Finding the Right Local PCB Manufacturer: A Comprehensive Guide
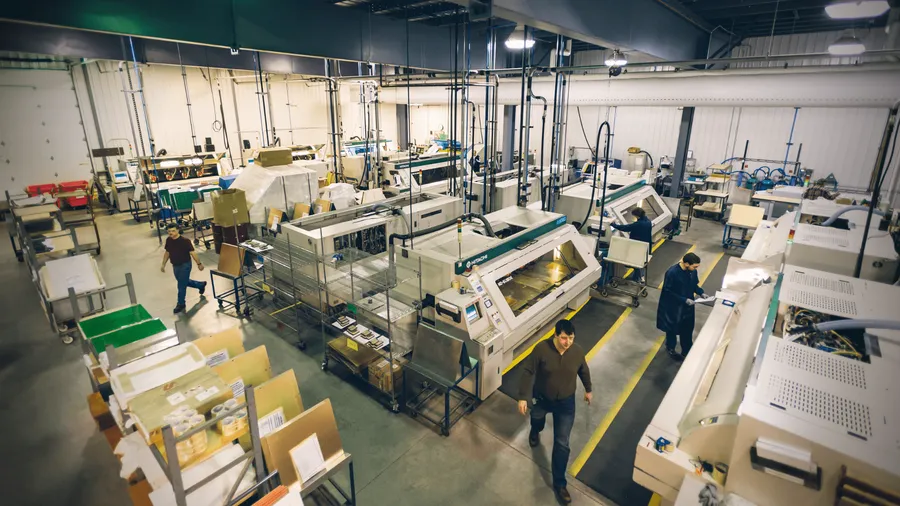
In today's tech-driven world, printed circuit boards (PCBs) are the backbone of countless electronic devices. Finding a reliable and local PCB manufacturer is crucial, whether you're an established tech company or a passionate hobbyist. This guide dives into what makes a great local PCB manufacturer and how to choose the right partner for your project.
Why Choose a Local PCB Manufacturer?
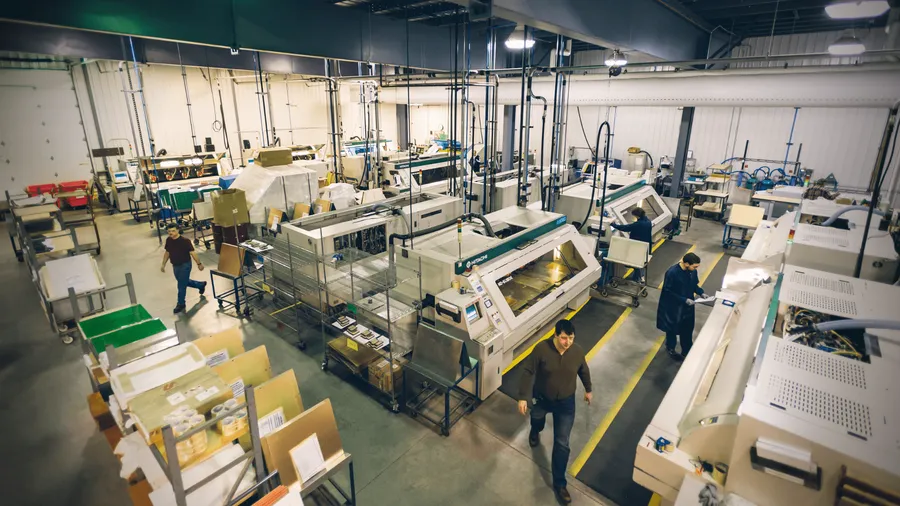
Selecting a local PCB manufacturer offers significant advantages over overseas alternatives, primarily due to enhanced control, faster turnaround, reduced logistical overhead, and improved communication throughout the production process. These benefits are crucial for projects requiring rapid prototyping, iterative design, and high levels of oversight.
- Faster Turnaround Times
Local manufacturers typically offer significantly shorter lead times compared to overseas suppliers. This is due to reduced shipping times and easier scheduling, allowing for quicker design iterations and faster project completion. - Reduced Shipping Costs
Shorter distances translate directly into lower shipping costs. This reduction in transportation expenses can significantly impact the overall budget, especially for projects requiring multiple prototype runs or larger production volumes. - Enhanced Communication
Direct and immediate communication with a local manufacturer streamlines the process. This allows for quick clarifications, faster resolution of issues, and seamless collaboration between design and production teams, ensuring that any unforeseen problem in the production process can be resolved more efficiently. - Better Control and Visibility
Working with a local partner allows for in-person visits to the manufacturing facility, providing greater insight into the production process and ensuring greater control over manufacturing quality. This level of transparency is particularly beneficial for projects with stringent quality standards. - Support for Local Economy
Choosing a local PCB manufacturer contributes to the local economy by supporting domestic businesses, creating local employment opportunities, and promoting the growth of local expertise within the electronics manufacturing sector. This also results in more accountability to local regulations and standards. - Reduced Risk of Supply Chain Disruptions
Relying on local supply chains can mitigate risks associated with international shipping delays, political instabilities, and trade regulations. This resilience in the supply chain is crucial for maintaining consistent production schedules and mitigating the impact of unexpected events.
