Choosing the Right Hi-Q PCB Manufacturer: A Comprehensive Guide
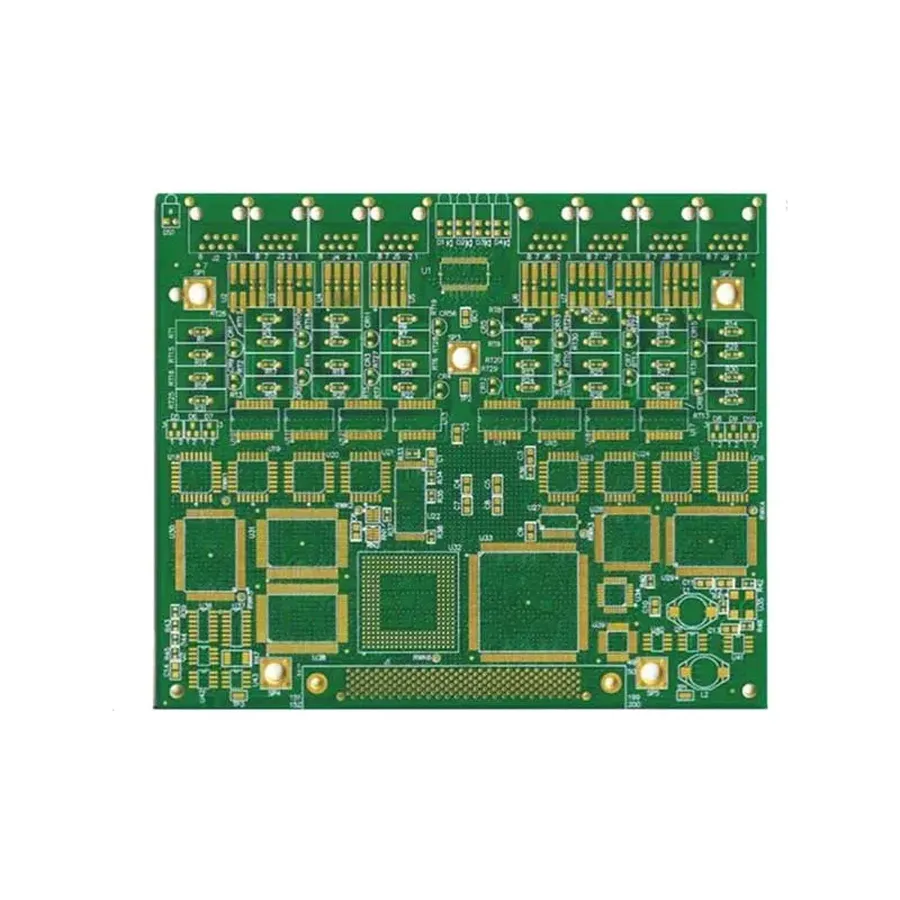
In today's rapidly evolving tech landscape, the demand for high-quality printed circuit boards (PCBs) is at an all-time high. From powering complex aerospace systems to everyday consumer electronics, PCBs form the backbone of countless applications. Choosing the right 'hi q pcb manufacturer' is not just about finding a supplier; it's about securing a reliable partner that understands your specific needs and delivers top-tier quality. This guide will help you navigate the critical aspects of selecting the right manufacturer to ensure your project's success, focusing on factors from certifications to customization capabilities.
