Finding the Right 8 Layer PCB Manufacturer: A Comprehensive Guide
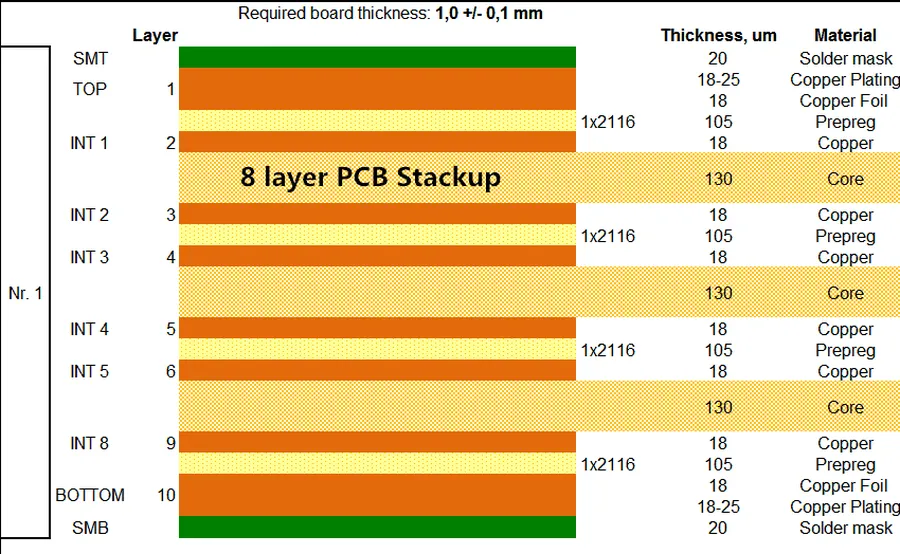
In our interconnected world, advanced electronics are powered by increasingly complex circuit boards. The 8-layer PCB, a workhorse for many sophisticated devices, requires precision and expertise in manufacturing. Much like a well-orchestrated symphony relies on each instrument, an efficient 8-layer PCB ensures harmonious functioning in critical applications. This guide serves as a beacon to navigate the landscape of 8 layer PCB manufacturers, ensuring you select a partner who understands your intricate needs.
Understanding 8 Layer PCBs and Their Applications
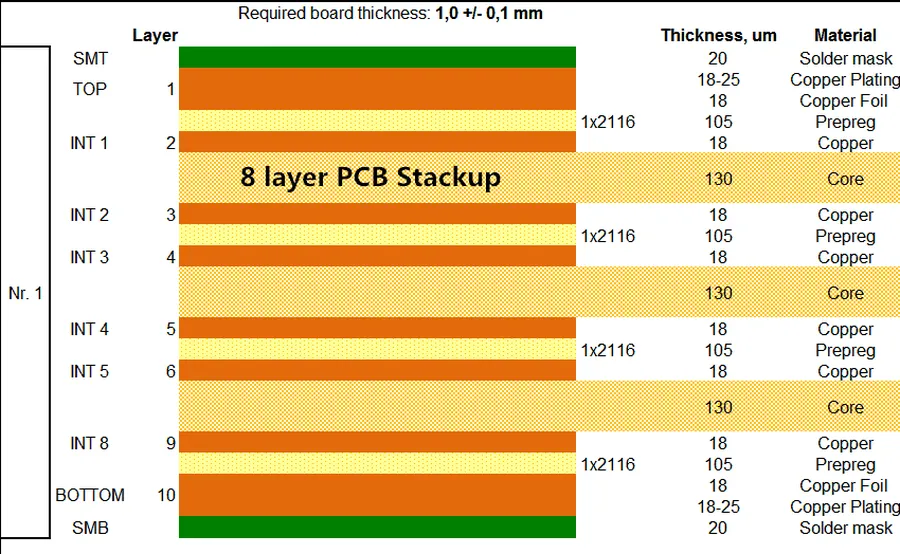
An 8-layer printed circuit board (PCB) is a sophisticated multi-layer structure, characterized by eight conductive layers of copper circuitry embedded within a stack of insulating substrate material. These boards offer a significant leap in complexity and performance compared to single or double-layer designs, enabling advanced electronic functionality. The increased layer count allows for enhanced routing flexibility, improved signal integrity, and greater component density.
