Choosing the Right Metal Core PCB Manufacturer
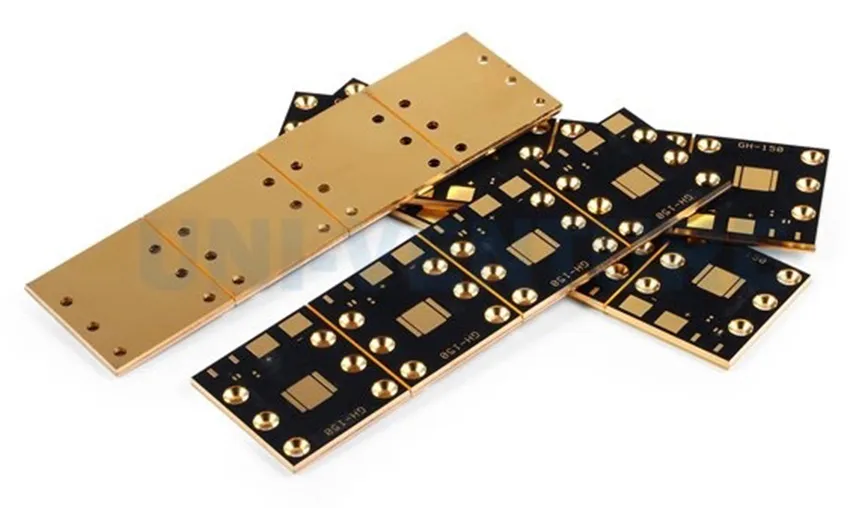
In today's fast-paced technological world, the demand for efficient heat dissipation in electronic devices is higher than ever. Metal core PCBs (MCPCBs), with their exceptional thermal performance, are at the heart of many applications, from high-power LEDs to automotive electronics. But how do you choose the right manufacturer for your specific needs? This article will guide you through the critical considerations, helping you find a trusted [metal core pcb manufacturer] to deliver the quality and performance your project requires.
Understanding Metal Core PCBs (MCPCBs)
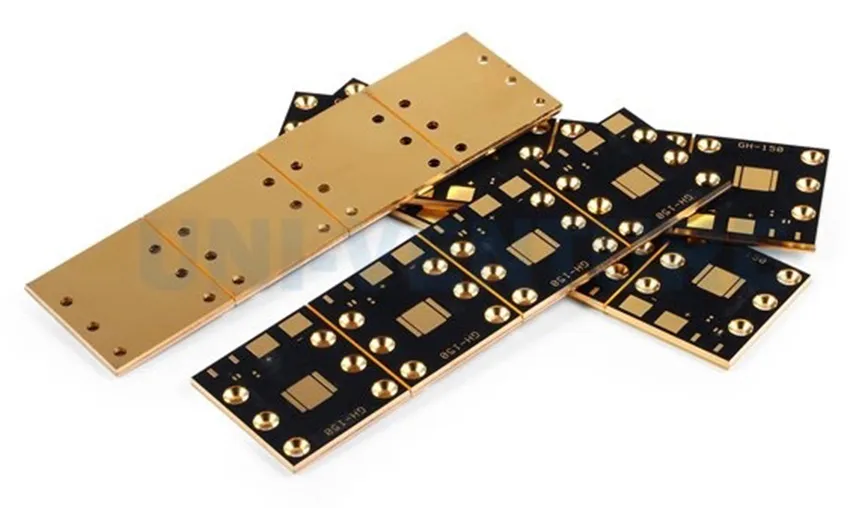
Metal Core PCBs (MCPCBs), also known as insulated metal substrate (IMS) PCBs, represent a significant departure from traditional FR-4 circuit boards by employing a metal base—typically aluminum or copper—as a core. This fundamental structural difference enables MCPCBs to excel in thermal management, offering superior heat dissipation capabilities crucial for high-power electronic applications.
