Choosing the Right SMT Stencil Manufacturer: A Comprehensive Guide
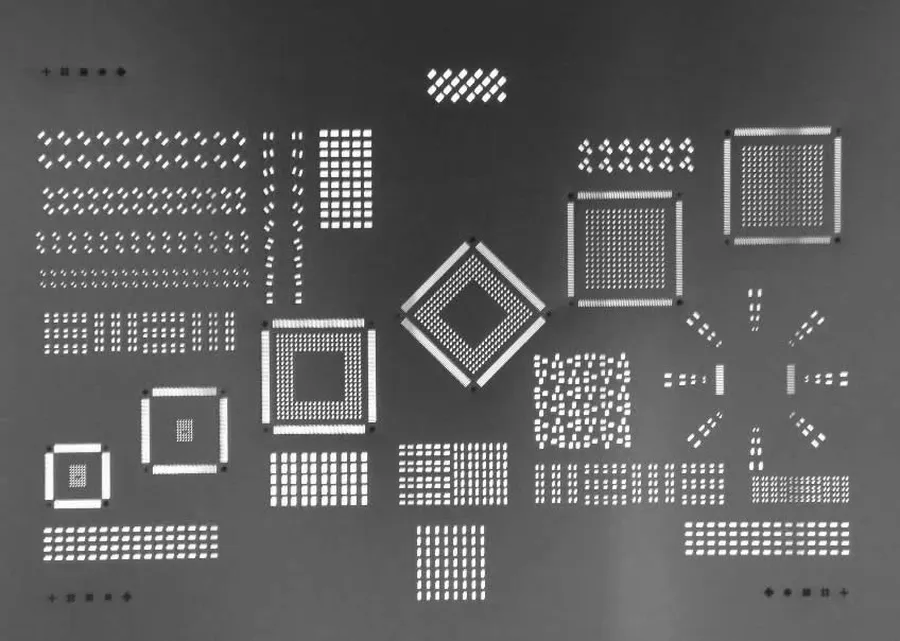
In today's electronics manufacturing landscape, precision is paramount. The SMT (Surface Mount Technology) stencil plays a pivotal role in ensuring accurate solder paste application onto printed circuit boards (PCBs). Just like an artist uses a stencil to create intricate designs, an SMT stencil manufacturer crafts the crucial tools for electronic assemblies. This guide will navigate you through the selection process, helping you choose the best SMT stencil manufacturer to meet your specific needs.
Understanding the Importance of SMT Stencils
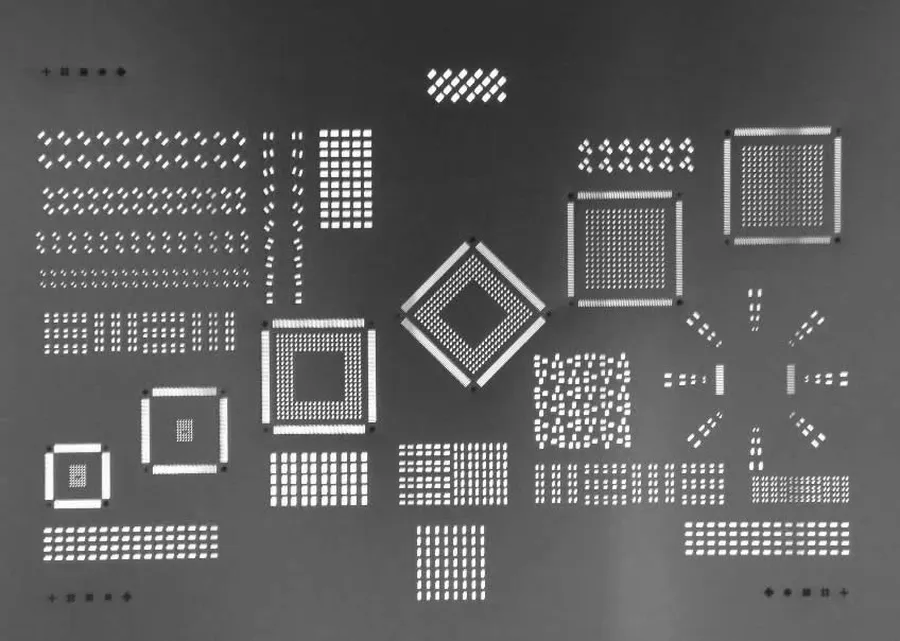
SMT stencils are fundamental tools in the Surface Mount Technology (SMT) process, serving as a critical intermediary for the precise application of solder paste onto printed circuit boards (PCBs). Their accurate design and manufacture directly impact the quality and reliability of assembled electronic devices by ensuring correct solder deposition, which is paramount for electrical connectivity and mechanical integrity of surface mount components. A high-quality stencil is, therefore, non-negotiable for consistent and reliable PCB assembly.
