Choosing the Right Small Batch PCB Manufacturer: A Comprehensive Guide
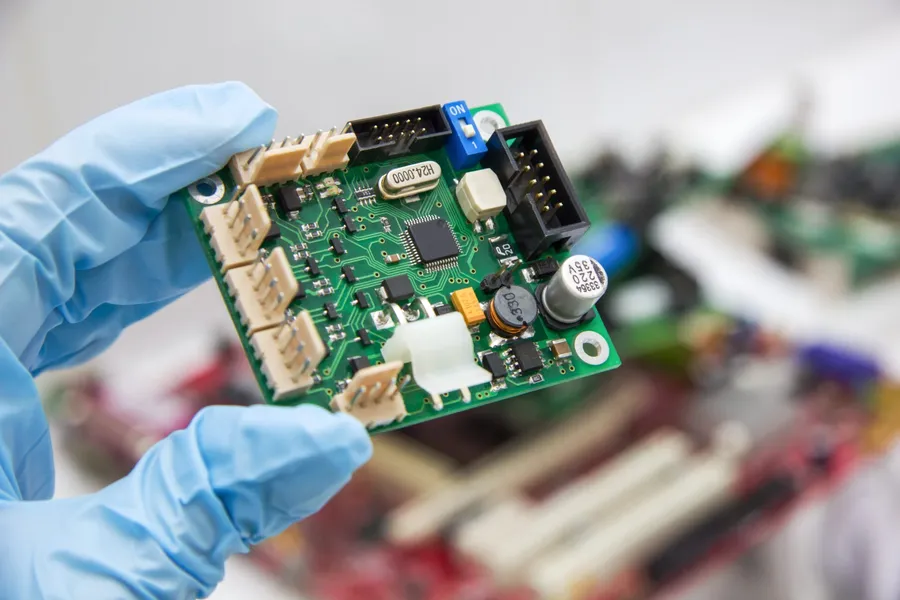
In today's rapidly evolving electronics landscape, the demand for custom and small batch PCBs is skyrocketing. Whether you're a hobbyist prototyping a new invention or a business developing a niche product, finding the right small batch PCB manufacturer is crucial. This article will guide you through the process, highlighting what to look for and how to make the best decision for your project, all while keeping in mind the importance of quality and cost-effectiveness in the world of PCB manufacturing.
Understanding Small Batch PCB Manufacturing Needs
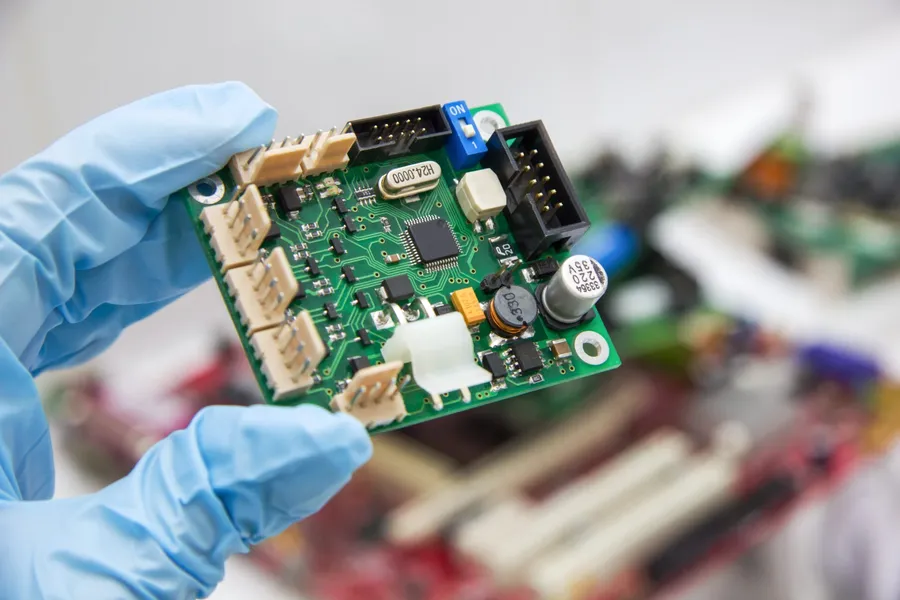
Small batch PCB manufacturing caters to projects requiring limited quantities of printed circuit boards, typically ranging from a few units to several hundred. This approach is particularly beneficial for prototyping, pilot runs, and specialized applications where large-scale production isn't necessary or cost-effective. Successfully navigating the small batch PCB landscape requires careful consideration of project requirements, production volumes, and cost constraints.
