Shared Self-Service Device Machine Solution
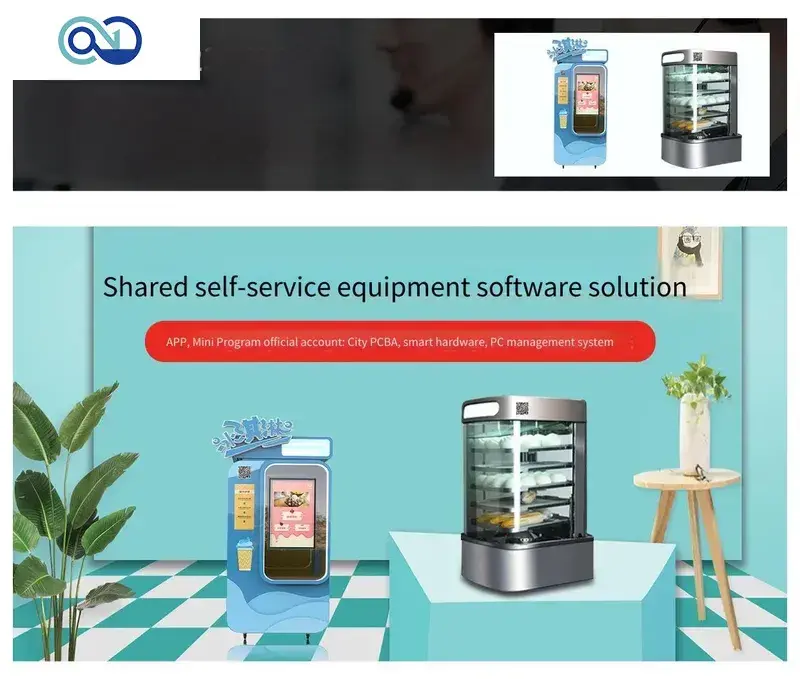
In an era where convenience and accessibility are paramount, shared self-service device machines have revolutionized industries from vending and retail to transportation and healthcare. These innovative systems, often found in high-traffic environments, empower users with instant access to services and products, fundamentally reshaping our daily interactions. But what truly underpins the reliability and efficiency of these ubiquitous devices? The answer lies at the heart of their electronic intelligence: advanced Printed Circuit Boards (PCBs). At Zero One Solution Limited, a leader in rapid-response PCB assembly, we understand the critical role these components play in bringing shared self-service solutions to life. This article will delve into the intricacies of developing and manufacturing robust PCB solutions tailored specifically for the demanding world of shared self-service device machines.
The Rise of Shared Self-Service Device Machines
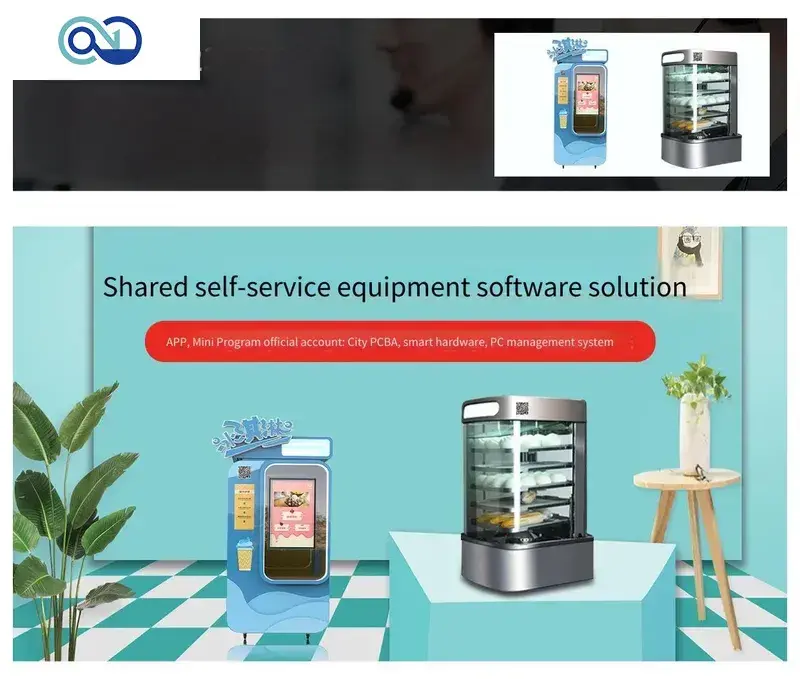
Shared self-service device machines are rapidly transforming how services are delivered across various sectors. Their increasing prevalence reflects a significant shift towards automated, user-centric solutions, driven by technological advancements and evolving consumer expectations. These machines offer numerous benefits, including enhanced efficiency, reduced operational costs, and improved customer convenience, making them a cornerstone of modern service delivery.
