Understanding Copper Clad Boards: Types, Uses, and Selection Guide
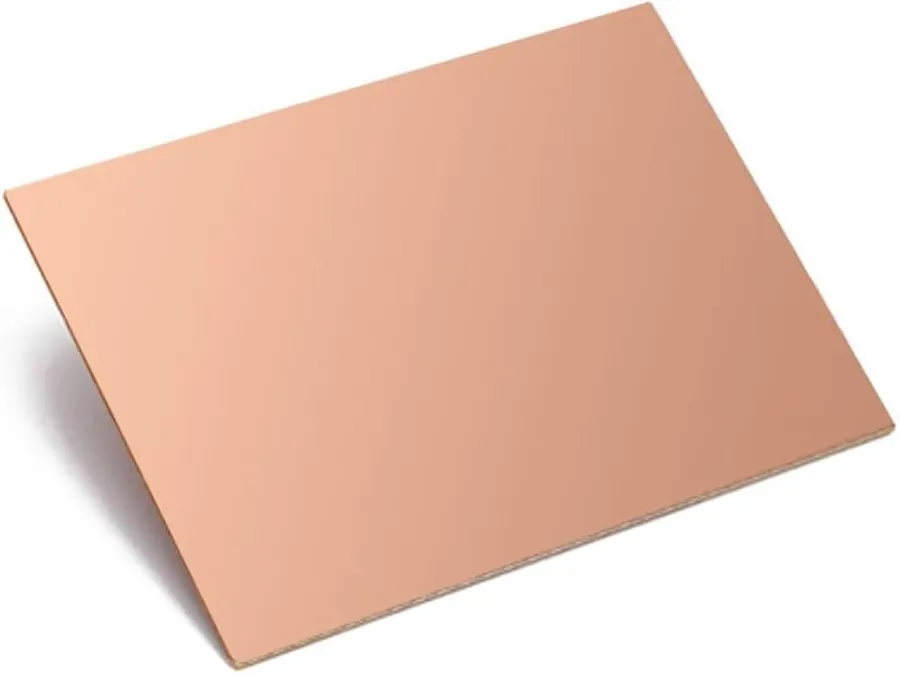
In our increasingly interconnected world, copper clad boards are the unsung heroes behind countless electronic devices. From the smartphones in our pockets to the complex systems powering industries, these foundational components play a crucial role. This article delves into the nature of copper clad boards, examining their diverse types, applications, and offering a guide to selecting the right board for your next project. We'll explore not only how they're used in electronics but also what it takes to bring them from a raw board to a functional circuit. Get ready to demystify the world of copper clad boards and uncover how they enable so much of modern technology.
What is a Copper Clad Board?
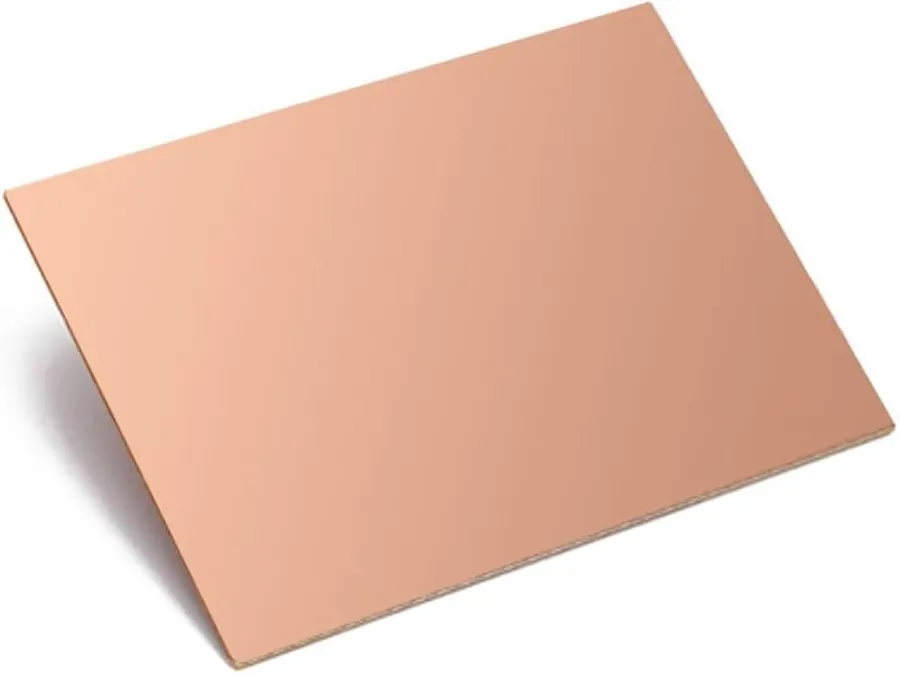
A copper clad board, at its core, is a composite material engineered for the fabrication of printed circuit boards (PCBs). It consists of a base substrate, typically a non-conductive material like fiberglass or a composite, onto which a thin layer of copper foil is bonded. This copper layer is the conductive medium that allows for the creation of electrical pathways. The base substrate provides mechanical support and electrical insulation.
