Choosing the Right Flex Rigid PCB Manufacturer: A Comprehensive Guide
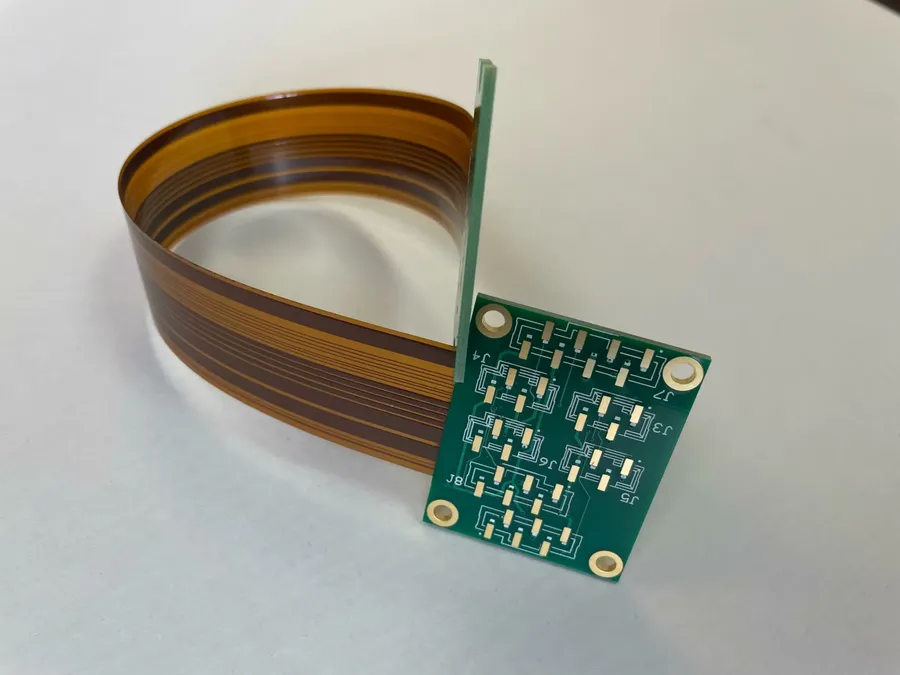
In today's world of compact and innovative electronics, flexible and rigid-flex printed circuit boards (PCBs) are increasingly vital, acting as the nervous system of countless devices. Finding the right flex rigid PCB manufacturer is crucial for any project requiring a blend of flexibility and structural strength. This article provides a comprehensive guide, navigating the nuances of selecting the optimal manufacturing partner and empowering you with the knowledge to make informed decisions.
Understanding Flex and Rigid-Flex PCBs
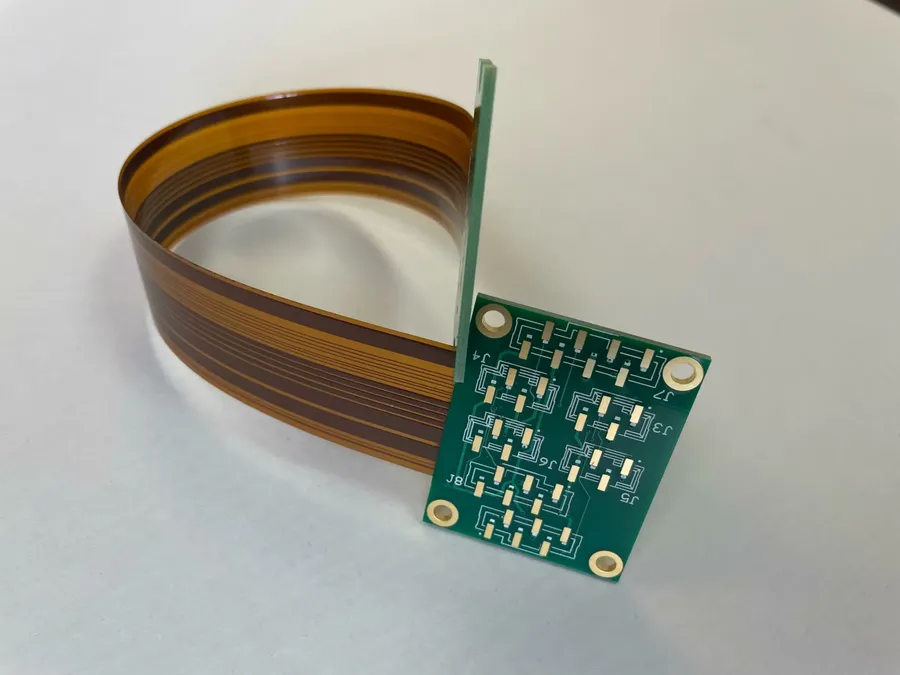
Flexible printed circuit boards (PCBs), often called flex PCBs, and rigid-flex PCBs represent two distinct approaches to circuit board design, each offering unique advantages. Flex PCBs are characterized by their ability to bend and conform to various shapes, while rigid-flex PCBs combine the benefits of both rigid and flexible boards into a single interconnected structure. This section elucidates the core differences, applications, and advantages of these technologies.