Key Considerations When Choosing a PCB Manufacturer
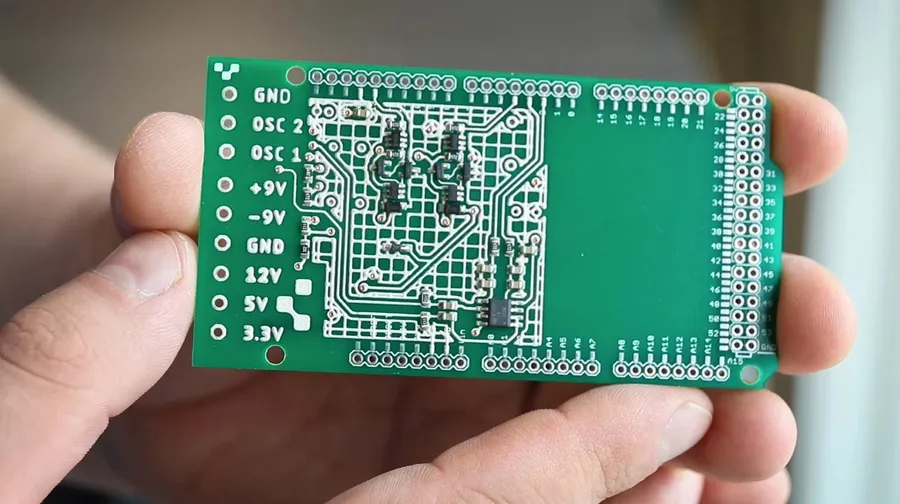
Selecting the right PCB manufacturer is crucial for the success of any electronics project. This decision hinges on a careful evaluation of several key factors that align with the specific requirements of your design and production needs. These factors encompass the manufacturer's fabrication capabilities, material expertise, assembly services, and commitment to quality assurance.
- Fabrication Capabilities
Assess the manufacturer's capacity to produce the type of PCB you require, whether it's single-sided, double-sided, or multilayer. Verify their ability to handle the complexity of your design, including the number of layers, trace width/spacing, and via requirements. Advanced designs may require specialized equipment and processes. Ensure they support your specific design rules and tolerances. - Material Expertise
Different applications necessitate different PCB materials. Common options include FR-4, which is versatile and widely used; aluminum, known for its heat dissipation properties; and flexible substrates, such as polyimide. Confirm the manufacturer has experience and certifications working with the specific material required for your project. - Assembly Services
Determine if the manufacturer provides PCB assembly services, which can save time and reduce logistical complexity. Check if they offer surface mount technology (SMT), through-hole, or mixed assembly capabilities. If assembly is needed, inquire about their component sourcing process and quality control measures. Consider the level of assembly services required (e.g., partial, full turnkey). - Quality Control Measures
Rigorous quality control is essential for reliable PCB performance. Ensure the manufacturer employs thorough inspection processes, including electrical testing (e.g., flying probe, bed of nails) and automated optical inspection (AOI). Look for certifications such as ISO 9001 or IPC standards that guarantee quality management practices. Transparency regarding their defect analysis and corrective actions is crucial.