Understanding the nuances between prototype, low-volume, and mass production is crucial to selecting the right manufacturing approach. While prototypes are designed to test a design and often require only a few boards, low-volume runs cater to smaller production runs for specific products. Mass production refers to large-scale manufacturing.
Production Type | Quantity | Purpose | Cost Per Unit | Typical Lead Times |
---|---|---|---|---|
Prototype | 1-10 units | Design validation, Proof of concept | High | Fastest |
Low-Volume | 10-500 units | Pilot runs, Niche products | Medium to High | Medium |
Mass Production | 500+ units | Large-scale product manufacturing | Lowest | Longest |
Furthermore, defining project specific parameters is critical, these include the complexity of the PCB design, materials needed (e.g., FR-4, aluminum), and required turnaround time. These factors directly influence the selection of the ideal small batch manufacturer.
Key Factors to Evaluate in a PCB Manufacturer
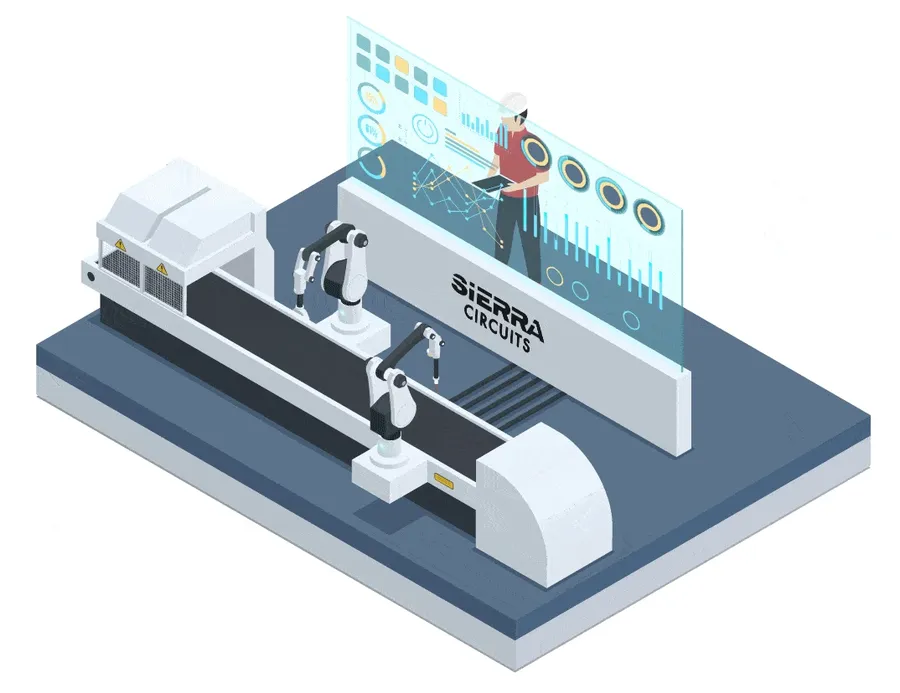
Selecting the right PCB manufacturer is crucial for the success of any electronics project. Beyond cost, several factors significantly influence the quality, reliability, and suitability of the final product. These considerations encompass manufacturing capabilities, material options, tolerances, and quality assurance processes.
When evaluating a small batch PCB manufacturer, it is essential to consider their manufacturing capabilities. This includes:
- Surface Mount Technology (SMT)
SMT is the dominant method for assembling electronic components directly onto the surface of a PCB. Manufacturers should have the equipment and expertise to handle various SMT component sizes and complexities, such as fine-pitch integrated circuits and Ball Grid Arrays (BGAs). - Through-Hole Technology
While less prevalent than SMT, through-hole assembly is still necessary for certain components that require stronger mechanical connections. A capable manufacturer will offer both SMT and through-hole capabilities to support mixed-technology designs. - Mixed-Technology Assembly
Many designs require a mix of both SMT and through-hole components. Confirm the manufacturer's ability to handle these complex assemblies and ensure a seamless fabrication process. This can reduce the workload of a designer. - Advanced Processes
Depending on your PCB needs, advanced processes might be necessary, such as blind and buried vias, microvias, impedance control, and fine-line geometries. Check if the manufacturer is equipped to handle these more sophisticated fabrication techniques.
