Streamlining Your Electronics: How to Order PCB with Components
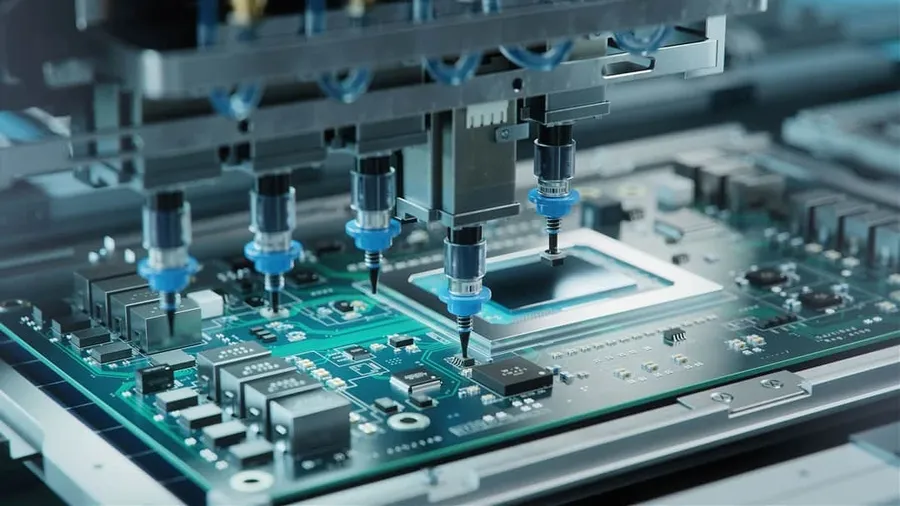
In today's fast-paced world of electronics, the ability to quickly and efficiently bring a design from concept to reality is crucial. Ordering a printed circuit board (PCB) with pre-populated components not only accelerates the prototyping process but also reduces manufacturing errors and time. This article explains the essential steps involved in ordering PCBs with components, seamlessly bridging the gap between innovative designs and tangible products.
Understanding the PCB Assembly Process
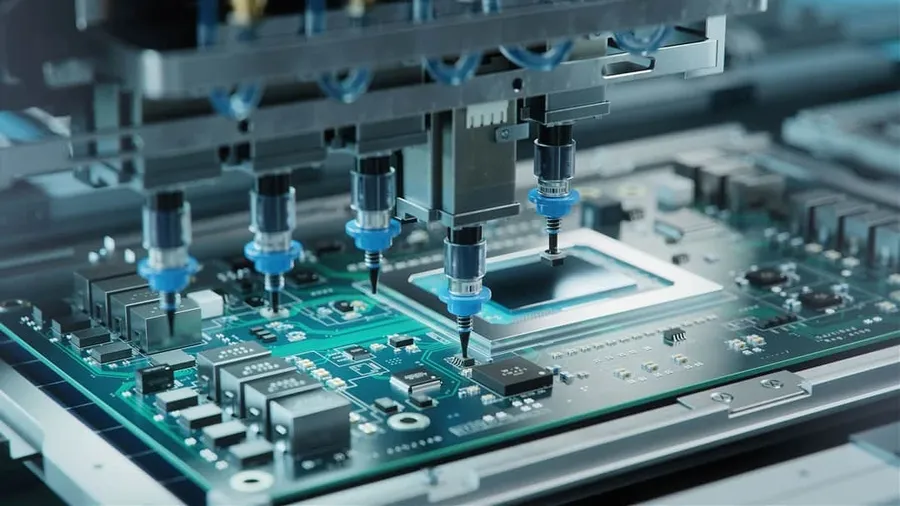
The Printed Circuit Board (PCB) assembly process is a multi-stage operation that transforms a bare PCB into a functional electronic module. It encompasses a series of carefully orchestrated steps, commencing with the initial design and culminating in a fully tested and operational product, ready for integration into a larger system or device. This process involves the strategic placement of electronic components onto the PCB, securing them through soldering techniques, and rigorous testing to ensure performance and reliability.