Unlike FR-4 boards, which rely on the resin for heat dissipation, MCPCBs leverage the high thermal conductivity of their metal core to efficiently transfer heat away from heat-generating components. This enhanced thermal performance is achieved through a dielectric layer that separates the metal core from the conductive copper layers, preventing short circuits while still allowing efficient thermal transfer. The choice of metal, typically aluminum or copper, influences the PCB's overall thermal performance, cost and application suitability. This construction allows for the attachment of heat sinks directly to the metal core as well as the use of higher wattage and higher density applications. This results in a significant improvement in operational reliability and extended lifespans for electronic devices. Therefore, MCPCB's are an essential component for modern electronics requiring efficient thermal management.
Key Materials Used in MCPCBs: Aluminum vs. Copper
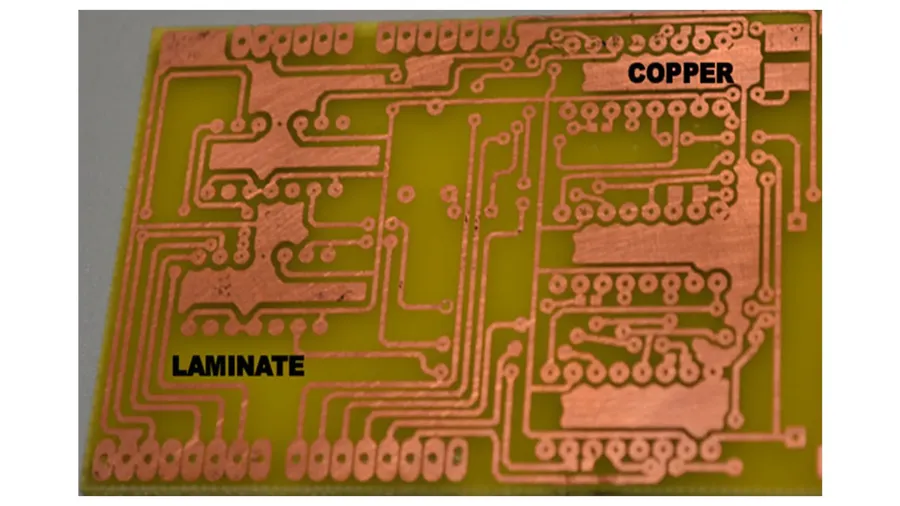
The selection of base material in Metal Core PCBs (MCPCBs) is crucial for achieving desired thermal performance and cost-effectiveness. Aluminum and copper are the two most common materials used, each offering distinct advantages and disadvantages, that a metal core pcb manufacturer can advise you on based on your specific requirements.
Property | Aluminum | Copper |
---|---|---|
Thermal Conductivity | 200-240 W/m·K | 385-400 W/m·K |
Cost | Lower | Higher |
Weight | Lighter | Heavier |
Mechanical Strength | Moderate | High |
Corrosion Resistance | Good (can be further improved with surface treatments) | Good, but can oxidize |
Applications | General LED lighting, power electronics, automotive | High-power LEDs, high-frequency applications, complex circuits |
Aluminum MCPCBs are favored in applications where cost is a major consideration, such as general lighting and lower-power electronics. Their lighter weight is advantageous in some applications. On the other hand, copper MCPCBs are the preferred choice in high-performance applications where optimal heat dissipation is essential. Although more expensive, copper offers superior thermal performance.
The ultimate material selection should be based on a comprehensive evaluation of your project's thermal needs, cost constraints, and performance requirements. Consulting with a metal core PCB manufacturer will ensure the optimal material is used.
