Choosing the Right Aerospace PCB Manufacturer: A Comprehensive Guide
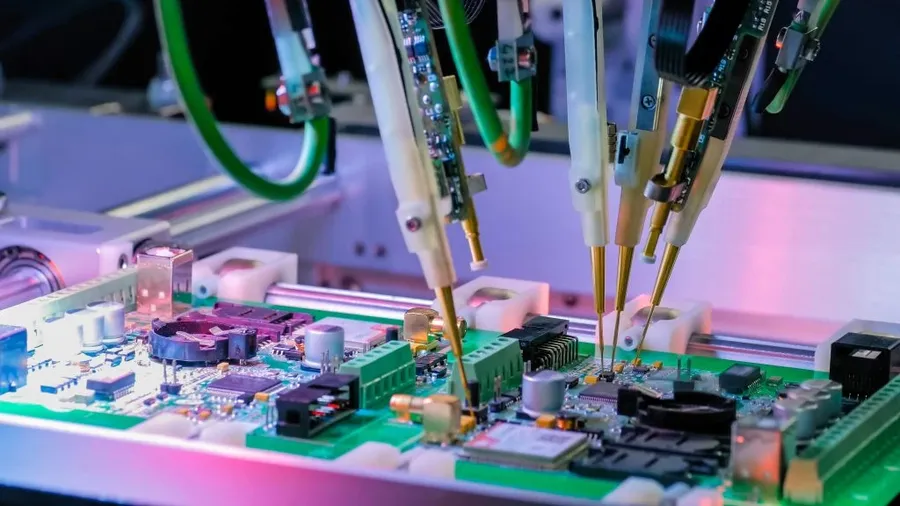
The aerospace industry demands the highest levels of reliability and performance from its components, and printed circuit boards (PCBs) are no exception. As the backbone of critical electronic systems, aerospace PCBs must withstand extreme conditions while performing complex functions flawlessly. Choosing the right aerospace PCB manufacturer is paramount for mission success. This article will guide you through the critical factors to consider when selecting a partner for your aerospace PCB needs, ensuring robust and dependable performance for your demanding applications.
Understanding the Unique Demands of Aerospace PCBs
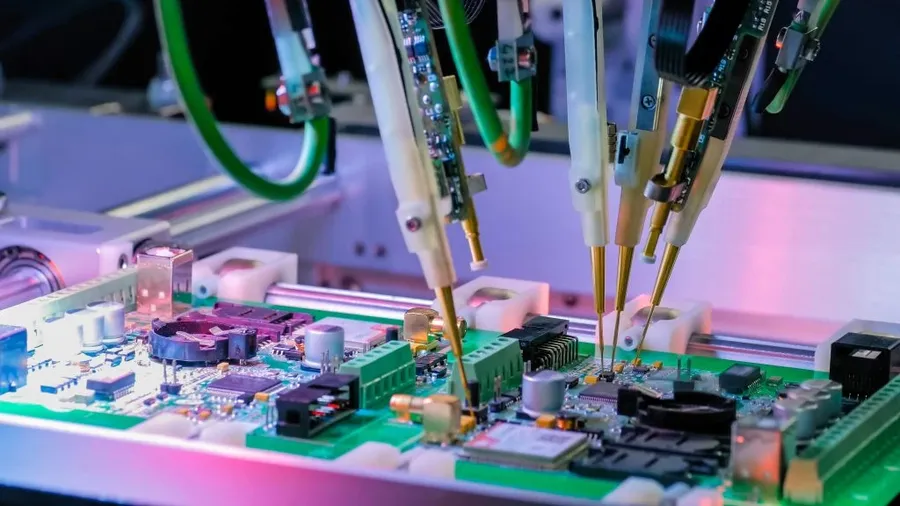
Aerospace printed circuit boards (PCBs) operate under extreme conditions that demand exceptional performance and reliability, far surpassing the requirements of typical consumer electronics. These rigorous demands stem from the critical nature of aerospace applications, where component failure can lead to catastrophic consequences. Aerospace PCBs must withstand extreme temperature variations, intense vibrations, and high levels of radiation, all while maintaining signal integrity and operational functionality. The selection of materials, manufacturing processes, and quality control protocols are therefore paramount, making the choice of an experienced aerospace PCB manufacturer a critical decision.
