Unveiling the Power of 4-Layer PCBs: Design, Stackup, and Applications
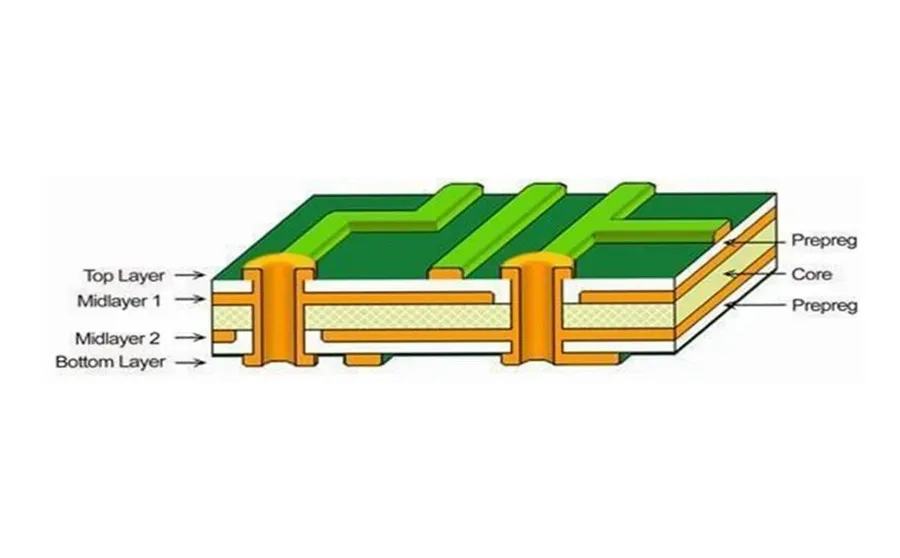
In the intricate dance of electronics, the 4-layer PCB emerges as a versatile workhorse, bridging the gap between simplicity and sophistication. Much like the layers of a carefully crafted cake, a 4-layer PCB balances signal integrity, power distribution, and cost-effectiveness, making it a cornerstone of countless modern devices. This article delves into the heart of 4-layer PCB technology, revealing its construction, design nuances, and the wide array of applications that rely on its capabilities, empowering you to understand and effectively utilize this essential component.
Understanding the Anatomy of a 4-Layer PCB
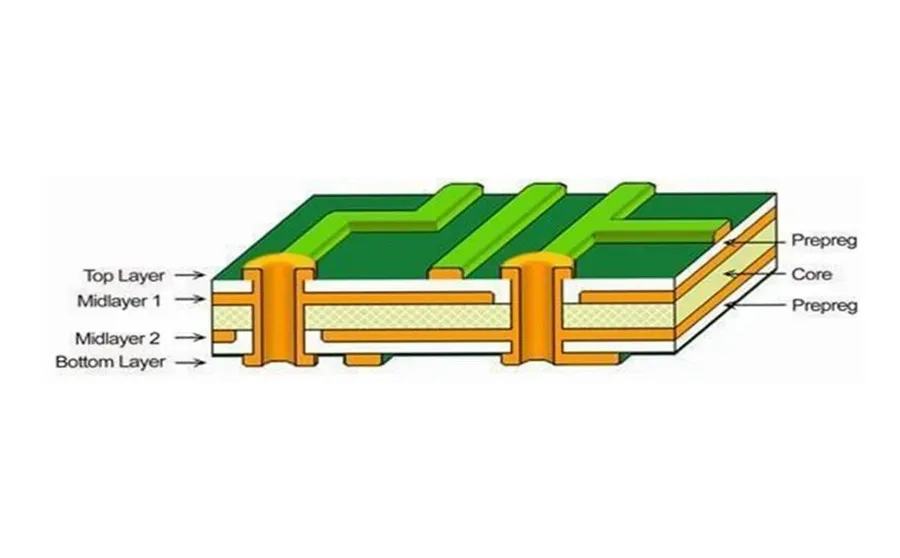
A 4-layer Printed Circuit Board (PCB) is constructed with four distinct layers of conductive material, typically copper, separated by insulating dielectric material. This arrangement provides a balance between complexity and performance, making them suitable for a wide range of electronic applications. Understanding the specific arrangement and purpose of each layer is fundamental to effective PCB design.