Feature | Single-Layer PCB | Double-Layer PCB | 8-Layer PCB |
---|---|---|---|
Number of Conductive Layers | 1 | 2 | 8 |
Routing Flexibility | Limited | Moderate | High |
Signal Integrity | Low | Moderate | High |
Component Density | Low | Moderate | High |
Complexity | Low | Medium | High |
Cost | Low | Medium | High |
Typical Applications | Simple Electronics | Consumer Electronics | Industrial, Medical, Aerospace |
The complexity of an 8-layer PCB introduces new design considerations, necessitating advanced engineering techniques for optimal performance. These include precise impedance control, meticulous layer stackup to mitigate noise, and thorough thermal management to ensure reliability. Common applications of 8-layer PCBs include: * **Industrial Automation:** High-precision control systems, robotics, and sensor networks demand sophisticated circuitry. * **Medical Devices:** Imaging equipment, patient monitoring systems, and diagnostic tools benefit from enhanced signal integrity and compact form factors. * **Telecommunications:** Networking infrastructure, high-speed data transmission, and signal processing require complex routing and minimal interference. * **Aerospace and Defense:** Avionics, radar systems, and satellite communications rely on robust performance under extreme conditions. * **High-Performance Computing:** Servers, data centers, and advanced processors leverage increased signal density and thermal control for advanced applications. * **Advanced Consumer Electronics**: High-end smartphones, gaming consoles, and virtual reality headsets use 8-layer PCBs to manage complex integrated circuits and high-speed data transfer.
Key Considerations When Selecting an 8 Layer PCB Manufacturer
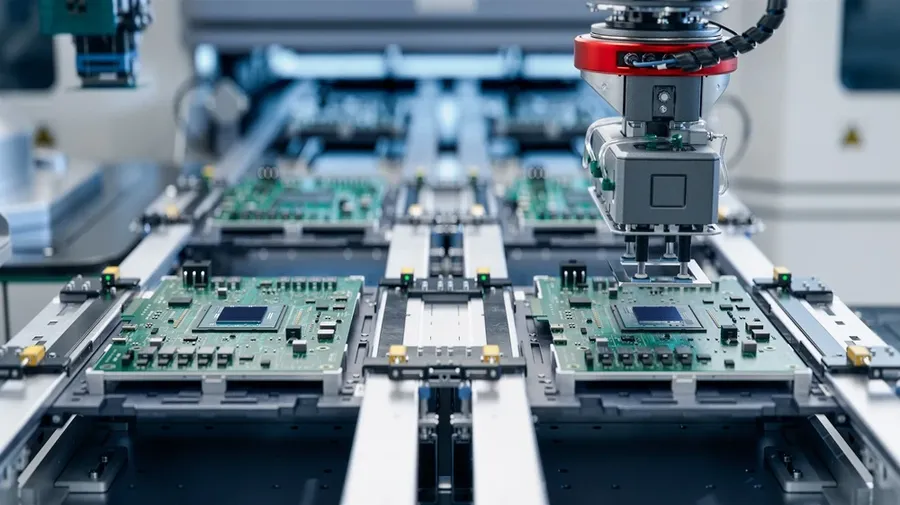
Selecting the right 8-layer PCB manufacturer is crucial for the success of any electronic product that relies on high-performance multilayer boards. This section delves into the essential factors to consider, ensuring the chosen partner can meet specific project requirements, from design complexity to final quality and reliability.
The selection process should encompass a thorough evaluation of the manufacturer's capabilities, materials, certifications and quality control processes, and lead time management. Each aspect directly influences the performance, reliability, and overall cost of the final product.