- Extreme Temperature Tolerances
Aerospace PCBs are subjected to a wide range of temperatures, from the extreme cold of space to the high heat generated by onboard electronics. The materials and construction must be capable of withstanding these fluctuations without degradation or failure. This includes considerations for thermal expansion and contraction rates and the glass transition temperature (Tg) of the substrate materials. - Vibration and Shock Resistance
During launch and flight, aerospace PCBs experience significant vibration and shock loads. The boards must be designed to withstand these forces without fracturing or experiencing component failures. This requires robust mechanical design, appropriate component selection, and secure mounting techniques. - High Reliability Standards
The reliability of aerospace PCBs is of paramount importance. A failure can result in loss of mission, equipment damage, or even loss of life. Therefore, manufacturers must adhere to stringent quality control measures and ensure that the PCBs meet the highest performance and durability standards. Redundancy and fail-safe mechanisms are often employed in the design to mitigate risks. - Radiation Hardening
PCBs used in space applications are exposed to harmful radiation that can affect their performance and lifespan. Radiation-hardening techniques may include using radiation-resistant materials, circuit design that minimizes radiation impact, or protective shielding. The type and level of radiation exposure must be considered during the design and manufacturing process. - Signal Integrity
Maintaining signal integrity in aerospace PCBs is crucial for reliable data transmission and control. High-frequency signals can be affected by impedance mismatches, crosstalk, and other interference. The PCB layout must be carefully designed to minimize these issues. - Size and Weight Constraints
Aerospace applications often have strict size and weight limitations. PCBs must be designed to be as compact and lightweight as possible while maintaining full functionality. This often necessitates the use of multi-layer PCBs and advanced manufacturing techniques.
Key Certifications and Standards for Aerospace PCB Manufacturers
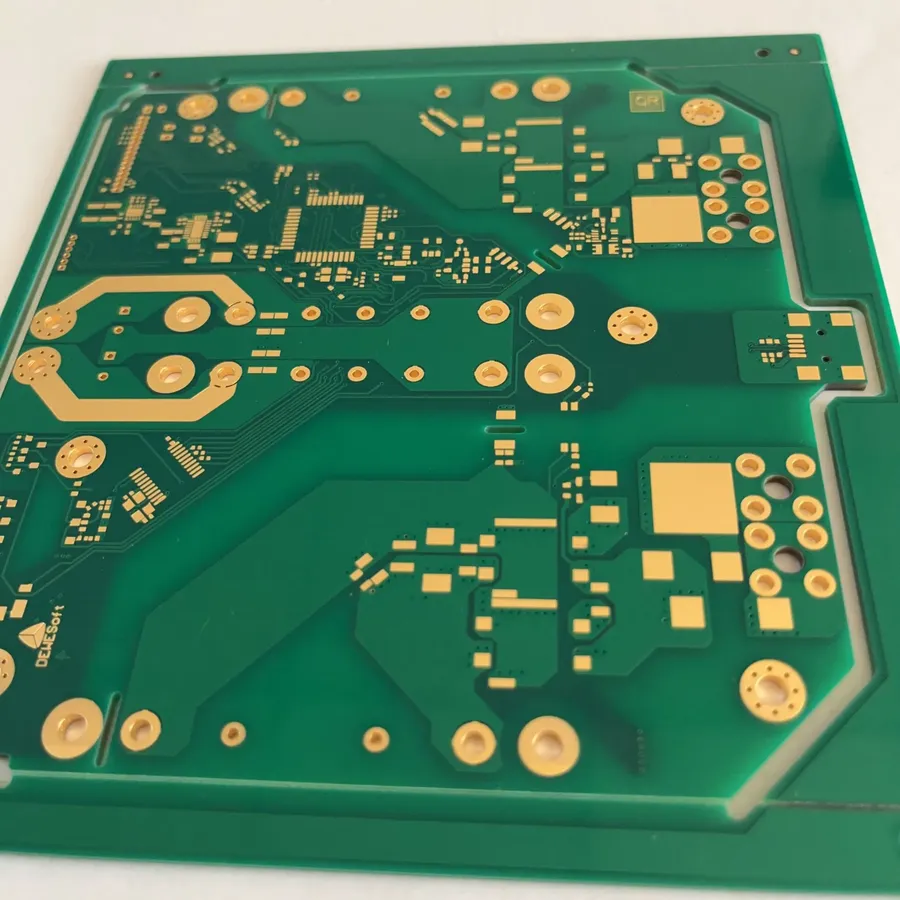
Aerospace PCB manufacturing demands adherence to stringent certifications and standards to ensure reliability and performance in harsh operating environments. These certifications and standards are not merely bureaucratic hurdles; they are critical for validating a manufacturer's capabilities and commitment to quality, ultimately safeguarding the integrity of aerospace systems. Choosing a manufacturer compliant with these benchmarks significantly reduces the risks associated with faulty components.
