Choosing the Right Sonic PCB Manufacturer: A Comprehensive Guide

In the fast-paced world of electronics, finding the right PCB manufacturer is crucial. Similar to how a well-structured musical piece relies on precision and harmony, high-quality PCBs form the foundation of modern devices. This article explores how to navigate the options, focusing on what to consider when selecting a 'sonic pcb manufacturer,' drawing on insights from companies like Sonic Manufacturing Technologies and their peers in the field.
Understanding Sonic PCB Manufacturing Services

Sonic PCB manufacturing encompasses a comprehensive suite of services crucial for producing high-quality printed circuit boards. These services include PCB design, fabrication, assembly, and rigorous testing, each essential for ensuring the final product meets the specified performance and reliability standards. The decision between in-house and outsourced manufacturing options significantly impacts project timelines, cost, and quality.
Advanced technologies and sophisticated production floor capabilities, such as those employed by Sonic Manufacturing, are pivotal in achieving precision and consistency. These capabilities can include automated assembly lines, advanced testing equipment, and specialized processes for handling complex designs and materials.
- PCB Design Services
This involves translating electronic circuit schematics into detailed PCB layouts, optimizing for performance, manufacturability, and cost. It includes component placement, trace routing, and consideration of thermal and signal integrity. - PCB Fabrication
The fabrication process transforms the design layout into physical PCBs. This involves etching, drilling, plating, and layering materials to create the conductive traces and connections. The precision and quality of the fabrication directly impact the final board's functionality. - PCB Assembly
Assembly is the process of placing electronic components onto the fabricated PCBs. This can range from simple manual assembly to fully automated pick-and-place machines, ensuring consistent and accurate component mounting. - PCB Testing
Rigorous testing is necessary to ensure the assembled PCBs are functioning correctly. This can involve various techniques such as in-circuit testing (ICT), functional testing, and other specific tests based on product requirements.
Aspect | In-House Manufacturing | Outsourced Manufacturing |
---|---|---|
Control | Greater control over the entire process | Less direct control, dependent on manufacturer's processes |
Cost | Higher initial investment in equipment and facilities | Potentially lower per-unit costs for large quantities |
Turnaround Time | Potentially faster for prototypes or small batches | May involve longer lead times |
Expertise | Requires investment in internal expertise | Access to manufacturer's specialized knowledge |
Scalability | Limited by in-house capacity | More flexible scaling for large volume production |
Key Factors to Consider When Choosing a Sonic PCB Manufacturer
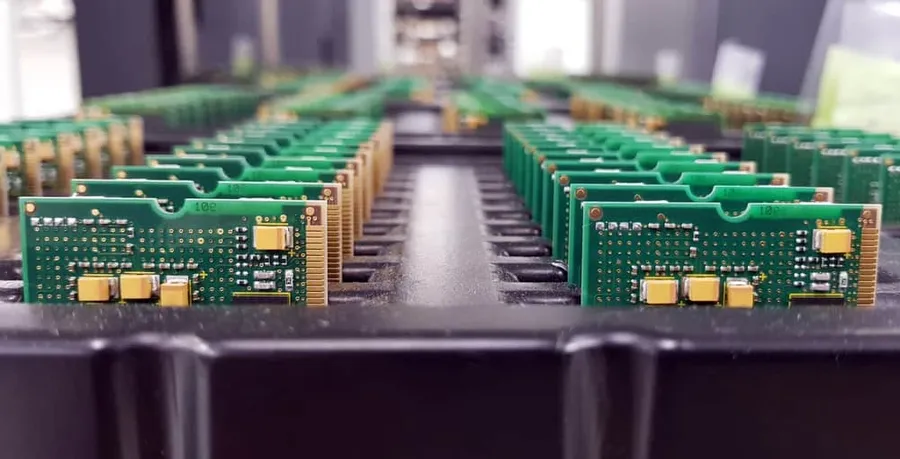
Selecting the right sonic PCB manufacturer is critical for ensuring the quality and timely delivery of electronic products. Several key factors must be carefully evaluated to make an informed decision, directly impacting the final product's performance and project timelines. These factors include production capabilities, quality certifications, turnaround time, cost-effectiveness, and engineering support, all of which must align with the specific needs of your project. For instance, Sonic Manufacturing Technologies exemplifies a provider that emphasizes these crucial aspects, offering a benchmark for what clients should seek in a PCB manufacturing partner.
