Decoding Flex PCB Price: Factors, Costs, and Smart Buying
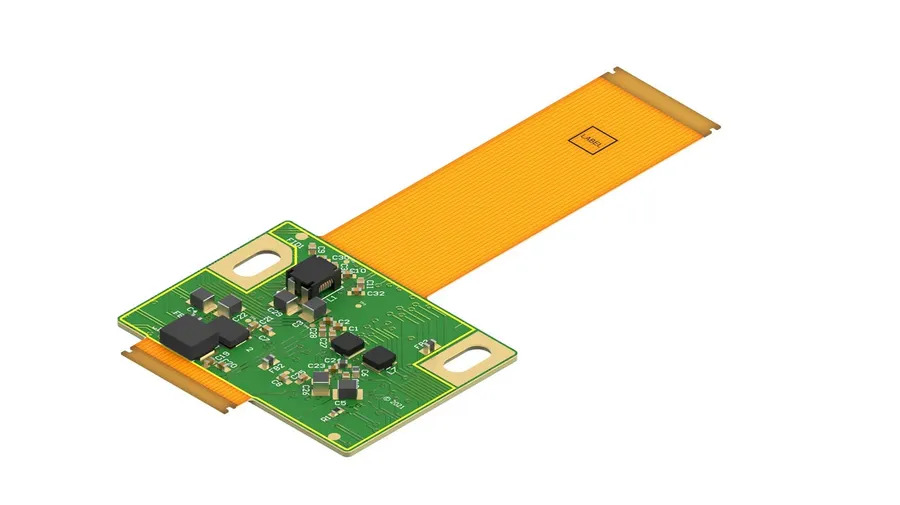
In today's rapidly evolving electronics landscape, Flexible PCBs (Flex PCBs) are becoming essential, offering unparalleled adaptability and design freedom. But what about the 'flex pcb price'? This is a critical factor for any project, and the cost can vary significantly. This article breaks down the intricate world of flex PCB pricing, exploring the factors that influence cost, and providing practical guidance to make informed decisions. Understanding these elements will empower you to optimize your projects while keeping your budget in check. From everyday wearable devices to advanced robotics, flex PCBs are everywhere, and navigating their price point is the key to success.
Key Factors Affecting Flex PCB Price
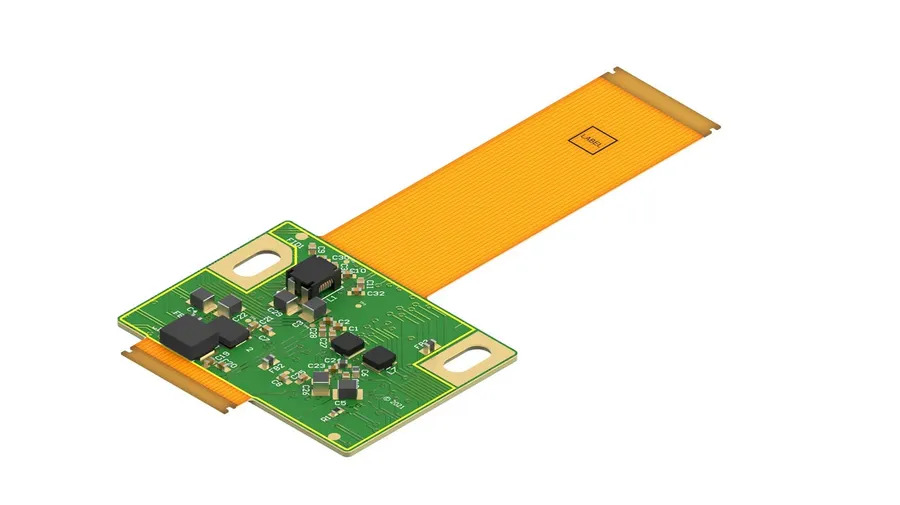
The price of flexible printed circuit boards (PCBs) is not monolithic; it's a composite of several interconnected factors. Understanding these key determinants—material selection, board dimensions, layer complexity, and production scale—is crucial for cost-effective procurement. Variations in these aspects lead to significant price fluctuations, highlighting the need for informed decision-making in the design and manufacturing process of flex PCBs.