The performance of a copper clad board is determined by the properties of both the base substrate and the copper foil. The substrate's mechanical strength and thermal resistance impact the board's reliability. The copper foil’s thickness, purity and adhesion affect its electrical conductivity. The manufacturing process ensures that the copper layer is firmly adhered to the substrate, which is critical for reliable performance. Let's look at these in more detail.
Layer | Material | Role | Key Properties |
---|---|---|---|
Base Substrate | FR-4 (Fiberglass Epoxy), CEM-1, Phenolic | Provides mechanical support and electrical insulation | Mechanical strength, thermal resistance, electrical insulation |
Copper Foil | Copper | Provides a conductive pathway for electrical signals | Conductivity, thickness, adhesion |
Types of Copper Clad Boards
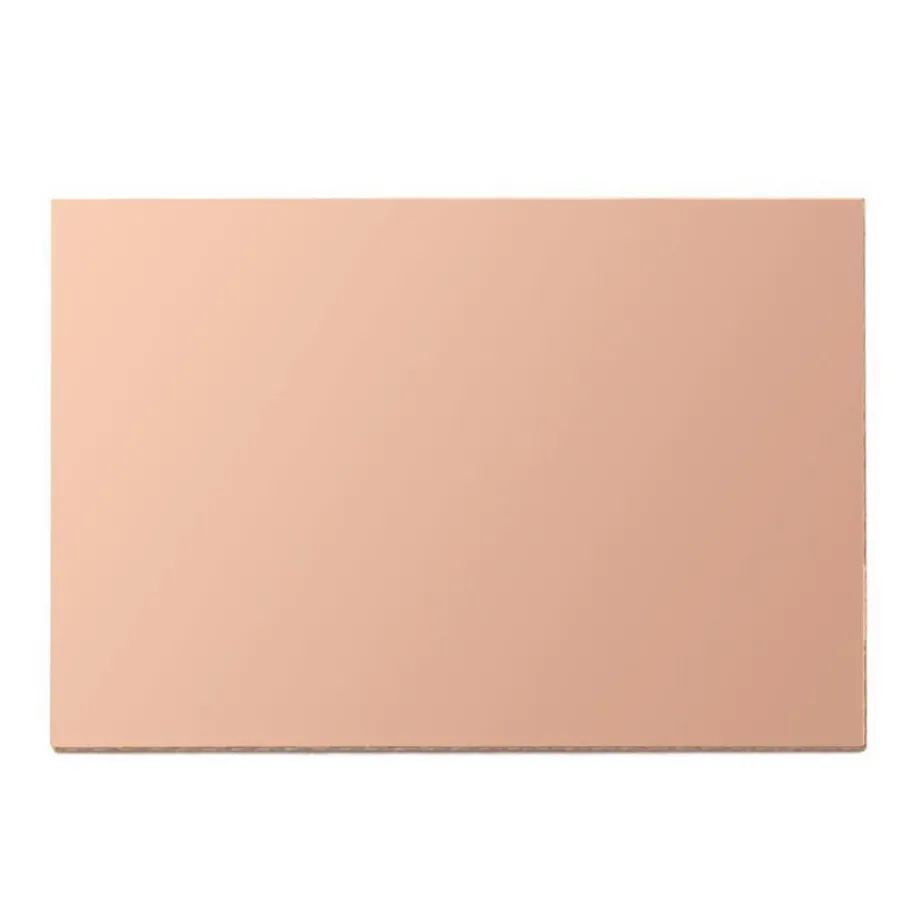
Copper clad boards are fundamental to electronics manufacturing, serving as the base for printed circuit boards (PCBs). They are available in several configurations, each tailored for different applications based on complexity, cost, and performance requirements. The primary types are single-sided, double-sided, and multi-layered boards, each offering distinct advantages and disadvantages.