Understanding the Importance of Hi-Q PCBs
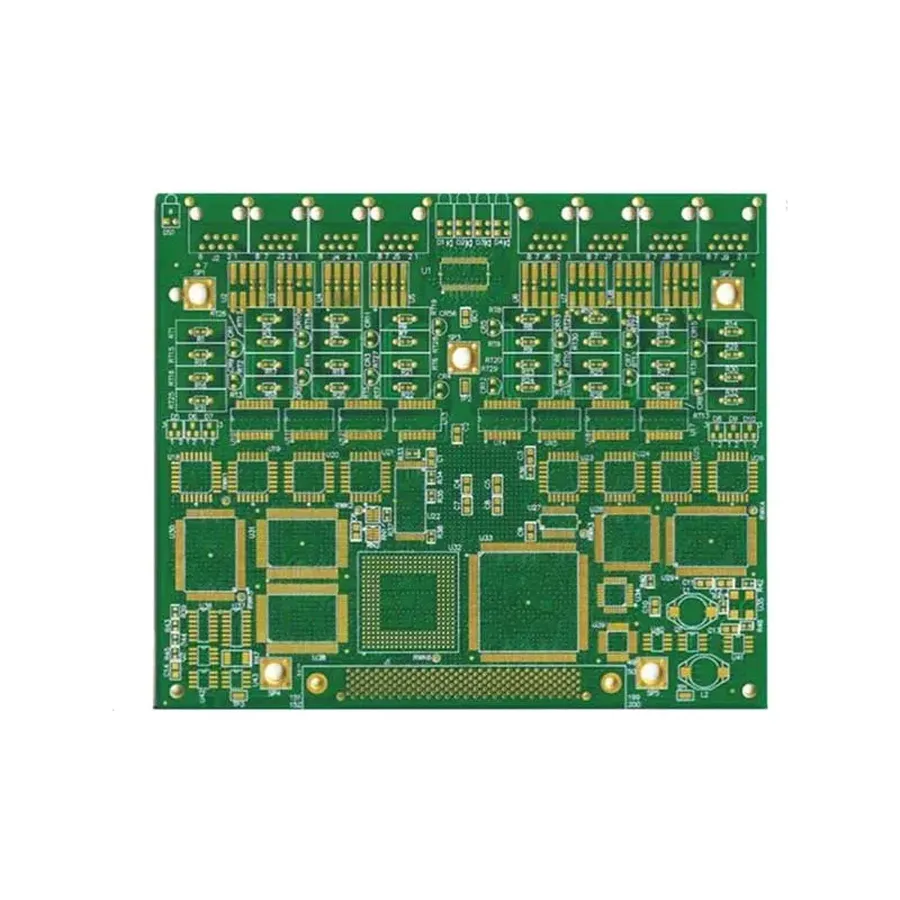
High-quality printed circuit boards (PCBs), often referred to as Hi-Q PCBs, are fundamental to the reliability, longevity, and performance of electronic devices. The selection of a reputable 'hi q pcb manufacturer' is not merely a logistical consideration but a strategic imperative that directly impacts the success of any electronic project. Conversely, employing low-quality PCBs can lead to a cascade of issues, including premature device failure, inconsistent performance, and increased maintenance costs. This section explores why opting for superior PCB manufacturing is crucial.
The performance of electronic devices is directly tied to the quality of their PCBs. High-quality PCBs, produced by a reputable 'hi q pcb manufacturer', exhibit superior electrical characteristics, such as low signal loss and stable impedance, ensuring signal integrity and efficient power delivery. They are constructed with high-grade materials and undergo rigorous testing, reducing the likelihood of failures due to shorts, opens, or delamination. This reliability is essential for devices operating in critical applications where failure is not an option.
Key Certifications and Standards for Hi-Q PCB Manufacturers
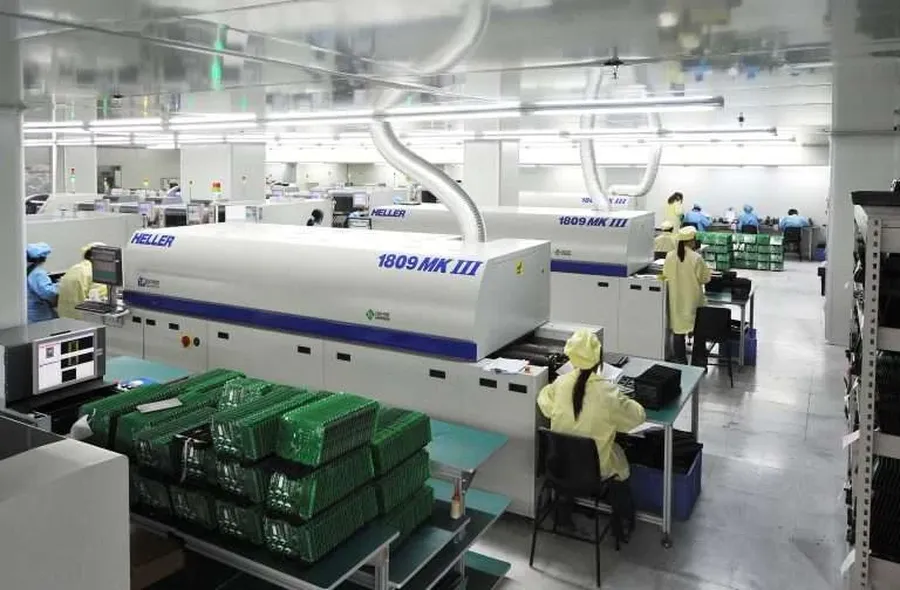
For a high-quality PCB, adherence to industry standards is paramount. Certifications such as ISO 9001, UL, and others serve as verifiable benchmarks of a manufacturer's commitment to quality. These certifications ensure that a 'hi q pcb manufacturer' operates under a robust quality management system, consistently delivering reliable and compliant products, which significantly reduces risk and enhances the overall performance and longevity of electronic devices.
