Fast PCB Prototyping: Your Guide to 24 Hour PCB Manufacturers
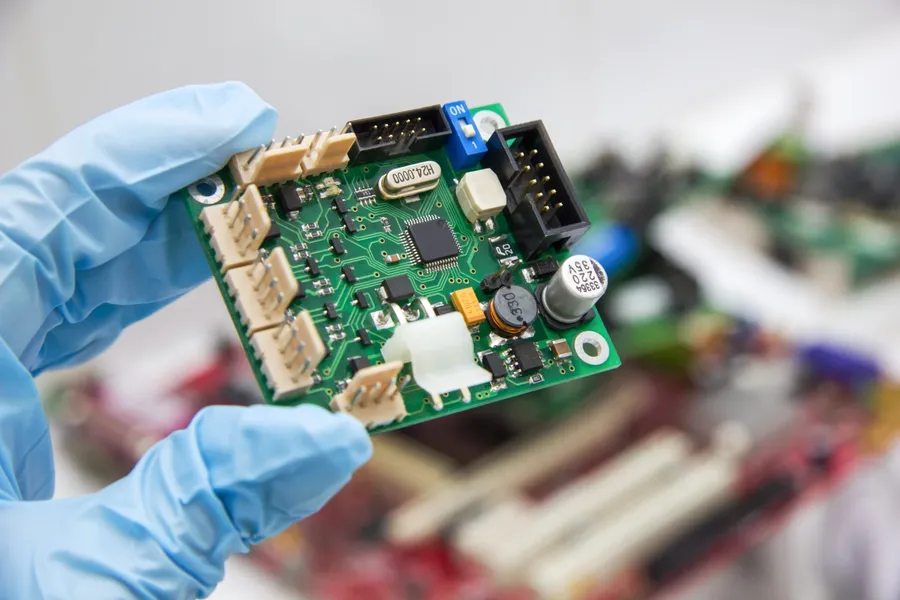
In today's fast-paced electronics industry, time is of the essence. Whether you're a startup needing a rapid prototype or a large company requiring quick turnaround, accessing a reliable 24 hour PCB manufacturer can be crucial to success. This article explores the landscape of 24-hour PCB manufacturing, providing insight into what to look for and how to choose the right partner for your needs. We’ll delve into the processes, considerations, and options available, helping you to make informed decisions about your PCB production timeline.
What is 24 Hour PCB Manufacturing?
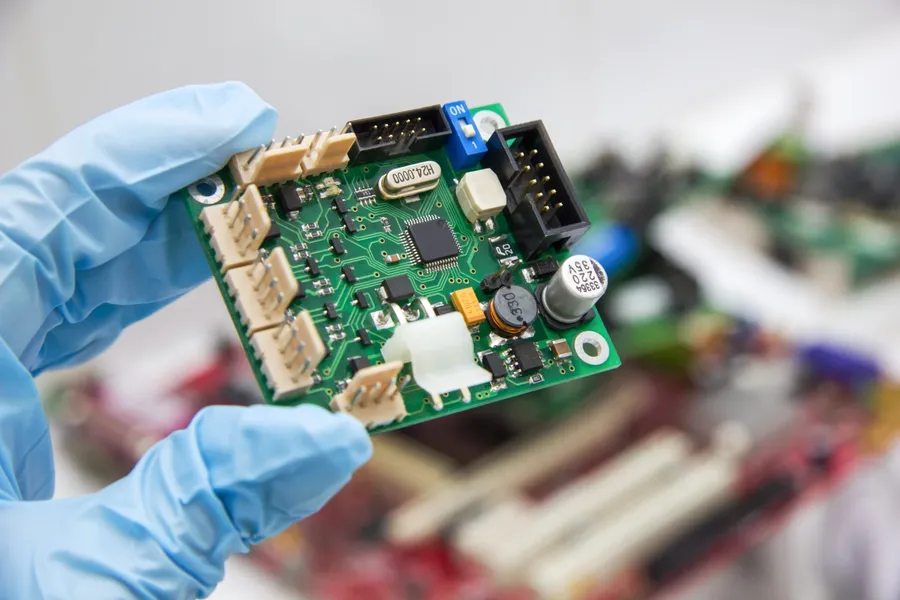
24-hour PCB manufacturing refers to the rapid production of printed circuit boards (PCBs) within a 24-hour timeframe from the time the design is finalized and submitted for manufacturing. This expedited process is crucial for rapid prototyping, quick design iterations, and time-sensitive projects where minimal delay is critical. It leverages advanced technologies, streamlined workflows, and efficient material management to drastically reduce the typical PCB production timeline.