The choice of materials directly impacts a PCB’s performance and reliability. Consider these material-related aspects:
- Material Options
Standard materials such as FR-4 are common, but other options like aluminum-backed PCBs, high-frequency laminates (e.g., Rogers), and flexible materials may be required. The chosen material should align with application requirements for thermal performance, signal integrity, and flexibility. - Tolerances
Tolerances define the permissible variations in PCB dimensions, copper trace width, and hole diameters. A manufacturer should be capable of adhering to required specifications and tolerances.
Quality control and certifications are vital for ensuring the reliability of manufactured PCBs. Key considerations are:
- Certifications
Certifications like ISO 9001, ISO 13485, or IATF 16949 indicate a manufacturer's commitment to quality management systems. Check for certifications relevant to the industry that the PCB will be deployed in. For example, a medical device should have an ISO 13485 certified PCB manufacturer. - Quality Control Processes
A reputable manufacturer should employ rigorous quality control processes, including in-process inspections, automated optical inspection (AOI), and electrical testing. Inquire about their testing methods and defect tracking. This is vital to ensure long term product reliability.
Cost Analysis: Balancing Budget and Quality
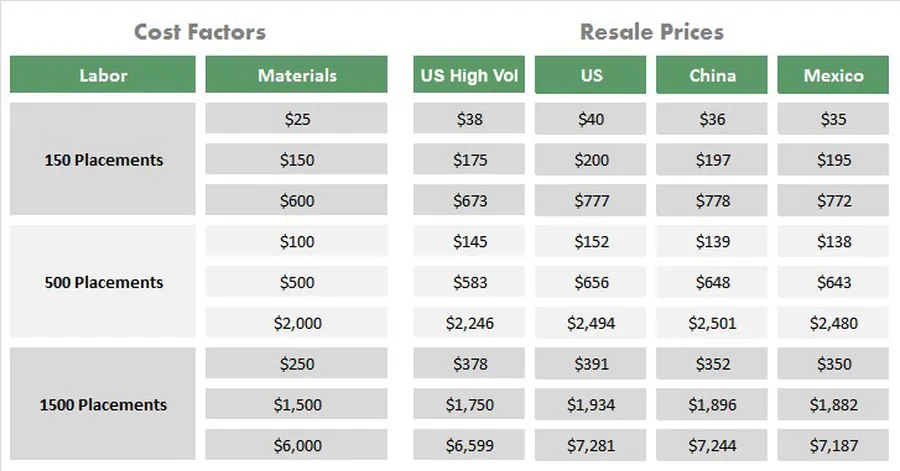
Cost analysis is crucial when selecting a small batch PCB manufacturer, requiring a thorough examination of pricing structures to balance budgetary constraints with the desired quality. A seemingly low per-board cost might be offset by high setup fees or shipping costs, making the total project cost the most important factor.
Several factors influence the final cost of a small batch PCB order. Understanding these drivers allows for more effective cost management and negotiation:
- Setup Fees
These are one-time charges to prepare the manufacturing line for your specific design. These can include tooling, programming and material handling. - Per-Board Costs
The direct cost of manufacturing each individual PCB, highly influenced by material choice, layer count, and board complexity. - Shipping Costs
Dependent on shipping speed and location and may include duties and taxes. - Material Costs
Vary significantly based on substrate type (FR-4, Rogers, etc.), copper thickness, and other specific material requirements. - Complexity of Design
Features such as the number of layers, microvias, and impedance control requirements will drive up the cost. - Quantity
Although focused on small batch, some economies of scale can still be achieved by increasing the number of units ordered.
A thorough cost comparison involves more than just looking at the per-board price. Below is a structured approach:
- Obtain Detailed Quotes
Request quotes from multiple manufacturers. Ensure these quotes itemize all costs including setup fees, per-board costs, shipping, and any other additional fees. - Analyze Pricing Structures
Compare cost structures and pricing for similar requirements between the manufacturers. Watch out for hidden costs, or additional costs that are not clear. - Consider Total Project Cost
Calculate the overall cost, not just the cost per board. Setup fees or additional services can sometimes make one manufacturer’s offer less competitive in total cost. - Factor in Quality Standards
Evaluate the cost against the quality of materials, production processes, and quality assurance. A lower price may not be worth it if the end product is substandard. - Negotiate when possible
Negotiate pricing with manufacturers where possible, particularly if there are large volumes to be made, or the relationship is long-term.