Factor | Description | Key Questions to Ask |
---|---|---|
Fabrication Capabilities | Ability to manufacture different types of PCBs. | Can you produce single-sided/double-sided/multilayer PCBs? What are your minimum trace width and spacing capabilities? Do you support blind/buried vias? |
Material Expertise | Experience working with specific PCB materials. | Do you have experience with FR-4, aluminum, polyimide? Are material certifications available? |
Assembly Services | Provision of PCB assembly in-house. | Do you offer SMT, through-hole, or mixed assembly? What is your component sourcing process? Can you provide turnkey solutions? |
Quality Control Measures | Processes to ensure reliable PCB performance. | Do you have quality certifications? What are your inspection and testing procedures? |
Understanding Different Types of PCB Services
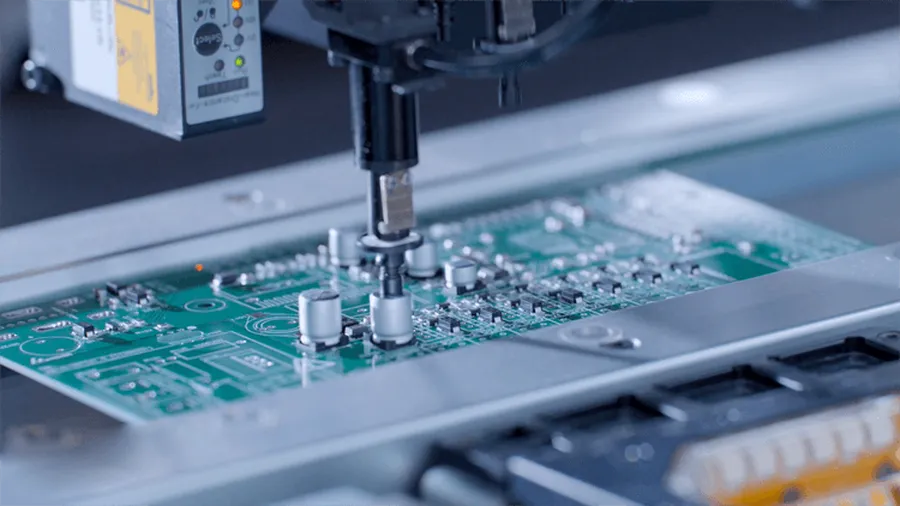
PCB manufacturers offer a range of services tailored to meet diverse project needs, typically encompassing PCB fabrication, PCB assembly, and comprehensive turnkey solutions. Understanding these distinctions is crucial for selecting the most appropriate service model for your specific requirements, ensuring both efficiency and cost-effectiveness.
Service Type | Description | Typical Applications | Key Considerations |
---|---|---|---|
PCB Fabrication | Manufacturing of the bare PCB, including etching, drilling, and plating, based on provided design files (Gerber files). | Projects where customers will perform their own component assembly; prototyping and small-batch runs. | Requires precise design files; consider lead times and capabilities of the fabricator. |
PCB Assembly | Placement and soldering of electronic components onto the bare PCB. This includes SMT (Surface Mount Technology) and through-hole assembly. | Projects where clients have a bare PCB and need components mounted; medium-volume production. | Requires a Bill of Materials (BOM) and component procurement capabilities; assess assembly capabilities and quality standards. |
Turnkey Solutions | Comprehensive service covering everything from PCB fabrication and assembly to component procurement and functional testing. | Projects where a complete solution is needed and for those wanting to save time managing multiple vendors; larger volume productions. | Offers convenience and reduced coordination overhead; evaluate end-to-end quality control and project management. |
Each of these services caters to varying levels of customer involvement and project complexities. PCB fabrication focuses solely on producing the physical board, while assembly involves populating the board with components. Turnkey solutions streamline the process by encompassing all phases from design to finished product. Choosing the correct service ensures the process is optimized for both cost and efficiency.
Cost Factors to Consider with PCB Manufacturing
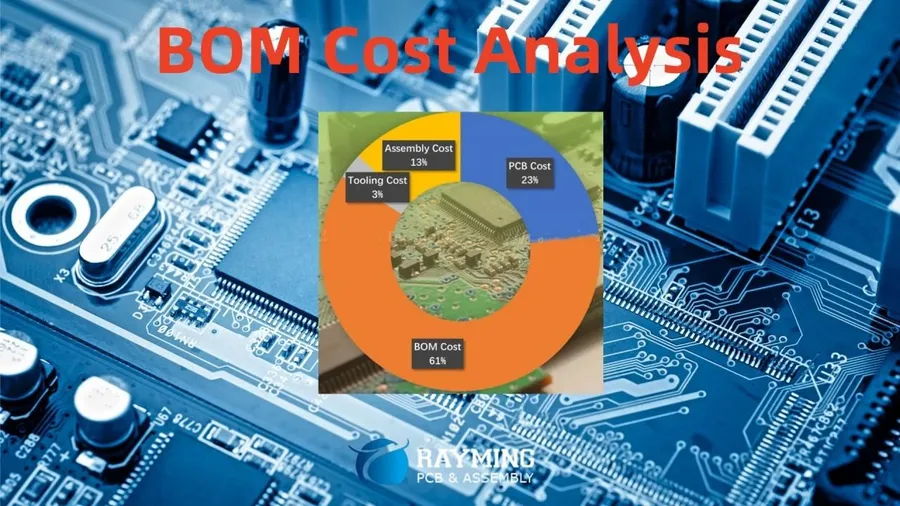
Understanding the intricacies of PCB manufacturing costs is crucial for project budgeting and financial planning. Several factors interact to determine the final price of a printed circuit board, and careful consideration of each can lead to significant cost savings without sacrificing quality.