Factor | Description | Importance |
---|---|---|
Manufacturing Capabilities | Ability to produce specified trace widths, spacing, hole diameters, and via types. | Critical for achieving the desired electrical performance and design density. |
Material Selection | Options for base materials (e.g., FR-4, high-Tg FR-4) and prepreg materials. | Affects thermal performance, signal integrity, and overall board reliability. |
Certifications | Compliance with industry standards such as ISO 9001, UL, IPC standards. | Ensures the manufacturer adheres to established quality and safety guidelines. |
Quality Control Processes | Implementation of rigorous testing, including AOI, electrical tests, and functional tests. | Minimizes defects and enhances overall product quality and reliability. |
Lead Times | Expected duration from design submission to board delivery. | Directly impacts project timelines and production schedules. Shorter lead times can be advantageous, but should not compromise quality. |
Production Processes | Understanding of each step in the production process, from design review to final testing. | Ensure consistent quality and allow proper integration with the overall project pipeline. |
Top 8 Layer PCB Manufacturers: A Comparative Analysis
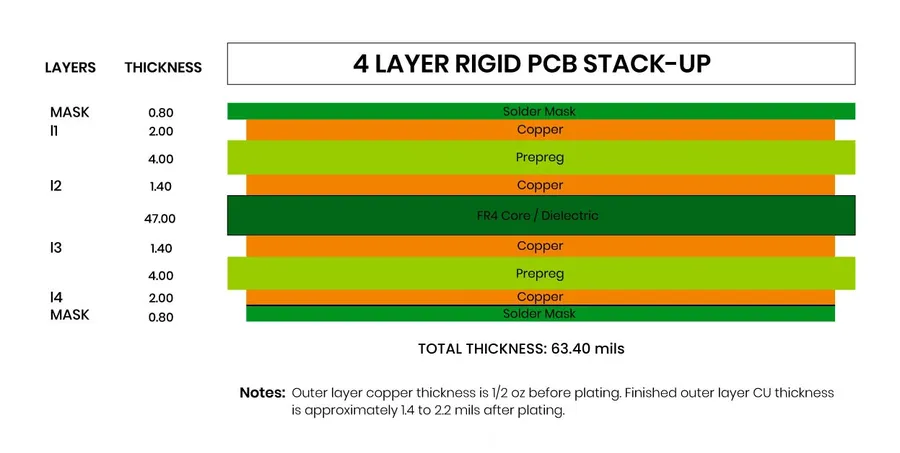
Selecting the right 8-layer PCB manufacturer is crucial for project success. This section offers a comparative analysis of leading manufacturers based on their expertise, technological capabilities, customer feedback, and pricing structures, aiming to streamline the selection process for our readers.
Manufacturer | Expertise | Technology | Customer Feedback | Pricing | Typical Lead Time |
---|---|---|---|---|---|
Manufacturer A | High reliability boards, complex designs | Advanced HDI, fine-line etching, controlled impedance | Positive, responsive customer service, good for prototyping | Premium, higher for lower volumes | 2-4 weeks |
Manufacturer B | Large volume production, cost effective solutions | Automated lines, standard material selections, wide range of surface finishes | Consistent quality, good for large orders, slightly slower response | Competitive, scalable pricing | 3-5 weeks |
Manufacturer C | Specialized in high-speed boards, RF applications | Low-loss laminates, high-precision fabrication, advanced testing capabilities | Highly skilled engineering support, preferred for specialist requirements | High, best for specific material or precision needs | 4-6 weeks |
Manufacturer D | Fast turnaround prototyping, low to medium volumes | Quick-turn capabilities, online quoting and ordering platforms | Good communication, ideal for iterating designs, occasional tolerance issues | Moderate, balanced pricing for prototypes | 1-3 weeks |
Manufacturer E | General purpose boards, consistent quality, good all rounder | Established technologies, wide range of sizes, standard PCB manufacturing process | Good support, suitable for many applications, can get busy | Moderate, fair prices | 2-4 weeks |
Note: This table provides a general overview. Specific project needs may dictate the most suitable manufacturer. It is recommended to reach out to several manufacturers to compare detailed quotations and samples to ensure optimal project fit. The typical lead times listed may vary based on specific board design and volume requirements. Pricing can vary drastically depending on project specifications.