Critical Factors When Selecting a Metal Core PCB Manufacturer
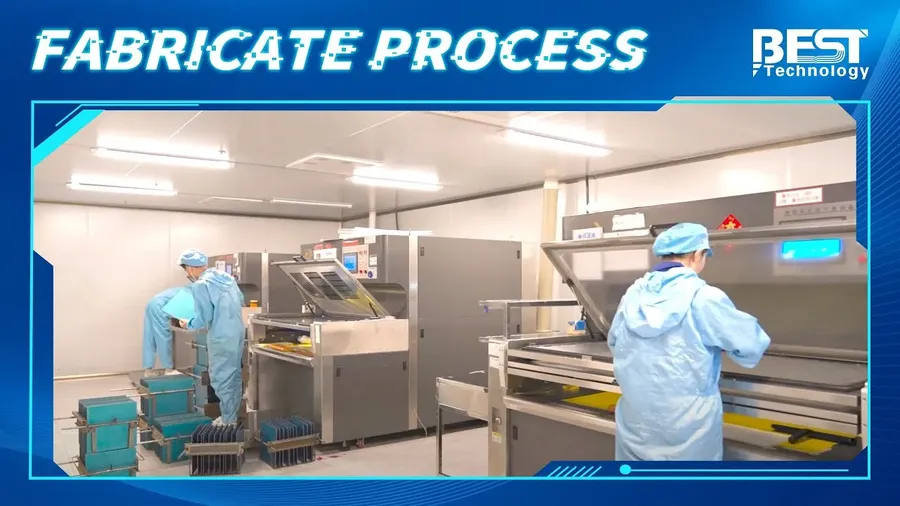
Selecting the right metal core PCB (MCPCB) manufacturer is crucial for ensuring the quality, reliability, and performance of your electronic products. The ideal manufacturer will possess a blend of experience, robust certifications, advanced production capabilities, reliable material sourcing, and stringent quality control protocols. This section outlines the key factors to consider when making this important decision.
- Experience and Expertise
A manufacturer's track record in producing MCPCBs is paramount. Look for companies with a substantial history in this specific area, demonstrating a deep understanding of the unique challenges associated with MCPCB fabrication. Years of experience often correlate with a higher likelihood of delivering consistent, high-quality products. Evaluate their past projects and case studies if possible to assess their ability to meet specific requirements. - Certifications and Compliance
Verify that the manufacturer holds relevant certifications such as ISO 9001 (Quality Management), ISO 14001 (Environmental Management), and potentially industry-specific certifications (e.g., IATF 16949 for automotive applications). These certifications confirm that the manufacturer adheres to established standards in quality, environmental management, and ethical manufacturing. Compliance with international standards provides added assurance. - Production Capabilities
Assess the manufacturer's production capacity, technology, and equipment. Ensure they possess the necessary machinery and infrastructure to handle your volume requirements without compromising quality. This includes examining their precision capabilities for various manufacturing steps such as lamination, drilling, etching, and surface treatment. It also means evaluating their in-house ability to manage processes like surface finish application, solder mask application, and final electrical testing. A well-equipped manufacturer minimizes the risk of bottlenecks and ensures better control over production quality. - Material Sourcing and Quality
The quality of the raw materials directly impacts the performance and reliability of the MCPCB. Ensure that the manufacturer has established relationships with reputable suppliers and can provide material certifications to verify the composition and properties of the metal cores (e.g. aluminium or copper), dielectric materials, and soldermask. A transparent and well documented supply chain reduces the risk of using substandard or counterfeit materials. - Quality Control Processes
A robust quality control system is non-negotiable. Inquire about the manufacturer's testing methodologies throughout the fabrication process, including initial material verification, in-process quality checks, and final product inspection. The use of advanced testing equipment such as automated optical inspection (AOI) and electrical testing tools is an indicator of a high quality operation. Furthermore, manufacturers should be able to provide documentation to prove the quality and testing of each manufactured batch. - Communication and Support
Effective communication and responsive customer support are essential for a smooth collaboration. Opt for a manufacturer that can provide clear and timely updates on production schedules, offer technical support to resolve design queries and technical issues, and have a streamlined ordering and delivery process. Transparent communication can help prevent misunderstandings and ensure timely delivery of your MCPCBs. - Cost and Pricing Structure
While cost is undoubtedly a key consideration, it should not be the sole determining factor. Evaluate the manufacturer's pricing structure relative to the other factors mentioned, namely experience, compliance, quality of materials and quality control. A significantly lower price may indicate compromises in quality or material used in construction. Ensure the manufacturer provides a clear and detailed breakdown of costs and that there are no hidden fees.
