Finding the Right Low Quantity PCB Manufacturer: A Comprehensive Guide
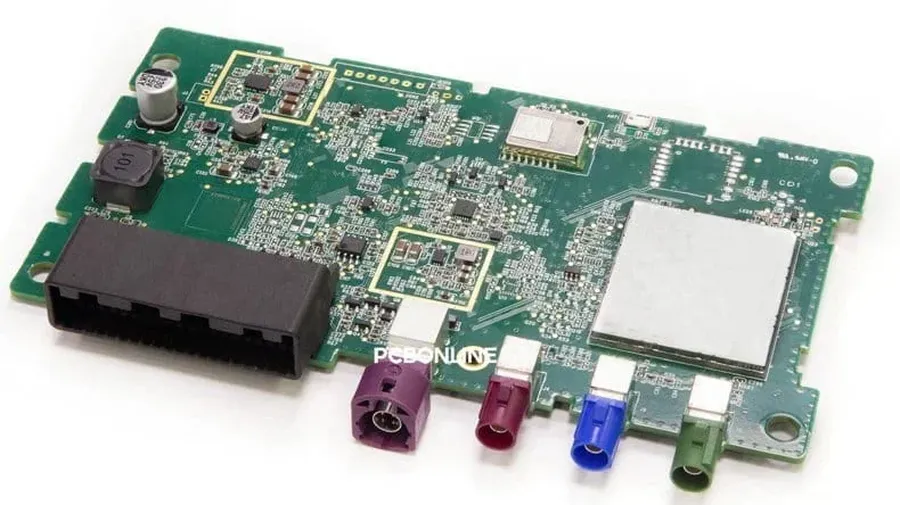
In today's rapidly evolving electronics landscape, the demand for low quantity PCB production has surged, particularly for prototypes, niche products, and startups. This need for agile, cost-effective manufacturing has made finding the right low quantity PCB manufacturer crucial for innovation and rapid product development. This article provides a comprehensive guide to navigating the world of low-volume PCB production, helping you understand the key considerations and choose the best partner for your project.
Understanding Low Quantity PCB Manufacturing
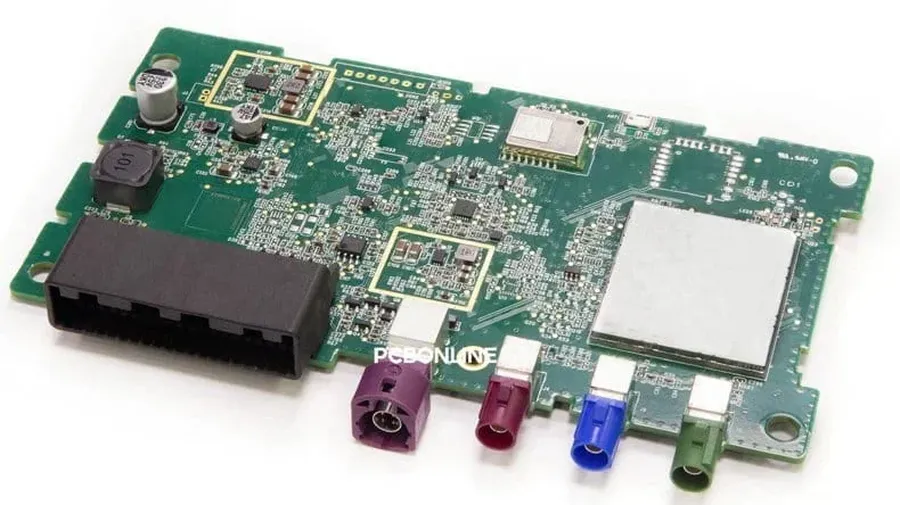
Low quantity PCB manufacturing refers to the production of printed circuit boards in small batches, typically ranging from a few units to a few hundred. This approach contrasts sharply with mass production, where thousands or millions of PCBs are manufactured. The economics, processes, and priorities of low-quantity production differ significantly, making it suitable for prototyping, specialized projects, and niche applications.
- Quantity Range
Low quantity generally encompasses runs from a single board up to a few hundred units. - Pricing Impact
Per-unit costs in low-quantity runs are higher due to setup costs and less efficient economies of scale. - Lead Times
Lead times for small batches can sometimes be shorter than mass production, particularly for prototype runs and fast-turn services. - Application Focus
This type of manufacturing is often favored for research and development, customized devices, and low-volume commercial products.
