Decoding PCB Manufacturing Equipment Costs: A Comprehensive Guide
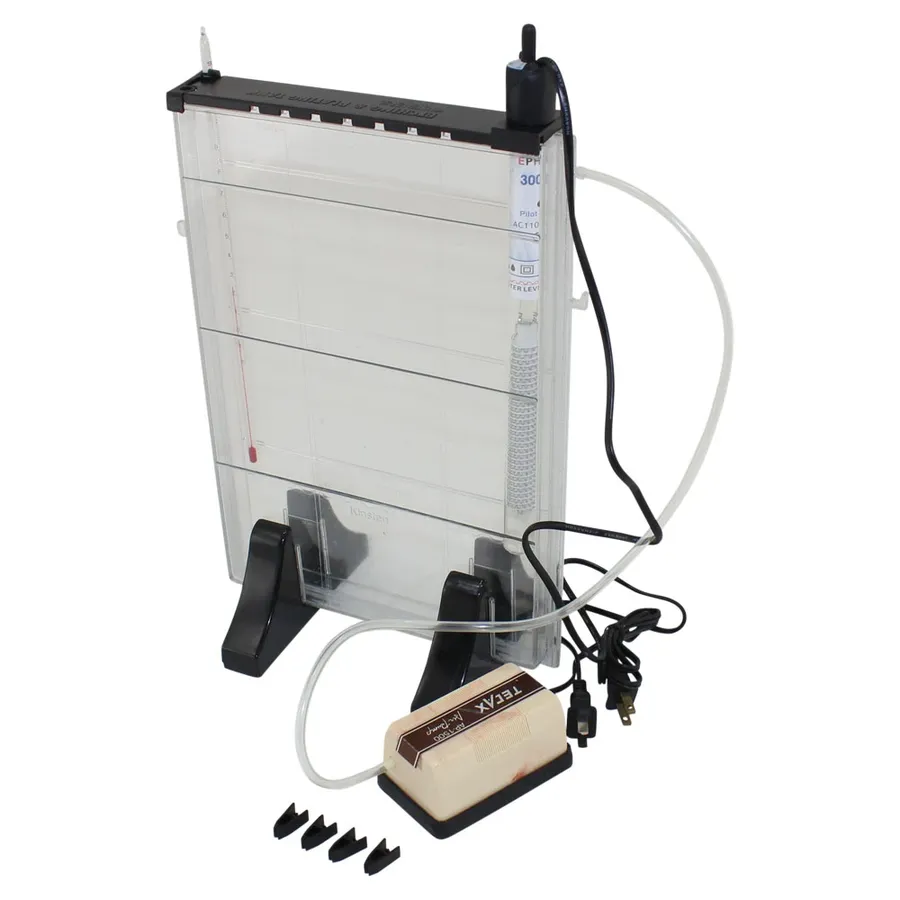
From smartphones to spacecraft, printed circuit boards (PCBs) are the backbone of modern electronics. But what does it actually cost to set up the production line? Understanding PCB manufacturing equipment costs is essential for businesses of all sizes, from startups to established manufacturers. This guide will unravel the complex factors influencing these costs, offering insights into everything from basic etching machines to sophisticated surface mount technology (SMT) lines, and how these expenses directly relate to the final product cost and market pricing. This article will guide you through the jungle of the PCB manufacturing equipment, and help you find the best solutions for your project's budget.
