Understanding Printed Circuit Boards: A Comprehensive Guide
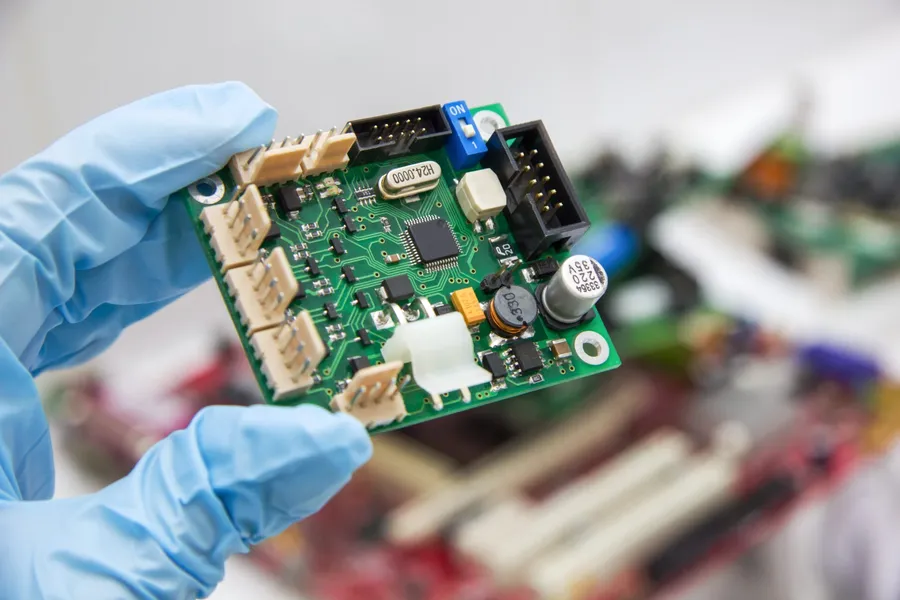
In our increasingly digital world, printed circuit boards (PCBs) are the unsung heroes enabling the functionality of almost every electronic device we use daily. From smartphones and computers to medical equipment and industrial machinery, these intricate boards are the foundation upon which modern technology is built. This article explores the core concepts of PCBs, guiding you through their definition, composition, design, and real-world applications, offering a solid understanding of this critical component in the realm of electronics.
What is a Printed Circuit Board (PCB)?
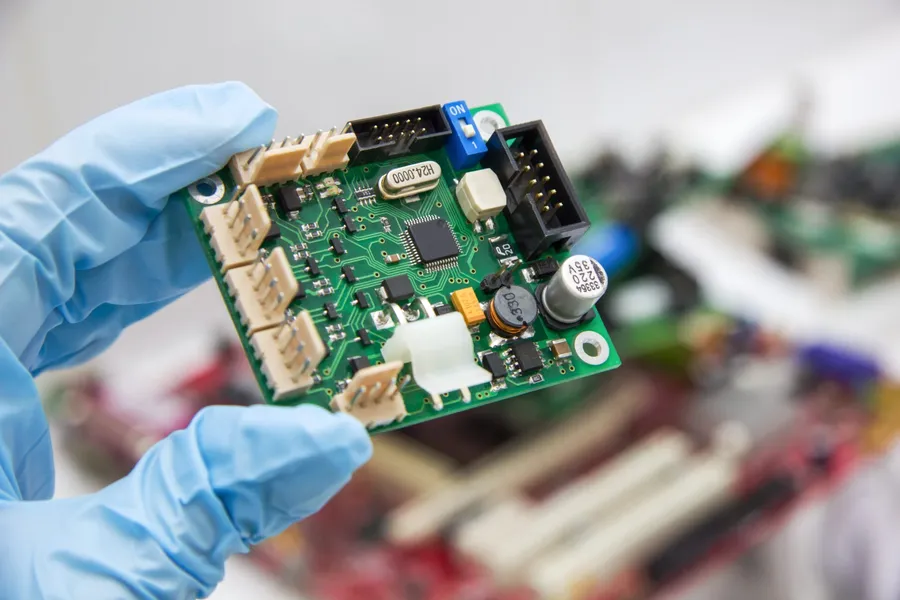
A Printed Circuit Board (PCB) serves as the foundational platform for electronic components, providing both the necessary mechanical support and the intricate electrical connections required for a functional electronic device. Essentially, it's the 'backbone' of nearly every modern electronic device, ensuring components are correctly interconnected to perform their designated tasks.
