Choosing the Right Teflon PCB Manufacturer: A Comprehensive Guide
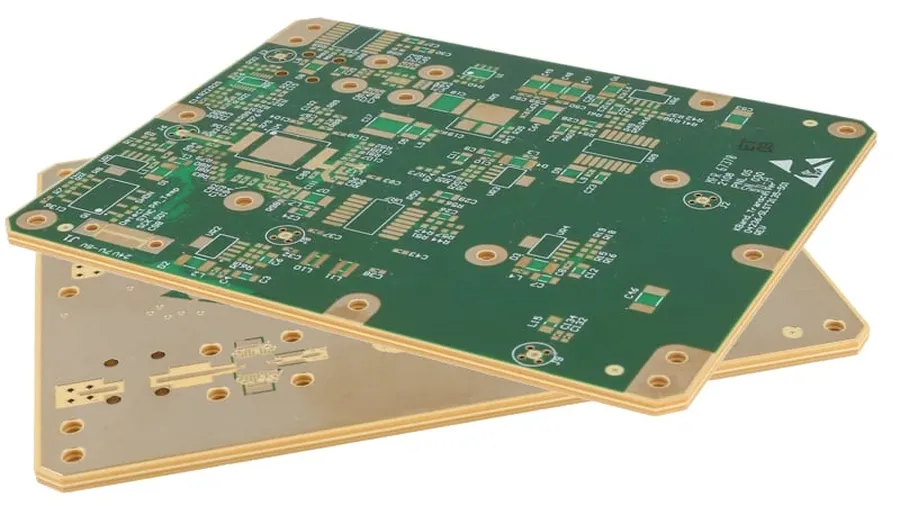
In today's rapidly advancing tech landscape, high-frequency applications demand exceptional materials. Teflon PCBs, known for their superior dielectric properties and thermal stability, are increasingly crucial. Choosing the right Teflon PCB manufacturer is paramount to the success and reliability of your electronic devices. This guide explores essential aspects to help you make an informed decision, ensuring your project benefits from the best in PCB technology. We will demystify the selection process, looking at key criteria and considerations when selecting a teflon pcb manufacturer.
Understanding Teflon PCB Material (PTFE)
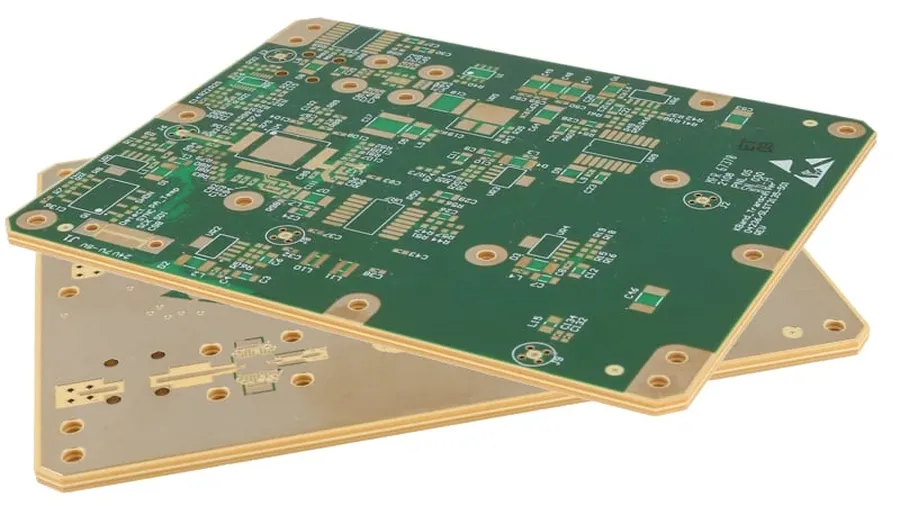
Polytetrafluoroethylene (PTFE), commonly known as Teflon, is a high-performance fluoropolymer renowned for its exceptional electrical, thermal, and chemical properties, making it an ideal substrate for printed circuit boards (PCBs) in demanding high-frequency applications. Its unique molecular structure imparts a low dielectric constant, enabling faster signal propagation and reduced signal loss, along with superior thermal stability, ensuring reliable performance across a broad range of temperatures, and excellent chemical resistance, safeguarding its integrity in harsh environments.