Factor | Description | Impact |
---|---|---|
Production Capabilities | The range of PCBs a manufacturer can produce (e.g., single-layer, multi-layer, rigid, flex), along with their production volume and technological sophistication. | Directly affects the manufacturer's ability to handle diverse PCB designs and complex projects, impacting both the technical feasibility and scalability of production. |
Quality Certifications | Evidence of adherence to industry standards and quality management systems, such as ISO 9001, ISO 13485 (for medical devices), and IPC standards. | Ensures that the manufacturer maintains a consistent quality of products, minimizing defects and meeting required compliance standards, which is crucial for reliable performance. |
Turnaround Time | The time taken from placing an order to receiving the final PCBs, including fabrication, assembly, and any necessary testing. | Affects project timelines significantly. Shorter turnaround times allow faster product development and time-to-market, which is essential for competitive advantage. |
Cost-Effectiveness | The overall cost, including manufacturing, assembly, and testing, relative to the quality and services provided. | Balances budget constraints with the quality needed, and affects project profitability. Identifying a manufacturer that offers optimal value ensures cost efficiency without compromising quality. |
Engineering Support | The availability of expert engineering support for design optimization, problem-solving, and technical assistance throughout the manufacturing process. | Reduces the risk of errors and ensures that PCB designs are producible, and can help optimize performance. Effective engineering support can address complex challenges that may occur. |
Geographic Location and its Impact on Manufacturing
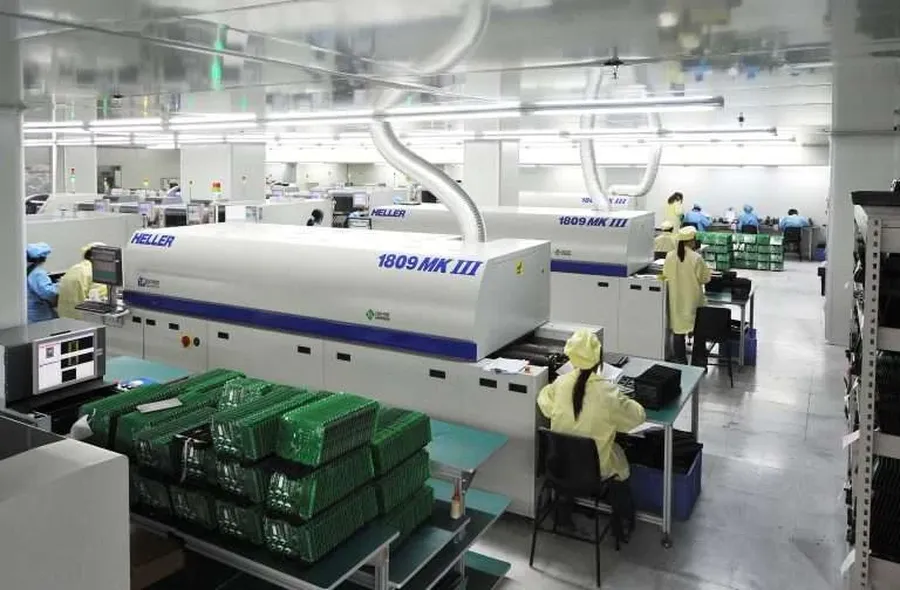
The geographical location of a PCB manufacturer significantly impacts various aspects of the manufacturing process, from logistics and communication to cost and turnaround time. Selecting between a local and an overseas manufacturer requires careful evaluation of these factors, especially when considering the complexities of global supply chains.
When evaluating PCB manufacturers, the decision between domestic and international options hinges on several key trade-offs, impacting factors beyond pure cost. For instance, while a manufacturer closer to your location, such as one in the US like Sonic Manufacturing Technologies, might offer quicker shipping and ease of communication, offshore manufacturers may present more economical solutions and a broader range of production capabilities. Each decision carries distinct logistical implications which need to be accounted for.