Type | Description | Complexity | Cost | Typical Applications |
---|---|---|---|---|
Single-Sided | Copper layer on one side of the substrate. | Lowest | Lowest | Simple electronics, educational projects, basic prototyping |
Double-Sided | Copper layers on both sides of the substrate. | Medium | Medium | Intermediate-complexity electronics, common consumer devices, moderate power applications |
Multi-Layered | Multiple copper layers separated by insulating material. | Highest | Highest | High-density electronics, advanced computing, telecommunications, aerospace |
The selection of copper clad board type should be driven by the specific project requirements. Single-sided boards are ideal for basic applications where complexity and performance demands are low. As complexity and performance demands increase, double-sided and multi-layered boards are more appropriate. The increased costs associated with the double-sided and multi-layered options are offset by the capabilities and densities they enable.
Common Materials Used in Copper Clad Boards
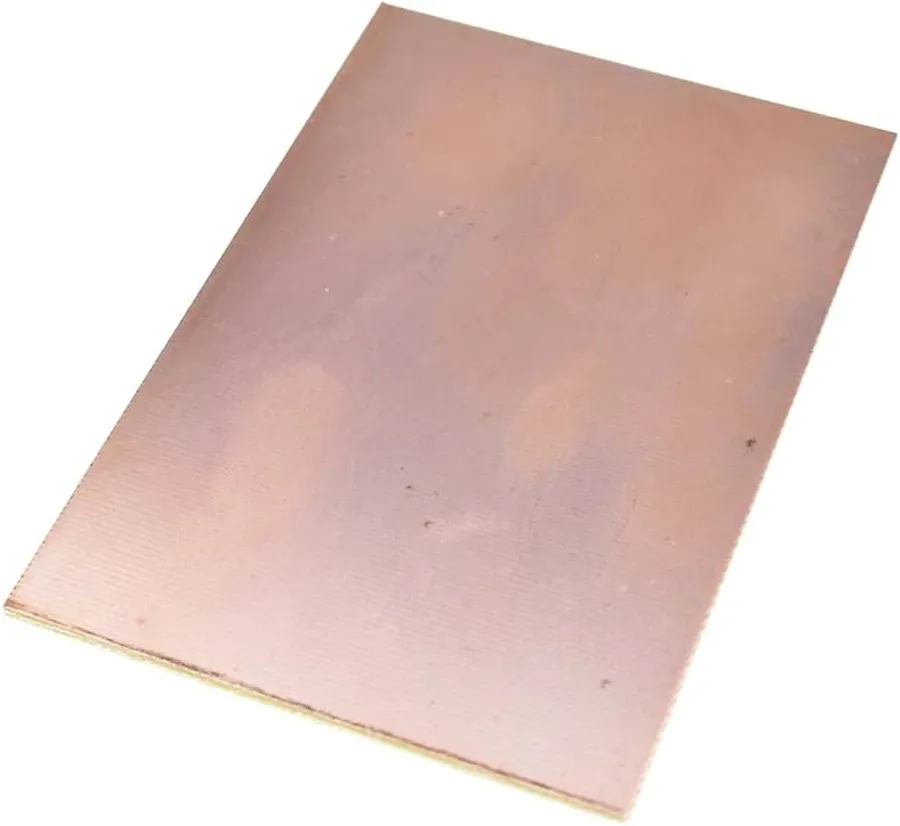
The performance and suitability of a copper clad board are heavily influenced by the base materials used. Common substrates include FR-4, CEM-1, and phenolic, each offering a unique combination of properties concerning fire resistance, mechanical strength, and cost. Selecting the appropriate base material is crucial to achieving the desired performance for a given application.