Certification/Standard | Description | Importance for Aerospace PCBs |
---|---|---|
AS9100 | A quality management standard specific to the aerospace industry, developed by the International Aerospace Quality Group (IAQG). | Ensures the manufacturer has robust processes for quality control, risk management, and continuous improvement, which is essential for the high reliability demands of aerospace applications. |
ITAR Compliance | The International Traffic in Arms Regulations (ITAR) governs the export and import of defense-related articles and services, including certain PCB technologies. | Mandatory for manufacturers involved in U.S. defense and aerospace projects, ensuring sensitive information and technologies are not mishandled or exported illegally. |
MIL-SPEC Standards | Military specifications that define performance and testing requirements for electronic components used in military and aerospace applications. | Guarantees that PCBs meet specific military performance levels, including environmental stress, durability, and operational reliability under challenging conditions. |
IPC Standards | These industry-consensus standards related to PCB design, manufacturing and assembly process. Includes, but is not limited to: IPC-A-600 (Acceptability of Printed Boards), IPC-6012 (Qualification and Performance Specification for Rigid Printed Boards), IPC-A-610 (Acceptability of Electronic Assemblies) | These standards are developed to ensure the quality, reliability and proper performance in the end product. |
Materials and Fabrication Techniques Essential for Aerospace PCBs
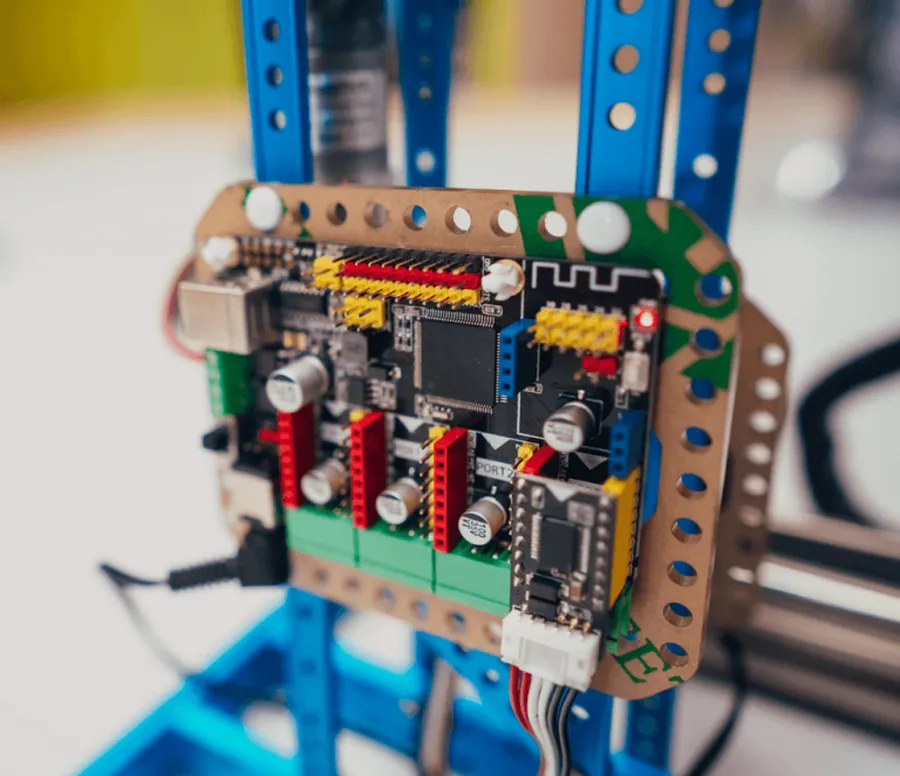
Aerospace PCBs demand exceptional performance characteristics, necessitating the use of high-performance materials and advanced fabrication techniques. These requirements stem from the extreme conditions encountered in aerospace applications, including wide temperature variations, intense vibration, and stringent reliability standards. An aerospace pcb manufacturer must possess expertise in selecting appropriate materials and employing precise fabrication methods to meet these demands.