MCPCB Manufacturing Process: Step-by-Step
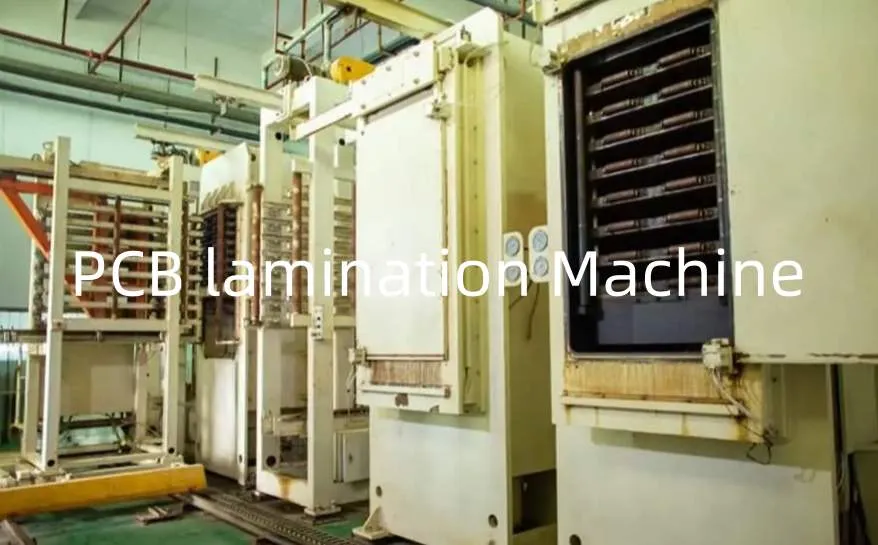
The manufacturing of Metal Core PCBs (MCPCBs) involves a precise sequence of steps, each crucial for achieving the desired thermal performance and electrical functionality. This process differs significantly from that of standard FR-4 PCBs due to the presence of a metal core, which necessitates specialized techniques for material handling and processing.
- Material Preparation
The process begins with selecting and preparing the core material, typically aluminum or copper. This includes cutting the metal sheet to the required dimensions and cleaning its surface to ensure optimal bonding with the dielectric layer. The core material's thickness is carefully controlled to meet thermal and structural requirements. Proper handling is critical to prevent contamination or damage. - Dielectric Layer Application
A thermally conductive dielectric material is applied to the prepared metal core. This layer provides electrical insulation while facilitating heat transfer. Various methods are used, including lamination, coating, and direct bonding, depending on the dielectric material used and the performance specifications. The uniformity and thickness of this layer are crucial for consistent performance. - Copper Foil Lamination
Copper foil layers are laminated onto the dielectric layer to form the conductive pathways. This step involves precise alignment and controlled pressure and temperature settings to achieve a strong bond. The copper foil thickness is chosen based on the current carrying capacity requirements of the circuit. This process is typically conducted in a cleanroom to prevent contamination. - Circuit Patterning
The desired circuit pattern is transferred onto the copper foil using photolithography. A photoresist material is applied, exposed to UV light through a mask, and then developed to reveal the pattern. The exposed copper is then etched away, leaving behind the desired conductive traces and pads. This step requires precise control over the etching process to ensure accurate circuit geometry. - Solder Mask Application
A solder mask is applied to protect the conductive traces from oxidation and prevent solder bridges during assembly. This layer also provides insulation and helps to define the areas for component soldering. The solder mask is typically applied using a screen printing or photo-imaging process. Accurate registration is essential to ensure all exposed pads are properly covered. - Surface Finishing
The exposed copper pads and traces are surface finished to improve solderability and prevent corrosion. Common finishes include HASL (Hot Air Solder Leveling), ENIG (Electroless Nickel Immersion Gold), and OSP (Organic Solderability Preservative). The selection of finish depends on the application requirements and the required solderability characteristics. - Final Testing and Quality Control
Each completed MCPCB undergoes rigorous testing to verify its electrical performance, thermal characteristics, and overall quality. Tests include electrical continuity and isolation tests and thermal performance evaluations. Visual inspections are also performed to identify any defects. Quality checks throughout the entire manufacturing process are critical to ensure the finished product meets specifications.
Cost Considerations for Metal Core PCBs
The overall cost of metal core PCBs (MCPCBs) is influenced by a combination of factors, and understanding these can be crucial for effective budgeting and project planning. This section will delve into the key elements that contribute to the final price of an MCPCB, enabling informed decision-making when selecting a manufacturer and specifying board requirements.
