Choosing the Right Quick Turn PCB Manufacturer for Your Project
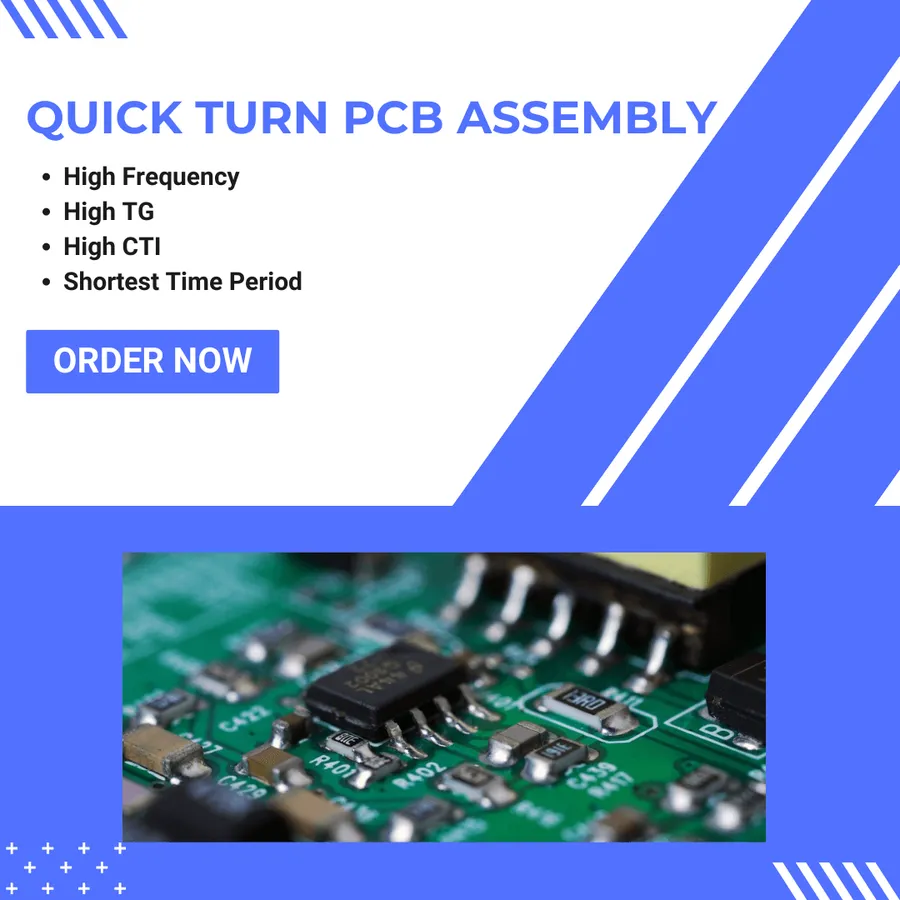
In today’s rapidly evolving tech landscape, time is of the essence, especially for electronic projects. That's where quick turn PCB manufacturers become invaluable. These specialists expedite the production of printed circuit boards, enabling rapid prototyping and faster product launches. This article explores how to select the optimal quick turn PCB manufacturer for your needs, considering crucial factors that ensure your project's success.