Types of SMT Stencils: Framed vs. Frameless
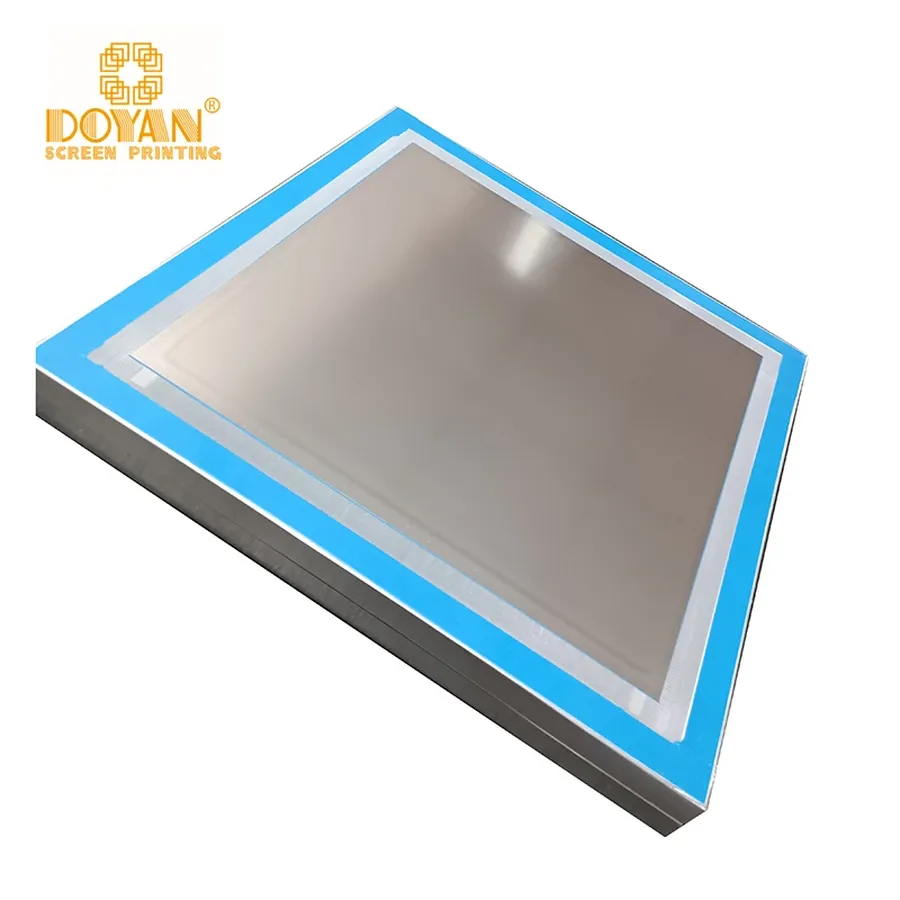
SMT stencils are crucial for applying solder paste accurately onto circuit boards; these stencils are generally categorized into two primary types: framed stencils and frameless stencils. The selection of stencil type greatly affects the cost, precision, and efficiency of PCB assembly operations.
Feature | Framed Stencil | Frameless Stencil |
---|---|---|
Structure | Stencil sheet permanently mounted on a frame | Stencil sheet tensioned and held in a frame during use, and removed after use. |
Cost | Higher initial cost, primarily due to frame. | Lower initial cost, only the stencil sheet itself. |
Durability | Robust and less prone to damage with frame support. | More delicate and requires careful handling, storage. |
Storage | Requires more storage space because of the frame. | Requires less storage space. |
Precision | Generally highly accurate due to consistent tension. | Accuracy depends on the tensioning frame. |
Reusability | More durable, can be reused many times. | Stencil sheet is not re-usable. |
Application | Suitable for high volume production and automated systems. | Suitable for low to mid-volume production. |
The choice between framed and frameless stencils depends on a range of factors, including production volume, budget constraints, and the available equipment in the assembly line. Framed stencils are typically more suitable for large-scale, automated processes where consistency and durability are paramount. Frameless stencils, on the other hand, can be a cost-effective option for smaller runs where storage space is limited.