Factor | Description | Impact on Price |
---|---|---|
Material Type | Selection of substrate (e.g., polyimide, PET) and copper type. | Higher performing materials generally increase costs. |
Board Size | Physical dimensions of the PCB. | Larger board sizes directly correlate with higher material usage and processing costs. |
Layer Count | Number of conductive layers within the PCB. | Increased layers lead to more complex manufacturing processes and higher costs. |
Production Volume | Quantity of boards in a single production run. | Larger production volumes typically result in lower per-unit costs. |
Tolerances | Permissible variations in PCB dimensions and characteristics. | Tighter tolerances require more precise manufacturing and increase cost. |
Surface Finishing | The type of plating or coating on the PCB. | Specialized finishes or materials add to overall cost. |
Material Types and Their Cost Implications
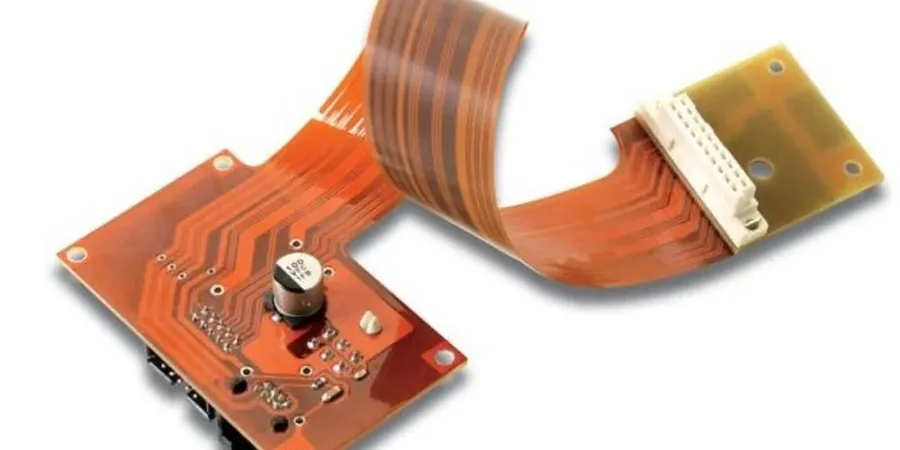
The selection of materials in flexible printed circuit boards (PCBs) significantly impacts the final flex PCB price. Different substrates and copper types exhibit varying costs, directly influencing the overall manufacturing expenses. Understanding these material cost implications is crucial for effective budgeting and design choices.
Material Type | Description | Cost Implication | Common Uses |
---|---|---|---|
Polyimide (PI) | High-performance polymer with excellent thermal and chemical resistance. | Higher cost due to superior properties and manufacturing complexity. | Aerospace, medical devices, high-reliability applications. |
Polyester (PET) | Cost-effective polymer with good flexibility but lower temperature resistance. | Lower cost compared to polyimide, suitable for less demanding applications. | Consumer electronics, disposable devices, low-cost applications. |
Liquid Crystal Polymer (LCP) | Exceptional electrical and mechanical properties, excellent dimensional stability and can be used in high-frequency applications. | Highest cost of the typical substrates, best performance. | High-frequency signal transmission, high-precision applications. |
Rolled Annealed (RA) Copper | Copper that has undergone annealing process with superior flexibility, especially good for dynamic flexing applications. | Higher cost than electrodeposited copper due to specialized manufacturing. | Dynamic flex applications, high reliability interconnects. |
Electrodeposited (ED) Copper | Copper deposited using electrolysis, common type for PCB manufacturing. | Lower cost than rolled annealed copper and good for static or low flex applications. | General-purpose flex circuits, static applications. |
The choice between rolled annealed copper and electrodeposited copper is particularly critical. Rolled annealed copper, while more expensive, offers superior flexibility and is essential for dynamic flexing applications. Electrodeposited copper, being more cost-effective, is suitable for static or low-flex applications. Substrate selection often depends on performance requirements. Polyimide is best for high-temperature and high-reliability scenarios, while PET provides a more cost-effective option for less demanding applications. LCP is the best performance, but most expensive material for high-frequency applications.
