Choosing the Right Electronic PCB Assembly Manufacturer: A Comprehensive Guide
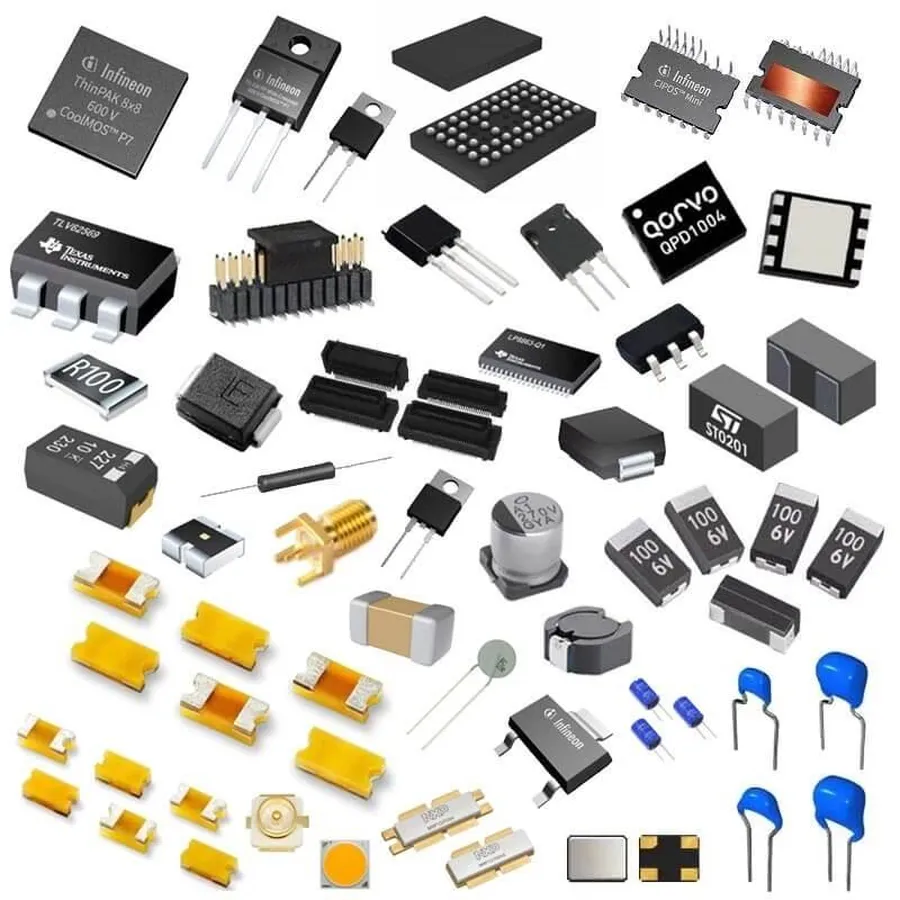
In today's rapidly evolving tech landscape, electronic PCB assembly is the backbone of countless devices. Choosing the right manufacturer is crucial for success, impacting product quality and time-to-market. This guide delves into the key aspects of selecting an electronic PCB assembly manufacturer, providing insights that bridge technical considerations with strategic business decisions, ensuring your product is brought to life with expertise and precision.
Understanding Your PCB Assembly Needs
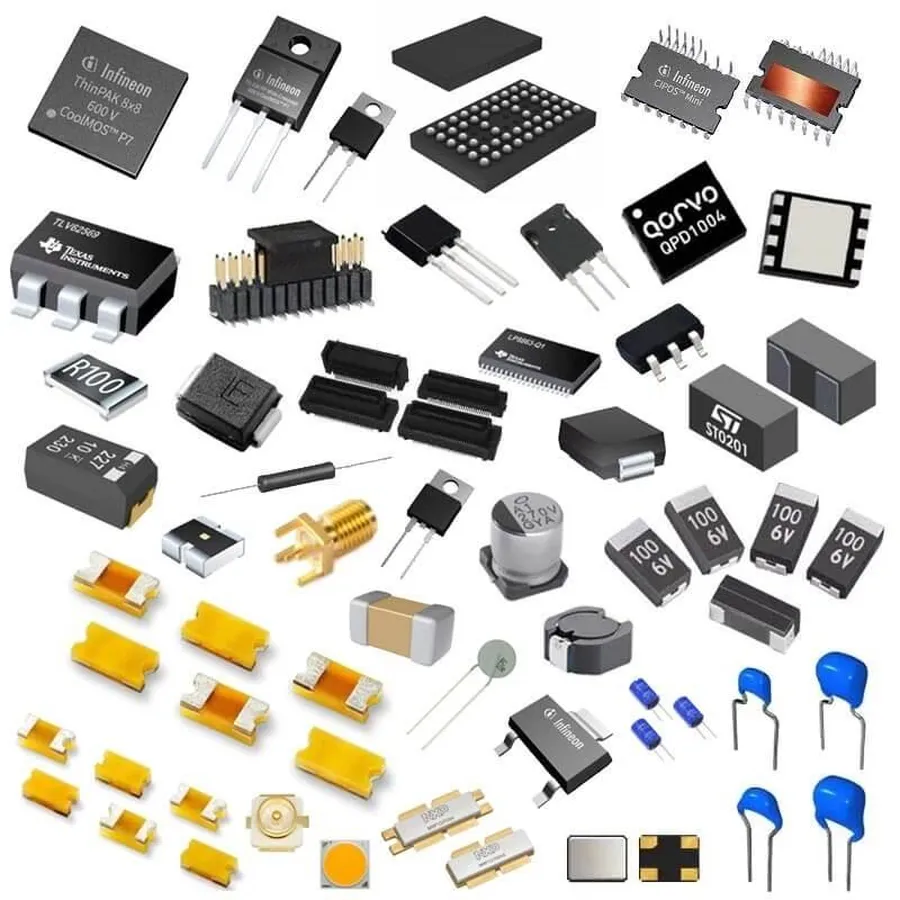
Prior to engaging an electronic PCB assembly manufacturer, a meticulous assessment of your specific project needs is paramount. This foundational step dictates the selection of a partner capable of delivering a product that aligns precisely with your requirements, mitigating risks associated with incompatibility and ensuring a successful production outcome. Defining these needs encompasses a range of parameters, including production volume, the complexity of the PCB design, necessary quality certifications, and required turnaround times. These factors interact to determine the most suitable manufacturer for your project.
Parameter | Description | Impact on Manufacturer Selection |
---|---|---|