In a typical 4-layer PCB stackup, the layers are often allocated as follows: * **Top Layer (Signal Layer):** This outermost layer is used for routing signal traces and placing components. * **Inner Layer 1 (Ground Plane):** This layer serves as a dedicated ground plane, providing a low-impedance return path for signals. This is critical for minimizing signal noise and interference. * **Inner Layer 2 (Power Plane):** This layer acts as a power plane, distributing power to the various components on the board. * **Bottom Layer (Signal Layer):** This outermost layer, similar to the top layer, is also used for routing signals and placing components.
The Crucial Role of Stackup in 4-Layer PCBs
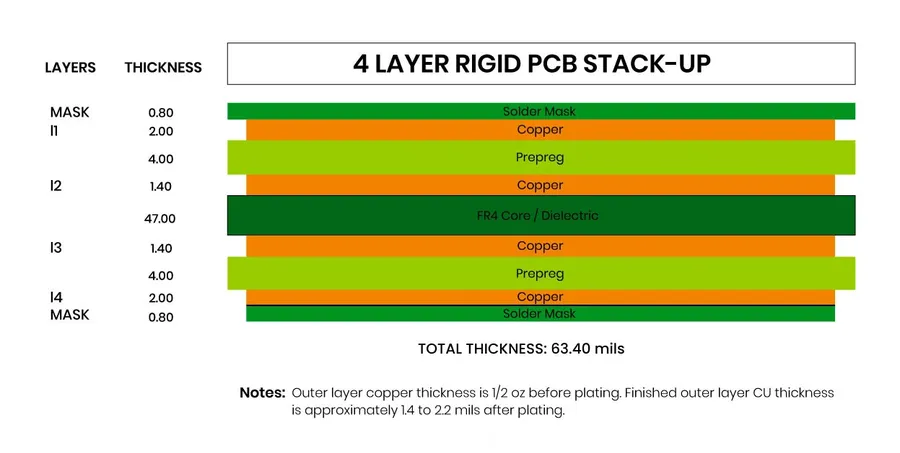
The stackup of a 4-layer PCB is paramount to its overall performance, influencing signal integrity, impedance control, and electromagnetic compatibility (EMC). A well-defined stackup strategically arranges the signal, power, and ground layers to optimize signal transmission and minimize noise.
Common 4-layer PCB stackup configurations typically involve a signal layer on the top and bottom surfaces, with a ground plane and a power plane in the inner layers. This arrangement creates a defined impedance for signal traces, essential for high-speed designs. Variations in stackup might include having two signal layers adjacent or splitting the power plane into multiple voltage rails to reduce the need for multiple power layers. Selecting an appropriate stackup is not arbitrary; it requires a deep understanding of the specific functional and performance requirements of the board, such as signal frequency, power needs, and sensitivity to noise.
Stackup Type | Description | Advantages | Disadvantages | Use Cases |
---|---|---|---|---|
Signal-Ground-Power-Signal | The most common configuration, with two outer signal layers, an inner ground layer, and an inner power layer. | Good impedance control, simplified routing, good noise performance. | Limited routing flexibility on inner layers, less space for power distribution. | General-purpose applications, medium-speed circuits, sensors, data acquisition |
Signal-Power-Ground-Signal | Outer signal layers, followed by a power plane and a ground plane in the middle. | Reduced DC resistance in power distribution, improved power integrity. | May increase overall thickness, slightly more complex routing. | High-power circuits, analog circuits, where power delivery is important. |
Signal-Signal-Ground-Power | Two outer signal layers, followed by inner ground and power layers. | Good for high-speed signal routing on the outer layers, suitable for controlled impedance applications | May result in less effective EM shielding and increased power noise. | High-speed digital circuits where signal integrity is a priority |
The chosen stackup directly impacts the signal integrity by defining the signal path and controlling the impedance. For instance, placing a ground plane close to a signal layer creates a controlled impedance environment, reducing signal reflections and ensuring accurate signal transmission. An incorrect stackup can lead to impedance mismatches, signal reflections, and increased EMI (Electromagnetic Interference), compromising overall system performance. Therefore, a carefully considered stackup is the foundation of a successful 4-layer PCB design.