Layer Count and Complexity
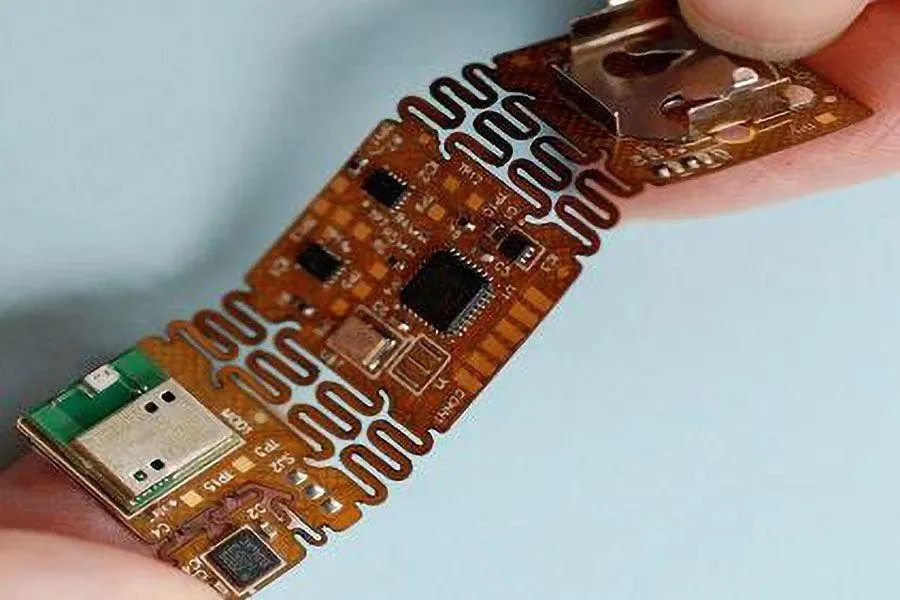
The number of layers in a flexible PCB significantly impacts its cost due to the increased complexity of manufacturing. Each additional layer necessitates more intricate processing steps, driving up both material usage and production time, thus escalating the overall price of the flex PCB.
Layer Count | Complexity | Cost Impact | Application Examples |
---|---|---|---|
Single-Layer | Simplest | Lowest | Basic circuits, simple connections |
Double-Layer | Moderate | Moderate | Common for various applications, increased circuit density |
Multi-Layer (3+ Layers) | High | Highest | Complex electronics, high-density interconnect, signal integrity needs |
As the layer count increases, so does the number of manufacturing processes required, which can include lamination, drilling, and plating, leading to a directly proportional increase in the final flex PCB price. The precision required for alignment and layer bonding in multi-layer PCBs is another factor contributing to the price difference compared to simpler single or double-layer boards.
Manufacturing and Design Considerations Impact on Flex PCB Price
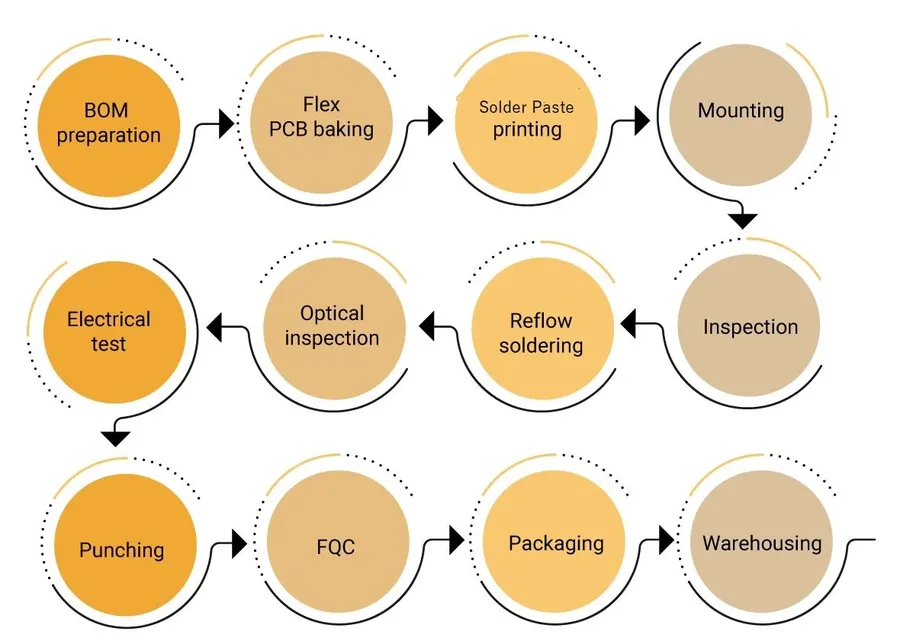
The manufacturing and design of flexible PCBs significantly influence their final cost. Factors such as design complexity, specific features, and required production techniques all contribute to variations in price. Understanding these elements is crucial for cost-effective flex PCB procurement.