Production Volume | Quantity of PCBs required (prototype, low, medium, high) | Determines if the manufacturer specializes in prototyping, small-batch runs, or large-scale production. Affects pricing, lead times and tooling. |
PCB Complexity | Number of layers (single-sided, double-sided, multi-layer), component types (SMT, through-hole), trace density | Specifies the manufacturer's need for specific machinery and skilled operators, and its ability to handle advanced assembly technologies such as fine pitch components and complex routing. |
Required Certifications | Industry-specific quality standards (ISO 9001, AS9100, IPC standards, etc.) | Indicates the manufacturer’s adherence to stringent quality controls and compliance standards, which may be crucial for certain applications. |
Turnaround Time | Time frame for completing the assembly process | Influences which manufacturers are able to accommodate required timelines, with options ranging from rapid turnaround prototyping to longer lead times for large orders. |
Key Factors to Evaluate in an Electronic PCB Assembly Manufacturer
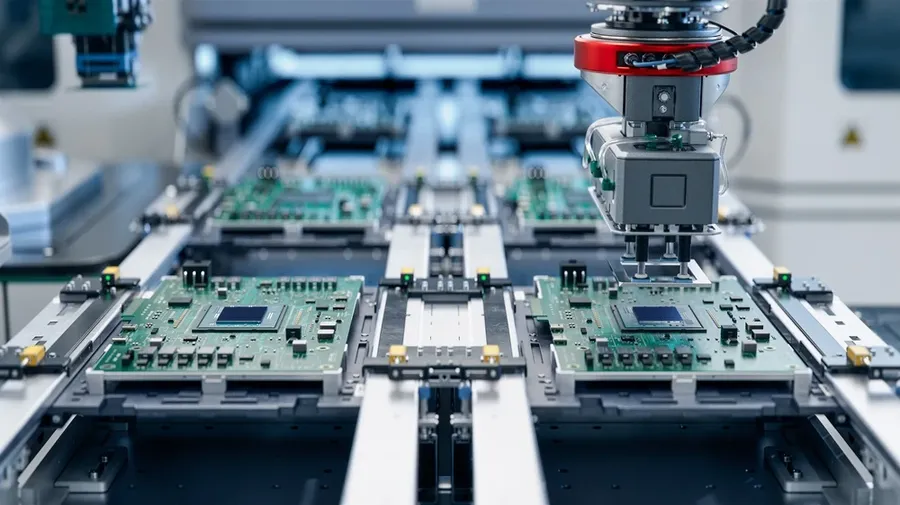
Selecting the right electronic PCB assembly manufacturer is crucial for ensuring the quality and reliability of your final product. This section will explore the key factors that should be evaluated, including manufacturing capabilities, technology, quality control, and materials sourcing. Each of these areas plays a critical role in the overall success of your PCB assembly project.