In summary, cost analysis for small batch PCB manufacturing requires careful evaluation of all cost components and a balanced consideration of price, quality, and reliability. Focusing solely on the lowest per-board price can be a costly mistake, and a more comprehensive analysis of all contributing factors is critical.
Turnaround Time: Speed vs. Precision
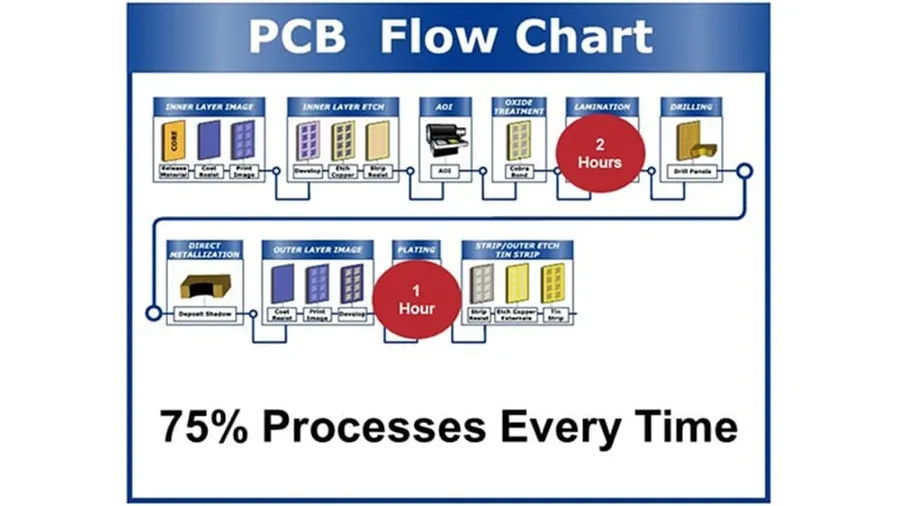
Turnaround time in small batch PCB manufacturing is a critical factor, representing the duration from design submission to the delivery of finished boards. It involves a trade-off between speed and precision, where expedited timelines may necessitate compromises, while stringent quality demands typically extend the production cycle. Understanding this dynamic is crucial for project planning and selection of a suitable manufacturer.
The quoted turnaround time significantly impacts project timelines, and is influenced by various factors:
- Manufacturing Complexity
Designs with intricate layouts, multiple layers, or fine features require more processing time. - Material Availability
Lead times can be extended due to material sourcing if there are non-standard or specialized materials. - Manufacturing Queue
During busy periods, manufacturers may have backlogs, leading to longer production times. - Specialized Processes
Processes such as controlled impedance or specific surface finishes require additional time.
When assessing turnaround time, consider the following:
- Project Requirements
Determine if you need rapid prototyping or high-quality production boards. Fast turnarounds may be adequate for initial testing, but production runs demand more rigor and validation steps, potentially increasing the lead time. - Manufacturer Capabilities
Evaluate whether the manufacturer can reliably meet the advertised turnaround time and if they use streamlined processes for efficient production. - Communication
Clear and responsive communication between customer and manufacturer can prevent delays, especially when clarifying design specifications or material availability.
Choosing between speed and precision requires a careful evaluation of your project's needs and your trade-off preference. If fast turnaround is paramount, ensure the manufacturer maintains quality control within the expedited timeframe. If higher quality and precision is required, be prepared to accept a longer lead time.
