Choosing the Right PCB Laminate: A Guide to Top Manufacturers

In our interconnected world, printed circuit boards (PCBs) are the unsung heroes powering everything from smartphones to satellites. The quality of a PCB often hinges on its core material – the laminate. This article delves into the world of PCB laminate manufacturers, helping you navigate the complex landscape of materials and suppliers. We'll explore key players in the industry and what makes them stand out, connecting the technical aspects of PCB manufacturing with the daily technologies we depend on. Choosing the correct pcb laminate manufacturer can impact the performance and reliability of your electronic devices.
Understanding PCB Laminate Materials

PCB laminates form the foundational insulating layer of printed circuit boards (PCBs), providing the structural base upon which conductive pathways are etched. The selection of the appropriate laminate is critical, as it directly influences a PCB's electrical performance, thermal management, and overall reliability. These materials are composite structures composed of a resin matrix reinforced with a substrate, typically woven fiberglass or paper.
The primary purpose of a PCB laminate is to provide mechanical support and electrical insulation for the conductive layers of a PCB. The raw materials utilized by pcb laminate manufacturers significantly impact these aspects. The most common raw material components include:
- Resin Systems
Epoxy resin is the most prevalent thermosetting polymer, prized for its balance of cost, performance, and ease of processing. Other resins, such as polyimide, cyanate ester, and PTFE (Teflon), are selected for specialized applications demanding higher thermal stability, lower dielectric loss, or specific electrical properties. - Reinforcement Materials
Woven fiberglass fabric is a common reinforcing material, giving mechanical strength and stability to the laminate. The weave style and glass type influence the dielectric constant and other mechanical properties. Paper-based reinforcements, though less common in high-performance applications, offer cost-effective solutions in less demanding products. High-performance laminates may employ non-woven aramid fiber reinforcement for increased durability and improved electrical properties. - Fillers
Inorganic fillers, such as silica, are frequently added to the resin system to control the dielectric constant, reduce CTE, and improve thermal conductivity. These fillers directly influence the mechanical and electrical characteristics of the final laminate. The shape, size and composition of the fillers are crucial in achieving a balance of properties. Nano-fillers are increasingly being researched for enhanced performance. - Copper Foil
Copper foil is bonded to one or both sides of the laminate, which forms the conductive layer. The foil's thickness and surface treatment are crucial for the overall performance of the board. The method of copper foil adherence is also a crucial aspect of laminate manufacturing.
Key Properties of PCB Laminates
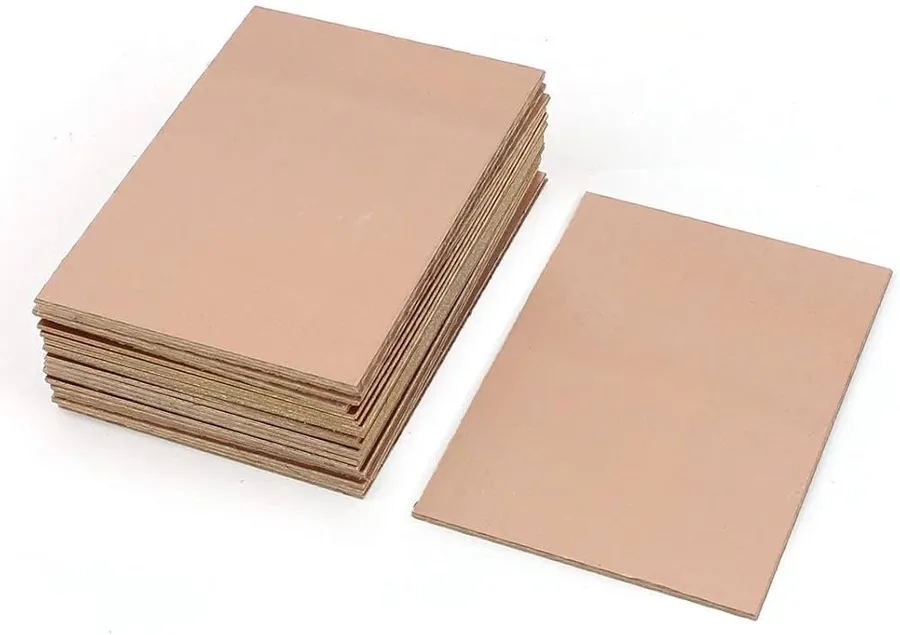
The performance and reliability of a Printed Circuit Board (PCB) are significantly influenced by the properties of its laminate material. Selecting the appropriate laminate, therefore, requires a thorough understanding of these key characteristics, which are critical when evaluating pcb laminate manufacturers. These properties dictate how well the PCB will function under various operating conditions, from electrical performance to thermal management.