Feature | Flex PCB | Rigid-Flex PCB |
---|---|---|
Flexibility | Highly flexible, can bend and fold | Combines rigid and flexible sections |
Construction | Typically composed of flexible materials like polyimide | Composed of both rigid materials (e.g., FR-4) and flexible substrates |
Layer Count | Single-sided, double-sided, or multi-layer | Often multi-layered with connections between rigid and flex areas |
Applications | Dynamic flexing, tight spaces, wearable electronics | Complex devices, high-density packaging, and space-constrained applications |
Cost | Generally less expensive for simpler designs | Generally more expensive due to complexity and additional processing |
Assembly | Can require specific handling during assembly | Combines standard rigid PCB assembly with specialized flex handling |
The flexibility of flex PCBs enables them to be used in applications requiring dynamic bending or folding, such as in medical devices, wearable electronics, and automotive systems. Rigid-flex PCBs provide a more robust solution, enabling complex interconnectivity within a confined space, often used in aerospace, military, and high-end industrial equipment. The choice between them depends heavily on the specific demands of the application.
Key Factors to Consider When Choosing a Manufacturer
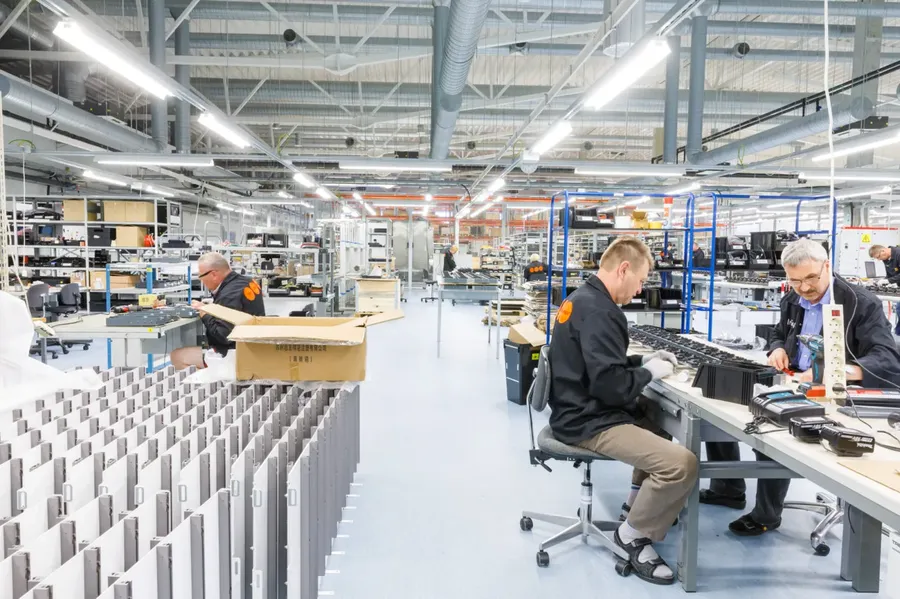
Selecting the right flex rigid PCB manufacturer is crucial for ensuring the success of your project. This decision hinges on several key factors that go beyond just cost, encompassing a manufacturer's capabilities, expertise, and commitment to quality. A comprehensive evaluation across these aspects will lead to a reliable and high-performing partnership.