Small Batch PCB Manufacturer Comparison: Top Players
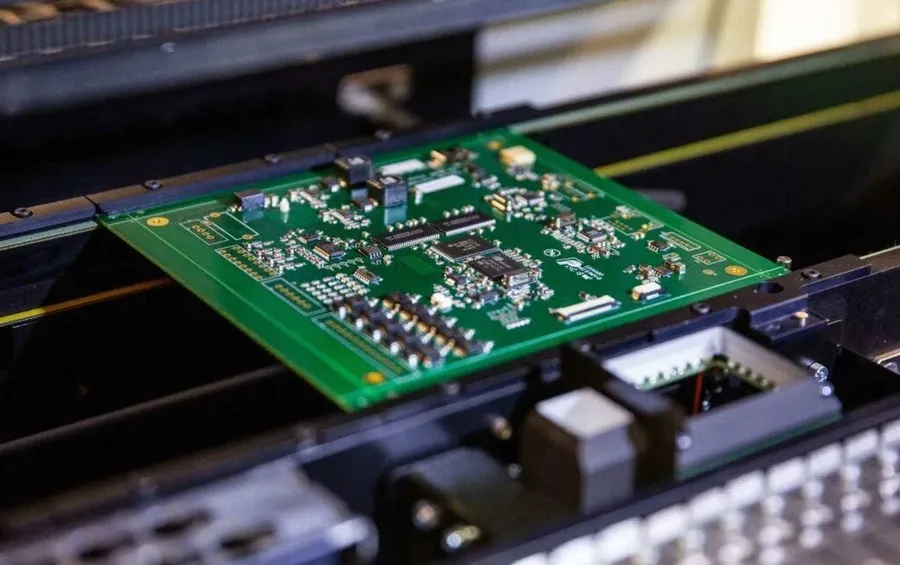
The small batch PCB manufacturing landscape is populated by several key players, each with unique strengths, weaknesses, and specializations. Understanding these nuances is crucial for selecting the ideal partner for your project. This section provides an overview of some of the most popular manufacturers.
Manufacturer | Strengths | Weaknesses | Specializations | Typical Lead Times | Cost Range |
---|---|---|---|---|---|
JLCPCB | Highly competitive pricing, fast turnaround, wide range of options, user-friendly online platform. | Can experience longer shipping times outside of Asia, limited customer support options, may not be ideal for highly complex boards with tight tolerances. | Prototyping and low-volume production, standard FR-4 PCBs, SMT assembly. | 3-7 days (manufacturing) + shipping | Very low to low |
PCBWay | Wide range of materials and advanced options, strong customer service, good for complex designs. | Higher pricing compared to JLCPCB, can have a slightly longer lead time. | Complex multilayer PCBs, flexible PCBs, advanced materials, SMT assembly. | 5-10 days (manufacturing) + shipping | Low to Mid-range |
OSH Park | High-quality, consistent results, focus on small batches, simple ordering process. | Limited material options, can be more expensive for larger orders, slower turnaround times. | Prototyping and hobbyist projects, focus on quality over price | 10-15 days (manufacturing) + shipping | Mid-range |
Seeed Studio Fusion | Offers a wide range of services including PCB manufacturing, assembly, and components sourcing, strong for IoT and prototyping. | Can be more expensive than JLCPCB for basic boards, lead times may vary depending on services used. | Prototyping and small-batch production, IoT projects, SMT Assembly. | 5-12 days (manufacturing) + shipping | Low to Mid-range |
AllPCB | Good pricing for small batches, offers instant online quoting, provides a user-friendly platform for placing orders. | Customer service is adequate but not the best, may not always meet precise deadlines, limited advanced manufacturing options. | Standard FR-4 PCBs, small batch production. | 4-8 days (manufacturing) + shipping | Very low to low |
This comparison table provides a concise overview to aid in your decision-making. The best manufacturer for your needs depends heavily on the specific requirements of your project, including complexity, budget, and desired turnaround time. Always evaluate individual needs thoroughly, comparing quotes to ensure cost-effective and suitable solutions.
PCB Assembly Services: Options and Considerations
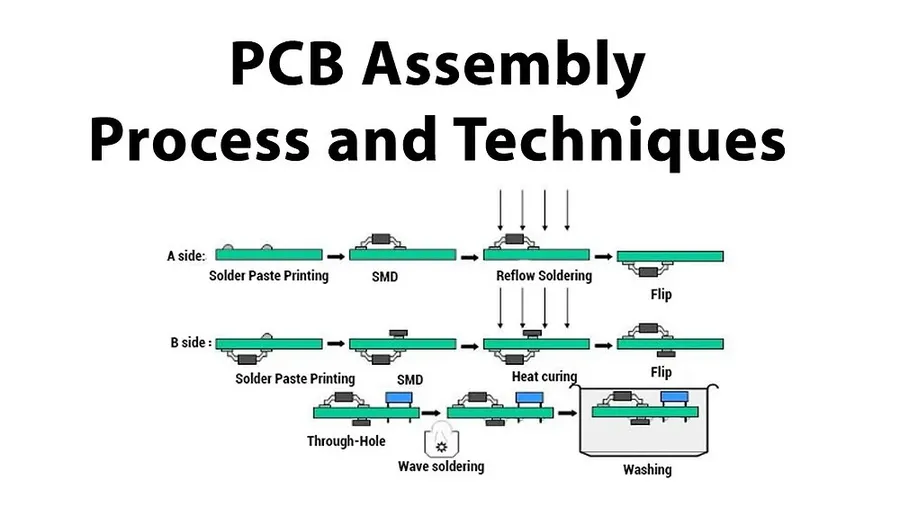
For small batch PCB production, assembly services offer a streamlined approach to manufacturing, moving beyond bare board fabrication. These services range from component sourcing to complete board assembly using technologies like Surface Mount Technology (SMT) and through-hole mounting. Understanding these options is crucial for optimizing both cost and time.