Key Factors to Consider When Choosing a Low Quantity PCB Manufacturer
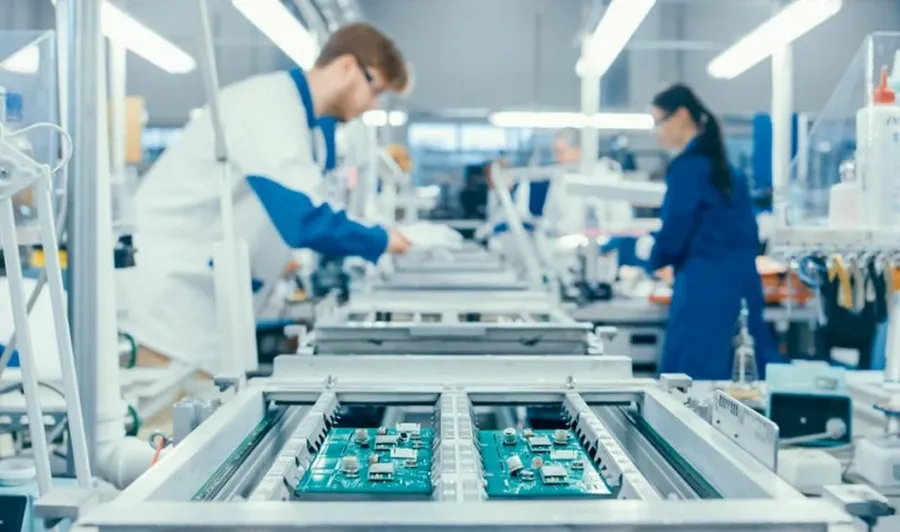
Selecting the right low quantity PCB manufacturer requires careful consideration of several crucial factors that directly impact the cost, timeline, and quality of your final product. These factors involve inherent trade-offs, necessitating a balanced approach tailored to your specific project requirements.
- Cost
The price per PCB is often the primary consideration. Low quantity production typically incurs higher unit costs compared to mass production due to setup fees and smaller economies of scale. It's important to obtain detailed quotes that include all potential costs – not just board fabrication, but also tooling, testing, and any additional services. Compare quotes thoroughly and consider the overall value offered, rather than solely focusing on the lowest price. The cheapest option may compromise on quality or lead times. - Lead Time
Lead time is the total time required from placing an order to receiving the finished PCBs. For low quantity runs, the lead time can vary significantly depending on the manufacturer's production capacity, material availability, and the complexity of the design. Manufacturers offering quick-turn or rush services often charge a premium, but these may be essential for time-sensitive projects. Assess your project timeline and choose a manufacturer that can reliably meet your deadlines. It's also crucial to understand if the manufacturer quotes turnaround time based on working days or calendar days. - Quality Standards (IPC Class)
Quality should never be compromised, even in small quantity orders. PCB quality standards are often defined by the IPC (Association Connecting Electronics Industries) classes, such as Class 2 for general electronics and Class 3 for high-reliability applications. Ensure your manufacturer can meet the required IPC class standard for your project, this ensures the performance and reliability of your electronic device. Certifications can also give confidence in their process control and quality standards. - Assembly Services (SMT, Through-Hole, Mixed)
Consider whether the manufacturer offers the required assembly services. Surface Mount Technology (SMT) is common for modern designs, while Through-Hole technology is often used for larger components. Some projects require mixed technology assembly combining both. Check the manufacturer's capabilities in component placement accuracy, soldering techniques, and testing procedures to ensure quality and compatibility with your PCB design. If you're providing components, understand the manufacturer's process for handling customer-supplied components. - Component Sourcing
If you need components sourced for assembly, check whether the manufacturer offers this as a service. If so, evaluate their supplier network, component sourcing capabilities, and pricing. Sourcing components through the manufacturer can simplify the process, but it’s vital to ensure they use high-quality components from reputable vendors. If you are providing your own components, ensure that the manufacturer's component handling process is transparent and appropriate. - Geographical Location
The geographical location of the manufacturer affects shipping costs and lead times. Domestic manufacturers may offer faster shipping and easier communication, but could also come with a higher cost. International manufacturers might be more cost-effective, but may have longer shipping times and potential language barriers. Consider the legal and intellectual property considerations associated with working with international manufacturers. It's also essential to factor in import/export duties.