Several factors contribute to the growing adoption of shared self-service devices:
- Technological Advancements:
The Internet of Things (IoT), advanced sensors, and secure payment systems have enabled the development of sophisticated self-service machines. - Market Demand:
Consumers increasingly prefer self-service options for their speed, convenience, and 24/7 availability. - Economic Benefits:
Businesses can reduce labor costs and improve efficiency by deploying self-service machines. - Expanding Applications:
From retail kiosks to automated healthcare devices, self-service machines are finding applications in diverse industries.
The underlying electronics, particularly Printed Circuit Boards (PCBs), play a critical role in enabling the functionality and reliability of these machines. High-quality PCB design and assembly are essential for ensuring the continuous and efficient operation of shared self-service devices.
- What are the key benefits of using shared self-service device machines?
Shared self-service device machines offer numerous advantages, including increased efficiency, reduced operational costs through minimized labor, and enhanced customer convenience with 24/7 availability. They also enable businesses to scale services more effectively and gather valuable data on user behavior. - In which industries are shared self-service device machines most commonly used?
These machines are utilized across various sectors, including retail (self-checkout kiosks), transportation (ticketing machines), healthcare (automated dispensing systems), and entertainment (vending machines). Their adaptability makes them suitable for any industry seeking to streamline service delivery. - How do technological advancements contribute to the growth of shared self-service device machines?
Advances in IoT connectivity, sensor technology, secure payment processing, and user interface design have significantly enhanced the functionality and reliability of self-service machines. These technologies enable features like remote monitoring, real-time data analytics, and seamless user experiences. - What role do PCBs play in shared self-service device machines?
Printed Circuit Boards (PCBs) serve as the central nervous system of these devices, integrating all electronic components and ensuring seamless communication between them. The quality and design of PCBs are crucial for the machine's performance, durability, and overall reliability. - What are the key challenges in deploying shared self-service device machines?
Challenges include ensuring security against vandalism and theft, maintaining consistent uptime, managing software updates remotely, and addressing user accessibility concerns. Robust hardware design and proactive maintenance strategies are essential to overcome these challenges. - How can businesses ensure the security of shared self-service device machines?
Security measures include implementing tamper-proof enclosures, using encrypted communication protocols, integrating surveillance systems, and conducting regular security audits. Additionally, employing advanced authentication methods like biometric scanning can enhance security.
Core Technological Requirements for Self-Service Devices
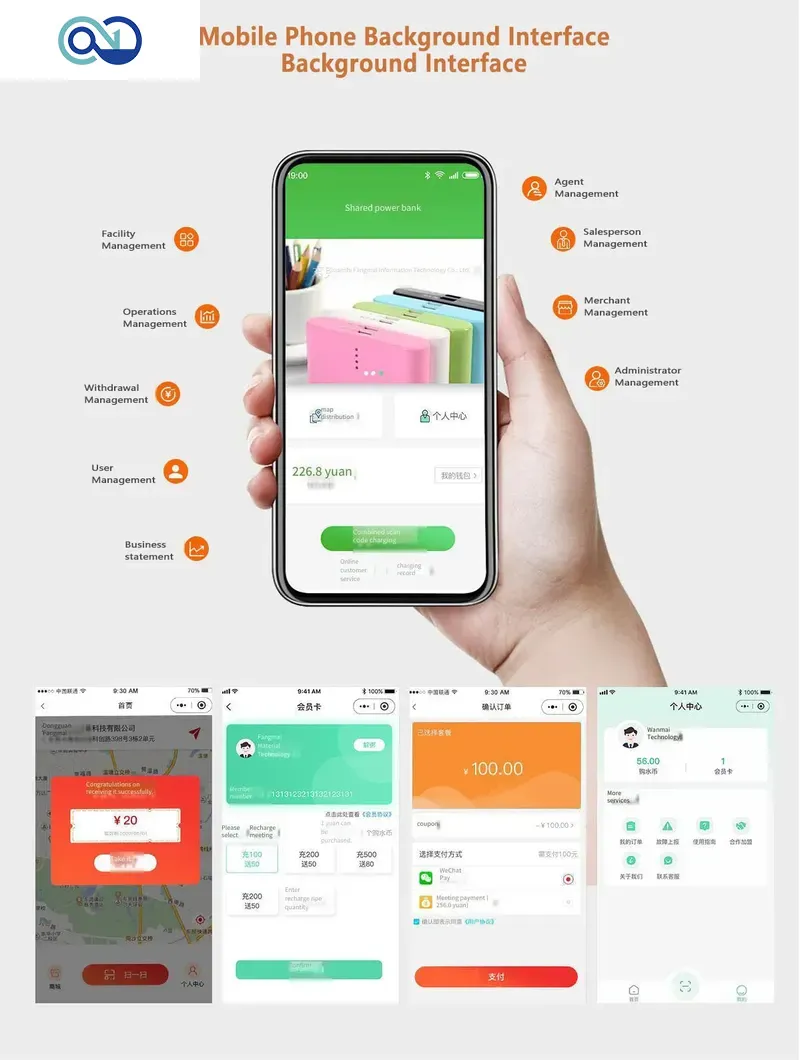
Shared self-service devices rely on a combination of technologies to deliver convenient and efficient services. Meeting the fundamental technological requirements—including robust connectivity, secure payment processing, intuitive user interfaces, and stable operating systems—is critical for the success of any self-service deployment. These elements are underpinned by reliable, high-performance electronic components and integrated systems.