Factor | Local Manufacturer (e.g., Sonic Manufacturing in California) | Overseas Manufacturer (e.g., Sonic Tech India) |
---|---|---|
Shipping Time | Faster, shorter lead times due to proximity | Longer, may be subject to international shipping delays |
Shipping Costs | Lower shipping costs | Higher shipping costs, especially for large quantities |
Communication | Easier and more immediate communication within similar time zones and language | Potential communication barriers and time zone differences |
Customs and Tariffs | Minimal customs and tariff issues | Complex customs procedures and potential import tariffs |
Visit and Auditing | Easier to visit facilities for audits and meetings | Difficult and costly to visit facilities for audits and meetings |
Intellectual Property Protection | Stronger legal protection under domestic law | Potentially weaker IP protection in certain overseas locations |
Cost | Generally higher production costs but lower overall costs in terms of logistics and communication | Generally lower production costs, but may be offset by increased shipping, customs, and communication costs |
Turnaround time | Faster production lead times due to proximity and efficient communication | Longer production lead times due to geographical distances and customs procedures |
Comparing Sonic PCB Manufacturers: A Table Analysis
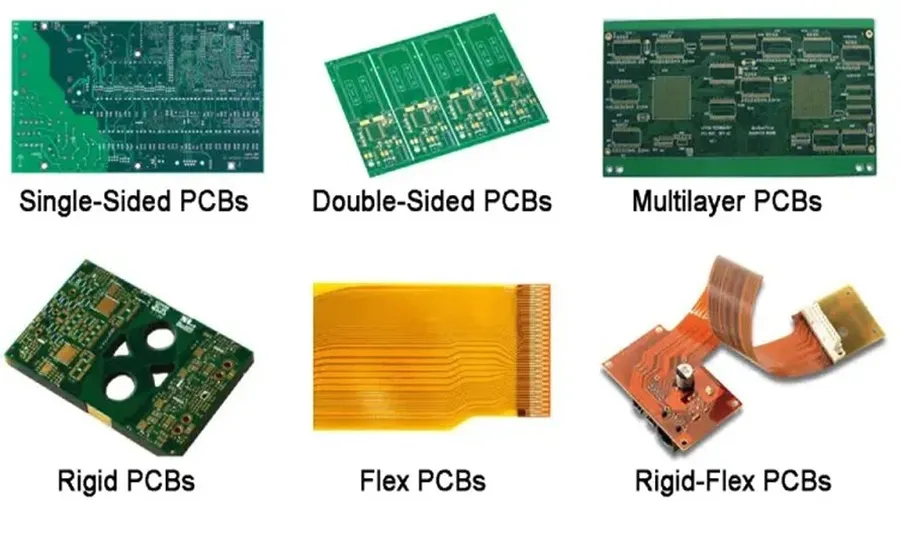
A thorough comparison of sonic PCB manufacturers requires a detailed look at several key factors beyond just name recognition, as differences in technology, certifications, pricing, and customer support can significantly influence the outcome of your project. This section provides a structured analysis to help you navigate the landscape of PCB manufacturing options.
Manufacturer | Technology Focus | Key Certifications | Typical Pricing (Relative) | Customer Support | Geographic Location | Specialization |
---|---|---|---|---|---|---|
Sonic Manufacturing Technologies (Hypothetical) | High-mix, low-volume; SMT, Through-hole | ISO 9001, ISO 13485, AS9100 | Medium to High | Dedicated project managers, technical support | USA (California) | Medical, Aerospace |
Sonic Technology India Inc (Hypothetical) | Cost-effective solutions, Medium-volume, SMT | ISO 9001 | Low to Medium | Email support, technical documentation | India | Consumer Electronics |
Manufacturer X (Hypothetical) | Advanced HDI PCBs, Fine-pitch BGA | ISO 9001, IPC-A-600 | High | 24/7 technical support | USA (Multiple Locations) | Telecommunications, Data Centers |
Manufacturer Y (Hypothetical) | Quick-turn prototypes, Small-batch assembly | ISO 9001, UL Certified | Medium | Responsive online chat, phone support | Europe | Industrial automation |
Manufacturer Z (Hypothetical) | Large-scale production, Automated assembly | ISO 14001, OHSAS 18001 | Low | Limited direct support, focus on volume | Asia (Multiple Locations) | High volume electronics |
The Role of PCB Design in the Manufacturing Process
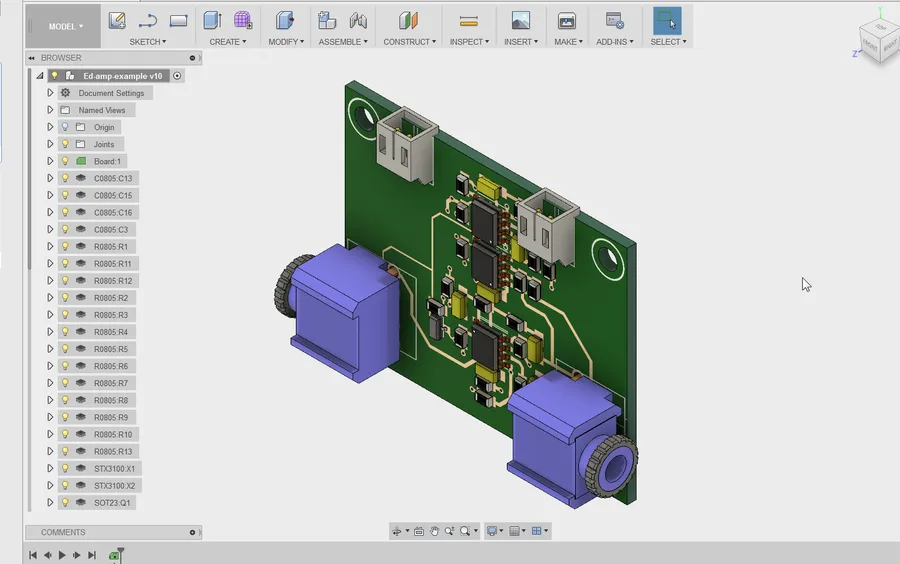