Basic PCB Manufacturing Equipment: Essential Tools and Their Costs
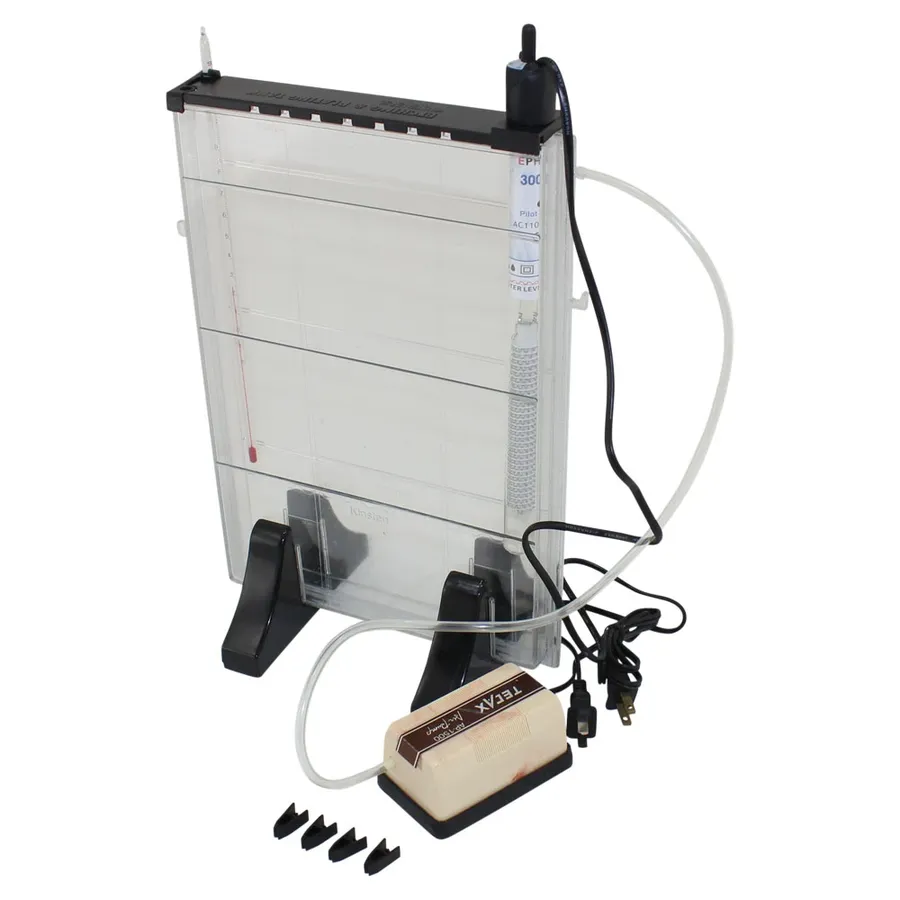
The foundation of any PCB manufacturing process lies in a set of essential tools. These fundamental pieces of equipment, including etching machines, drilling machines, and manual solder stations, dictate the capabilities and cost-effectiveness of basic PCB production. Understanding the price ranges associated with these tools is crucial for budgeting and planning.
Equipment | Description | Typical Price Range |
---|---|---|
Etching Machine | Removes unwanted copper from the PCB | $500 - $5,000 |
Drilling Machine | Creates holes for components and vias | $1,000 - $10,000 |
Manual Solder Station | Used for soldering components | $100 - $500 |
Laminator | Used to apply dry film or photoresist to a PCB panel | $200 - $3000 |
Exposure Unit | Used to expose photoresist for PCB manufacturing. | $500 - $3000 |
It is important to note that the price range of each piece of equipment can vary widely, depending on the capacity, features, and precision of the machine. For example, a basic etching tank might be at the lower end of the spectrum, while a more advanced automated etching system with precise chemical controls may fall at the upper end. Similarly, manual solder stations, while the least expensive, offer a much lower throughput compared to automated soldering systems that are much more costly and used in advanced PCB fabrication.
SMT Equipment Costs: Understanding the Price of Automation
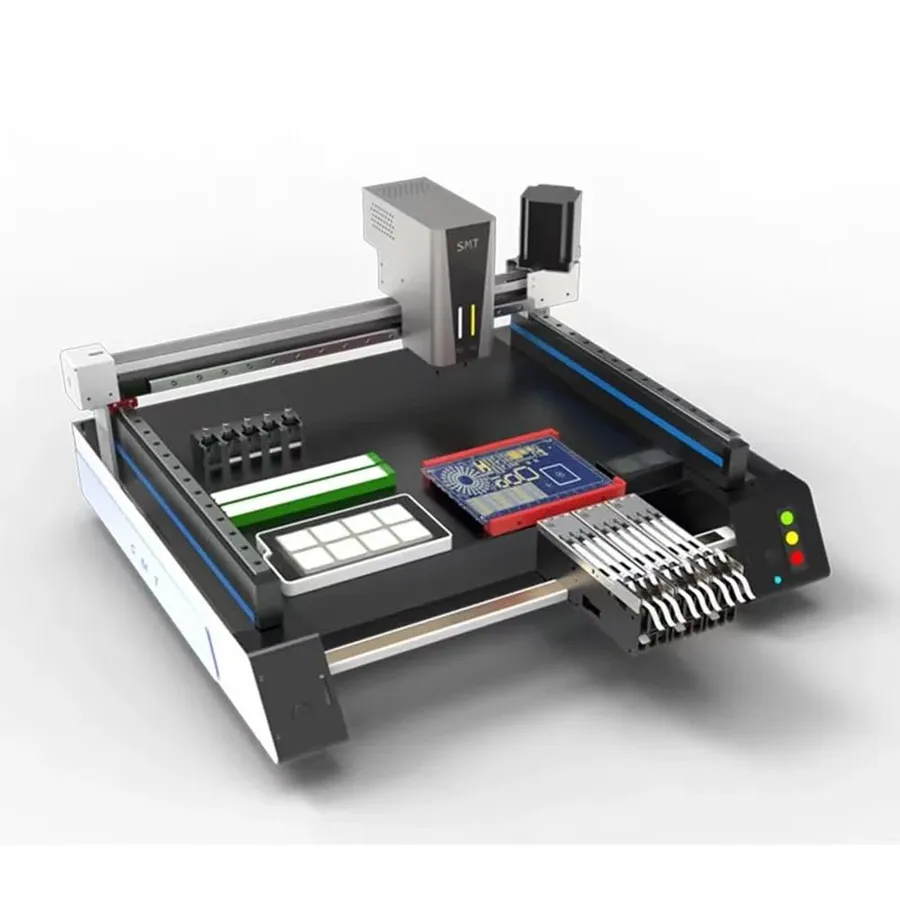
Surface Mount Technology (SMT) equipment represents a significant investment in PCB manufacturing, primarily due to the automation it provides. This section will explore the costs associated with key SMT machinery, including pick-and-place machines, reflow ovens, and solder paste printers, while examining the balance between upfront expenses and potential long-term operational efficiencies. The adoption of SMT technology enhances production precision and speed, but these benefits come with considerable initial financial considerations.