- Manufacturing Capabilities
Assess the manufacturer's ability to handle your specific requirements, including layer count, material compatibility, impedance control, and the precision of their tolerances. This ensures they can reliably produce your desired design. - Material Expertise
Verify their knowledge of flex and rigid materials (such as Polyimide and FR4), as material choice significantly affects PCB performance and durability. A manufacturer should guide you in selecting the optimal material based on your application. - Certifications and Standards
Look for ISO certifications and adherence to IPC standards, which indicate a commitment to quality and process control. These certifications help to ensure that the manufacturer has a standardized approach to quality and can reliably produce high-quality boards. - Quality Control Processes
Examine the manufacturer's quality control procedures at each stage of production, from material intake to final inspection. This includes ensuring that appropriate testing equipment and personnel are in place to detect and address potential flaws.
Manufacturing Capabilities and Specializations
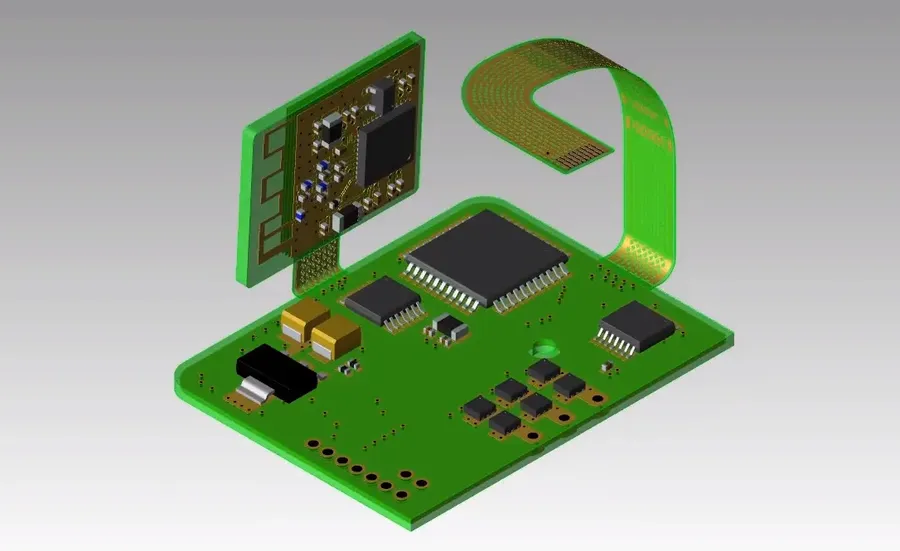
A critical aspect in selecting a flex rigid PCB manufacturer is evaluating their technological prowess. This encompasses several key areas, including the complexity of layer counts they can handle, their proficiency in managing various materials, the maximum panel size they can process, their capability for precise impedance control, and their ability to achieve tight manufacturing tolerances. These factors collectively determine the suitability of a manufacturer for specific project requirements.
Capability | Description | Importance |
---|---|---|
Layer Count | Number of conductive layers in the PCB. | Determines circuit complexity; higher counts for intricate designs. |
Material Handling | Expertise in managing different materials (e.g., polyimide, FR4). | Ensures compatibility and performance based on application requirements. |
Maximum Panel Size | Largest size of PCB that the manufacturer can process. | Affects design flexibility, yield, and cost for large layouts. |
Impedance Control | Ability to maintain a specific electrical resistance. | Critical for high-frequency signal integrity and performance. |
Tight Tolerances | Precision in dimensions and features of the PCB. | Necessary for high-density and precision-engineered circuits. |
Material Selection and Compatibility
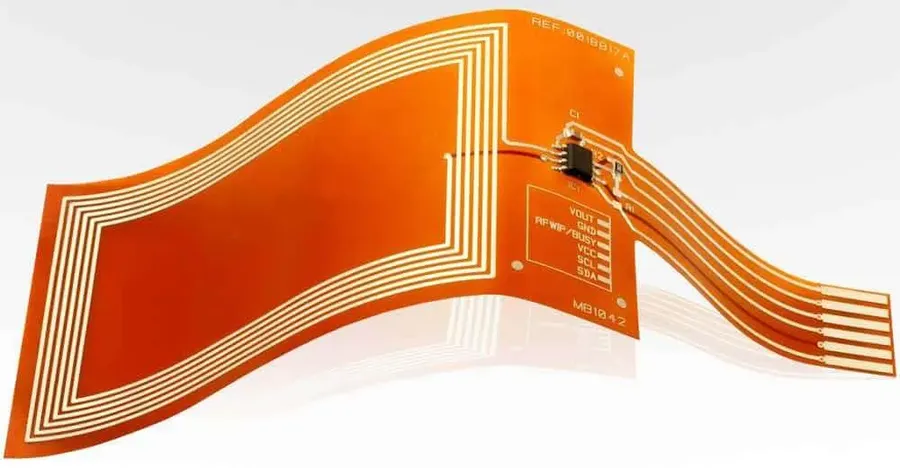
The selection of materials is paramount in the design and manufacturing of flex and rigid-flex PCBs, directly influencing performance, reliability, and longevity. A capable manufacturer will possess in-depth knowledge and a wide array of material options to meet the unique demands of diverse applications.