The basic structure of a PCB comprises a substrate material, which is typically a non-conductive base, and conductive pathways, generally made of copper, that form the electrical circuit. The substrate provides the mechanical structure, while the copper traces etched onto it enable the flow of electrical signals between components.
Key Materials Used in PCB Fabrication
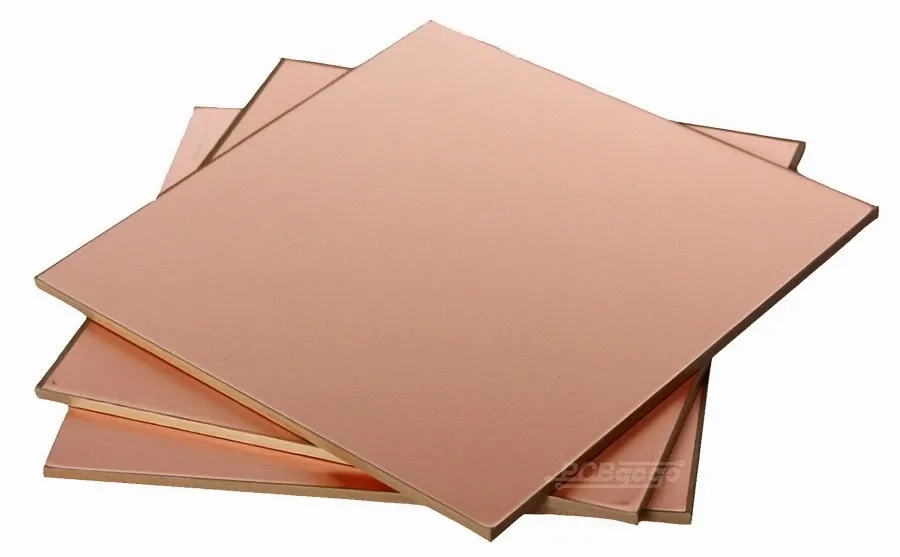
The performance and reliability of a printed circuit board (PCB) are significantly influenced by the materials used in its fabrication. These materials provide the necessary mechanical support, electrical insulation, and conductive pathways for electronic components to function correctly. The selection of these materials is critical and depends on the intended application, operating environment, and cost considerations.
Material | Description | Key Properties | Typical Applications |
---|---|---|---|
FR-4 | A composite material made from woven fiberglass cloth with an epoxy resin binder. | Good electrical insulation, high strength-to-weight ratio, flame retardant, cost-effective. | Most general purpose PCBs, common in consumer electronics and industrial applications. |
Metal Core (Aluminum/Copper) | Metal substrate with a dielectric layer and copper circuitry. | Excellent thermal conductivity, good mechanical strength. | LED lighting, power electronics, applications requiring efficient heat dissipation. |
Rigid-Flex Materials | Combination of rigid and flexible materials, typically polyimide or polyester based. | High flexibility, can withstand repeated bending, high-density interconnections. | Aerospace, medical devices, portable electronics, applications that require complex 3D shapes. |
High-Frequency Laminates (e.g., PTFE) | Laminates with low dielectric constant and loss tangent, commonly Polytetrafluoroethylene (PTFE) based. | Excellent signal integrity, low loss at high frequencies, stable performance over temperature. | RF circuits, microwave communication, high-speed digital applications. |
Beyond the substrate, copper is the most common conductive material used to create traces and pads on a PCB. It is preferred for its excellent conductivity and relatively low cost. Other conductive materials, such as gold or nickel, are sometimes used for plating to enhance the conductivity, solderability, and corrosion resistance of the copper.