Material | Fire Resistance | Mechanical Strength | Cost | Typical Applications |
---|---|---|---|---|
FR-4 | Good (Self-extinguishing) | High | Moderate | General-purpose PCBs, consumer electronics, industrial control systems |
CEM-1 | Moderate | Moderate | Lower | Single-sided PCBs, cost-sensitive applications, less demanding environments |
Phenolic | Low (Flammable) | Low | Low | Simple, low-cost applications, such as educational kits, non-critical electronics |
FR-4 (Flame Retardant type 4) is the most commonly used substrate for PCBs. It is a composite material made of woven fiberglass cloth with an epoxy resin binder. FR-4 offers a good balance of electrical properties, mechanical strength, and fire resistance, making it suitable for a wide variety of applications. While slightly more expensive than CEM-1 and phenolic, its versatility and reliability make it the preferred choice for many projects. CEM-1 (Composite Epoxy Material 1) is a composite material consisting of a paper substrate with a fiberglass layer and an epoxy resin binder. It offers a cost-effective alternative to FR-4 for less demanding applications. Phenolic is the least expensive substrate material, primarily composed of paper bonded with a phenolic resin. It exhibits lower mechanical strength and is not flame retardant, limiting its use to simple, non-critical electronics where cost is the primary consideration.
Copper Thickness and Its Significance
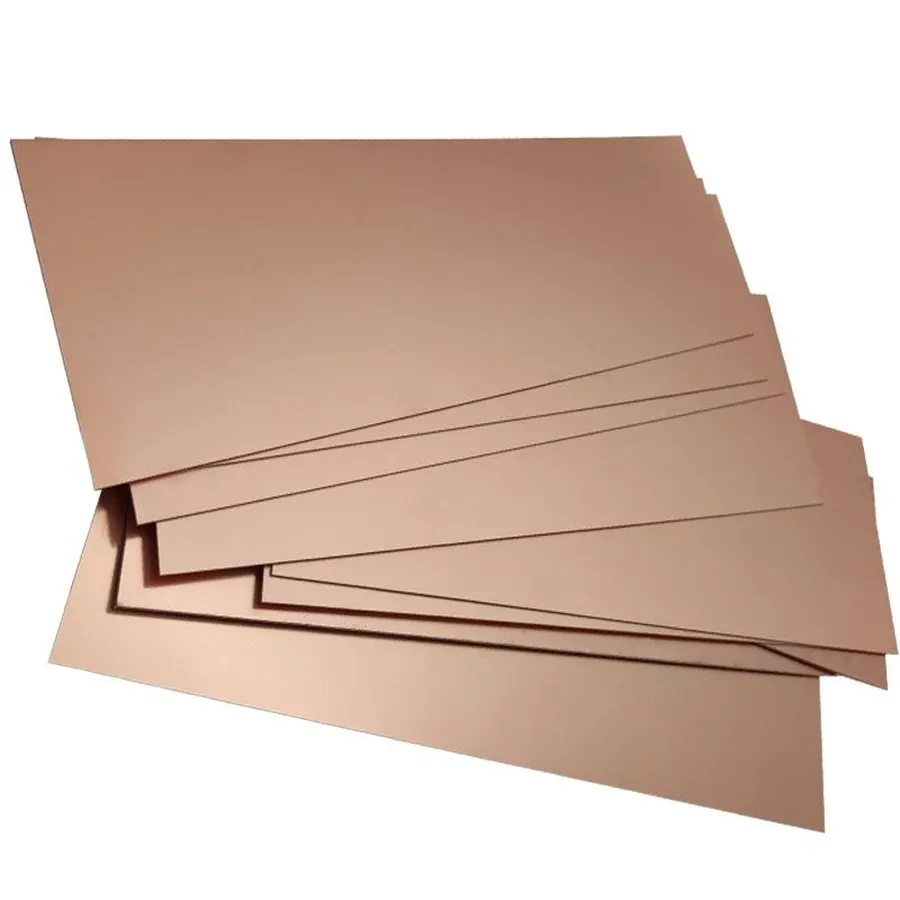
Copper thickness, typically measured in ounces per square foot (oz/ft²), is a critical parameter in copper clad boards that directly influences their electrical performance. This measurement refers to the weight of copper spread over a one square foot area and dictates the board's ability to handle electrical current without overheating or experiencing signal degradation. The appropriate copper thickness ensures the reliable operation of electronic circuits.
Copper Thickness (oz/ft²) | Approximate Thickness (µm) | Typical Applications | Current Carrying Capacity |
---|---|---|---|
0.5 oz | 17.5 µm | Low-power signal circuits, simple hobby projects | Lower |
1 oz | 35 µm | General-purpose electronics, most common thickness | Moderate |
2 oz | 70 µm | Higher current applications, power electronics | Higher |
3 oz or more | 105 µm+ | High-power applications, demanding thermal management | Very High |
The current-carrying capacity of a copper trace increases with thickness, but also with trace width. The thicker the copper, the more current it can handle without excessive heat build-up, making it a critical design factor in ensuring longevity of the board. Selecting the proper thickness is crucial, balancing performance requirements, cost, and manufacturing considerations.