The key assembly options and considerations include:
- Component Sourcing
Manufacturers can handle the procurement of all necessary electronic components. This simplifies the process, especially for those dealing with complex Bill of Materials (BOM). It also ensures compatibility and reduces the risk of counterfeit parts, this can be particularly beneficial for small batch production where sourcing parts may be more costly or time-consuming for the client. - Surface Mount Technology (SMT)
SMT is the predominant method for placing components directly onto the surface of the PCB. It's efficient for high-density designs and automated assembly. This technology is favored for its accuracy and speed, leading to consistent results even in small batches. - Through-Hole Assembly
Through-hole assembly involves inserting components with leads into drilled holes on the PCB and soldering them to pads. While generally less automated than SMT, through-hole is necessary for specific types of components like connectors and larger capacitors. Many manufacturers offer both SMT and through-hole assembly options. - Turnkey PCB Assembly
Turnkey assembly is an end-to-end service where the manufacturer handles all aspects of PCB fabrication and assembly, including component sourcing, SMT, and through-hole assembly and final testing. This is beneficial for small batch production, especially for inexperienced clients, as it reduces complexity and ensures a finished and tested product. It also eliminates the need to manage multiple vendors. - Partial Assembly
Partial assembly involves the manufacturer assembling only some of the components on the board, while others may be provided or assembled by the client. Partial assembly can be a cost-effective option, especially for components that can easily be added by the client after assembly. - Full Turnkey vs Partial Turnkey Assembly
Choosing between full turnkey and partial assembly comes down to project requirements, cost, and in-house capability. Full turnkey is beneficial for time-saving and reducing overhead, while partial assembly may offer more cost control and flexibility where the client is sourcing some of the parts themselves.
Service | Description | Benefits | Considerations |
---|---|---|---|
Component Sourcing | Manufacturer handles procurement of all parts | Simplifies process, ensures compatibility, reduces counterfeit risk | May increase costs if sourcing is done by the manufacturer, BOM accuracy is crucial |
Surface Mount Technology (SMT) | Automated placement of components on PCB surface | High-density, efficient, accurate | Requires specialized equipment |
Through-Hole Assembly | Insertion of components into PCB holes and soldering | Necessary for certain components, reliable | May be less automated than SMT |
Turnkey PCB Assembly | Manufacturer handles all aspects from fabrication to assembly | Reduces project complexity, time-saving, tested final product | May be more expensive than partial assembly |
Partial Assembly | Manufacturer assembles select components | Cost control, flexibility | More management overhead for client |
Frequently Asked Questions About Small Batch PCB Manufacturing
This section addresses common questions regarding small batch PCB manufacturing, providing clarity on typical batch sizes, the distinction between prototyping and low-volume production, required file formats, and common lead times.
- What are the typical batch sizes considered 'small batch' in PCB manufacturing?
The definition of a 'small batch' can vary by manufacturer, but generally ranges from a few boards (e.g., 5-10) up to a few hundred (e.g., 250-500). It's crucial to discuss specific needs with the manufacturer to understand their capabilities and pricing tiers for your project's quantity. - What is the key difference between prototyping and low-volume PCB production?
Prototyping focuses on rapidly creating a small number of boards to validate the design and functionality. It prioritizes speed and flexibility, with potentially lower production quality and less stringent testing. Low-volume production, while still not mass production, aims for a larger quantity (but still considered small) of PCBs with higher quality standards, greater repeatability, and more robust testing. - What file formats are typically required by small batch PCB manufacturers to begin production?