Understanding Quick Turn PCB Manufacturing
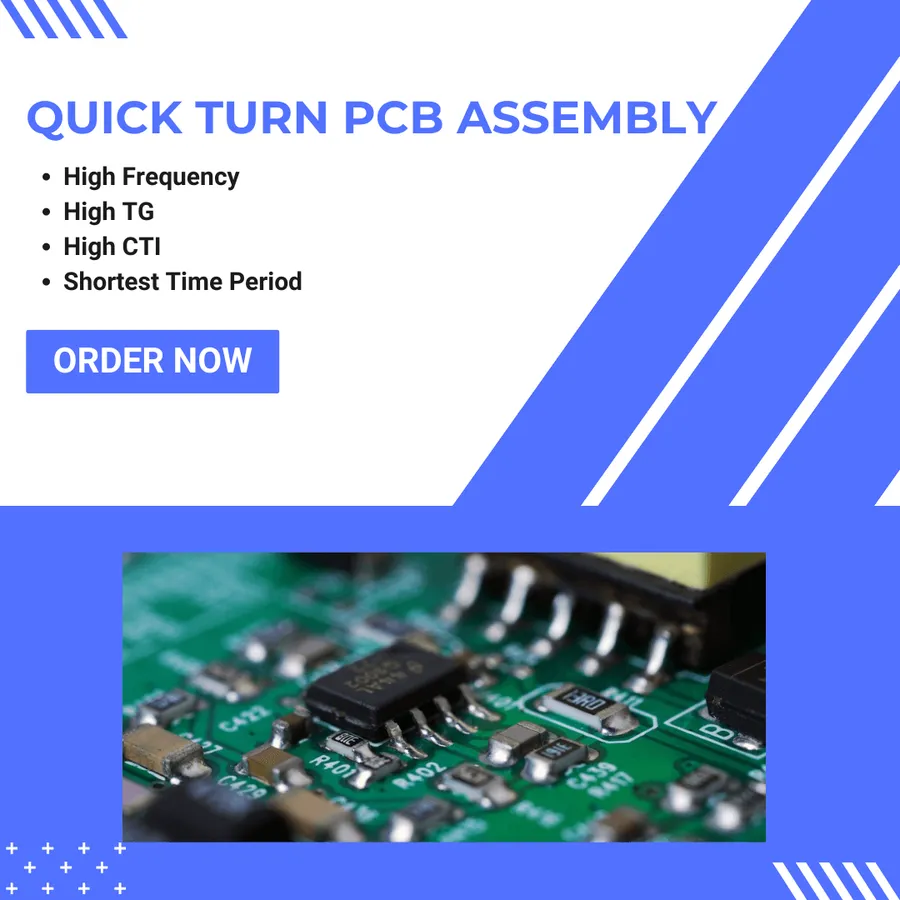
Quick turn PCB manufacturing is a specialized process designed to rapidly produce printed circuit boards, significantly reducing the time between design finalization and the delivery of physical boards. This expedited service is crucial for projects requiring quick prototyping, iterative design adjustments, and time-sensitive production schedules, differentiating itself from standard PCB manufacturing with a focus on speed and agility.
Key Factors When Selecting a Quick Turn PCB Manufacturer
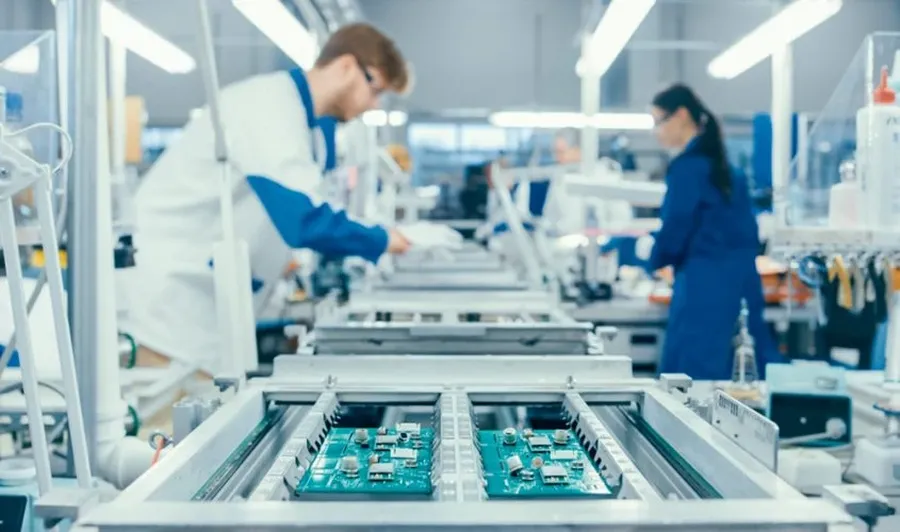
Selecting the right quick turn PCB manufacturer is crucial for the success of any project requiring rapid prototyping or fast production cycles. This decision hinges on several key factors, each influencing the project's timeline, budget, and overall quality. Evaluating these elements meticulously is essential to ensure your chosen manufacturer aligns with your project requirements and expectations.