For low-power applications, such as signal processing or simple digital circuits, a standard 1 oz/ft² copper layer is generally sufficient and cost-effective. In contrast, high-power applications, such as motor controllers or power supplies, require thicker copper layers (2 oz/ft² or more) to manage the higher current levels, prevent overheating, and ensure that the electrical performance is not compromised.
Applications of Copper Clad Boards
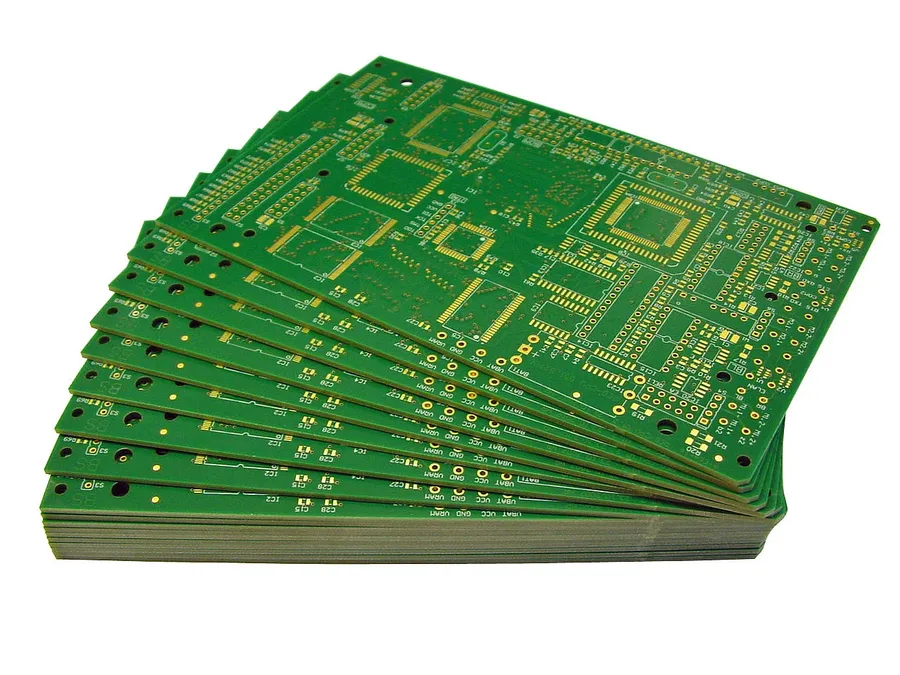
Copper clad boards serve as the foundational building blocks for a vast array of electronic devices and systems, owing to their versatility and essential role in circuit construction. They facilitate the creation of printed circuit boards (PCBs), which are integral to nearly all modern electronics, from simple consumer gadgets to sophisticated industrial machinery.
- Prototyping and Development
In the prototyping phase, copper clad boards are indispensable. They allow engineers and hobbyists to rapidly develop and test circuit designs without the need for complex and expensive custom manufacturing. Their ease of modification and etching makes them perfect for iterative design processes. - DIY Electronics and Hobbyist Projects
For the DIY electronics community, copper clad boards are a staple. They provide an accessible medium for individuals to create their own electronic projects, ranging from simple circuits to more complex microcontroller-based systems. The ability to etch custom circuits at home makes them extremely popular. - Mass Production of Electronic Products
Copper clad boards form the backbone of mass-produced electronics. They are used in everything from smartphones and computers to automotive electronics and medical devices. The reliability and ease of mass fabrication make them a cost-effective choice for high-volume manufacturing. - Educational Purposes
Educational institutions use copper clad boards to teach electronics and circuit design to students. The hands-on experience of designing and creating PCBs on these boards is invaluable in illustrating electronic theory and practical application. - Aerospace and Defense
In the demanding aerospace and defense sectors, copper clad boards are used for their reliability and performance. They are found in communication systems, navigation equipment, and control circuitry, where robustness and precision are critical. - Medical Devices
Medical equipment heavily relies on copper clad PCBs, where stability and signal integrity are paramount. They are used in diagnostic tools, therapeutic devices, and patient monitoring systems. The boards need to meet stringent quality standards to ensure patient safety and device reliability.