Types of Low Quantity PCB Assembly Services
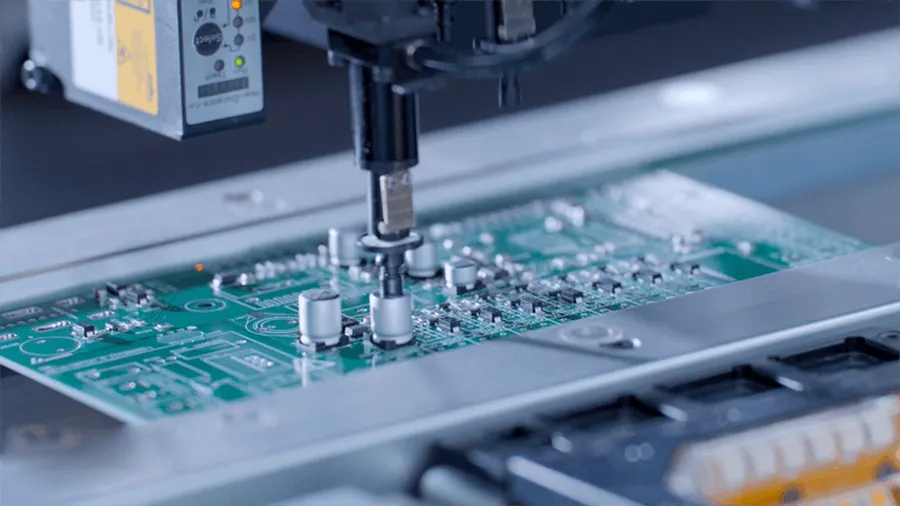
Low quantity PCB assembly encompasses several methods, each with distinct characteristics impacting cost, turnaround time, and suitability for different applications. Understanding these differences is crucial for selecting the most appropriate assembly approach for your project, especially when dealing with smaller production volumes.
The primary methods include Surface Mount Technology (SMT), Through-Hole Technology (THT), and Mixed Technology assembly. Each offers a unique set of advantages and disadvantages that designers must carefully consider when specifying their assembly requirements.
Assembly Type | Description | Advantages | Disadvantages | Typical Use Cases |
---|---|---|---|---|
Surface Mount Technology (SMT) | Components are mounted directly onto the surface of the PCB. Automated process. | High component density, miniaturization, good for mass production, lower cost in volume, relatively faster assembly. | Requires specialized equipment and expertise, can be challenging for manual rework, not ideal for large or high-power components. | Consumer electronics, portable devices, high-density circuits where miniaturization is paramount. |
Through-Hole Technology (THT) | Components have leads that are inserted into holes in the PCB and soldered on the other side. | Stronger mechanical connections, easier for manual rework, suitable for larger or high-power components, more robust than SMT. | Lower component density, larger board size, often more labor-intensive assembly, less suitable for mass production. | Power supplies, industrial control systems, applications requiring high reliability and mechanical strength. |
Mixed Technology | Combines both SMT and THT components on the same PCB. | Flexibility to use the best technology for each component type, utilizes the advantages of both SMT and THT, suitable for complex designs. | More complex assembly process, requires both SMT and THT equipment, higher cost than using only one technology, more complex logistical considerations. | Complex electronic systems, embedded systems, prototype boards where flexibility is key. |
Low-volume assembly presents unique challenges such as managing minimum order quantities for components, ensuring quality with less automation, and optimizing processes for frequent changeovers.