Property | Description | Impact on PCB Functionality |
---|---|---|
Dielectric Constant (Dk or εr) | A measure of a material's ability to store electrical energy. It is the ratio of the permittivity of a material to the permittivity of free space. | Impacts signal impedance, transmission speeds, and signal integrity. Lower Dk values are typically preferred for high-speed applications to reduce signal delay and losses. Higher values can result in greater capacitance. |
Dissipation Factor (Df or tanδ) | Also known as the loss tangent, it quantifies how much energy is lost as heat in the dielectric material. | Affects signal attenuation, signal quality, and power efficiency. Lower Df values are crucial for high-frequency applications to minimize signal loss and maintain signal fidelity. |
Thermal Conductivity (k) | A material's ability to conduct heat. | Essential for thermal management. Higher thermal conductivity enables efficient heat dissipation from heat-generating components, preventing overheating and ensuring long-term reliability. Crucial for PCBs in high-power applications. |
Coefficient of Thermal Expansion (CTE) | A material's tendency to expand or contract with temperature changes. | Critical for reliability, especially in temperature cycling and extreme temperature environments. Mismatched CTE between the laminate, copper, and other components can lead to stress, cracking, and delamination of the PCB. |
Glass Transition Temperature (Tg) | The temperature at which the laminate material transitions from a rigid to a softened state. | Affects the mechanical and thermal stability of the PCB. It limits the maximum operating temperature and affects overall mechanical integrity. |
Moisture Absorption | The laminate's ability to absorb moisture from the surrounding environment. | Excessive moisture absorption can alter the electrical and mechanical properties of the laminate, including increased Dk, Df, and reduced insulation resistance and increased risk of electrical shorts. Moisture also impacts the CTE. Low moisture absorption is essential for maintaining consistent performance in humid environments. |
Flexural Strength | The material's ability to withstand bending forces before fracturing. | Affects the durability of the PCB against mechanical stress, vibration, and assembly processes. High flexural strength is beneficial for boards subject to physical handling and mechanical strain during fabrication and assembly. |
Top Global PCB Laminate Manufacturers: A Detailed Overview
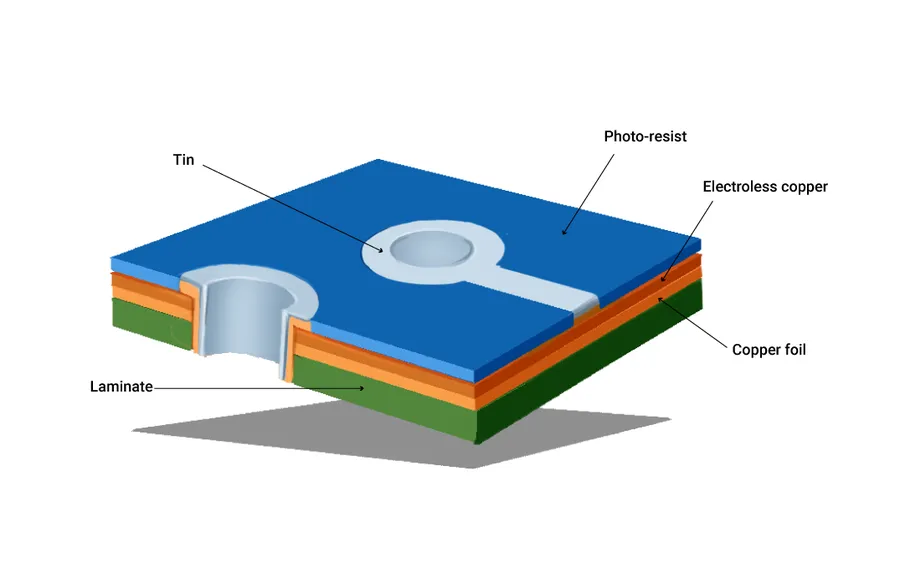
The selection of a PCB laminate manufacturer significantly impacts the performance and reliability of electronic devices. This section profiles some of the leading global manufacturers, highlighting their unique strengths, product portfolios, and geographic presence to assist in making informed sourcing decisions. We will explore key players like Isola, Rogers, and Shengyi, who are instrumental in shaping the PCB laminate industry.