- Connectivity (IoT)
Self-service devices must be seamlessly connected to the internet for remote monitoring, software updates, data transmission, and real-time inventory management. This requires robust and reliable IoT connectivity, often achieved through Wi-Fi, cellular, or Ethernet connections. The choice of connectivity depends on the device's location and specific application requirements. - Payment Processing
Secure and seamless payment processing is a core requirement for most self-service devices. This involves integrating payment gateways that support various payment methods, including credit/debit cards, mobile payments (NFC), and QR codes. Compliance with PCI DSS standards is crucial to protect sensitive customer data and prevent fraud. - User Interfaces
Intuitive and user-friendly interfaces are essential for a positive user experience. Touchscreen displays, interactive buttons, and clear visual cues guide users through the self-service process. The UI design should be simple, responsive, and accessible to users of all abilities. - Robust Operating Systems
Self-service devices need stable and secure operating systems to manage hardware resources, run applications, and ensure reliable operation. Embedded Linux, Android, and Windows IoT are common choices, offering varying degrees of customization, security, and support. The OS should be optimized for the specific hardware and software requirements of the device. - Reliable Electronic Components
High-quality and reliable electronic components are the foundation of any self-service device. This includes microcontrollers, sensors, power management ICs, communication modules, and display drivers. Selecting components from reputable manufacturers and conducting thorough testing are essential for ensuring long-term reliability and performance. - Integrated Systems
Self-service devices often require integration of multiple systems, such as payment terminals, barcode scanners, printers, and dispensing mechanisms. These systems must work seamlessly together to provide a complete self-service solution. Careful planning and testing are needed to ensure compatibility and reliable operation.
The Pivotal Role of PCBs in Self-Service Solutions
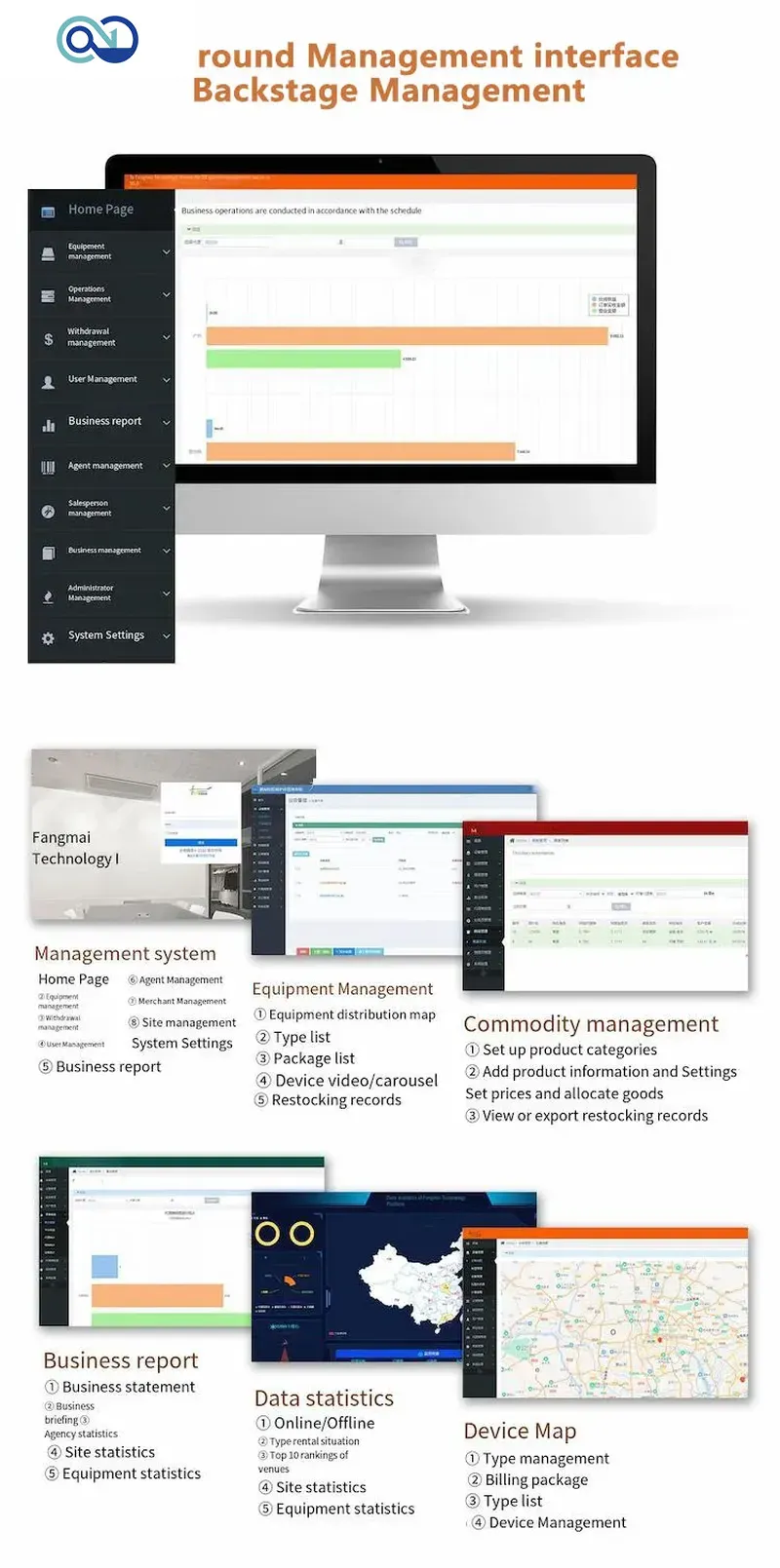
Printed Circuit Boards (PCBs) are the backbone of shared self-service devices, acting as the central nervous system that integrates and controls all electronic components. Their design and quality directly impact the functionality, reliability, and longevity of these machines. Meeting specific characteristics like durability, compact design, effective thermal management, and power efficiency is crucial for ensuring continuous operation in diverse environments.