The widespread adoption of copper clad boards stems from their fundamental role in creating functional electronic systems and facilitating innovation across countless industries. Their adaptability allows them to be utilized in a plethora of applications, meeting the diverse needs of both individual creators and large-scale manufacturers.
How to Work with Copper Clad Boards: Etching Techniques
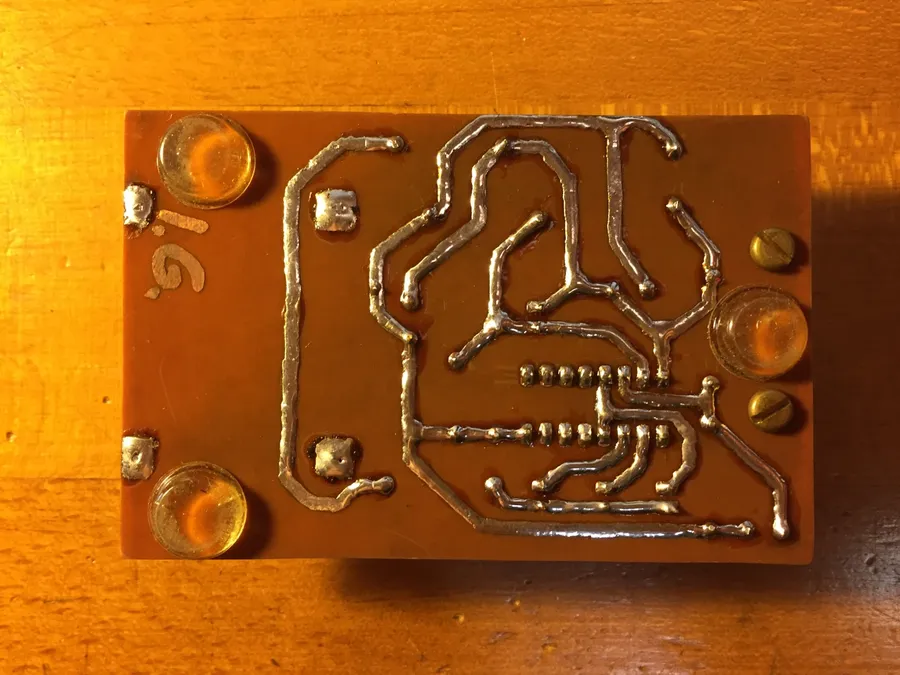
Etching is a critical process in creating custom Printed Circuit Boards (PCBs) from copper clad boards. It involves selectively removing copper from the board, leaving behind the desired circuit traces. This process requires careful planning and execution to achieve accurate and reliable results.
The etching process typically involves several key steps:
- Design and Transfer
First, the desired circuit layout is designed using PCB design software. This design is then transferred onto the copper clad board using a resist material. - Applying the Resist
A resist material, which is resistant to the etchant, is applied to the copper surface. Common resist materials include photoresist (applied with UV light exposure), toner transfer (using a laser printer), or permanent marker. The resist protects the copper that is to remain as the final circuit. - Etching
The board is then immersed in an etchant solution, which chemically removes the unprotected copper. Commonly used etchants include ferric chloride or ammonium persulfate. The etching process needs to be monitored carefully, it is necessary to avoid over-etching which can damage the desired copper tracks. - Resist Removal
After etching, the resist material is removed, revealing the finished PCB with the copper traces corresponding to the designed circuit. - Cleaning and Inspection
Finally, the etched PCB is thoroughly cleaned to remove any residual etchant and resist and visually inspected for any defects.
Safety Precautions are critical when working with etchants, as these chemicals are corrosive and can cause burns or irritation. Always wear appropriate personal protective equipment, including gloves, eye protection, and a lab coat or apron. Ensure proper ventilation is used when etching, as fumes can be harmful. Dispose of used etchant solutions appropriately, according to local regulations.