A Comparison of Popular Low Quantity PCB Manufacturers
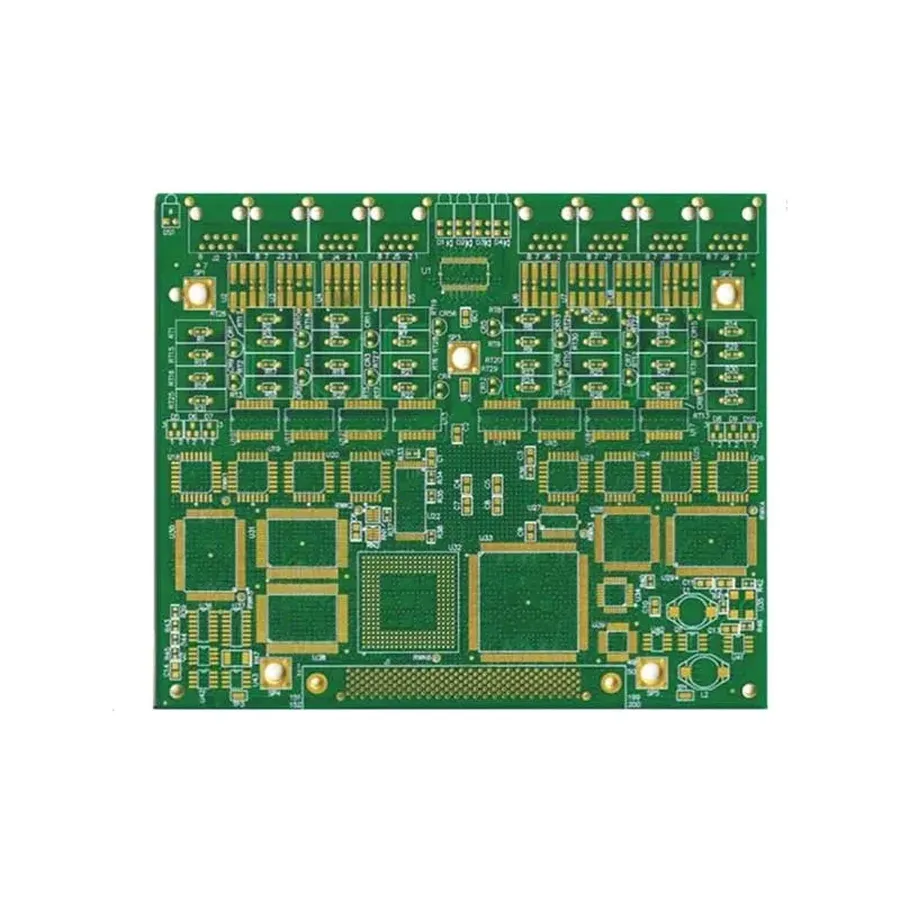
Selecting the right low quantity PCB manufacturer is crucial for project success. This section provides a comparative overview of several well-known manufacturers, focusing on key factors like cost, lead time, service quality, and special offers. While this comparison is not exhaustive due to the dynamic nature of the market, it aims to provide a useful starting point for your decision-making process.
Manufacturer | Typical Lead Time | Price Point | Service Quality | Special Offers | Notes |
---|---|---|---|---|---|
PCBWay | 2-7 days (prototyping) | Competitive | High | New user coupons, discounts for volume | Known for fast turnaround on prototypes and a broad range of services. |
JLCPCB | 3-10 days (prototyping) | Very Competitive | Good | Regular promotions, cost-effective for small runs | A very popular choice for affordable prototyping and low volume production. |
Other (e.g., local manufacturers) | 1-14 days | Variable | Variable | May offer personalized service or custom options | Consider local manufacturers for faster service or specialized needs but price can vary greatly. |
Cost-Effective Strategies for Low Quantity PCB Production
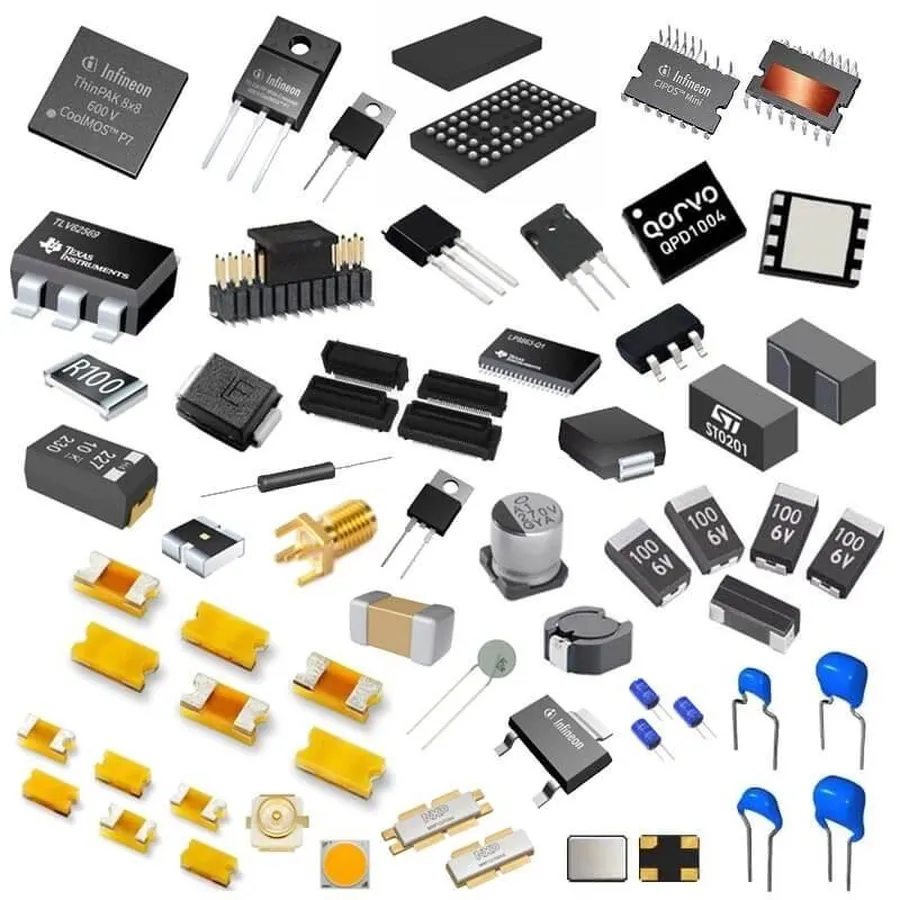
Minimizing costs in low quantity PCB production requires a strategic approach that extends beyond simply finding the cheapest manufacturer. It involves optimizing design choices, material selection, and production strategies to achieve the desired balance of cost, performance, and quality.