Here's a breakdown of why PCBs are so vital in self-service solutions:
- Centralized Component Integration
PCBs provide a structured platform for mounting and connecting various electronic components, ensuring seamless communication and functionality within the self-service device. - Signal Routing and Power Distribution
PCBs efficiently route electrical signals and distribute power to all components, optimizing performance and minimizing signal interference. - Thermal Management
Effective PCB design incorporates thermal management techniques to dissipate heat generated by electronic components, preventing overheating and ensuring reliable operation. - Durability and Reliability
High-quality PCBs are built to withstand the demands of continuous operation and environmental factors, ensuring long-term reliability of the self-service device. - Compact Design
PCBs enable the creation of compact and efficient self-service devices, maximizing functionality in a minimal footprint.
The following table outlines key PCB characteristics crucial for self-service applications:
Characteristic | Importance | Considerations |
---|---|---|
Durability | Essential for withstanding constant use and potential environmental stressors. | Material selection (e.g., FR-4, Aluminum), robust construction techniques. |
Compact Design | Critical for space-constrained self-service machines. | High-density interconnect (HDI) technology, multi-layer PCBs. |
Thermal Management | Prevents overheating and ensures component longevity. | Heat sinks, thermal vias, proper component placement. |
Power Efficiency | Reduces energy consumption and extends operational lifespan. | Optimized trace routing, low-power components. |
Signal Integrity | Maintains signal quality for reliable data transmission. | Controlled impedance, proper grounding techniques. |
Therefore, quality PCB manufacturing and assembly are non-negotiable for achieving the desired performance and longevity in shared self-service device solutions. Selecting a reliable PCB partner is paramount.
Zero One Solution Limited's Expertise in PCB Assembly for Self-Service
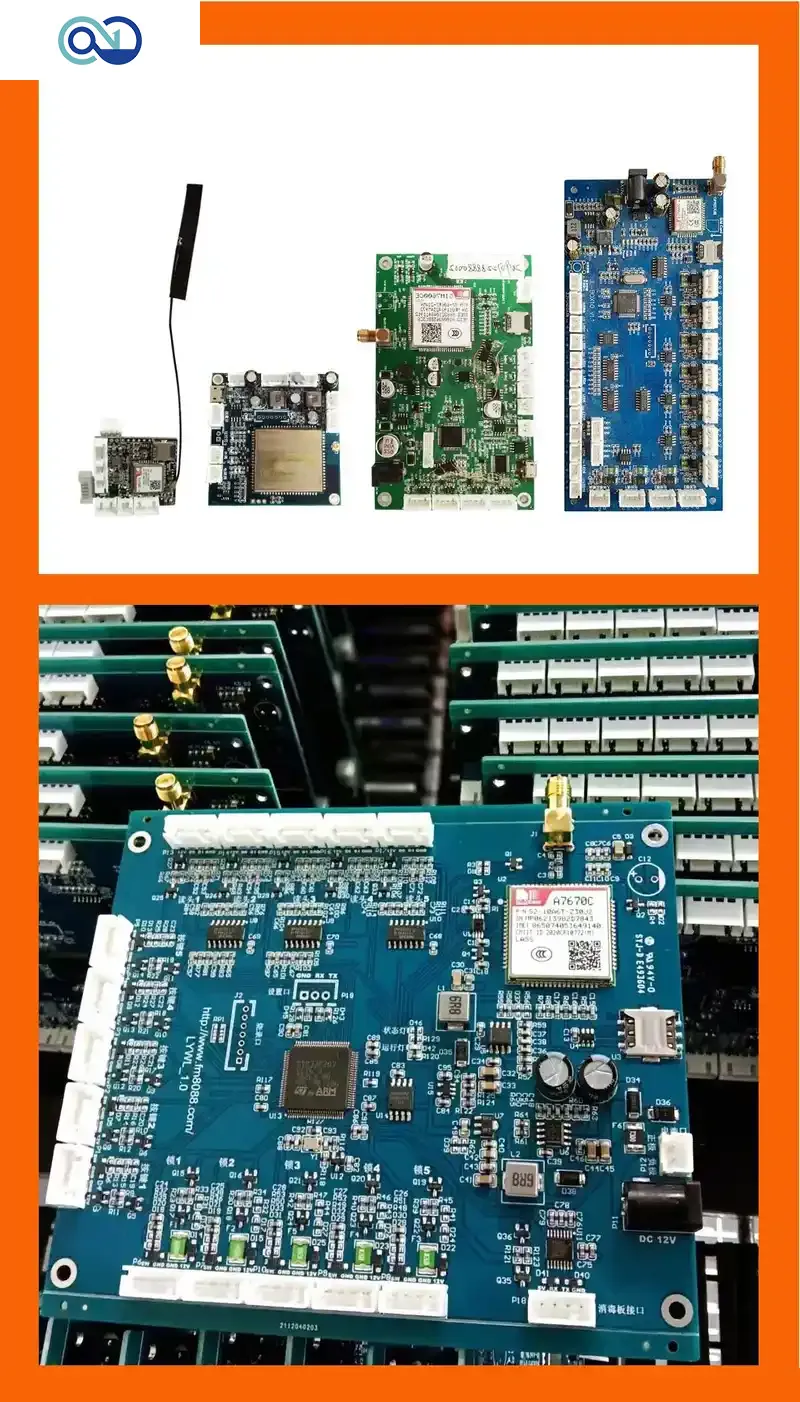