Optimizing 4-Layer PCB Stackup for Controlled Impedance
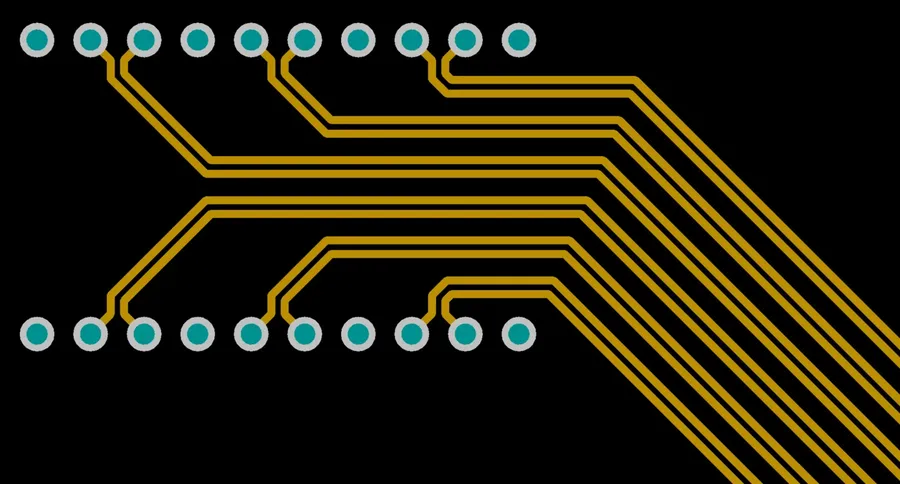
Achieving controlled impedance, particularly the common 50-ohm target, is paramount in 4-layer PCB design to ensure signal integrity and minimize signal reflections. This requires careful consideration of the layer stackup, trace dimensions, and dielectric material properties. A well-designed stackup minimizes impedance variations, resulting in high performance and signal integrity.
Parameter | Description | Impact on Impedance |
---|---|---|
Trace Width | The width of the signal trace on the PCB layer. | Wider traces generally lower impedance. |
Trace Thickness | The thickness of the copper trace. | Thicker traces generally lower impedance. |
Trace Spacing | The distance between signal traces and adjacent ground/power planes. | Closer spacing to ground planes lowers impedance. |
Dielectric Height | The thickness of the dielectric material between layers. | Thinner dielectric material generally lowers impedance. |
Dielectric Constant | A measure of the ability of a material to store electrical energy. | Higher dielectric constant lowers impedance. |
To achieve a 50-ohm impedance, it's necessary to use impedance calculation tools or simulation software. These tools account for the intricate interplay of the parameters mentioned above. A typical microstrip configuration, where a signal trace is on an outer layer with a ground plane beneath it, or a stripline configuration, where a signal trace is embedded between two ground planes, will be used. The choice between these depends on the design and interference factors.
Furthermore, beyond 50-ohm impedance, other specific impedance requirements may exist for certain signals, such as differential pairs. These require meticulous design considerations. Utilizing impedance control techniques during the PCB design phase is essential to ensure that the PCB operates within the required specifications, ensuring consistent signal performance. Impedance control is not just a design feature but an integral part of the fabrication process, where each layer's copper thickness and dielectric separation needs to be consistent to achieve the desired results.