The core of 24-hour PCB manufacturing lies in optimizing every step of the production process. This includes automated design file processing, CNC drilling and milling, fast etching, rapid solder mask application, and accelerated curing techniques. The entire operation is designed to be highly efficient, ensuring that the PCB fabrication process is completed within a single day. Key to achieving such speed is having readily available materials and a high level of automation.
Key Features of a Reliable 24 Hour PCB Manufacturer

Selecting a reliable 24-hour PCB manufacturer is crucial for projects requiring rapid prototyping and quick turnaround times. The ideal manufacturer should not only provide fast production but also maintain high standards of quality, precision, and customer service. These factors are critical in ensuring that your PCB design translates into a functional and reliable product within the tight 24-hour timeframe.
- Quick and Accurate Quote Process
A streamlined and automated quote process is essential for a 24-hour PCB manufacturer. This ensures that you receive a detailed and transparent quote rapidly, without unnecessary delays that can hamper your timeline. The quicker the quote, the sooner you can proceed with production. - Advanced Manufacturing Equipment
State-of-the-art manufacturing equipment is a cornerstone of a dependable 24-hour PCB service. This includes high-speed drills, automated pick-and-place machines, and precise etching equipment. Advanced equipment not only ensures speed but also maintains the necessary precision for complex designs. - Readily Available Materials
A reliable manufacturer will have a wide array of materials readily available in stock, avoiding delays due to material procurement. This availability includes common materials like FR-4, as well as more specialized options, ensuring they can meet the diverse needs of various projects. - Robust Quality Control Measures
Even with tight deadlines, the manufacturer must not compromise on quality. Implementing robust quality control measures, like Automated Optical Inspection (AOI) and electrical testing, ensures that every PCB meets the required specifications. This helps catch any manufacturing defects early on, saving time and resources. - Efficient Communication Channels
Effective communication is crucial for a 24-hour PCB manufacturer. You should have easy access to project updates and support throughout the manufacturing process, enabling timely resolution of issues and clarifications. This includes prompt response times and dedicated customer support. - Experience with Quick-Turn Manufacturing
A manufacturer experienced in quick-turn PCB production is better equipped to handle the unique demands of a 24-hour timeframe. This means they are familiar with the required processes and can anticipate potential challenges, ensuring a smoother and more efficient turnaround. - Transparent Pricing Structure
A clear and detailed pricing structure is vital. The manufacturer should be upfront about costs associated with expedited services, so you can budget accordingly and avoid hidden fees. Transparent pricing builds trust and helps in long-term business relationships.
Comparing 24 Hour PCB Manufacturers: A Table Analysis
Selecting the right 24-hour PCB manufacturer requires a thorough comparison of their capabilities, pricing, and services. This section provides a comparative table analysis, highlighting key differences among several manufacturers known for quick-turn PCB production. This will allow you to make an informed decision based on your specific project requirements, considering factors such as cost, material availability, production capacity, and geographical location, alongside the range of additional services offered such as assembly.