- Design and Preparation:
This initial stage involves the creation of a detailed PCB layout using specialized software, followed by the generation of essential files like Gerber files and Bill of Materials (BOM). Accurate design and meticulous preparation are crucial for subsequent steps. - Component Sourcing:
The next phase entails acquiring the necessary electronic components, which includes resistors, capacitors, integrated circuits (ICs), and connectors, based on the BOM. Strategic component sourcing ensures both cost-effectiveness and availability, and can be accomplished through manufacturer's services, distributors, or in-house inventory. - PCB Fabrication:
The bare PCBs are manufactured based on the design files, a process that includes etching, drilling, and surface finishing. The quality of the fabricated board directly affects the overall assembly and performance of the final product. - Solder Paste Application:
Solder paste, a mixture of solder alloy and flux, is precisely applied to the PCB pads using a stencil. This step is critical for creating the electrical connections between the components and the board during the soldering process. - Component Placement:
Electronic components are placed onto the solder paste-laden pads using automated pick-and-place machines. Precise placement is imperative to avoid short circuits and ensure proper circuit functionality. The component placement information is derived from the BOM and placement data file. - Soldering:
The PCB assembly undergoes reflow soldering, where it passes through a controlled temperature oven. The heat melts the solder paste, creating permanent electrical and mechanical connections between components and the PCB. Different types of soldering methods and temperature profiles can be utilized based on component types. - Inspection and Quality Control:
The assembled PCB boards undergo both manual and automated visual inspection as well as electrical testing. This helps identify any defects, missing components, or soldering issues. Comprehensive testing is necessary to ensure the functionality and performance of the assembled PCB. - Testing and Verification:
Functional testing is performed to verify that the assembled PCB meets the performance requirements and specifications. Tests range from basic continuity checks to complex system-level testing, ensuring the reliability of the final product. The testing strategy is an integral part of the assembly process, and includes both in-circuit testing and functional testing.
Choosing the Right PCB Manufacturer
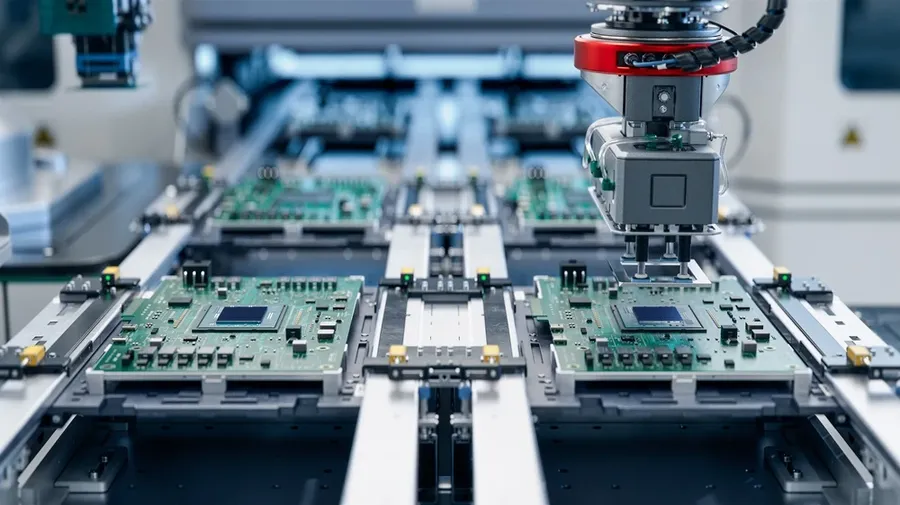
Selecting the appropriate PCB manufacturer is a critical decision that significantly impacts the cost, quality, and delivery timeline of your assembled PCBs. A careful evaluation of factors such as cost, turnaround time, technological capabilities, and the manufacturer's expertise is paramount to achieving a successful project.