Manufacturer | Strengths | Product Specializations | Geographic Presence | Key Offerings |
---|---|---|---|---|
Isola | High-performance materials, strong R&D, focus on high-speed and high-frequency applications. | High-speed digital, RF/microwave, advanced packaging laminates. | Global, with manufacturing in North America, Europe, and Asia. | A wide range of FR-4, halogen-free, and high-performance laminates. |
Rogers Corporation | Specialized in high-frequency and high-performance materials, known for materials designed for demanding applications. | RF/microwave, advanced connectivity, automotive and aerospace materials. | Global, with manufacturing and R&D facilities in multiple countries. | RO4000 series, RT/duroid laminates, and custom material solutions. |
Shengyi Technology Co., Ltd. | Large-scale production capabilities, cost-effective solutions, rapid growth, focus on mass-market applications. | Standard FR-4, CEM-3, halogen-free, and flexible laminates. | Primarily in Asia, with expanding global sales presence. | Extensive line of copper clad laminates suitable for a variety of PCB applications. |
Panasonic | Strong in consumer electronics, diverse material portfolio, high-reliability solutions. | Rigid, flexible, and rigid-flex laminates, including materials for high-speed and power applications. | Global, with significant presence in Asia and expanding to other regions. | Halogen-free laminates, low-loss materials, and specialty laminates for electronics. |
Taconic | Specialized in PTFE-based laminates, high-frequency applications, and advanced materials. | RF/microwave, aerospace, military and automotive industries. | Global, with manufacturing facilities in the United States and Europe. | PTFE woven glass laminates, non-woven materials for extreme applications. |
Factors to Consider When Choosing a PCB Laminate Manufacturer
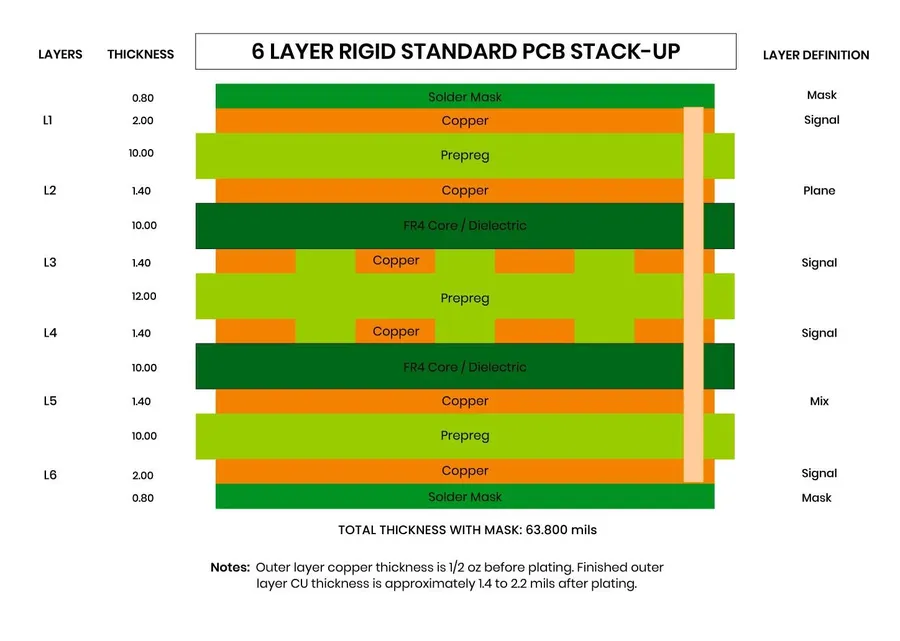
Selecting the right PCB laminate manufacturer is a critical decision that significantly impacts the performance, reliability, and cost-effectiveness of your printed circuit boards. This section outlines the key factors that should guide your selection process, ensuring you choose a partner that aligns with your project requirements and long-term goals.