Cost Factor | Description | Impact on Cost |
---|---|---|
Board Type | Single-sided, double-sided, or multilayer PCBs. | Multilayer PCBs are significantly more expensive due to increased complexity and materials. |
Number of Layers | The quantity of conductive layers within the PCB. | Cost increases proportionally with the number of layers. |
Materials | FR-4, aluminum, high-frequency laminates, etc. | High-performance materials like Rogers or ceramics are more costly than standard FR-4. |
Board Size | The physical dimensions of the PCB. | Larger PCBs require more material, increasing costs. |
Complexity of Design | Features like fine-pitch components, blind vias, and impedance control. | Intricate designs necessitate advanced manufacturing processes, raising costs. |
Surface Finish | Options include HASL, ENIG, immersion tin, etc. | Gold plating (ENIG) is more expensive than lead-free HASL. |
Quantity | The number of PCBs ordered. | Per-unit cost generally decreases as quantity increases due to economies of scale. |
Testing Requirements | Specific testing procedures such as flying probe, in-circuit testing. | Comprehensive testing increases the cost but enhances reliability. |
Turnaround Time | Expedited or rush production. | Faster turnaround times typically come with a premium. |
Balancing cost and quality is paramount. While opting for the cheapest options may reduce initial costs, it can lead to reliability issues and increased long-term expenses. Therefore, it is advised to collaborate with the manufacturer to optimize design choices, materials, and processes that meet performance requirements while remaining within budget.
Turnaround Time and Lead Times: What to Expect
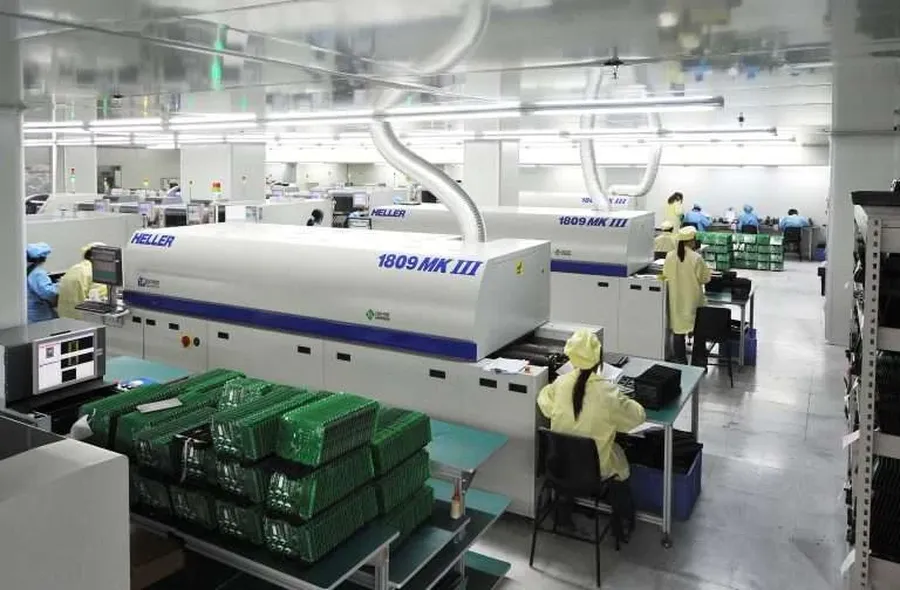
Understanding turnaround time and lead times is crucial for effective project management when sourcing PCBs. These metrics represent the duration required to complete the fabrication and assembly processes, respectively, and can significantly impact project timelines. While some manufacturers may offer expedited services for quick-turn prototypes, typical production runs will have longer lead times. Proper planning, including realistic expectations for turnaround, is therefore essential for successful PCB procurement.
Process | Typical Turnaround Time | Factors Affecting Time |
---|---|---|
PCB Fabrication | 2-10 business days | Board complexity, number of layers, material availability, manufacturer capacity |
PCB Assembly | 3-15 business days | Component availability, assembly complexity, order quantity, manufacturer capacity |
Turnkey Solutions | 5-20 business days | Combined factors of fabrication and assembly, project complexity, specific requirements |
Several factors influence both turnaround time and lead times for PCB manufacturing. These include the board's complexity (single-sided, double-sided, multilayer), the number of layers, the materials used (FR-4, aluminum, etc.), the complexity of the design, and the manufacturer's current workload. Component availability can also have a significant impact on assembly lead times. For example, a design with very specific components or materials may experience delays if those components are not readily available or have long lead times from the supplier. Moreover, the manufacturing capacity of the chosen manufacturer, such as available production lines and staff, plays an important role. Choosing a manufacturer with the capacity to meet your deadlines and requirements is crucial. In addition, a clear understanding of the manufacturer's scheduling process can help prevent bottlenecks and delays.