Design/Manufacturing Factor | Cost Impact | Explanation |
---|---|---|
Design Complexity | High | Intricate layouts with fine lines and small vias necessitate advanced manufacturing processes, increasing costs. |
Impedance Control | Medium to High | Precise control of impedance requires tight tolerances and special materials, adding to the expense. |
Plated Holes and Castellated Holes | Medium | These features involve additional processing steps, such as drilling and plating, which increase manufacturing time and costs. |
Surface Finish | Low to Medium | The type of surface finish (e.g., ENIG, HASL) affects cost due to material and process variations; more sophisticated finishes are more expensive. |
Solder Mask Requirements | Low to Medium | Specific solder mask requirements (color, thickness, and precision) can affect the complexity and cost of the manufacturing process. |
Production Techniques | Medium to High | Advanced techniques like laser direct imaging (LDI) and micro-via drilling impact costs due to specialized equipment and expertise. |
Production Volume and Its Effect on Price
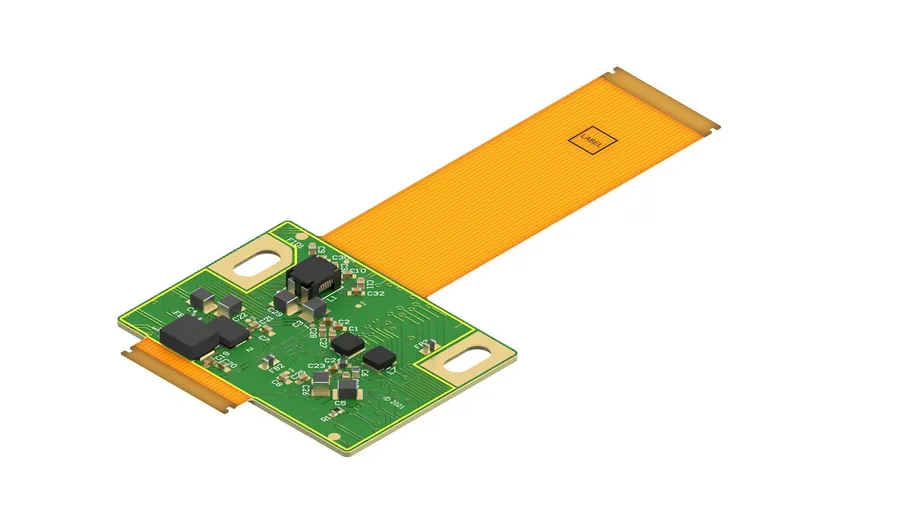
The quantity of flex PCBs ordered significantly impacts the per-unit price due to economies of scale. Larger production runs spread fixed costs over more units, resulting in lower individual costs, whereas smaller orders, especially prototypes, bear a higher per-unit price due to setup costs and lower material usage efficiencies. Understanding this relationship is crucial for cost-effective procurement of flexible printed circuits.
Order Volume | Cost Factor | Impact on Price | Typical Application |
---|---|---|---|
Prototypes (1-10 Units) | High setup costs, material waste | Highest per-unit price | Initial design verification, proof of concept |
Small Runs (10-100 Units) | Moderate setup costs, some material waste | Relatively high per-unit price | Pilot production, early market testing |
Medium Runs (100-1000 Units) | Lowered setup costs, reduced material waste | Moderate per-unit price | Small to mid-size production runs, niche markets |
Large Runs (1000+ Units) | Minimal setup costs, efficient material use | Lowest per-unit price | High-volume consumer electronics, mass production |
Estimating Flex PCB Costs: A Practical Guide
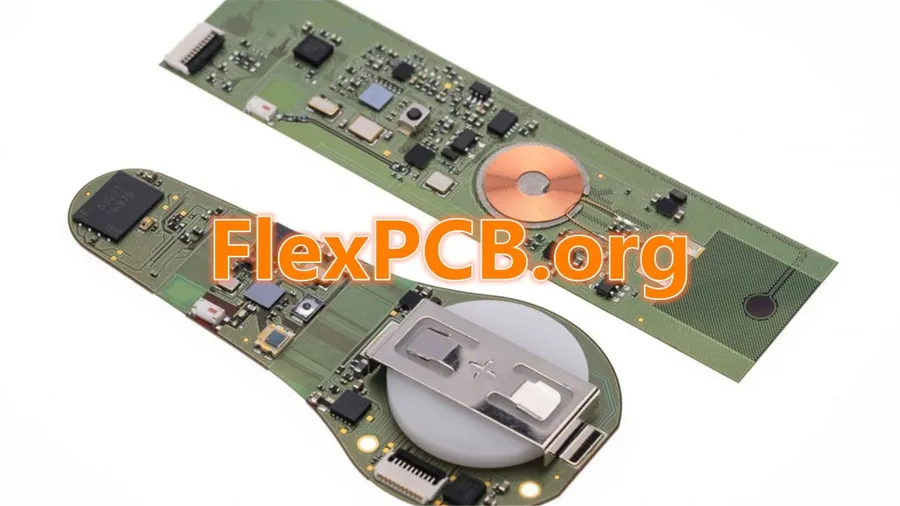
Accurately estimating the cost of flexible PCBs is crucial for effective project planning and budget management. This section provides practical methods for deriving these estimates, ranging from simple rules of thumb to detailed request for quotation (RFQ) procedures. Employing these techniques helps in securing cost-effective solutions and avoiding unexpected financial challenges.