Several factors should be considered when selecting a PCB manufacturer. These include:
- Cost
The total cost of PCB manufacturing and assembly should fit your project's budget, including tooling, setup fees, component costs, and assembly charges. - Turnaround Time
The time required to complete the fabrication and assembly process should align with your project timeline. Some manufacturers offer expedited services at a premium. - Technological Capabilities
Ensure the manufacturer can handle your PCB design complexity, including layer count, minimum trace width/spacing, and component type (e.g., BGA, fine pitch). - Component Sourcing Options
Assess whether the manufacturer offers component sourcing services, and whether you can supply your own components. Consider their inventory and access to authorized distributors. - Assembly Expertise
Evaluate the manufacturer's experience with assembling similar designs and complexity. Review their equipment, certifications, and previous work if possible. - Minimum Order Quantity (MOQ)
Consider the manufacturer's MOQ, especially for prototype orders. Some manufacturers offer flexible options for small orders. - Quality Control Measures
Inquire about the manufacturer's quality control processes, including inspection and testing procedures. Look for manufacturers with certifications like ISO standards. - Geographic Location
Consider the geographic location of the manufacturer as it will impact shipping costs and lead time.
By thoroughly considering these factors, you can make a well-informed decision when selecting a PCB manufacturer that meets the specific requirements and constraints of your project, optimizing for cost, time, and quality.
Preparing Your Design Files for Ordering
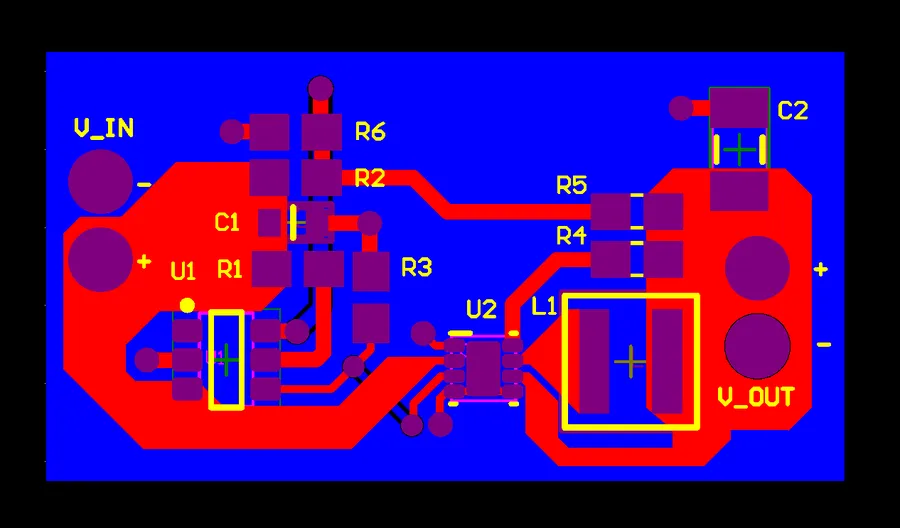
Accurate and comprehensive design files are paramount for a successful PCB assembly order. These files act as blueprints for both fabrication and assembly, ensuring that the final product matches your design specifications. The primary files include Gerber files, a Bill of Materials (BOM), and component placement data, each serving a distinct but crucial purpose in the manufacturing process.
Let's delve deeper into each of these critical components:
- Gerber Files
Gerber files are the standard file format used in the PCB manufacturing industry, containing the geometric data for each layer of your PCB (copper layers, silkscreen, solder mask, etc.). Ensure these files are generated correctly from your design software, using the appropriate settings for your manufacturer's capabilities. Incorrect Gerber files can lead to errors in fabrication, which will cascade into assembly issues. It's crucial to verify all layers are present and aligned as intended using a Gerber viewer before submitting them. - Bill of Materials (BOM)
A Bill of Materials (BOM) is a comprehensive list of all components required for assembly. It should include accurate part numbers, manufacturer names, package types, and quantities. A well-formatted and detailed BOM avoids delays caused by incorrect component orders or missing components. Include information such as component designators (e.g., R1, C2), footprints, and any special notes related to purchasing or component orientation. - Component Placement Data
Component placement data is necessary for automated pick-and-place machines during PCB assembly. This file typically contains the X and Y coordinates, rotation, and layer for each component, ensuring the components are placed precisely and accurately on the board. Ensure the placement data corresponds with your BOM, and use the correct units (typically mm or inches).