Key Factors to Consider When Selecting an SMT Stencil Manufacturer
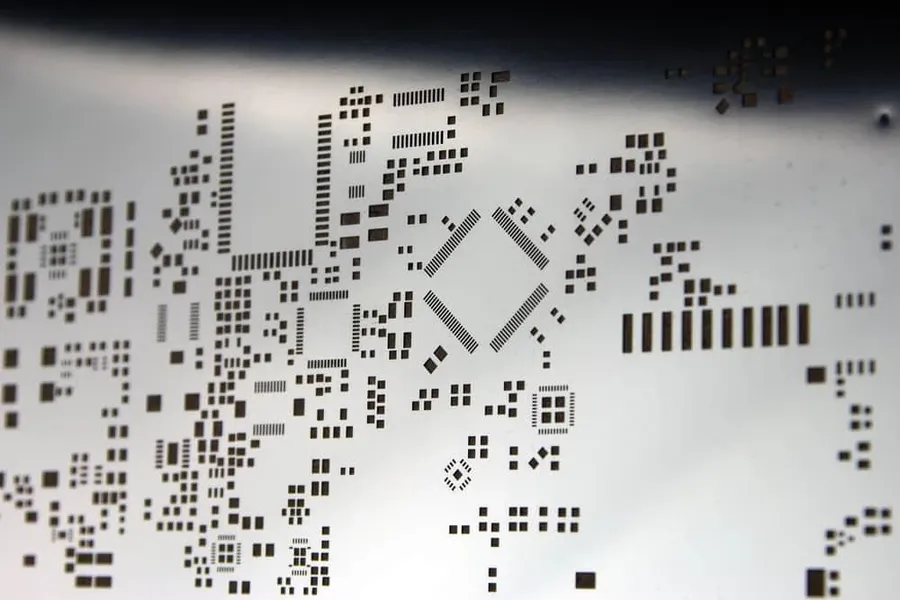
Selecting the right SMT stencil manufacturer is crucial for ensuring the quality and reliability of your PCB assembly process. Several key factors warrant careful consideration to ensure optimal results. These factors include the stencil material, precision, turnaround time, cost, and the level of customization offered.
- Stencil Material
The most common materials are stainless steel and, less frequently, nickel. Stainless steel is favored for its durability, cost-effectiveness, and resistance to wear. Nickel stencils offer increased hardness and smoother aperture walls but come at a higher cost. The choice hinges on your project’s specific demands and tolerances. - Precision
Precision in stencil manufacturing is measured by the accuracy of aperture placement and dimensions, the smoothness of aperture walls, and the consistency of stencil thickness. Laser-cut stencils generally provide high precision, whereas electroformed stencils offer the smoothest aperture walls. High precision stencils are crucial for fine-pitch components, ensuring accurate solder paste deposition. - Turnaround Time
The time taken from order placement to stencil delivery is crucial, particularly for projects with tight schedules. Different manufacturers have varying production capacities and delivery times. Evaluate this aspect in line with project timelines. Faster turnaround times often come with added costs. - Cost
The cost of SMT stencils varies depending on material, size, complexity, and the manufacturer's pricing structure. Analyze the overall cost, encompassing tooling charges, the cost of materials, and other related fees. It's crucial to consider the cost-effectiveness of the solution, factoring in both initial cost and long-term quality. - Customization Options
Customization options include varying stencil thickness, specific aperture shapes or sizes, and unique frame designs. Stencil manufacturers should be able to accommodate project-specific requirements. A flexible manufacturer that can handle unique projects is often a valuable asset.