The printed circuit board (PCB) design phase is fundamental to the success of any electronic product. A well-executed PCB layout is not merely a schematic translation, but a carefully crafted blueprint that dictates the functionality, reliability, and manufacturability of the final assembly. It is an iterative process, requiring collaboration between design engineers, and manufacturing teams and represents a critical juncture where design intent meets physical realization.
Professional PCB design services are essential because they bring expertise in several key areas:
- Component Placement and Routing
Optimizing the physical layout of components and their interconnections to minimize signal interference, reduce impedance, and maximize heat dissipation which directly impacts performance and longevity. - Design for Manufacturability (DFM)
Adhering to design rules and guidelines specific to the manufacturing processes used by sonic PCB manufacturers. This ensures that the design is physically realizable on the production floor, preventing costly rework and delays and improving yields. Consideration is given to aspects such as trace width and spacing, via sizes, and component pad sizes. - Signal Integrity Analysis
Employing simulation tools to analyze signal behavior within the PCB, ensuring reliable signal transmission at high speeds. This is critical to the performance of modern electronics. - Thermal Management
Designing the PCB layout to effectively dissipate heat generated by electronic components. Effective heat management is key to the longevity and stability of electronic devices and prevents thermal failure. - Material Selection
Choosing the appropriate PCB materials (e.g., FR-4, ceramic) based on thermal and electrical requirements. Material properties directly affect signal integrity, thermal performance, and overall durability.
The integration of PCB design with manufacturing at a company like Sonic Manufacturing, allows for a cohesive process from schematic capture to final product, fostering high quality control and efficient production. This integration means a seamless feedback loop between design and manufacturing teams, which allows issues to be addressed in the early stages of development, avoiding costly rework and accelerating time to market.
In summary, PCB design is an indispensable element of the manufacturing process. A professional approach to PCB design ensures high-quality, reliable, and manufacturable products, and maximizes the efficiency of the manufacturing processes, ultimately delivering products that meet or exceed customer expectations.
Prototyping and Testing for Quality Assurance
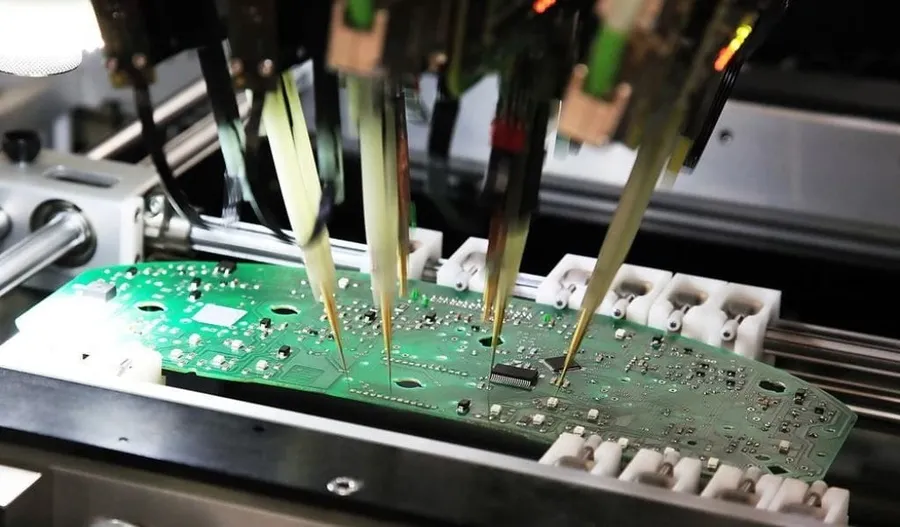
Rigorous prototyping and testing are paramount in PCB manufacturing to ensure the final product's reliability and performance. These processes identify potential design flaws or manufacturing defects early, preventing costly issues down the line and ensuring the manufactured PCBs meet the stringent requirements for their intended applications. A sonic pcb manufacturer's capabilities in these areas directly affect overall product quality and dependability.