Manufacturers typically require Gerber files (RS-274X or X2 format) which contain all the necessary information for each layer of the PCB, including copper traces, solder mask, silkscreen, and drill data. A Bill of Materials (BOM) file listing all components with their specifications is essential for assembly services. Also, a centroid file, also called a pick-and-place file, is required if you need automated assembly. - What are common lead times for small batch PCB manufacturing?
Lead times can vary significantly depending on the complexity of the design, the manufacturer's capacity, and any additional services (e.g., assembly). Typical lead times range from 2-10 business days for manufacturing and an additional 2-5 days if assembly is needed. Fast-turnaround options often have a higher cost, but can greatly reduce lead times. Confirm lead times before placing your order for better scheduling. - Do small batch PCB manufacturers offer design assistance?
Some PCB manufacturers offer design rule checks and design for manufacturability (DFM) services. These checks review the design files and ensure they are manufacturable and compliant with design rules. Some may offer full design support, but it's more common to have a design before hand to help speed up the process. The cost of these services can vary by manufacturer. - What quality control measures are typically used in small batch PCB manufacturing?
Quality control measures can vary. Some typical measures include automated optical inspection (AOI), electrical testing of the bare boards, and visual inspections during the manufacturing and assembly processes. Some manufacturers also provide reports for impedance measurements to confirm the correct impedance for high speed PCB designs. A comprehensive QC system helps to verify the quality and reliability of each board. - How do I choose between different surface finishes, and which is most suitable for my application?
The choice of surface finish depends on the application and the environment it's used in. HASL provides a good solderable surface and is cost-effective, but it isn't good for fine pitched components. ENIG provides excellent solderability and a flat surface, making it perfect for fine pitch components. OSP provides a cost-effective solution that is solderable, but needs to be soldered within 12 months. Consult with the manufacturer on what is the best surface finish for your needs.
Actionable Advice for Choosing a Small Batch PCB Manufacturer
Selecting the right small batch PCB manufacturer requires a methodical approach to ensure the final product meets specifications, budget, and timeline. This section provides practical, actionable advice to guide you through the selection process, from initial preparation to ensuring the reliability of your finished boards.
- Prepare Comprehensive Documentation
Before reaching out to manufacturers, assemble a detailed documentation package. This should include Gerber files, bill of materials (BOM), specific layer stack-up requirements, any design rules, assembly drawings, and testing specifications. Thorough documentation minimizes ambiguity, reduces errors, and allows manufacturers to provide accurate quotes and realistic lead times. - Define Your Needs Clearly
Explicitly define your project's requirements: the number of boards you need (even for potential future orders), desired materials (FR-4, aluminum, etc), the complexity of the board (single-sided, double-sided, multilayer), any special features (impedance control, blind/buried vias), surface finish, acceptable tolerances, and required assembly methods. Clear and concise specifications help manufacturers understand your requirements and ensures the final product aligns with your expectations. - Request Multiple Quotes
Do not settle for the first quote you receive. Contact at least three different manufacturers. Provide each manufacturer with the same detailed documentation to ensure the quotes are comparable. Analyze the quotes based on more than just price, consider factors such as quality, turnaround time, communication responsiveness, and additional services offered. - Check Manufacturing Capabilities
Confirm that the manufacturer has the specific capabilities required for your project. Do they have the right machinery for SMT, through-hole, or mixed-technology assembly? Can they handle the specific materials you need? What tolerances can they achieve? If your project has complex requirements, prioritize manufacturers who can demonstrate that they have the experience and technology to handle them. - Evaluate Certifications and Quality Control
Verify that the manufacturer has the necessary certifications (ISO 9001, IPC standards, etc). Certifications indicate that they adhere to established quality control processes. Request information on their testing procedures (e.g., flying probe, visual inspection, functional tests) and quality assurance protocols. High-quality PCBs are often worth a slightly higher price if it reduces risk in the long run. - Establish Effective Communication Channels
Establish clear and direct communication channels with your selected manufacturer. Ensure they have a responsive point of contact to address any questions, clarifications, or changes during the production process. Good communication is crucial for resolving issues quickly and efficiently, preventing delays, and ensuring a smooth production process. - Start with a Prototype Run
If this is a new design, consider starting with a prototype run before placing a large order. This allows you to test the functionality, fit, and performance of the board. Any design flaws or manufacturing issues can be identified and corrected, minimizing the risk of large-scale production errors.