Manufacturer | Location | Typical Turnaround (Hours) | Base Material Options | Layer Count | Min Track/Space (mm) | Price (USD, for example) | Additional Services |
---|---|---|---|---|---|---|---|
Manufacturer A | USA | 24-48 | FR-4, Aluminum | 1-8 | 0.1 | $50 - $200 | Assembly, Design Review |
Manufacturer B | China | 24-72 | FR-4, Flexible | 1-16 | 0.075 | $30 - $150 | Stencil Service, Testing |
Manufacturer C | Europe | 48-72 | FR-4, High Tg | 1-12 | 0.12 | $70 - $250 | Impedance Control, Panelization |
Manufacturer D | USA | 24-48 | FR-4, Rogers | 1-6 | 0.09 | $80-$300 | X-Ray Inspection |
Manufacturer E | China | 24-48 | FR-4, CEM-1 | 1-4 | 0.15 | $20 - $100 | None |
Commonly Used Materials in Quick Turn PCB Manufacturing
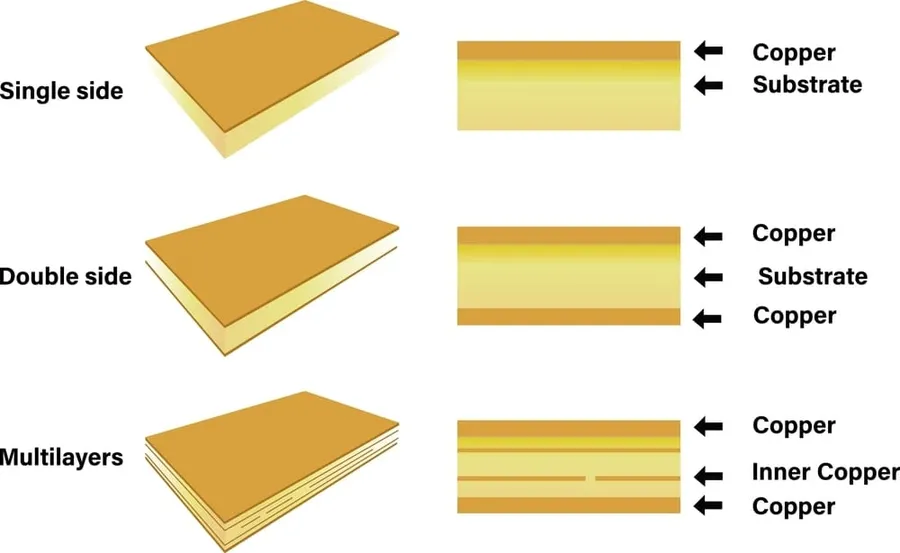
The selection of materials for quick-turn PCB manufacturing is critical for achieving rapid turnaround times while maintaining performance and reliability. This section details commonly used materials optimized for speedy production, focusing on their properties and suitability for various applications.
Material | Description | Properties | Typical Applications | Suitability for Quick Turn |
---|---|---|---|---|
FR-4 (Flame Retardant 4) | A composite material made of woven fiberglass cloth with an epoxy resin binder. | Good mechanical strength, good electrical insulation, flame retardant, cost-effective, widely available. | General-purpose PCBs, consumer electronics, industrial control systems, prototyping. | Highly suitable due to its common availability and ease of processing |
High-Tg FR-4 | Similar to FR-4 but with a higher glass transition temperature (Tg). | Improved thermal resistance, better performance at elevated temperatures, good electrical insulation. | High-temperature applications, automotive electronics, power electronics. | Suitable, but availability of higher Tg variants may slightly impact lead times compared to standard FR-4 |
Aluminum Substrates | A metal core substrate with a thin layer of dielectric material and copper foil. | Excellent heat dissipation, good mechanical strength, lightweight. | LED lighting, power supplies, automotive electronics. | Good for some applications but may require special processing, which can slightly increase turnaround time compared to standard FR-4 |
Rogers Materials | A range of high-frequency laminates with low dielectric loss and stable dielectric constant. | Excellent electrical performance at high frequencies, low insertion loss, good thermal stability. | RF and microwave circuits, wireless communication, high-speed digital circuits. | May increase turnaround times due to limited availability and specialized processing needs |