The evaluation process should include a thorough assessment of the manufacturer's capabilities, their technological proficiency, quality control, and ethical sourcing of materials. These aspects significantly impact the final quality and reliability of assembled PCBs.
Factor | Description | Impact on PCB Quality and Reliability |
---|---|---|
Manufacturing Capabilities | Capacity to handle your project's volume, complexity, and size. Includes SMT, through-hole, and mixed technology assembly capabilities. | Directly affects the manufacturer's ability to meet your specific requirements and deadlines. Inadequate capacity can lead to delays and quality issues. |
Technology | Utilization of modern equipment and processes, such as automated pick-and-place machines, reflow ovens, and advanced inspection tools (AOI, X-ray). | Ensures precision, consistency, and efficiency. Obsolete equipment can result in inconsistent results and lower yields. |
Quality Control Processes | Adherence to strict quality standards, including ISO certifications, comprehensive inspection, and testing procedures. | Critical for ensuring that PCBs meet required performance and reliability standards. Inadequate QC can lead to field failures and increased costs. |
Materials Sourcing | Transparent and ethical sourcing of high-quality components and materials from reliable suppliers. | Impacts the long-term performance and reliability of the PCB. Substandard materials can lead to premature failures and safety concerns. |
Certifications and Compliance | Compliance with industry standards, such as ISO 9001, AS9100, and others specific to your industry. | Assures adherence to quality management systems and industry requirements, enhancing the reliability and consistency of the PCB manufacturing process |
Prototyping and Low-Volume PCB Assembly vs. High-Volume Production
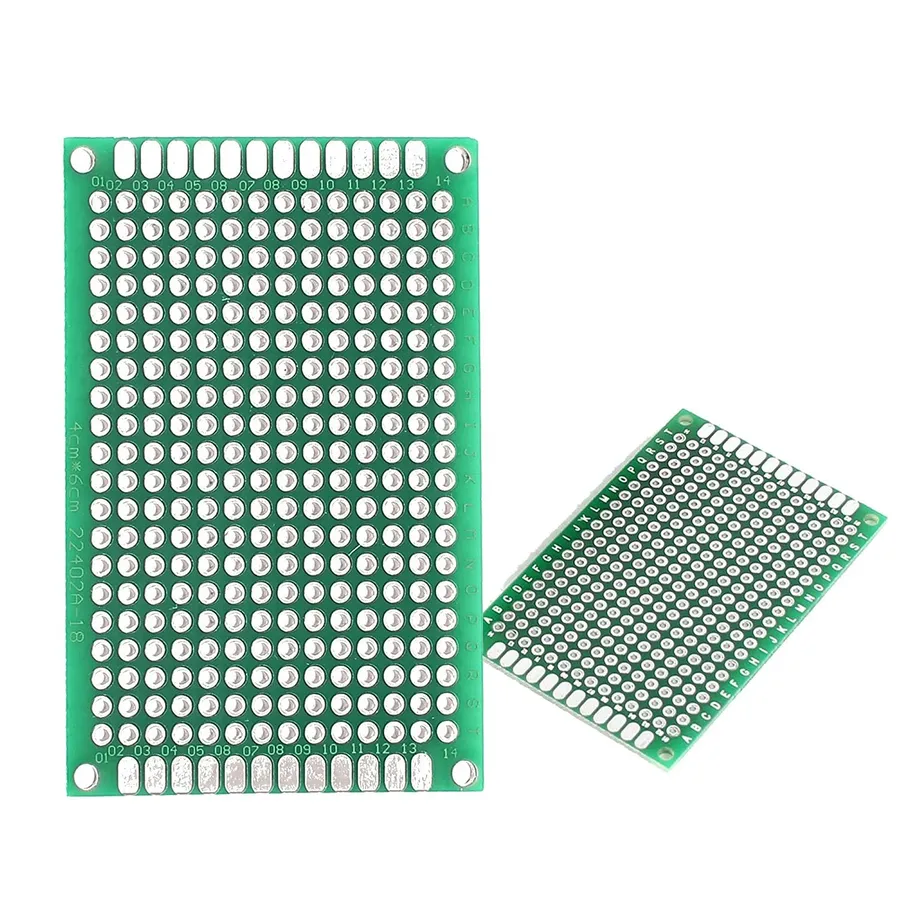
The requirements and processes for PCB assembly differ significantly between prototyping/low-volume production and high-volume manufacturing. Understanding these distinctions is critical for selecting the right manufacturer and ensuring optimal outcomes for your specific project needs.