Equipment | Description | Typical Price Range (USD) | Operational Impact |
---|---|---|---|
Pick-and-Place Machine | Automated placement of surface mount components onto PCBs. | 5,000 - 500,000+ | High precision, high speed, reduced labor, initial high capital expenditure. |
Reflow Oven | Melts solder paste to create permanent electrical connections. | 2,000 - 150,000+ | Ensures even heating, critical for solder joint quality, energy costs involved. |
Solder Paste Printer | Applies solder paste onto PCB pads for component placement. | 1,000 - 40,000+ | Ensures consistent solder paste application, improves yield, relatively lower initial cost |
Automated Optical Inspection (AOI) System | Inspects PCBs for defects such as misaligned or missing components. | 10,000 - 100,000+ | Improves quality control, reduces defects, medium-to-high capital investment |
Stencil Cleaner | Cleans solder paste stencils efficiently. | 2,000 - 20,000+ | Improves stencil reusability, essential for high-volume production, moderate cost |
Used vs. New PCB Equipment: Weighing Cost and Reliability
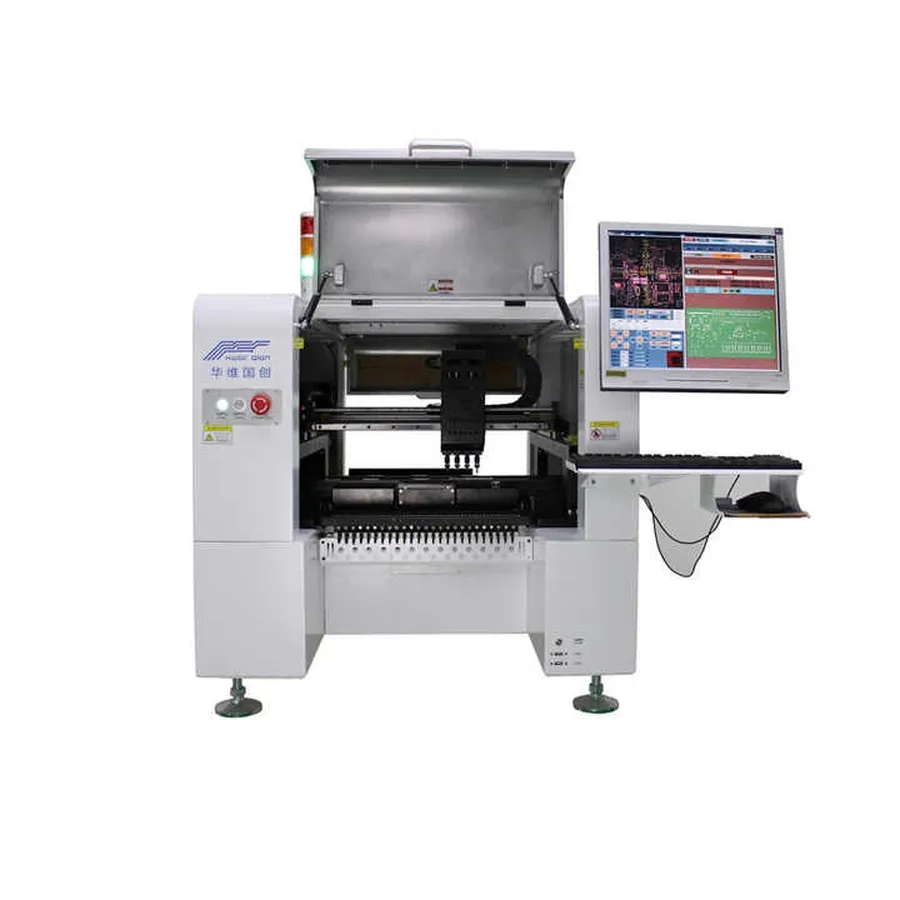
The decision between investing in new or used PCB manufacturing equipment involves a careful balance of cost savings against potential risks in reliability and longevity. While pre-owned equipment offers a lower initial investment, it's crucial to consider factors such as warranty, maintenance needs, and potential downtime, which can significantly impact production efficiency and overall costs.