- Optimize PCB Design
Efficient PCB design is paramount in reducing production costs. Reducing the number of layers, using standard component footprints where possible, and minimizing the board area can substantially lower costs. It is important to consider design complexity and its impact on manufacturing costs early in the design phase, as complex designs require more processing time and resources, thus increasing overall cost. Avoiding unnecessary vias and tight spacing that require finer tolerances will help reduce manufacturing costs. - Select Cost-Effective Materials
The selection of PCB materials has a significant impact on cost. While high-performance materials such as Rogers or Taconic offer superior electrical and thermal properties, standard materials like FR-4 are often more cost-effective and suitable for most applications. Careful consideration of the required material properties ensures that the best-suited material is used, allowing for the balance between cost and performance. Choosing standard thicknesses also helps. - Panelization and Combining Orders
Panelizing multiple boards into a single manufacturing panel can reduce material usage and processing costs by maximizing the use of a single manufacturing panel. This is especially effective when producing multiple copies of the same design or different designs that fit together in a panel. Similarly, combining your orders with others to form a larger batch can lower the cost per board by taking advantage of the economies of scale that come from larger manufacturing runs. This often involves being a bit more patient with the production schedule, but the cost savings can make it a worthwhile trade-off. - Utilize Open-Source Resources
Leveraging open-source PCB design software and resources can reduce upfront costs associated with licensing expensive tools. Numerous free or low-cost software options are available, allowing for a budget-conscious approach to PCB design. Furthermore, open-source hardware libraries can help reduce design time by utilizing pre-existing footprints. - Design for Manufacturability (DFM)
DFM is a key strategy for minimizing manufacturing costs by ensuring that the PCB design is easy to manufacture. This involves following design guidelines, such as maintaining sufficient clearances and using standard component sizes. By adhering to DFM principles, potential issues during production can be avoided which can reduce the cost of troubleshooting and rework. It also reduces the potential of mis-aligned layers, and other manufacturing defects.
Turnaround Time Considerations for Small Batch PCB Manufacturing
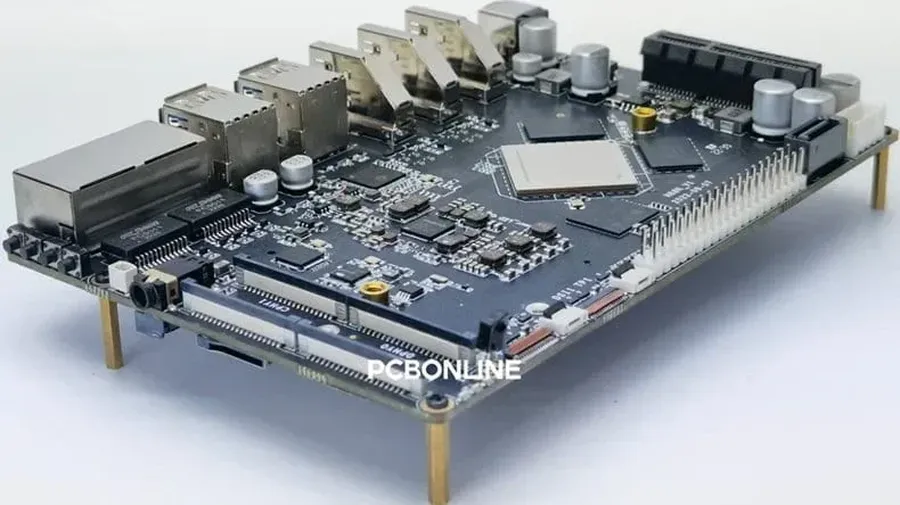
Turnaround time, or lead time, in low-quantity PCB manufacturing is the period from when a manufacturer receives your design files to when the finished boards are shipped. This critical factor is influenced by several variables, including the complexity of the PCB design, material availability, and the manufacturer's production capacity. Understanding these influences and planning accordingly is paramount to avoiding project delays.