- Low Dielectric Constant
PTFE's low dielectric constant (typically around 2.1) is a critical property for high-frequency PCB applications. This enables faster signal speeds and reduces signal loss, minimizing signal distortion and maintaining signal integrity. This is crucial in high-speed data transfer and RF applications. - Thermal Stability
Teflon exhibits excellent thermal stability, maintaining its properties across a wide temperature range. This is vital for applications where PCBs are exposed to extreme temperatures, ensuring reliable performance and preventing degradation of material properties that can lead to circuit failure. - Chemical Resistance
PTFE's inert nature makes it highly resistant to most chemicals, acids, and solvents. This characteristic is essential for PCBs used in harsh industrial environments, ensuring that the board’s integrity and performance are not compromised by exposure to corrosive substances. - Moisture Resistance
PTFE is hydrophobic and resists moisture absorption. This prevents electrical short circuits and signal degradation caused by moisture ingress, enhancing reliability in humid environments.
Key Considerations When Selecting a Teflon PCB Manufacturer
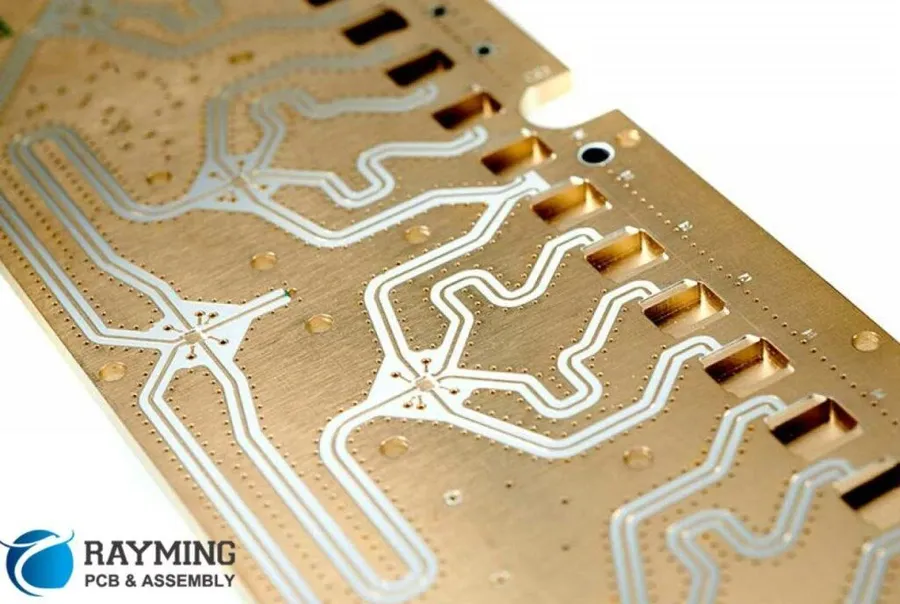
Selecting the right Teflon PCB manufacturer is crucial for ensuring the quality, reliability, and performance of your high-frequency electronic devices. This selection process requires careful evaluation of several key factors to guarantee a successful partnership.