- Turnaround Time
The speed at which a manufacturer can produce and deliver PCBs is paramount for quick turn projects. Evaluate their stated lead times and factor in any potential delays based on complexity or current order volume. A manufacturer that offers multiple turnaround options can provide flexibility. - Manufacturing Capabilities
Assess the manufacturer's technological prowess, including their ability to produce multi-layer PCBs, HDI boards, flex PCBs, and other specialized designs. Ensure they are equipped to handle the specific requirements of your designs in terms of feature size, tolerances, and materials. - Quality Standards
The manufacturer's commitment to quality is paramount. Verify their quality control processes, testing methods, and adherence to industry standards and certifications like ISO 9001. A robust quality assurance system minimizes errors and ensures the reliability of the final product. - Material Options
The range of materials a manufacturer can handle can impact performance. Consider your application needs, and confirm they offer the material specifications you need or can advise you of appropriate alternatives, e.g., FR-4, Polyimide, Aluminum, etc. - Cost Efficiency
Understanding the cost drivers of quick turn PCBs is important, not just the headline price, but consider total cost including tooling, setup, and expedited delivery options. Discuss the cost implications for design iterations and look for opportunities for cost optimization, while ensuring no compromise on quality. - Customer Support
Effective communication, responsiveness, and dedicated project managers are invaluable during the manufacturing process. Prompt and clear communication reduces errors, avoids delays, and provides opportunities to discuss your project, receive updates, and address concerns as soon as they arise. - Experience
Look for manufacturers with a proven track record in quick turn PCB manufacturing. Evaluate their portfolio of projects, customer testimonials, and case studies. This can help gauge their proficiency and reliability to ensure they are equipped to handle your specific project needs.
Turnaround Time: Speed vs. Reliability
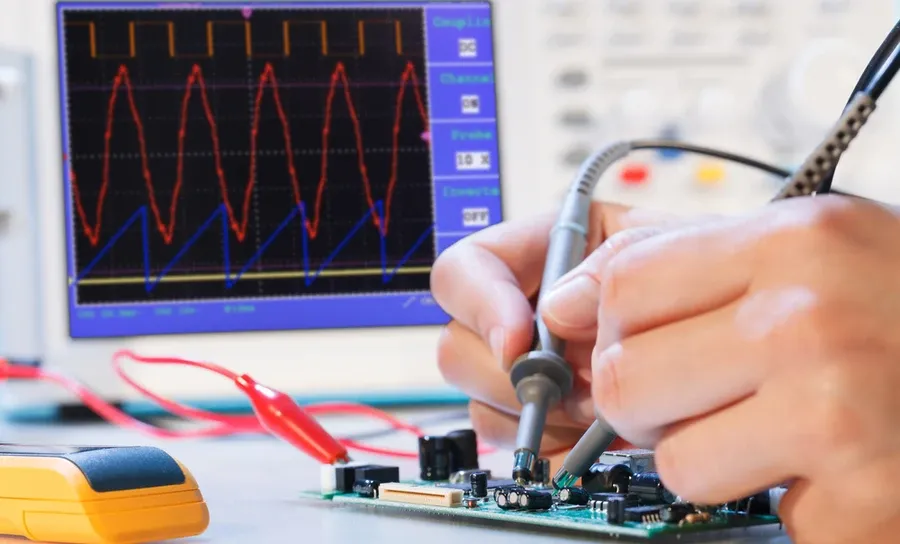
In quick-turn PCB manufacturing, turnaround time is a critical factor that often involves a trade-off between speed and reliability. Understanding these options and their implications for cost and quality is essential for project success. The goal is to select a turnaround time that meets project deadlines without compromising the integrity and functionality of the final printed circuit board.
- Standard Turnaround Time
Typically ranging from 5 to 10 business days, this option provides a balance between cost and speed. It is suitable for projects where deadlines are not excessively tight and allows for more thorough quality checks. - Express or Expedited Turnaround Time
Offering delivery within 24 to 72 hours, expedited services cater to urgent prototyping needs. However, this speed comes at a higher cost and may entail a slightly increased risk of minor defects due to the accelerated manufacturing schedule. Manufacturers might use priority scheduling and streamlined processes to achieve these fast turnarounds. - Balancing Speed and Reliability
The selection of turnaround time should align with project requirements. For example, initial prototyping phases might benefit from faster turnaround times, while mass production may prioritize reliability, allowing for longer turnaround times and more detailed inspections. A thorough understanding of the manufacturer's process and quality protocols is important.