Material | Key Characteristics | Aerospace Application | Advantages | Disadvantages |
---|---|---|---|---|
Polyimide | High temperature resistance, excellent dimensional stability, good electrical properties | High-temperature engine control systems, flexible circuits in satellites | Exceptional thermal stability, reliable performance in harsh environments | Higher cost compared to standard materials |
PTFE (Teflon) | Excellent high-frequency performance, low dielectric constant, low loss | Radar systems, high-frequency communication modules, signal processing | Superior signal integrity, minimal signal loss, ideal for high-speed applications | Mechanically less robust, more challenging to fabricate compared to other materials |
FR-4 with high Tg | Improved temperature resistance, enhanced mechanical strength | General purpose aerospace electronics, less demanding thermal environments | Cost-effective alternative to polyimide, good balance of properties | Lower thermal stability than polyimide, not suitable for extremely high temperatures |
Copper | Excellent electrical conductivity, good thermal properties | Conductors, vias, and pads in all aerospace PCBs | High conductivity, provides excellent electrical signal transmission | Susceptible to oxidation, requires proper surface treatment |
In addition to material selection, advanced fabrication techniques are crucial for aerospace PCBs. These include:
- Multi-layer Boards
Fabrication of boards with numerous layers to achieve increased circuit density and complexity, critical for complex aerospace systems - Controlled Impedance Design
Careful design and fabrication of PCB traces to achieve precise impedance, essential for signal integrity and high-frequency signal transmission which is vital for aerospace communication and radar systems. - Microvia Technology
Utilizing very small vias for dense interconnections, essential for miniaturized components in aerospace applications. Enables complex routing and enhances circuit density. - Rigid-Flex Circuitry
Integration of rigid and flexible sections within the same PCB, enabling greater design freedom and optimizing space in compact and complex aerospace systems - Surface Finish
Employing durable and reliable surface finishes, such as ENIG (Electroless Nickel Immersion Gold), for enhanced solderability and corrosion resistance, which is important for long-term performance and reliability.
Top Aerospace PCB Manufacturers: A Comparative Overview
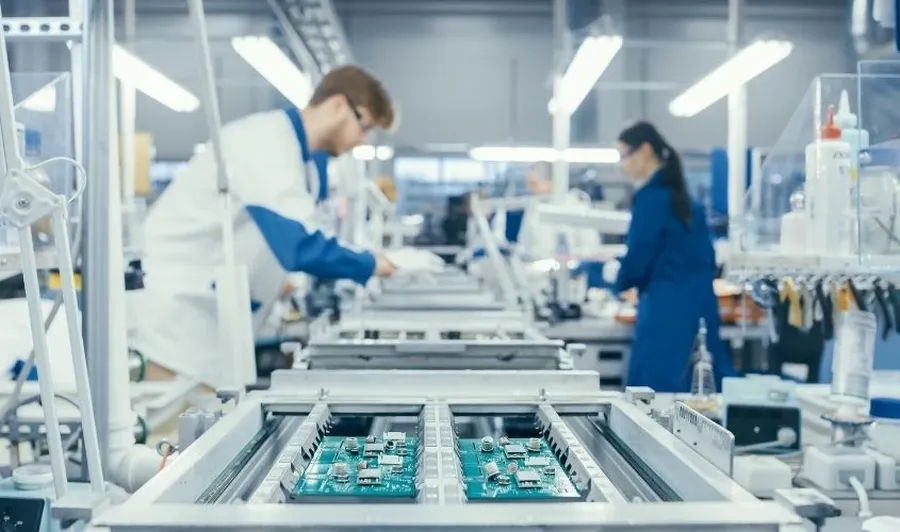
Selecting the right aerospace PCB manufacturer is crucial for ensuring the reliability and performance of electronic systems in demanding aerospace applications. This section provides a comparative analysis of several leading manufacturers, focusing on their specializations, certifications, and manufacturing capabilities. This comparison will enable informed decision-making when selecting a partner.