- Tips for Planning and Ensuring Timely Delivery
Begin by clearly defining your project timeline and communicating this to potential manufacturers. Obtain quotes from different manufacturers to understand the variance in lead times. Plan well in advance, allowing a buffer for unexpected delays. Ensure all design files are complete and accurate before submitting for fabrication to avoid rework delays. Select a manufacturer with good communication practices that keeps you updated during the process and has a reputation for meeting deadlines. Consider the manufacturer's location; local PCB manufacturers often have faster turnaround times and are more responsive.
Quality Control and Certifications for PCBs
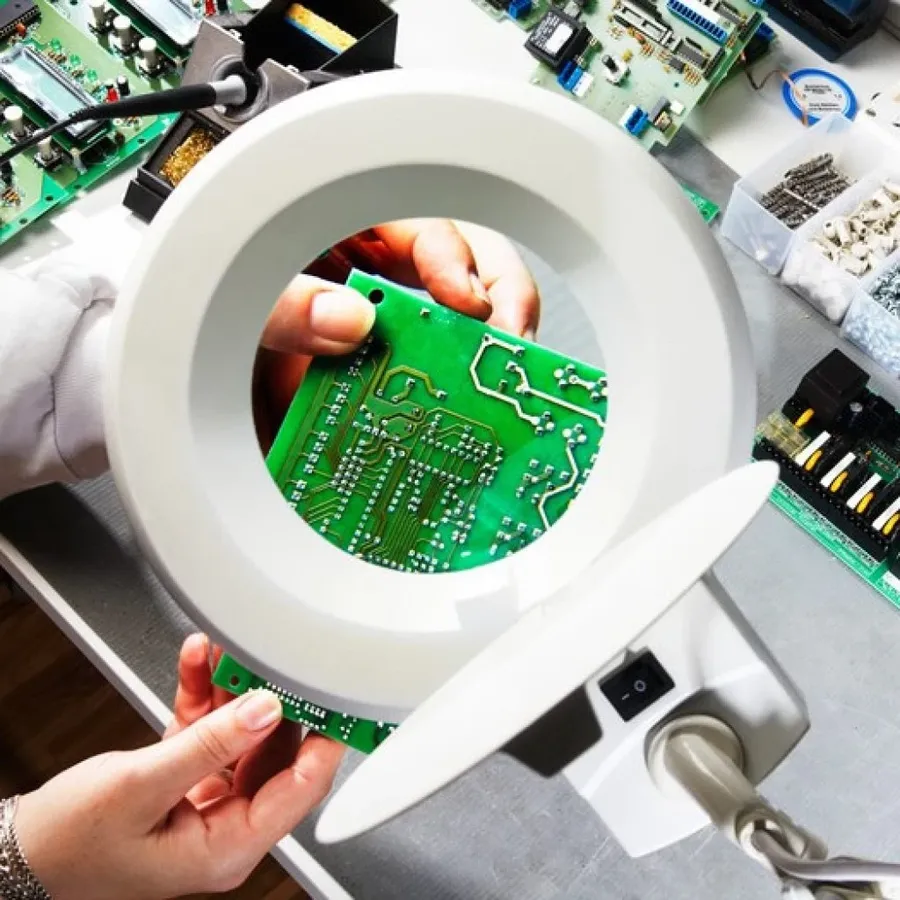
Rigorous quality control and adherence to industry certifications are paramount for ensuring the reliability and performance of printed circuit boards (PCBs). These measures guarantee that the manufactured boards meet the required specifications and perform consistently across their intended applications, minimizing risks of malfunction and costly failures.
For PCB manufacturing, adherence to established industry standards and certifications is non-negotiable. These standards dictate the acceptable levels of quality, tolerances, and testing procedures. Selecting a manufacturer that actively adheres to such standards is crucial for obtaining dependable and consistent PCBs, this also mitigates risks of potential production errors.
- IPC Standards
The IPC (Association Connecting Electronics Industries) standards are the globally recognized benchmarks for PCB design, manufacturing, and assembly. They provide guidelines for all aspects of the PCB process. For instance, IPC-A-600 defines the acceptance criteria for printed boards, and IPC-6012 specifies the performance and qualification requirements for rigid boards. Compliance with these standards ensures the quality and reliability of the manufactured PCBs. - ISO 9001 Certification
ISO 9001 is an international standard that sets out the requirements for a quality management system (QMS). PCB manufacturers with ISO 9001 certification demonstrate that they have established a formal QMS, a critical factor in maintaining quality consistency. The manufacturer will have defined procedures for controlling all the key aspects of the production process including, design review, materials management, process control, testing, and handling of non-conforming products. - UL Certification
Underwriters Laboratories (UL) certification is a safety certification that indicates that a PCB manufacturer’s products and processes have met UL’s safety standards, which are focused on fire prevention and electrical safety. This certification is particularly important for PCBs used in products that require compliance with safety regulations. UL certification can cover materials, construction, and production processes. - RoHS Compliance
The Restriction of Hazardous Substances (RoHS) directive restricts the use of certain hazardous materials, such as lead, mercury, and cadmium, in electronic equipment. RoHS compliance is a mandatory standard for most electronic products sold in the European Union and many other regions. For environmentally-responsible PCB manufacturing, choosing a manufacturer that is compliant with RoHS regulations is very important.
