Choosing the Right Isola PCB Manufacturer: A Comprehensive Guide
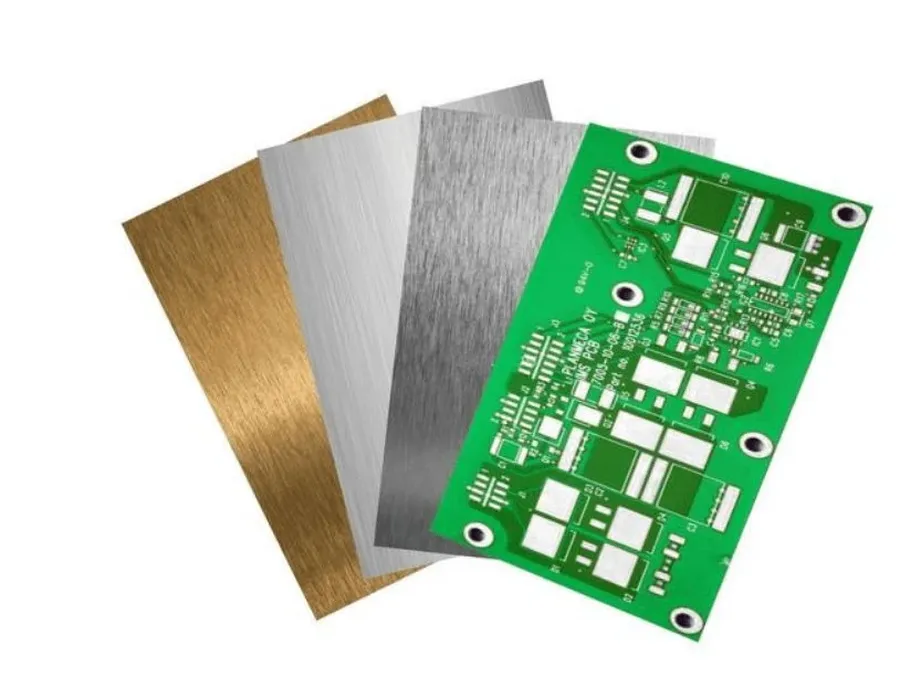
In today's fast-paced tech world, the foundation of most electronic devices lies in printed circuit boards (PCBs). Choosing the right PCB manufacturer, especially when it comes to specialized materials like those from Isola, is crucial for ensuring optimal performance and reliability. Isola is a global leader in producing high-quality copper-clad laminates and dielectric prepregs, making them a go-to choice for many PCB designs. This article provides an in-depth look at Isola PCBs, what they offer, and how to choose the right manufacturer.
Understanding Isola's Role in PCB Manufacturing
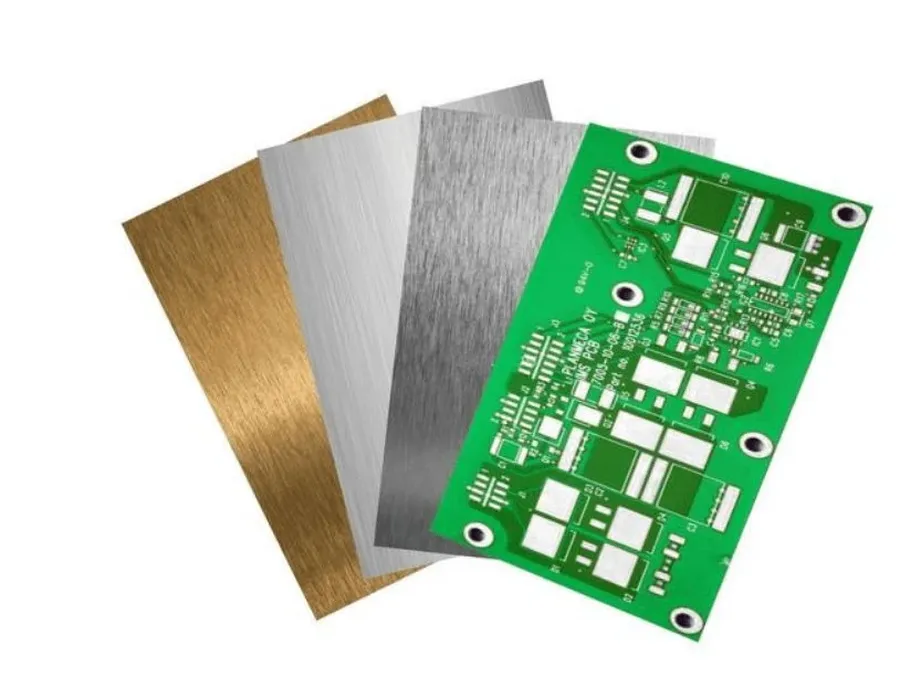
Isola stands as a critical force within the printed circuit board (PCB) industry, functioning not merely as a supplier of materials but as a key innovator in the design and production of high-performance PCB substrates. Their primary focus involves the engineering and manufacturing of the core dielectric materials, such as laminates and prepregs, that form the foundational layers of advanced PCBs, thereby directly influencing the electrical, thermal, and mechanical performance of the final product.
