Finding Your Ideal OEM PCB Manufacturer: A Comprehensive Guide
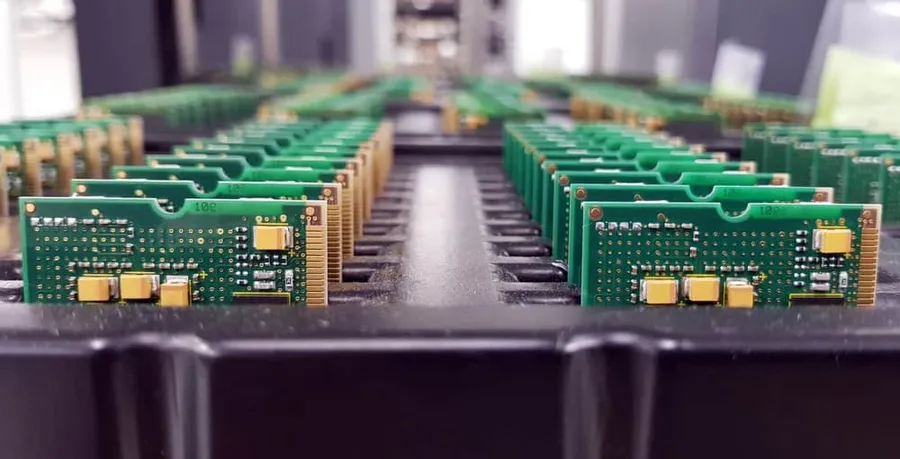
In today's fast-evolving electronics landscape, selecting the right OEM PCB manufacturer is crucial for product success. From intricate circuit designs to large-scale production, the right partner ensures quality, reliability, and cost-effectiveness. This guide explores the key aspects to consider when choosing an OEM PCB manufacturer, offering insights to help you make informed decisions and build durable and reliable products.
Understanding OEM PCB Manufacturing
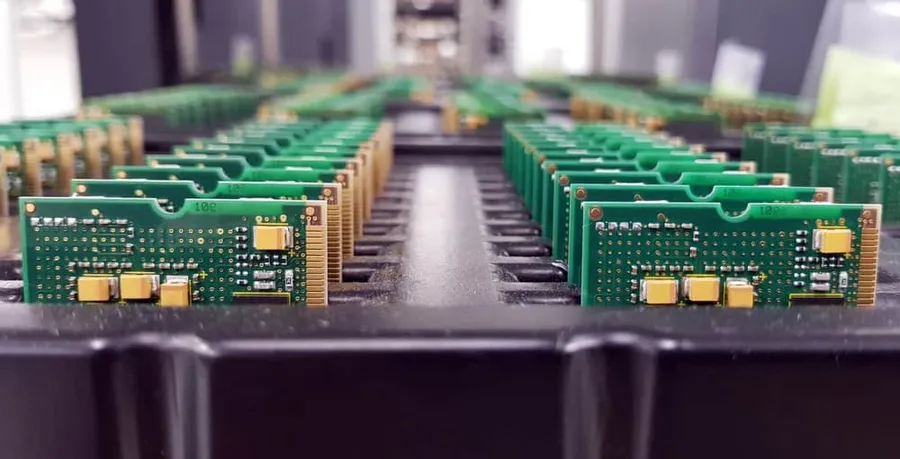
In the printed circuit board (PCB) industry, an Original Equipment Manufacturer (OEM) specializes in fabricating PCBs according to designs and specifications provided by other companies. These manufacturers concentrate on the physical production process, often without involvement in the initial design phases or direct sales to end-users. The OEM's core competency is high-volume, cost-effective manufacturing, leveraging specialized equipment and processes to meet the needs of their clients.
- Focus on Manufacturing
OEM PCB manufacturers are experts in the actual production of PCBs, using specialized machinery and techniques to ensure precision and consistency. - Specification-Driven Production
They produce PCBs according to detailed specifications, including materials, layer counts, and performance parameters, provided by their clients. - No Direct End-User Sales
OEMs typically don't handle direct sales to the final consumers, instead selling to companies that incorporate PCBs into their finished products. - Scalable Production Capacity
OEMs are geared to handle both prototypes and large-scale manufacturing runs, enabling their customers to efficiently meet market demand.
Why Choose an OEM PCB Manufacturer?
