention in material handling. By automating the replenishment process, fewer operators are needed to manage and transport materials, leading to direct labor cost savings. This allows skilled personnel to focus on higher-value tasks such as process optimization and quality control. - Optimized Inventory Management
The solution's real-time inventory tracking capabilities provide a clear view of material levels across the production floor. This enables proactive inventory management, minimizing the risk of stockouts and reducing the need for safety stock. Optimized inventory levels translate directly into lower holding costs and reduced working capital requirements. - Reduced Material Waste
The AI-driven predictive replenishment feature ensures that materials are delivered to the production line just in time, minimizing the risk of material expiration or damage due to prolonged storage. This leads to a significant reduction in material waste, particularly for components with limited shelf lives or specific storage requirements. - Minimized Capital Expenditure
Unlike traditional setups where each machine requires its own dedicated refueling system, the Shared Refueling Machine Solution serves multiple production lines or machines simultaneously. This centralized approach reduces the overall capital expenditure required for material handling equipment, resulting in a lower total cost of ownership. - Lower Machine Downtime Costs
By automating the material replenishment process, the Shared Refueling Machine Solution minimizes machine downtime associated with manual refills. Continuous material flow ensures that machines are always ready to operate, maximizing production output and reducing the costs associated with idle equipment and lost production time. - Reduced Errors and Rework
Automated material handling reduces the risk of human error in material selection and placement. This leads to a decrease in production defects and rework, saving both time and material costs. The increased accuracy also improves overall product quality and reduces the likelihood of customer returns.
Enhanced Flexibility and Scalability for Future Growth
The Shared Refueling Machine Solution excels in providing enhanced flexibility and scalability, crucial for manufacturers adapting to fluctuating demands and embracing rapid prototyping. Its shared nature allows for swift production line reconfigurations and seamless adjustments to operational scale, ensuring agility in dynamic manufacturing landscapes.
- Production Line Reconfiguration
The system's design facilitates effortless adjustments to production line layouts, enabling manufacturers to quickly adapt to new product introductions or changes in demand. This is in stark contrast to fixed, machine-specific refueling systems that require significant downtime and investment for reconfiguration. - Scalability on Demand
Whether scaling up for mass production or scaling down during periods of lower demand, the Shared Refueling Machine Solution adapts seamlessly. Its centralized resource management allows for efficient allocation of materials across multiple lines, eliminating the need for redundant infrastructure. - Ideal for Rapid Prototyping
The system’s agility is particularly advantageous for rapid prototyping environments, where quick turnaround times and frequent material changes are essential. It supports the fast-paced innovation cycle by providing a flexible and responsive material replenishment system. - Reduced Capital Expenditure
By serving multiple production lines, the shared refueling system avoids the need for individual refueling systems for each machine, resulting in significant cost savings and a better ROI. - Support for High-Mix, Low-Volume Production
The system’s flexibility makes it well-suited for high-mix, low-volume production environments. It can handle frequent material changes and small batch sizes without compromising efficiency. - Future-Proofing Operations
Investing in a shared refueling solution future-proofs manufacturing operations by providing a scalable and adaptable infrastructure. As production needs evolve, the system can easily be expanded or reconfigured to meet new requirements.
Zero One Solution Limited's Expertise in Implementing Advanced Solutions
Zero One Solution Limited stands as a leader in providing comprehensive PCB assembly solutions, leveraging over a decade of experience in PCB design, manufacturing, and assembly. Our core strength lies in delivering tailored, one-stop services that address the unique challenges of each client, ensuring seamless integration and optimal performance of the Shared Refueling Machine Solution within their existing infrastructure.
Our expertise spans the entire PCB lifecycle, from initial design and rapid prototyping to high-volume manufacturing and meticulous assembly. This holistic approach enables us to understand and address the intricate dependencies between each stage, resulting in solutions that are not only innovative but also highly practical and efficient.
