Understanding the Core of Induction: A Deep Dive into Induction Circuit Boards
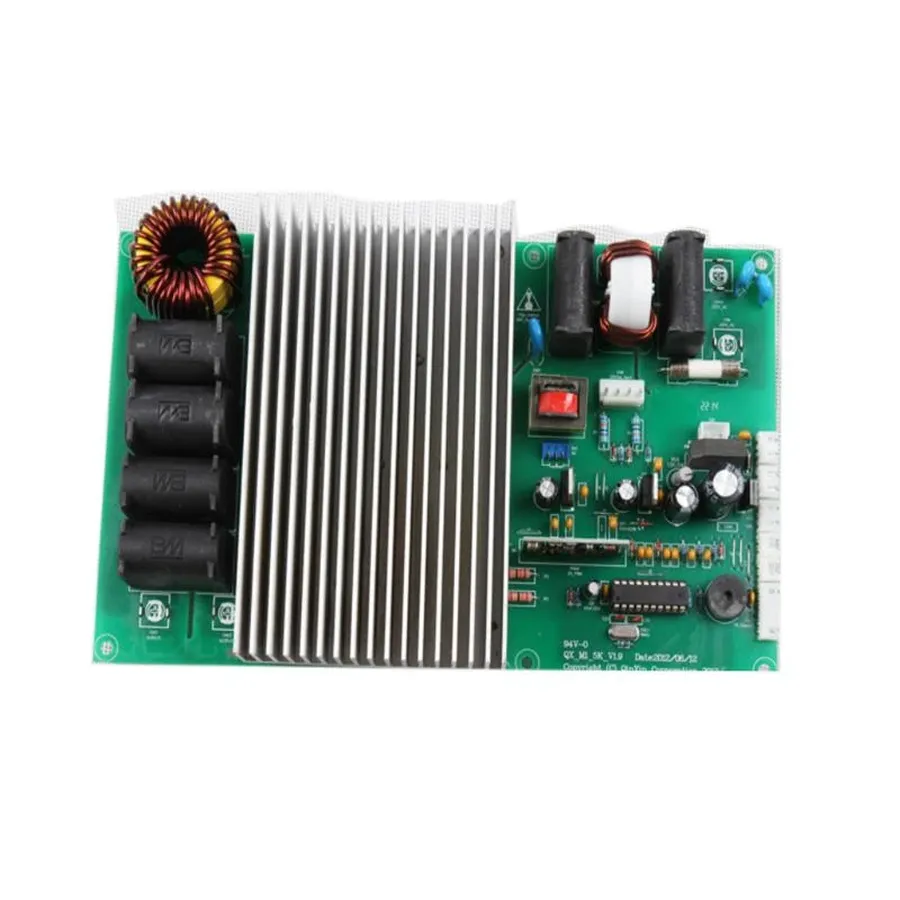
The modern marvel of induction heating, seamlessly integrated into our kitchens and industries, relies heavily on a seemingly simple component: the induction circuit board. This unsung hero is the brain behind the precise and efficient heat generation. From induction cooktops that instantly bring water to a boil to industrial applications that require targeted heating, understanding the mechanics of an induction circuit board not only demystifies the technology but also opens doors to possibilities in its application and maintenance. We'll delve into the inner workings of these boards, examining their functionality and providing troubleshooting tips, all while showcasing the essential role of these powerful electronics.
What is an Induction Circuit Board?