Analyzing PCB Stackup for 8 Layer Boards
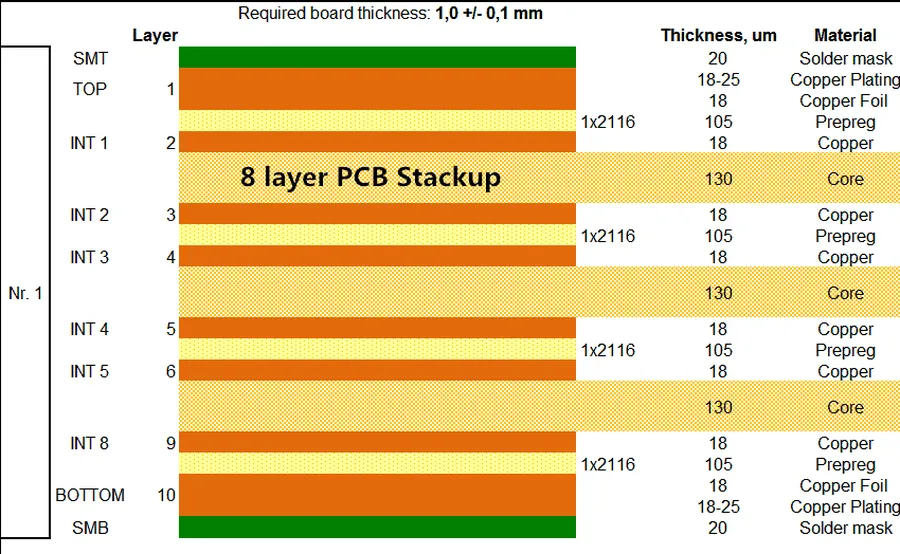
The stackup design of an 8-layer PCB is paramount for achieving optimal performance, influencing impedance control, signal integrity, and thermal management. A well-engineered stackup ensures that signal transmission is efficient, minimizing signal loss and crosstalk, while effectively managing heat dissipation. The arrangement of conductive layers and dielectric materials directly affects these critical parameters.
A skilled manufacturer plays a critical role, not only in executing the fabrication process but in advising on the optimal stackup configuration to ensure signal integrity and reliability. Understanding material properties, layer spacing, and the target application of the PCB are all essential to selecting the correct stackup for any given design.
Parameter | Impact | Consideration |
---|---|---|
Layer Arrangement | Impedance control, signal integrity, power distribution | Careful placement of signal and power layers |
Dielectric Material | Signal loss, thermal properties, cost | Selection of appropriate FR4, high-Tg, or other materials |
Layer Thickness | Impedance, manufacturing feasibility | Trade-off between impedance requirements and practical etching limitations |
Copper Weight | Current carrying capacity, heat dissipation | Matching copper weight to power requirements |
Ground Planes | Signal return paths, noise reduction | Continuous ground planes for stable return paths |
Common stackup configurations often include dedicated ground and power planes, which significantly reduce noise and provide low impedance paths, improving signal integrity. For instance, a four-signal-layer stackup with embedded power and ground planes provides a balanced approach for both signal routing and power distribution. The key to effective stackup design is a thorough understanding of the intended application and specific performance requirements of the circuit.
Considerations such as controlled impedance for high-speed signals, material selection based on thermal needs, and the number of vias required for layer transitions are critical. A manufacturer with expertise in these parameters will be able to guide a design through the process from concept through to fabrication.
Cost Factors Affecting 8 Layer PCB Production
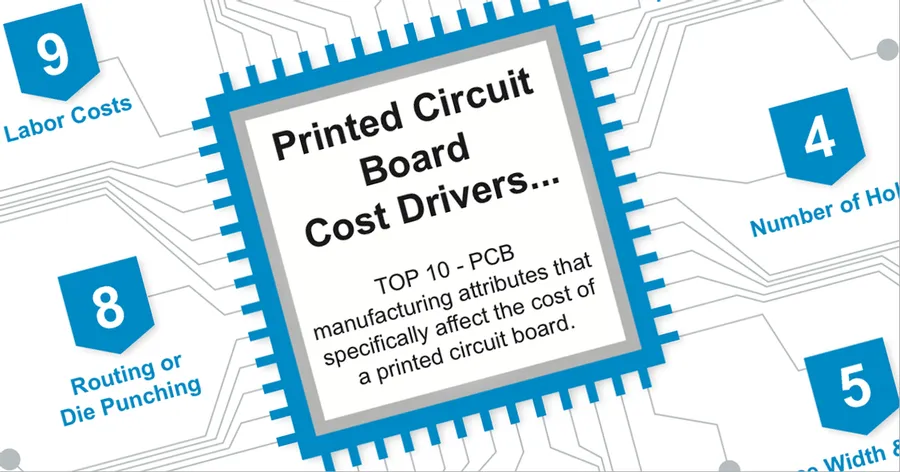
The cost of producing 8-layer PCBs is influenced by a multitude of factors, extending beyond just material costs. These drivers include design complexity, production volume, material selection, surface finish requirements, manufacturer location, lead times and desired precision, all of which contribute to the overall expense.