Feature | Prototyping/Low-Volume | High-Volume |
---|---|---|
Focus | Flexibility, quick turnaround, design validation | Efficiency, cost optimization, consistency |
Process | Manual or semi-automated assembly, focus on design changes. | Highly automated assembly lines, standardized processes. |
Setup Costs | Higher per-unit cost, lower overall setup cost | Lower per-unit cost, higher initial setup cost |
Material Sourcing | More flexible material options, rapid procurement | Bulk material purchasing, emphasis on cost-effective sourcing. |
Lead Times | Shorter lead times, faster iterations | Longer lead times, stable production runs |
Ideal Manufacturer | Smaller, agile manufacturers, design focused manufacturers | Large-scale manufacturers with high automation capability |
Selecting a manufacturer that aligns with your production volume needs is crucial to avoid unnecessary costs and delays. Manufacturers specializing in prototypes often prioritize flexibility and quick turnaround times, while those focused on high-volume production emphasize automation and cost efficiency. It’s important to verify that the manufacturer's capabilities match the requirements of your specific phase of the product lifecycle.
Location, Turnaround Time and Lead Times Considerations
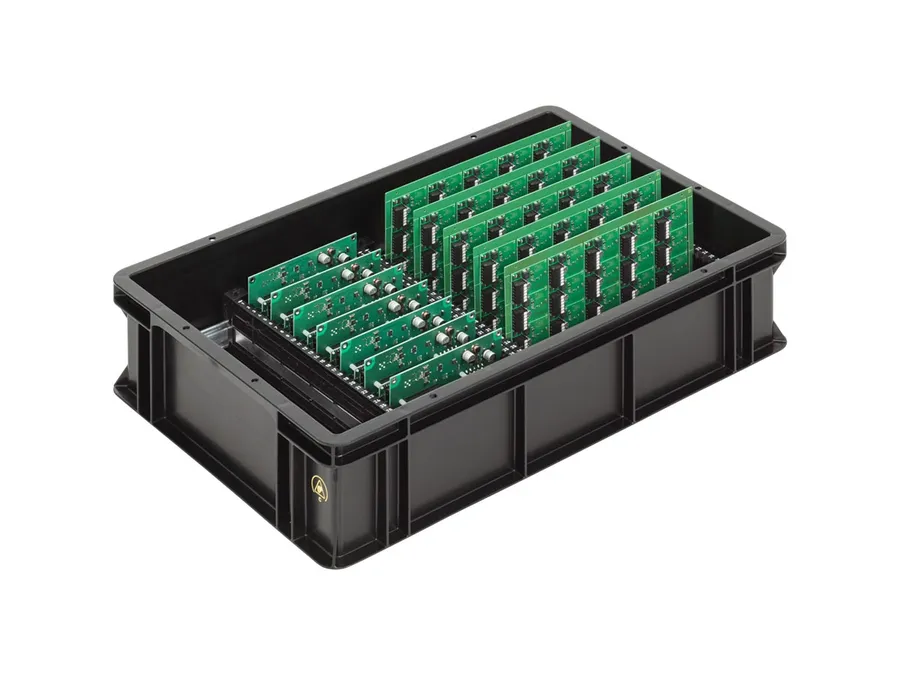
Selecting the location of your electronic PCB assembly manufacturer significantly impacts turnaround time, lead times, and overall project costs. This section explores the trade-offs between domestic and overseas manufacturing, focusing on logistical, communication, and financial aspects, as well as production timelines.
Factor | Domestic Manufacturing | Overseas Manufacturing |
---|---|---|
Lead Times | Generally shorter; faster prototyping and revisions | Potentially longer due to shipping and customs |
Turnaround Time | Faster due to proximity and less complex logistics | Slower, impacted by shipping distances and potential delays |
Logistics | Simpler, easier to manage with local teams | More complex; involves international shipping, customs, and potential delays |
Communication | Easier to collaborate due to fewer language and time zone barriers | Can be challenging, with language barriers, time zone differences and cultural nuances |
Cost | Typically higher labor and overhead expenses | Often lower due to cheaper labor and operational costs |
Intellectual Property Protection | Generally stronger due to local legal systems | Increased risk, requiring careful agreements and due diligence |
Quality Control Oversight | Easier to monitor and make on-site visits | More difficult to monitor due to geographical distance |
The choice between domestic and overseas manufacturing should be based on a comprehensive evaluation of your specific project requirements. Domestic manufacturers may offer faster turnaround times, easier communication, and stronger quality control, whereas overseas manufacturers typically provide cost advantages. Considerations must also include material lead times, which can vary based on component availability and supplier locations.