Feature | New Equipment | Used Equipment |
---|---|---|
Initial Cost | Higher | Lower |
Reliability | Generally Higher | Potentially Lower |
Warranty | Typically Included | Often Limited or Absent |
Maintenance | Lower Short-Term | Potentially Higher, Unpredictable |
Technology | Latest Features | Older Technology |
Lifespan | Longer | Potentially Shorter |
Downtime | Lower Likelihood | Higher Potential |
Parts Availability | Readily Available | May Be Limited or Obsolete |
Used PCB manufacturing equipment can be a viable option, particularly for startups or smaller operations with limited budgets. However, thorough due diligence is paramount. This includes a detailed inspection by a qualified technician, a review of the equipment's maintenance history, and a clear understanding of the seller's return and warranty policies. Furthermore, consideration must be given to the availability of spare parts and the potential for future obsolescence of the used equipment.
Facility and Infrastructure Costs for PCB Production
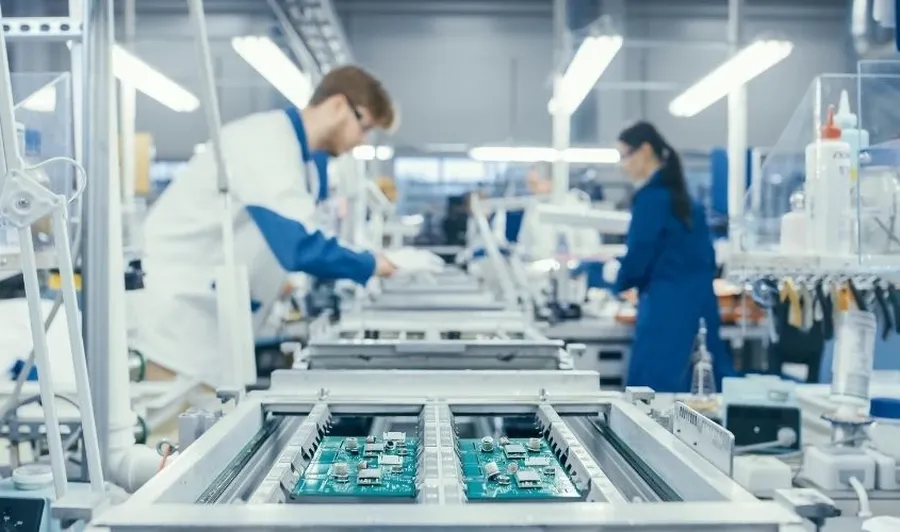
Establishing a PCB manufacturing facility necessitates significant upfront investment in infrastructure beyond just the manufacturing equipment. These foundational costs, encompassing space, environmental controls, and utilities, substantially impact the overall budget and operational efficiency of the production process. Careful consideration and planning are crucial to manage these costs effectively.
- Space Acquisition Costs
Space can be the largest single infrastructure cost, which can be the purchase or lease of a suitable facility. The cost varies widely based on location, size, and condition, with additional expenditure sometimes needed to modify existing structures to accommodate manufacturing processes and specialized equipment. - Environmental Control Systems
PCB manufacturing requires stringent environmental controls to maintain product quality and comply with environmental regulations. These systems include air filtration, temperature and humidity controls, and waste disposal, which involve a significant investment in specialized equipment and ongoing maintenance. Costs scale with factory size and specific process requirements. - Utilities Infrastructure Costs
Reliable utility services are essential for continuous PCB production. Setup costs for electrical systems (including transformers and backup power), compressed air, water supply, and industrial waste water treatment directly impact operational efficiency, including initial installation and ongoing usage costs. The scale is often based on the volume of the production - Permitting and Compliance Costs
Obtaining permits and licenses related to building code compliance, environmental standards, and safety regulations is critical and varies widely by region. These costs can add to the overall project expenses, due to variations in local and national regulations.