4-Layer PCB Design Guidelines: Essential Tips for Success
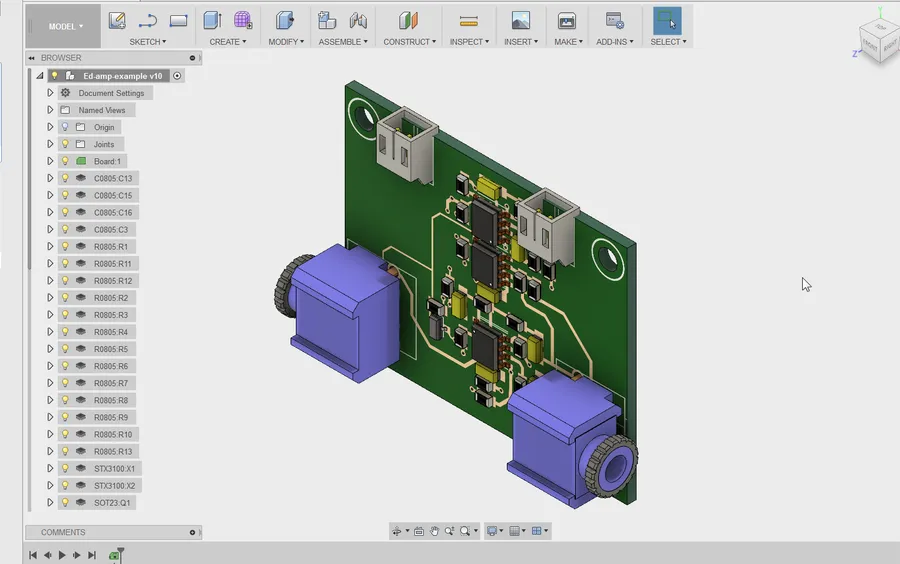
Effective 4-layer PCB design hinges on adherence to key guidelines that ensure both functionality and reliability. These guidelines encompass routing strategies, component placement, and the appropriate use of vias to manage signal integrity, power distribution, and thermal characteristics.
- Strategic Routing
Prioritize signal layer routing. Keep high-speed signals on the top or bottom layers, adjacent to the ground plane, to minimize impedance mismatches. Avoid long parallel traces to mitigate crosstalk. Always strive for the shortest path to reduce signal reflection. - Component Placement
Place critical components on the top layer to facilitate easy access for testing and rework. Group components by function, minimizing track lengths between related elements. Decoupling capacitors should be placed as close as possible to the power pins of integrated circuits, which minimizes impedance and increases system stability. - Via Management
Employ vias judiciously to minimize impedance discontinuities. Use multiple vias for power and ground connections to minimize resistance and inductance. Employ via-in-pad techniques where feasible to conserve routing space and enhance thermal conduction. - Power and Ground Planes
Utilize one of the inner layers as a solid ground plane and another as a power plane. These planes should be as large as possible to minimize impedance and provide adequate current return paths. Make sure to use sufficient decoupling capacitors to minimize noise in the system. - Thermal Considerations
For components that generate significant heat, place them on the outer layers, close to copper pours that act as thermal radiators. Consider using thermal vias connected to heat sinks on the backside for efficient heat dissipation - Clearance and Spacing
Maintain sufficient clearance between traces, pads, and planes to avoid shorts. Follow IPC standards for trace widths and clearances based on voltage and current levels to prevent arcing and guarantee product longevity
Applications of 4-Layer PCBs: Where They Shine
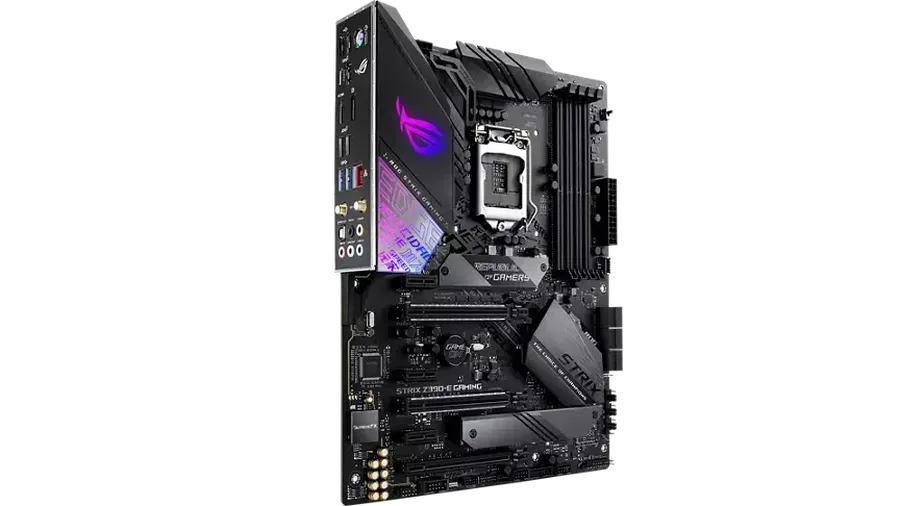
4-Layer PCBs strike a balance between cost, complexity, and performance, making them suitable for a wide array of applications across various industries. Their multi-layer structure allows for effective routing of signals and power, alongside dedicated ground planes, crucial for modern electronics.