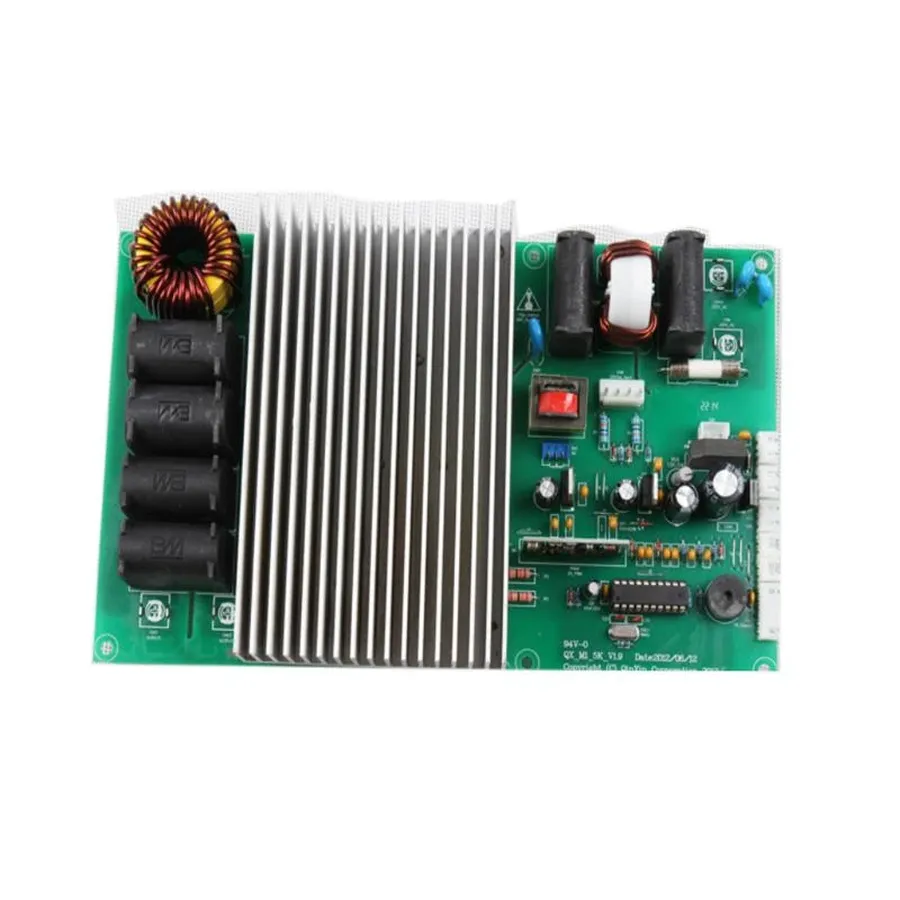
An induction circuit board is the central component in induction heating systems, responsible for converting electrical energy into a high-frequency electromagnetic field. This field, when interacting with ferromagnetic cookware, induces heat directly within the cookware itself, making it the core of an induction cooktop or industrial heater. The board's design is critical for efficient and controlled energy transfer.
The fundamental components of an induction circuit board include a power supply, which converts mains AC power to a suitable DC voltage; an oscillator circuit that generates the high-frequency AC needed for induction; control circuitry that regulates power and temperature; and essential components like capacitors, inductors, and transistors for power switching and shaping the electromagnetic field. These components work together to ensure precise heating performance.
Types of Induction Circuit Boards
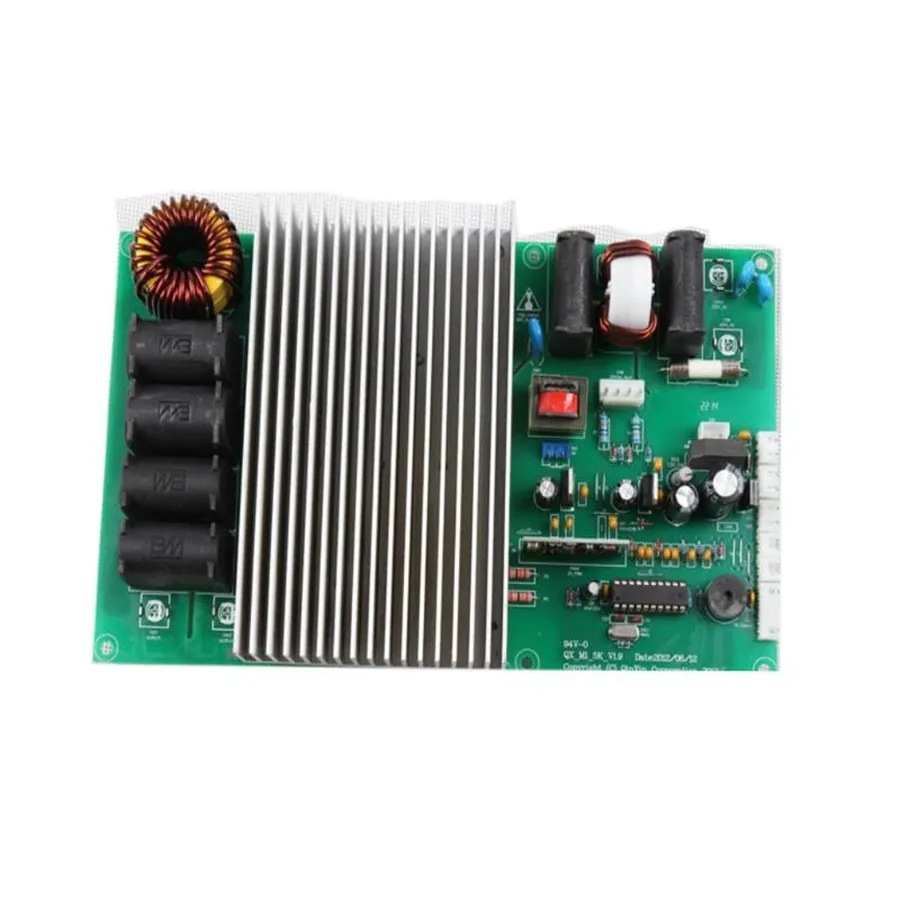
Induction circuit boards vary significantly based on their intended application, primarily differing in power output and control sophistication. These differences directly impact their design, component selection, and overall performance. Understanding these variations is crucial for selecting the appropriate board for specific heating needs, from domestic cooking to demanding industrial processes.