Besides adhering to certifications, a comprehensive quality control process should include routine inspections at various production stages, and employing both manual and automated inspections, alongside utilizing a rigorous testing process. These measures ensure the PCB adheres to the required electrical specifications and design parameters. Such measures would include optical inspection, electrical testing, and automated test equipment (ATE) to ensure each board meets the desired levels of performance and reliability. The application of these protocols is a sign of a professional PCB manufacturer.
In summary, choosing a local PCB manufacturer with strong quality control practices and relevant industry certifications like IPC standards, ISO 9001, UL certification, and RoHS compliance is essential for the reliability and consistent performance of the PCBs. These certifications provide an objective measure of the manufacturer's commitment to quality. Additionally, strong internal quality control processes are equally important for the success of your project.
Frequently Asked Questions About Local PCB Manufacturing
This section addresses common queries regarding local PCB manufacturing, providing clear and concise answers to help you navigate the process effectively. We aim to clarify key aspects related to who makes PCBs, cost factors for assembly, identifying top manufacturers, and the reasons behind PCB shortages.
- Who manufactures PCBs?
PCBs (Printed Circuit Boards) are manufactured by specialized companies that possess the equipment and expertise to fabricate and assemble electronic circuits. These manufacturers can range from small, local businesses to large international corporations. They utilize processes such as etching, drilling, and lamination to create the circuit boards that form the backbone of electronic devices. Some manufacturers also offer assembly services, placing electronic components onto the finished boards. - How much does it cost to get a PCB assembled locally?
The cost of PCB assembly varies widely depending on several factors, including the complexity of the board, the number of layers, the types of components used, the quantity of boards required, and the assembly method (SMT, through-hole, or mixed). Smaller production runs or highly complex boards tend to have higher per-unit costs. For a precise estimate, you should share your Gerber files, BOM (Bill of Materials), and assembly requirements with the manufacturer. - Who is the best local PCB manufacturer?
The "best" PCB manufacturer is subjective and depends on your specific project requirements. Factors to consider include the manufacturer's experience, the range of services offered (e.g., fabrication, assembly, testing), the quality of their products, their communication, their pricing, their location, and their adherence to quality standards and certifications. Researching online reviews, requesting quotes from multiple vendors, and asking for samples will help you determine the best local fit for your needs. - Why is there a PCB shortage?
PCB shortages have been influenced by global events, including supply chain disruptions, increased demand for electronics, material shortages, and factory closures. These factors have combined to create a bottleneck in the PCB production process, affecting availability and lead times. Additionally, the industry is experiencing increased demand from growing sectors like EVs, IoT and AI, which puts a strain on production capacity. Working closely with your local PCB manufacturer and planning lead times is critical during times of shortages. - What is the difference between PCB fabrication and PCB assembly?
PCB fabrication involves the production of the bare circuit board itself, while PCB assembly refers to placing and soldering electronic components onto the fabricated board. Fabrication creates the layers, circuits, and features, whereas assembly mounts the required parts onto the board and makes the board functional. Some manufacturers offer both services, simplifying the entire process. - What types of PCB material are available from local manufacturers?
Local PCB manufacturers typically work with various materials, including the common FR-4 (Flame Retardant 4), aluminum for enhanced thermal performance, and flexible substrates for specialized applications. The material selected affects the cost and performance of the board. Discuss your requirements with your local manufacturer so they can guide you in making the best material choice for your product. - How do I get a quote from a local PCB manufacturer?
To get an accurate quote, you'll need to provide the manufacturer with your PCB design files (Gerber files), a Bill of Materials (BOM) listing all components, the quantity of boards needed, and any special requirements. Providing accurate and complete information helps ensure you get a precise quote and reduces delays. If you do not have the Gerber files, a local manufacturer may be able to design the PCB for you with your electrical diagrams.