By carefully preparing these three sets of design files, you will significantly reduce the risk of errors, delays, and cost overruns during the PCB assembly process. Double-checking all your files before submitting will help ensure the production of a high-quality and functional product.
Component Sourcing: Simplifying the Process
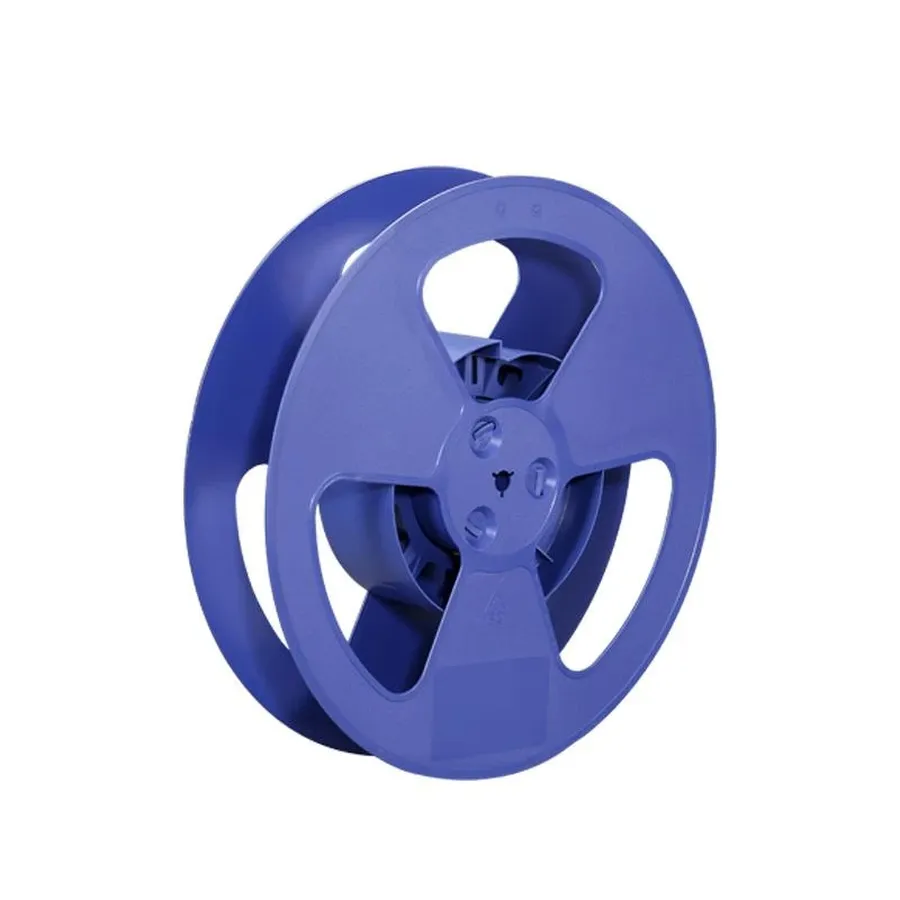
Effective component sourcing is crucial for successful PCB assembly. This section explores various strategies to obtain the necessary electronic components, ensuring both cost-efficiency and timely project completion. We'll discuss using manufacturer-provided services, leveraging distributors, and managing your own component inventory.