- Experience and Expertise
A manufacturer's track record in producing Teflon PCBs is paramount. Prior experience working with PTFE materials ensures they understand the unique handling requirements and manufacturing processes involved. Look for manufacturers who can demonstrate a history of successful projects in your target application domain, whether it's aerospace, telecommunications or medical. - Certifications and Standards
Verify the manufacturer's adherence to industry standards by looking for certifications like ISO 9001, AS9100 (for aerospace), or IATF 16949 (for automotive). These certifications confirm that the manufacturer has robust quality management systems and processes in place, minimizing risks of errors. - Technological Capabilities
Assess whether the manufacturer possesses the necessary technology and equipment to handle Teflon PCB fabrication. This includes advanced machinery for drilling, etching, plating, and lamination, as well as processes required to work with the unique characteristics of PTFE such as its low coefficient of thermal expansion. Confirm they have the required technology for your desired specifications, including RF and microwave designs. - Quality Control Measures
Robust quality control is essential to ensure the end product meets required specifications. Inquire about the manufacturer's quality checks performed during the production process, as well as the test equipment they use to test for impedance, signal loss, and other critical factors. Look for manufacturers offering comprehensive testing procedures, including electrical tests, micro-section analysis, and peel tests. - Design File CAM Examination
A critical aspect of the manufacturing process is the design file CAM examination. Prior to fabrication, it is essential for the manufacturer to examine your design files thoroughly for any potential manufacturing issues that could impact the final product, this ensures the design is ready for fabrication, and minimizes waste due to errors. - Communication and Support
Effective communication is essential. Choose a manufacturer who provides responsive customer service and engineering support, from design consultation to ongoing technical assistance. Evaluate the responsiveness to inquiries and their ability to provide timely updates on production schedules and delivery times.
Teflon PCB Material Brands: Rogers, Taconic, and More
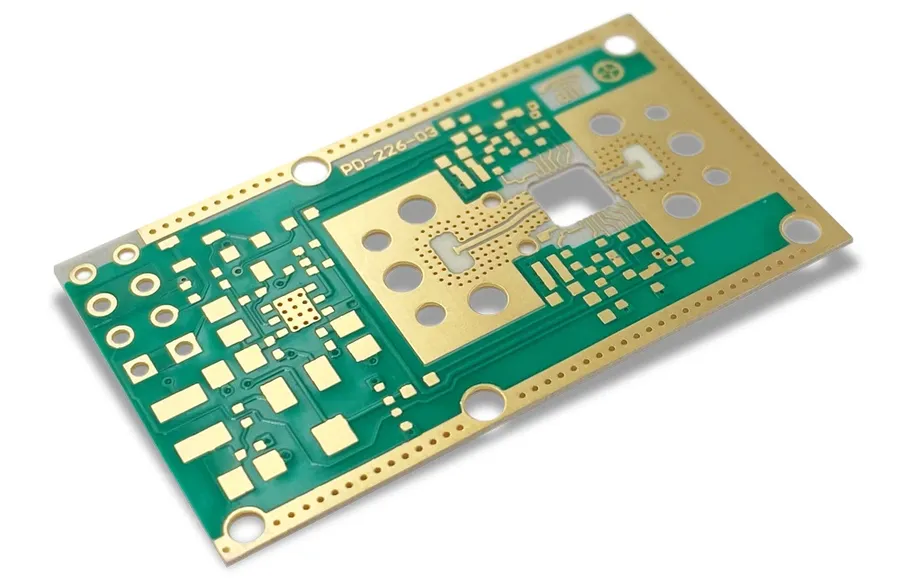
The selection of Teflon PCB materials significantly impacts performance in high-frequency applications. Key brands such as Rogers and Taconic offer specialized PTFE-based laminates, each with unique characteristics that cater to different performance demands. A competent Teflon PCB manufacturer will have expertise in handling these materials, ensuring precise fabrication and optimal performance of the final product.