Choosing a PCB Manufacturer for Prototypes vs. Production Runs
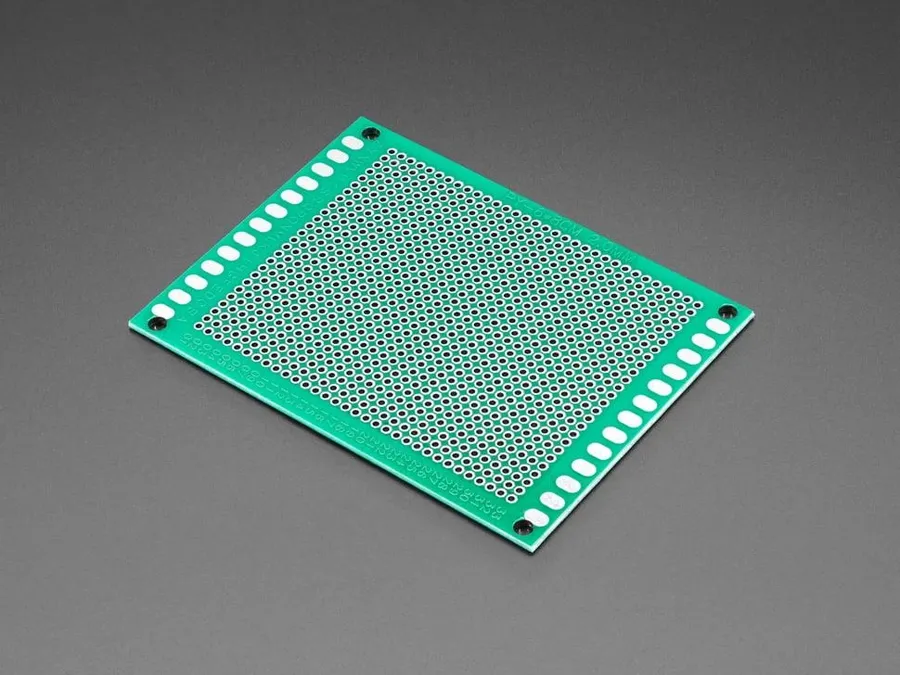
Selecting a PCB manufacturer requires different considerations depending on whether you are producing prototypes or running full-scale production. Prototypes demand flexibility and speed, while production runs prioritize cost-effectiveness and scalability. Understanding these differences is crucial for project success.
Feature | Prototype Runs | Production Runs |
---|---|---|
Volume | Low (1-100s) | High (1000s+) |
Cost per Unit | Higher | Lower |
Turnaround Time | Fast | Longer |
Design Flexibility | High | Lower |
Minimum Order Quantity (MOQ) | Lower or none | Higher |
Material Flexibility | More choice and flexibility | limited by the bulk material purchases |
Quality Focus | Early debugging and design validation | Consistent quality control |
Scalability | Less relevant | Critical |
Case Study: The Benefits of Partnering with a Local San Jose PCB Manufacturer
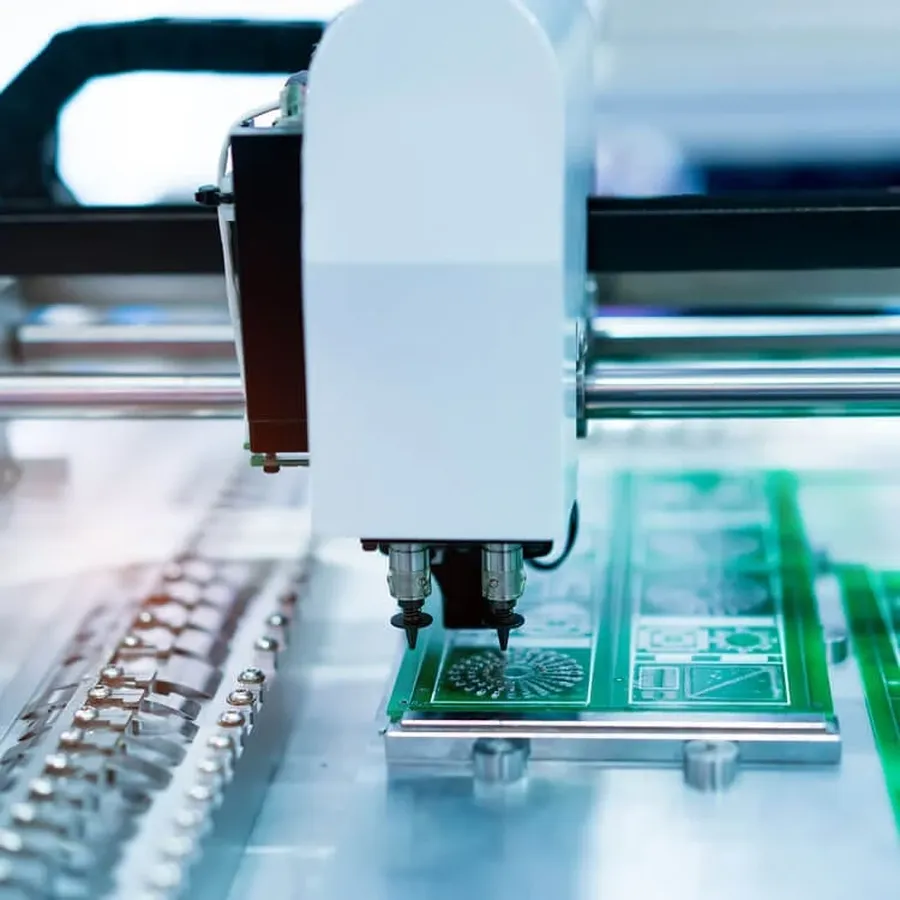
The advantages of choosing a local PCB manufacturer, particularly in a technology hub like San Jose, California, are substantial. This case study explores real-world benefits experienced by businesses that have strategically partnered with local PCB manufacturers within the Silicon Valley area, including San Jose and nearby cities. These collaborations highlight the tangible advantages of localized production, ranging from improved communication and faster turnaround times to enhanced quality control and direct collaboration.