Factor | Description | Impact |
---|---|---|
Material | Stainless steel, nickel | Durability, cost, aperture quality |
Precision | Aperture accuracy and smoothness | Solder paste deposit control |
Turnaround Time | Production and delivery speed | Project timelines, responsiveness |
Cost | Overall pricing of the stencil | Project budget and profitability |
Customization | Ability to adapt to unique needs | Project flexibility and accuracy |
Evaluating SMT Stencil Manufacturing Capabilities
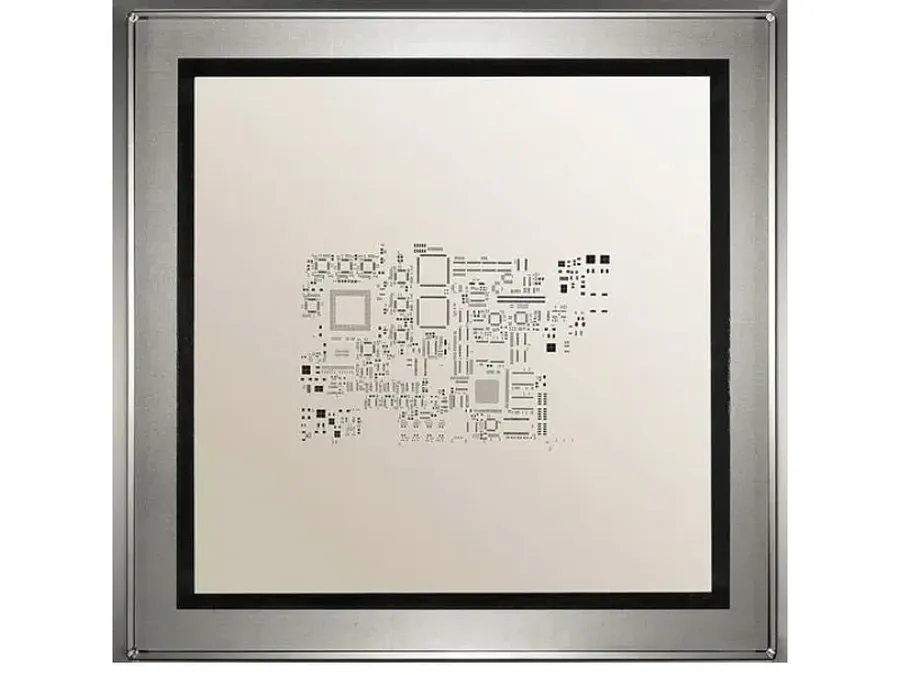
The quality of an SMT stencil is directly linked to the manufacturing processes employed. Manufacturers utilize various techniques, each with its own impact on stencil precision, durability, and overall performance. Understanding these methods is crucial for selecting a stencil that meets the specific requirements of your PCB assembly process. Key manufacturing capabilities include laser cutting, electroforming, and chemical etching; each has unique characteristics that dictate the suitability of the resultant stencil for different applications.
Manufacturing Process | Description | Advantages | Disadvantages | Typical Applications |
---|---|---|---|---|
Laser Cutting | A high-powered laser precisely cuts openings in the stencil material. | High accuracy and repeatability, flexible design capabilities, relatively fast turnaround. | Can produce slightly tapered apertures, may not be ideal for extremely fine-pitch applications. | General-purpose SMT stencils, medium to high-volume production |
Electroforming | A layer of metal is deposited onto a substrate using electrodeposition. The unwanted metal is removed, leaving precise openings. | Extremely precise and smooth apertures, excellent for fine-pitch components, ability to produce complex designs with smooth sidewalls. | Relatively more expensive and longer manufacturing time compared to laser cutting. | Ultra-fine pitch applications, complex component designs, high-precision requirements. |
Chemical Etching | Chemicals are used to remove metal from the stencil material in the areas not protected by a mask. | Cost-effective for large quantities and relatively simple designs. | Lower precision compared to laser cutting or electroforming, suitable for larger pitch components only, sidewalls may be less smooth and precise. | Larger pitch components, basic designs, low to medium-volume production. |
Material Selection: Stainless Steel vs. Other Options
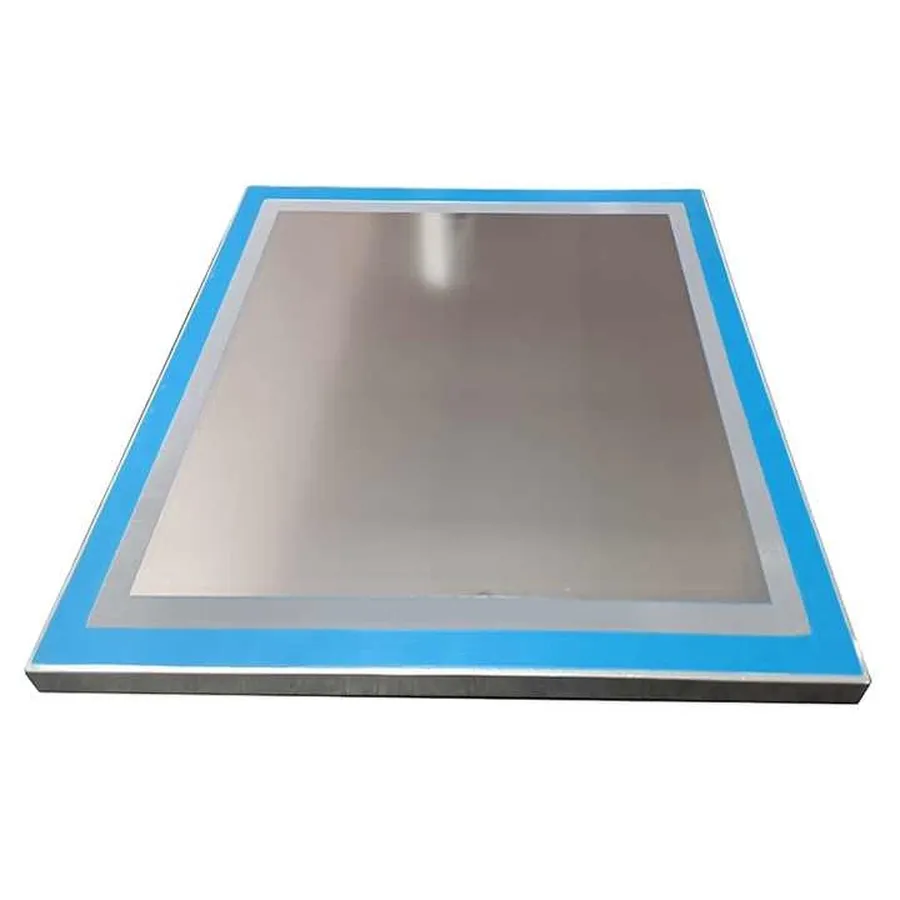
The selection of materials for SMT stencils is crucial, directly impacting the stencil's performance, durability, and ultimately, the quality of the printed solder paste. Stainless steel is the most prevalent material due to its balance of properties, but other options like nickel and composite materials offer unique advantages for specialized applications.
Material | Durability | Accuracy | Cost | Typical Applications | Notes |
---|---|---|---|---|---|
Stainless Steel | High | Good | Moderate | General SMT assembly | Standard choice, good balance of properties |
Nickel | Very High | Excellent | High | Fine-pitch components, high-precision applications | Offers improved hardness and smoother aperture walls. |