Cost Factor | Description | Impact on Cost |
---|---|---|
Base Material (Aluminum vs. Copper) | The choice of base material significantly affects cost due to differences in material price and processing difficulty. | Copper MCPCBs are generally more expensive due to higher material cost and more complex processing requirements, while aluminum provides a more cost-effective alternative. |
Board Size and Complexity | Larger boards or designs with intricate features such as complex routing or multiple layers will result in higher costs. | Larger and more complex boards require more materials, more processing time, and potentially specialized fabrication processes, leading to higher prices. |
Number of Layers | The number of layers in an MCPCB impacts the fabrication complexity and therefore, the cost. | Multi-layer MCPCBs are more expensive due to the added materials, processing steps, and precision needed for lamination and layer registration. |
Thermal Requirements | High thermal conductivity requirements, may need specialized materials or treatments, influencing costs. | Demands for high thermal performance may necessitate high-grade materials or additional features, resulting in increased cost |
Quantity | The order quantity has a direct impact on the unit price of an MCPCB. | Larger production runs typically benefit from economies of scale, reducing the per-unit cost, while smaller orders usually have a higher per-unit price due to setup and overhead costs. |
Surface Finish | Different surface finishes have different costs associated with them. | High-performance surface finishes can increase the cost while a standard one will have less of an impact on the total. |
Manufacturer's Pricing Structure | Each manufacturer will have their own pricing model, and some may have higher costs due to better quality materials, certification, technology or high production costs. | Different manufacturers have varying overhead, material costs, and labor costs, resulting in price differences. It’s important to gather several quotes to understand the pricing landscape. |
Metal Core PCB Design Guidelines
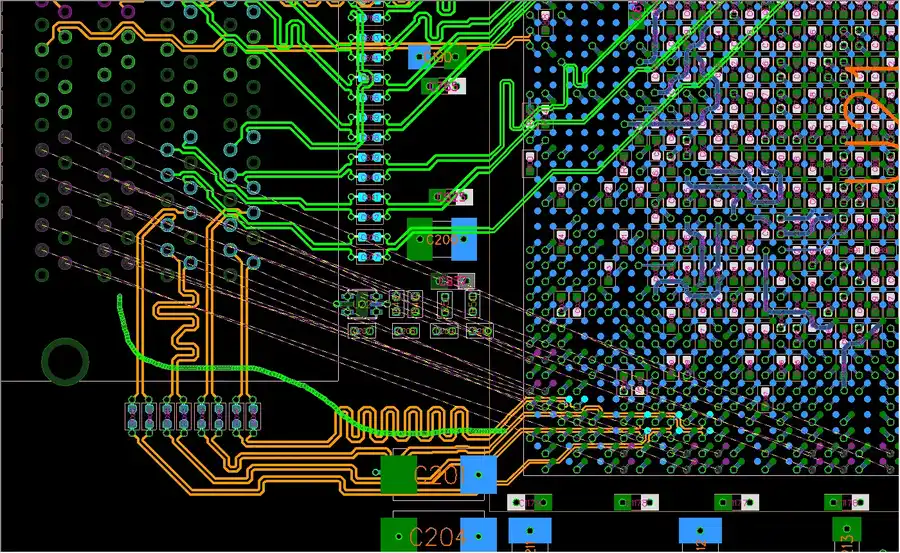
Designing Metal Core PCBs (MCPCBs) requires careful consideration of thermal management, layout strategies, and component selection to ensure optimal performance and reliability. These guidelines are crucial for designers to follow, and it's always recommended to review your designs with your chosen metal core PCB manufacturer to ensure manufacturability and performance requirements are met.