Turnaround Time | Typical Duration | Cost | Reliability | Best Use Case |
---|---|---|---|---|
Standard | 5-10 business days | Moderate | High | General prototyping, moderate timelines |
Express/Expedited | 24-72 hours | High | Moderate to High | Urgent prototyping, tight deadlines |
Manufacturing Capabilities and Technologies
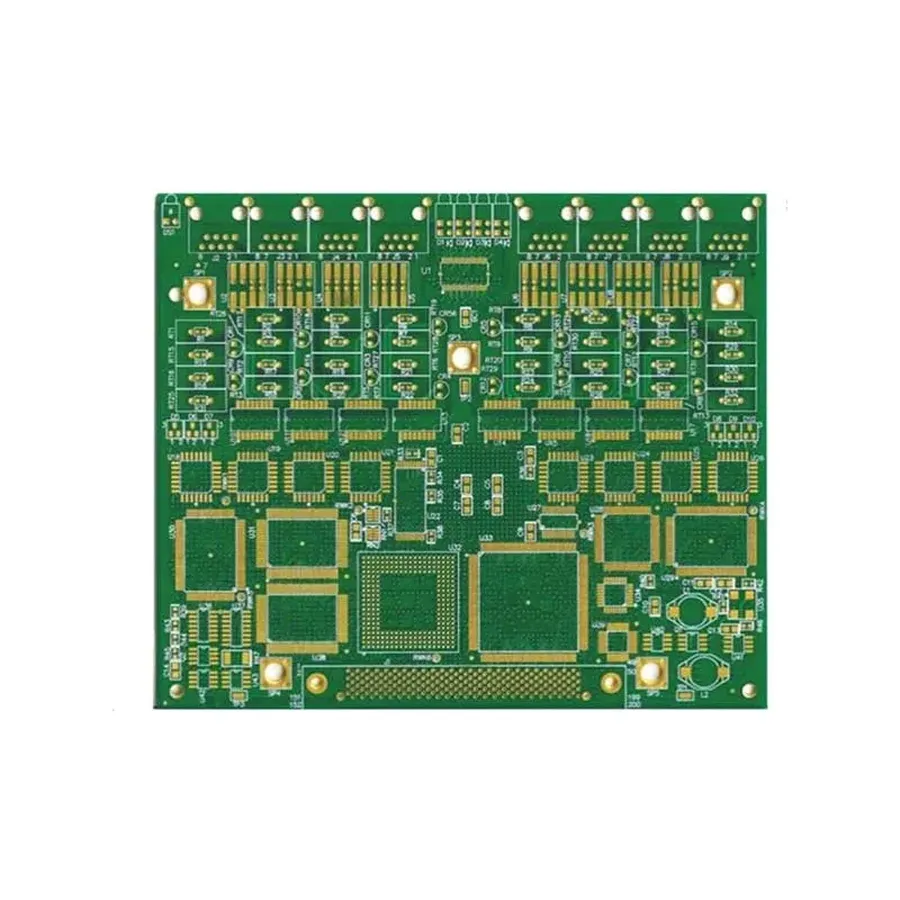
A critical aspect of selecting a quick turn PCB manufacturer is evaluating their manufacturing capabilities and the technologies they employ. These directly impact the complexity, precision, and functionality of the final product. The ability to handle diverse design requirements, from simple single-layer boards to complex multi-layered and specialized designs, is paramount for a successful partnership.
Quick turn PCB manufacturers need to offer a range of technologies to cater to different project needs. This includes capabilities for:
- Multilayer PCBs
The capability to produce PCBs with multiple layers, typically 4, 6, 8, or more, which allows for increased circuit density and design complexity. The number of layers available and the manufacturer's ability to maintain signal integrity across them should be considered. - HDI (High Density Interconnect) Boards
The capability to manufacture boards with very fine lines and micro vias, enabling higher component density and smaller form factors. This is crucial for applications requiring miniaturization and high performance. - Flex PCBs
The ability to fabricate flexible circuits, which are essential for applications requiring bending, folding, or conforming to irregular shapes. The manufacturer's experience with different flex materials and their lamination capabilities are important. - Specialized Materials
The range of available materials that goes beyond standard FR-4, including materials with high thermal conductivity, specific dielectric properties, or suitability for high-frequency applications. The availability of these materials ensures that specific design requirements for unique environments can be met. - Surface Finishes
A variety of surface finish options, such as ENIG (Electroless Nickel Immersion Gold), HASL (Hot Air Solder Leveling), or OSP (Organic Solderability Preservative). The choice of finish impacts solderability and corrosion resistance and is determined by the design and application. - Controlled Impedance
The ability to manufacture boards with controlled impedance characteristics for high-speed signals, and the ability to meet specific impedance requirements specified in the design data. This is important for maintaining signal quality in data-intensive applications
When evaluating a manufacturer, consider not only the range of capabilities but also their precision, tolerances, and the level of technological expertise applied to ensure quality results.