The complexity of the design significantly affects lead time. A simple single-layer PCB will have a shorter lead time compared to a complex multi-layer board with intricate routing, vias, and special material requirements. Manufacturers typically optimize their processes for common configurations. When dealing with complex boards, additional time is allocated for specialized tooling, processing, and quality checks. Similarly, the selection of materials, especially for specialized applications, may impact lead times due to the availability of such materials from suppliers.
The manufacturer’s capacity is another critical factor impacting lead times. Smaller manufacturers with less capacity might have longer standard lead times. Conversely, manufacturers with high production volume and well-defined workflows can often offer quicker turnaround times. The number of projects currently in queue affects available machine time and resource availability, thereby impacting the overall production time. It's crucial to inquire directly with manufacturers for precise lead times based on the specific project requirements.
For projects with strict deadlines, manufacturers often provide quick-turn or rush services. These expedited options come with increased costs due to the need to prioritize the order, potentially disrupting established production schedules, and require manufacturers to operate outside of normal work hours. However, they can be necessary to ensure time-sensitive projects adhere to deadlines. It is essential to understand the implications of both standard and quick-turn options during the planning phase of a project.
To mitigate potential delays, consider these best practices when planning a timeline for a low-quantity PCB project: Firstly, allow ample time for design finalization to avoid unexpected changes that delay production. Secondly, discuss timelines and capacity with the manufacturer early in the process. Thirdly, establish clear communication channels, and regularly check in with the manufacturer on progress, addressing any potential delays proactively. By adhering to these guidelines, PCB fabrication projects can be effectively managed, avoiding unnecessary delays and extra costs.
Frequently Asked Questions about Low Quantity PCB Manufacturing
Navigating the landscape of low quantity PCB manufacturing can raise numerous questions. This section addresses common concerns, offering practical insights to optimize your experience, covering turnaround times, material availability, and achieving the best possible finish, all while balancing cost and quality.
- What is the typical turnaround time for low quantity PCB orders?
Turnaround times for low quantity PCB orders can vary significantly depending on several factors, including the manufacturer's production capacity, the complexity of the PCB design, and material availability. Standard lead times generally range from a few days to a couple of weeks. However, many manufacturers offer expedited 'quick-turn' services for an additional fee, which can reduce lead times significantly, sometimes to as little as 24-48 hours. - Are there any current PCB material shortages affecting low quantity orders?
While global supply chains are dynamic, occasional shortages of specific materials can affect PCB manufacturing. It is recommended to proactively communicate with your manufacturer to check the availability of essential components and materials. Consider alternative materials when appropriate; these options might be more readily available and potentially more cost-effective. - How can I achieve the best surface finish for my low quantity PCBs?
Achieving the desired surface finish depends on the PCB's intended application. Options include HASL (Hot Air Solder Leveling), ENIG (Electroless Nickel Immersion Gold), and Immersion Tin. ENIG provides excellent solderability and is ideal for fine-pitch components, while HASL is generally more cost-effective. Consider the trade-offs between cost, durability, and solderability when selecting your surface finish. Check your manufacturer's capabilities as not all may offer the complete range of finishes. - How can I optimize cost without compromising quality in low quantity PCB production?
Several strategies can help optimize costs for low quantity PCB production without sacrificing quality. These include: 1. Optimizing your PCB design by minimizing the number of layers and via holes, as well as using standard component footprints, 2. Combining your orders with others to get better bulk pricing, if possible, 3. Engaging with the manufacturer early to receive design recommendations and to catch manufacturability errors, 4. Selecting cost-effective materials that meet your design specifications without over engineering, 5. Considering panelization when feasible to save money per board. - How can I expedite the turnaround time for my low quantity PCB order?
To expedite your low quantity PCB order, consider: 1. Choosing a manufacturer that offers quick-turn or rush services, 2. Ensuring all design files and BOM (Bill of Materials) are accurate and error-free, 3. Choosing standard material choices when possible, 4. Communicating frequently with the manufacturer to promptly address any potential issues, 5. Confirming a clear timeline with the manufacturer before initiating production. It is important to be aware that expedited services usually incur additional costs. - What are the common challenges associated with low-volume PCB assembly?