- Consumer Electronics
Many consumer devices like smartphones, tablets, and wearable devices rely on 4-layer PCBs. Their compact size and performance capabilities make them ideal for handling the complexity of these gadgets while keeping costs reasonable. - Industrial Control Systems
In industrial settings, 4-layer PCBs are found in control panels, automation equipment, and sensor interfaces. Their ability to manage both digital and analog circuits with a good level of noise immunity is essential for reliable operation in harsh industrial conditions. - Automotive Electronics
Automotive applications, such as infotainment systems, engine control units (ECUs), and driver-assistance systems often use 4-layer PCBs. They provide the necessary performance for signal processing and control, while meeting stringent size and environmental requirements. - Medical Devices
Medical devices, such as diagnostic equipment, monitoring systems, and portable medical instruments, utilize 4-layer PCBs for their balance of reliability, performance, and cost. The boards need to meet strict quality standards and handle sensitive data effectively. - Networking and Communication Equipment
4-Layer PCBs are crucial for networking devices like routers, switches, and communication modules. They offer the signal integrity required for transmitting high-speed data, while remaining within acceptable cost and size parameters for mass deployment. - Aerospace and Defense
While more complex boards are common, 4-layer PCBs find uses in various aerospace and defense applications, particularly in support equipment, control systems, and sensor interfaces. Their balance of performance and size can be a critical asset in these industries.
4-Layer PCB Manufacturing Process: A Brief Overview
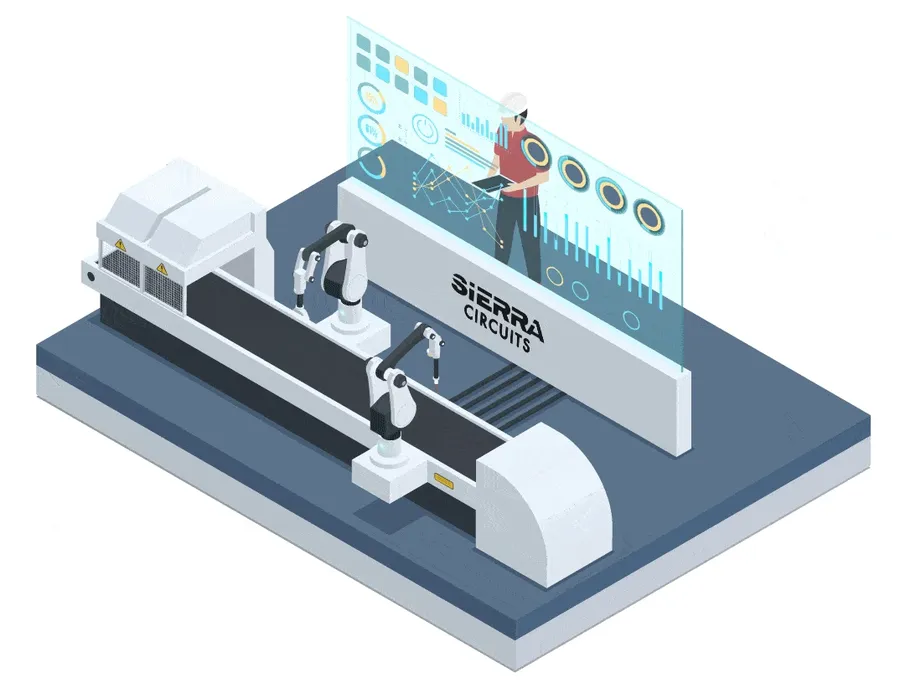
The fabrication of 4-layer PCBs is a sophisticated process involving multiple stages, transforming raw materials into functional circuit boards. This process demands precision and adherence to strict quality control measures to ensure reliable performance.