Cost Analysis and Budgeting for PCB Assembly
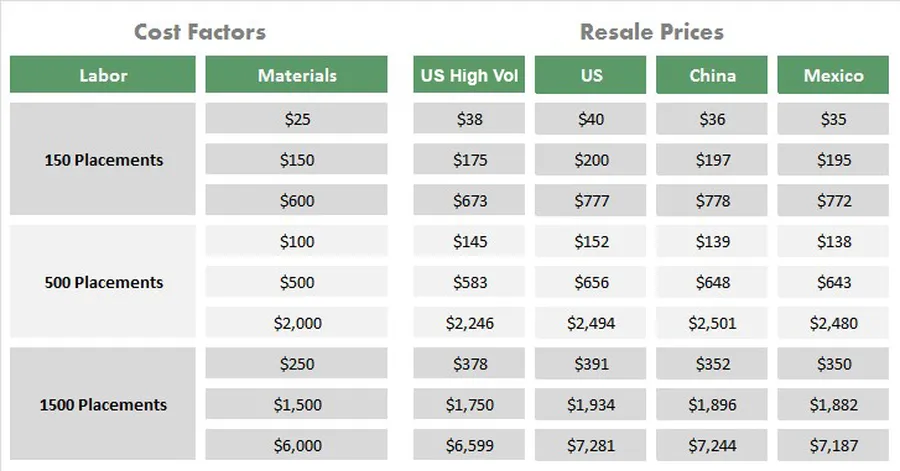
Accurately analyzing and budgeting for PCB assembly costs is crucial for project success, influencing both financial viability and product quality. Understanding the cost drivers enables informed decision-making and facilitates effective resource allocation, ensuring the final product meets both performance and economic requirements.
Cost Factor | Description | Impact on Overall Cost | Optimization Strategies |
---|---|---|---|
Material Costs | Price of PCB substrates (e.g., FR-4, aluminum), components (resistors, capacitors, ICs), and solder materials. | High: Directly impacts overall cost, varying with material type and component specifications. | Standardize component selection, bulk purchasing, negotiate with suppliers, and use alternative materials where appropriate. |
Labor Costs | Expenses for manual assembly, machine operation, testing, and quality inspection. | Medium to High: Varies based on complexity, automation level, and geographic location. | Utilize automated assembly processes, optimize production workflow, and explore manufacturing locations with favorable labor rates. |
Tooling Costs | Expenses related to stencils, fixtures, and other manufacturing tools. | Medium: Primarily significant during initial setup or when changes are introduced to the design. | Re-use existing tooling when possible, and design for manufacturability (DFM) to minimize tooling needs. |
Testing Costs | Costs associated with quality control measures, including AOI, X-ray inspection, and functional tests. | Medium: Vital for ensuring quality; may increase with more rigorous testing protocols. | Optimize testing strategy based on project needs, use cost-effective testing methods, and prioritize critical tests. |
NRE Costs | Non-recurring engineering costs, including design setup, programming of assembly machines, and prototyping. | Medium: Predominantly a one-time cost but significant during the initial stages. | Carefully plan designs and consider design for manufacturability (DFM) to reduce changes and iterations. Design robust test plans to reduce any re-spins. |
Shipping and Logistics | Transportation costs of raw materials and finished goods, along with custom fees and import duties. | Medium: Dependent on the source of materials and destination of finished boards. | Consolidate shipments, select efficient shipping methods, and consider nearshore options to reduce logistic costs. |
Volume of Production | Production quantities of the circuit boards being manufactured. Typically broken into prototype, low volume, medium volume, and high volume. As well as the quantity being produced within the production run. | High: Significant impact of the price per board, as manufacturing setup costs can be averaged over larger quantities. | Forecast future requirements accurately, consider batching production runs, and use scaling to reduce material costs. |
Quality Control and Testing Methods in PCB Assembly
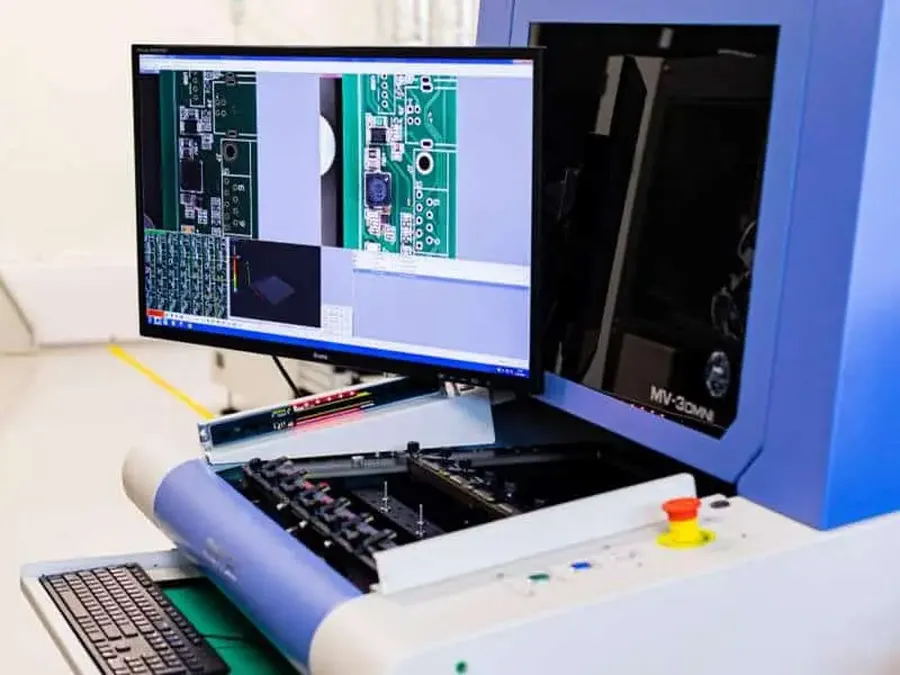
Rigorous quality control and testing are paramount in electronic PCB assembly to ensure the reliability and performance of the final product. Manufacturers employ a variety of techniques, including automated optical inspection (AOI), X-ray inspection, and functional testing, to identify and rectify defects throughout the assembly process. These measures are not just about catching errors; they are integral to building a reputation for producing high-quality, dependable circuit boards.
Testing Method | Description | Purpose | Technology |
---|---|---|---|