Zero One Solution Limited excels in delivering comprehensive PCB solutions tailored for shared self-service device machines. Our expertise spans the entire product lifecycle, from initial design and rapid prototyping to precision manufacturing and advanced assembly. We provide a one-stop service designed to accelerate your product development timeline and ensure the highest quality outcomes for your self-service applications.
- Rapid Prototyping Services
We offer rapid prototyping services that allow you to quickly test and refine your designs. This fast turnaround helps accelerate the development process and reduces time to market. - Design Expertise
Our team of experienced engineers provides expert PCB design services, optimizing layouts for performance, manufacturability, and cost-effectiveness. We ensure your PCBs meet the specific requirements of your self-service device application. - Manufacturing Precision
Zero One Solution Limited is committed to manufacturing PCBs with the highest precision. We use state-of-the-art equipment and rigorous quality control processes to ensure that every PCB meets our exacting standards. - Advanced Assembly Processes
Our advanced assembly processes guarantee accurate and reliable component placement and soldering. This is critical for the performance and longevity of PCBs used in demanding self-service environments. - One-Stop Service
We streamline the entire PCB production process, offering a complete one-stop service from design to assembly. This simplifies project management, reduces lead times, and ensures seamless integration of all components. - What types of self-service device applications benefit from Zero One Solution Limited's PCB assembly expertise?
Our expertise benefits a wide range of self-service applications, including vending machines, kiosks, payment terminals, ticketing systems, and automated retail solutions. We tailor our services to meet the unique needs of each application. - How does Zero One Solution Limited ensure the quality of PCBs for self-service devices?
We implement rigorous quality control procedures throughout the entire PCB production process, from material selection to final inspection. This includes automated optical inspection (AOI), in-circuit testing (ICT), and functional testing to ensure the highest levels of reliability and performance.