- Material Quality and Consistency
The quality of raw materials used by pcb laminate manufacturers is the most important factor to consider. Consistent material properties ensure the reliability and uniformity of your PCBs. Look for manufacturers with rigorous quality control processes and certifications to back their claims, such as ISO 9001 and IATF 16949. - Pricing
While cost is always a consideration, it should not be the sole determinant. A balance must be struck between cost and material quality, ensuring that you are getting the performance you need within your budgetary constraints. Obtain multiple quotes from different pcb laminate manufacturers to compare costs, and consider total cost of ownership, not just initial purchase price. - Manufacturing Capabilities and Capacity
Assess the manufacturer's production capacity, capabilities, and whether they can meet the specific requirements of your project. This includes evaluating equipment, process controls, and the complexity of laminates they can handle. Consider their technology roadmap to ensure they remain aligned with your future needs. - Lead Times and Delivery Schedules
Timely delivery of PCB laminates is critical for project completion, making lead times a critical consideration. Inquire about the manufacturer's typical lead times, production processes, and logistics capabilities. Delays in raw material supply can lead to critical bottlenecks in production. - Technical Support and Communication
Effective communication and technical support are essential for a successful partnership. Choose manufacturers who provide access to technical staff that are knowledgeable about material properties, applications, and can quickly resolve issues when they arise. Good support demonstrates a manufacturer's commitment to their customers. - Certifications and Compliance
Ensure that the pcb laminate manufacturers adheres to industry-standard certifications and compliance requirements, such as RoHS (Restriction of Hazardous Substances) and UL (Underwriters Laboratories) certifications. This ensures the materials are safe, environmentally responsible, and suitable for their application. - Geographic Location and Supply Chain
Consider the manufacturer's geographic location, as it can impact shipping costs, lead times, and supply chain risks. A well-established and robust supply chain is crucial to ensure consistent delivery, especially when faced with fluctuations in global conditions.
Comparing Different Types of PCB Laminates
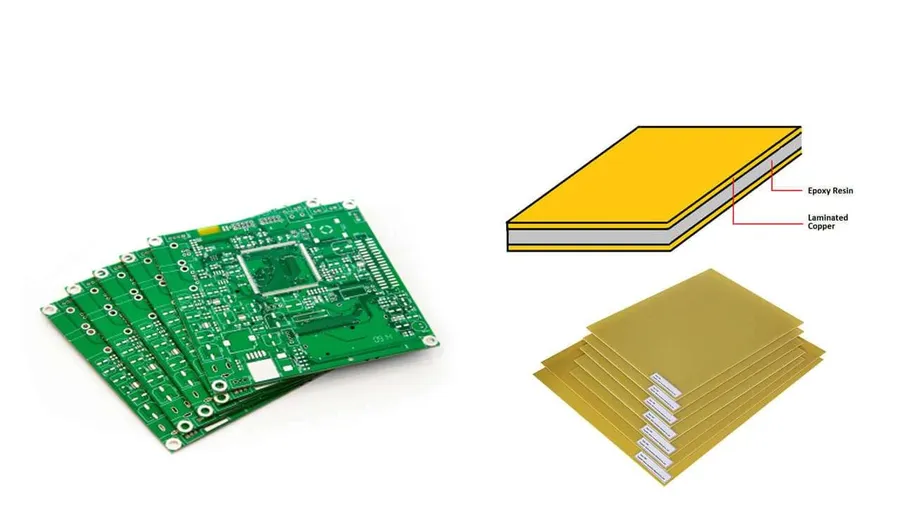
The selection of PCB laminate is a critical decision impacting the performance and reliability of electronic devices. This section provides a comparative analysis of common laminate types, focusing on their properties and suitable applications. Understanding these differences is crucial for engineers in selecting the optimal material from pcb laminate manufacturers.