Automated Optical Inspection (AOI) | Uses high-resolution cameras to visually inspect PCBs for defects such as missing components, misaligned parts, solder joint issues, and wrong polarity. | Identifies defects early in the assembly process, preventing downstream problems. | 2D and 3D High resolution optical imaging. |
X-ray Inspection | Employs X-ray technology to inspect internal solder joints, particularly beneath Ball Grid Array (BGA) components and other hidden connections. | Detects internal defects like solder voids, bridging, and insufficient solder, which are not visible through optical inspection. | X-ray radiography or tomography |
In-Circuit Testing (ICT) | Tests individual components and the circuit board's connectivity by applying electrical signals and measuring the response. | Verifies if each component is functioning and properly connected; ideal for mass production. | Bed of nails or flying probe testers. |
Functional Testing (FCT) | Tests the assembled PCB under simulated operating conditions to evaluate its performance. | Ensures the assembled board performs as designed and meets the required specifications. | Customized test fixtures and software. |
Solder Paste Inspection (SPI) | Measures the amount of solder paste deposited on the PCB pads before component placement. | Verifies that the correct amount of paste is applied, preventing solder joint defects. | 3D optical measurement |
In addition to these core testing methods, manufacturers will employ several other strategies to assure quality. These may include incoming quality control of raw materials (components and PCB substrates), strict adherence to manufacturing process controls, and environmental testing (temperature, humidity, vibration) to assess board robustness. It is also necessary for PCB assembly manufacturers to maintain the appropriate certifications, such as ISO 9001 or AS9100, as evidence of their commitment to quality and adherence to industry best practices. These certifications ensure that the manufacturer has established, documented and is following quality management systems and processes. Furthermore, it’s necessary to select a manufacturer with a commitment to continuous improvement and a culture of quality.
Frequently Asked Questions About Electronic PCB Assembly
This section addresses common questions regarding electronic PCB assembly, providing clear, concise answers to help you navigate the complexities of the manufacturing process and choose the right partner. We delve into manufacturer selection, cost considerations, and process details to ensure you have the necessary information.
- Who is the best PCB manufacturer?
The 'best' PCB manufacturer is subjective and depends heavily on your specific project needs. Factors to consider include the complexity of your design, volume requirements, required certifications, and desired turnaround time. There isn't a single 'best' manufacturer but rather a best fit for your unique situation. Researching manufacturers based on their specialized areas is critical. - How much does it cost to get a PCB assembled?
The cost of PCB assembly is influenced by several key variables. These include the complexity of the PCB design (number of layers, component density), the quantity of boards required, the type of components used (surface mount vs. through-hole), the level of testing needed (AOI, functional testing), and the geographical location of the assembly facility. Obtaining quotes from multiple manufacturers is advised to find the best price to performance ratio. Be transparent about your project needs to get accurate quotes. - What certifications should a PCB assembly manufacturer have?