Material Brand | Key Characteristics | Typical Applications | Manufacturer Considerations |
---|---|---|---|
Rogers Corporation (e.g., RT/duroid series, RO4000 series) | Low dielectric constant, stable electrical performance, excellent thermal characteristics, low loss tangent. | Aerospace and defense, high-speed digital, wireless communications, automotive radar. | Requires precise handling due to material properties, critical for impedance control, expertise in multilayer builds needed. |
Taconic (e.g., TLY series, RF series) | Consistent electrical properties, low moisture absorption, good mechanical stability, excellent chemical resistance. | Microwave antennas, high power RF, medical imaging, test equipment. | Expertise in etching and bonding processes, careful lamination techniques for consistent performance, precise fabrication is essential. |
Other Manufacturers (e.g., Neltec, Isola) | Offer a range of PTFE-based materials with specific performance characteristics. | Varies depending on the material and its properties, typically for high-frequency and specialized applications. | Manufacturer needs detailed understanding of the material's processing requirements, compatibility with different plating and etching methods. |
Understanding material nuances is crucial; Rogers RT/duroid, known for consistent dielectric properties, suits demanding high-speed digital circuits, whereas Taconic's materials are often chosen for their moisture resistance and mechanical stability in RF and microwave designs. A manufacturer should provide material datasheets for customer validation. The chosen material will directly influence a product's performance.
Capabilities of a Teflon PCB Manufacturer
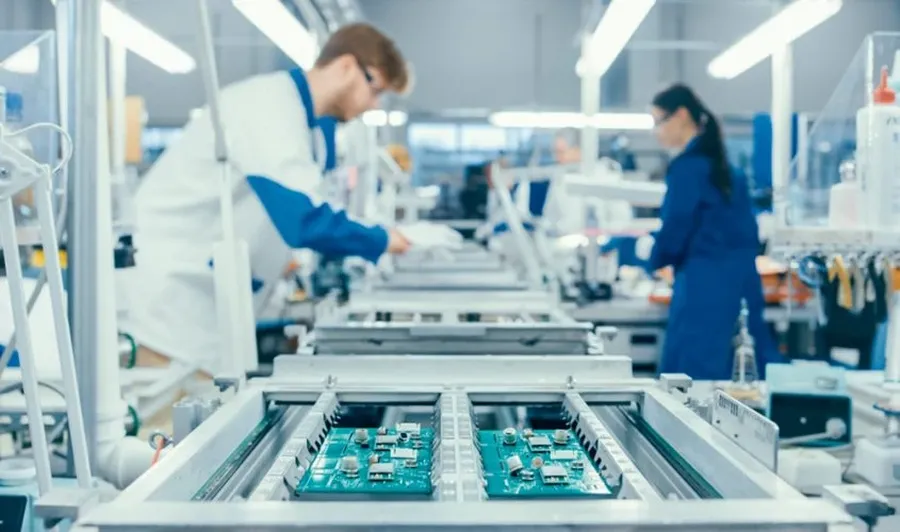
Selecting a Teflon PCB manufacturer requires careful consideration of their manufacturing capabilities to ensure they can meet the specific demands of your project. These capabilities extend beyond standard PCB production and often involve specialized techniques necessary for processing PTFE (Teflon) materials.
- Quick-Turn Prototyping
The capability to produce prototypes rapidly is critical for verifying designs and making necessary adjustments before committing to full-scale production. A manufacturer with quick-turn capabilities can significantly reduce development time and costs. - Mass Production
A reliable manufacturer should possess the capacity for mass production to handle large orders without sacrificing quality or turnaround time. This involves scalable equipment and efficient manufacturing processes. - Specialized Processing for RF and Microwave Applications
Manufacturing Teflon PCBs for high-frequency applications like RF and microwave circuits demands specific expertise and equipment. This includes precise impedance control, tight tolerance fabrication, and the ability to handle the unique characteristics of PTFE materials during processing, such as specialized etching and plating processes to maintain the low loss properties. - Material Handling Expertise