Material | Description | Typical Applications | Advantages | Disadvantages |
---|---|---|---|---|
Polyimide (PI) | A high-performance polymer known for its excellent flexibility, thermal stability, and chemical resistance. | Flexible circuits in aerospace, medical devices, and high-temperature environments. | Excellent flexibility, high-temperature resistance, chemical resistance | Higher cost compared to other materials, can absorb moisture. |
FR-4 | A glass-reinforced epoxy laminate, commonly used for rigid PCB cores. | Rigid sections of rigid-flex PCBs, standard electronic devices | Cost-effective, readily available, good mechanical strength. | Not flexible, limited thermal resistance compared to polyimide. |
Polyester (PET) | A thermoplastic polymer offering good dielectric properties and flexibility. | Low-cost flex circuits, membrane switches, and consumer electronics. | Low cost, good flexibility, ease of processing | Lower temperature resistance, limited chemical resistance. |
Liquid Crystal Polymer (LCP) | High-performance polymer with superior dimensional stability and electrical performance. | High-frequency applications, advanced packaging, and high-density interconnects. | Excellent electrical properties, low moisture absorption, good dimensional stability. | More expensive than other materials. |
A critical aspect of material selection is ensuring compatibility between the flexible and rigid portions of a rigid-flex PCB. The coefficient of thermal expansion (CTE) of each material must be considered to prevent stress and potential failure during thermal cycling. Manufacturers should possess the expertise to recommend material pairings that offer optimal performance and reliability. Furthermore, the chosen materials must align with the intended application environment regarding temperature range, chemical exposure, and mechanical stresses.
Quality Control and Certifications
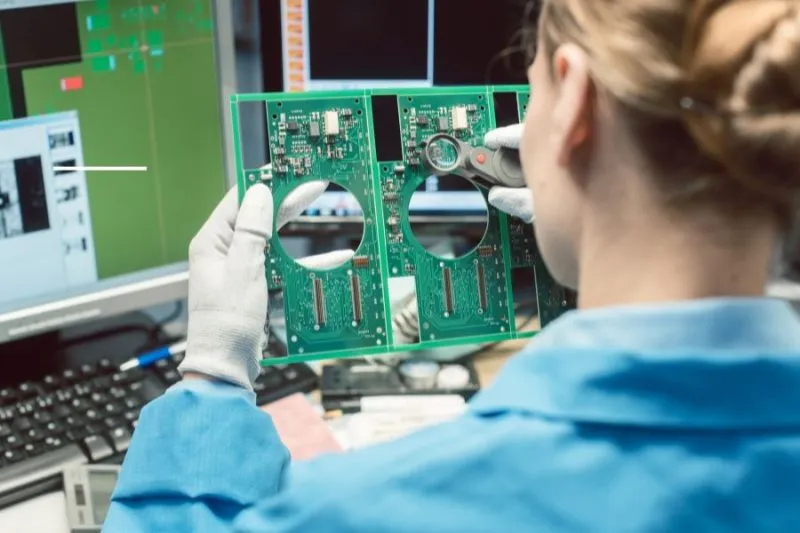
Rigorous quality control and adherence to industry certifications are paramount when selecting a flex rigid PCB manufacturer. These measures minimize defects, ensure reliability, and provide assurance that the final product meets stringent performance standards. A manufacturer's commitment to quality is directly linked to the longevity and success of the electronic device incorporating the PCB.