Quality Assurance and Certifications
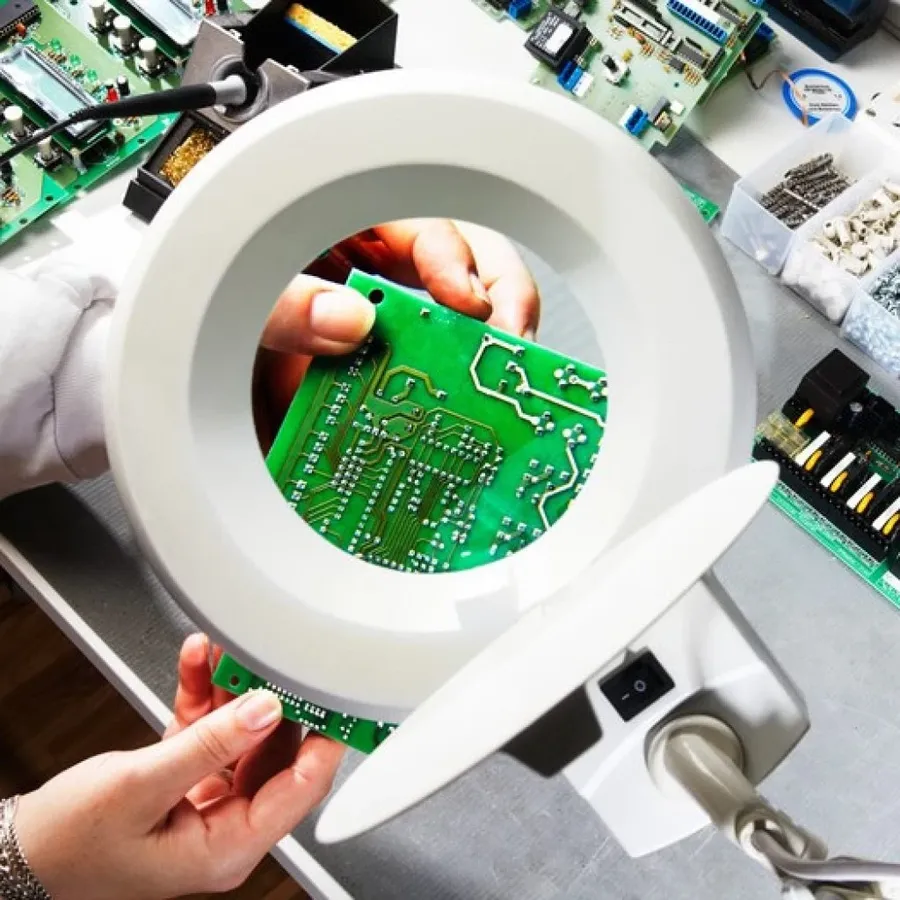
Rigorous quality assurance and adherence to industry certifications are paramount when selecting a quick turn PCB manufacturer. These measures ensure that the manufactured PCBs meet specified performance, reliability, and safety standards, which is crucial for the success and longevity of your electronic product. A commitment to quality reduces the risk of defects and subsequent costly redesigns or production delays.
Here's a breakdown of key quality assurance elements and certifications to consider:
- ISO 9001 Certification
This is a globally recognized standard for quality management systems. A manufacturer holding this certification demonstrates its ability to consistently provide products and services that meet customer and regulatory requirements. It's a benchmark for efficient process management and continuous improvement. - IPC Standards
The IPC standards, specifically IPC-A-600 (Acceptability of Printed Boards) and IPC-6012 (Qualification and Performance Specification for Rigid Printed Boards), define requirements for PCB fabrication. Compliance with these standards ensures consistent quality and reliability across different production batches and different manufacturers. - Testing and Inspection Processes
A reliable manufacturer will employ various testing and inspection methods throughout the manufacturing process. This includes automated optical inspection (AOI), electrical testing (flying probe, bed-of-nails), and X-ray inspection for multilayer boards. These processes help identify defects early and maintain consistent quality standards. - Material Traceability
The ability to track the origin and processing of materials used in PCB fabrication is vital for quality control. This ensures that only high-quality, certified materials are used and that the manufacturing process adheres to the specified parameters. - Process Control
Robust process control includes monitoring critical process parameters such as temperature, humidity, and etching rates. This level of control helps to ensure consistent quality and reduces variability. - Supplier Quality Management
A manufacturer that rigorously qualifies its own suppliers demonstrates a commitment to overall quality. They ensure that raw materials and subcomponents meet the same high standards as their own products.