Certification | Description | Relevance to Hi-Q PCB Manufacturing |
---|---|---|
ISO 9001 | An international standard for quality management systems, focusing on continuous improvement, customer satisfaction, and process efficiency. | Ensures the manufacturer has a documented and effective quality management system, crucial for consistent PCB production. |
UL Certification | A safety certification that indicates products have been tested for safety and comply with nationally recognized standards. | Confirms that the PCBs are safe for use in various applications, especially critical in high-power and sensitive electronic devices. |
IPC Standards (e.g., IPC-A-600, IPC-6012) | Industry standards set by the IPC - Association Connecting Electronics Industries. They cover acceptability of printed boards, qualification and performance specifications for rigid boards. | Compliance to these standards guarantees that PCB’s are manufactured to globally accepted standards for quality and reliability of PCBs. |
RoHS Compliance | Restriction of Hazardous Substances directive, limiting the use of specific hazardous materials like lead, mercury, cadmium, etc. | Demonstrates the manufacturer's commitment to environmental responsibility and ensures PCBs are safe for use and disposal. |
IATF 16949 | Quality management system standard specifically for the automotive industry. | Confirms rigorous quality controls and processes, which are applicable in many high-reliability applications beyond automotive. |
Evaluating Manufacturing Capabilities and Technologies
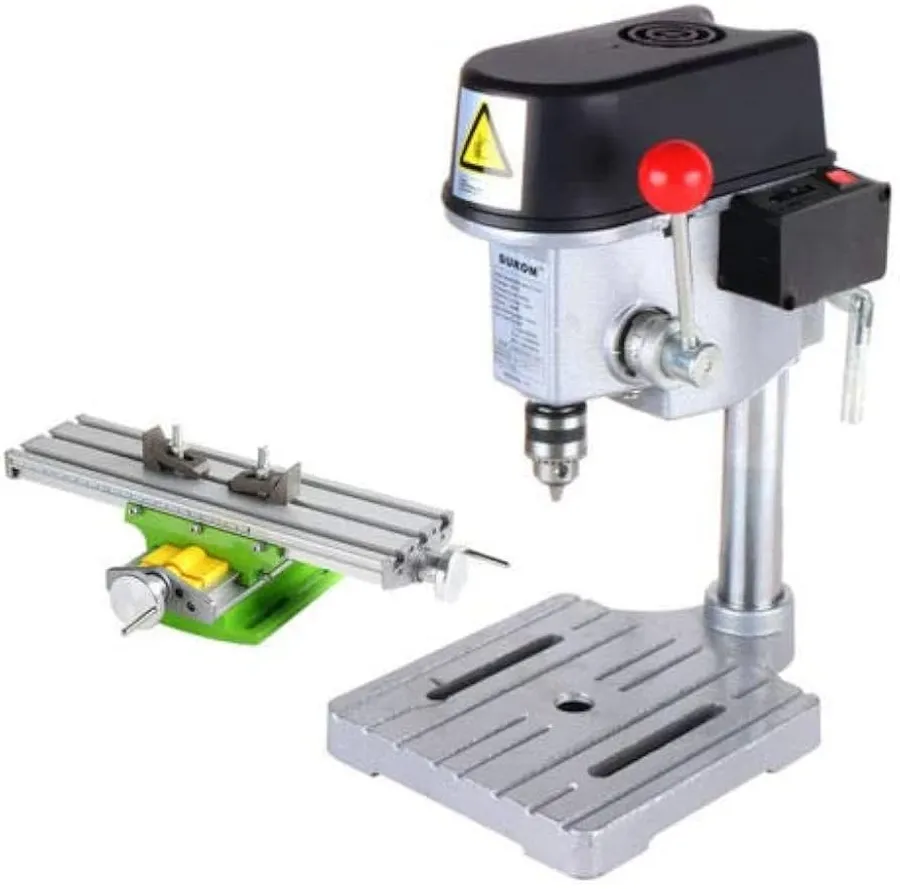
A critical aspect of selecting a 'hi q pcb manufacturer' is a thorough evaluation of their manufacturing capabilities and the technologies they employ. The sophistication of a manufacturer's equipment directly impacts their ability to produce high-quality, complex PCBs, including advanced designs using multilayer, flex, rigid-flex, and high-density interconnect (HDI) technologies. A top-tier manufacturer should demonstrate a commitment to investing in and utilizing cutting-edge technology, such as laser drilling and advanced plating techniques.