Key Isola PCB Materials and Their Applications
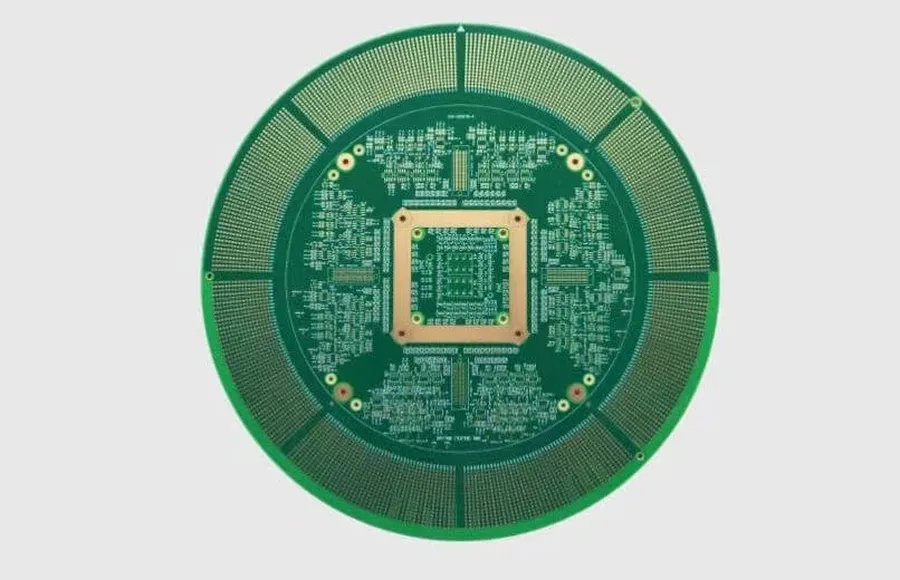
Isola's product portfolio is centered around high-performance laminates crucial for printed circuit boards (PCBs). These materials are engineered to meet specific performance requirements across diverse applications, ranging from consumer electronics to high-reliability aerospace and military systems. Understanding the properties and applications of key Isola materials such as 370HR, IS410, and FR408 is essential for selecting the appropriate PCB laminate.
- Isola 370HR
370HR is a popular high-performance epoxy laminate known for its excellent thermal reliability, making it suitable for multilayer PCBs used in demanding thermal environments. It exhibits a higher glass transition temperature (Tg) compared to standard FR-4 materials, enabling it to withstand more severe operating conditions without compromising electrical performance. Common applications include automotive electronics, industrial equipment, and high-density interconnect (HDI) PCBs. - Isola IS410
IS410 is a cost-effective alternative to high-Tg laminates while still offering improved performance characteristics over standard FR-4. It is a halogen-free material designed to meet stringent environmental regulations. IS410 is often used in consumer electronics, telecommunications equipment, and mid-range computing applications where thermal performance and environmental compliance are important factors. It balances price with reliability effectively. - Isola FR408
FR408 is a high-performance laminate developed for applications requiring superior electrical properties and high-speed signal integrity. It features a low dielectric constant (Dk) and low loss tangent (Df), making it ideal for high-frequency circuits, advanced communication systems, and networking hardware where signal fidelity and minimal losses are critical. Its enhanced electrical performance allows for higher data rates and improved signal transmission. It is commonly used in high-end networking and server equipment.