Types of Printed Circuit Boards
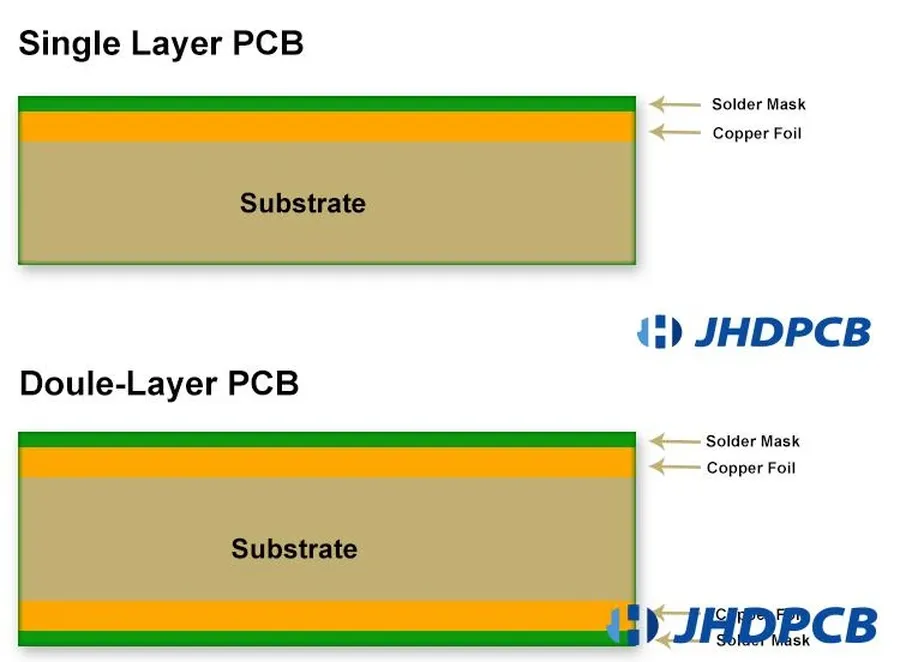
Printed circuit boards (PCBs) are categorized based on their layer count, construction, and specific application needs. The choice of PCB type significantly impacts the functionality, cost, and complexity of electronic devices.
PCB Type | Description | Applications | Advantages | Disadvantages |
---|---|---|---|---|
Single-Layer PCB | Contains conductive material on only one side of the substrate. | Simple electronics, basic circuits, lighting, low-cost devices. | Low cost, easy to manufacture, suitable for simple designs. | Limited component density, not suitable for complex circuits. |
Double-Layer PCB | Has conductive material on both sides of the substrate. | Power supplies, basic audio circuits, industrial control, most common type. | Higher circuit density than single-layer, more complex circuits possible. | Still limited in density compared to multilayer, less effective with high speed signals. |
Multilayer PCB | Features three or more layers of conductive material within the board. | High-end computers, servers, advanced medical equipment, complex signal processing. | Very high density, capable of complex designs, excellent signal integrity. | Expensive, complex to manufacture, longer lead times. |
Flexible PCB | Constructed on a flexible substrate, allowing it to bend and flex. | Wearable devices, automotive applications, printers, camera lens systems. | Flexible, lightweight, can fit into tight spaces, vibration resistance. | More expensive than rigid boards, potential for tearing or damage. |
Rigid-Flex PCB | Combines flexible circuits with rigid board sections. | Aerospace, military, medical equipment, high-end electronics. | Combines advantages of both rigid and flex boards, enhanced reliability. | Complex to design and manufacture, higher cost than rigid or flexible PCBs alone. |
HDI PCB | High-Density Interconnect PCB featuring very fine lines and vias. | Smartphones, tablets, high-performance computing, complex integrated circuits. | Extremely high density, suitable for miniaturized devices, better signal integrity. | More expensive, requires specialized manufacturing processes. |
Metal Core PCB | Features a metal core (typically aluminum or copper) for heat dissipation. | LED lighting, power electronics, high power equipment, high temperature applications. | Excellent thermal management, good mechanical stability. | Can be heavier, potentially more expensive, different manufacturing needs. |
The PCB Design Process
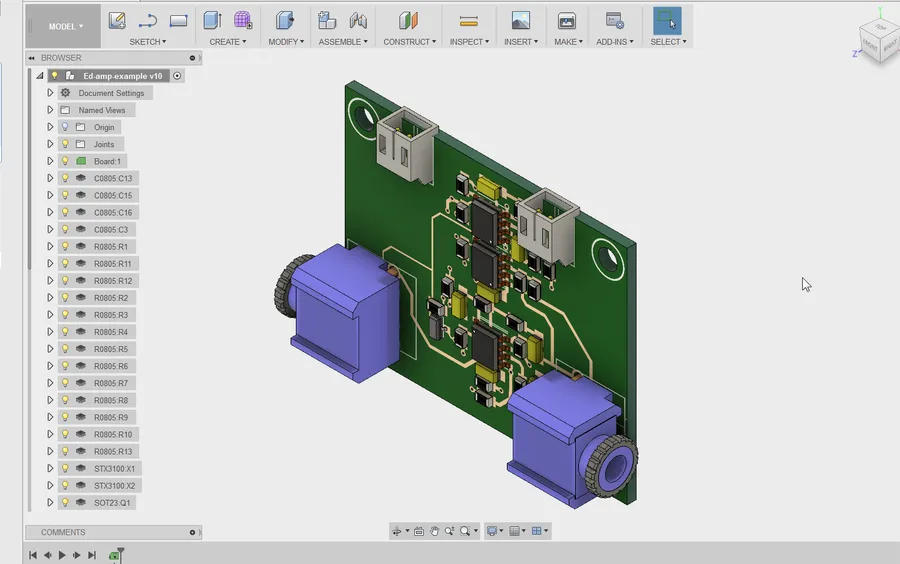