Technology | Description | Application | Key Considerations |
---|---|---|---|
Multilayer PCBs | PCBs with three or more conductive layers. They provide increased circuit density. | Complex electronics, requiring compact designs. | Layer count, material thickness, and impedance control capabilities. |
Flexible PCBs (Flex PCBs) | PCBs built on flexible substrates allowing them to bend and conform to specific shapes. | Applications needing flexibility and miniaturization, such as wearables and automotive electronics. | Flex material, bending radius and connection reliability. |
Rigid-Flex PCBs | Combination of rigid and flexible circuit boards. | Applications requiring both rigidity and flexibility, such as medical devices and aerospace applications. | Transition from rigid to flex areas, material compatibility and mechanical stress analysis. |
High-Density Interconnect (HDI) PCBs | PCBs with finer lines and smaller vias providing higher component density. | Advanced electronics, demanding miniaturization and high functionality. | Microvia size, layer alignment and advanced plating process. |
Laser Drilling | Precision drilling technology for small vias and microvias. | Critical for HDI PCBs and fine pitch designs. | Laser type, accuracy, consistency and speed of drilling. |
Material Selection and Its Impact on PCB Performance
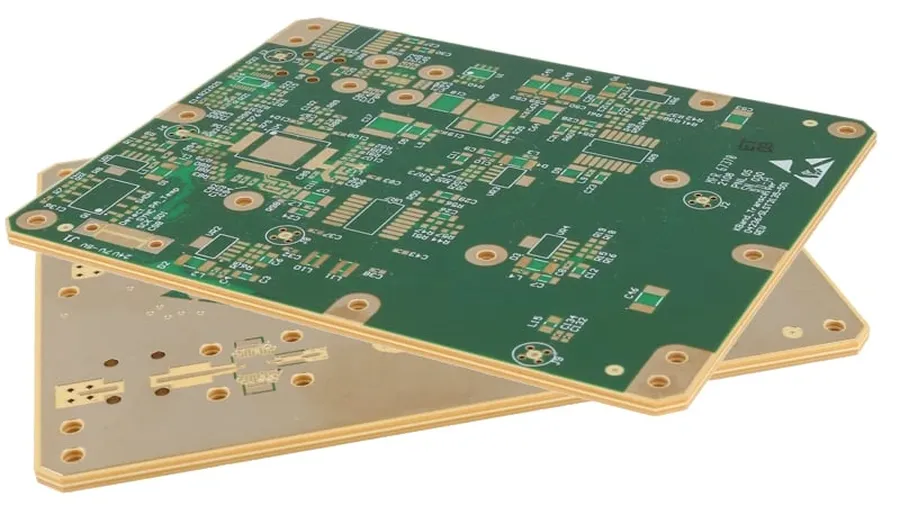
The selection of materials for printed circuit boards (PCBs) is paramount to their performance, directly influencing factors such as temperature resistance, signal integrity, and overall durability. A high-quality (Hi-Q) PCB manufacturer understands the nuanced relationship between material properties and application requirements, offering a range of options tailored to specific needs.