Type | Power Rating | Typical Application | Control Complexity | Key Features |
---|---|---|---|---|
Home Induction Cooktop | 1.5 kW - 3.5 kW (per zone) | Residential cooking, light-duty heating | Moderate | Multiple cooking zones, precise temperature control, timer functions, safety features. |
Commercial Induction Cooktop | 3.5 kW - 7.0 kW (per zone) | Restaurants, catering, professional cooking | Moderate to High | Higher power output, robust construction, continuous operation, enhanced control features |
Industrial Induction Heater | 5 kW - 800+ kW | Metal melting, forging, heat treatment, heavy-duty heating | High | Very high power output, water cooling, precise energy delivery, integrated process control. |
Portable Induction Cooker | 1 kW - 2 kW | Temporary cooking solutions, single person households | Simple | Low power consumption, simple interface, portable design, basic safety features |
The power ratings listed are typical values; actual ratings can vary significantly depending on design and manufacturer specifications. Furthermore, industrial applications often require custom-designed circuit boards with specific control systems, tailored to meet the demands of unique processes, which can go to several Megawatts.
How Does an Induction Circuit Board Function?
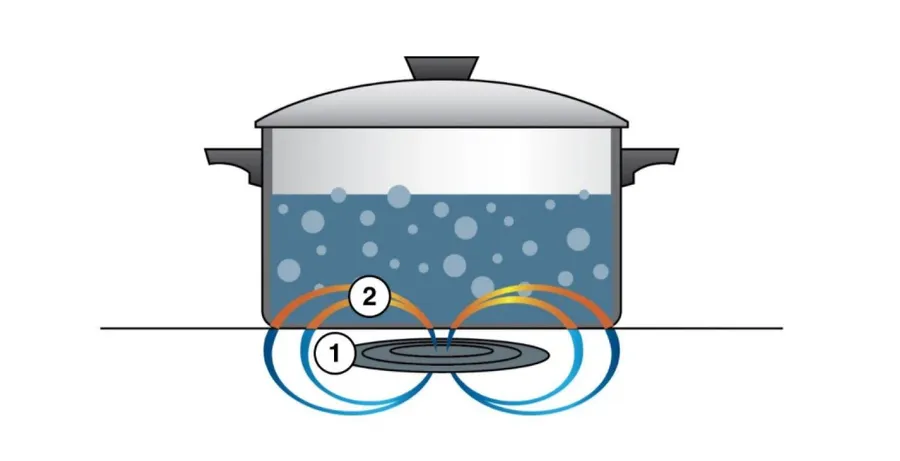
Induction circuit boards operate by transforming electrical energy into a high-frequency alternating magnetic field. This field, when interacting with ferromagnetic cookware, induces eddy currents within the cookware's base, leading to rapid and efficient heat generation. The process is a sophisticated interplay of electrical and magnetic principles, precisely controlled by the circuit board's components.
- Oscillator Circuit
At the heart of the system is an oscillator circuit that generates a high-frequency alternating current. This alternating current is crucial for creating the rapidly changing magnetic field required for induction heating. - Induction Coil
The high-frequency current flows through an induction coil, typically a copper coil, creating a dynamic magnetic field. This coil is strategically positioned beneath the cooktop's surface. - Interaction with Cookware
When ferromagnetic cookware is placed on the cooktop, the magnetic field penetrates the cookware's base, inducing eddy currents. These currents generate heat through the cookware's inherent electrical resistance, resulting in rapid and direct heating. - Feedback Control
Sophisticated feedback circuits monitor the temperature and adjust the power output to maintain a stable cooking temperature. This ensures precise heating and prevents overheating, adding to the overall efficiency and safety of the induction system.
The induction circuit board not only generates the magnetic field but also manages the power delivery and temperature control. Sophisticated feedback loops and control circuitry are integrated to regulate the heating process, ensuring energy efficiency and preventing thermal runaway. This control aspect is crucial for providing consistent and safe cooking.
Common Issues and Troubleshooting for Induction Circuit Boards
Induction circuit boards, while robust, can encounter various issues that impede their functionality. These problems typically manifest as a failure to heat, inconsistent temperature control, or complete system shutdown. Understanding the common failure points and employing systematic troubleshooting steps can often resolve these issues, restoring the induction system to full operation.