Comparing Isola Materials: 370HR, IS410, FR408
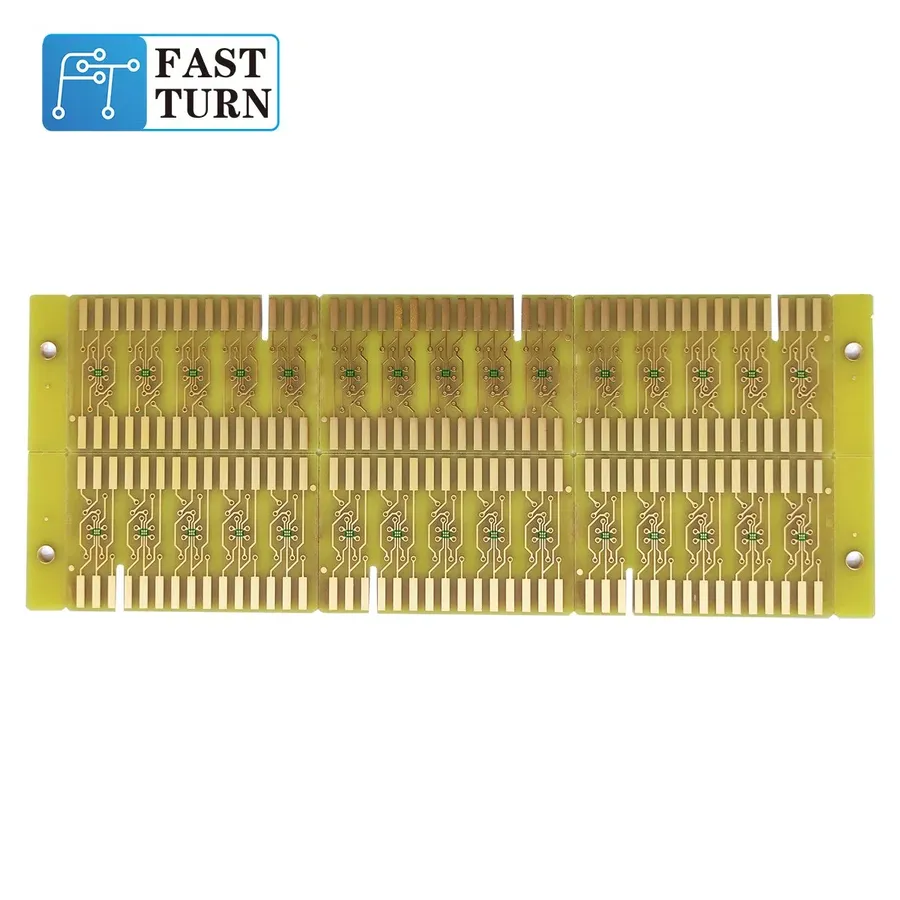
Selecting the appropriate laminate material is crucial for optimizing PCB performance. Isola offers a range of high-performance laminates, with 370HR, IS410, and FR408 being among the most popular. This section provides a detailed comparison of these materials, focusing on their thermal, electrical, and mechanical properties, to aid in informed material selection for specific applications.