- Material Selection
The process begins with the selection of appropriate base materials, typically involving a fiberglass-reinforced epoxy resin known as FR-4, which provides structural integrity and electrical insulation. Copper foil is chosen for its high electrical conductivity and ability to be patterned. - Inner Layer Imaging
The inner copper layers are patterned using photolithography. A photosensitive resist is applied to the copper foil, exposed to UV light through a mask, and then chemically developed to remove unwanted copper. This creates the first two layers of the circuit. - Layer Lamination
The patterned inner layers are meticulously stacked and laminated using heat and pressure with prepreg material acting as a binding agent and an insulator, forming a rigid core that becomes the structural foundation of the PCB. - Outer Layer Imaging
Similar to inner layer fabrication, the outer layers are also etched using a photolithographic process to define the tracks, pads and other conductive features on the top and bottom surfaces of the PCB. - Drilling
Precision drilling creates through-holes (vias) that electrically connect different layers of the board. These are essential for signal routing and component mounting. - Plating
The drilled holes are plated with copper through an electrolytic deposition process. This establishes a robust conductive path through the PCB, connecting vias across different layers and creating a continuous circuit. - Solder Mask Application
A solder mask is applied over the entire PCB surface, except for the component pads. This protective layer prevents solder from bridging between unintended connections during assembly. - Surface Finish
A surface finish, such as HASL (Hot Air Solder Leveling), ENIG (Electroless Nickel Immersion Gold), or OSP (Organic Solderability Preservative) is applied to the exposed copper pads, improving their solderability and resistance to corrosion. - Silkscreen Printing
The final step involves printing a silkscreen layer for component references and branding. - Electrical Testing
Each PCB undergoes a comprehensive electrical test to ensure that all connections are working as designed, identifying any potential shorts or open circuits. - Profiling and Singulation
The PCB panel is then precisely cut to the final individual board shape. The boards are then separated from the panel via a process called singulation.
Cost Considerations for 4-Layer PCBs
The cost of a 4-layer PCB is determined by a multitude of factors, primarily revolving around material choices, design complexity, and production volume. Understanding these cost drivers is crucial for effective budget management in electronics projects. By carefully considering each aspect, you can optimize your design for cost efficiency without compromising performance.
Cost Factor | Description | Impact on Cost |
---|---|---|
Material Selection | The type of substrate material (e.g., FR-4, polyimide), copper thickness, and finish (e.g., HASL, ENIG) directly affect the price. | Higher performing materials and finishes increase the cost. For example, ENIG is more expensive than HASL. |
PCB Size and Dimensions | The overall size and dimensions of the PCB impact material usage and production time. | Larger boards consume more material and may require more complex handling in manufacturing, increasing the cost. |
Design Complexity | Factors such as the number of vias, trace density, fine-pitch components, and special features increase manufacturing difficulty. | More complex layouts require precise manufacturing processes, leading to higher costs. |
Layer Count | While this section focuses on 4-layer PCBs, the number of layers is a primary cost driver. | Each additional layer increases material cost and manufacturing complexity, which increases price over a 2 layer board. |
Production Volume | The quantity of PCBs produced in a single run affects the unit price. | Higher production volumes usually result in lower per-unit costs due to economies of scale. |
Manufacturing Process | Specific manufacturing requirements such as laser drilling, blind or buried vias can affect price. | Specialized processes usually incur a premium. |
Testing and Quality Control | Thorough electrical testing and inspection of the boards. | Advanced testing or specialized tests increases cost. |
Frequently Asked Questions About 4-Layer PCBs
This section addresses common questions about 4-layer PCBs, providing clarity on their design, stackup, routing, and application. These FAQs aim to resolve typical user concerns and enhance understanding.