The prototyping stage allows for iterative design adjustments and validation before committing to full-scale production. Following prototyping, systematic testing is performed to ensure design specifications are met and the PCBs are fit for purpose. This testing phase is vital to the entire product's dependability.
The capabilities of a sonic PCB manufacturer directly affect the thoroughness and efficacy of quality control. Utilizing advanced equipment and comprehensive testing methods, manufacturers can identify and rectify errors, thus improving the product’s reliability and performance.
Frequently Asked Questions About Sonic PCB Manufacturing
This section addresses common questions regarding sonic PCB manufacturing, providing clarity on lead times, material selection, PCB types, and compliance standards. Understanding these aspects is crucial for a successful manufacturing partnership.
- What are typical lead times for sonic PCB manufacturing?
Lead times vary based on complexity, order quantity, and the manufacturer's current workload. For standard PCBs, expect 1-3 weeks, while complex or high-volume orders might take longer. Always confirm specific lead times with your chosen sonic PCB manufacturer, such as Sonic Manufacturing Technologies, during the quotation process. - What materials are commonly used in sonic PCB manufacturing?
Common PCB materials include FR-4 (a fiberglass epoxy laminate), as well as materials like polyimide, aluminum, and Rogers for specialized applications. The choice of material depends on the application's thermal, electrical, and mechanical requirements. A high-quality sonic PCB manufacturer will help you choose the correct material. - What are the different types of PCBs offered by a sonic PCB manufacturer?
Sonic PCB manufacturers typically offer single-sided, double-sided, and multi-layer PCBs. Single-sided PCBs have conductive layers on one side, double-sided on both, and multi-layer PCBs have three or more conductive layers, enabling greater circuit density and functionality. The complexity of your design dictates the required PCB type. - Why are compliance standards important in sonic PCB manufacturing?
Compliance standards, such as IPC standards, ensure PCBs meet quality, reliability, and safety requirements. Adherence to these standards is critical for product performance and safety. A reputable sonic PCB manufacturer will be certified and rigorously follow these standards. These standards are related to manufacturing processes and product quality, ensuring interoperability between different manufacturers. - Can sonic PCB manufacturers handle high-volume orders?
Many manufacturers, including those specializing in sonic PCBs, are equipped to handle both low and high-volume production. High-volume capabilities often require automated processes, and may have facilities such as Sonic Tech India to manage increased demand. Always verify capacity with the specific manufacturer to ensure they can meet your project needs and deadlines. - Does a sonic PCB manufacturer offer design assistance?
Reputable sonic PCB manufacturers, such as Sonic Manufacturing Technologies, often provide design support services. This may include design review, layout assistance, and signal integrity analysis. This collaboration ensures the PCB design is optimized for manufacturability and performance, which leads to a more reliable final product and efficient production cycle. - What are the key considerations when choosing a sonic PCB manufacturer?
Key factors include production capabilities, material options, quality certifications, turnaround time, cost-effectiveness, and engineering support. Choosing a manufacturer that aligns with these requirements ensures a smooth and successful manufacturing experience.