Cost Factor | Description | Impact on Cost |
---|---|---|
Material Costs | Type of substrate (e.g., FR-4, High-Tg), copper thickness, and prepreg materials. | Higher cost for specialized materials (e.g., high-Tg, specific laminates). Increased copper thickness also raises cost. |
Design Complexity | Number of vias, trace width and spacing, layer alignment accuracy, impedance control requirements. | Higher complexity leads to increased manufacturing difficulty, longer production times and potentially lower yields increasing cost. |
Production Volume | Quantity of boards being manufactured in a single production run. | Higher volumes generally result in lower per-unit cost due to economies of scale. Small production runs are more expensive. |
Surface Finish | Type of finish applied to the PCB (e.g., HASL, ENIG, Immersion Tin). | Premium finishes like ENIG increase cost compared to basic HASL due to the materials and processes required. |
Manufacturer Location | Geographical location of the PCB manufacturer. | Manufacturers in some regions may offer lower labor costs or reduced overhead, which leads to lower prices. Other locations may have higher production costs. |
Lead Times | Time required for the manufacturer to complete the PCB production. | Faster lead times often incur premium charges, whereas longer lead times may reduce production costs. |
Desired Precision | Manufacturing tolerances, high precision requirements. | Tighter tolerances and higher precision require more advanced manufacturing processes, and may affect yield rates thus incurring additional costs. |
Frequently Asked Questions About 8 Layer PCB Manufacturing
This section addresses common queries regarding 8-layer PCB manufacturing, providing clear and concise answers to help you navigate this complex topic. We aim to clarify key aspects, assisting you in making informed decisions when selecting a manufacturer.
- What exactly is an 8-layer PCB?
An 8-layer PCB is a printed circuit board consisting of eight conductive layers of copper, separated by insulating material (typically prepreg and core). These layers allow for complex circuit routing, improved signal integrity, and increased functionality compared to single or double-layer boards. The layers are interconnected by vias. - Who is the largest PCB manufacturer in the world?
While market share fluctuates, several manufacturers consistently rank highly in terms of volume and revenue. Identifying the absolute 'largest' can be complex due to variations in reporting and metrics. However, companies like TTM Technologies, Nippon Mektron, and Unimicron are generally considered among the leading global PCB manufacturers. - Which company manufactures PCBs?
Numerous companies around the globe manufacture PCBs, ranging from large multinational corporations to smaller, specialized firms. These manufacturers vary in their capabilities, production volume, and target markets. When choosing a manufacturer, it’s crucial to consider factors like their experience with 8-layer boards, their manufacturing technology, and their quality control processes. - Which PCB manufacturer is best for my project?
The 'best' PCB manufacturer is highly dependent on your project's specific requirements. Factors like design complexity, required precision, material specifications, desired lead time, and budget all play critical roles in choosing a manufacturer. For example, a small scale project might benefit from a vendor like JLCPCB, while higher precision and higher volume projects may demand a larger more established vendor. - What are the benefits of using an 8-layer PCB?
8-layer PCBs offer several advantages over simpler boards, including increased routing density, better signal integrity, improved power distribution, and enhanced functionality. The multiple layers allow for more complex circuits to be implemented within a smaller footprint, which can result in smaller, more efficient electronic devices. They also offer better control of impedance, leading to higher performance at speed. - How does the cost of an 8-layer PCB compare to other PCB types?
The cost of an 8-layer PCB is generally higher than that of single, double, or even 4-layer PCBs due to the increased complexity of fabrication. Factors influencing cost include material costs, the complexity of the design, drilling and plating process for vias, and the required tolerances. However, for many applications, the added cost is justified by the performance and density improvements. - What are typical lead times for manufacturing an 8-layer PCB?