The design of a printed circuit board (PCB) is a multi-stage process that transforms an abstract electronic circuit into a physical reality. It involves converting a schematic diagram into a functional board layout using Electronic Design Automation (EDA) tools, requiring meticulous attention to electrical, thermal, and mechanical aspects.
- Schematic Capture
The initial phase involves creating a schematic diagram that depicts the electrical connections and components of the circuit. This is typically done using EDA software, where components are selected from a library and wired together virtually. This step ensures a functional circuit before any physical layout is considered. Accuracy in this phase is critical to avoid design flaws. - PCB Layout
Once the schematic is complete, the next step is translating it into a physical board layout. This involves placing components, routing traces, and creating ground planes on the PCB. The layout must adhere to design rules to maintain signal integrity and manage thermal dissipation. Considerations include minimizing trace lengths, controlling impedance, and properly spacing components. EDA tools help optimize component placement for thermal and signal performance. - Design Rule Check (DRC)
After the layout is finalized, a thorough design rule check (DRC) is performed to ensure that the board meets manufacturing specifications and electrical requirements. This involves verifying trace widths and clearances, proper pad connections, and adherence to material constraints. Errors identified during the DRC are corrected before moving forward, ensuring the final product can be produced without issue and will function correctly. - Gerber File Generation
The final design output is a set of Gerber files, which provide instructions to the PCB manufacturer. These files detail the copper layers, solder mask, silkscreen, and drill locations. Accurate Gerber files are crucial for manufacturing, so they are usually verified for any missing information or errors before the project moves on to the fabrication stage. - Design Considerations
Effective PCB design requires careful consideration of signal integrity, impedance matching, and thermal management. Signal integrity ensures that signals are transmitted clearly without degradation, while impedance matching minimizes reflections that can cause signal loss. Thermal management prevents overheating and component failure by efficiently dissipating heat. Ignoring these considerations can result in unreliable performance or even failure of the final electronic product.