Tailored Solutions: Customizing PCBs for Unique Self-Service Needs
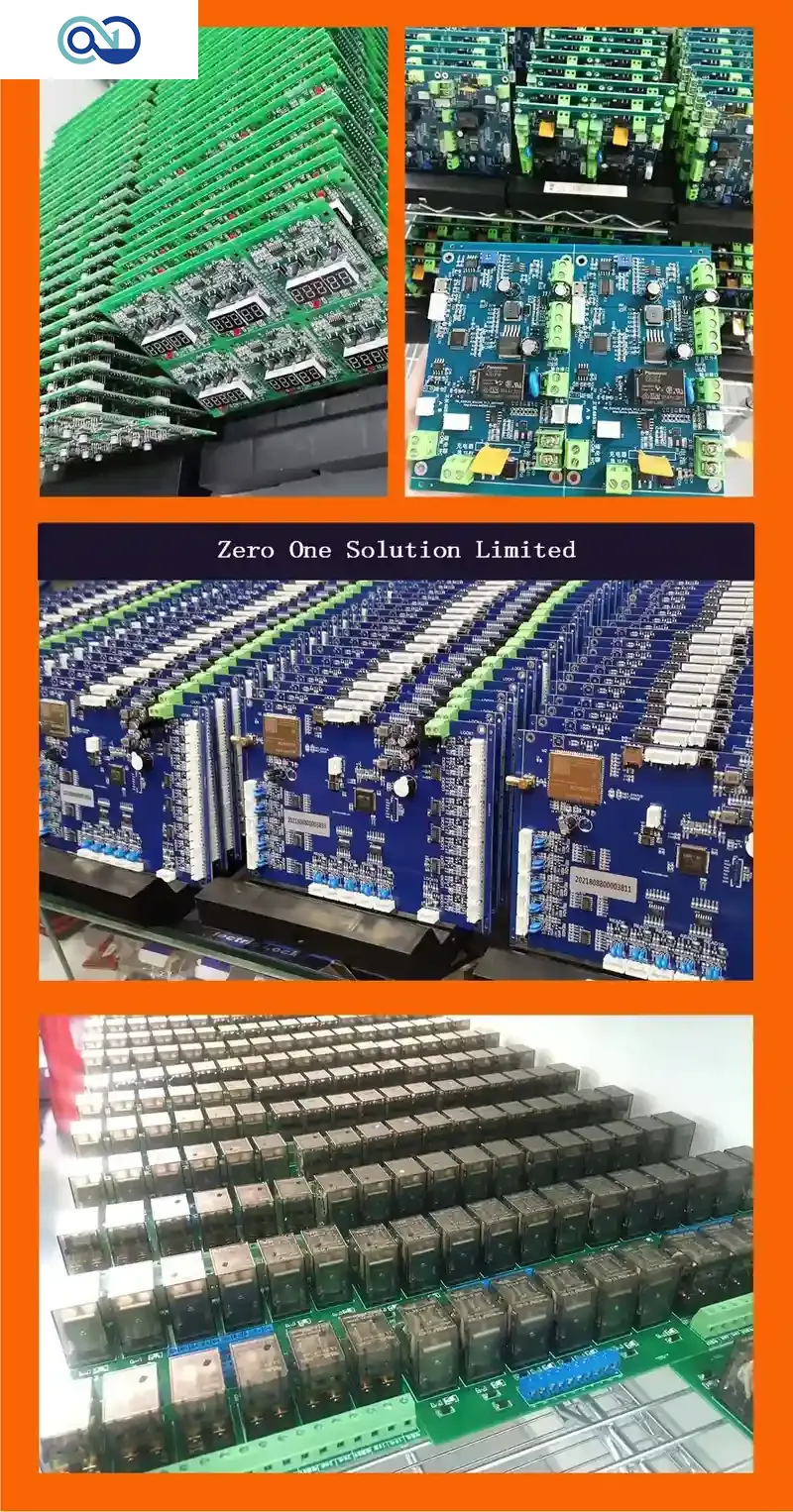
Custom PCB design and manufacturing are paramount for shared self-service applications, given their diverse requirements. Zero One Solution Limited excels in collaborating with clients to create bespoke PCB solutions, addressing specific functionalities, form factors, and environmental challenges. Our focus is on adapting and innovating to meet unique project demands, ensuring optimal performance and reliability.
The ability to tailor PCB solutions is critical because self-service devices vary widely in their applications, from vending machines and kiosks to automated lockers and information terminals. Each application presents unique demands in terms of size, power consumption, environmental resilience, and functionality. Standard, off-the-shelf PCBs often cannot meet these specific requirements, leading to suboptimal performance or even failure.
Zero One Solution Limited leverages its expertise to provide custom PCB services, ensuring that every client receives a solution perfectly aligned with their needs. Here's how we approach customization:
- Collaborative Design
We work closely with clients to understand their specific requirements, including functionality, size constraints, power needs, and environmental conditions. This collaborative approach ensures that the final PCB design meets all project specifications. - Material Selection
We carefully select materials that offer the best combination of performance, durability, and cost-effectiveness for the application. This includes considering factors such as thermal conductivity, resistance to moisture, and mechanical strength. - Advanced Manufacturing Techniques
We employ advanced manufacturing techniques to create PCBs with complex geometries, high component densities, and tight tolerances. This enables us to meet the demands of even the most challenging self-service applications. - Prototyping and Testing
We offer rapid prototyping services to allow clients to test and refine their designs before committing to full-scale production. Our rigorous testing procedures ensure that the final PCB meets all performance and reliability requirements. - Environmental Adaptation
We design PCBs to withstand the environmental conditions in which the self-service device will operate, whether it's extreme temperatures, humidity, or exposure to harsh chemicals. This ensures long-term reliability and performance.
Here are a few examples of how Zero One Solution Limited has customized PCBs for unique self-service needs:
- Vending Machines
For vending machines, we design PCBs that are compact, energy-efficient, and capable of handling a wide range of payment options. We also incorporate features such as temperature sensors and motor control circuits. - Automated Lockers
For automated lockers, we design PCBs that are secure, reliable, and capable of interfacing with various locking mechanisms. We also incorporate features such as user authentication and remote monitoring. - Interactive Kiosks
For interactive kiosks, we design PCBs that are high-performance, feature-rich, and capable of supporting a variety of user interfaces. We also incorporate features such as touch screen controllers and audio amplifiers.