Lead times for 8-layer PCB manufacturing vary depending on the manufacturer’s workload, the complexity of the board, and the specific requirements of the order. Simple prototypes may have lead times of one to two weeks, while larger production runs or more complex designs may take several weeks. It's crucial to confirm lead times with your chosen manufacturer, and include a lead time buffer in your development timeline.
The Future of 8 Layer PCB Technology
The landscape of 8-layer PCB technology is rapidly evolving, driven by the increasing demands for higher performance, greater miniaturization, and enhanced reliability in modern electronics. These advancements are crucial for supporting emerging applications in high-speed data communications, artificial intelligence, and advanced medical devices, which require robust and efficient circuit boards.
- Advanced Materials
The limitations of traditional FR-4 materials are driving research into new substrate materials with improved electrical and thermal properties. These include materials with lower dielectric constants for high-speed applications, and those with higher thermal conductivities to manage increased heat dissipation. Thermoplastic polymers and ceramics are showing promise in this area. These materials will enable faster signal transmission, reduced losses, and improved operational temperature ranges. - Enhanced Fabrication Techniques
Advanced fabrication techniques such as modified semi-additive processes (mSAP) and laser direct imaging (LDI) are becoming increasingly prevalent for manufacturing high-density interconnects (HDI) with finer traces, smaller vias, and tighter spacing. These techniques enable manufacturers to create complex circuit designs more reliably and accurately than before. This precision will lead to higher density PCBs, decreased form factor, and increased functionality within compact devices. - High-Speed Data Applications
The demand for high-speed data transfer is fueling the need for PCBs with superior signal integrity, and controlled impedance. Advanced materials, and precise stackup designs are being used to ensure optimal performance for applications such as data centers, high-speed networking, and telecommunications. Future PCB designs will focus more on signal optimization and minimal signal degradation at high frequencies. - AI and Machine Learning Hardware
The computational demands of AI and machine learning are creating a need for PCBs with high power density, efficient thermal management, and reliable performance under intense loads. Future PCBs for AI hardware are likely to incorporate advanced cooling solutions, high-performance substrates, and precise layer registration for the high density interconnections needed to support these applications. - Future Stackup Designs
Future stackup designs are expected to become more complex, requiring careful consideration of layer arrangement and material selection to optimize for both electrical and thermal performance. These designs will incorporate more advanced features like microvias, via-in-pad, and back-drilling to improve signal integrity and reduce signal loss. The focus of stackup design will be to push the limits of performance and miniaturization. - Alternative Substrates
Beyond traditional FR-4, alternative substrate materials such as PTFE (Teflon), polyimide, and ceramic materials are gaining attention for their specific performance advantages. PTFE, for instance, provides lower dielectric loss for high-frequency applications, while ceramic substrates excel in thermal management. The adoption of these specialized substrates will be tailored to specific needs in high-performance applications.
Practical Tips for Working with Your 8 Layer PCB Manufacturer
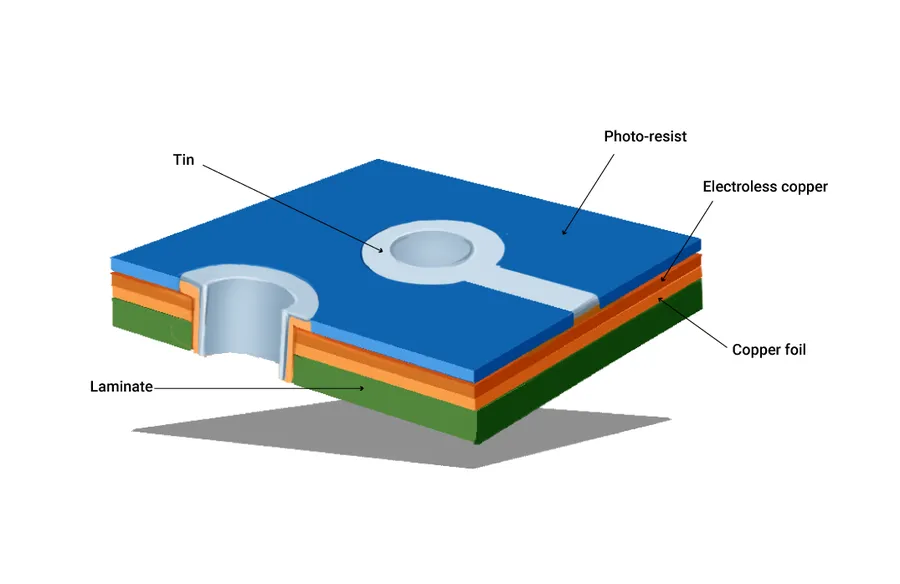
Effective collaboration with your 8-layer PCB manufacturer is paramount to achieving high-quality, on-time, and within-budget production. This section provides actionable strategies for enhancing communication, ensuring file accuracy, and implementing quality control checkpoints throughout the development process.