Key aspects of Zero One Solution Limited's expertise include:
- Comprehensive PCB Design Services
Our design team excels in creating optimized PCB layouts that maximize signal integrity, minimize noise, and ensure manufacturability. We utilize cutting-edge software and simulation tools to validate designs and identify potential issues early in the development process. - Rapid Prototyping Capabilities
We specialize in rapid-response R&D prototype manufacturing, empowering clients to quickly test and iterate their designs. Our advanced prototyping facilities and streamlined processes enable us to deliver high-quality prototypes in record time. - Advanced Manufacturing Processes
Our state-of-the-art manufacturing facilities are equipped with the latest SMT and through-hole assembly equipment, ensuring precise and reliable component placement. We adhere to stringent quality control standards throughout the manufacturing process to guarantee the highest levels of product quality. - Seamless Integration and Customization
We understand that every client has unique requirements. Our team works closely with each client to customize the Shared Refueling Machine Solution to their specific needs, ensuring seamless integration with their existing MES/ERP systems and production workflows. - Global Supply Chain Network
Headquartered in Shenzhen, China, and with a branch office in Dubai, we operate strategically within a global PCBA supply chain network. This allows us to access worldwide resources and support, ensuring timely delivery and competitive pricing.
By partnering with Zero One Solution Limited, clients gain access to a wealth of expertise and resources, enabling them to accelerate product development, optimize manufacturing processes, and achieve significant cost savings. We are committed to providing innovative solutions that empower our clients to thrive in today's dynamic and competitive market.
Real-World Impact: Case Studies and Success Stories
The true value of the Shared Refueling Machine Solution lies in its tangible impact on manufacturing operations. While specific client data remains confidential, we can illustrate the benefits through generalized case studies and success stories that reflect common scenarios and outcomes observed across various implementations.
Consider these examples:
- Scenario 1: High-Mix, Low-Volume Production
A company specializing in rapid prototyping faced challenges with frequent material changeovers and significant downtime. Implementing the Shared Refueling Machine Solution allowed them to centralize material replenishment, drastically reducing changeover times by up to 70%. This resulted in a 25% increase in overall throughput and significantly improved responsiveness to customer demands. - Scenario 2: High-Volume, Standardized Production
A large-scale electronics manufacturer struggled with material waste and inefficient inventory management. By adopting the AI-driven predictive replenishment feature of the Shared Refueling Machine Solution, they optimized material ordering and minimized excess inventory. This led to a 15% reduction in material costs and a 10% improvement in OEE due to reduced stockouts and machine downtime. - Scenario 3: Expansion and Scalability
A rapidly growing PCB assembly firm needed to scale its operations without incurring massive capital expenditure. The Shared Refueling Machine Solution provided a flexible and scalable material handling system that allowed them to add new production lines without investing in dedicated refueling machines for each line. This resulted in a 40% reduction in capital expenditure compared to the traditional approach and enabled them to quickly adapt to increasing market demand. - Scenario 4: Addressing Labor Costs
Faced with rising labor costs, a manufacturing plant automated its material handling processes using the Shared Refueling Machine Solution. By reducing the need for manual material replenishment, they were able to reallocate valuable human resources to more strategic tasks, resulting in a 20% reduction in labor costs associated with material handling and a significant improvement in employee morale. - Scenario 5: Enhanced Traceability and Quality Control
A medical device manufacturer required stringent material traceability and quality control. The Shared Refueling Machine Solution provided real-time inventory tracking and seamless integration with their MES system, enabling them to trace every component used in their products and ensure compliance with regulatory requirements. This significantly reduced the risk of recalls and improved overall product quality.
These case studies demonstrate the versatility and effectiveness of the Shared Refueling Machine Solution in addressing a wide range of manufacturing challenges. By optimizing material flow, reducing costs, and enhancing flexibility, this solution empowers businesses to achieve significant improvements in efficiency, productivity, and profitability.
FAQs: Understanding the Shared Refueling Machine Solution
This section addresses frequently asked questions about the Shared Refueling Machine Solution, providing clarity on key aspects such as integration, maintenance, ROI, and compatibility. These answers are designed to give you a comprehensive understanding of how this solution can benefit your PCB assembly operations.
- How complex is the integration of the Shared Refueling Machine Solution with existing SMT lines?