Teflon (PTFE) is a unique material to work with that requires a mastery of handling, and processing techniques. This includes temperature and chemical handling, and ensuring accurate cutting and drilling due to its inherent properties. - Layer Count Capabilities
The ability to produce multi-layered PCBs with Teflon substrates is crucial for complex designs. Manufacturers should be able to handle various layer counts while maintaining precision and signal integrity, including the use of specialized bonding techniques to ensure the integrity of the layers. - Advanced Drilling and Milling
Precision in drilling and milling are required for Teflon PCBs due to the materials low hardness and high expansion coefficient. This is critical for signal integrity and connectivity and requires specialized equipment and techniques
Teflon PCB Applications
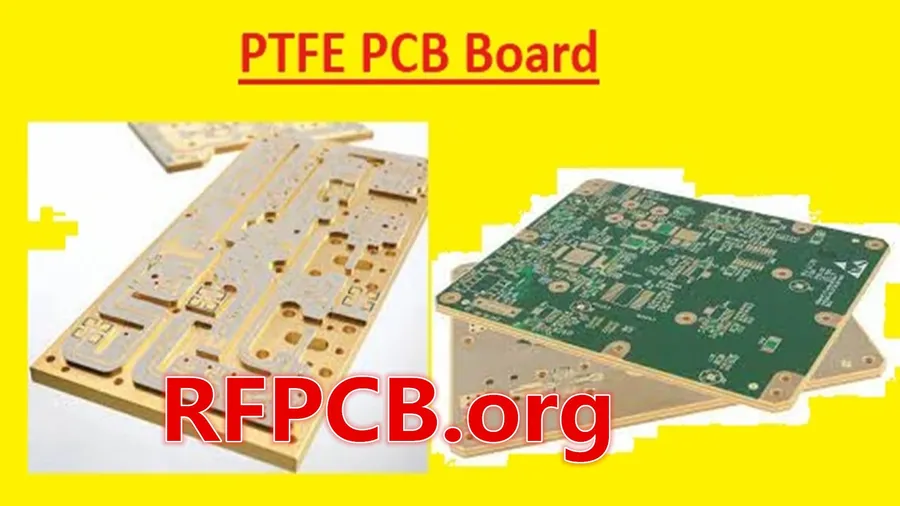
Teflon PCBs, leveraging the exceptional properties of polytetrafluoroethylene (PTFE), find critical applications across diverse high-performance sectors. Their low dielectric constant, minimal signal loss, and superior thermal stability make them indispensable in demanding environments where signal integrity and reliability are paramount.
- Aerospace
In aerospace, Teflon PCBs are used in radar systems, communication devices, and satellite electronics. Their ability to withstand extreme temperatures and radiation, along with their low signal loss, ensures reliable performance in harsh operational conditions. - Telecommunications
Teflon PCBs are widely used in high-frequency telecommunications equipment such as antennas, RF amplifiers, and microwave circuits. Their low dielectric loss and consistent electrical performance at high frequencies are essential for maintaining signal integrity and maximizing network efficiency. - Medical Devices
In medical applications, Teflon PCBs are employed in diagnostic imaging equipment (such as MRI and ultrasound), patient monitoring systems, and implantable devices. Their biocompatibility, chemical resistance, and stable electrical performance ensure reliable and safe operation in sensitive medical environments. - Radar Systems
Teflon PCBs are crucial in radar systems for both military and civilian use. The low signal attenuation and stable dielectric properties of PTFE allow for precise detection and ranging, making them ideal for advanced radar applications like weather monitoring, air traffic control, and defense systems. - High-Speed Computing
As data transmission speeds increase, high-performance computing applications are beginning to leverage the high-speed signal transfer capabilities of Teflon PCBs. This trend is likely to accelerate as these industries continue to push the boundaries of performance and reliability in data processing and storage.
Cost Factors and Budget Considerations for Teflon PCBs
The cost of Teflon PCBs is influenced by a confluence of factors, including raw material expenses, manufacturing intricacies, and the scale of production. Understanding these cost drivers is crucial for effective budget planning and achieving cost-efficient outcomes in your PCB projects.