Polyimide | A high-performance polymer with excellent thermal stability and flexibility. | High thermal resistance, good flexibility, chemical resistance, excellent dielectric properties. | Flexible PCBs, high-temperature applications, aerospace electronics. | May not be optimal for the shortest turnaround due to specialized processing techniques. |
Design Considerations for 24 Hour PCB Manufacturing
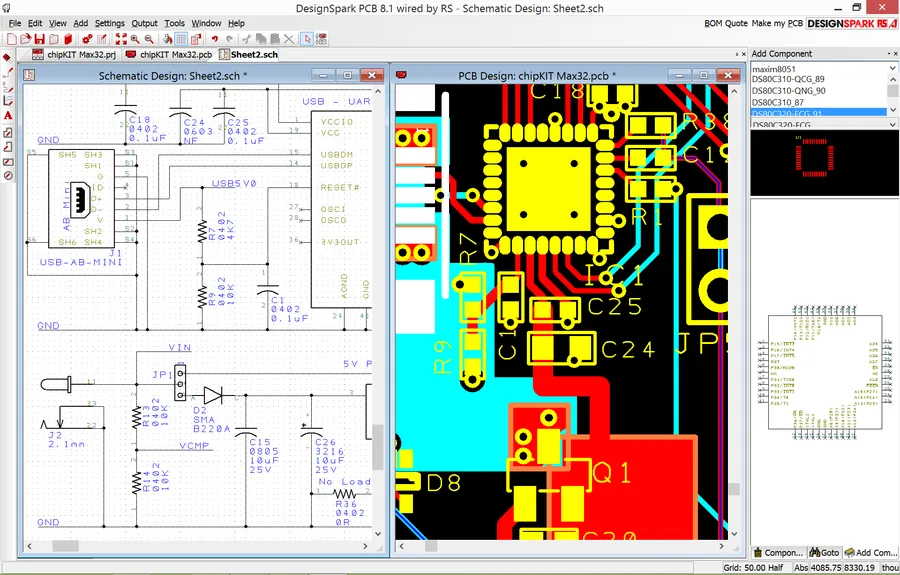
Designing for 24-hour PCB manufacturing necessitates a focus on simplicity and manufacturability to ensure a smooth and rapid production process. Key design parameters such as trace widths, layer counts, via design, and panelization must be carefully considered to minimize delays and ensure the design is optimized for quick turnaround fabrication.
- Trace Widths and Spacing
Opt for standard trace widths and clearances that are within the capabilities of most quick-turn PCB manufacturers. Avoid excessively fine traces or very tight spacing, as these may require more specialized processes and could potentially slow down production. - Layer Count
Stick to common layer counts (e.g., 1, 2, or 4 layers) whenever possible. More complex layer stacks can significantly increase processing time and are less readily available for expedited services. - Via Design
Utilize standard via sizes and avoid complex via structures, such as blind or buried vias, which can add significant time to manufacturing. Through-hole vias are the easiest and fastest to produce. - Panelization
Consider panelizing your PCB design if you are ordering multiple boards or if it suits the manufacturer's standard panel sizes. This can improve efficiency and reduce the cost per board. However, discuss panelization with your manufacturer to ensure their guidelines are followed. - Component Footprints
Use standard component footprints from libraries to ensure rapid assembly. Any custom or unusual component footprints may delay the process due to manual intervention or additional checking. - Avoid Complex Features
Minimize the use of complex shapes, small cutouts, or non-standard features as they may increase manufacturing complexity. Simplify the design to ensure quick and reliable production. - Clear Markings and Labels
Include clear markings and labels in your design for easy identification and assembly. This can streamline the process and reduce the likelihood of errors.
Streamlining Your PCB Order for Rapid Turnaround
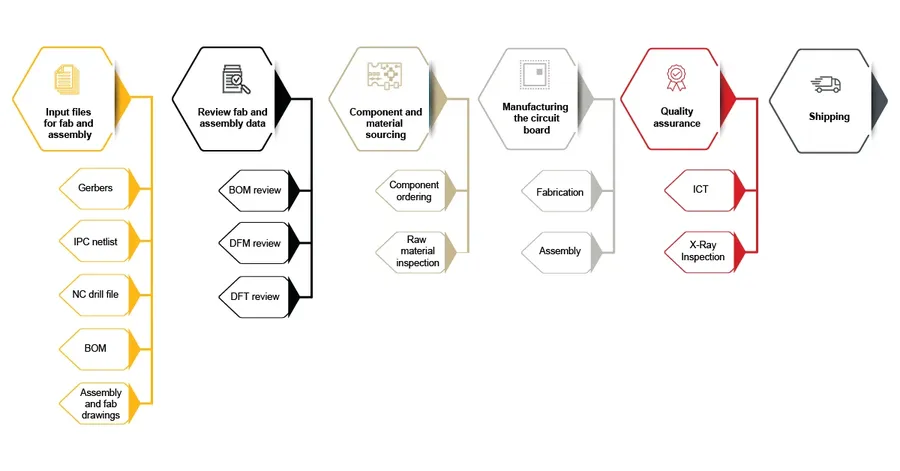
To maximize the efficiency of a 24-hour PCB manufacturing service, meticulous preparation of your design files and specifications is paramount. This proactive approach minimizes delays and ensures a smooth, rapid production process, allowing you to fully leverage the capabilities of a quick-turn manufacturer.