Integration complexity varies based on your current setup. The Shared Refueling Machine Solution is designed with modularity in mind, allowing for flexible adaptation to different SMT line configurations. Zero One Solution Limited provides comprehensive support, including on-site assessment, customized integration plans, and dedicated technical teams to ensure a smooth and efficient transition. - What kind of maintenance does the Shared Refueling Machine Solution require?
The Shared Refueling Machine Solution is engineered for reliability and minimal downtime. Maintenance typically includes routine inspections, cleaning of material pathways, and software updates. Zero One Solution Limited offers various maintenance packages, including remote diagnostics, on-site support, and preventative maintenance schedules, to keep your system running optimally. - How is the ROI calculated for the Shared Refueling Machine Solution?
ROI is calculated by considering several factors, including reduced labor costs, decreased material waste, increased throughput, and improved OEE. By consolidating material replenishment and automating processes, the Shared Refueling Machine Solution significantly lowers operational expenses and boosts production efficiency, resulting in a compelling return on investment. We provide detailed ROI projections based on your specific manufacturing environment. - Is the Shared Refueling Machine Solution compatible with all types of SMT lines and components?
The solution is designed to be highly adaptable and compatible with a wide range of SMT lines and components. It supports various feeder types, component sizes, and material handling requirements. Our team will assess your specific needs and tailor the solution to ensure seamless compatibility with your existing equipment and processes. - What level of training is required for operators to use the Shared Refueling Machine Solution?
The Shared Refueling Machine Solution features an intuitive user interface, minimizing the learning curve for operators. Zero One Solution Limited provides comprehensive training programs, including on-site instruction and remote support, to ensure your team is fully proficient in operating and maintaining the system. The training covers all aspects of the solution, from basic operation to advanced troubleshooting. - How does the AI-driven predictive replenishment feature work?
The AI-driven predictive replenishment feature uses advanced algorithms to analyze historical production data, current inventory levels, and upcoming production schedules. By identifying patterns and trends, the system anticipates material needs and automatically triggers replenishment orders, preventing stockouts and minimizing downtime. This ensures a continuous and efficient material flow, optimizing production efficiency. - What measures are in place to ensure material traceability and prevent errors?
The Shared Refueling Machine Solution incorporates robust material traceability features, including barcode scanning, RFID tracking, and real-time inventory monitoring. These measures ensure accurate material handling, prevent errors, and provide complete visibility into the material flow throughout the production process. This reduces the risk of defects and ensures the highest levels of quality control.
The Shared Refueling Machine Solution from Zero One Solution Limited is more than just a piece of equipment; it's a strategic investment in the future of your manufacturing operations. By embracing this advanced, shared industrial automation, you can achieve unparalleled efficiency, significant cost reductions, and a competitive edge in the global market. Don't let traditional bottlenecks slow down your innovation. Contact Zero One Solution Limited today to discover how our expertise can accelerate your product development and empower your success.
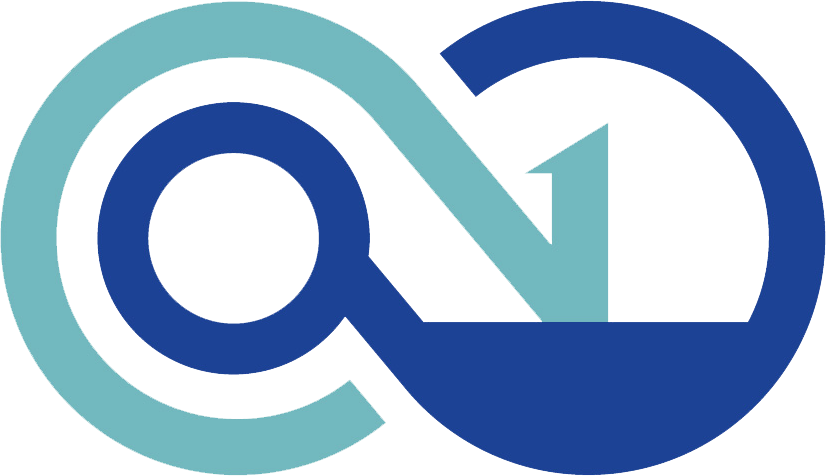