Composite Materials | Variable | Variable | Variable | Specialized applications (e.g., large panels) | Properties dependent on specific composition. |
While Stainless steel (typically 304 or 316 grade) offers a good balance of properties, including chemical resistance, it's crucial to assess application-specific needs when evaluating other materials. For instance, nickel provides increased hardness and smoother aperture walls that contribute to enhanced paste release, which is particularly beneficial for fine-pitch components. Composite materials may offer unique combinations of properties, such as thermal stability and resistance to warping for large PCB panels, however they are less commonly used due to the variability in performance.
Frequently Asked Questions About SMT Stencils
This section addresses common inquiries regarding SMT stencils, providing clarity on their lifespan, manufacturing processes, appropriate thicknesses, and the distinctions between solder paste stencils and other types of stencils used in electronics manufacturing.
- What exactly is an SMT stencil?
An SMT (Surface Mount Technology) stencil is a thin sheet, typically made of stainless steel or nickel, with precisely cut openings that correspond to the pads on a printed circuit board (PCB). It's used to deposit solder paste onto the PCB prior to the placement of surface mount components. The stencil ensures that the right amount of solder paste is applied to the correct locations, a critical step in automated PCB assembly. - How long does an SMT stencil typically last?
The lifespan of an SMT stencil depends on several factors, including the material, the number of uses, the cleaning frequency, and the handling practices. A well-maintained stainless steel stencil can last for thousands of prints. However, factors like damage from improper cleaning, physical deformation, or wear can shorten its life. Framed stencils generally have a longer usable life due to the frame providing rigidity and protection. - What are the primary methods for manufacturing SMT stencils?
The most common methods for manufacturing SMT stencils include laser cutting, chemical etching, and electroforming. Laser cutting is widely used for its precision and versatility, involving a laser beam to vaporize the material to create apertures. Chemical etching uses a chemical to dissolve away the unwanted material. Electroforming is a highly precise method that creates stencils with very smooth walls and is used for fine-pitch components. Each method offers different trade-offs in terms of precision, cost, and turnaround time. - What is the minimum stencil thickness used in SMT assembly?
The minimum stencil thickness is determined by the smallest components being used in the circuit. Very small components (like 0201 or 01005 packages) will require thinner stencils that allow for a smaller volume of solder paste to be deposited. Common stencil thicknesses range from 3 mil (0.076 mm) to 8 mil (0.203 mm), but the minimum may be as low as 2 mil (0.051 mm). The actual minimum thickness depends on the paste type and the manufacturing method, as well as the component size. - What is the difference between a solder paste stencil and other stencils?