Property | 370HR | IS410 | FR408 |
---|---|---|---|
Tg (Glass Transition Temperature) | 180°C | 190°C | 200°C |
Dielectric Constant (Dk) @ 1GHz | 4.0 | 3.7 | 3.66 |
Dissipation Factor (Df) @ 1GHz | 0.008 | 0.007 | 0.009 |
Thermal Conductivity (W/m·K) | 0.3 | 0.35 | 0.45 |
Moisture Absorption (%) | 0.15 | 0.10 | 0.08 |
Applications | High-reliability, high-temperature, multilayer boards | High-speed digital, low-loss applications | High-frequency, high-speed, high-performance applications |
How to Choose a Reliable Isola PCB Manufacturer
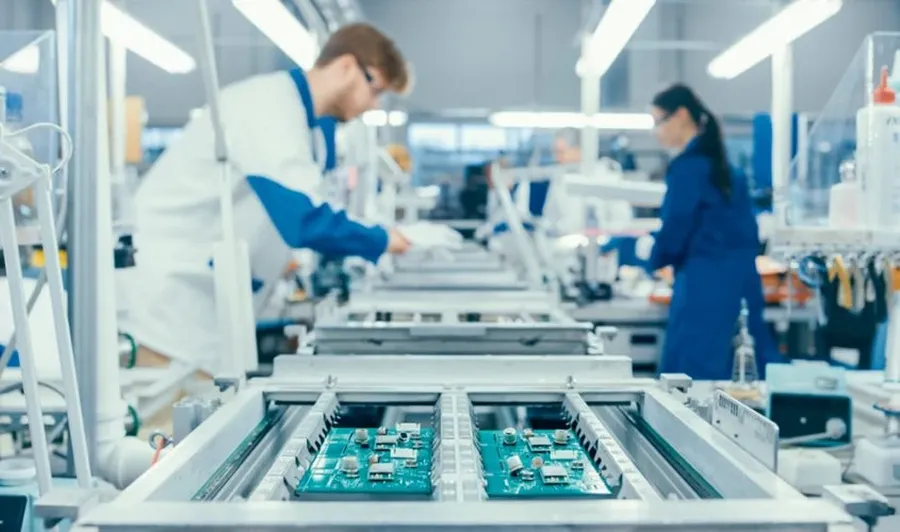
Selecting a dependable Isola PCB manufacturer is paramount to ensuring the quality and performance of your final product. This requires a meticulous evaluation process that goes beyond mere cost comparisons. Key factors include the manufacturer's experience with Isola materials, their production capabilities, their established quality control systems, and a clear understanding of your budgetary constraints.
- Experience with Isola Materials
Verify the manufacturer's history and expertise in handling Isola laminates. Look for evidence of prior projects using materials like 370HR, IS410, and FR408. Experience translates into better material handling, processing, and ultimately, higher quality PCBs. A manufacturer that understands the nuances of each material will minimize the risk of defects and enhance performance. - Production Capabilities
Assess the manufacturer's production capacity to ensure they can meet your volume requirements without compromising quality. Confirm their ability to accommodate the required PCB complexity, including layer count, trace width, and via size. Evaluate their equipment and technologies to ensure they align with your design specifications, leading to consistent fabrication of intricate boards. - Quality Control System
A robust quality control system is non-negotiable. Confirm the manufacturer’s certifications (e.g., ISO 9001) and verify the types of testing and inspections they conduct throughout the manufacturing process. This should include checks for dimensional accuracy, electrical performance, and material integrity. A rigorous QC process minimizes defects and ensures the PCBs meet stringent standards, contributing to product longevity. - Cost Considerations
While cost is a factor, prioritize value over the lowest price. Consider the manufacturer’s pricing structure relative to their capabilities and experience. Seek a balance between cost and quality by looking at the total cost of ownership, which includes manufacturing, potential defects, and long-term reliability. This approach minimizes future expenses due to subpar performance or premature failures. - Technical Support and Communication
Assess the manufacturer's ability to provide technical support and maintain open communication throughout the project. A collaborative relationship where technical questions are addressed and guidance is readily available will lead to streamlined processes and improved outcomes. This transparency ensures your requirements are met, and any issues are resolved promptly. - Lead Times
Evaluate the manufacturer's typical lead times and their ability to adhere to project deadlines. Inquire about their procedures for handling expedited orders. Consistent lead times and schedule adherence are critical to keeping projects on track, reducing delays and ultimately ensuring a smoother product launch.