The following are common issues that may be encountered:
- Blown Fuses
A common cause of failure is a blown fuse, typically resulting from a power surge or a component failure within the circuit. This is often the first point of failure to check. Replacing a blown fuse with the correct rating is crucial, and if fuses continue to fail, further investigation into the underlying cause is required, as it may indicate a more significant issue such as a short circuit. - Overheating
Overheating is another frequent problem that can stem from insufficient heat dissipation or a faulty component causing excessive heat generation. This can lead to thermal shutdown or permanent damage to the circuit board. Ensure proper ventilation around the induction unit and check for damaged or failing components. Also verify that the heat sinks are properly mounted and free from obstructions. - Power Delivery Failures
Power delivery issues can range from a loose connection to a defective power supply component. These failures will result in the device not powering on or operating erratically. Inspecting all power connections for secure seating, and carefully checking power components using a multimeter for signs of malfunction, can pinpoint the source of the problem. If the power supply is deemed faulty, replacement will likely be necessary, potentially with a matching or compatible component. - Component Malfunctions
A faulty component on the board, such as an IGBT, capacitor, or driver IC, can cause a variety of malfunctions, often characterized by abnormal heating or complete failure of the board. If a specific component is determined to be the source of the issue, it will need to be replaced with an identical or appropriate substitute. Diagnosing a failed component often requires a multimeter and the ability to understand circuit diagrams. - Sensor Failures
Failed sensors can cause issues such as erratic temperature readings or error codes. These sensors may monitor temperature, current, or voltage. Replacement of a faulty sensor is typically the only resolution.
Practical troubleshooting tips:
- Visual Inspection
Begin with a thorough visual inspection. Look for signs of damage, such as burnt components, bulging capacitors, or broken connections. - Use of a Multimeter
Use a multimeter to test continuity, voltage, and resistance across various points on the circuit. This can help pinpoint short circuits, open circuits, or component failures. - Check connections
Ensure all connections are tight and secure. Loose connections can cause intermittent failures or complete power loss. This is particularly important to review on the high-current and high-voltage power leads. - Thermal Management
Verify that the heat sinks are properly mounted and that ventilation is sufficient. Overheating can damage components and should be addressed to ensure optimal performance. - Consult a qualified technician
If troubleshooting proves to be too difficult, or you are not comfortable with electronic repairs, consult a qualified technician.
Induction Circuit Board Design Considerations
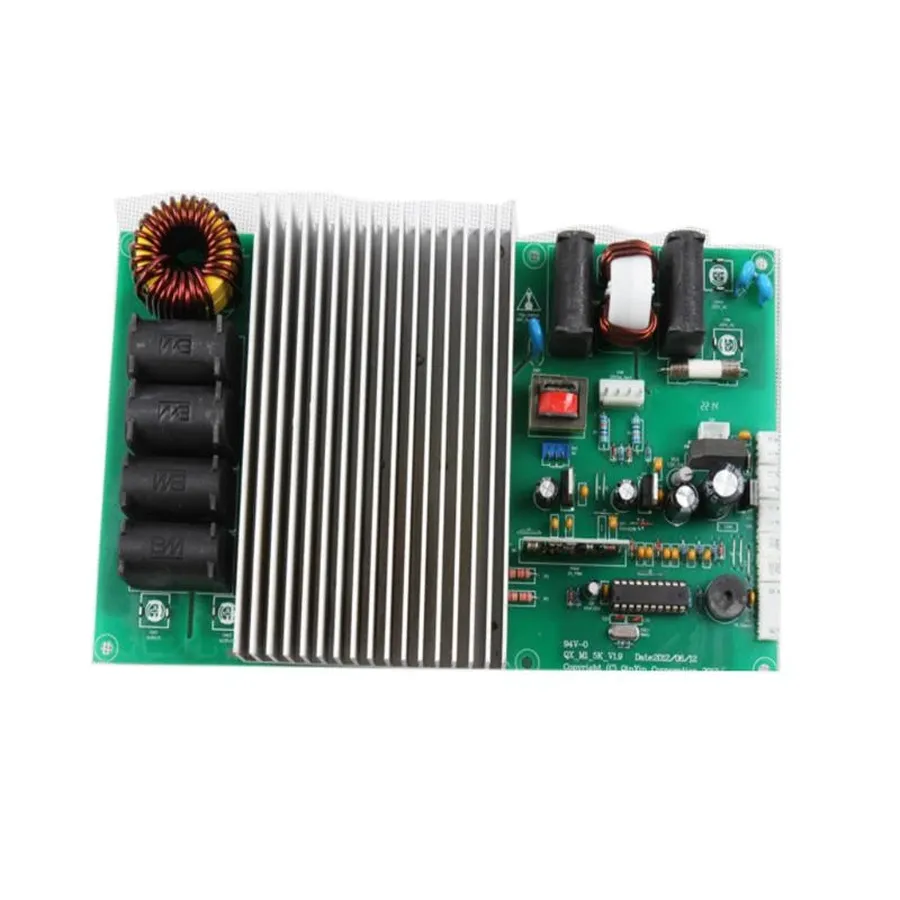
Efficient design of an induction circuit board requires a holistic approach, carefully balancing performance, reliability, and safety. This involves critical considerations such as thermal management to prevent overheating, strategic component selection to ensure optimal power delivery, and the integration of comprehensive safety features, particularly in high-power applications.