Etchant Type | Description | Advantages | Disadvantages | Typical Usage |
---|---|---|---|---|
Ferric Chloride (FeCl3) | A common etchant, usually supplied as a solid and mixed with water. Turns copper into soluble copper chloride | Relatively inexpensive, easy to use, works at room temperature, long shelf life | Stains easily, etches relatively slowly, solution is opaque making it difficult to see the etching process, highly corrosive, produces corrosive waste. | Home etching, educational purposes, small scale projects. |
Ammonium Persulfate ((NH4)2S2O8) | An alternative etchant which is also mixed with water. Copper is dissolved as a copper sulfate salt. | Clear solution enables real time visual observation, Fast etching rate, less prone to staining. | More expensive than ferric chloride, produces a less stable solution with limited shelf life, can be temperature dependent. | High precision or rapid prototyping, applications where visibility is important, professional production. |
Frequently Asked Questions About Copper Clad Boards
This section addresses common questions regarding copper clad boards, providing clear and concise answers to aid understanding and decision-making.
- What exactly is a copper clad board?
A copper clad board is a foundational material in electronics, comprising a base substrate, typically made of materials like FR-4, that is coated with a thin layer of copper foil on one or both sides. This copper layer provides a conductive surface for creating electrical circuits by etching away the unwanted copper, leaving behind the desired conductive traces. - What are the primary disadvantages of using copper cladding?
While essential, copper cladding does have some limitations. Its primary disadvantages include susceptibility to oxidation and corrosion if not properly treated or protected, and the process of etching the copper can be complex and generate environmentally damaging byproducts if not handled responsibly. - What are the typical applications of copper clad boards?
Copper clad boards are widely used in electronics for creating printed circuit boards (PCBs). They are essential for everything from simple DIY electronics projects and prototyping to large-scale production of consumer electronics, industrial equipment, and automotive systems. - Is 'copper clad' the same as 'copper bonded'?
The terms 'copper clad' and 'copper bonded' can be related but not always identical. 'Copper clad' specifically refers to a substrate with a layer of copper foil attached via a cladding process. 'Copper bonded' can sometimes be used more broadly, possibly referring to processes like diffusion bonding where the copper layer is fused directly to another material. In most contexts related to PCBs, 'copper clad' is the more appropriate and accurate term. - How do I choose the right copper clad board for my project?
Choosing the right copper clad board involves several considerations. You need to consider the application, the complexity of the circuit, the power requirements, and environmental factors. Specific factors include: material type (FR-4, CEM-1 etc.), copper thickness (measured in ounces), single or double-sided, overall board size, and budget constraints. High-frequency applications may require specialized substrate materials. - Can I reuse copper clad boards after etching?
Generally, once a copper clad board has been etched, it's not reusable for creating a new circuit. This is because the copper is removed irreversibly by the etching process, and the remaining traces are specific to the initial circuit design. However, some waste copper can be reclaimed and recycled. - What is the typical shelf life of copper clad boards?
Copper clad boards do not have a hard expiration date, but they should be stored correctly to avoid oxidation of the copper. They should be stored in a dry and low humidity environment, and away from direct sunlight, high temperatures and any corrosive fumes. Proper storage will ensure the copper surface remains conductive and easy to etch for future use.
Selecting the Right Copper Clad Board: A Buyer's Guide
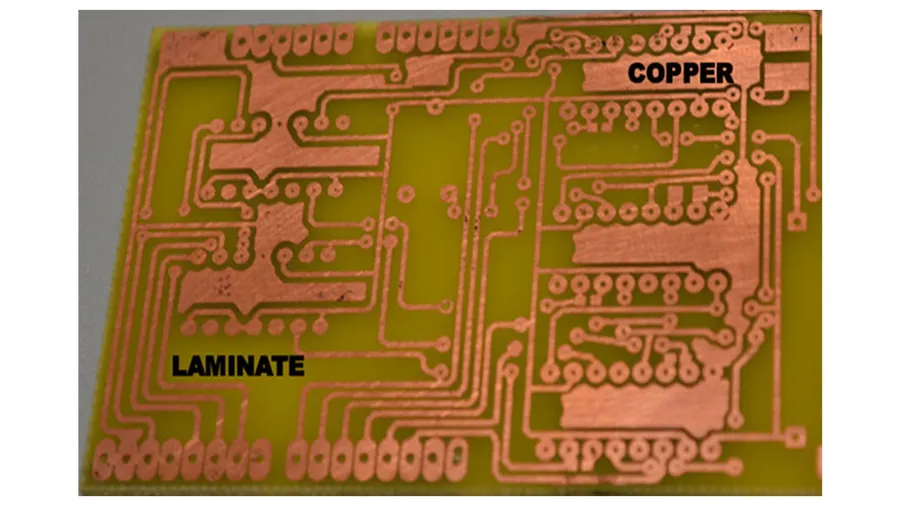
Choosing the correct copper clad board is crucial for the success of any electronics project, whether it's a simple prototype or a complex commercial product. The selection process involves balancing several critical factors: size, material, copper thickness, and budget. A systematic approach to these considerations ensures optimal performance and cost-effectiveness.