The term "solder paste stencil" is generally synonymous with an SMT stencil; its primary purpose is to apply solder paste in the SMT process. While other stencils may exist for applications outside of SMT (e.g. applying adhesives or protective coatings), SMT stencils are specifically designed for the precise deposition of solder paste which consists of a mix of solder particles, flux and other compounds. Their precision, material composition, and fabrication methods are optimized for this purpose. - How should SMT stencils be cleaned and maintained?
SMT stencils should be cleaned regularly to remove residual solder paste, which can affect the quality of future prints. Manual cleaning with a non-abrasive cleaner and lint-free cloths or automated stencil cleaners with appropriate solvents are common methods. Proper storage in a clean, dry environment, away from physical damage and deformation, is also critical for maintaining stencil quality and longevity. Adhering to manufacturer-recommended cleaning procedures is essential. - Are there environmental considerations when using SMT stencils?
Yes, environmental considerations are important. The cleaning solvents used with stencils can be harmful if not handled and disposed of responsibly. Additionally, the materials used to manufacture stencils often have to be sourced responsibly and with recycling or disposal in mind. Many suppliers are working to use materials and processes that reduce their overall environmental impact. Compliance with environmental and safety regulations should be considered when selecting a stencil manufacturer and when cleaning stencils.
Cost-Effective Strategies for SMT Stencil Procurement
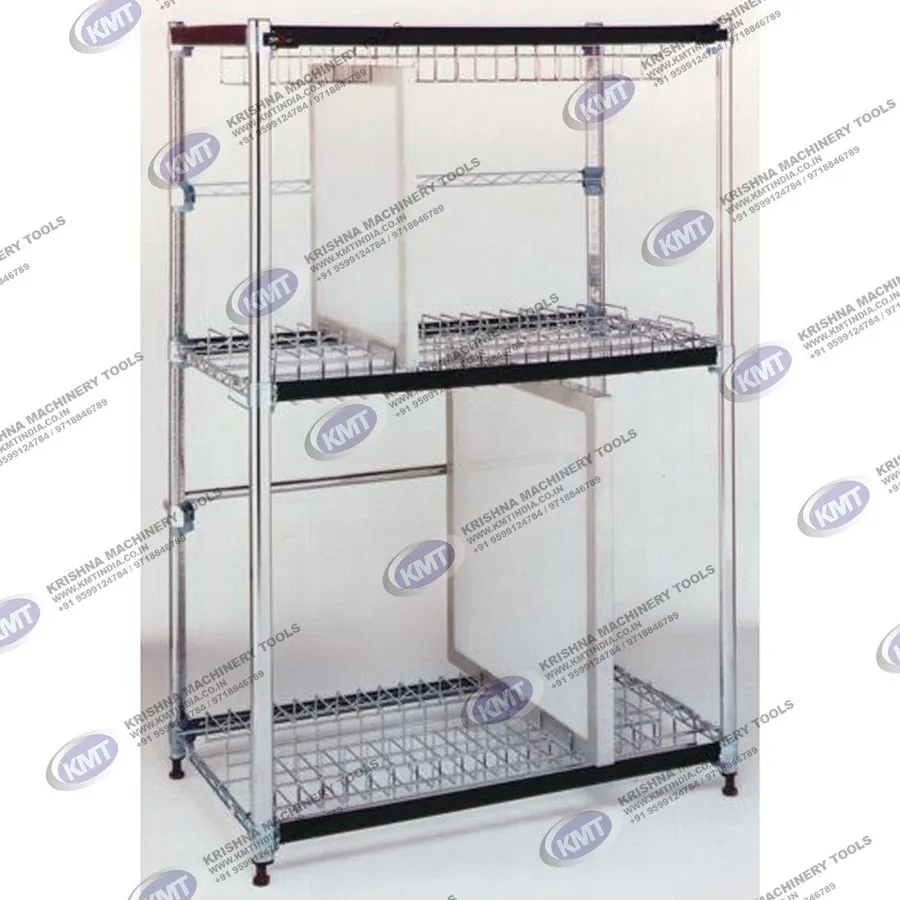
Optimizing SMT stencil procurement costs without sacrificing quality requires a strategic approach that considers order volumes, stencil types, and supplier relationships. By carefully evaluating these factors, businesses can achieve significant savings while maintaining the precision and reliability necessary for effective PCB assembly.