- Manufacturer's Component Services
Many PCB manufacturers offer component sourcing services. This integrated approach can streamline the process, reducing lead times and simplifying logistics. Manufacturers often have established relationships with component suppliers, potentially leading to better pricing and availability. However, their selections might be limited to specific vendors or components they frequently handle. - Purchasing from Distributors
Utilizing electronic component distributors provides access to a wide range of parts from various manufacturers. Distributors like Digi-Key, Mouser, and Arrow offer comprehensive catalogs, making it easier to find specialized or hard-to-source components. This flexibility comes with the potential for higher prices, especially for smaller quantities, and the added responsibility of verifying component authenticity. - Utilizing Your Own Component Inventory
If your company maintains an internal stock of components, this can lead to significant cost savings and faster assembly times. However, careful inventory management is necessary to ensure the availability of the required parts and avoid obsolescence. Utilizing your inventory can also reduce the need to order smaller batches, which often carry higher per-unit costs. - Considerations for Sourcing
When choosing a sourcing strategy, factors like component availability, lead time, cost, and component authenticity should all be considered. The right approach will depend on the specific project requirements and resources available. For low volume prototypes, purchasing from distributors might be the simplest option, but for large production runs manufacturer services might be more economical.
Step-by-Step Guide to Placing Your Order
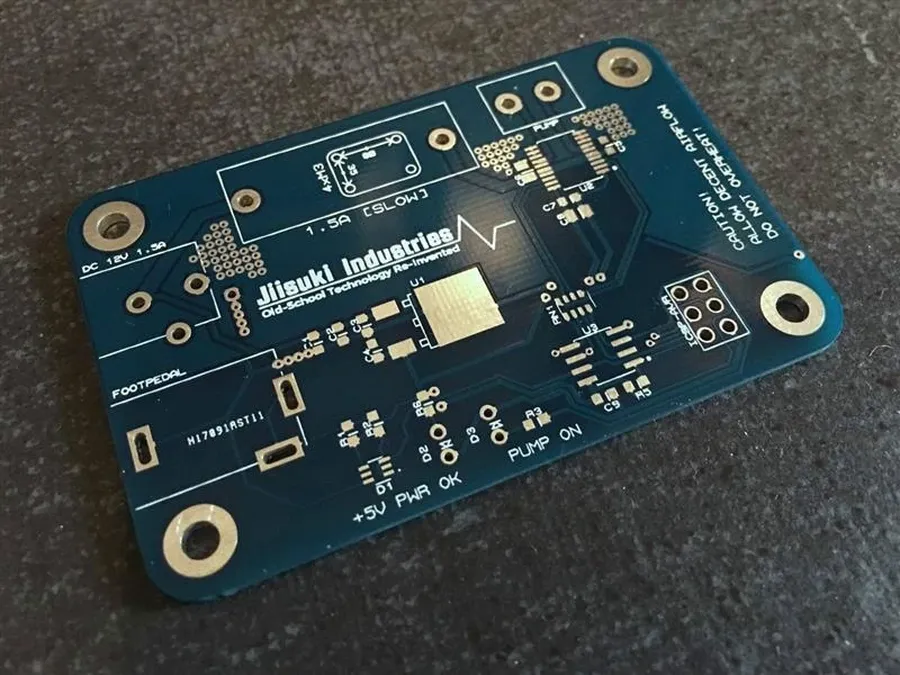
Successfully ordering PCBs with components involves a systematic approach, transitioning from design to a finished product. This section provides a detailed walkthrough of the process, focusing on online quoting and order management, empowering you to navigate the process with confidence and efficiency.
- Prepare Your Design Files
Ensure you have all necessary files ready. This includes Gerber files for the PCB layout, a Bill of Materials (BOM) listing all components with their specifications, and a component placement file (centroid file) indicating the exact location and orientation of each component. These files are critical for accurate fabrication and assembly. - Select a PCB Manufacturer and Assembly Service
Choose a manufacturer that meets your project's requirements. Consider factors like cost, turnaround time, technology capabilities (e.g., minimum trace width, number of layers), and assembly expertise. Many manufacturers offer online quote tools, making this step convenient. - Upload Your Files and Obtain a Quote
Most manufacturers provide a platform to upload your Gerber files, BOM, and placement file. After uploading, specify the quantity of PCBs and any special requirements. The system will generate a quote based on your specifications. Review the quote carefully, paying attention to the price breakdown and lead times. - Verify the BOM and Component Sourcing
Double-check that your BOM accurately reflects the required components. If you are using the manufacturer’s component sourcing, verify component availability and pricing, and make sure they meet your technical requirements before proceeding. Otherwise, prepare your own components to send to the manufacturer for assembly. - Confirm Your Order and Make Payment
Once you have verified the quote and component sourcing, confirm your order. Follow the manufacturer’s instructions to make the payment. Ensure you have saved a copy of the order details and payment confirmation. - Track Your Order
Many manufacturers provide an online platform for tracking the status of your order. Monitor the progress from fabrication to assembly, and finally to shipping. Be prepared to address any queries or requests from the manufacturer during the process. - Receive and Inspect Your Assembled PCBs
Upon receiving the PCBs, carefully inspect them for any manufacturing defects. Compare against your initial design and BOM to ensure all components are placed correctly. If you notice any discrepancies, contact the manufacturer to address the issue promptly.