Material | Key Characteristics | Typical Applications | Advantages | Disadvantages |
---|---|---|---|---|
FR-4 | Glass-reinforced epoxy laminate, versatile and cost-effective. | General-purpose electronics, consumer devices. | Good balance of electrical and mechanical properties, widely available, low cost. | Limited high-frequency performance, moderate temperature resistance. |
Rogers Materials (e.g., 4350B, 4003C) | High-performance laminates with superior electrical characteristics. | RF and microwave applications, high-speed digital circuits. | Excellent dielectric constant stability, low loss tangent, high-frequency performance. | Higher cost, may require specialized fabrication techniques. |
Polyimide | High-temperature resistant polymer with excellent flexibility. | Flexible circuits, aerospace, automotive applications with extreme temperature conditions. | Exceptional temperature resistance, high tensile strength, flexible | Higher cost, can be more challenging to fabricate than FR-4. |
Metal Core PCBs (MCPCB) | Metal base, commonly aluminum, with a dielectric layer. | LED lighting, power electronics, thermal management applications. | Superior heat dissipation, mechanical stability, improved lifespan. | More complex manufacturing, higher cost compared to traditional PCBs. |
Teflon(PTFE) | Thermoplastic polymer with excellent electrical insulation. | High-frequency applications, microwave, aerospace | Extremely low dielectric loss, high chemical resistance, temperature stability. | High cost, special processing required due to its chemical resistance. |
- FR-4:
The most commonly used material due to its balance of cost and performance. However, it may not be suitable for high-frequency applications or extreme temperatures. - Rogers:
Preferred for applications requiring high signal integrity, such as RF and microwave circuits, where its low dielectric loss is critical. - Polyimide:
Offers high-temperature resistance and flexibility, making it suitable for flexible circuits and harsh environments. - Metal Core PCBs (MCPCB):
Ideal for applications requiring efficient heat dissipation, such as LED lighting, and power electronics. - Teflon(PTFE):
Offers exceptional high-frequency performance and stability, with the highest chemical and temperature resistance.
Customization Options Offered by Hi-Q PCB Manufacturers
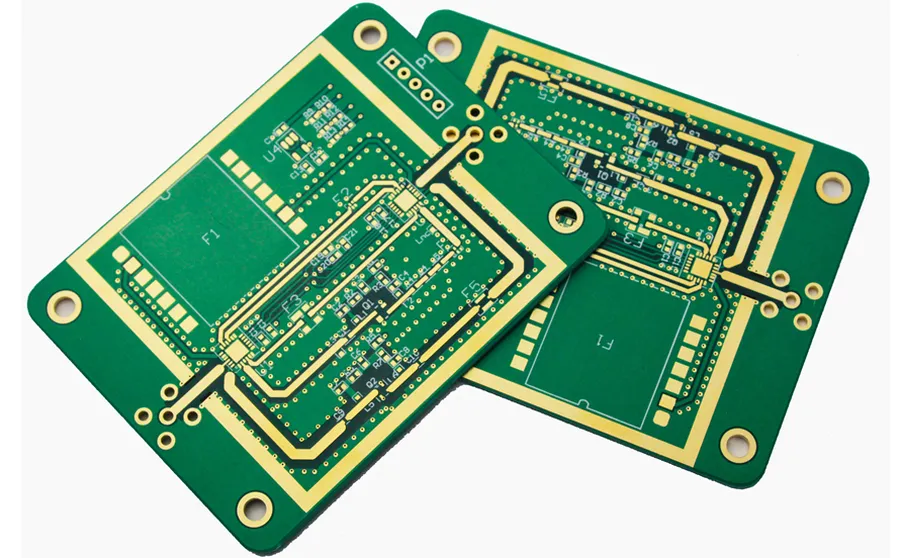
A critical aspect of selecting a 'hi q pcb manufacturer' lies in their capacity to provide customized solutions tailored to specific project requirements. This customization extends beyond standard offerings to include variations in board size, layer counts, and unique design features, necessitating a flexible manufacturing approach. An ideal manufacturer should not only accommodate these needs but also possess the agility to handle prototype orders, facilitating iterative design and testing processes.