Laminate Type | Dielectric Constant (εr) | Loss Tangent (tan δ) | Thermal Conductivity (W/mK) | Coefficient of Thermal Expansion (CTE, ppm/°C) | Typical Applications |
---|---|---|---|---|---|
FR-4 | 4.2 - 4.8 | 0.02 - 0.03 | 0.2 - 0.3 | 12 - 18 | General purpose, consumer electronics, low-speed digital circuits |
High-Tg FR-4 | 4.2 - 4.8 | 0.02 - 0.03 | 0.25 - 0.4 | 10 - 16 | Higher temperature applications, power supplies, automotive electronics |
High-Speed Laminate (e.g., Rogers 4350B) | 3.48 | 0.0037 | 0.62 | 50 | High-frequency circuits, RF/microwave applications, high-speed digital |
Flexible Laminate (e.g., Polyimide) | 3.2 - 3.5 | 0.002 - 0.005 | 0.2 - 0.4 | 10 - 20 | Flexible circuits, wearable electronics, dynamic bending applications |
Halogen-Free Laminate | 4.0-4.4 | 0.018-0.025 | 0.2-0.35 | 12-16 | Environmentally conscious designs, general electronics |
Applications of Various Laminate Materials
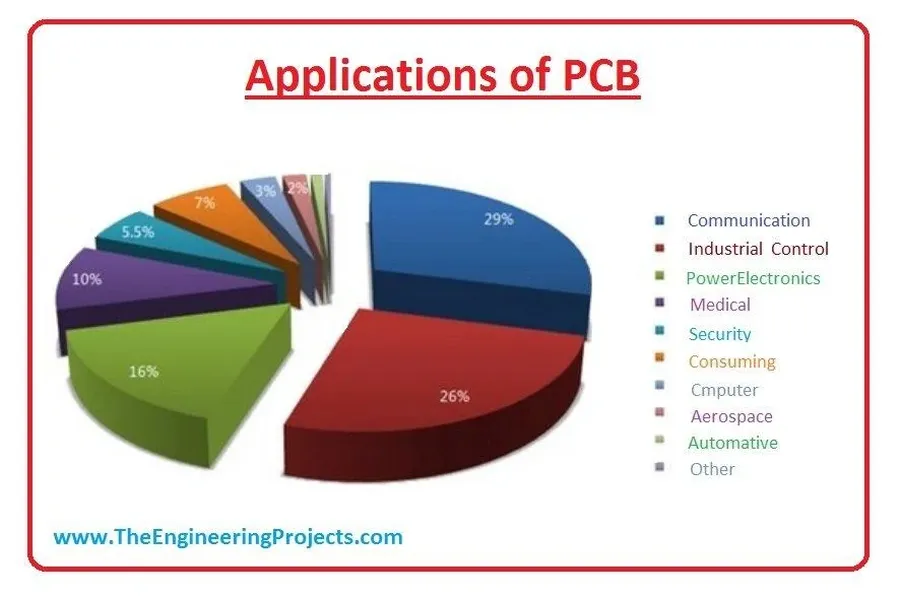
The selection of PCB laminate material is fundamentally driven by the application's specific performance requirements and environmental conditions. Different industries, such as automotive, aerospace, consumer electronics, and high-speed data transmission, necessitate distinct laminate properties to ensure reliability and optimal functionality.