Frequently Asked Questions About Ordering PCB with Components
This section addresses common questions and concerns that arise when ordering PCBs with components, providing clarity on critical aspects of the process to ensure a smooth experience.
- How should components be arranged on a PCB for optimal assembly?
Component arrangement significantly affects assembly efficiency and performance. It's crucial to follow design rules for spacing to prevent soldering issues and ensure reliable operation. Consider the assembly method (manual or automated) and orient components for ease of placement and soldering, adhering to manufacturer's guidelines. - Do PCB manufacturers typically offer component sourcing services?
Many PCB manufacturers, particularly those offering assembly services, do provide component sourcing. This can be a convenient option, streamlining the ordering process. However, it's important to compare their component pricing with that of distributors and consider using your own inventory when appropriate. - What does a typical PCB order with components include?
A typical order includes the fabricated PCB board and all specified electronic components assembled on the board. Key elements include gerber files for PCB layout, a bill of materials (BOM) detailing all parts, and component placement data. Some manufacturers also include testing and quality reports, depending on your requirements. - What is the minimum component spacing required on a PCB?
Minimum component spacing depends on the manufacturer's capabilities, the component types, and the soldering method. Generally, it's crucial to adhere to the manufacturer's design rules and IPC standards, which specify minimum distances between component pads and other components to prevent shorts and facilitate proper soldering. Specific component datasheets will detail minimum footprint requirements. - What factors should be considered when selecting components for PCB assembly?
Component selection should be based on several factors including electrical requirements, physical size, temperature specifications, cost, and availability. You should check component datasheets thoroughly to understand the electrical characteristics (voltage, current, power, etc), footprint dimensions, and reliability. Choosing reliable, readily available components helps streamline sourcing and reduce time to market. - What if my chosen components are not available through the manufacturer?
If your components aren’t available from the manufacturer, you'll need to source them yourself and provide them to the manufacturer for assembly. You can use electronic component distributors or your own inventory. Ensure all the parts are compatible and of the quality you require and deliver the components to your PCB manufacturer on time. - What kind of information is needed for a PCB assembly order?
To ensure successful PCB assembly, you need to provide the Gerber files for the PCB, a Bill of Materials (BOM) listing all components including specifications and part numbers, pick-and-place data specifying component locations and orientations, and any specific assembly instructions. This will allow the PCB assembler to fabricate and assemble the PCB accurately.