Several case studies illustrate the benefits of partnering with local San Jose PCB Manufacturers:
- Reduced Turnaround Time for Rapid Prototyping:
A local San Jose startup developing a novel medical device needed rapid prototyping of their PCB designs. By partnering with a manufacturer within the area, they achieved a turnaround time of 48 hours for initial boards, allowing for swift design iterations and faster time-to-market. This dramatically shortened the development cycle when compared to sourcing from overseas, which could take several weeks and require iterative international shipping. - Enhanced Collaboration and Design Optimization:
A Bay Area robotics firm collaborated directly with a local manufacturer to optimize a complex multi-layer PCB design. The close proximity enabled frequent in-person meetings with the manufacturing team, leading to design refinements that enhanced performance and reduced manufacturing costs. This level of collaborative design was enabled by the geographical proximity. - Improved Communication and Real-Time Issue Resolution:
A local technology company producing industrial sensors experienced an unforeseen issue during the assembly process. Having a local manufacturer allowed for immediate on-site consultation and issue resolution, minimizing production downtime. This quick response was critical for maintaining timely project delivery, and avoided potential delays related to time-zone and communication barriers. - Cost Savings Through Reduced Shipping and Logistics:
A San Jose-based electronics firm significantly reduced shipping costs and time by sourcing PCB manufacturing locally. They also mitigated potential risks of international shipping damages and lengthy customs procedures, thereby decreasing potential disruptions to their product line.
These examples demonstrate the clear benefits of partnering with a local PCB manufacturer in San Jose and the broader Silicon Valley. The advantages range from faster prototype development, improved design collaboration, and quicker issue resolution to reduced shipping costs and lead times. For companies operating in this region, these localized benefits can be critical to their success.
Selecting the right local PCB manufacturer is essential for the success of any electronics project. By carefully considering factors like location, services, cost, quality control, and turnaround times, and using resources like San Francisco Circuits or Bay Area Circuits, you can ensure that your PCBs meet your specific requirements and achieve optimal performance. Partnering with a local manufacturer offers the benefits of closer communication, faster turnaround times, and a greater understanding of your project's needs, all while supporting local economies.
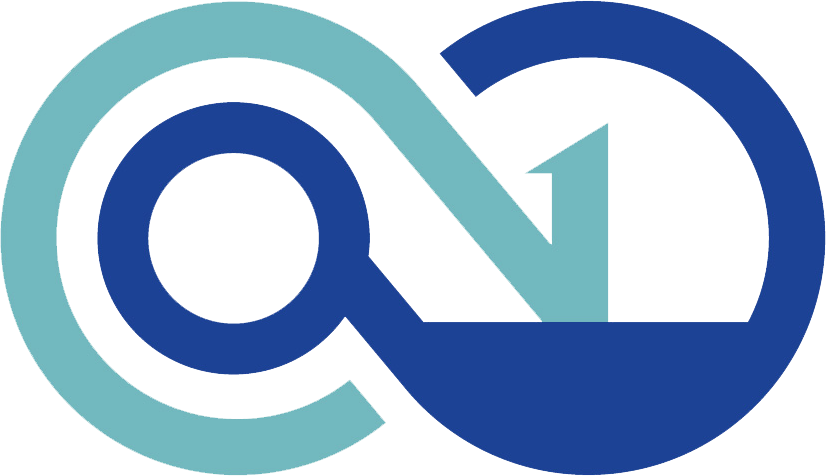