Cost Efficiency and Budgeting
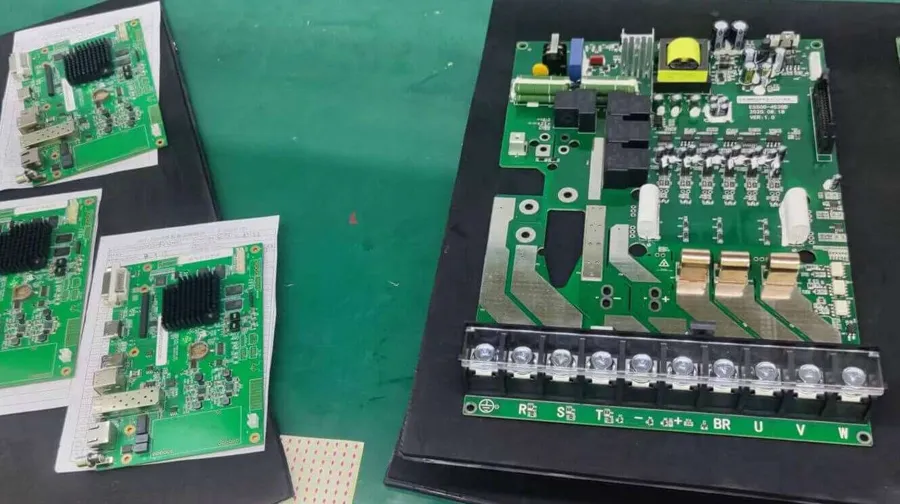
Effective cost management in quick-turn PCB manufacturing is crucial for project success, requiring a balance between budget constraints and maintaining high quality and timely delivery. Understanding the cost drivers and implementing strategic cost-saving measures is essential to optimize your investment in PCB production.
Cost Factor | Description | Optimization Strategies |
---|---|---|
PCB Size and Layer Count | Larger PCBs and more layers increase material usage and manufacturing complexity, leading to higher costs. | Optimize board size and layer count where possible; consider component placement for minimal board area. |
Material Selection | Advanced materials (e.g., high-Tg FR4, Rogers) are more expensive than standard FR4. | Use standard FR4 for typical applications; consider advanced materials only when required. |
Surface Finish | ENIG and other advanced finishes are more costly than HASL. | Choose HASL for cost-sensitive projects or ENIG for more demanding applications. |
Drill Hole Sizes and Quantity | More drills, especially smaller ones, increase production time and costs. | Standardize drill hole sizes; minimize the use of micro vias if possible. |
Turnaround Time | Faster turnaround times often involve a premium or rush fee. | Plan ahead and allow sufficient lead time to avoid rush fees. |
Volume of PCBs | Higher quantity orders typically reduce the per-unit cost due to economies of scale. | Consolidate multiple smaller orders into larger volume orders if feasible. |
Design Complexity | Intricate PCB designs with fine lines, small vias, and complex shapes result in increased manufacturing costs. | Simplify board layout where possible; adhere to standard design rules. |
Testing Requirements | Advanced electrical testing, such as flying probe or functional testing, adds to overall costs. | Incorporate a design for testability; use automated test equipment where possible. |
To optimize cost without compromising quality, consider the following:
- Design for Manufacturing (DFM)
Adhering to DFM guidelines from the outset minimizes rework and avoids expensive manufacturing errors by optimizing the design for the manufacturer’s capabilities and processes. - Negotiate Pricing
Always negotiate pricing, particularly for volume orders, as many manufacturers offer discounts based on order quantity or longer lead times. - Standardized Components
Use standardized components that are readily available and less expensive. Minimizing custom and hard-to-source components can help reduce overall material and labor costs. - Panelization
Panelize your boards, where possible to optimize the use of materials during PCB fabrication. If panelizing is not possible, consider allowing the manufacturer to panelize to reduce costs. - Utilize Software Tools
Utilize software tools like design rule checks (DRC) to ensure compliance with manufacturers' capabilities, reducing iterations, rework and subsequent costs.
Customer Support and Communication with Your Quick Turn PCB Manufacturer
Effective communication and responsive customer support are paramount when selecting a quick turn PCB manufacturer. A manufacturer that is readily accessible, provides clear answers, and offers proactive problem-solving can significantly streamline the manufacturing process, mitigate delays, and minimize the potential for costly errors. The selection of a manufacturer that values communication and prioritizes your project's needs is essential to a successful outcome.
The significance of clear communication extends beyond just answering questions. It involves a proactive approach, where the manufacturer anticipates potential issues and communicates them early, offering solutions to keep the project on track.