- What exactly is a 4-layer PCB and what defines it?
A 4-layer PCB is a printed circuit board composed of four conductive layers, typically made of copper, separated by insulating substrate material. These layers are arranged in a specific order, known as the stackup, which includes signal, power, and ground layers. The key characteristic is the number of conductive layers, impacting routing complexity, impedance control, and overall performance. - What is the difference between a 4-layer PCB and a 4-layer PCB stackup?
A 4-layer PCB refers to the physical circuit board itself, having four conductive layers. The 4-layer PCB stackup, on the other hand, defines the specific arrangement of those four layers, including the order and the materials used. The stackup directly influences signal integrity and impedance. - How do you effectively route signals in a 4-layer PCB?
Routing in a 4-layer PCB requires careful planning. Typically, the two outer layers are used for signal routing, while inner layers are often dedicated to ground and power planes. Utilizing vias to transition between layers is crucial for connectivity. Good routing practices also include minimizing trace lengths and avoiding sharp bends to reduce signal distortion. Impedance matching through controlled trace width is important. - What is the best stackup configuration for a 4-layer PCB?
A common and often optimal stackup for a 4-layer PCB is signal/ground/power/signal. This configuration provides a dedicated ground plane which helps in reducing noise and improving signal integrity. Other stackup options exist but generally, this configuration is a robust option for most applications. Consider the specific application and performance requirements when determining the best stackup - How do you choose the right layer thickness for a 4-layer PCB?
Layer thickness selection is primarily driven by impedance control needs. The dielectric material thickness and copper trace widths have a direct impact on the characteristic impedance. Common thicknesses are 1.6mm for the total PCB thickness and specific thicknesses for the different dielectric and copper layers. The specific thicknesses must be chosen to match the application requirements and impedance specifications. - How does the choice of substrate material impact the performance of 4-layer PCBs?
The substrate material has a big impact on thermal performance, signal loss and electrical characteristics of the PCB. FR-4 is the most commonly used and cost effective material. Higher frequency applications often require better dielectrics, such as Rogers or other materials. The correct choice depends on the specific demands of the application and cost targets. - Are there any specific considerations when designing 4-layer PCBs for high-speed applications?
For high-speed applications, it's crucial to consider impedance matching, trace routing, and stackup carefully. Maintaining controlled impedance of signal traces is essential to minimize signal reflections. Ground planes should be solid and uninterrupted to reduce noise. Additionally, differential pair routing must be done carefully and with matched trace lengths. Selecting a good substrate material is also important for high speed applications.
Comparing 4-Layer PCBs to Other PCB Types
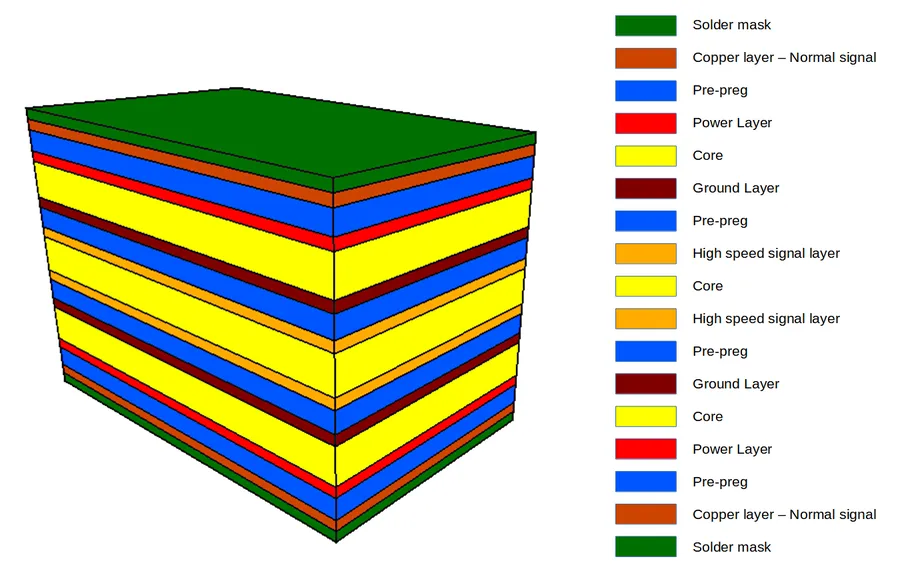
Understanding the nuances between different PCB layer counts is crucial for selecting the right board for your project. This section provides a comparative analysis of 4-layer PCBs against 2-layer and 6-layer PCBs, highlighting their respective strengths and limitations to inform your design choices.