- ISO Certifications
ISO certifications, such as ISO 9001, demonstrate a manufacturer's commitment to maintaining a robust quality management system. This certification ensures consistent manufacturing processes, documentation, and continuous improvement efforts, which ultimately translate into more reliable PCBs. Furthermore, other relevant ISO certifications related to specific industries may be beneficial. - IPC Standards
Adherence to IPC standards, particularly IPC-A-600 (Acceptability of Printed Boards) and IPC-6012 (Qualification and Performance Specification for Rigid Printed Boards), is critical. These standards define the acceptable criteria for PCB manufacturing and assembly, guaranteeing that the manufacturer adheres to industry best practices and ensuring the consistent quality of the delivered product. For flex PCBs, IPC-6013 is a standard to consider. Different classes (Class 1, Class 2, and Class 3) within these standards reflect varying levels of product reliability based on intended end-use, for example, medical electronics require a higher level of performance and reliability than consumer electronics. - Robust Quality Assurance Processes
In addition to certifications, a reputable manufacturer will implement comprehensive quality assurance (QA) processes. These processes should include a thorough inspection at each stage of production, such as incoming material inspection, in-process checks, and final inspection. Techniques used may include Automated Optical Inspection (AOI), X-ray inspection, and electrical testing to identify any potential defects or deviations from specified requirements. Traceability of materials and manufacturing steps is also essential for quick issue identification and root cause analysis. - Material Traceability
A robust quality system includes the ability to track all materials used in the manufacturing process. This traceability ensures that any issues can be traced back to the source, allowing for quicker resolution and the prevention of future errors. - Importance of these Processes
Failing to adhere to robust quality control and certification guidelines can result in defects in the manufactured PCB, leading to product failures, costly recalls, and damage to your brand's reputation. The selection of a manufacturer with high quality control standards and certifications is a critical component of product success.
Cost Considerations and Pricing Strategies
Selecting a flex-rigid PCB manufacturer involves a crucial assessment of cost, which goes beyond the per-unit price. Understanding various pricing models, tooling charges, and the crucial balance between cost and quality is paramount for budget management and project success. This section details key cost factors and strategies to evaluate when choosing a manufacturing partner.
Cost Factor | Description | Impact |
---|---|---|
Unit Price | The cost per PCB. Typically decreases with higher volume orders. | Directly impacts overall project budget. |
Tooling Costs | Non-recurring expenses for creating the necessary tools and setups, such as stencils and custom jigs. | Significant for small runs or custom designs, less impact for larger volumes. |
NRE (Non-Recurring Engineering) Charges | One-time fees for design review, test fixture development, and process setup. | Impactful for prototypes and small batch runs, may be waived for recurring orders. |
Material Costs | Price of raw materials such as Polyimide, FR4, adhesives, and copper. | Highly variable based on material selection and market fluctuations. |
Layer Count | More complex boards with higher layer counts lead to increased costs. | Complexity and material usage drive up costs, impacts functionality. |
Assembly Costs | Expense related to populating the PCB with electronic components. | Varies based on component density and complexity. |
Testing and Inspection | Costs associated with various tests including electrical testing, AOI, and functional testing. | Essential for quality assurance, can impact final price. |
Shipping and Handling | Expenses to deliver finished boards | Affects overall project budget, needs careful planning. |
When evaluating manufacturers, it's imperative to scrutinize the pricing structure for different production volumes. Prototype runs, small batch production, and large-scale orders often carry different pricing scales. Tooling charges are a significant consideration, particularly for initial orders of complex flex-rigid PCB designs.
Additionally, manufacturers may offer a fixed-cost per panel, or charge by area. Understanding these nuances will help in making cost-effective decisions.
The balance between cost and quality is a critical consideration. While price is important, choosing the cheapest option can result in subpar quality and costly rework. Evaluate the manufacturer's quality control and reliability track record alongside pricing. A slightly higher cost from a reputable manufacturer could lead to long-term savings through better reliability and reduced product failures.
Lead Times and Delivery Schedules
Efficient lead times and reliable delivery schedules are paramount in the selection of a flex rigid PCB manufacturer. These factors directly impact project timelines and overall success, making it essential to thoroughly evaluate a manufacturer's production capabilities and logistical efficiency.
Several interconnected factors influence lead times, including the complexity of the design, material availability, the manufacturer's current workload, and the quantity of PCBs ordered. It is vital to understand these variables to accurately assess a potential manufacturer's ability to meet your deadlines.