- Use Standard File Formats
Submit your PCB design using industry-standard formats such as Gerber RS-274X or Gerber X2 files, along with Excellon drill files. These formats are universally compatible with manufacturing equipment, reducing the risk of misinterpretation and processing delays. Always include a clear readme file detailing file layers, their purpose, and any special instructions. Avoid proprietary or custom file formats that may require additional translation or processing time. - Double-Check Design Rules
Verify that your PCB design strictly adheres to the manufacturer's Design Rule Check (DRC) specifications prior to submission. Pay close attention to trace widths and spacing, via sizes and clearances, solder mask and silkscreen specifications, and board outline dimensions. Correcting design violations during the manufacturing stage is time consuming and can lead to significant delays. Use a robust PCB design software with integrated DRC capabilities and utilize online DRC checks from manufacturers to ensure no issues. - Provide Clear Layer Stacking Information
Clearly define your layer stack-up including material type, thickness for each layer (both core and prepreg materials), copper thickness, and surface finish requirements. A well-documented layer stack up ensures the manufacturer understands your precise construction requirements, avoiding any ambiguities. Include the materials' data sheet where possible. If you are using special impedance controlled traces, add documentation to specify the impedance requirements. - Accurate Bill of Materials (BOM)
Provide an accurate BOM with comprehensive part numbers, manufacturer details, and component footprints. Ensure that part numbers precisely match the parts needed and that there are no component issues that can impact manufacturing, assembly, or testing. If parts are obsolete or end-of-life, clearly mark on the BOM and specify suitable replacements. Any error in the BOM can delay your entire manufacturing process and assembly. - Include Fabrication Notes
Add detailed fabrication notes or a readme file containing specific instructions, such as special material requirements, any impedance-controlled layers, specific board finish requirements, or any specific manufacturing requests (e.g., panelization, scoring, or fiducial marks) to minimize misinterpretations and manufacturing errors, leading to delays. Include information about specific hole tolerances or other unique requirements for the board. - Panelize Efficiently
If you require multiple PCBs, panelize the boards yourself according to the manufacturer's specifications. This can save time and reduce costs by allowing for more efficient processing of the boards during production. Always add tooling holes and fiducials within the panel according to the manufacturers specification. Consult with the manufacturer on the most optimal panel design based on their equipment and processing workflow. - Communicate Clearly
Maintain open and clear communication with your manufacturer. Promptly address any questions they may have about your design or specifications and ask any questions that you may have to ensure accuracy in the output. Clear and timely communication allows for fast resolution of manufacturing issues and can expedite your order.
Beyond Manufacturing: What about Assembly & Testing?
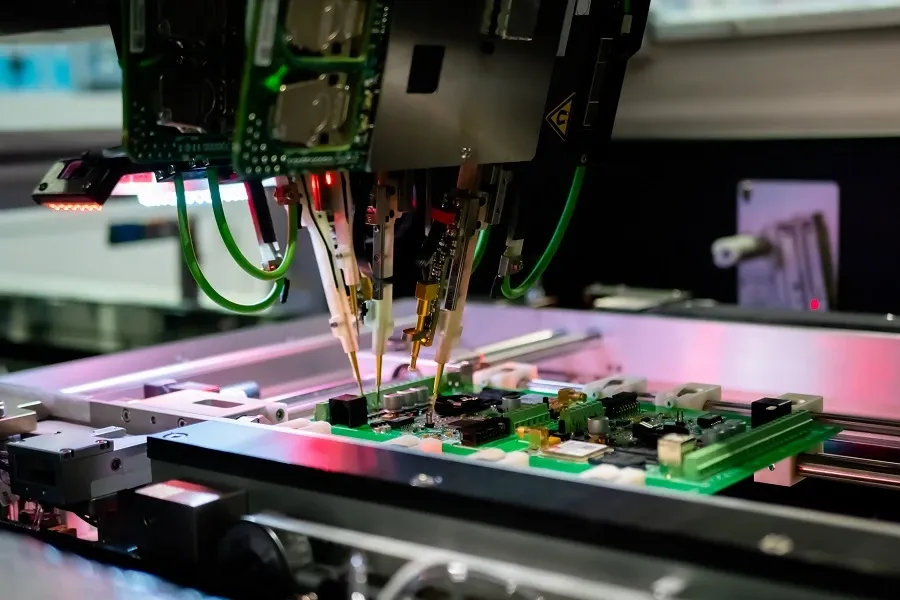
While rapid PCB fabrication is crucial, the subsequent steps of assembly and testing are equally vital to achieving a fully functional product within a tight timeframe. Integrating these processes efficiently is key to leveraging the benefits of a 24-hour PCB manufacturing service. This section examines options for quick-turn assembly and testing, focusing on critical considerations for project deadlines.