Here's a breakdown of the major cost factors:
- Material Costs:
Teflon (PTFE) and related high-performance materials have a higher price point compared to standard FR-4 substrates. The specific type of Teflon material (e.g., filled vs. unfilled, specific brand) significantly affects cost. - Manufacturing Complexity:
The complexity of the PCB design, including layer count, trace width, and via size, directly impacts manufacturing time and cost. High-precision requirements for high-frequency applications further increase costs. - Production Volume:
Larger production runs generally result in lower per-unit costs due to economies of scale. Small or prototype runs incur higher costs. The manufacturer setup costs for specialized materials and processing also contribute to this. - Specialized Processing:
Teflon PCBs often require specialized equipment and processes, particularly for RF and microwave applications. These may include specialized etching, impedance control, or controlled dielectric constant management. Such processes drive up costs but are necessary for high reliability. - Design Specifications:
Tight tolerances, specific surface finishes (e.g., ENIG), and special requirements will further contribute to the final cost. Consider the impact of these specifications during your design phase. - Testing and Quality Assurance:
Rigorous testing and quality assurance protocols, which are particularly important for high-reliability applications, can add to overall cost.
Budgeting Strategies:
- Detailed Design Review:
A thorough review of your design to identify any costly or unnecessary complexity will help optimize the project for manufacturing efficiency and cost savings. For example, can you widen traces or reduce via count? - Early Engagement with Manufacturer:
Consult with potential manufacturers early in the design phase. They can provide valuable insights regarding material availability, manufacturability, and cost implications of different design choices. The manufacturer can also help you understand the tradeoffs between material performance and cost. - Accurate Specification and Quote Request:
Provide accurate and complete technical specifications to obtain the most realistic quote. Vague requirements can lead to cost overruns. Be clear about testing, IPC class requirements, and delivery expectations. - Evaluate Multiple Quotes:
Obtain quotes from several reputable manufacturers to ensure you are getting competitive pricing, balancing cost with quality and service capabilities. - Prototype Before Production:
Invest in a small prototype run to validate your design and avoid expensive revisions during mass production.
Frequently Asked Questions About Teflon PCBs
This section addresses common questions regarding Teflon PCBs, clarifying key differences, applications, and manufacturing considerations. Understanding these nuances is crucial for making informed decisions when selecting a Teflon PCB manufacturer and utilizing these specialized boards effectively.
- What is the difference between PTFE and Teflon?
PTFE (Polytetrafluoroethylene) is the chemical name for the polymer, while Teflon is a brand name owned by Chemours (formerly DuPont). Essentially, they are the same material; Teflon is simply the more commonly recognized trade name for PTFE. - Are PCBs made of Teflon?
While not all PCBs are made of Teflon (PTFE), it is a specialized material used in high-performance applications. The base material of most PCBs is FR-4 (a composite material made of woven fiberglass cloth with epoxy resin), while Teflon PCBs utilize PTFE as their dielectric substrate. PCBs made of Teflon are often used when high speed, high frequency and temperature are required. - Are Teflon PCBs different from FR-4 PCBs?
Yes, Teflon PCBs and FR-4 PCBs differ significantly. Teflon PCBs offer superior electrical performance at high frequencies, with a lower dielectric constant and loss tangent, as well as better thermal stability and chemical resistance. FR-4 is more cost-effective and suitable for general-purpose applications, while Teflon is used in niche areas that require specialized electrical properties. - What should be considered for PCB assembly using Teflon materials?
When assembling Teflon PCBs, consider their lower mechanical strength compared to FR-4 and their susceptibility to surface contamination. This is important, as the bond strength between the copper traces and the substrate is much lower than with FR-4 and can be damaged during assembly. Use proper tooling and low temperatures to prevent damage. Cleanliness of the surface is also paramount for reliable soldering, and specialized techniques and materials may be necessary. - Which company manufactures Teflon (PTFE) material?
The primary manufacturer of Teflon (PTFE) material is Chemours. However, many companies use PTFE in their specialized materials for PCB substrates. For example, Rogers Corporation, Taconic and Ventec are well known for their high-frequency PCB materials utilizing PTFE in their formulations. - What are the advantages of using Teflon PCBs?