Design Consideration | Description | Importance |
---|---|---|
Thermal Management | Effective heat dissipation mechanisms using heat sinks, thermal vias, and airflow designs to prevent component overheating. | Crucial for maintaining component reliability and extending the lifespan of the circuit board. |
Component Selection | Choosing components based on current and voltage ratings, temperature tolerances, and switching speeds, such as high-frequency MOSFETs, gate drivers, and capacitors. | Ensures efficient and reliable power conversion and the correct generation of the high-frequency electromagnetic field. |
Safety Features | Inclusion of overcurrent protection, short circuit protection, overvoltage protection, temperature sensors, and fail-safe mechanisms to prevent damage and hazards. | Vital for protecting the circuit board and connected appliances, as well as preventing potential harm to the user. |
Electromagnetic Interference (EMI) Management | Shielding, filtering, and appropriate layout strategies to minimize electromagnetic emissions to avoid interference with other devices and comply with regulations. | Essential for compliance with electromagnetic compatibility (EMC) standards and ensuring reliable operation of nearby electronic equipment. |
Power Supply Efficiency | Optimization of power supply circuitry to reduce energy losses and improve overall system efficiency. This may include resonant converters or soft-switching techniques to minimize switching losses. | Maximizes energy transfer to the load, reducing heat generation and overall power consumption. |
Induction Circuit Board Maintenance and Longevity
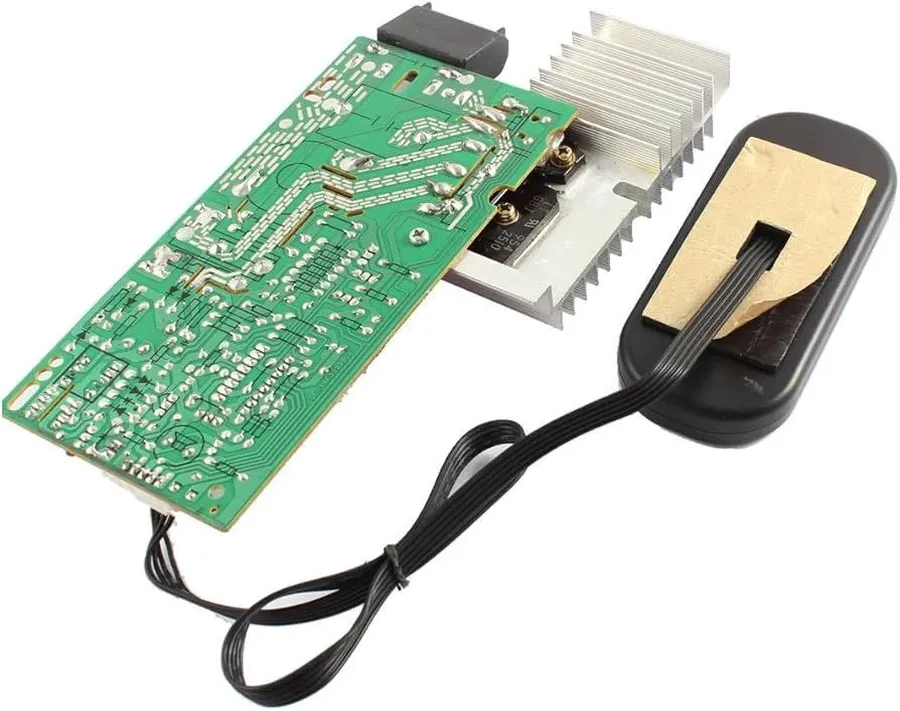
Maintaining the longevity and optimal performance of an induction circuit board is crucial for the reliable operation of your induction heating appliance. Proper care not only extends the lifespan of the circuit board but also ensures efficient and safe heating. This section provides practical advice on maintaining your induction circuit board, ensuring optimal performance, and determining when professional help is necessary.