- Rule of Thumb Method
A basic approach involves utilizing cost per area or cost per layer estimates based on industry benchmarks. While simplistic, this method provides a preliminary cost approximation. It often uses metrics like price per square inch or price per layer, providing a ballpark figure that can be quickly calculated. However, it should be noted that this method does not take specific design intricacies into account. - Online Calculators
Many PCB manufacturers offer online cost calculators, which allow for more detailed estimation by inputting specific parameters such as material type, layer count, board dimensions, and desired quantities. These tools provide a more accurate preliminary estimate compared to rules of thumb. They are highly effective for initial pricing and comparison but are limited by the calculator's specific functionality. - Request for Quotation (RFQ)
For precise cost estimations, submitting a detailed RFQ to multiple manufacturers is essential. An RFQ should include all specifications, such as Gerber files, material requirements, layer stack-up details, and specific manufacturing tolerances and finishes. This method provides the most accurate pricing as it takes the intricacies of each project into account.
Method | Accuracy | Effort | Use Case |
---|---|---|---|
Rule of Thumb | Low | Low | Initial Quick Estimation |
Online Calculators | Medium | Medium | Preliminary Detailed Estimation |
Request for Quotation (RFQ) | High | High | Precise Cost Determination |
Flex PCB Pricing: Prototypes vs. Mass Production
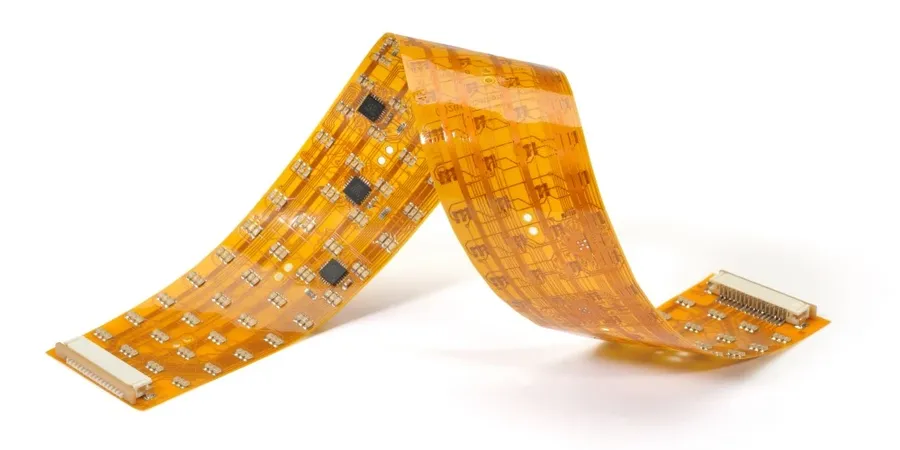
The cost of flexible PCBs varies significantly depending on whether they are produced as prototypes or in mass quantities. Prototype runs, characterized by smaller quantities, often involve higher per-unit costs due to setup expenses and less efficient manufacturing processes. Conversely, mass production leverages economies of scale to reduce the per-unit price. Understanding this dynamic is crucial for budget planning and project management.