Key certifications demonstrate a manufacturer's commitment to quality and industry standards. Common certifications include ISO 9001 (Quality Management System) and AS9100 (Aerospace Quality Management). Depending on the industry or application, additional certifications like ISO 13485 (Medical Devices) or IATF 16949 (Automotive) may be required. Confirming that your manufacturer holds the necessary certifications ensures that they adhere to rigorous industry standards. - What is the typical lead time for PCB assembly?
Lead times for PCB assembly can vary greatly based on multiple factors. These factors include the order complexity, volume of the order, materials availability, and the manufacturer's current workload. Simple, prototype orders may have a lead time of a few days to a week, while large-scale, complex orders could take several weeks. It’s important to get a clear lead time from your selected manufacturer before committing to the order, to plan your product schedule accurately. - What is the difference between SMT and through-hole assembly?
Surface Mount Technology (SMT) involves components mounted directly on the surface of the PCB, offering greater miniaturization and automation. Through-hole assembly requires components to be inserted through holes in the PCB and then soldered on the opposite side, which is generally used for larger components requiring strong mechanical connections or in low volume specialized boards. SMT is the dominant method for high volume production due to efficiency, where through-hole is typically reserved for larger components. - What testing methods are typically used in PCB assembly?
Common testing methods include Automated Optical Inspection (AOI), which uses cameras to check solder joints and component placement; X-ray inspection, which is used to examine hidden solder joints and internal layers; and functional testing, which verifies that the assembled board operates according to its design specifications. These tests ensure the reliability and performance of the PCB assembly, so select a manufacturer who has these capabilities and a robust QC process. - Should I choose a domestic or overseas PCB assembly manufacturer?
The choice between domestic and overseas manufacturers depends on various factors. Domestic manufacturers often provide faster turnaround times, better communication, and potentially higher quality due to more robust regulations. Overseas manufacturing may be more cost-effective, particularly for high-volume orders, but may pose challenges in communication and logistics. Carefully consider your needs for turnaround time, quality requirements, and budget before deciding.
Building a Successful Partnership with Your Electronic PCB Assembly Manufacturer

Establishing a robust and successful partnership with your electronic PCB assembly manufacturer is paramount to ensuring consistent quality, timely delivery, and cost-effectiveness. This relationship should be viewed as a strategic alliance, where open communication, transparent practices, and collaborative efforts are pivotal for long-term success.
- Clear Communication Channels
Establishing clear and consistent communication channels is critical. This includes designating points of contact, setting up regular meetings, and implementing a system for addressing queries and concerns promptly. Consistent communication ensures both parties are aligned on project goals and specifications. - Transparent Pricing
A transparent pricing model builds trust and fosters a strong partnership. The manufacturer should provide detailed breakdowns of costs, including materials, labor, and other expenses. This level of transparency allows for effective budgeting and prevents unexpected cost escalations. - Collaborative Design Reviews
Engage in collaborative design reviews with the manufacturer. Their expertise can be invaluable in identifying potential design flaws or suggesting improvements that can enhance manufacturability, reduce costs, and improve the performance of the final product. This collaborative approach is beneficial during the initial design phase and throughout the production process. - Regular Performance Reviews
Schedule regular performance reviews to assess the manufacturer's performance based on agreed-upon metrics, such as quality, delivery time, and responsiveness. These reviews provide an opportunity for continuous improvement and help maintain a high level of accountability. - Long-Term Vision
A successful partnership requires a shared long-term vision. Both the customer and the manufacturer should work towards common goals, such as continuous improvement in quality and efficiency, as well as growth and innovation. This long-term perspective is essential for building a mutually beneficial and lasting relationship.