- Regular Cleaning
Ensure the area around the circuit board and its cooling components is kept free of dust and debris. Use a soft, dry cloth or a brush for cleaning. Avoid using liquids or abrasive cleaners that can damage the board's components. - Proper Ventilation
Ensure adequate airflow around the induction unit. Do not obstruct any vents, as this can lead to overheating of the circuit board and premature failure. Proper ventilation helps maintain the board's operating temperature within safe limits. - Avoiding Overloads
Adhere to the specified power ratings of the induction unit and cookware. Overloading the system can cause excessive current flow and heat generation, potentially damaging components of the circuit board. Using cookware with the proper base material and size is essential. - Using Suitable Cookware
Only use cookware specifically designed for induction cooktops. Incompatible cookware can lead to inefficient heating, overheating of the circuit board, and potential damage. Ensure your cookware base is ferromagnetic and flat to maintain good contact. - Monitoring for Abnormalities
Regularly check for any unusual sounds, smells, or changes in the appliance's performance, such as intermittent heating or error codes. These can be indicators of an issue with the circuit board that needs attention. Addressing these early can help prevent more extensive damage. - Professional Inspections
Schedule periodic inspections by qualified technicians, especially in cases where the induction board is used frequently or in demanding applications. Professional inspections can identify potential problems before they become severe and can also provide preventive maintenance. - Recognizing When to Replace
If you notice recurring issues, performance degradation, or physical damage to the board, it may be time to consider replacement. Trying to fix a significantly damaged board can lead to unsafe operation or further damage to the induction unit. Prioritize replacement when repair is not feasible.
Frequently Asked Questions About Induction Circuit Boards
This section addresses common queries regarding induction circuit boards, providing clear, concise answers to help users understand their function, design, and maintenance. We aim to resolve common misconceptions and provide practical insights based on fundamental engineering principles.
- What type of circuit is required for an induction cooktop?
Induction cooktops require a resonant inverter circuit. This circuit typically uses high-frequency switching transistors to convert standard AC power into high-frequency AC, which is then fed to the induction coil. This design is critical for generating the rapidly changing magnetic field necessary for induction heating. - How does an induction circuit board work?
An induction circuit board works by converting electrical energy into a high-frequency alternating current (AC), which flows through a coil. This current generates a rapidly changing magnetic field. When a ferromagnetic material, such as specific cookware, is placed within this magnetic field, eddy currents are induced within the material, leading to resistive heating directly within the pan. - What is the role of the PCB in an induction circuit board?
The Printed Circuit Board (PCB) serves as the foundation of the induction circuit board, providing a structural base and electrical connections for all the components. It includes conductive tracks for signal and power distribution, and its design is critical for ensuring the efficient operation and thermal management of the entire circuit. - What are the two main types of circuit boards?
The most fundamental types of circuit boards are single-sided and double-sided boards. Single-sided boards have conductive traces on only one side, while double-sided boards have traces on both sides, allowing for more complex circuits and increased component density. Multilayer boards also exist for even more complex applications. - Why do induction cooktops require such high power circuit boards?
Induction cooktops demand high-power circuit boards to rapidly generate the necessary magnetic fields for efficient heating. The power requirements are dictated by the need to induce substantial eddy currents in the cookware, providing quick and efficient heat transfer. - How often should I replace the circuit board in my induction cooktop?
The longevity of an induction circuit board depends on various factors such as usage frequency, operating conditions, and design quality. Under normal circumstances, a well-maintained board can last for many years. However, if problems are frequent or the unit is older than 10 years, preventative replacement may be sensible. - Can I repair an induction circuit board myself?
Repairing an induction circuit board requires specialized knowledge and skills due to its complex components and high voltage operation. Improper handling can pose safety risks and result in further damage. It's typically advisable to seek professional repair services, however, replacing fuses can be a basic repair a user might try.