Characteristic | Prototypes | Mass Production |
---|---|---|
Quantity | Small (e.g., 1-100) | Large (e.g., 1000+) |
Per-Unit Cost | High | Low |
Setup Costs | High per unit | Lower per unit |
Lead Time | Potentially shorter | May be longer but more predictable |
Process Optimization | Limited | High |
Strategies to reduce costs in both prototype and mass production phases include optimizing the design for manufacturability (DFM), using standard materials, and careful selection of the manufacturing partner. For prototypes, minimizing the complexity, avoiding tight tolerances can keep the price low. In mass production, the focus shifts to negotiating favorable rates based on volume, streamlining processes and minimizing waste. Typical pricing can vary significantly based on complexity. For simple single layer flex circuits, mass production may result in prices of under a dollar each at high volume, while prototypes may be ten times more expensive or more per piece. More complex multilayer designs will be significantly more expensive.
Frequently Asked Questions about Flex PCB Pricing
Understanding the cost of flex PCBs can be complex. This section addresses frequently asked questions to clarify pricing factors and help you make informed decisions.
- How much does a flex PCB typically cost?
The cost of a flex PCB varies significantly based on factors like material, layer count, size, complexity, and order volume. Prototypes can range from a few hundred to over a thousand dollars, while mass production can bring the per-unit cost down to a few dollars. It's crucial to obtain specific quotes from manufacturers to determine the actual cost for your project. - What factors cause significant variance in flex PCB prices?
Several factors contribute to the variability in flex PCB prices, including the type of substrate used (polyimide typically costs more than PET), the number of layers required (more layers increase complexity and cost), the board size and design complexity, the required tolerances and surface finishes, and the overall production volume. Specific design features like impedance control and plated holes will also impact cost. - Are flex PCBs generally more expensive than rigid PCBs?
Yes, flex PCBs tend to be more expensive than rigid PCBs due to their complex manufacturing processes and specialized materials. The inherent flexibility and the challenges in handling these materials during production contribute to the higher cost. However, their unique advantages often justify the higher price for applications requiring flexibility and compactness. - How can I minimize the cost of my flex PCB?
Cost minimization can be achieved by optimizing your design for manufacturability, using standard materials and specifications, reducing the number of layers, considering panelization for higher production volumes, and accurately forecasting the order volume to take advantage of bulk discounts. Consulting with your manufacturer early in the design process can also help identify potential cost-saving measures. - What is the impact of prototype runs on the overall cost?
Prototype runs are typically more expensive on a per-unit basis than mass production because they involve setup costs and smaller batch sizes. The initial tooling, setup, and programming have a high fixed cost that is spread across fewer units. However, prototyping is crucial for identifying and correcting design flaws before committing to mass production, potentially saving significant costs and time in the long run. A well-tested prototype can reduce unexpected cost overruns in large production runs. - Does the choice of surface finish affect the flex PCB price?
Yes, the choice of surface finish can impact the flex PCB price. Options like ENIG (Electroless Nickel Immersion Gold) provide excellent solderability and corrosion resistance but can be more expensive. HASL (Hot Air Solder Leveling) is a more cost-effective alternative but has some limitations in terms of flatness. Choosing the appropriate surface finish based on your application requirements can help balance performance and cost. - What are the key questions to ask a PCB manufacturer when requesting a quote?
When requesting a quote, inquire about the material options and their cost implications, lead times, the manufacturer's experience with flexible PCBs, any setup or tooling costs, and their production capabilities for your desired quantity and design requirements. Request a detailed breakdown of costs to understand how each factor contributes to the overall price and assess if that specific manufacturer is the right fit for your budget.