- Responsive Communication Channels
Look for manufacturers that offer multiple channels for communication, including phone, email, and online chat, as well as dedicated project managers. This ensures that you can reach the right person quickly when you need support. - Proactive Updates
A good manufacturer will keep you updated on the progress of your project, proactively flagging any issues and providing estimated completion timelines so that you have insight into the process. - Technical Support
Assess the availability and expertise of the manufacturer's technical support team. They should be able to answer questions about design rules, material selection, and other technical aspects of your project to ensure a smooth fabrication process. - Dedicated Project Managers
Having a dedicated project manager can simplify communication, providing a single point of contact for all your queries. This can greatly reduce confusion and improve the efficiency of the process. - Easy to Work With
The ideal manufacturer is easy to work with, understands your specific needs, and is willing to work with you collaboratively to achieve your goals.
Quick Turn PCB Manufacturer: Domestic vs. Overseas Options
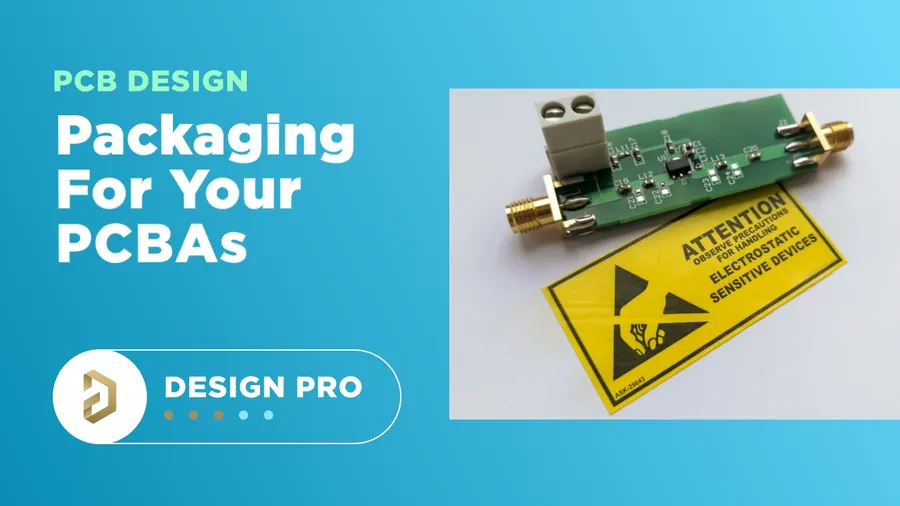
The selection between domestic and overseas quick-turn PCB manufacturers involves a multifaceted evaluation encompassing lead times, cost structures, communication efficacy, and geopolitical considerations. Each option presents distinct advantages and disadvantages that must be carefully weighed against project-specific needs and constraints.
Factor | Domestic Manufacturers | Overseas Manufacturers |
---|---|---|
Lead Times | Typically shorter, often within days or a few weeks | Potentially longer, ranging from weeks to months, due to shipping and customs |
Cost | Generally higher due to labor and operational costs | Often lower due to reduced labor and manufacturing overhead |
Communication | Easier due to similar time zones and language, often with more responsive customer support | Can be challenging due to time zone differences, language barriers, and less immediate responsiveness |
Quality Control | Often perceived as having stricter quality control due to closer oversight and adherence to domestic standards | Quality varies; rigorous selection is crucial, with some offering quality on par with domestic counterparts |
Intellectual Property Protection | Stronger protection under domestic laws and regulations | More vulnerable to IP theft; robust contracts and NDAs are important safeguards |
Geopolitical Factors | More stable supply chains and reduced geopolitical risks | Susceptible to global trade policies, tariffs, and political instability which can affect lead times and pricing. |
Supply Chain | More transparent and easier to manage due to geographical proximity | Supply chain can be complex and more difficult to manage due to distance and other external factors. |
The decision between domestic and overseas manufacturers hinges on project priorities. Domestic options are advantageous when rapid turnaround, stringent quality, and robust intellectual property protection are paramount. Conversely, overseas manufacturers might be more appealing for cost-sensitive projects with longer lead time allowances and where stringent requirements are less critical. Thorough due diligence of either option is a must.
Frequently Asked Questions About Quick Turn PCB Manufacturing
Navigating the quick turn PCB manufacturing process often involves a number of key questions. Addressing these common queries ensures a smoother and more efficient fabrication cycle, preventing potential delays and ensuring your PCBs meet the required specifications.