- Quick-Turn Assembly Options
Several manufacturers offer expedited assembly services alongside their PCB fabrication. This can range from simple component placement to more complex surface mount technology (SMT) assembly. The availability of these options depends on the complexity of your design and the manufacturer's capabilities. - Factors Affecting Assembly Timelines
Assembly timelines are influenced by factors such as the number of components, the types of components (e.g., through-hole vs. SMT), the complexity of the placement, and the availability of necessary parts. Sourcing components in parallel with PCB manufacturing can save valuable time. - Importance of Design for Assembly (DFA)
Designing your PCB with assembly in mind is critical for a quick turnaround. Considerations like component spacing, orientation, and the use of standardized footprints facilitate smoother assembly processes. DFA also minimizes the risk of errors and rework during assembly. - Testing Options for Rapid Verification
Basic testing methods such as visual inspection and continuity checks are often part of a quick-turn assembly service. More extensive testing, such as functional tests or in-circuit testing (ICT), may be offered but could impact the overall timeline. Defining required testing levels at the outset is crucial. - Integration with Manufacturing
Integrating assembly and testing with your chosen PCB manufacturer allows for a streamlined process where the manufacturing and assembly are coordinated to reduce delays. This often involves sharing a bill of materials (BOM) and assembly instructions early in the manufacturing process. - Component Sourcing and Lead Times
The availability of components is a major factor for quick turn assembly. Utilizing manufacturers with in-house component warehousing or having components readily available is crucial to avoiding delays. Lead times for difficult to source parts must be considered.
Frequently Asked Questions about 24 Hour PCB Manufacturing
Navigating the world of quick-turn PCB manufacturing can raise several questions. This section addresses common inquiries regarding 24-hour PCB manufacturing, focusing on cost implications, potential delays, and strategies for selecting a dependable manufacturer.
- How does 24-hour turnaround time affect the cost of PCBs?
Expedited PCB manufacturing generally involves a premium due to the priority handling, rapid setup, and potential overtime required. Costs can vary based on manufacturer, PCB complexity, material, and order volume. Expect to pay more for a 24-hour service compared to standard lead times. - What are the most common causes of delays in 24-hour PCB manufacturing?
Delays often stem from design file errors, material availability issues, high order volumes, complex board designs, or a lack of communication. Ensure your Gerber files are accurate, BOMs are complete, and any special requirements are clearly stated in advance to minimize potential delays. - How can I choose a reliable 24-hour PCB manufacturer?
Look for manufacturers with established reputations, transparent pricing structures, clear communication channels, advanced equipment, robust quality control processes, and readily available customer support. Review customer testimonials and case studies before committing. - Can all PCB designs be manufactured within 24 hours?
Not all PCB designs are suitable for 24-hour production. Complex, multi-layer boards or those using exotic materials may require longer production times. It's essential to confirm your design's feasibility with the manufacturer during the quote phase. - What is the typical production process for 24-hour PCBs?
The process includes rapid design file verification, accelerated CAM processing, streamlined PCB fabrication, automated assembly (if applicable), and immediate quality checks. The key is efficiency and minimizing downtime between processes. - Are there any design best practices for quick turn PCB manufacturing?
Yes, using standard materials and component footprints readily available to the manufacturer, designing for manufacturability (DFM) with generous trace widths, pad sizes, and clearances, adhering to the manufacturer's specific design rules, and simplifying board layouts will expedite the fabrication. - What should I do if I experience issues with my 24-hour manufactured PCB?
Communicate with the manufacturer immediately with any issues that arise. Provide them with detailed error descriptions and supporting documentation. A reliable 24-hour manufacturer should provide responsive support and resolution to ensure customer satisfaction and board functionality.