By offering tailored PCB solutions, Zero One Solution Limited empowers its clients to create innovative and reliable shared self-service devices that meet the evolving needs of their customers. Our commitment to customization, quality, and innovation makes us the ideal partner for any self-service project.
Quality Assurance and Reliability in Self-Service Device PCBs
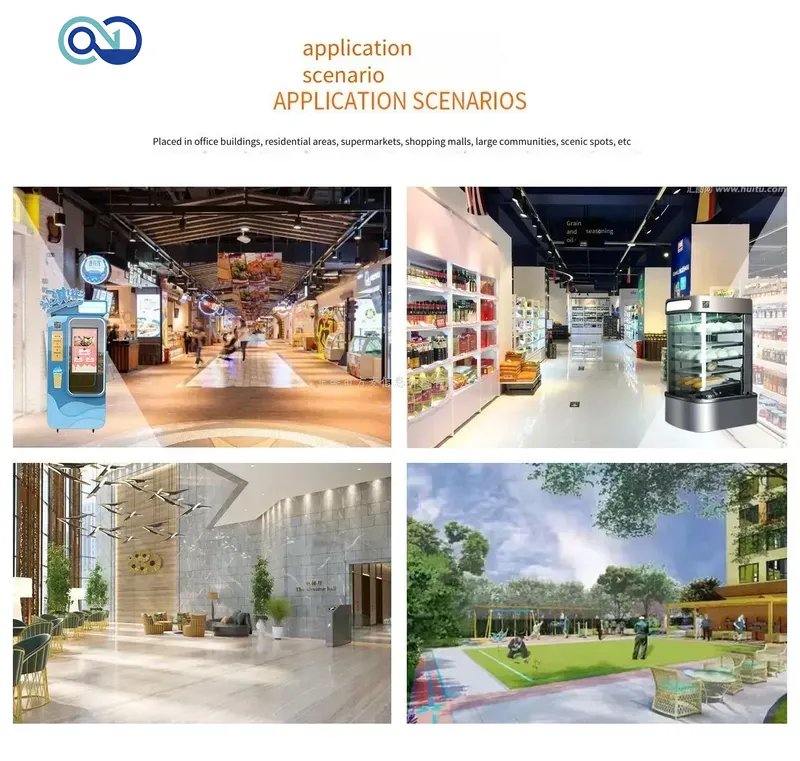
Ensuring the reliability and longevity of PCBs used in shared self-service devices is paramount. At Zero One Solution Limited, we implement rigorous quality control and testing procedures, encompassing material selection, manufacturing standards, environmental testing, and adherence to industry certifications. This comprehensive approach guarantees robust components capable of withstanding demanding operational cycles, a crucial factor for the continuous and dependable performance of self-service machines.
- What material selection processes are used to ensure PCB reliability?
We meticulously select PCB materials based on their ability to withstand thermal stress, humidity, and mechanical vibrations. High-Tg (glass transition temperature) materials and those compliant with industry standards like IPC-4101 are prioritized to ensure long-term reliability in diverse operating environments. - What manufacturing standards does Zero One Solution Limited adhere to for self-service device PCBs?
Zero One Solution Limited adheres to stringent manufacturing standards, including IPC-A-600 (Acceptability of Printed Boards) and IPC-A-610 (Acceptability of Electronic Assemblies). These standards ensure that our PCBs meet the highest quality benchmarks for self-service applications. - What environmental testing procedures are employed to validate PCB performance?
Our PCBs undergo comprehensive environmental testing, including thermal cycling, humidity testing, and vibration analysis. These tests simulate real-world operating conditions, ensuring that our PCBs can withstand the environmental stressors encountered in self-service device deployments. - Which industry certifications does Zero One Solution Limited hold for PCB manufacturing?
Zero One Solution Limited maintains certifications such as ISO 9001 (Quality Management System), demonstrating our commitment to consistent and high-quality PCB manufacturing processes. These certifications validate our ability to meet the stringent requirements of the self-service device industry. - How does Zero One Solution Limited ensure the long-term reliability of PCBs in self-service machines?
We conduct accelerated life testing (ALT) to simulate years of operation in a compressed timeframe. This allows us to identify potential failure points early in the product lifecycle and implement corrective actions, ensuring the long-term reliability of our PCBs. - What types of quality control checks are performed during PCB assembly?
During PCB assembly, we perform automated optical inspection (AOI), X-ray inspection, and in-circuit testing (ICT) to detect defects such as missing components, solder joint issues, and electrical faults. These checks ensure that the assembled PCBs meet our rigorous quality standards. - How are components selected to withstand demanding operational cycles in self-service devices?