Manufacturer | Specialization | Key Certifications | Manufacturing Capabilities | Typical Lead Time | Additional Services |
---|---|---|---|---|---|
Company A | High-reliability, mission-critical PCBs | AS9100, ISO 9001, ITAR | Multi-layer PCBs, rigid-flex PCBs, HDI PCBs | 4-8 weeks | Design Support, Assembly |
Company B | Complex, high-density PCBs for aerospace and defense | AS9100, MIL-PRF-55110, Nadcap | Controlled impedance PCBs, embedded components, RF PCBs | 6-10 weeks | DFM analysis, Reliability Testing |
Company C | Quick-turn prototyping and small batch production | ISO 9001, ISO 13485 | Standard PCBs, quick turn prototyping, small batch production | 2-4 weeks | Prototyping, fast turnaround |
Company D | Specialty Materials for harsh environments | AS9100, ITAR | Polyimide PCBs, PTFE PCBs, high-Tg PCBs | 6-12 weeks | Material selection assistance, impedance control |
Company E | PCB assembly and system integration | ISO 9001, IPC-A-610 | Turnkey PCB assembly, box build assembly | 8-12 weeks | Full system integration, component sourcing |
The Importance of Testing and Quality Control for Aerospace PCBs
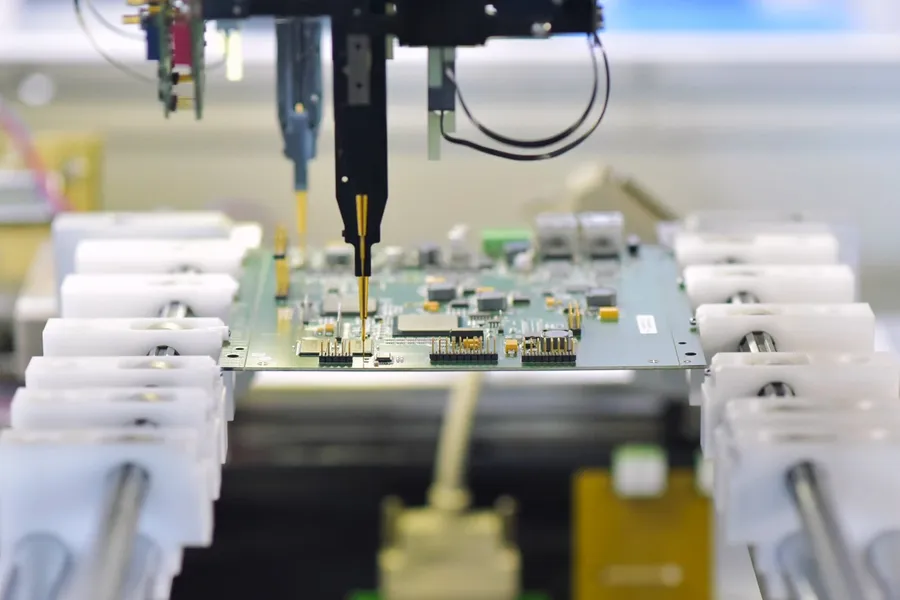
Rigorous testing and quality control are paramount in aerospace PCB manufacturing due to the extreme reliability demanded by aerospace applications. These PCBs must function flawlessly under harsh conditions, making comprehensive testing at every stage of production a non-negotiable requirement. The slightest defect can lead to catastrophic system failures, underscoring the crucial role that meticulous testing plays.
Aerospace PCB manufacturers employ a variety of sophisticated testing methods to ensure the highest level of product reliability. These tests can be broadly categorized into electrical testing, environmental stress screening, and functional testing.
Testing Method | Description | Purpose |
---|---|---|
Electrical Testing | Includes continuity testing, insulation resistance testing, and impedance control testing. | Verifies the electrical integrity of the PCB by ensuring proper connections and isolation between circuits and controlling signal quality. |
Environmental Stress Screening (ESS) | Involves temperature cycling, vibration testing, and humidity testing. | Assesses the PCB's ability to withstand extreme environmental conditions and ensures that it operates reliably under these conditions. |
Functional Testing | Simulates the operational environment to confirm the overall performance of the PCB. | Tests the PCB's ability to perform its intended functions within a specific system and identifies any operational issues. |
Automated Optical Inspection (AOI) | Uses cameras to capture images of the PCB and compare them to the design specifications. | Detects defects such as shorts, opens, or missing components in the PCB. |
X-ray Inspection | Uses X-rays to inspect the PCB's inner layers and solder joints. | Identifies potential flaws that would not be visible using traditional visual inspection and evaluates the quality of internal connections. |
These testing methods are complemented by rigorous quality control processes, which encompass all phases of production from design to final inspection and ensure that the printed circuit boards meet the stringent requirements demanded of aerospace applications. This holistic approach to quality ensures the manufacture of highly reliable aerospace PCBs.