Software and Design Tools: The Hidden Costs of PCB Manufacturing
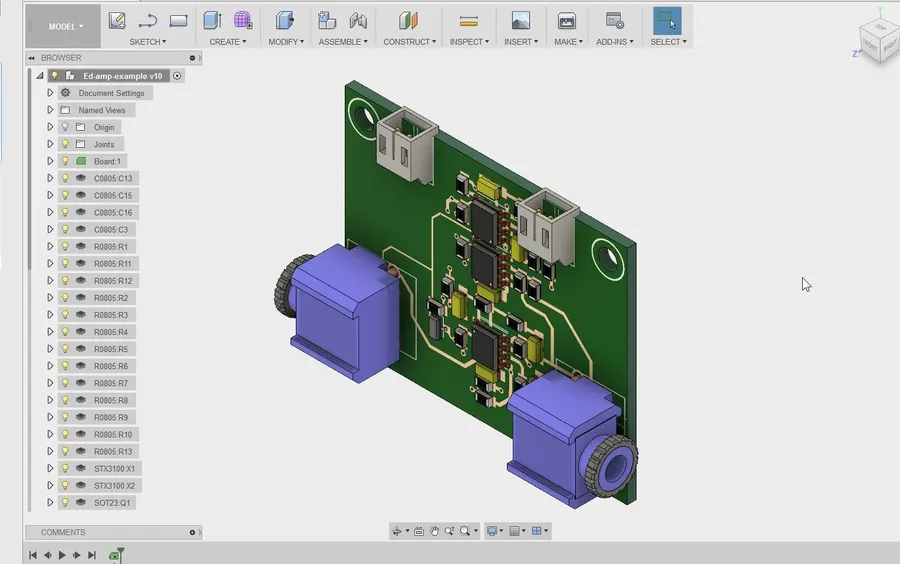
While physical equipment constitutes a major portion of PCB manufacturing costs, the often-overlooked expenses associated with software and design tools are critical for efficient and precise production. These digital tools are essential for every stage, from initial design to final production.
PCB design software, Computer-Aided Manufacturing (CAM) software, and other related tools are indispensable for translating ideas into manufacturable designs, therefore these software have an important role in PCB manufacturing.
- PCB Design Software
This includes Electronic Design Automation (EDA) suites that facilitate the creation of PCB layouts. These softwares vary in cost depending on features and licensing models. Options range from free, open-source software to expensive commercial packages that can cost thousands of dollars per license annually. Key features include schematic capture, layout design, and simulation capabilities. The cost can range from $0 to $10,000+ per year. - CAM Software
CAM software is used to prepare PCB designs for manufacturing by converting design files into instructions that machines understand. This software performs functions such as generating Gerber files, optimizing tool paths, and preparing designs for drilling and routing. The cost can vary from a few hundred dollars to several thousand dollars, depending on the complexity and functionality. Consider also the yearly cost of updates and maintenance. - Simulation and Analysis Tools
These tools are used to simulate and analyze the performance of PCBs before production. Simulation software can identify and rectify design issues like thermal problems and signal integrity issues. High-end simulation tools can be expensive but may prevent costly errors during production. The cost can be from a few hundred dollars to over $5000 annually. - Other Essential Software
This category includes software for data management, quality control, and project management, all necessary for efficient workflow and compliance. The cost here can be variable, depending on specific needs, it can range from free to several thousand dollars annually.
It is essential to also factor in the expenses associated with training personnel to effectively utilize these software tools. Continuous updates and maintenance fees for the software should also be considered as ongoing expenses.
PCB Manufacturing Equipment Cost Table: A Detailed Breakdown
A detailed breakdown of PCB manufacturing equipment costs is essential for budgeting and planning. The following table provides estimated price ranges for various types of equipment, from basic tools to advanced automated systems. These ranges can assist in making cost-effective decisions when setting up or expanding a PCB production facility. Prices are subject to change based on manufacturer, specific features, and market conditions.