We select components with extended temperature ranges, high endurance ratings, and robust packaging to ensure they can withstand the continuous operational cycles of self-service devices. Our component selection process prioritizes reliability and longevity to minimize downtime and maintenance costs.
Future Trends in Shared Self-Service Technology and PCB Innovation
The shared self-service device market is on the cusp of significant transformation, driven by innovations like AI integration, advanced sensor technology, enhanced security, and a growing emphasis on sustainable design. These trends are poised to redefine PCB design and manufacturing, demanding solutions that are not only more efficient and reliable but also environmentally conscious. Zero One Solution Limited is strategically positioned to embrace these advancements, offering cutting-edge PCB solutions that meet the evolving needs of this dynamic sector.
- How will AI integration impact PCB design for self-service devices?
AI integration will lead to smarter, more adaptive self-service devices. PCBs will need to support advanced processing capabilities, potentially incorporating specialized AI accelerators or high-performance computing modules. Expect to see designs optimized for machine learning tasks, such as facial recognition, predictive maintenance, and personalized user experiences. - What role will advanced sensor technology play in future self-service machines?
Advanced sensors will enable self-service machines to gather more comprehensive data about their environment and users. This includes sensors for temperature, humidity, air quality, proximity, and even biometric data. PCBs will need to accommodate a wider range of sensor interfaces and ensure seamless data transmission for improved functionality and data analytics. - Why is enhanced security becoming a critical factor in self-service device PCBs?
As self-service devices handle more sensitive data and financial transactions, security becomes paramount. Future PCBs will need to incorporate advanced security features such as hardware-based encryption, secure boot processes, and tamper-resistant designs to protect against data breaches and unauthorized access. - How is sustainable design influencing PCB manufacturing for self-service applications?
Sustainability is driving demand for eco-friendly PCB materials and manufacturing processes. This includes using recyclable substrates, reducing energy consumption during production, and minimizing waste. Expect to see more self-service devices incorporating PCBs designed for easy disassembly and component reuse, aligning with circular economy principles. - What are the challenges and opportunities in adapting PCB design to support flexible and foldable self-service devices?
The rise of flexible and foldable displays in self-service machines presents unique challenges for PCB design. PCBs will need to be flexible enough to conform to curved surfaces or withstand repeated bending without compromising performance. This requires innovative materials, interconnect technologies, and manufacturing techniques, opening up new possibilities for device form factors and user interfaces. - How can Zero One Solution Limited help navigate these future trends in PCB innovation?
Zero One Solution Limited is dedicated to staying at the forefront of PCB technology. We invest in research and development to explore new materials, manufacturing processes, and design techniques that address the evolving needs of the self-service device market. Our expertise in rapid prototyping, custom design, and high-quality assembly enables us to deliver innovative PCB solutions that empower our clients to succeed in this dynamic landscape. We work closely with our clients to understand their unique requirements and provide tailored solutions that meet their specific challenges.
In conclusion, the proliferation of shared self-service device machines is a testament to their transformative power, driven by the demand for efficiency, accessibility, and convenience. At the core of every reliable and high-performing self-service unit lies a meticulously designed and expertly assembled PCB. Zero One Solution Limited stands as your premier partner in navigating this complex landscape, offering unparalleled expertise in rapid prototyping, design, manufacturing, and assembly of PCBs tailored for the unique demands of shared self-service applications. Our commitment to quality, speed, and innovation ensures that your vision for the next generation of self-service technology can be realized with precision and reliability. Don't let manufacturing complexities hinder your progress. Partner with Zero One Solution Limited to accelerate your product development and empower your shared self-service device machines with the robust electronic foundations they deserve. Contact us today to discuss how our one-stop PCB solutions can bring your innovative ideas to market faster.
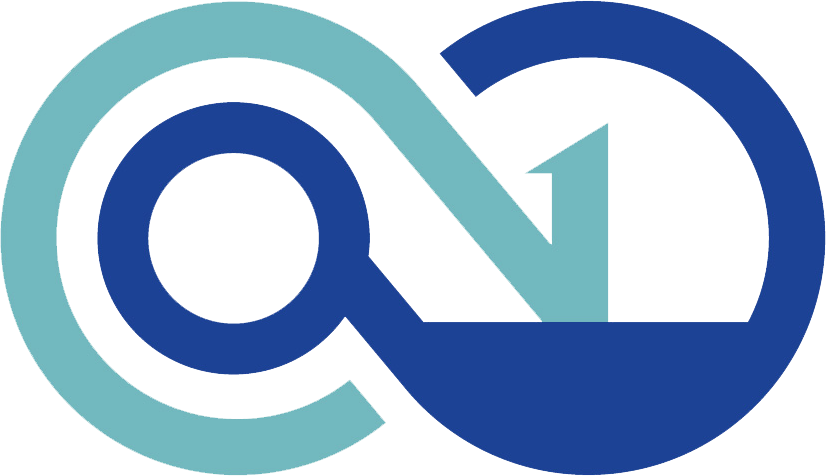