Where to Find the Best Flex PCB Prices
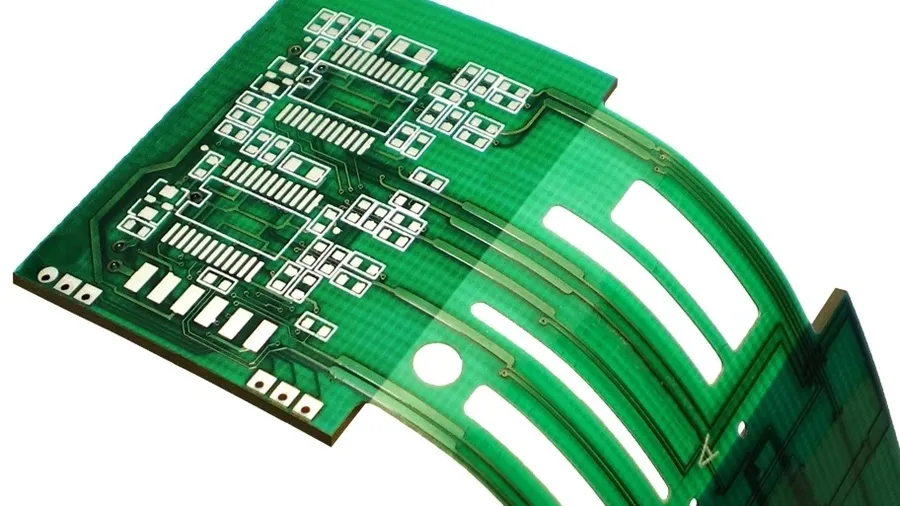
Securing the best flex PCB prices requires a strategic approach to selecting a suitable manufacturer. It's crucial to balance cost-effectiveness with the assurance of high-quality production. This section outlines key considerations when evaluating suppliers, ensuring you find a partner that aligns with both your budgetary and quality needs.
- Assess Manufacturer Specialization
Prioritize manufacturers with proven experience in flexible PCB fabrication. Specialized expertise often translates to better process control, higher yields, and potentially lower costs due to optimized workflows. - Evaluate Manufacturing Capabilities
Confirm that the manufacturer can handle your specific requirements for material types, layer counts, board dimensions, and tolerances. Verify their equipment capabilities and process controls to meet your technical specifications. - Request and Compare Quotes
Obtain quotes from multiple suppliers, clearly specifying your design requirements and production volumes. Analyze the cost breakdowns to understand the underlying factors contributing to the final price. Avoid choosing solely based on the lowest price, as this can often lead to trade-offs in quality. - Prioritize Quality and Certification
Ensure that the manufacturer adheres to industry quality standards, such as ISO 9001. Certifications indicate a commitment to quality and a well-defined quality management system. Request samples and conduct thorough quality checks. - Review Turnaround Times
Inquire about turnaround times, particularly for prototypes and pilot runs. Time to market is critical, and delays can be costly. Ensure that the manufacturer's lead times align with your project timelines. - Consider Communication and Support
Effective communication is essential throughout the manufacturing process. Choose a manufacturer that is responsive, transparent, and proactive in addressing any issues that may arise. Strong customer support can significantly minimize risks and improve efficiency. - Explore Value-Added Services
Investigate additional services such as design assistance, assembly, and testing. These can streamline the process and reduce overall costs. A full-service provider can be more advantageous by managing all aspects of production.
Understanding the factors that affect the flex pcb price is crucial for successful project management. By considering the materials used, design complexity, production volume, and manufacturing techniques, you can better control your costs while ensuring your project's performance. As flex PCB technology advances and becomes more accessible, staying informed about these pricing factors and optimizing your designs can offer a competitive edge in the market. Whether you need a simple prototype or large-scale production, knowing how flex pcb price works allows for informed decision-making, ensuring high-quality and cost-effective outcomes. Considering the rapid advancement in this technology, we can expect further optimization of flex PCB costs in the future.
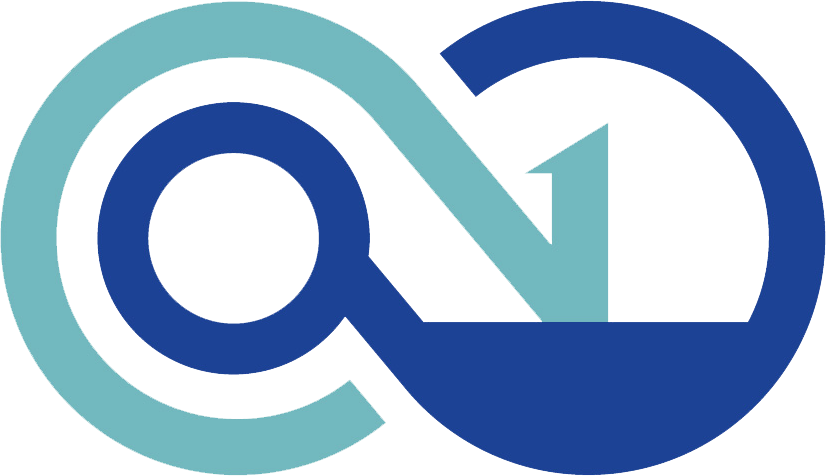