- Board Size and Shape Customization
High-quality PCB manufacturers offer the flexibility to produce PCBs in various sizes and shapes, deviating from standard rectangular formats to accommodate unique device enclosures or spatial constraints. This ensures optimal fit and performance within the intended application. - Layer Count Flexibility
Manufacturers provide a range of layer count options, from single-layer to complex multilayer boards, enabling the creation of circuits with varying degrees of complexity and density. This is crucial for designs requiring multiple signal layers or power planes. - Unique Design Features
A superior PCB manufacturer can accommodate unique design requirements, such as impedance control, via-in-pad technology, or specific plating finishes. These features are essential for optimizing signal integrity and performance in high-speed applications. - Prototype Manufacturing
An essential service offered by a hi-q PCB manufacturer is the ability to produce small prototype batches rapidly. This allows for testing and validation of designs before committing to large-scale production. This service is crucial for identifying design flaws early in the process, saving both time and cost in the long run. - Design Assistance and Consultation
Many reputable manufacturers also offer design assistance and consultation services. This allows them to collaborate with clients, offering expert advice on design optimization, material selection, and manufacturability, ensuring the final product meets all specifications.
Lead Times, Production Volume, and Scalability
Efficient lead times, flexible production volumes, and scalability are critical when selecting a 'hi q pcb manufacturer'. Understanding a manufacturer's capabilities in these areas ensures that your project timelines are met, regardless of the required quantity, and that they can adapt to future growth.
Factor | Description | Implications |
---|---|---|
Lead Time | The time required from order placement to delivery of PCBs. | Directly affects project timelines; shorter lead times minimize delays. |
Production Volume | The manufacturer's capacity to produce PCBs in varying quantities. | Ensures a manufacturer can accommodate both small prototypes and large-scale runs. |
Scalability | The manufacturer's ability to adapt production to meet changing demand. | Allows for future expansion and flexibility without major disruption. |
A dependable 'hi q pcb manufacturer' will have established processes to handle fluctuations in demand, meeting delivery schedules, and offering options to expedite production when needed.
Quality Control and Testing Procedures
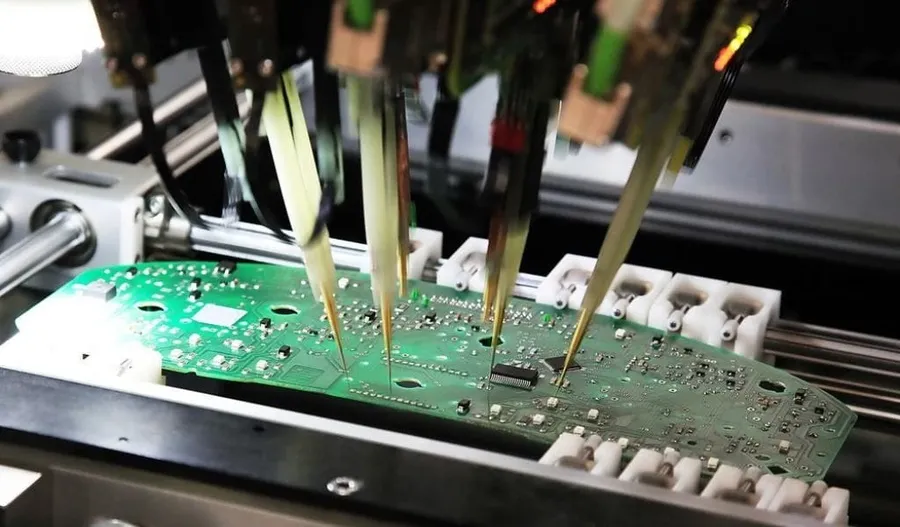
Rigorous quality control and testing procedures are paramount in ensuring the reliability and performance of printed circuit boards (PCBs). A high-quality (hi-q) PCB manufacturer employs a suite of inspection and testing methods to detect and rectify defects before boards are shipped to customers, thereby safeguarding the integrity of electronic devices and systems relying on these boards.