Isola PCB Manufacturing Process
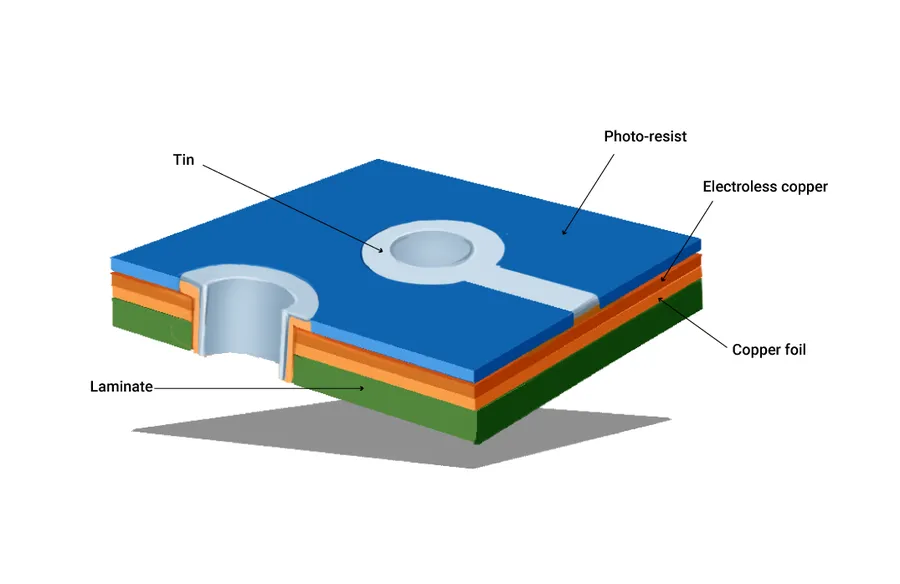
The manufacturing process for Isola PCBs is a multi-stage procedure that transforms raw materials into finished circuit boards, emphasizing precision and quality control at each step. This process involves several key stages, from preparing the Isola laminates to the final quality inspection, and it's essential for understanding the capabilities and limitations when working with an Isola PCB manufacturer.
- Material Preparation
The process begins with selecting the appropriate Isola laminate, such as 370HR, IS410, or FR408, based on the PCB's performance requirements. The chosen laminate is then cut to the required panel size and prepared for subsequent processing. This includes cleaning and, if necessary, pre-treatment to enhance adhesion in the following steps. Accurate dimensioning and handling are crucial at this stage to ensure consistent board quality. - Inner Layer Processing
For multilayer PCBs, the inner layers are processed first. This involves imaging the circuit patterns onto the copper-clad laminate using photolithography. The exposed copper is then etched away, leaving behind the desired circuit traces. Following etching, these layers are inspected for defects and undergo any necessary cleaning or repair processes before proceeding. - Lamination
The core of the PCB manufacturing process is the lamination stage. Here, the inner layers, along with prepreg (a resin-impregnated fiberglass cloth), and the outer copper foils, are stacked together under controlled temperature and pressure. This process uses a combination of heat and pressure to bond the layers together, creating a monolithic board structure. The specific parameters used for lamination (temperature, pressure, duration) are crucial and depend on the type of Isola material and the PCB design. - Drilling
After lamination, the circuit board goes through a drilling process where the plated through-holes (PTH) and vias are created. These holes are critical for electrical connection between different layers. Precision drilling is vital, and modern drilling machines use computer-aided technology to ensure accurate hole placement. The drilled holes are then cleaned and treated in preparation for the metallization process. - Metallization
The drilled holes are metallized using a chemical plating process, providing electrical connection between layers. This step creates a conductive path through the PCB, enabling signal and power transfer across different layers. The plated through-holes are then subject to another inspection to guarantee the metallization quality before going to the next stage. - Outer Layer Processing
Similar to the inner layers, the outer layer processing involves imaging, etching, and stripping to define the final circuit traces and pads. Once this process is complete, the board's surface is prepared for applying solder mask. These patterns are created using photolithography and precise chemical etching. - Solder Mask Application
A solder mask is applied to the PCB to protect the copper traces and prevent solder bridging during assembly. The solder mask is typically a polymer that's applied to the entire surface and then cured using UV light. Openings are created over the pads where components will be soldered. After solder mask application the PCB is usually silk screened for component placement reference. - Surface Finish
Surface finish is the final step before the PCB can be populated. The exposed copper pads and through-holes require surface finish to ensure solderability. Common surface finishes include HASL (Hot Air Solder Leveling), ENIG (Electroless Nickel Immersion Gold), and OSP (Organic Solderability Preservative). This is critical to protect the copper and ensure reliable soldering. - Electrical Testing
Before the PCB is shipped, it undergoes rigorous electrical testing to ensure that all traces and connections are correct. This may involve flying probe testing or fixture testing, which are designed to detect shorts and opens. The test results help in identifying manufacturing defects. - Final Quality Control
The PCB is subject to a final quality control inspection before being released for packaging. This includes a visual inspection to ensure that no surface blemishes are present and all dimensions meet the specifications. Boards that pass are then packaged and prepared for shipment to the customer.