PCB Manufacturing Overview
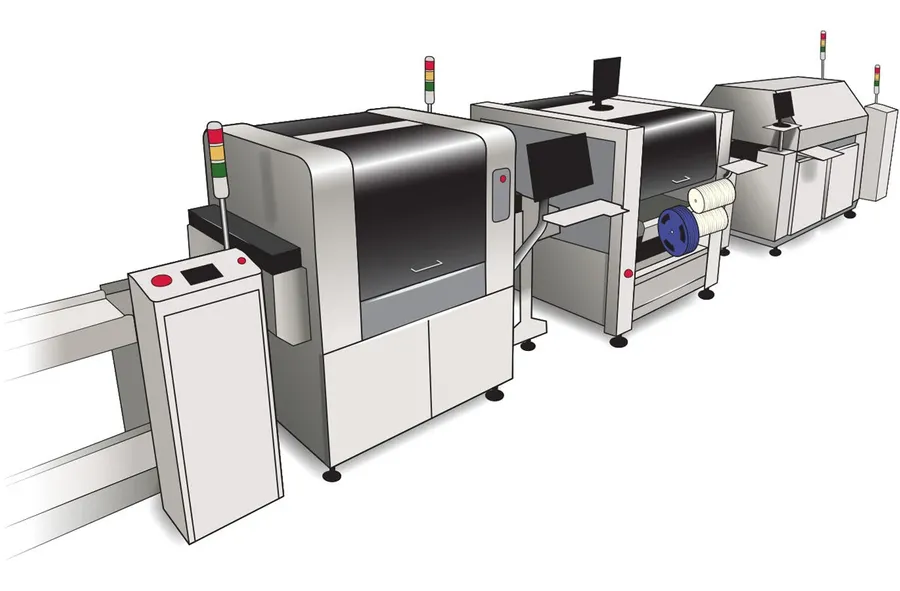
The fabrication of printed circuit boards (PCBs) is a complex, multi-stage process that transforms a digital design into a physical substrate that provides both mechanical support and electrical connections for electronic components. This process includes creating conductive pathways, known as traces, and pads for component attachment, as well as drilling holes for component leads and vias, and applying a solder mask and silkscreen for protection and identification.
The PCB manufacturing process can vary depending on the type of board being produced, the complexity of the design, and the volume of production. However, the core steps remain consistent across most manufacturing methods. Below, we delve into the various stages and highlight the advantages and disadvantages of different approaches.
Manufacturing Step | Description | Methods | Advantages | Disadvantages |
---|---|---|---|---|
Material Preparation | Cutting the base material (e.g., FR-4) into the required panel sizes. | Shearing, Sawing | Precise cutting, fast | May create rough edges if not careful |
Inner Layer Imaging | Transferring the circuit pattern to copper clad laminate using a photo-imaging process. | Photolithography | High precision | Multi-stage process |
Etching | Removing the unwanted copper, leaving only the conductive traces and pads. | Chemical etching | Efficient for large-scale production | Requires careful handling of chemicals |
Layer Alignment and Lamination | Stacking the etched layers with prepreg (an adhesive layer) and pressing under heat and pressure to create the multilayer PCB. | Hydraulic Press Lamination | Ensures strong layer adhesion | Can be time-consuming for thick boards |
Drilling | Creating holes for component leads, vias (interlayer connections), and mounting. | CNC drilling, Laser drilling | High precision drilling, automation | Requires specialized equipment |
Plating | Applying copper, and other metals to the inner walls of the drilled holes to establish electrical connection between layers. | Electrolytic Plating | Good electrical conductivity | Can be costly |
Outer Layer Imaging and Etching | Transferring the final circuit pattern to the outer layer using photo-imaging and etching. | Photolithography | High resolution pattern transfer | Needs specific chemicals |
Solder Mask Application | Applying a solder mask to protect the traces and pads from oxidation and prevent solder bridging during assembly. | Screen printing, photo-imaging | Protects board from damage | Needs precise alignment |
Silkscreen Printing | Printing component labels, logos, and other identifiers on the PCB surface. | Screen printing, inkjet printing | Good visibility, cost-effective | Limited resolution |
Surface Finish | Applying a protective finish to the exposed copper to prevent oxidation, improve solderability, and protect the material. | ENIG, HASL, Immersion Silver, OSP | Good solderability and protection | Each has different characteristics in cost, protection, and processing. |
Electrical Test | Testing the PCB to ensure the electrical connections are accurate and functional using in-circuit testing or flying probe testing. | Automated Optical Inspection (AOI), in-circuit testing (ICT) | Identifies manufacturing defects | Expensive equipment |
Profiling and Separation | Cutting individual PCBs from the panel. | Routing, v-scoring | Provides dimensionally accurate board | May introduce stress |
The choice of manufacturing methods depends on factors such as the quantity needed, cost constraints, and design complexity. For example, high-volume production often uses automated processes, while low-volume prototyping may employ more manual techniques. Choosing the right method can optimize both the quality and the cost-effectiveness of PCB production.