- Strategic Order Volume
Consolidate stencil orders where possible to leverage volume discounts offered by manufacturers. Evaluate your production schedule to accurately estimate stencil needs and minimize the frequency of small, expensive orders. Consider creating a buffer stock for recurring designs to benefit from larger order quantities. - Stencil Type Selection
Match the stencil type to the specific requirements of each PCB project. For high-volume production runs, a durable framed stencil may be the most cost-effective choice in the long term, as they are more robust and can withstand repeated use, reducing the need for frequent replacements, which is cost effective and time-saving, whilst for prototyping and low-volume production frameless stencils offer a lower initial cost. - Material Considerations
While stainless steel is the most common and reliable material for SMT stencils, explore alternatives if project specifications allow. Consider the life cycle and required accuracy for each type. For instance, nickel stencils offer even higher precision, but may not be required for every application and may have a higher cost. - Optimized Design for Manufacturability (DFM)
Ensure that PCB designs are optimized for stencil manufacturability. This can minimize the complexity of stencil production, leading to lower costs and quicker turnaround times. Complex designs, such as very small aperture sizes or very fine pitch, can increase manufacturing costs. - Supplier Relationship Management
Establish a good working relationship with your chosen manufacturer. Consistent partnerships often result in improved pricing and service, as suppliers are more likely to accommodate your specific needs. Regular communication and feedback will contribute to a more efficient and cost-effective process. - Negotiation and Quotation
Always obtain multiple quotations and do not hesitate to negotiate pricing, especially for larger projects or when securing long-term supply agreements. Price transparency is vital, be aware of any hidden costs and ensure they are clearly defined before engaging the manufacturer. - Careful Handling and Storage
Prolong the usable life of your stencils by implementing proper handling and storage procedures. Store stencils in a clean, dry environment and handle with care to prevent damage. This will minimise the frequency of replacement.
Comparing SMT Stencil Manufacturers: A Table Analysis
Selecting the right SMT stencil manufacturer is crucial for ensuring the quality and consistency of PCB assembly. This section provides a comparative analysis of different manufacturers, highlighting their strengths, weaknesses, and ideal project applications. This structured comparison will enable informed decision-making based on specific needs and project requirements.
Manufacturer | Strengths | Weaknesses | Ideal Project Types | Material Options | Technology | Turnaround Time |
---|---|---|---|---|---|---|
Manufacturer A | High precision, excellent laser cutting quality, strong customer support | Higher cost, longer lead times for complex stencils | High-density, fine-pitch SMT assembly, prototypes | Stainless steel, Nickel | Laser Cutting, Nano-coating | 3-7 business days |