Advantages of Using Isola Materials for PCBs
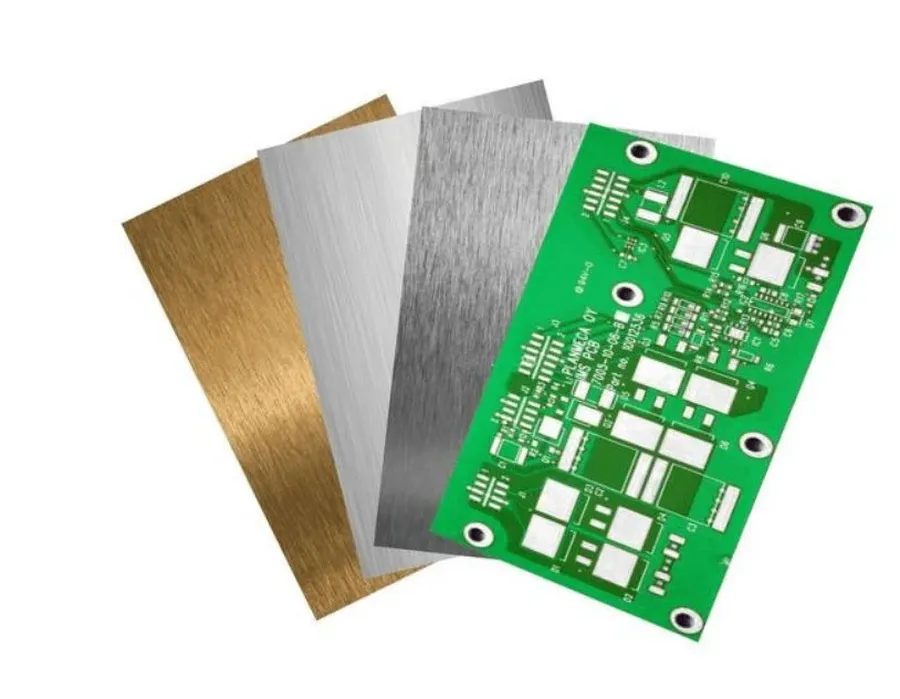
The selection of Isola materials in PCB manufacturing is a strategic decision, primarily driven by the inherent advantages these materials offer. These benefits span across enhanced performance, exceptional reliability, and superior material durability, particularly in demanding operational environments.
- Enhanced Performance
Isola materials are engineered to provide superior electrical characteristics, including lower signal loss and consistent impedance control. This is crucial for high-frequency applications where signal integrity is paramount. The controlled dielectric constant and dissipation factor ensures minimal signal degradation. - Superior Reliability
The robust nature of Isola laminates allows for reliable performance in diverse operating conditions, including extreme temperatures and humidity. The materials' resistance to thermal stress helps prevent delamination and other failures, thus increasing the operational lifespan of PCBs. - Improved Durability
Isola materials offer enhanced mechanical strength and durability, making PCBs less susceptible to physical damage during handling and operation. The materials resist deformation and wear and tear, ensuring consistent performance and reliability over time. This robustness is vital in high-stress, industrial and automotive applications. - High-Temperature Performance
Materials like Isola 370HR and others are designed to operate at higher temperatures without compromising performance. This is essential in applications where significant heat generation is expected, ensuring PCBs maintain stable electrical properties under thermal stress. - Compliance with Industry Standards
Isola materials conform to various industry standards, ensuring that the PCBs manufactured using these materials meet strict quality and safety requirements. This compliance facilitates market acceptance and regulatory approvals. Specifically, Isola materials often comply with IPC standards for PCB manufacturing. - Reduced Life Cycle Costs
While the initial cost of Isola materials may be higher than some alternatives, their enhanced performance and durability can lead to reduced life cycle costs. Fewer failures, longer operational lifespans, and increased reliability can result in significant long-term savings. This is particularly valuable for complex or critical applications where failure can have significant implications.
Frequently Asked Questions About Isola PCBs
This section addresses common queries regarding Isola PCBs, providing clear and concise answers to help you understand Isola's role and its materials in the PCB manufacturing industry.
- What does Isola manufacture?