Quality Control and Testing
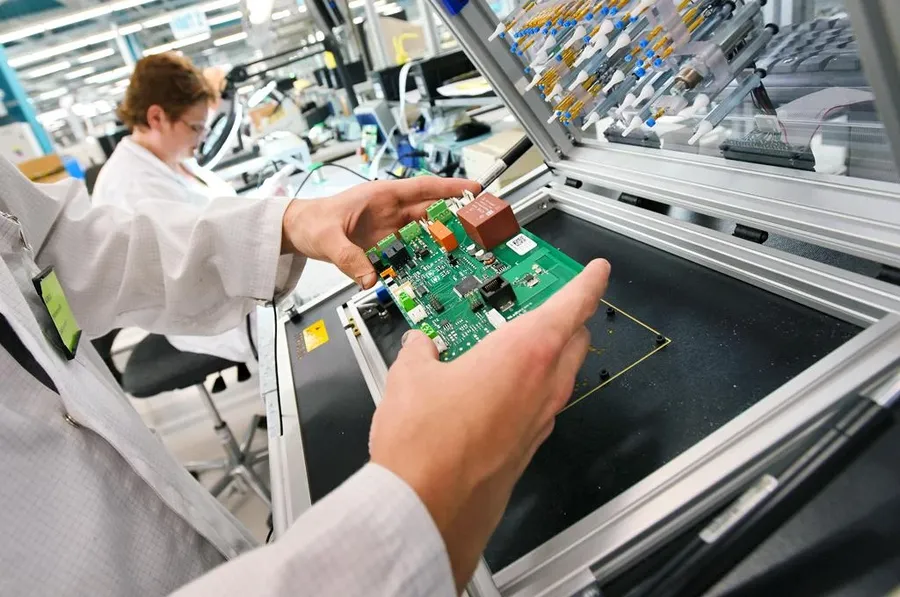
Rigorous quality control and testing are paramount in ensuring that assembled PCBs meet the required functional, reliability, and quality standards. This phase is not merely a formality but a critical step in verifying that the manufacturing process has yielded a product that performs as intended and will endure in its operational environment.
Without thorough testing, hidden defects and design flaws can lead to costly field failures, reputational damage, and compromised product performance. The emphasis on quality at this stage is an investment in the long-term success and robustness of the electronic product.
- Visual Inspection:
A preliminary examination of the PCB assembly for obvious defects such as misaligned components, solder bridges, or damaged parts. High-resolution cameras and trained personnel are typically employed for this task. - Automated Optical Inspection (AOI):
AOI systems use cameras to capture detailed images of the PCB and software to compare these images with a known good standard. This detects defects like solder joint issues, missing components, or incorrect polarity. - In-Circuit Testing (ICT):
ICT uses test points on the PCB to measure the electrical performance of individual components and circuits. This validates that components are connected correctly and functioning within their specified parameters. - Functional Testing:
This involves testing the PCB assembly in its intended application. It verifies that the board performs all required functions correctly under simulated or actual working conditions. This may include power cycling, signal integrity tests, and performance benchmarks. - X-Ray Inspection:
X-ray technology is used to inspect hidden solder joints, especially on complex packages like BGAs (Ball Grid Arrays). This ensures that solder connections are reliable and free from voids or other defects. - Environmental Testing:
PCBs may undergo environmental testing to assess their performance under conditions such as temperature fluctuations, humidity, and vibration. These tests simulate real-world scenarios to verify durability and long-term reliability.
Cost Optimization Strategies for Ordering PCBs with Components
Reducing the cost of ordering PCBs with components involves a multifaceted approach, from initial design considerations to efficient sourcing and order management. Strategic cost optimization throughout the entire process can significantly lower overall expenses without compromising quality.
- Design Optimization
Streamlining your PCB design reduces material costs and complexity. Simplifying the design by minimizing layers, via count, and board size can significantly lower fabrication costs. Consider using standard component footprints and sizes to minimize the need for custom components, which can significantly increase both cost and lead time. - Efficient Component Sourcing
Compare prices from multiple distributors for the same components. Consider using manufacturer's services or purchasing directly from component manufacturers. Evaluate alternative parts to see if they offer the same functionality at a lower cost. Always consider the trade-offs of cost versus lead time; cheaper components may have longer lead times. - Order Consolidation
Consolidate orders to take advantage of volume discounts from both component suppliers and PCB assembly houses. Plan ahead to place orders for multiple projects together when possible. This not only reduces individual per-project costs but also minimizes shipping fees. Using a consolidated bill of materials (BOM) can also assist in this process. - Standardization
Whenever possible, use standard, commonly available components to reduce cost and lead times. Unique and custom components often come with higher cost and longer delivery times. Design your boards to accommodate a range of widely available component options. - Panelization
For smaller boards, consider panelizing your PCB design to have multiple boards manufactured on a single panel. This can greatly reduce manufacturing costs because it improves the efficient use of materials and equipment. Panelization is usually done by the manufacturer, but it is important to discuss it with them before placing your order.