A manufacturer's production capacity, often measured in panels per week or month, indicates their ability to handle your order volume, and manufacturers specializing in flex and rigid-flex PCBs may have different limitations compared to conventional PCB manufacturers. Clear communication with the manufacturer is crucial to understand their capabilities and to ensure that their lead time estimations are aligned with project requirements.
Furthermore, a robust delivery schedule involves more than just manufacturing; it includes thorough quality checks, packaging, and shipping logistics. Manufacturers should have established procedures to track shipments, offer delivery updates, and resolve any issues that may arise during transit. Delays in shipment can offset carefully planned project schedules, therefore, detailed logistical planning and transparent communication of any foreseeable issues are critical.
Frequently Asked Questions About Flex Rigid PCBs
This section addresses common questions concerning the design, materials, and manufacturing limitations of flexible and rigid-flex printed circuit boards, providing clear and concise answers to aid in your decision-making process.
- What are the key design considerations for flex-rigid PCBs?
Key design considerations include managing the transition areas between the rigid and flexible sections to minimize stress, ensuring adequate copper trace adhesion to withstand bending, and accounting for material flexibility in calculations. Additionally, proper impedance control and via design are critical for maintaining signal integrity across the entire PCB. - Which materials are commonly used in flex and rigid-flex PCB manufacturing?
Common materials include Polyimide (PI) for the flexible layers, offering excellent thermal and mechanical properties, and FR4 (Flame Retardant 4) for the rigid sections. Other materials may include flexible adhesives, coverlays, and stiffeners, depending on the application requirements. The choice depends on factors such as operating temperature, chemical resistance, and flexibility demands. - What are the typical manufacturing limitations for flex-rigid PCBs?
Manufacturing limitations may include maximum panel size, minimum trace width and spacing, layer count limitations, and tight tolerance requirements in the flex region. Bending radius, via design, and impedance control are additional challenges that need careful planning to ensure a reliable design. Furthermore, the assembly process requires more manual intervention that can impact production scalability. - How do I choose the correct thickness for my flex and rigid-flex PCB?
The appropriate thickness depends on various factors, including the required flexibility, operating environment, and mechanical stresses. Generally, thinner flexible layers enhance bending capabilities, while thicker rigid sections offer stability. The overall thickness must accommodate component assembly and ensure the PCB meets its structural and operational requirements. Furthermore, the material type must be able to cope with the thickness requirements without degrading overall performance. - What is the typical cost difference between rigid, flex and rigid-flex PCBs?
Rigid PCBs are typically the most cost-effective, flex PCBs are more expensive due to the specialized materials and processes. Rigid-flex PCBs are often the most expensive due to the complex manufacturing procedures of bonding flexible and rigid layers. The cost is also affected by material types, layer count, design complexity, and production volume; it's critical to balance cost with performance when selecting these options. - Are there specific design guidelines for vias in a rigid-flex PCB?
Yes, vias in a rigid-flex PCB should be carefully designed to minimize the risk of cracking or failure, especially in the transition areas. Vias in the flexible regions should ideally be designed with tear drops and plated to accommodate bending. Vias should be placed further away from the bend lines to avoid mechanical stress and potential issues such as through hole cracks. Furthermore, using blind or buried vias within the rigid sections can simplify routing and improve density. - What type of testing is needed to ensure the reliability of flex-rigid PCBs?
Reliability testing should include flex testing, impedance control checks, thermal stress testing, and visual inspection of critical areas. Electrical testing should be comprehensive to ensure proper functionality of the flex and rigid regions, along with component assembly. Accelerated life testing can also be used to identify potential failure points and predict long-term reliability and performance.