Isola primarily manufactures high-performance laminate materials used in the production of printed circuit boards (PCBs). These materials include a variety of resin systems reinforced with glass fabric, tailored to meet specific performance requirements such as thermal management, signal integrity, and high-speed data transmission. Isola does not manufacture finished PCBs but supplies the core materials that PCB manufacturers use. - Who is the largest PCB manufacturer in the world, and how does Isola compare?
While specific rankings can vary, large PCB manufacturers include companies like TTM Technologies, Unimicron, and other significant players in the electronics industry. Isola, on the other hand, is not a PCB manufacturer but a critical supplier of the raw laminate materials these manufacturers utilize. Isola's position is therefore upstream in the supply chain, focused on material science and technology rather than the production of finished circuit boards. Isola is a technology driver and key material supplier to those leading PCB manufacturers. - Which PCB company is considered the best?
The notion of 'best' depends significantly on the application and specific requirements of the end product. Different manufacturers excel in different areas, such as high-volume production, complex designs, or specific material expertise. There is no single best PCB manufacturer. Factors such as experience with specific materials (like Isola laminates), production capabilities, quality control processes, and cost-effectiveness, should all be considered in the selection process. It's advisable to evaluate options based on your specific needs rather than seeking a single 'best' option. - What are the primary applications of Isola materials in PCBs?
Isola materials are used in a wide array of applications, including high-speed digital circuits, RF and microwave applications, automotive electronics, aerospace, and industrial control systems. They are especially valued in applications that demand high thermal performance, low signal loss, and high reliability. The selection of specific Isola materials will depend on the required performance specifications. - What is the significance of Isola's 370HR material?
Isola's 370HR material is a popular choice due to its enhanced thermal performance and reliability. It is often used in applications requiring higher operating temperatures, where traditional materials might fail or suffer performance degradation. This makes 370HR suitable for use in demanding environments where reliability and high temperature performance is essential. It bridges the gap between standard FR-4 materials and higher performance, often more expensive, options. - How does Isola ensure the quality of its laminate materials?
Isola maintains strict quality control processes throughout its manufacturing processes, adhering to international standards and certifications. The company uses advanced testing techniques to assess electrical, mechanical, and thermal properties of its laminates, ensuring that every batch meets rigorous specifications. Additionally, Isola invests heavily in research and development to continually improve material performance, thus ensuring consistent and high-quality products. - Can I source Isola laminates directly from Isola?
Isola primarily supplies its laminate materials to PCB manufacturers rather than directly to end users. While it might be possible to purchase directly in some regions or situations, it is generally more efficient for companies to source Isola material via reputable PCB manufacturers with whom they have established working relationships. This allows for a smooth and effective manufacturing process.
Cost Considerations When Sourcing Isola PCBs
Sourcing Isola PCBs involves a comprehensive understanding of various cost factors that extend beyond the initial material purchase. These factors span material expenses, manufacturing processes, and the long-term performance and durability of the final product. A thorough cost analysis is crucial for making informed decisions that balance immediate expenditure with long-term value.
- Material Costs
Isola laminates, known for their high performance, can have a higher initial cost compared to standard FR-4 materials. Material prices fluctuate based on resin type, copper thickness, and specific performance characteristics (e.g., high Tg, low loss). Selecting the correct material for the application is critical to prevent overspending on unnecessary high performance materials. - Manufacturing Expenses
The complexity of PCB design directly affects manufacturing costs. Factors such as the number of layers, via type (blind, buried, through-hole), board size, and precision requirements can impact the overall price. Isola materials with specific high performance requirements may necessitate adjustments in manufacturing parameters or specialized equipment, which adds to the expense. - Fabrication Yield Rates
The yield rate of the manufacturer plays a significant role in the overall cost. Low yield rates due to manufacturer inexperience or limitations may result in more waste and increased costs. Choosing a manufacturer with experience and a proven history of high fabrication yield is key to a cost effective final product. - Long-Term Value and Durability
While Isola materials may have a higher initial price, their enhanced performance and reliability can offer significant long-term savings. These include reduced field failures, lower maintenance costs, and extended product lifespan, which are pivotal factors in minimizing the total cost of ownership. Products such as high reliability automotive and aerospace devices benefit significantly from the added performance and durability. - Supply Chain Factors
Fluctuations in supply chain can impact pricing. These fluctuations include changes in raw material availability, logistics and transportation costs, and political factors. Partnering with a reliable supplier capable of consistent and dependable material supply is critical in managing risk and minimizing potential price volatility.