Frequently Asked Questions about Printed Circuit Boards
This section addresses common questions regarding printed circuit boards (PCBs), providing clear and concise answers to enhance understanding of their function, limitations, and applications. We aim to clarify frequently encountered queries, drawing on established engineering principles and industry best practices.
- What is the fundamental purpose of a printed circuit board (PCB)?
A PCB serves as the foundational platform for electronic components, providing both mechanical support and electrical connections. It replaces traditional point-to-point wiring, offering a structured and efficient method for connecting components. - How does a PCB differ from a motherboard?
While both PCBs and motherboards are circuit boards, a motherboard is a specific type of PCB, typically the main circuit board in a computer or other complex electronic device. A motherboard incorporates numerous additional features like expansion slots, chipset and various interfaces that a general PCB doesn't typically possess. A PCB in comparison is more general in its application, being used in a wide array of different electronic devices with various complexity. - What factors can lead to the failure of PCBs?
PCB failure can result from various factors, including thermal stress leading to solder joint fatigue, excessive electrical current causing trace damage, physical damage from impact or vibration, and environmental factors like moisture and corrosion. Additionally, poor design choices, such as inadequate thermal management or insufficient spacing between traces, can also contribute to failures. - What are the primary types of printed circuit boards?
The most common types of PCBs are single-layer, double-layer, and multilayer boards. Single-layer PCBs have conductive traces on one side, while double-layer PCBs have traces on both sides. Multilayer PCBs incorporate multiple layers of traces, separated by insulating material, enabling more complex circuits within a smaller area. Additionally, there are specialized types like flexible PCBs (flex PCBs), rigid-flex PCBs (combination of rigid and flex), and high-density interconnect PCBs (HDI PCBs) for more specific applications. - Are PCBs repairable, and if so, to what extent?
The repairability of a PCB depends on the nature and severity of the damage. Minor issues such as broken solder joints or faulty components can often be repaired by skilled technicians. However, severe damage to the PCB substrate, trace corrosion, or multi-layer delamination can make repairs impractical or unfeasible. In some cases, the cost of repairs can exceed the cost of a replacement, especially for low cost boards. - What are some of the most important considerations when designing a PCB?
Key design considerations include signal integrity to minimize interference and maintain signal quality, impedance matching to ensure efficient power transfer, thermal management to prevent overheating and component failures, selecting the appropriate PCB material for intended operating environment, manufacturability to reduce production costs and lead times, and following industry best practices and standards. - What are the typical applications of PCBs in modern technology?
PCBs are essential components in nearly all electronic devices, including consumer electronics like smartphones and laptops, automotive systems like engine control units, medical devices like diagnostic equipment, aerospace systems like navigation and control equipment, and industrial automation systems like programmable logic controllers. Their adaptability makes them an indispensable part of modern technology.