Below are specific applications and how different laminate materials meet their unique demands:
- Automotive Industry
Automotive applications demand PCB laminates that can withstand harsh environmental conditions, including extreme temperatures, humidity, and vibrations. Materials with high thermal and mechanical reliability, such as those based on FR-4 with enhanced Tg (glass transition temperature) or specialized high-temperature laminates, are commonly used for engine control units, safety systems, and infotainment modules. - Aerospace and Defense
Aerospace applications require laminates with exceptional reliability, performance at extreme temperatures and resistance to harsh environments and radiation. High-performance materials like polyimide or PTFE-based laminates are used in critical systems such as avionics, satellite communication, and radar, where signal integrity and thermal stability are paramount. These materials often feature low dielectric constant (Dk) and low dissipation factor (Df) for optimal signal propagation. - Consumer Electronics
Consumer electronics, including smartphones, tablets, and laptops, typically use FR-4 laminates due to their cost-effectiveness and adequate performance for general applications. High-density interconnect (HDI) technologies often utilize specialized resin systems with very fine line and space capabilities, while flexible laminates are essential for foldable devices and compact designs. - High-Speed Data Transmission
High-speed data transmission applications, such as networking equipment, servers, and telecommunications infrastructure, require materials with excellent signal integrity at high frequencies. Laminates with low Dk and low Df, such as those based on modified epoxy, hydrocarbon or fluoropolymer materials, are used to minimize signal loss and distortion, which are critical for maintaining reliable data transfer rates. Materials that allow for controlled impedance and minimize signal reflection are preferred. - Medical Devices
Medical devices, which often require high precision and reliability, may employ specialized laminates depending on their function. Implantable devices require biocompatible materials, while diagnostic equipment might use laminates with specific electrical characteristics to ensure accurate readings. The choice of laminate must align with stringent medical standards.
In summary, selecting the correct laminate material is not just about meeting the basic mechanical and electrical requirements, but also about ensuring the overall longevity, efficiency, and safety of the final product within its intended environment. Each industry and application has specific demands that must be carefully evaluated to achieve optimal performance.
Frequently Asked Questions About PCB Laminate Manufacturers
This section addresses common questions regarding PCB laminates, focusing on material selection, industry certifications, and standards, particularly when choosing a PCB laminate manufacturer. Understanding these aspects is crucial for ensuring the quality and performance of your printed circuit boards.
- What are the primary factors to consider when selecting a PCB laminate material?
Key factors include the dielectric constant (Dk), which affects signal speed; dissipation factor (Df), which impacts signal loss; thermal conductivity, crucial for heat management; and the coefficient of thermal expansion (CTE), vital for reliability under temperature changes. The intended application also plays a significant role in material selection. Specific performance requirements, such as signal integrity, thermal performance, and environmental conditions, must be carefully considered. - What certifications should I look for when choosing a PCB laminate manufacturer?
Certifications such as ISO 9001 for quality management and ISO 14001 for environmental management are essential indicators of a manufacturer's commitment to quality and sustainability. UL certification for safety is also crucial, particularly for materials used in electronics. Furthermore, industry-specific certifications, such as those related to aerospace or automotive standards, might be necessary depending on the application. Ensure the certifications are current and applicable to the specific products offered. - How does the dielectric constant (Dk) affect PCB performance?
The dielectric constant (Dk) is a crucial parameter as it affects the speed at which electrical signals travel through the PCB. A lower Dk results in faster signal propagation, which is particularly important in high-speed applications. Furthermore, Dk influences the characteristic impedance of the circuit, which needs to be carefully controlled to minimize reflections and maintain signal integrity. Variations in Dk can lead to signal distortion and performance degradation, highlighting the need for material consistency. - What is the impact of the Coefficient of Thermal Expansion (CTE) on PCB reliability?
The CTE mismatch between the laminate and other components, such as copper and solder, can induce stress during thermal cycling, potentially leading to cracks, delamination, and eventual failure of the PCB. Selecting a laminate with a CTE that closely matches that of other materials is vital to ensure long-term reliability, especially in applications with harsh temperature conditions. Understanding the CTE characteristics of different laminate materials is crucial to designing robust and durable circuit boards. - What are the differences between FR-4 and high-performance laminates?