Factors Beyond Manufacturing: Design Support and Intellectual Property Protection
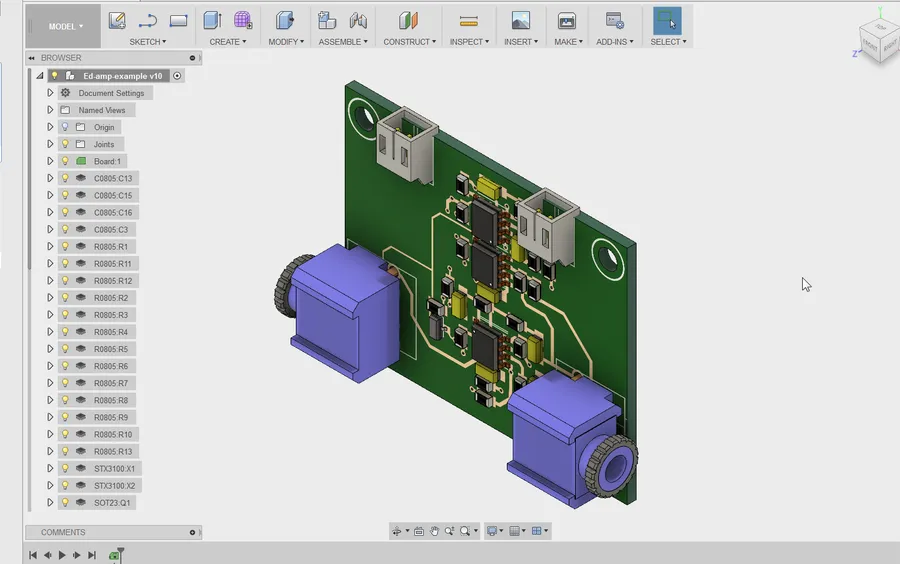
Selecting an aerospace PCB manufacturer extends beyond mere fabrication capabilities; it requires careful consideration of design support and intellectual property (IP) protection. A robust manufacturer will offer comprehensive design and engineering services, and will have robust systems in place to safeguard your proprietary designs and technology.
Design support encompasses a range of services crucial for the successful development of complex aerospace PCBs. These services include:
- Design for Manufacturability (DFM) Analysis
Expert analysis of PCB designs to identify potential manufacturing issues, optimizing designs for efficient production, reducing costs, and minimizing delays. DFM considerations are critical to ensuring that the PCB can be reliably produced at high yields. - Schematic Capture and Layout
Assistance in translating electronic schematics into physical PCB layouts. This service includes optimizing component placement, signal routing, and layer stack-up to meet specific performance requirements and standards. Expert knowledge is necessary in complex aerospace applications to ensure signal integrity and minimize noise. - Signal Integrity Analysis
Simulations and analysis to ensure that signals on the PCB meet required quality criteria, preventing issues like signal degradation or interference. For high speed or high-frequency applications typical in aerospace electronics, signal integrity analysis is essential to maintain reliable performance. - Thermal Management Design
Designing PCBs with proper heat dissipation mechanisms to ensure operational reliability, especially in the extreme thermal environments encountered in aerospace applications. Effective thermal management prevents components from overheating and failing, ensuring system performance and longevity. - Material Selection Guidance
Providing expert advice on the best materials to use for aerospace PCBs based on specific performance requirements such as thermal and mechanical stress or requirements for specific electrical properties. Choosing the right materials is vital for achieving reliable operation in harsh aerospace environments.
Intellectual Property protection is equally critical, especially with the complex designs and specialized technologies involved in aerospace PCBs. A reputable aerospace PCB manufacturer will ensure the following:
- Non-Disclosure Agreements (NDAs)
Enforce strict NDAs to protect your design and technology from unauthorized disclosure. These agreements ensure the manufacturer understands their obligations to protect your confidential design information. - Secure Data Handling
Implementing secure systems for handling design files and other sensitive information. A manufacturer should have robust IT systems in place to prevent data breaches and unauthorized access. - Controlled Access
Restricting access to design files and production processes to authorized personnel only. This ensures that only necessary personnel are privy to sensitive design information, minimizing risks of leaks or misappropriation. - IP Awareness Training
Educating employees on the importance of IP protection and the penalties for misuse. This ensures that all staff, including those on the manufacturing line, understand the sensitivity of design information. - Secure Supply Chain Management
Ensuring all suppliers and partners involved in the manufacturing process also adhere to strict confidentiality agreements. Extending IP protection to the supply chain is critical to prevent leakage of technology to third parties.
By selecting a manufacturer with robust design support and stringent IP protection measures, you secure not only the physical production of your aerospace PCBs, but also ensure the integrity and competitiveness of your product development efforts.
Frequently Asked Questions About Aerospace PCB Manufacturing
This section addresses common questions regarding aerospace PCB manufacturing, providing concise and informative answers to help you navigate the complexities of this specialized field. These FAQs cover critical requirements, necessary certifications, quality assurance, and best design practices.