- What is the typical turnaround time for quick turn PCBs?
Quick turn PCB turnaround times can vary significantly based on manufacturer capabilities, complexity of the design, and current workload. Generally, expect lead times to range from 24 hours to a few days for simple designs, with more complex boards requiring slightly longer. Always confirm turnaround times with your manufacturer before placing an order. - What file formats are required for PCB fabrication?
The industry-standard file format is Gerber, which includes files for each layer of the PCB design, drill files, and solder mask/silk screen data. Some manufacturers may also accept ODB++ or IPC-2581 formats. Ensure all files are complete and accurately represent your design to prevent delays. - What are the most common PCB materials used in quick turn manufacturing?
FR-4 is the most commonly used material for quick turn PCBs because of its balance of cost, performance, and availability. Other materials like aluminum, polyimide, or Rogers materials may be available for specialized applications. Confirm with your manufacturer about material availability and options for your project. - How do I avoid delays during PCB fabrication?
Avoiding delays requires meticulous preparation. Double-check your design against the manufacturer's Design Rule Check (DRC) specifications, ensure all files are correctly formatted, and communicate clearly with the manufacturer. Respond quickly to any queries from the manufacturer during the process to prevent production delays. - What are the typical minimum order quantities for quick turn PCBs?
Minimum order quantities (MOQs) for quick turn PCBs can vary significantly among manufacturers. Some offer prototyping services with no minimum quantity, while others might require a small batch. It is crucial to clarify MOQ requirements with your chosen manufacturer before committing to an order. Consider the total number of PCBs required for your project and select a manufacturer that aligns with your volume needs to optimize cost and project timelines. - What design rule checks (DRC) should I be aware of before submitting my files?
Design Rule Checks (DRC) are essential to ensure your PCB design is manufacturable. These checks include minimum trace widths, spacing between traces, via sizes, annular rings, and clearance requirements, as well as soldermask and silkscreen specifications. Each manufacturer provides specific DRC guidelines; adherence to these is crucial for preventing errors and delays in production. Always review the manufacturer's DRC documentation and adjust your design accordingly before submitting files. Failing to pass DRC could result in additional revision cycles. - Can I request a specific surface finish for my quick turn PCBs?
Yes, you can typically specify a surface finish for your quick turn PCBs, with options like HASL (Hot Air Solder Leveling), ENIG (Electroless Nickel Immersion Gold), and OSP (Organic Solderability Preservative) being the most common. The choice of finish depends on application requirements, solderability needs, and environmental concerns. ENIG provides excellent flatness and solderability but comes at a higher cost compared to HASL. Ensure you clarify your preferred surface finish requirements with your quick turn manufacturer before placing the order, as this impacts the manufacturing process and the performance of your PCB.
Choosing the right quick turn PCB manufacturer is a critical step in the success of any electronics project. By carefully considering turnaround times, manufacturing capabilities, quality standards, costs, and customer support, you can ensure your PCBs are produced efficiently and meet your specific requirements. Leveraging a reliable quick turn PCB manufacturer enables you to bring innovative products to market faster and more effectively. When time is of the essence, your choice of a quick turn pcb manufacturer makes all the difference. Remember to always prioritize quality and communication to ensure project success.
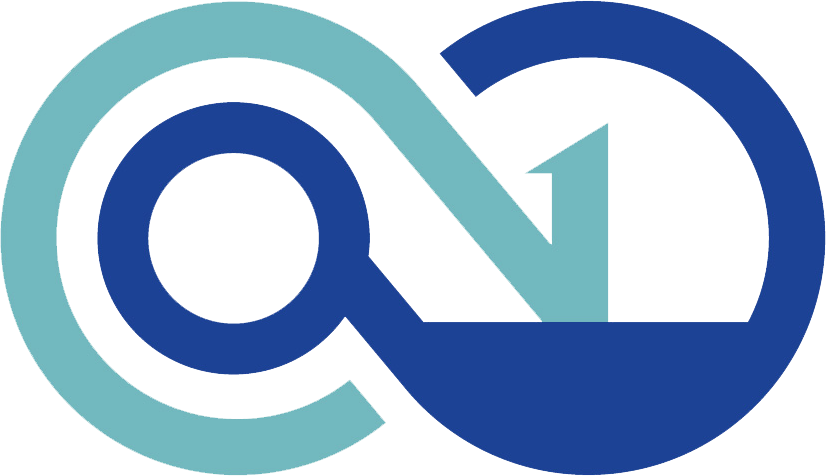