FR-4 is the most common and cost-effective PCB laminate, suitable for general applications with moderate performance requirements. High-performance laminates, on the other hand, often utilize more advanced materials to provide superior electrical and thermal properties. These advanced laminates typically offer lower Dk and Df, better thermal conductivity, and improved dimensional stability, making them suitable for high-speed, high-frequency, and high-reliability applications, such as in aerospace or telecommunications. The cost is typically higher for high-performance materials due to more complex manufacturing processes and specialty materials. - How do I choose a PCB laminate manufacturer for specialized applications?
For specialized applications, it is vital to select a manufacturer with a proven track record in producing the specific type of laminate needed. Consider the manufacturer's expertise, their capabilities for handling the material, and the availability of material testing data. Case studies or customer reviews showcasing the manufacturer's experience with similar applications can also offer valuable insight into their suitability. Furthermore, their ability to meet industry-specific certifications and standards is paramount. - Are there any environmental considerations when choosing PCB laminate materials?
Yes, increasingly, environmental considerations are paramount. Look for manufacturers offering laminates with reduced halogen content or those produced using environmentally friendly processes. The use of recycled or sustainable materials is also becoming more prevalent. Compliance with regulations like RoHS (Restriction of Hazardous Substances) is crucial for many applications. Choosing materials with a lower environmental impact is essential for sustainability and regulatory compliance. Also consider the ease of material disposal and its impact on the environment at the end of the product's life.
Future Trends in PCB Laminate Materials
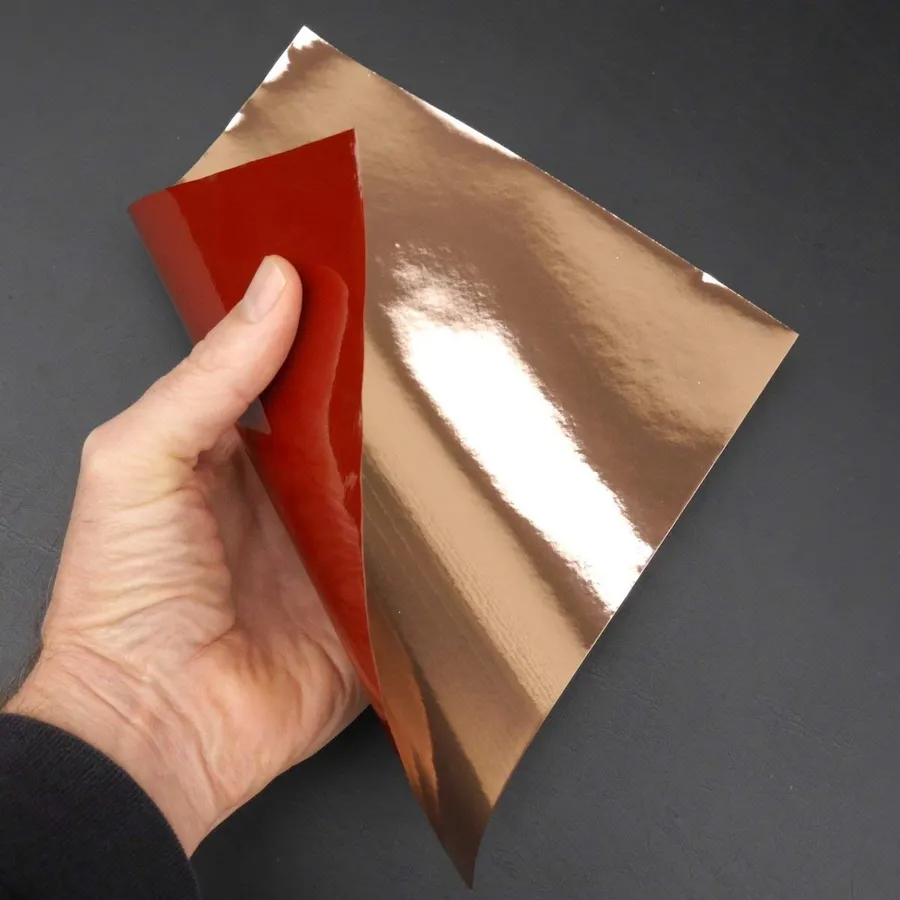
The PCB laminate industry is experiencing a rapid evolution, driven by the demands of emerging technologies and a growing emphasis on environmental responsibility. Future trends point towards innovative materials and advanced manufacturing processes to meet these challenges. These advancements will not only enhance the performance of PCBs but also contribute to a more sustainable and efficient electronics industry, influencing how pcb laminate manufacturers operate.