Top Flex Rigid PCB Manufacturers Comparison
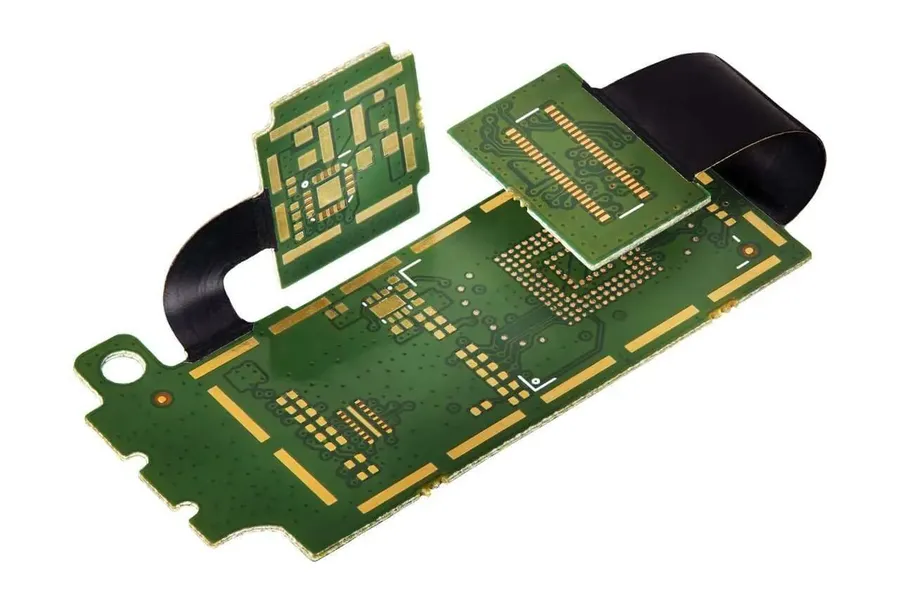
Selecting the ideal flex rigid PCB manufacturer requires a comprehensive evaluation of their capabilities, expertise, and alignment with your specific project requirements. This section provides a comparative analysis of leading manufacturers, highlighting their strengths, weaknesses, and specializations to facilitate an informed decision.
Manufacturer | Strengths | Weaknesses | Specializations | Typical Application |
---|---|---|---|---|
Company A | High-layer count capabilities, advanced material handling | Higher cost for small volume production, longer lead times on complex designs | Aerospace, Medical devices with high precision needs | Advanced instrumentation |
Company B | Strong prototype and small batch production, quick turnaround | Limited capabilities for very complex multilayer structures | Consumer electronics, wearable technologies | Wearable Device |
Company C | Excellent cost-effectiveness for large-scale production, good material options | Less flexibility for highly customized designs or specialized materials | Automotive, industrial controls | Automotive sensors |
Company D | Specialization in flexible PCB materials, highly experienced | May not be as competitive for purely rigid-flex designs | Medical, implantable devices | Implantable Devices |
Company E | Strong international presence and global supply chain | May have longer lead times and potentially higher shipping costs | Telecommunications, global supply chain products | Telecommunications Equipment |
Selecting the right flex rigid PCB manufacturer requires careful consideration of various factors, from technical capabilities to quality control and cost-effectiveness. By thoroughly evaluating your options and aligning them with your project needs, you can ensure the successful implementation of your flex and rigid-flex PCB designs. Remember that the right manufacturer is a partner in your success, guiding you through the process and ensuring that your boards meet the highest standards of performance and reliability. Partnering with the right flex rigid PCB manufacturer is vital to bringing your innovative products to life.
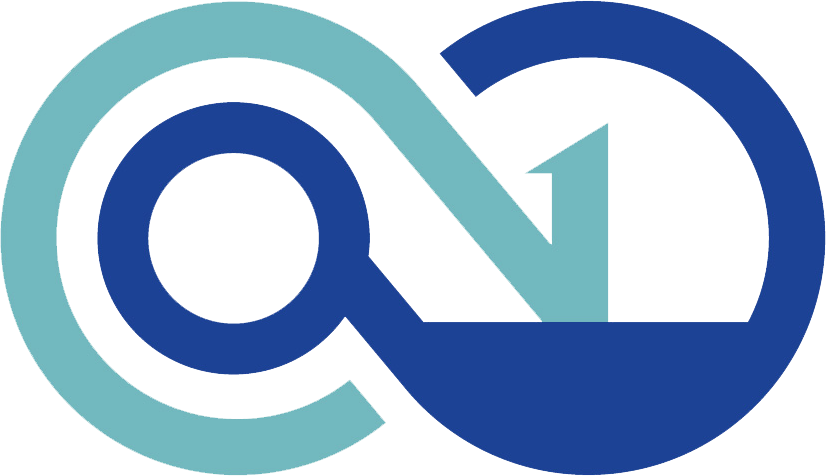