The Future of PCB Assembly and Technology Trends
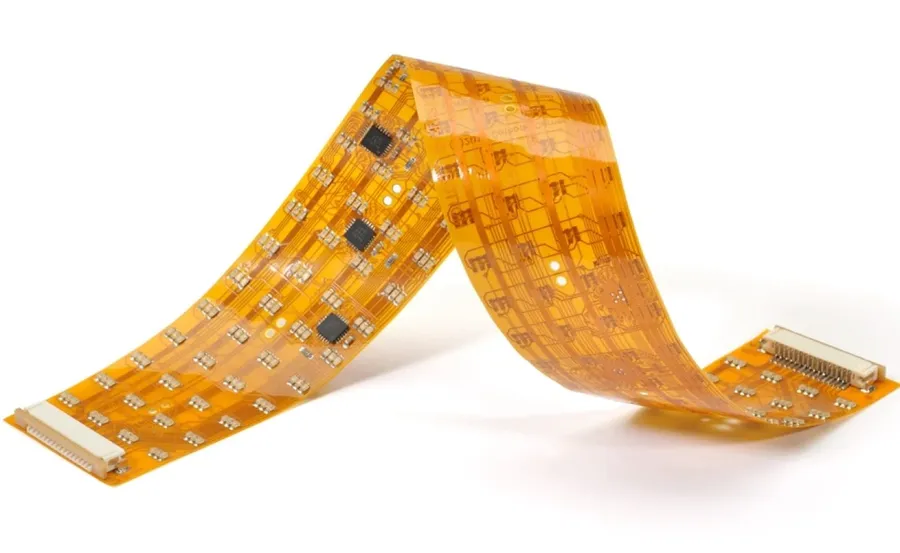
The electronic PCB assembly landscape is rapidly evolving, driven by the demand for smaller, more powerful, and more reliable electronic devices. This section explores the key trends shaping the future of PCB assembly, providing insights into how these advancements will impact the selection of manufacturing partners and the design process.
These trends not only present challenges, but also provide opportunities for innovation in design and manufacturing, ensuring the ongoing evolution of electronics. Keeping abreast of these developments is essential for anyone involved in the production or development of electronic devices.
- Miniaturization and High-Density Interconnect (HDI)
The relentless push towards smaller and more compact electronic devices necessitates miniaturization in PCB assembly. This includes finer traces and spaces, smaller components (e.g., 0201 and 01005 passives), and the use of HDI technologies such as microvias and buried vias. Manufacturers need advanced equipment and expertise to handle these complexities. - Advanced Materials
New materials are continuously being developed to enhance PCB performance and reliability. These include: high-frequency laminates for faster signal transmission, thermally conductive materials for better heat dissipation, and flexible substrates for wearable and bendable electronics. Manufacturers must be able to work with these advanced materials, which may require special processes and handling. - 3D Printing of PCBs
Additive manufacturing techniques such as 3D printing are beginning to play a role in PCB prototyping and even low-volume production. This can enable more complex geometries and potentially faster turnaround times for specialized applications. However, it may not be suitable for all production needs, especially where fine tolerances or very high volumes are required. - Automated Assembly Processes
Automation and robotics are becoming increasingly important in PCB assembly to improve efficiency, reduce errors, and handle complex tasks. This includes automated component placement, soldering, and inspection, which improve throughput and ensures consistent quality. Manufacturers that invest in automated systems will likely offer higher-quality products at lower prices. - Embedded Components
Embedding components directly within the layers of the PCB is becoming more prevalent. This offers greater density and component protection while reducing overall size. Manufacturers require specific techniques for embedding components effectively. - Increased Focus on Sustainability
Driven by global environmental concerns, the industry is trending towards more sustainable manufacturing practices, which include using eco-friendly materials and recycling components. Manufacturers with eco-friendly processes will likely be more sought after in the future.
Choosing the right electronic PCB assembly manufacturer is a critical decision that impacts the overall success of your product. By carefully considering your needs, evaluating potential partners on key criteria such as expertise, technology, quality control, and cost, you can secure a reliable partner that can bring your designs to life with precision and quality. Partnering with a experienced and skilled electronic pcb assembly manufacturer ensures quality and speed in the development of cutting edge technologies.
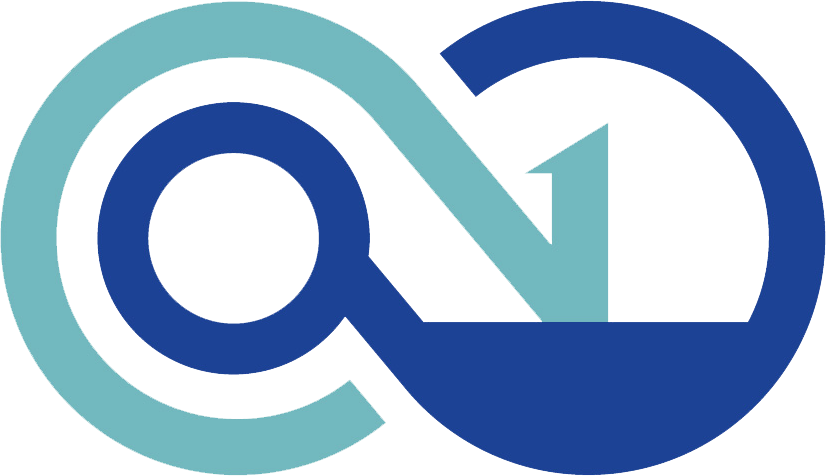