Common Applications of Printed Circuit Boards
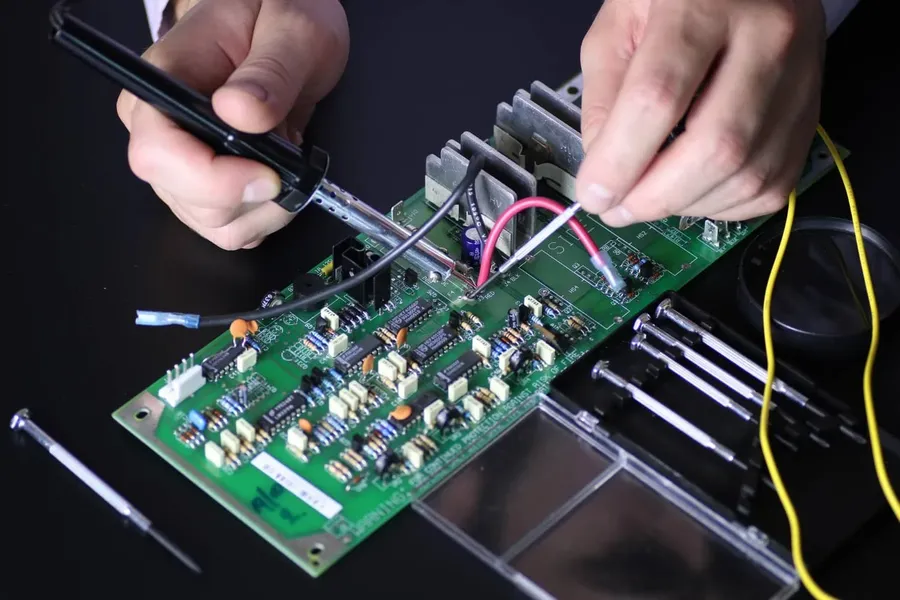
Printed circuit boards (PCBs) are the ubiquitous foundation of modern electronics, facilitating connections and mechanical support for electronic components across a diverse range of applications. Their adaptability and reliability make them indispensable in virtually every industry that utilizes electronic technology.
- Consumer Electronics
PCBs are at the heart of everyday devices such as smartphones, laptops, tablets, televisions, and gaming consoles. They enable the complex circuitry required for these devices to function. - Automotive Electronics
Modern vehicles rely heavily on PCBs for engine control units (ECUs), infotainment systems, advanced driver-assistance systems (ADAS), and other electronic control systems. Their durability and reliability are critical in harsh automotive environments. - Medical Devices
PCBs are essential in medical equipment, ranging from diagnostic tools like MRI and X-ray machines to patient monitoring devices and implantable medical devices. Precision and reliability are paramount in these applications. - Aerospace
In the aerospace industry, PCBs are used in aircraft control systems, navigation systems, communication equipment, and satellite technology, where high reliability and performance under extreme conditions are critical. - Industrial Automation
PCBs are vital in industrial control systems, robotics, automation equipment, and process monitoring. They facilitate precision control and efficient operation of industrial processes. - Telecommunications
From cellular towers to network switches and routers, PCBs are used extensively in all aspects of telecommunications infrastructure, enabling reliable data and voice communication. - Renewable Energy Systems
PCBs play a key role in solar inverters, wind turbine control systems, and other renewable energy technologies, enabling efficient power conversion and distribution.
Future Trends in PCB Technology
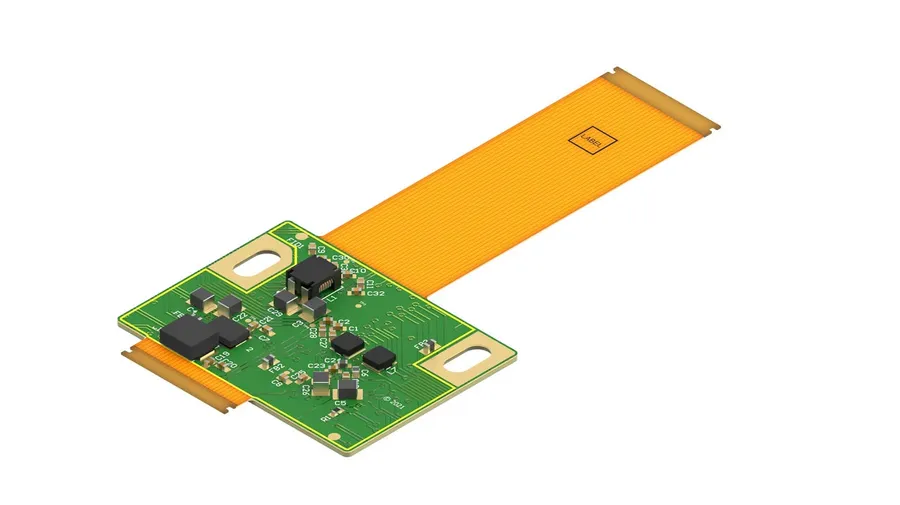
The printed circuit board (PCB) industry is in a state of constant evolution, driven by the increasing demands for smaller, faster, and more efficient electronic devices. This section explores the key trends shaping the future of PCB technology, encompassing advancements in materials, design, and manufacturing processes.