Feature | 2-Layer PCB | 4-Layer PCB | 6-Layer PCB |
---|---|---|---|
Complexity | Simplest, suitable for basic circuits. | Moderate complexity, balance of performance and cost. | Higher complexity, for advanced applications. |
Cost | Lowest cost. | Moderate cost. | Higher cost. |
Routing Flexibility | Limited, routing on two layers only. | Improved, with dedicated power/ground planes and signal routing layers | Most flexible, with additional signal layers for complex layouts. |
Signal Integrity | Most susceptible to noise and signal degradation. | Better performance with dedicated power/ground planes to reduce EMI and crosstalk. | Highest performance with multiple signal layers and tightly controlled impedance. |
Power Distribution | More challenging, requires wide traces. | Good power distribution through dedicated power planes. | Excellent power distribution capabilities with multiple power planes. |
Size and Density | Lower density due to limited routing. | Moderate density, suitable for many applications. | Highest density to accommodate complex circuits. |
Applications | Simple consumer electronics, hobbyist projects. | Many electronic devices, including power supplies and microcontroller boards. | High-performance devices, communication systems, and advanced computing. |
Impedance Control | Basic impedance control is more challenging. | Good impedance control through stack-up selection and plane utilization. | Excellent impedance control for high speed signals and RF applications. |
The 4-layer PCB stands as a testament to the ingenuity of modern electronics, providing a robust and versatile platform for a myriad of applications. From the intricate layout of a smartphone to the robust control system of an industrial robot, the 4-layer PCB's careful balance of signal management, power distribution, and cost-effectiveness makes it an indispensable component. Whether you are designing your first circuit board or a seasoned engineer optimizing complex layouts, understanding the nuances of 4-layer PCB design is key to unlocking its full potential. The insights and guidelines discussed in this article will serve as a valuable starting point for your journey into the world of 4-layer PCBs, enabling you to confidently tackle design challenges and create innovative, reliable electronic systems.
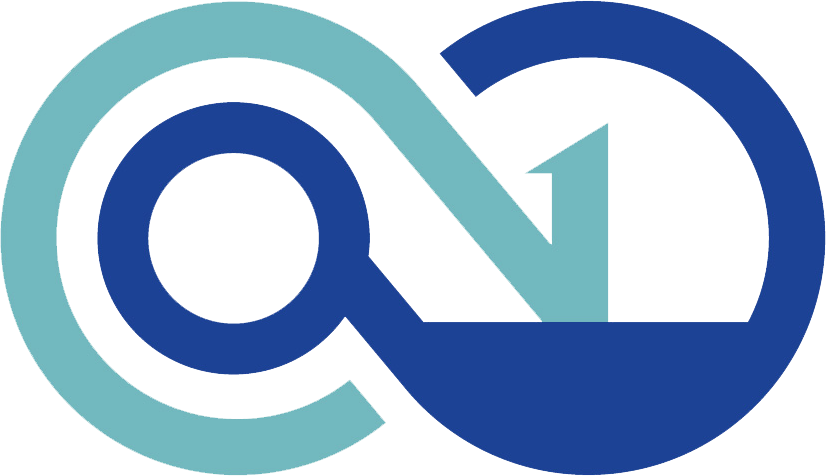