Real-World Case Studies and Applications
The expediency of 24-hour PCB manufacturing profoundly impacts various sectors, enabling rapid prototyping, swift product iterations, and time-sensitive project completions. This section explores some applications, showing how crucial fast turnaround times are in the PCB manufacturing world.
- Rapid Prototyping:
In the fast-paced product development landscape, engineers need to quickly validate designs and concepts. 24-hour PCB manufacturing drastically reduces the time between design and testing, allowing for faster experimentation and product refinement. This speed to prototype is crucial for iterative design processes, where small changes are tested, optimized, and re-tested, leading to a more refined final product. For instance, a startup developing a new IoT sensor might use a 24-hour service to iterate through several board designs within a week, reducing their time to market significantly. - Consumer Electronics:
The consumer electronics sector is known for its extremely short product cycles and rapid innovation. The ability to swiftly produce PCBs allows manufacturers to introduce new models and modifications to existing products faster than their competition. From new smartphone components to updated wearable tech, the fast-paced nature of the industry requires a manufacturing solution that can keep up. For example, a company releasing a new smartphone model can use 24-hour PCB manufacturing to quickly produce the prototype boards, thereby significantly shortening the time-to-market for the product. - Industrial Equipment:
In the industrial realm, the reliability of components is just as crucial as their speed. Industries such as automation, aerospace, and medical devices benefit greatly from 24-hour PCB manufacturing as quick turnaround times enable quick repairs or upgrades of systems. This rapid response ensures minimal disruption to production processes or critical operations. For instance, a factory relying on a specific control system might require a replacement PCB on short notice to avoid downtime, which could lead to significant revenue loss. Using a 24-hour PCB manufacturing service, the factory can minimize downtime and restore operations faster. - Educational Institutions and Research:
Universities and research institutions frequently need custom PCBs for laboratory setups and experiments. Using a 24-hour PCB manufacturer allows researchers to quickly test different hypotheses without delay, supporting fast-paced research projects. This includes applications in robotics, material science, and embedded systems where experimentation with different circuits is a major component of progress. For example, a university research team developing a novel robot control system can use 24-hour PCB manufacturing to rapidly iterate the control board to test different functionalities and improve the robot's performance. - Emergency Repairs:
In emergency repair scenarios, such as in power plants or critical infrastructure systems, fast PCB production is essential to minimize downtime and prevent cascading failures. 24-hour PCB manufacturing can quickly restore functionality to essential systems, allowing for a rapid response to unexpected malfunctions.
Choosing the right 24 hour PCB manufacturer is crucial for projects with tight deadlines. By understanding the processes, materials, design considerations, and key questions, you can make informed decisions to ensure your project moves forward quickly and successfully. The speed provided by a 24 hour pcb manufacturer empowers companies to iterate designs and respond faster to market trends, keeping them ahead in a competitive environment. Looking forward, continued advancements in manufacturing technologies will further optimize turnaround times, supporting innovation in the tech sector.
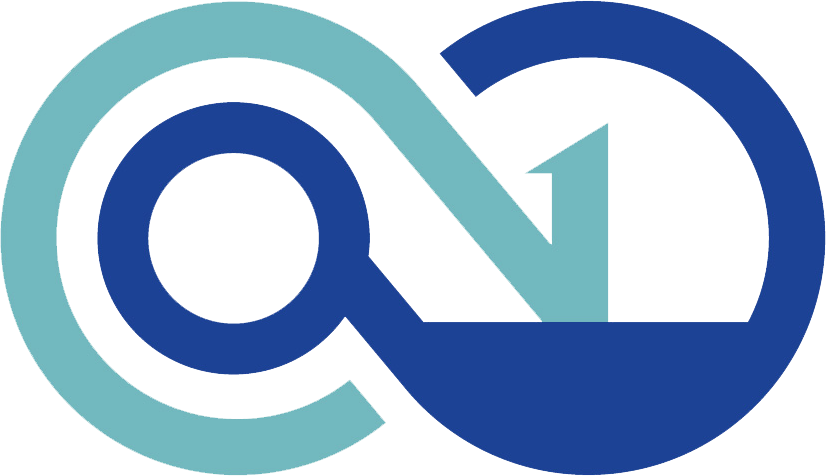