The Future of Small Batch PCB Manufacturing
The small batch PCB manufacturing sector is undergoing rapid transformation, driven by technological advancements and evolving market demands. These shifts are not only improving the efficiency and capabilities of PCB production but also fundamentally altering how products are developed and brought to market.
Several key trends are shaping the future of this industry:
- Increased Automation and Robotics:
The integration of robotics and automation in PCB manufacturing processes is steadily increasing. This includes automated pick-and-place machines for component assembly, automated optical inspection (AOI) systems for quality control, and automated material handling systems. The result is reduced manual labor, increased production speed, and enhanced precision in small batch PCB manufacturing. - Advanced Manufacturing Technologies:
Advanced manufacturing techniques, such as laser direct structuring (LDS) and additive manufacturing (3D printing) for PCB production, are being adopted for certain applications, especially for complex and specialized designs. This allows for greater design flexibility and the ability to create more intricate PCB layouts. - Smart Factories and IoT Integration:
The concept of smart factories, which leverages Internet of Things (IoT) technologies for real-time data collection, process monitoring, and predictive maintenance, is becoming more prevalent. This leads to optimized production flows, reduced downtime, and higher yield rates. - Emphasis on Sustainability and Eco-Friendly Practices:
There is an increasing focus on implementing sustainable manufacturing practices within the PCB industry. This includes the use of eco-friendly materials, the reduction of waste, and the adoption of more energy-efficient production methods. Many manufacturers are also working to comply with environmental regulations and standards. - Growing Demand for Flexible and Rapid Prototyping:
The accelerating pace of product development is driving the need for PCB manufacturers to provide greater flexibility and rapid prototyping services. This includes faster turnaround times, more efficient communication between designers and manufacturers, and on-demand manufacturing services. This allows businesses to iterate on design more quickly and get to market faster.
These technological advancements are not just impacting the manufacturing process but also influencing the world of small batch PCB manufacturers. The shift towards digital manufacturing allows for more efficient handling of small batch orders, where the same setup can be reused for different designs with slight variations. Additionally, these advances will enable a more distributed manufacturing model where PCB production can occur closer to the point of need, rather than being concentrated in large factories.
In conclusion, the future of small batch PCB manufacturing is heading towards greater automation, advanced techniques, and a focus on sustainability and agility. These trends will empower businesses to innovate faster, create more customized products, and bring them to market more efficiently. Selecting the right partner and keeping a close watch on technological trends is crucial for success.
Selecting the ideal small batch PCB manufacturer is a multifaceted decision that depends heavily on the specifics of your project. By carefully weighing cost, quality, turnaround time, and available services, you can ensure a successful manufacturing process. Keep the future of PCB manufacturing in mind, and look for a small batch pcb manufacturer that can grow with your business, and continue providing a quality and cost effective solution. Remember, the right partnership with a reliable small batch PCB manufacturer is critical for your project’s success.
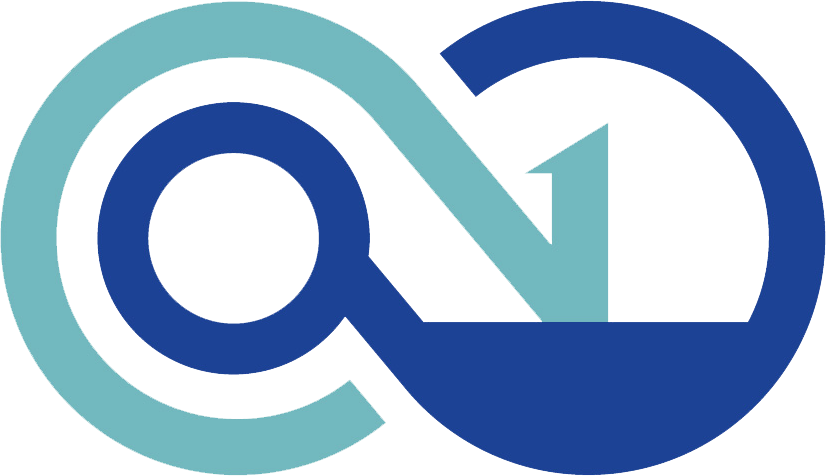