Equipment Type | Price Range (USD) | Description |
---|---|---|
Manual Etching Tank | $500 - $3,000 | Basic tank for chemical etching of PCBs, typically for small-scale or prototyping. |
PCB Drilling Machine (Manual) | $1,000 - $5,000 | Manual machines for drilling holes in PCBs, suitable for low-volume production. |
Manual Solder Station | $100 - $500 | Basic soldering tools for manual assembly and rework of PCB components. |
Automated Etching Machine | $5,000 - $50,000 | Automated systems for precise and consistent chemical etching, increasing throughput. |
CNC PCB Drilling Machine | $10,000 - $100,000+ | Computer Numerical Control machines for accurate drilling of complex PCB designs. |
Solder Paste Printer (Manual) | $500 - $2,000 | Manual screen printing tools for applying solder paste to PCBs. |
Pick and Place Machine (Entry-Level) | $10,000 - $50,000 | Entry-level automated machines for placing surface mount components onto PCBs. |
Reflow Oven (Benchtop) | $2,000 - $10,000 | Small to medium reflow ovens, typically for small batches and prototyping. |
Automated Solder Paste Printer | $10,000 - $80,000 | Automated systems for precise and high-throughput application of solder paste. |
Pick and Place Machine (High-Speed) | $50,000 - $500,000+ | High-speed, advanced automated systems for high-volume SMT assembly. |
Reflow Oven (Industrial) | $20,000 - $150,000+ | Industrial-grade reflow ovens for large-scale and high-precision PCB assembly. |
AOI Machine (Automated Optical Inspection) | $20,000 - $200,000+ | Automated optical inspection machines for quality control of assembled PCBs. |
Wave Soldering Machine | $15,000 - $100,000+ | Machines for through-hole component soldering, often used alongside SMT assembly. |
X-Ray Inspection System | $50,000 - $300,000+ | Advanced inspection systems for analyzing internal solder joints and component integrity. |
Frequently Asked Questions about PCB Manufacturing Equipment Costs
Understanding the costs associated with PCB manufacturing equipment is crucial for anyone looking to enter or scale within the industry. This section addresses the most frequently asked questions regarding these costs, providing clear and actionable insights.
- What is the estimated initial investment for starting a small PCB manufacturing factory?
The initial investment for a small PCB manufacturing facility can vary widely, typically ranging from $50,000 to $500,000 or more. This range depends on the level of automation, production volume, and the specific equipment chosen. Entry-level setups with manual or semi-automated machines can start on the lower end, while facilities using advanced SMT equipment with higher capacity require significantly higher capital. - How does the PCB manufacturing cost per square inch vary, and what factors affect it?
The cost per square inch for PCB manufacturing is not a fixed value and depends on multiple factors including the PCB layer count (single-layer, double-layer, or multi-layer), the type of materials used (FR-4, flex, etc.), the complexity of the design (number of vias, trace width, and spacing), the production volume, and the manufacturing process (such as chemical etching or laser direct imaging). These factors collectively determine the overall price, emphasizing the importance of optimizing the design and material selection for cost efficiency. - How does the volume of PCBs manufactured affect the overall cost?
Manufacturing volume has a significant impact on the unit cost of PCBs. Higher volumes typically lead to reduced per-unit costs due to economies of scale. This is because fixed costs associated with setup, tooling, and programming are spread across a larger number of units, lowering the average cost. Therefore, if a larger volume is feasible, it would be optimal to manufacture them in one go. - What are the primary cost drivers in PCB manufacturing beyond equipment?
Beyond equipment, significant costs in PCB manufacturing stem from material costs, labor expenses, design complexity, tooling, testing, and quality control processes. Material costs are influenced by the type and quantity of laminate, copper, and other materials used. Labor expenses depend on the degree of automation and the number of skilled operators required. Complex designs lead to higher manufacturing costs due to increased production time and resource consumption, while thorough testing and QC ensure that defects are caught early, minimizing the long-term cost associated with failures. Therefore, a comprehensive and holistic approach to evaluating all costs involved is essential in cost-cutting. - Is it more cost-effective to outsource or manufacture PCBs in-house?
The decision to outsource or manufacture PCBs in-house depends on various factors such as the production volume, required quality, desired turnaround times, and available budget. Outsourcing can be more cost-effective for low to medium volumes and allows access to specialized equipment and expertise without large capital investment. In-house manufacturing offers more control and faster turnaround times, but requires substantial investment in equipment, training, and infrastructure. Hence, a thorough evaluation of these factors and their potential impact on costs is necessary. - How can design choices affect the manufacturing cost of a PCB?
Design choices heavily influence manufacturing costs. Factors such as the number of layers, via types, trace width and spacing, component selection, and board dimensions directly affect both material usage and processing time. Designing for manufacturability (DFM) is vital for cost-effectiveness, as it reduces defects and makes the manufacturing process more streamlined. Designs that minimize complexity and optimize material usage can lead to significantly lower production costs. - What is the typical cost range for an SMT pick-and-place machine?
SMT pick-and-place machine costs vary greatly based on the speed, accuracy, and level of automation they provide. Manual machines and low-volume models can be found for under $10,000, while automated high-speed, high-accuracy systems can range from $50,000 to over $300,000. The specific requirements of a production line will determine the type and cost of the pick-and-place machine required, and a careful selection based on their cost-performance ratio is necessary.