- What are the critical performance requirements for aerospace PCBs?
Aerospace PCBs must withstand extreme conditions, including wide temperature ranges (-55°C to +125°C or more), high levels of vibration and shock, and exposure to radiation. They require high reliability, long operational life, and must be designed to ensure minimal signal interference while maintaining consistent performance. Material selection and design techniques must account for these conditions to ensure mission-critical functionality. - What certifications should I look for in an aerospace PCB manufacturer?
Key certifications include AS9100 (aerospace quality management system), ISO 9001 (general quality management), ITAR compliance (for handling defense-related technologies), and potentially MIL-SPEC standards (for military applications). These certifications demonstrate the manufacturer’s commitment to quality, traceability, and compliance with industry regulations. Confirm that these certifications are not only held, but properly implemented via a robust quality system. - How can I ensure the quality of my aerospace PCBs?
Quality assurance is paramount and should include rigorous testing protocols. These protocols include electrical testing to confirm circuit integrity, environmental stress screening (ESS) to simulate harsh operating conditions, functional testing to verify performance under load, and visual inspection using advanced imaging techniques. Ensure the manufacturer uses automated inspection equipment, provides comprehensive testing reports, and has robust traceability systems. - What are the best design practices for aerospace PCBs?
Best design practices include using high-performance materials such as polyimide or PTFE, implementing controlled impedance design for high-speed signal transmission, employing advanced thermal management techniques (such as thermal vias and heat sinks), and designing for high-density interconnect (HDI) requirements. A full understanding of aerospace PCB requirements will mean choosing a manufacturer with experience in aerospace requirements who can provide design for manufacture (DFM) feedback. Proper stack-up design and material selection are also critical to achieve reliability and manufacturability. - Who are some leading aerospace PCB manufacturers?
While specific manufacturers can vary, some leading companies are recognized for their capabilities in high-reliability PCB manufacturing for aerospace applications. Look for manufacturers that have demonstrated their competence through customer testimonials, published case studies, and the certifications mentioned previously. A thorough evaluation of their manufacturing experience, technology, capacity, and customer service is essential for selection. Always research customer feedback and project-specific performance for due diligence. - What is the importance of design support when choosing an aerospace PCB manufacturer?
Design support from your PCB manufacturer is essential for optimizing the manufacturability, performance, and reliability of your PCB. The manufacturer's involvement early in the design cycle can help avoid costly errors and ensure optimal manufacturing efficiency. An ideal manufacturer will provide a comprehensive suite of design services, from component selection to DFM analysis, while also ensuring your intellectual property (IP) remains secure. - How does intellectual property protection affect the selection of an aerospace PCB manufacturer?
Aerospace PCB designs often involve sensitive and proprietary technology. Therefore, choosing a manufacturer with robust IP protection measures is crucial. Ensure the manufacturer has strict policies and procedures to safeguard your design data, including secure data storage, controlled access protocols, and non-disclosure agreements (NDAs). Confirm that all personnel handling sensitive information are adequately trained in data protection best practices. This protects your intellectual property and minimizes the risk of unauthorized use or disclosure.
Future Trends in Aerospace PCB Manufacturing
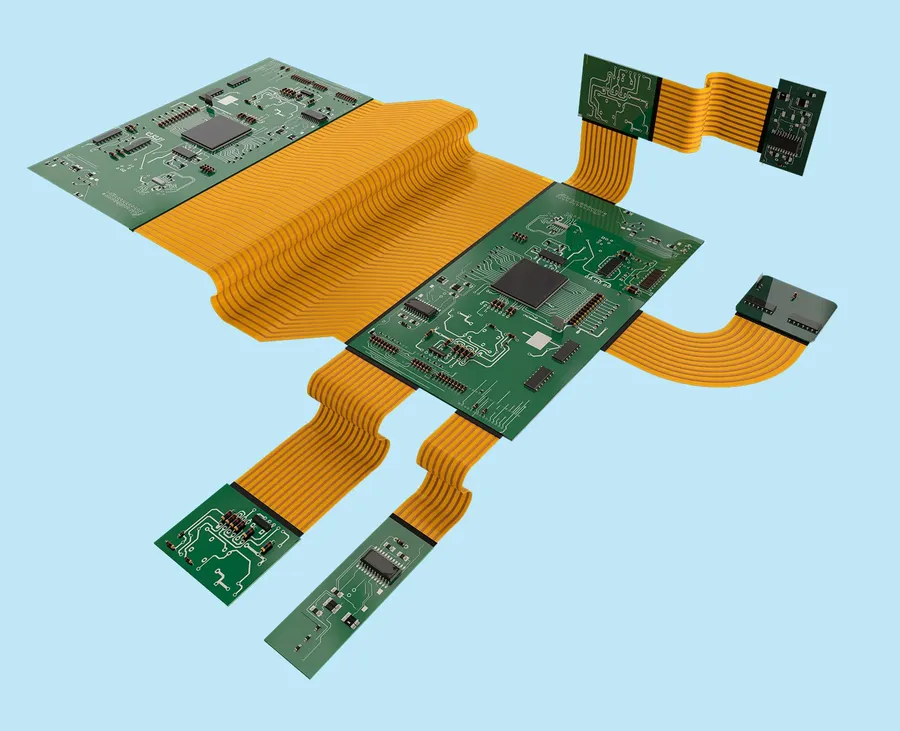
The aerospace PCB manufacturing sector is experiencing a rapid evolution driven by the demand for lighter, more reliable, and higher-performance electronic systems. Key trends include the adoption of advanced materials, embedded components, and innovative packaging solutions, all aimed at pushing the boundaries of what's achievable in aerospace applications.