- Visual Inspection
Visual inspection is the first line of defense in identifying gross defects such as scratches, misalignments, or open circuits. Skilled inspectors carefully examine boards under magnification, identifying anomalies that may escape automated detection systems. - Automated Optical Inspection (AOI)
AOI employs high-resolution cameras and image processing algorithms to automatically detect a wide range of defects, including shorts, opens, and missing components. This method enhances the efficiency and accuracy of visual inspection, particularly for complex multilayer boards with intricate circuitry. - Electrical Testing
Electrical testing validates the performance and functionality of the fabricated PCB, including continuity, shorts, and impedance checks. Techniques such as Flying Probe Testing, Bed of Nails Testing, and Functional Testing are commonly utilized, based on the volume and complexity of the circuit. - X-Ray Inspection
X-Ray inspection is crucial for examining internal features and multilayer boards where visual inspection is insufficient, enabling the detection of solder voids, misalignment, and other hidden flaws. - Controlled Impedance Testing
Controlled impedance testing ensures the signal integrity of high-speed circuits. This is accomplished through time-domain reflectometry (TDR) which verifies that the trace impedance meets design specifications. - Environmental Testing
Environmental testing includes checks under extreme temperature, humidity, and vibration conditions to ascertain the reliability and robustness of the PCB and ensure consistent performance under adverse environmental conditions.
Frequently Asked Questions About Hi-Q PCB Manufacturers
Selecting the right Hi-Q PCB manufacturer is critical for the success of any electronics project. This section addresses common questions to guide you in making informed decisions and ensuring you partner with a manufacturer that meets your specific needs.
- Who is the best PCB manufacturer?
Determining the 'best' PCB manufacturer is subjective and depends on project requirements. Factors to consider include technological capabilities, material options, certifications, quality control measures, pricing, and customer support. There isn't one universally 'best' manufacturer; rather, the ideal choice is one that best aligns with your project's demands and budget. - What are the signs of a high-quality PCB manufacturer?
A high-quality PCB manufacturer demonstrates several key characteristics: comprehensive certifications (ISO 9001, UL, etc.), advanced manufacturing capabilities (multi-layer, HDI, flex PCBs), a wide range of material options, robust quality control and testing processes (AOI, electrical testing), transparent pricing and payment terms, and excellent customer support. Look for a commitment to continuous improvement and adherence to industry best practices. - How do I select a PCB manufacturer for my specific application?
Begin by identifying your specific application needs: required performance parameters (temperature, signal integrity, etc.), physical characteristics (size, layer count), materials, and budget. Research manufacturers that specialize in your particular requirements, request samples, and evaluate their responsiveness and technical expertise. Consider their experience with similar projects and check customer reviews and testimonials. - How do I evaluate the pricing and payment terms of a PCB manufacturer?
Pricing should be transparent, with a clear breakdown of costs per unit, tooling, and any other associated expenses. Compare quotes from multiple manufacturers, ensuring you're comparing like-for-like specifications. Evaluate payment terms – consider the balance between upfront costs and payment upon delivery. Look for a manufacturer that offers pricing flexibility based on order volume and long-term relationships. - What are the average lead times for PCB production, and how should I plan for them?
Lead times vary based on the complexity of the PCB, manufacturer capacity, and production volume. Simple boards might take a few days; complex ones could take several weeks. To plan effectively, communicate lead times early in the project. Always buffer additional time, in case of unforeseen issues or manufacturing delays, and factor shipping time for international orders. Check the manufacturer's capacity to handle fluctuations in demand. - What should I consider for international supply chains when choosing a PCB manufacturer?
When selecting an international PCB manufacturer, consider the impact of shipping costs, tariffs, and potential import/export regulations. Communication can be more challenging across time zones, so prioritize manufacturers with strong customer service and responsiveness. Consider political risks, the manufacturer’s production capacity, and supply chain disruptions. Quality control might be more difficult to enforce with international suppliers, making on-site audits important for large projects. - What are common problems that occur with PCBs and how does a manufacturer help avoid them?