Optimizing PCB Manufacturing Costs: Tips and Strategies
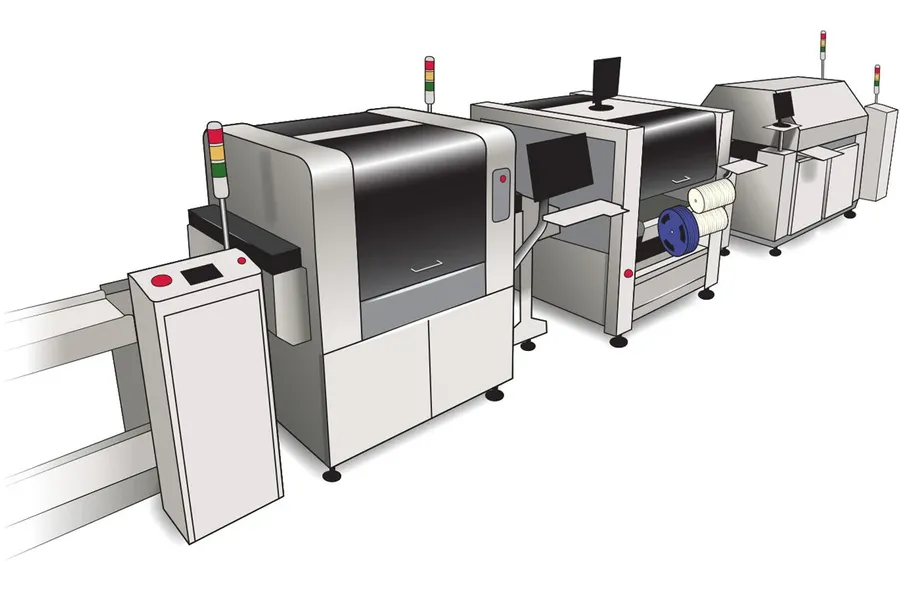
Reducing PCB manufacturing costs requires a multifaceted approach, addressing design, material selection, and supply chain efficiencies. Strategic cost optimization not only reduces expenditure but can also improve product quality and time-to-market.
- Design for Manufacturability (DFM)
Implementing DFM principles from the initial design phase is crucial. It involves simplifying designs, reducing the number of layers, using standard component sizes, and ensuring sufficient spacing. Such designs are easier and less expensive to manufacture, which in turn reduces overall production costs. This approach minimizes manufacturing defects and rework, saving both time and money. - Material Selection
Careful selection of materials can significantly impact costs. Opting for cost-effective base materials like FR-4, where suitable, instead of high-performance alternatives for non-critical applications reduces material costs without compromising functionality. Additionally, consider the cost and availability of different surface finishes, balancing performance requirements with budgetary constraints. - Efficient Supply Chain Management
Establishing a robust and efficient supply chain is essential to manage costs effectively. This involves carefully vetting suppliers, negotiating favorable pricing contracts, and optimizing inventory levels to minimize holding costs. Building long-term relationships with suppliers based on mutual trust and transparency can also lead to better pricing and delivery terms. Additionally, leveraging volume discounts and strategically scheduling orders can further lower costs. - Negotiate Pricing with Suppliers
Actively engaging in price negotiations with suppliers is a key cost reduction strategy. By understanding market dynamics and maintaining a competitive mindset, it is often possible to negotiate better rates. A regular review of supplier contracts is important, and building solid relationships can help create room for price negotiation. - Panelization and Batching
Panelizing small PCBs on a larger panel for manufacturing is a cost-effective strategy, enabling more boards to be produced in one manufacturing cycle. Batching orders can also significantly reduce per-unit costs, especially when combining orders with other PCB requirements. This reduces setup costs and production downtime. - Utilize Standard Component Sizes
Specifying standard-sized components rather than custom or less readily available parts simplifies the procurement process and reduces costs. Standardized parts are typically more affordable and easier to source, resulting in a more economical bill of materials (BOM) for PCB production. Standard components also minimize manufacturing time and potential complications.
Future Trends in PCB Manufacturing Technology and Pricing
The PCB manufacturing industry is on the cusp of significant transformation, driven by advancements in technology and materials science. These innovations are poised to reshape production processes and, consequently, equipment costs. Understanding these emerging trends is crucial for businesses looking to remain competitive and make informed investments.