Manufacturer B | Cost-effective, fast turnaround time, good for large volume orders | Lower precision for very fine-pitch components, limited customization options | Large volume, standard SMT assembly, cost-sensitive projects | Stainless steel | Laser Cutting | 1-3 business days |
Manufacturer C | Specializes in electroformed stencils, excellent for ultra-fine pitch components, high accuracy | Higher cost, longer lead times | Ultra-fine-pitch SMT, advanced technology assembly, highly precise applications | Nickel, Custom Alloys | Electroforming | 5-10 business days |
Manufacturer D | Offers a wide range of stencil types and materials, flexible customization, good for diverse projects | May have inconsistent quality, varying turnaround times | Mix-volume SMT assembly, custom projects, research and development | Stainless steel, Nickel, Polymer | Laser Cutting, Etching | 2-7 business days |
Manufacturer E | Good local support, fast turnaround for standard stencils, often offers PCB Assembly services | Limited technology options, limited material choices, may be costly if not local | Prototype SMT assembly, smaller volume PCB assembly, quick turn PCB needs | Stainless Steel | Laser Cutting | 1-3 business days |
Future Trends in SMT Stencil Technology
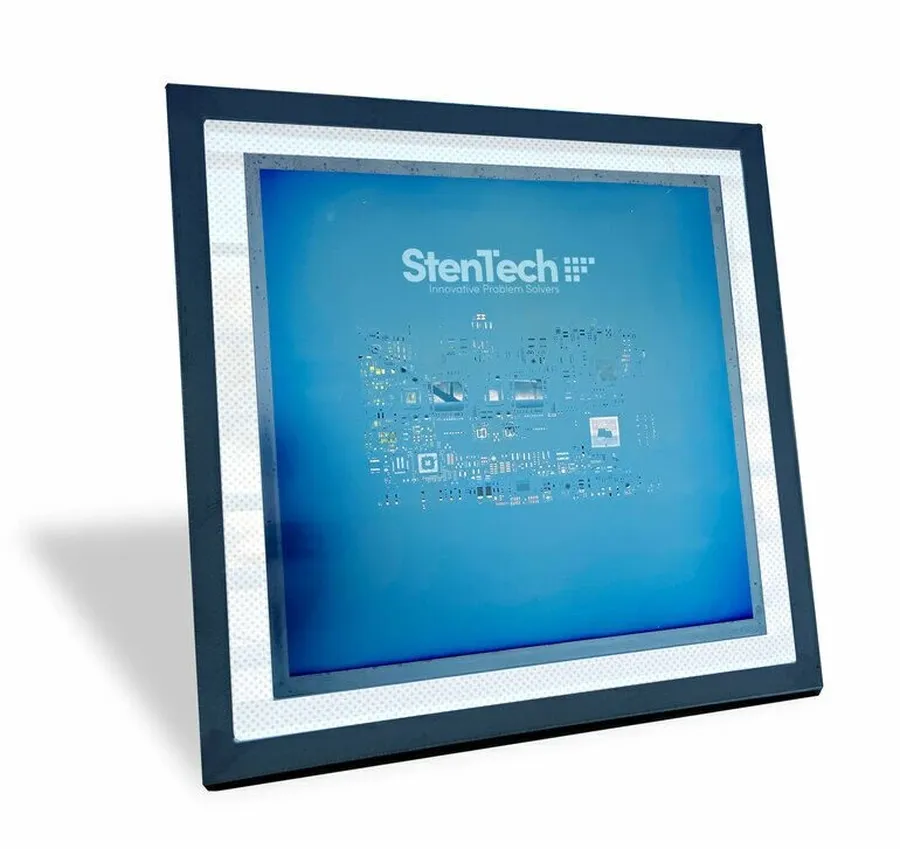
The landscape of SMT stencil technology is continually evolving, driven by the demand for increased precision, efficiency, and reliability in electronic assembly. Several key trends are emerging that promise to shape the future of SMT stencils, impacting both manufacturing processes and the performance of finished products. These advancements focus on materials, manufacturing methods, and stencil features.
One significant area of development is in nano-coatings. These ultra-thin layers applied to stencil surfaces improve solder paste release characteristics, reducing defects such as bridging and solder balling. This translates to higher yields and less rework. Additionally, research into alternative materials beyond traditional stainless steel, such as nickel alloys and polymers, aims to address specific application challenges. These materials may offer increased durability, improved fine-pitch printing capabilities, and even reduced cost in specific manufacturing volumes. Furthermore, process improvements such as refined laser cutting techniques, and electroforming processes are enhancing precision and consistency in stencil manufacturing. These technological strides facilitate finer feature geometries in stencils and improved performance overall.
Choosing the right SMT stencil manufacturer is a critical decision affecting the quality and efficiency of your PCB assembly process. By understanding the different types of stencils, evaluating manufacturer capabilities, and considering factors such as material, precision, and cost, you can select a partner that aligns with your manufacturing requirements. Working with a reputable SMT stencil manufacturer like those listed in this guide will ensure you are set up for success. Ultimately, the right stencil will contribute to the overall reliability and consistency of your electronic products, making your investment in the right SMT stencil manufacturer worthwhile.
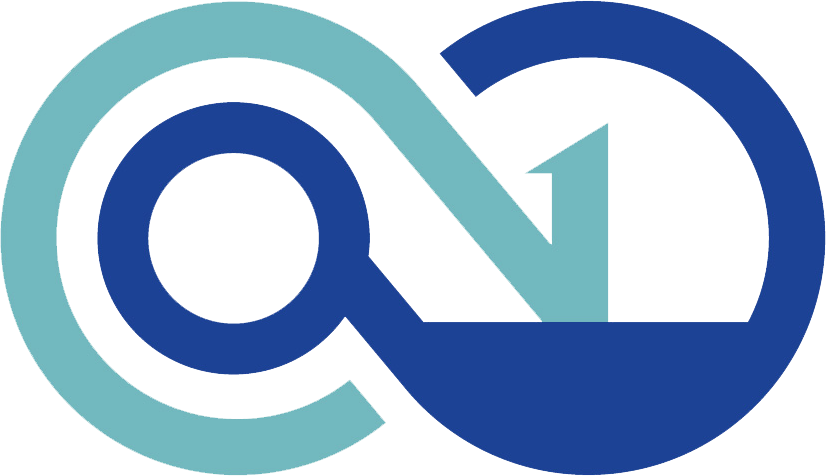