Teflon PCBs have several key advantages, including: very low dielectric constant and dissipation factor, which are essential for high-frequency signals, excellent thermal stability, which prevents thermal deformation of the board during operation, and good chemical resistance, which allows the PCBs to work in harsh environments. Teflon PCB also exhibits very low moisture absorption and high insulation resistance, which is especially needed for high voltage operation. - Are there any disadvantages to using Teflon PCBs?
Yes, there are some disadvantages, including a higher cost compared to FR-4 PCBs, greater difficulty in manufacturing and assembly, lower mechanical strength, and sensitivity to surface contamination. These factors must be considered when deciding whether to use a Teflon PCB.
Comparing Teflon PCB Manufacturers: A Practical Guide
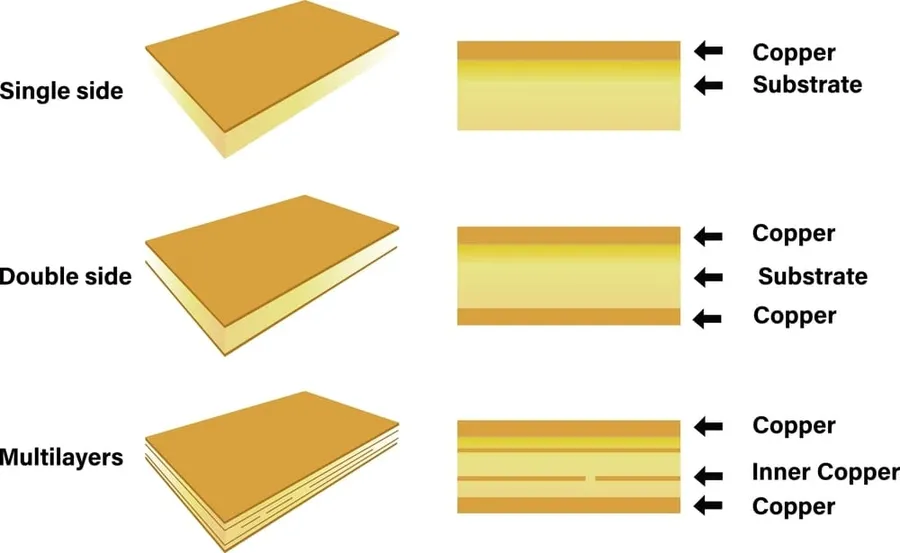
Selecting the right Teflon PCB manufacturer is crucial for project success, demanding a thorough comparison across several key metrics. This section provides a practical guide to navigate the selection process, emphasizing a structured approach for identifying a manufacturer that aligns with your specific project requirements.
Evaluation Criteria | Manufacturer A | Manufacturer B | Manufacturer C |
---|---|---|---|
Experience in Teflon PCBs | 10+ years, specialized in RF applications | 5 years, general PCB manufacturing | 15+ years, broad experience including aerospace |
Certifications (ISO 9001, AS9100) | ISO 9001, AS9100 | ISO 9001 | ISO 9001, AS9100, Nadcap |
Material Expertise | Rogers, Taconic | Rogers only | Rogers, Taconic, other high-performance brands |
Turnaround Time (for Prototypes) | 5-7 days | 10-14 days | 3-5 days |
Manufacturing Capabilities | Quick-turn, mass production, RF processing | Standard mass production | Quick-turn, mass production, specialized RF/MW processing |
Quality Control | Rigorous CAM analysis, electrical testing | Standard QC checks | Advanced CAM analysis, automated optical inspection, electrical testing |
Price (per board, rough estimate) | $$$ | $$ | $$$$ |
Design Support | In-house design review and DFM | Limited design support | Extensive design support, RF optimization |
This table facilitates a side-by-side comparison, focusing on key factors such as experience, certifications, material expertise, turnaround time, manufacturing capabilities, quality control measures, pricing, and design support. The selection of a suitable Teflon PCB manufacturer should prioritize those factors which are most relevant to the intended application and budget constraints of the project. The table above is a simplified example, and actual evaluation should include specific details relevant to the project.