The Future of Induction Circuit Board Technology
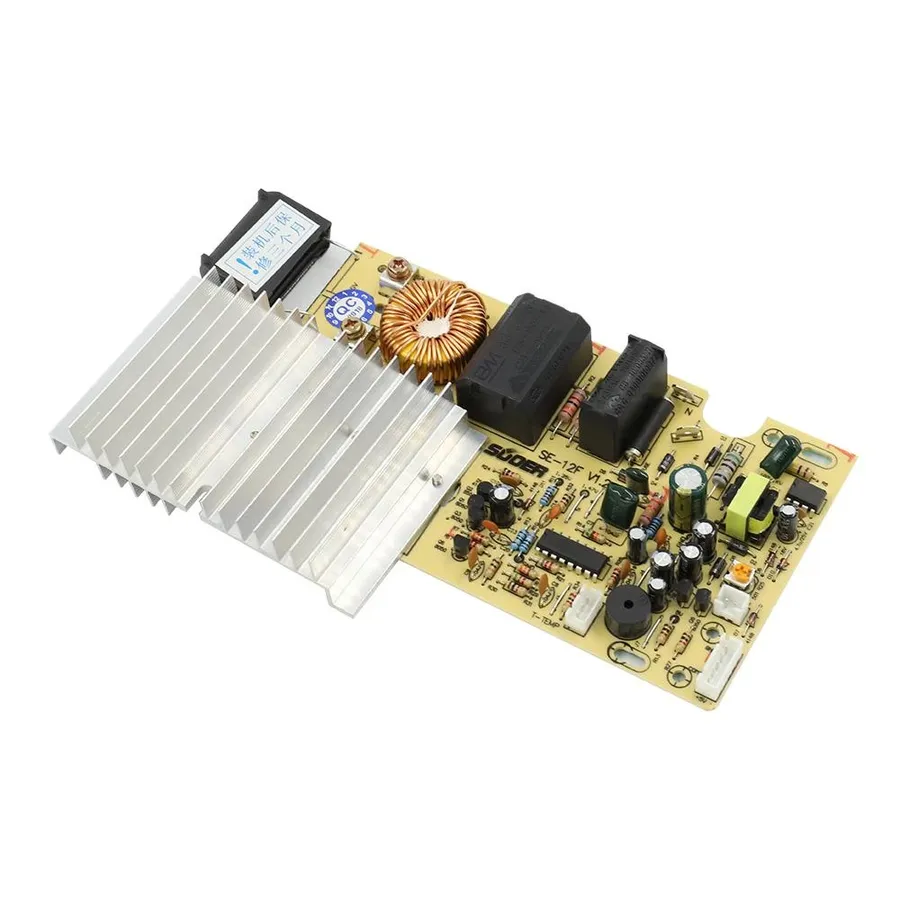
The landscape of induction circuit board technology is rapidly evolving, driven by demands for increased efficiency, greater control, and seamless integration with modern systems. Innovations in materials, component design, and control algorithms are paving the way for the next generation of induction heating solutions.
A significant focus is on enhancing energy efficiency. New circuit designs are incorporating advanced power electronics components, such as wide-bandgap semiconductors (e.g., GaN and SiC), to reduce switching losses and improve overall energy conversion rates. These advancements are crucial for minimizing energy waste and promoting sustainable heating solutions.
Precision control is another key area of development. Modern induction circuit boards are increasingly equipped with sophisticated microcontrollers and digital signal processors (DSPs) to enable more precise temperature management. This allows for fine-tuning of heating profiles, thereby optimizing cooking performance and reducing the risk of overheating or burning food.
Integration with smart home systems is becoming increasingly common, with manufacturers incorporating technologies such as Wi-Fi and Bluetooth to allow for remote control and monitoring. These features enable users to adjust settings from their smartphones or other connected devices. Additionally, some systems are starting to utilize artificial intelligence (AI) algorithms to learn user preferences and automatically adjust heating profiles.
Innovations in materials science are also playing a crucial role. New materials, such as high-temperature ceramics and advanced composites, are being explored for their ability to withstand the demanding conditions within induction cooktops and heaters. These materials offer improved thermal stability, reduced risk of component failure, and longer overall lifespans. Additionally, research is ongoing into the use of nanomaterials to further enhance performance and reduce the size and weight of induction circuit boards.
Looking ahead, we can anticipate further breakthroughs in induction circuit board technology, with increased emphasis on efficiency, safety, and user experience, leading to more sophisticated, versatile, and user-friendly heating solutions.
Comparative Analysis: Induction Circuit Boards vs. Other Heating Technologies
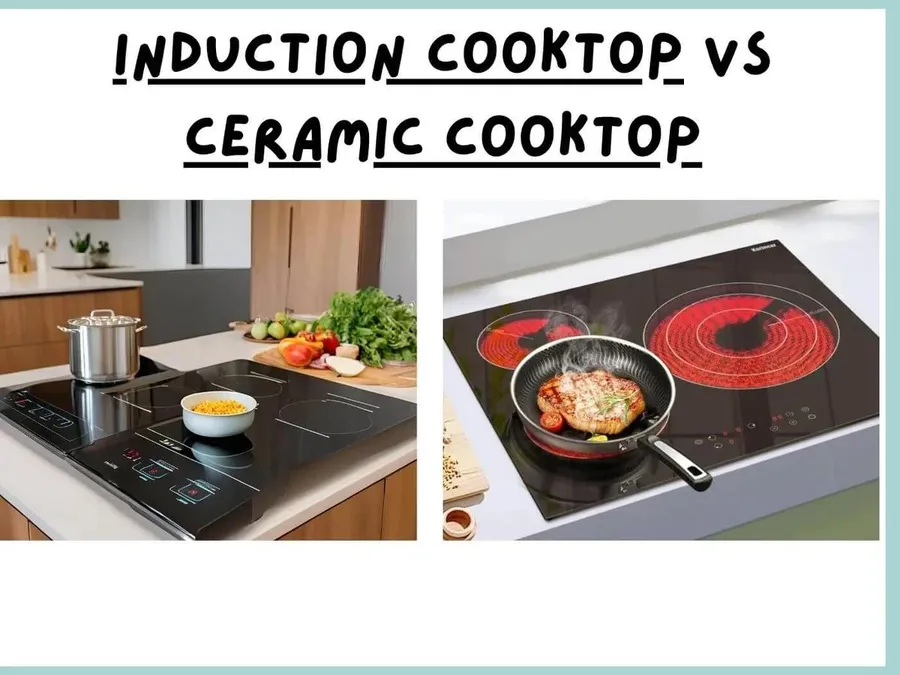
Induction heating, powered by induction circuit boards, presents a distinct alternative to traditional heating methods like gas and electric resistance. This section provides a comparative analysis, focusing on key differences in energy efficiency, safety, and speed, to help users make informed decisions based on their specific needs.