Future Trends in Isola PCB Technology
The trajectory of Isola PCB technology is marked by a relentless pursuit of enhanced performance, miniaturization, and sustainability, aligning with the rapidly evolving demands of the electronics industry. These advancements are not just incremental improvements but represent fundamental shifts in material science and manufacturing processes, impacting the design and capabilities of future electronic devices.
Several key trends are shaping the future of Isola PCB technology:
- Increased Focus on High-Speed and High-Frequency Materials
With the proliferation of 5G, IoT, and advanced radar systems, the demand for PCB materials capable of handling higher frequencies and faster data transfer rates is surging. Isola is actively developing new laminates with lower dielectric constants and loss tangents to minimize signal distortion and maximize performance in these applications. This includes pushing the boundaries of existing materials like their Astra MT series and exploring new material compositions. - Advancements in Thermal Management
As electronic devices become more powerful and compact, managing heat dissipation becomes critical. Isola is innovating in materials with improved thermal conductivity to efficiently draw heat away from sensitive components. This includes enhancing the thermal properties of existing materials and developing new thermal management solutions integrated directly into PCB laminates, often incorporating materials with high thermal conductivity such as ceramics and metallic compounds. - Miniaturization and Integration
The trend towards smaller and more integrated electronic devices necessitates further miniaturization in PCB technology. This involves Isola materials that support finer line widths and tighter spacing, enabling higher circuit densities. This also extends to integration, where more functionality is built into the material itself, potentially reducing the need for separate components and layering, driving down space requirements and simplifying the design and manufacturing process. - Sustainable and Eco-Friendly Materials
Growing environmental consciousness is pushing manufacturers to develop more sustainable and eco-friendly materials. Isola is researching and implementing solutions such as the use of bio-based materials and processes that reduce waste and energy consumption. This involves developing laminates with fewer harmful chemicals and implementing manufacturing methods that are more efficient and environmentally friendly. These efforts are not only driven by regulations but also by the demand from environmentally conscious customers and end-users. - Integration of Advanced Manufacturing Techniques
The evolution of PCB materials is closely linked to manufacturing innovation, Isola materials are being designed to accommodate advanced manufacturing techniques, such as additive manufacturing, which allow for the creation of more complex geometries and enable rapid prototyping. This alignment between material properties and advanced manufacturing techniques is expected to accelerate innovation and reduce turnaround times.
Choosing the right Isola PCB manufacturer is vital for ensuring the quality and performance of your electronic devices. Understanding the range of materials offered by Isola, evaluating potential manufacturers based on their expertise, and considering future trends will help you make informed decisions that lead to successful and reliable products. Isola, as a leading provider of copper-clad laminates and dielectric prepregs, plays a crucial role in the technology we use every day, underscoring the importance of careful selection of both materials and manufacturing partners.
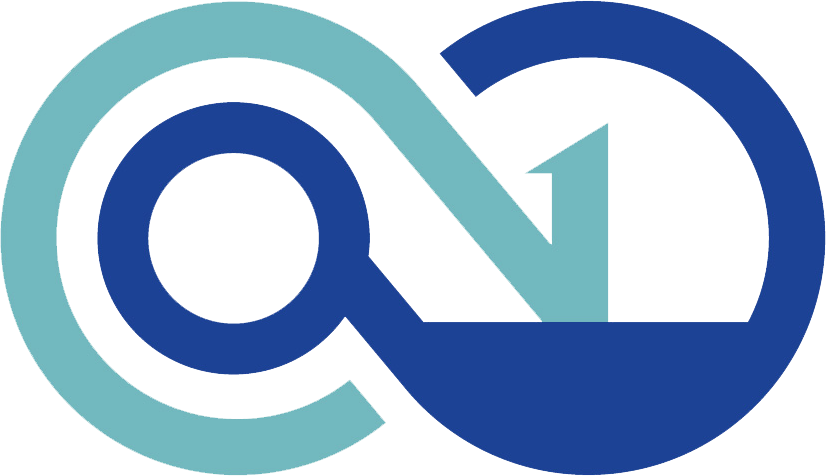