Future Trends in Sonic PCB Manufacturing Technologies
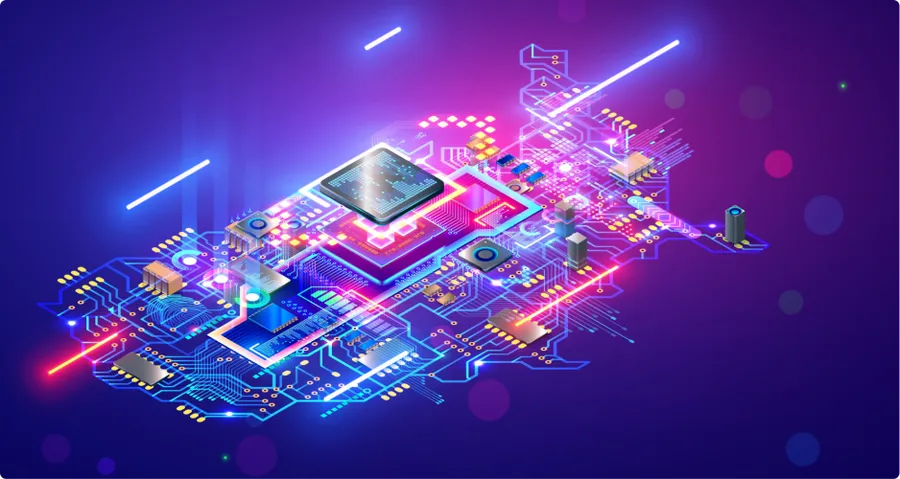
The sonic PCB manufacturing landscape is continually evolving, driven by advancements in materials, processes, and technologies. These changes are not only enhancing the capabilities of PCB manufacturers but are also reshaping the electronics industry as a whole. Understanding these emerging trends is crucial for businesses seeking to stay competitive and deliver high-performance, reliable electronic products.
- Advanced Materials
The pursuit of higher performance and miniaturization is driving the adoption of advanced materials in PCB manufacturing. This includes the use of new substrates with improved thermal and electrical properties, as well as the integration of nanomaterials to enhance conductivity and durability. These materials enable the creation of more robust and efficient circuits. - Automation and AI
The integration of automation and artificial intelligence (AI) is transforming PCB manufacturing processes. AI-driven systems can optimize production flows, predict maintenance needs, and improve quality control. Automated assembly lines and robotics reduce human error, enhance throughput, and decrease lead times, which significantly impacts the cost and efficiency of production. - Additive Manufacturing (3D Printing)
Additive manufacturing, or 3D printing, is emerging as a viable option for rapid PCB prototyping and customized production. It enables the creation of complex circuit geometries and multi-layer structures with greater flexibility than traditional methods. This technology significantly accelerates the design iteration process. - Flexible and Wearable Electronics
The demand for flexible PCBs is rising, particularly in the context of wearable electronics and IoT applications. Manufacturers are developing new techniques to fabricate PCBs that can bend, stretch, and conform to various shapes, leading to smaller and lighter electronic devices. This also requires advancements in conductive inks and materials that can withstand mechanical stress. - Sustainability
Growing environmental awareness is pushing the PCB manufacturing sector to adopt sustainable practices. This involves using eco-friendly materials, reducing waste and energy consumption, and implementing better recycling methods. Manufacturers are increasingly adopting practices to lower their environmental footprint and adhere to environmental regulations. - High-Frequency Circuit Design
The advancement of wireless communication and high-speed computing requires PCBs that can operate at increasingly higher frequencies. This demand pushes manufacturers to innovate in the areas of material selection, design tools, and fabrication processes. Manufacturers are constantly working on new techniques to address signal integrity and thermal management challenges.
Choosing the right sonic PCB manufacturer is a critical decision that impacts product quality and time to market. By carefully considering factors such as service offerings, technology, location, and cost, you can ensure a successful partnership. Companies like Sonic Manufacturing Technologies are leading the charge, but a thorough comparison of options ensures you will align with the best manufacturer to meet your specific needs. The evolution of sonic PCB manufacturing will continue to shape future technological advancements and product development.
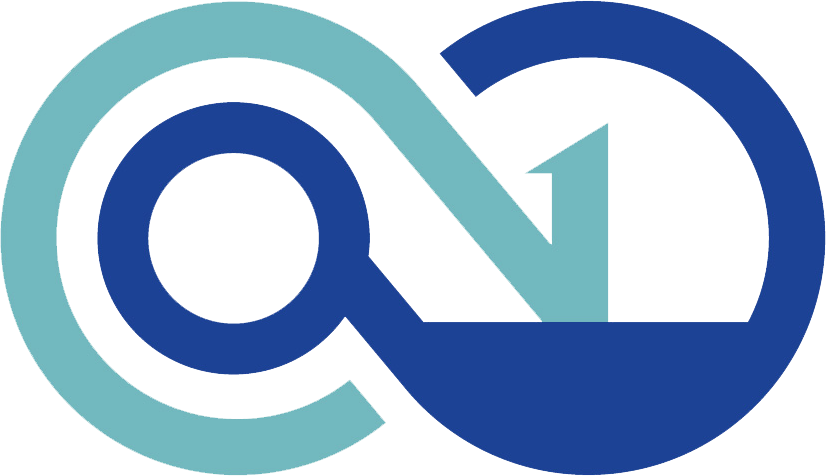