- Thermal Management
Prioritize heat dissipation in your design. Use thermal vias to conduct heat away from hot components to the metal core. Ensure sufficient surface area for heat sinking. Employ thermal analysis software to simulate heat flow and identify potential hotspots. - Layout Strategies
Place heat-generating components directly over the metal core for optimal thermal transfer. Minimize the distance between components and the thermal vias. Group components based on thermal considerations to achieve uniform temperature distribution. Avoid placing sensitive components near high heat generating areas. - Component Selection
Choose components with low thermal resistance. Select components that are compatible with the temperature requirements of the application. Consult component datasheets for thermal characteristics. Use thermally conductive adhesives and pads if applicable to improve thermal conductivity. - Layer Stackup
The layer stackup affects the overall thermal performance. Consider a thin dielectric layer between the copper layers and the metal core to reduce thermal resistance. A thick copper layer can also help with heat dissipation. Work with your manufacturer to optimize the layer stackup for your specific thermal requirements and application needs. - Mechanical Considerations
Account for mechanical constraints, such as mounting holes, edge plating, and overall board dimensions. Design with manufacturability in mind by incorporating appropriate spacing, clearances, and panelization guidelines that are provided by the manufacturer. Provide necessary mechanical support to the MCPCB to avoid warping. - Dielectric Layer
Choose a dielectric material with high thermal conductivity and good electrical properties. Minimize the thickness of the dielectric layer to decrease thermal resistance. Review the dielectric's performance under thermal and electrical stress conditions.
Frequently Asked Questions About Metal Core PCBs
This section addresses common questions about Metal Core PCBs (MCPCBs), providing clarity on their applications, performance, and limitations. Understanding these aspects is crucial for making informed decisions about incorporating MCPCBs into your electronic designs.
- What are the primary applications for MCPCBs?
MCPCBs are primarily used in applications requiring efficient heat dissipation, such as LED lighting, power electronics, automotive electronics, and high-power industrial equipment. Their ability to transfer heat away from components reduces thermal stress and improves the reliability and performance of electronic devices. - What are the key benefits of using an MCPCB compared to a traditional FR4 PCB?
The main advantage of an MCPCB over a traditional FR4 board is its superior thermal conductivity. The metallic core allows for significantly better heat dissipation, enabling higher power densities and improved long-term reliability. Additionally, MCPCBs can sometimes offer improved mechanical stability. FR4 boards, made from fiberglass and resin, are thermally insulating, making them unsuitable for high heat applications. - What are the common issues to avoid when using MCPCBs?
Common issues include poor material selection for your thermal requirements, insufficient thermal vias, improper lamination processes leading to poor thermal contact, and neglecting proper electrical isolation. Also, it is necessary to carefully select a manufacturing partner, as experience in this complex board technology is a must. Improper handling of the board can lead to damage, and thus, a high level of care is needed during the assembly process. - Is it better to use aluminum or copper as the core material for MCPCBs?
The choice between aluminum and copper depends on the specific application requirements. Copper offers superior thermal conductivity compared to aluminum but comes at a higher cost and is heavier. Aluminum is more cost-effective and lighter, making it suitable for a broader range of applications, particularly where cost and weight are critical. An aluminum core is preferred if the goal is to balance performance and cost. Copper is preferred if absolute best thermal performance is required. - How does the manufacturing process of an MCPCB differ from an FR4 PCB?
The primary difference lies in the core material and lamination process. MCPCBs involve bonding a metal core (typically aluminum or copper) with a dielectric layer and copper foil, while FR4 PCBs use a fiberglass-reinforced epoxy laminate. The lamination process for MCPCBs requires careful control over temperature and pressure to ensure good thermal contact between the core and the dielectric layer. Moreover, additional steps might include surface treatments to prevent corrosion in some designs. - Can MCPCBs be designed with multiple layers?
Yes, MCPCBs can be designed with multiple layers, but they are not as common as single or double-layer designs. While technically feasible, multilayer MCPCBs present additional manufacturing challenges and costs due to the complex lamination and alignment processes involved with the metal core. For multilayer design, you should discuss with your metal core PCB manufacturer during your initial planning. - What factors influence the cost of MCPCBs?
The cost of MCPCBs is influenced by factors such as the type of metal core (copper is more expensive than aluminum), board complexity (number of layers, board size), surface finish, required tolerances, and the manufacturing quantity. High-precision machining, tight tolerances, or specific surface treatments will raise costs, so it is best to engage with your metal core PCB manufacturer at an early stage in the process to optimize your board design for both performance and cost.
The Future Trends in Metal Core PCB Technology
The landscape of metal core PCB (MCPCB) technology is rapidly evolving, driven by the increasing demand for efficient thermal management solutions and enhanced performance in electronic devices. These advancements span materials science, manufacturing techniques, and application domains, promising to reshape how we approach PCB design and implementation.