- Embedded Components
Embedding components directly within the PCB layers reduces size and weight, crucial for aerospace applications where space and mass are critical. This also enhances signal integrity and reduces interconnect lengths, improving overall system performance and reliability. - Advanced Materials
The use of advanced materials like low-loss dielectrics, thermally conductive substrates, and flexible substrates is becoming more prevalent. These materials offer improved electrical performance, better thermal management, and enable more flexible designs for complex aerospace systems. Examples include advanced polyimides, PTFE composites, and ceramic-filled resins. - 3D Printing and Additive Manufacturing
Additive manufacturing techniques are revolutionizing PCB fabrication by enabling the creation of complex geometries and custom designs more efficiently than traditional methods. This allows for rapid prototyping and the production of specialized boards with unique performance requirements. - Integrated Passive Devices
Integrating passive components like resistors, capacitors, and inductors directly into the PCB reduces component count, improves performance, and saves space. This approach is crucial for designing high-density boards required in advanced aerospace systems. - Miniaturization
Continuing miniaturization efforts focus on creating even smaller and more densely populated PCBs. This is driven by the need for more compact electronics that can fit into increasingly constrained aerospace environments, while still maintaining required functionality and high reliability. - AI and Machine Learning in PCB Design and Manufacturing
AI and machine learning are being integrated into the PCB design and manufacturing process for improved design optimization, defect detection, and production process efficiency. These technologies are essential for ensuring quality and reliability, while simultaneously reducing development time and cost.
Selecting the right aerospace PCB manufacturer is a critical decision that can significantly impact the performance and reliability of your aerospace applications. By understanding the unique demands, certifications, materials, and testing requirements, you can make an informed choice and ensure your PCBs meet the rigorous standards of the aerospace industry. A trusted aerospace PCB manufacturer provides not only manufacturing capabilities, but also design support, stringent quality control, and intellectual property protection that are vital for mission success. Keep in mind that advancements in materials and manufacturing techniques are continually evolving the landscape, requiring a commitment to staying informed and adaptable.
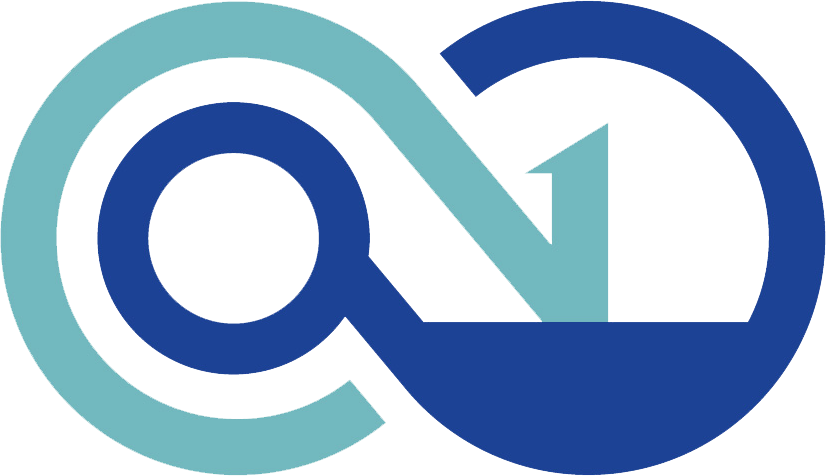