- Assess Project Requirements
Begin by defining the specific needs of your project. Consider the circuit complexity, operating environment, current-carrying capacity requirements, and the physical space available. Clear requirements will guide your material and parameter choices. - Size and Dimensions
Determine the necessary dimensions of the copper clad board based on the circuit layout and components. Common sizes are readily available, but custom sizes might be required for unique projects. Ensure the board is large enough to accommodate all components with adequate spacing. - Base Material Selection
Choose the appropriate base material (e.g., FR-4, CEM-1, phenolic). FR-4 is a versatile choice offering a good balance of properties, suitable for most applications. CEM-1 is more cost-effective but offers less fire resistance and mechanical strength. Phenolic is the least expensive, but has lower performance characteristics, and is best suited for very simple low-cost applications. The base material choice directly affects cost, durability, and operating temperatures. - Copper Thickness
Select the appropriate copper thickness, measured in ounces per square foot (oz/ft²). Thicker copper is essential for high-current applications as it reduces resistance and heat generation. Standard thicknesses range from 0.5 oz/ft² to 2 oz/ft² or higher, depending on the load. For lower power designs, a standard 1oz copper is usually sufficient. - Single-Sided, Double-Sided, or Multi-layer
Decide based on circuit complexity. Single-sided boards are suitable for simple circuits, double-sided boards provide more routing flexibility, and multi-layer boards are necessary for complex applications requiring numerous interconnections and signal layers. - Budget Constraints
Balance performance requirements with budgetary restrictions. Cost-effective solutions can often be found by optimizing material choices without compromising functionality, the balance between performance and budget can be managed during the design phase by strategic choices of materials and production methods. - Surface Finish
Consider the surface finish of the copper. Common options include HASL (Hot Air Solder Leveling), ENIG (Electroless Nickel Immersion Gold), and OSP (Organic Solderability Preservative). The finish affects the solderability and corrosion resistance of the board.
By systematically considering these factors, you can make informed decisions that align with your project requirements, leading to more reliable and successful outcomes in your electronics projects.
Copper clad boards are indispensable components in the world of electronics, from simple DIY projects to advanced industrial applications. Understanding their types, materials, and proper handling techniques is crucial for anyone involved in electronics design and development. We've covered a wide range of topics, from the fundamentals of the copper clad board structure to practical etching methods and selection criteria. The ongoing advancements in material science and manufacturing promise further innovations in this field. Armed with this knowledge, you're better equipped to navigate the world of copper clad boards and bring your electronic ideas to life.
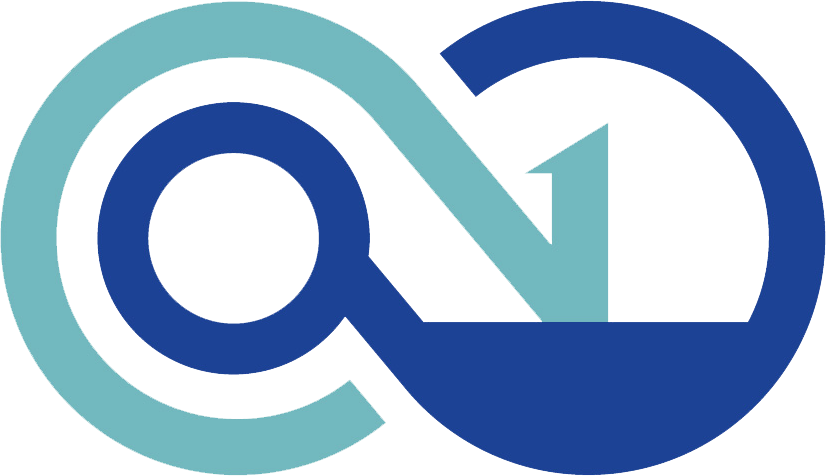