- Advanced Materials
Research is ongoing into novel materials with superior thermal conductivity and reduced weight compared to traditional aluminum and copper. These include composite materials, ceramics, and advanced alloys, which offer enhanced heat dissipation capabilities and potentially lower costs. For example, the use of graphite-based materials for enhanced thermal performance is being actively explored. - Additive Manufacturing Techniques
Emerging additive manufacturing, such as 3D printing, is poised to revolutionize MCPCB fabrication. These techniques offer the potential for intricate designs, reduced material waste, and rapid prototyping, enabling manufacturers to produce custom MCPCBs with greater flexibility. This will also allow for more conformal cooling structures and intricate thermal pathways to be designed directly into the PCB - Integrated Thermal Management
Future MCPCB designs will focus on integrating thermal management directly into the board structure. This includes embedding heat pipes, vapor chambers, and microchannel cooling systems within the MCPCB itself, leading to highly efficient and compact thermal solutions. These integrated approaches reduce the need for external heatsinks. - Miniaturization and High Density Interconnects
The trend towards smaller and more powerful electronic devices drives the need for MCPCBs with finer lines and higher density interconnects. Future technologies will enable the fabrication of complex multilayer MCPCBs with extremely fine feature sizes, providing a suitable platform for increasingly complex electronic circuits. This also aligns with the trend of integrating more components onto a single chip. - Smart MCPCBs
The integration of sensors, control circuitry, and feedback mechanisms directly into MCPCBs will facilitate smart thermal management. Such intelligent MCPCBs can monitor their own temperature and adjust their cooling systems automatically based on changing conditions, optimizing energy consumption and performance. This development is critical for demanding applications where thermal stability is crucial. - Sustainable Manufacturing Practices
Environmentally friendly manufacturing processes are gaining importance. Future MCPCB fabrication will focus on using recyclable materials, minimizing waste, and employing energy-efficient techniques. This trend includes the adoption of water-based processing chemicals and the reduction of hazardous waste output. The increased use of additive manufacturing techniques will help reduce the overall amount of material needed. - New Applications
MCPCB technology is continuously expanding into diverse applications beyond traditional LED lighting. This includes high-power electronics, automotive electronics, aerospace, and medical devices. Each of these applications presents specific challenges and requirements that drive further innovation in MCPCB technology. For example, the growth of electric vehicles is pushing the demand for high-reliability thermal management solutions.
Selecting the right [metal core pcb manufacturer] is paramount for the success of your project. By carefully evaluating the factors discussed, including materials, manufacturing processes, and the manufacturer's experience, you can secure a partner capable of delivering high-quality, thermally efficient MCPCBs. As the technology advances, continuing to stay informed about the latest trends will be crucial for maximizing performance and efficiency in your electronic designs.
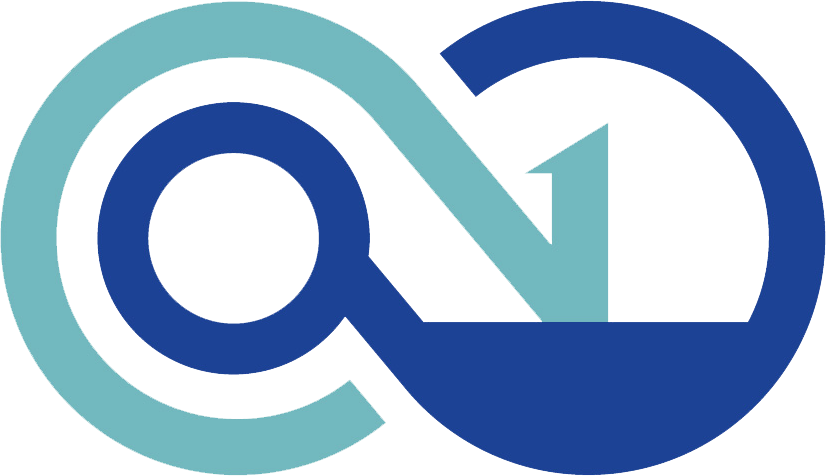