Common PCB problems include shorts, opens, incorrect component placement, and material defects. A good PCB manufacturer will employ robust quality control procedures, including automated optical inspection, and electrical testing, that reduces the chance for manufacturing-related issues. They will communicate early about any potential problems and offer options for how to mitigate them.
Comparing Hi-Q PCB Manufacturers: A Practical Guide
Selecting the right high-quality (Hi-Q) PCB manufacturer is a critical decision that can significantly impact the success of your electronic project. A structured comparison is essential to ensure that the chosen manufacturer aligns with your specific requirements. This section offers a practical framework for evaluating potential Hi-Q PCB manufacturers based on key criteria, providing actionable insights for a simplified and informed decision-making process.
Criteria | Description | Evaluation Metrics | Importance |
---|---|---|---|
Certifications | Accreditation to quality standards like ISO 9001, UL, and others. | Presence and validity of relevant certifications. | High: Demonstrates adherence to industry-recognized quality management systems. |
Manufacturing Capabilities | Range of technologies offered, such as multilayer, flex, rigid-flex, and HDI PCBs. Equipment and process sophistication. | Variety of board types, technology, and equipment. | High: Ensures the manufacturer can handle your specific PCB design and complexity. |
Material Selection | Availability of various materials like FR-4, Rogers, and others based on application needs. | Material options and expertise in material selection. | High: Directly impacts PCB performance under different operational conditions. |
Customization Options | Flexibility in accommodating specific design needs, including board size, layer count, unique features, and prototype orders. | Ability to meet custom requirements and handle prototypes. | Medium: Crucial for projects that require tailored solutions. |
Lead Times and Production Volume | Typical turnaround time for production and the capacity to handle various production volumes. | Lead time, minimum and maximum production volumes. | Medium: Essential for managing project timelines and scalability. |
Quality Control | Rigor and processes used for quality control, including visual inspection, AOI, and electrical testing. | Testing methods and QC procedures in place. | High: Ensures the reliability of the manufactured PCBs. |
Pricing | Pricing structures and transparency in cost breakdown. | Competitiveness of pricing and payment terms | Medium: Important for project budgeting and cost-effectiveness. |
Experience and Specialization | Manufacturer's years of experience and specific areas of expertise. | Years of operation, market sector experience, and project specialization. | Medium: Provides assurance of proven expertise and specialized knowledge |
Customer Reviews and Support | Feedback and testimonials from previous customers and accessibility of customer support. | Customer feedback and support accessibility. | Medium: Demonstrates customer satisfaction and responsiveness. |
Choosing the right 'hi q pcb manufacturer' is a critical decision that can significantly impact your project's success. By thoroughly evaluating certifications, technologies, customization options, and quality control procedures, you can find a reliable partner that meets your specific needs. When selecting a manufacturer, keep in mind the importance of quality, reliability and efficiency in your PCB. Ensure your chosen ‘hi q pcb manufacturer’ is not just a supplier but a vital part of your supply chain, contributing to the overall quality and performance of your final product.
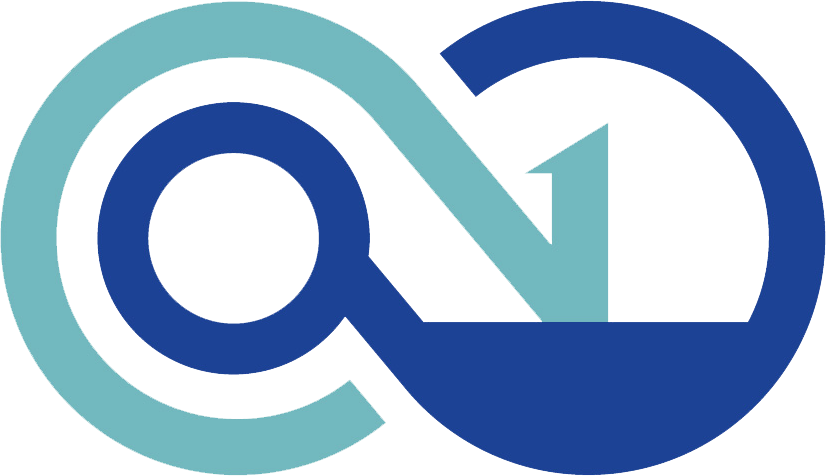