Optimization Strategy | Cost Reduction Impact | Implementation Complexity |
---|---|---|
Design Simplification | High | Medium |
Multi-Sourcing Components | Medium to High | Low to Medium |
Order Consolidation | Medium | Low |
Component Standardization | Medium | Low |
Panelization | Medium to High | Low to Medium |
Comparative Analysis of PCB Assembly Services
Selecting the ideal PCB assembly service requires a careful evaluation of various factors. This comparative analysis provides a structured overview of key differences between common service offerings to aid in your decision-making process. The table below highlights the strengths and weaknesses of various providers, helping you align the service with your project requirements and budget.
Service Provider | Turnaround Time | Cost | Component Sourcing | Assembly Capabilities | Minimum Order Quantity (MOQ) | Strengths | Weaknesses |
---|---|---|---|---|---|---|---|
JLCPCB | Fast (2-7 days) | Low | Yes (Basic) | SMT, THT | Low | Cost-effective for prototypes, Quick turnaround, Good for small to medium volumes | Limited component options, Potential quality concerns on complex assemblies |
PCBWay | Moderate (3-10 days) | Moderate | Yes (Expanded) | SMT, THT, BGA, Flexible PCB | Medium | Wider range of services and component options, Good for medium-sized productions, Known for better quality compared to JLCPCB | Slightly higher cost than JLCPCB, Longer lead times |
Seeed Studio Fusion | Moderate (5-12 days) | Moderate | Yes (Extensive) | SMT, THT | Medium | Extensive component sourcing, Strong support for open-source hardware, Good for prototyping and low-volume production | Can be pricier than JLCPCB, Longer lead times compared to JLCPCB |
Local Assembly House | Variable (1-4 weeks) | High | Flexible | Varies widely | Flexible | Customizable services, Strong customer support and direct communication, Suitable for complex and large scale builds | High cost, Longer turnaround time, May have minimum order requirements |
Turnkey Service | Variable (2-8 weeks) | High | Full Management | Full Range | High | Full management of PCB manufacturing and component sourcing, Ideal for large-scale production, High level of customization | Most expensive, Longest lead times, Less flexibility for prototypes |
Ordering PCBs with components is a streamlined process when approached systematically. By understanding the nuances of design preparation, component sourcing, and the assembly process, you can ensure the successful realization of your electronic projects. Choose your manufacturer wisely, prepare your design files carefully, and always prioritize quality and testing. Whether you're a hobbyist or a professional, understanding how to efficiently order PCB with components is key to navigating the complex world of electronic manufacturing and turning innovative ideas into reality, remember, ordering your PCB with components saves time and reduces the headache.
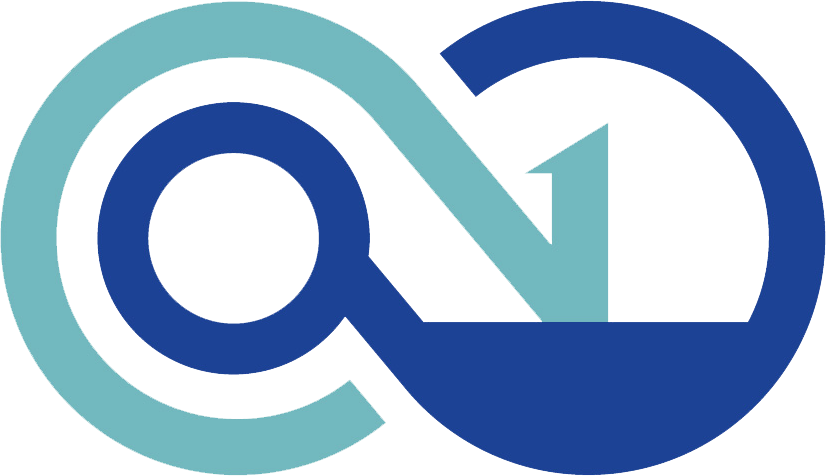