Challenges associated with low-volume PCB assembly include: 1. Higher per-unit cost due to the lack of economies of scale, 2. Sourcing issues for small quantities of components, 3. Setup costs and longer lead times compared to mass production, 4. The need for precise component placement and careful manual assembly to minimize defects, 5. Ensuring consistency and quality across all boards. Careful planning, selecting the right manufacturer, and meticulous execution will greatly reduce potential problems. - What file formats are required by most PCB manufacturers?
Most PCB manufacturers require Gerber files, which are industry-standard files containing all the necessary data for your PCB's layers, traces, pads, and more. You'll typically also need a drill file, a bill of materials (BOM), and optionally a centroid file for pick-and-place machines during assembly. Confirm with your chosen manufacturer for their exact requirements, as some may accept other formats. Submitting accurate and complete files is crucial for a smooth manufacturing process.
Tips for a Smooth Low Quantity PCB Assembly Process
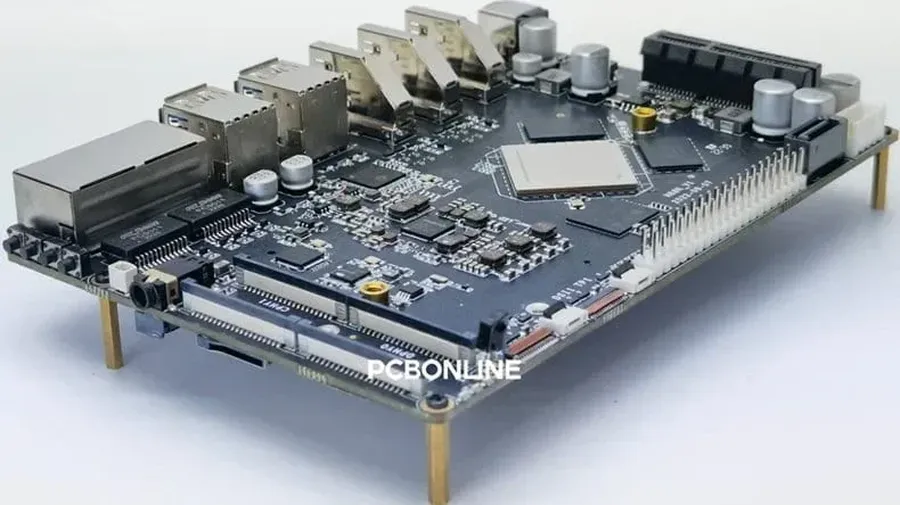
Ensuring a smooth low-quantity PCB assembly process requires meticulous planning, clear communication, and rigorous quality checks. By focusing on proactive measures in file preparation, manufacturer collaboration, and inspection protocols, you can significantly reduce the risk of delays, errors, and unnecessary costs.
- Prepare Manufacturing Files Meticulously
Generate Gerber files accurately and completely. Double-check all layers (copper, solder mask, silkscreen, drill) and ensure they match your design specifications. Include a drill file (Excellon format) and any necessary fabrication notes. Verify that the file names and formats are consistent with manufacturer requirements. - Communicate Effectively with the Manufacturer
Establish clear lines of communication with your chosen manufacturer. Clarify your project requirements, including material specifications (e.g., FR-4 thickness, copper weight), tolerances, finish requirements, and desired IPC class. Ask questions about any potential design issues or manufacturing constraints, and respond to manufacturer inquiries promptly. Provide a bill of materials (BOM) that is accurate, detailed, and includes part numbers and manufacturer information. - Optimize Your PCB Design for Manufacturability (DFM)
Adhere to the manufacturer’s DFM guidelines, which may include minimum trace widths, clearances, via sizes, and pad sizes. DFM also includes proper component placement and orientation, and providing sufficient space for assembly processes. This will reduce design revision iterations, and ensures a successful assembly process. - Verify Component Availability and Lead Times
Prior to placing an order, confirm the availability and lead times of all components on your BOM. Select alternative components if there are shortages or long lead times, where possible, or make adjustments to your designs. Communicate any component substitutions or changes to the manufacturer. - Perform Incoming Board Quality Checks
Upon receiving the manufactured boards, conduct thorough visual inspections for any defects, including misaligned layers, shorts, opens, or damaged pads. Measure dimensions against the design specifications. If your capabilities allow, conduct electrical testing to verify the integrity of the circuits before assembly. - Maintain Clear Documentation
Keep detailed records of all design files, BOMs, and manufacturer communications. Use a version control system to track changes and avoid errors. This will help streamline the process and facilitate quicker turnaround time for future projects. - Implement a Process for Quality Assurance
Establish a quality assurance process at various stages. This includes performing periodic reviews of documentation, performing random inspections of completed assemblies, and implementing a feedback system where any errors or process improvements are captured. Regular review will enable manufacturers to maintain quality and improve processes.