Future Trends and Innovations in Teflon PCB Manufacturing
The future of Teflon PCB manufacturing is poised for significant advancements, driven by the relentless pursuit of higher performance, miniaturization, and cost-effectiveness. Innovations are emerging across materials science, manufacturing processes, and application-specific designs, with a focus on meeting the increasingly demanding requirements of high-frequency electronics.
- Advanced Material Development
Research into new formulations of PTFE composites is ongoing, aimed at enhancing dielectric properties, thermal conductivity, and mechanical strength. This includes exploring fillers and additives to fine-tune material characteristics for specific applications, enabling the production of PCBs with improved electrical performance and robustness. - Miniaturization and High-Density Interconnect (HDI)
Future trends point towards finer line widths and spacing, enabling higher component density on Teflon PCBs. This involves adopting advanced manufacturing techniques like laser direct imaging (LDI), micro-via drilling, and improved plating processes to achieve precise and reliable interconnections in compact designs. - Integration of Smart Manufacturing Techniques
The incorporation of Industry 4.0 principles such as automation, data analytics, and machine learning is expected to optimize manufacturing processes. This should lead to improved production efficiency, reduced waste, and enhanced quality control, enabling more cost-effective and reliable production of Teflon PCBs. - Emergence of Additive Manufacturing
The potential of additive manufacturing (3D printing) for producing custom Teflon PCBs is being explored. This technology could allow for rapid prototyping and complex, customized designs not achievable through traditional methods. However, challenges remain in material handling and achieving consistent dielectric properties. - Enhanced Thermal Management Solutions
As electronic devices operate at higher frequencies and power levels, effective thermal management becomes crucial. Innovations in incorporating thermally conductive materials into Teflon PCB structures, as well as advanced heat dissipation techniques like integrated heat sinks and microfluidic cooling channels, will be essential for future high-performance applications. - Sustainability and Eco-Friendly Practices
Environmental concerns are pushing the industry towards more sustainable manufacturing processes and materials. This involves using eco-friendlier materials, optimizing resource utilization, and adopting recycling programs to minimize waste and the overall environmental impact of Teflon PCB production.
Selecting the right Teflon PCB manufacturer is essential for achieving optimal performance in high-frequency applications. By understanding the unique properties of Teflon, evaluating manufacturer capabilities, and considering cost factors, you can make informed decisions that ensure the success of your project. Partnering with an experienced teflon pcb manufacturer will be a key factor in high performance and long term reliability. Always explore future trends and technologies to stay ahead of the curve in this evolving field.
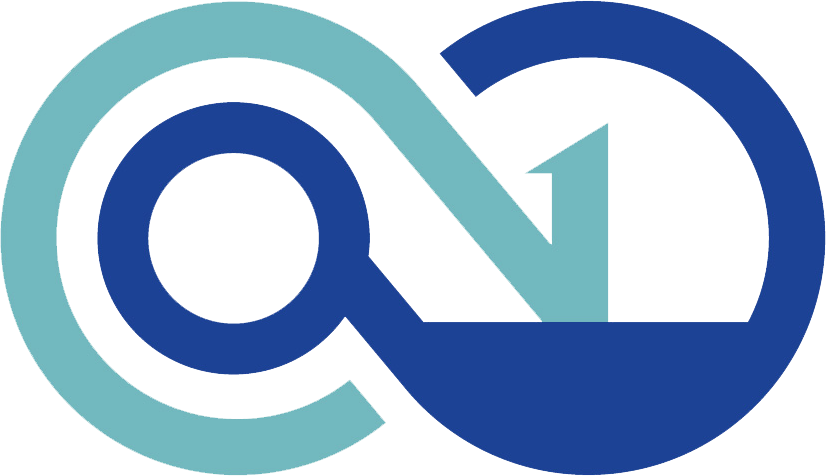