- Sustainable and Bio-Based Laminates
Growing environmental concerns are pushing the industry to explore sustainable and bio-based alternatives to traditional epoxy resins. This includes using materials derived from renewable resources, reducing reliance on fossil fuels and minimizing the carbon footprint of PCB manufacturing. - High-Frequency Laminates for 5G and 6G
The advent of 5G and the impending arrival of 6G technologies necessitate the development of laminates with superior high-frequency performance. These materials will feature low dielectric loss and stable signal integrity at millimeter-wave frequencies, ensuring reliable communication and data transmission. This will be crucial for pcb laminate manufacturers to adapt to emerging market needs. - Advanced Thermal Management Materials
As electronic devices become more powerful, effective thermal management becomes crucial. Future laminates will incorporate materials with improved thermal conductivity, enabling better heat dissipation and preventing component failure. Nanomaterials and composite structures are being explored for this purpose. - Embedded Components and Functionality
Future PCB laminates may include embedded components and functionality within the substrate itself. This will enable miniaturization, higher component density, and improved electrical performance. Embedding passives, for example, within the laminate can reduce board space and improve impedance control. - Flexible and Stretchable Laminates
The demand for flexible and stretchable electronics is on the rise, leading to the development of laminates that can conform to complex shapes and withstand mechanical stress. These materials will be vital for wearable devices, medical implants, and flexible displays. This includes both flexible circuits and even stretchable conductors integrated into the laminate.
The selection of a PCB laminate manufacturer is a critical decision impacting the quality and reliability of electronic products. This guide provides a comprehensive overview of key factors and leading suppliers, emphasizing the importance of informed choices. As technology evolves, PCB laminate manufacturers play a vital role in innovation, ensuring that the devices we use every day meet ever-increasing performance demands. As a concluding thought, consider staying informed about the latest advancements from these manufacturers to ensure the optimal performance of your designs.
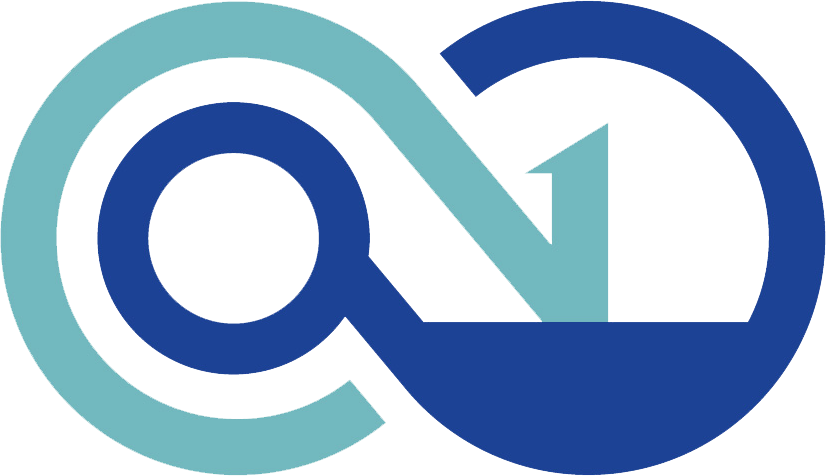