Low Quantity PCB Manufacturer Selection Checklist
Selecting the right low-quantity PCB manufacturer is crucial for the success of your project. This checklist provides a structured approach to ensure you cover all essential aspects, from initial design to final delivery.
- Design File Preparation:
Verify that your design files (Gerber, drill, BOM) are complete, accurate, and in the correct format specified by the manufacturer. Ensure all layers are correctly defined, and component footprints match the specified libraries. - Material Specifications:
Clearly define the desired PCB material (e.g., FR-4, aluminum), thickness, copper weight, and solder mask color. Confirm that the manufacturer can provide these specifications. - Quality Standards and Certifications:
Check if the manufacturer adheres to IPC standards (e.g., IPC-A-600) and possesses necessary certifications. Understand their quality control processes and testing procedures. - Manufacturing Capabilities:
Assess the manufacturer's capabilities, especially for your specific board complexity such as number of layers, minimum trace width, via size, and board size. Ensure their equipment and processes meet your technical requirements. - Lead Time and Turnaround:
Clarify typical lead times for low-quantity orders. Consider any trade-offs between cost and speed. If needed, inquire about quick-turn or rush services. - Pricing and Payment Terms:
Obtain a detailed quote for your project, including all costs. Understand the manufacturer's payment terms, available discounts, and potential setup fees. - Component Sourcing (If Applicable):
If you require component sourcing, evaluate the manufacturer's capabilities, pricing, and availability of components. Verify their methods of ensuring component quality. - Assembly Services (If Applicable):
Determine if the manufacturer offers PCB assembly services (SMT, through-hole, mixed). Consider if their assembly services meet your project requirements and quality expectations. - Communication and Support:
Assess the manufacturer's responsiveness and communication channels. Ensure that they provide technical support and can address potential issues efficiently. - Shipping and Handling:
Understand their shipping methods and packaging procedures. Verify they take the necessary steps to protect boards from damage during transit. Confirm shipping costs and insurance, if applicable. - Sample Boards and Test Orders:
If you have concerns about quality or reliability, ask to review sample boards or place a small test order to verify their production standards before committing to a larger project.
Selecting the right low quantity PCB manufacturer is critical for the success of any project that requires small batch production. By carefully considering the key factors outlined in this article, comparing different manufacturers, and employing cost-effective strategies, you can ensure high-quality results, timely delivery, and efficient use of resources. Always remember to clearly communicate your project requirements to potential low quantity pcb manufacturers. This will help ensure that your product is successfully and efficiently produced. Whether you're prototyping a new design or producing a limited run of specialized hardware, choosing the right manufacturing partner is the first step towards achieving your goals.
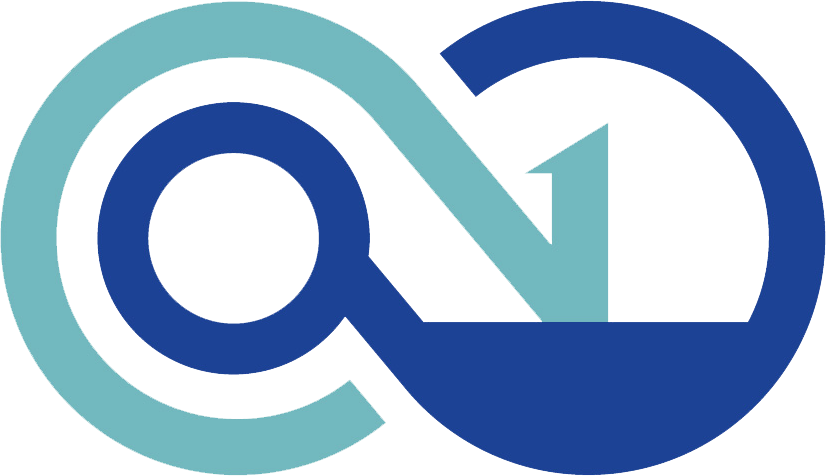