Feature | Induction Heating | Gas Heating | Electric Resistance Heating |
---|---|---|---|
Energy Efficiency | High (85-90%); Direct heating of cookware | Moderate (30-60%); Heat loss to the environment | Moderate (70-80%); Indirect heating of cookware |
Speed | Very Fast; Rapid heating due to direct induction | Moderate; Relies on flame to heat | Moderate; Slower heat up than induction |
Safety | High; Cooktop surface remains relatively cool; reduces the risk of burns | Moderate; Open flame poses a fire risk; gas leaks are a concern | Moderate; Hot surface can cause burns |
Control | Precise; Fine-grained temperature control | Moderate; Difficult to maintain consistent temperature | Moderate to Good; Some precision with controls |
Cost | Higher upfront cost but potentially lower operating costs due to higher efficiency | Lower upfront cost but ongoing gas expenses; higher long term cost | Lower upfront costs; higher energy consumption cost |
Environmental Impact | Lower; Efficient energy usage with no direct emissions | Higher; Contributes to carbon emissions | Moderate; Uses electricity which may be generated from fossil fuels, however cleaner options are also available |
Maintenance | Minimal; Requires cleaning of the smooth cooktop surface | Regular cleaning of burners; potential gas line maintenance | Low; Cleaning of the cooktop surface and coils. |
Choosing the right heating technology depends on specific requirements and constraints. Induction heating, while potentially having a higher initial cost, offers superior energy efficiency and safety, making it ideal for modern kitchens and frequent use. Gas heating, although less efficient and safe, may be favored for its lower upfront costs. Electric resistance heating serves as a middle ground, providing moderate efficiency and safety. By carefully considering these factors, users can select the heating method that best aligns with their unique needs and priorities.
In summary, the induction circuit board represents a remarkable piece of engineering that has revolutionized cooking and heating, and is indispensable in industrial applications. By understanding its fundamental function, various types, common troubleshooting techniques, and future technological advancements, we are better equipped to leverage its capabilities. As we look to the future, the induction circuit board will undoubtedly remain at the forefront of technological innovation, driving further efficiency and convenience for consumers and industry alike. The development of new materials, safety features, and smart integrations of circuit boards will continue to shape our future, further highlighting its role as a pivotal technology. With continued research and development, this technology is likely to become even more indispensable.
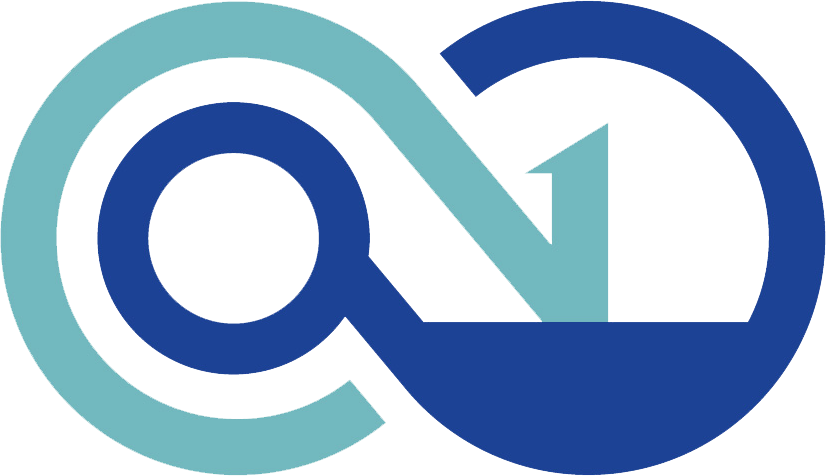