- Advanced Materials
The pursuit of enhanced performance is leading to the exploration of novel materials with superior electrical, thermal, and mechanical properties. This includes research into low-loss dielectrics for high-frequency applications, thermally conductive substrates for efficient heat dissipation, and flexible materials for wearable and bendable electronics. These materials often exhibit improved signal integrity, higher temperature resistance, and reduced signal loss compared to traditional materials like FR-4. - High-Density Interconnect (HDI) Technologies
As electronic devices become more compact, the need for higher circuit density is growing. HDI technologies, characterized by microvias and finer line widths and spacing, enable more components and functionality within a smaller footprint. These technologies are crucial for applications such as smartphones, wearables, and high-performance computing systems. - Flexible and Stretchable Electronics
Flexible and stretchable PCBs are emerging as key components in wearable devices, flexible displays, and biomedical sensors. These PCBs are built on flexible substrates allowing them to bend, twist, or stretch without losing functionality, expanding the design possibilities and application areas for electronics. This is often achieved through the use of flexible polyimides and specialized conductive inks. - Embedded Components
Embedding passive components (resistors, capacitors, inductors) directly within PCB layers not only reduces the board size, but also enhances electrical performance by minimizing parasitic effects. This approach leads to more compact designs, improved signal integrity, and enhanced system performance. It also reduces the number of solder joints and improves reliability. - Additive Manufacturing (3D Printing)
The advent of 3D printing techniques in PCB manufacturing offers the potential for rapid prototyping, customized designs, and on-demand production. Additive manufacturing enables the creation of complex three-dimensional geometries, facilitating integration of mechanical structures and electronic circuits in one single fabrication process. This method has the potential to shorten lead times and reduce manufacturing costs for specialized applications. - Advanced Thermal Management
With increased power density and miniaturization, effective thermal management of PCBs has become critical. Emerging technologies include integrated heat sinks, vapor chambers, and advanced cooling techniques to efficiently dissipate heat from high-power components, ensuring reliable operation and preventing thermal-induced failures.
Printed circuit boards are pivotal to modern electronics, forming the core of almost every device we use. From understanding their material composition and design process to exploring varied applications and future trends, this guide offers a comprehensive overview of PCBs. The continuous innovation in PCB technology will drive forward technological progress, highlighting the importance of this foundational component in the evolution of electronics.
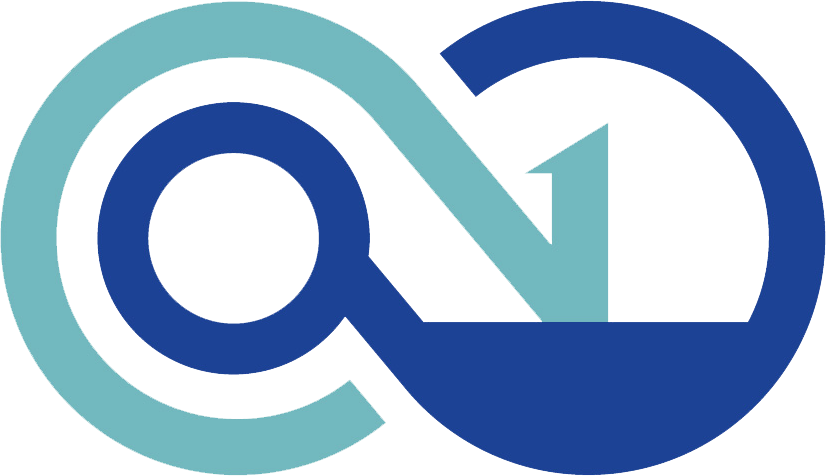