- Establish Clear Communication Channels
Define primary contacts on both sides and establish preferred methods of communication (email, phone, project management software). Regular updates and open discussions are vital for addressing potential issues promptly. - Provide Comprehensive Design Files
Submit complete and accurate design files, including Gerber files, drill files, bill of materials (BOM), and any necessary fabrication notes. Adhere to the manufacturer’s preferred file formats and naming conventions. - Review Design Rules and Specifications
Thoroughly review the manufacturer’s design rule check (DRC) and design for manufacturability (DFM) guidelines. Ensure your design complies with these specifications to avoid manufacturing delays and additional costs. - Clarify Material and Finish Requirements
Specify the desired materials, such as FR-4 or high-Tg options, copper thickness, and surface finishes (e.g., ENIG, HASL). Clearly define any special requirements to ensure appropriate material handling during manufacturing. - Incorporate Test Points
Include adequate test points in your design to facilitate electrical testing. This will help to identify any potential manufacturing errors or functional defects early in the process. - Implement Quality Assurance Checkpoints
Schedule quality control checks at various stages of the production process, including first article inspection (FAI), in-process inspections, and final functional testing. Document and address any deviations from the specifications. - Maintain Consistent Documentation
Keep detailed records of all communication, design revisions, and test results. This documentation will be invaluable for troubleshooting and future reference. Use version control to ensure that all parties have access to the latest versions of the design files.
Choosing the right 8 layer PCB manufacturer is pivotal for ensuring the quality, reliability, and performance of your electronic devices. Much like a bridge needs careful design and construction, the success of your advanced electronics project relies on a solid partnership with an expert manufacturer. From JLCPCB's rapid prototyping to PCBTok's advanced technologies, several options cater to specific needs and budgets. Consider stackup design, material selection, and lead time, and leverage the tips provided to foster a smooth collaboration process. By understanding your needs, asking the right questions and partnering with a qualified 8 layer PCB manufacturer, you can transform your vision into a tangible and successful product.
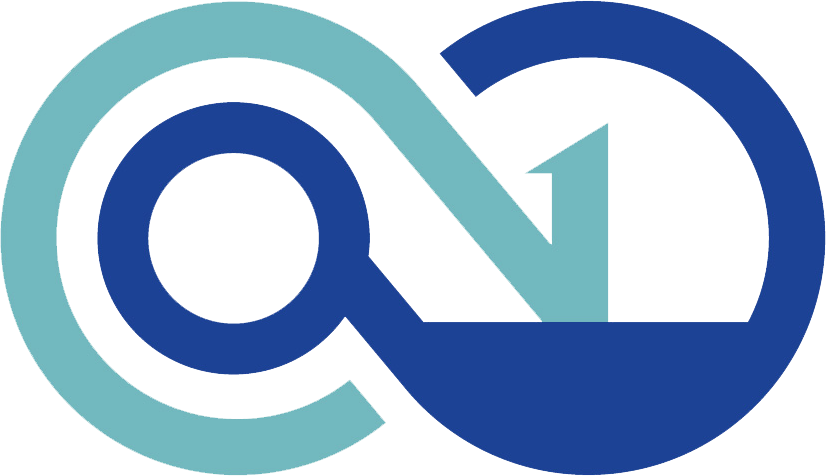