Several key trends are expected to influence the future of PCB manufacturing:
- Increased Automation and Robotics
The integration of robotics and automated systems will continue to expand beyond basic SMT assembly. Expect to see more automated material handling, quality control, and even in-line repair systems. This shift aims to enhance throughput, reduce human error, and lower labor costs. These advanced machines, while initially expensive, promise significant long-term cost efficiencies and improved precision. - Advanced Materials and Substrates
The use of new materials, such as flexible substrates, and novel polymers is gaining momentum, driven by the need for miniaturization and high-frequency applications. This will necessitate new equipment that can handle these specialized materials, which may initially drive up costs before economies of scale are realized. Examples include laser direct structuring (LDS) equipment for 3D circuitization and specialized etching and plating processes for new substrates. - Digitalization and Industry 4.0
The adoption of Industry 4.0 principles, such as IoT, data analytics, and cloud-based manufacturing execution systems (MES), will transform PCB production. This shift allows for predictive maintenance, real-time process monitoring, and optimized resource utilization. Equipment that integrates seamlessly with digital platforms and offers robust data capabilities will be highly valued. - Additive Manufacturing and 3D Printing
Additive manufacturing techniques, particularly 3D printing for PCB prototypes and custom designs, are becoming increasingly relevant. This allows for faster prototyping and on-demand manufacturing of specialized circuits. While still an emerging technology for mass production, advancements are expected in material compatibility, printing speed, and precision. The convergence of additive manufacturing and traditional techniques will create opportunities for new cost-effective hybrid manufacturing processes. - Miniaturization and High-Density Interconnect (HDI)
The relentless push for smaller, more compact electronic devices will continue to drive advancements in PCB technology, resulting in smaller trace widths and more complex multi-layer boards. This trend requires high-precision machines, including advanced laser drills and high-resolution imaging systems, which may initially increase equipment costs.
Impact on Pricing Structures:
- Initial Capital Expenditure
New technologies often come with high initial capital expenditure. Early adopters may face higher equipment costs. However, as the technology matures and market competition increases, prices are expected to decrease gradually. It's essential to plan investments strategically, considering both short-term and long-term benefits. - Operational Costs
While the initial investment in advanced equipment may be high, the implementation of automation, efficient resource utilization, and reduced labor will likely lead to lower operational costs. These cost savings could include lower energy use, reduced wastage, and higher production yields. Predictive maintenance enabled by digital systems will also lower downtime and repair expenses. - Total Cost of Ownership
The total cost of ownership (TCO) should be the primary factor in determining investment strategies. It is crucial to consider not only the initial equipment price, but also factors such as maintenance, training, lifespan, and long-term operational costs. A TCO analysis will help determine whether new, more expensive equipment is a financially sound decision compared to maintaining or investing in used equipment.
In conclusion, the future of PCB manufacturing will be defined by the integration of automation, advanced materials, digitalization, and additive manufacturing. While these trends might initially increase equipment costs, they also promise greater efficiency, lower operational costs, and higher product quality. Businesses must stay informed about these developments, carefully evaluate the costs and benefits of these technologies, and adopt a long-term strategy to remain competitive in the rapidly evolving landscape of PCB manufacturing.
Understanding the costs associated with PCB manufacturing equipment is crucial for any business involved in electronics production. Whether you're setting up a new facility or upgrading existing equipment, a clear grasp of the various factors influencing cost, from basic tools to high-end SMT lines, is key. By carefully considering your options, from new vs. used equipment to the latest manufacturing technologies, and utilizing the strategies outlined in this guide, you can make informed decisions that optimize your budget and ensure your business remains competitive in the dynamic field of PCB production. Remember to always stay abreast of the latest advancements and trends that may affect [pcb manufacturing equipment cost] and, consequently, your bottom line.
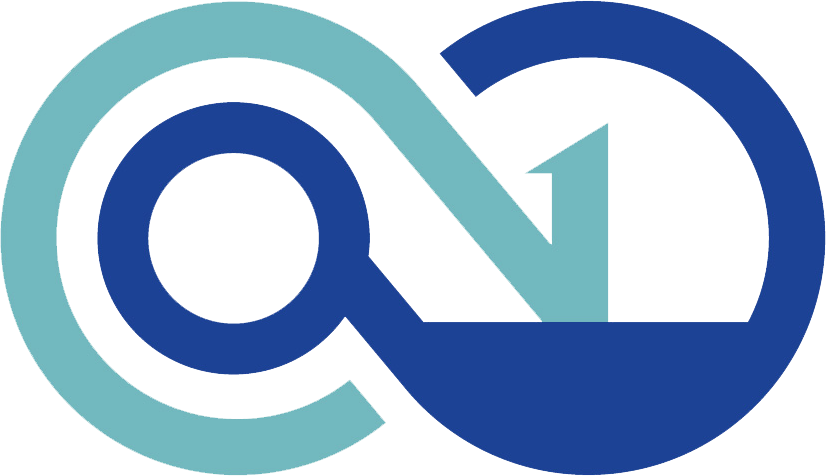