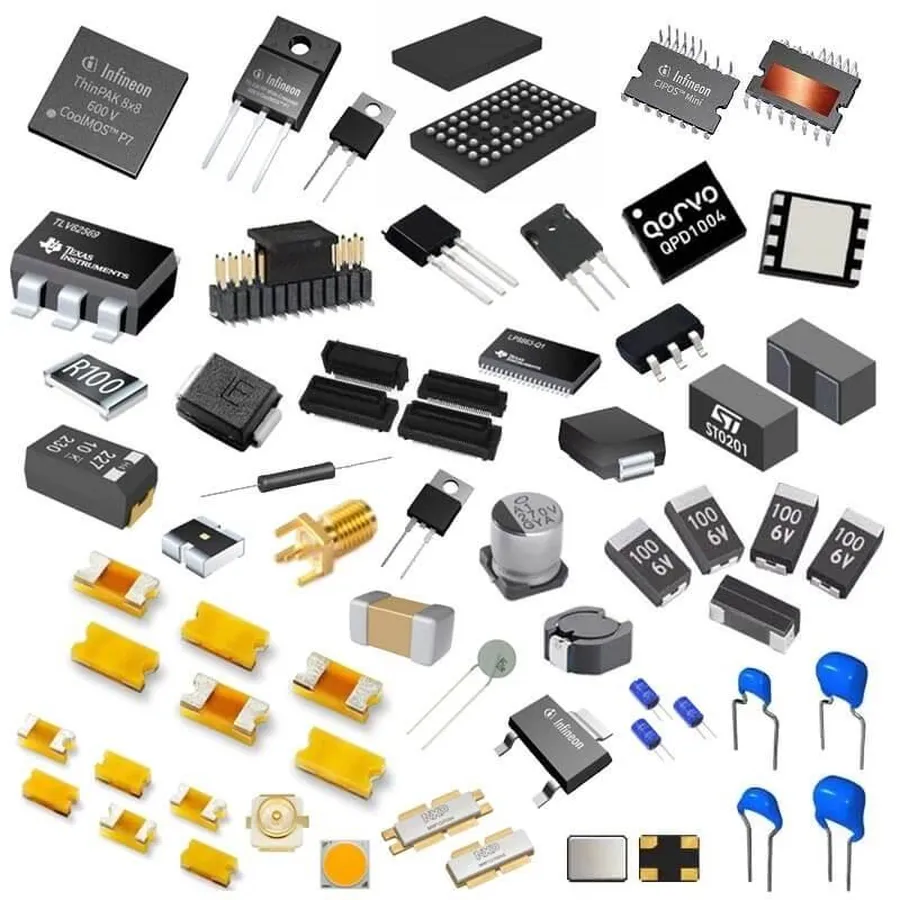
Opting for an Original Equipment Manufacturer (OEM) for your printed circuit boards (PCBs) offers significant advantages, primarily in cost-effectiveness and streamlined production. OEM PCB manufacturers specialize in producing boards to your exact specifications, leveraging their manufacturing expertise to deliver high-quality products at scale, without the overhead of design or end-user sales.
- Cost-Effectiveness at Scale
OEMs achieve lower per-unit costs through economies of scale, reducing the financial burden of large-volume PCB production. They optimize their processes for efficient manufacturing, which translates to savings for clients. - Specialized Manufacturing Expertise
OEMs possess deep expertise in PCB fabrication, focusing solely on manufacturing. This specialization allows them to hone their processes, use cutting-edge equipment, and consistently deliver high-quality PCBs, without the distraction of design or sales. - Streamlined Supply Chain
By engaging an OEM, businesses can create a more efficient supply chain by focusing on design and final product assembly, while the OEM handles the PCB production. This separation streamlines operations, ensuring a smooth transition from design to mass production. - Reduced Capital Investment
Companies avoid the need for heavy investment in PCB manufacturing facilities, equipment, and personnel by utilizing OEM services. This approach frees up resources to concentrate on core business activities like research, development, and marketing. - Access to Advanced Technologies
OEMs often invest in the latest PCB manufacturing technologies, including those for multilayer boards, fine-pitch designs, and unique material processing. This access to advanced capabilities can enhance the performance and complexity of your end products.
Key Factors to Consider When Selecting an OEM PCB Manufacturer
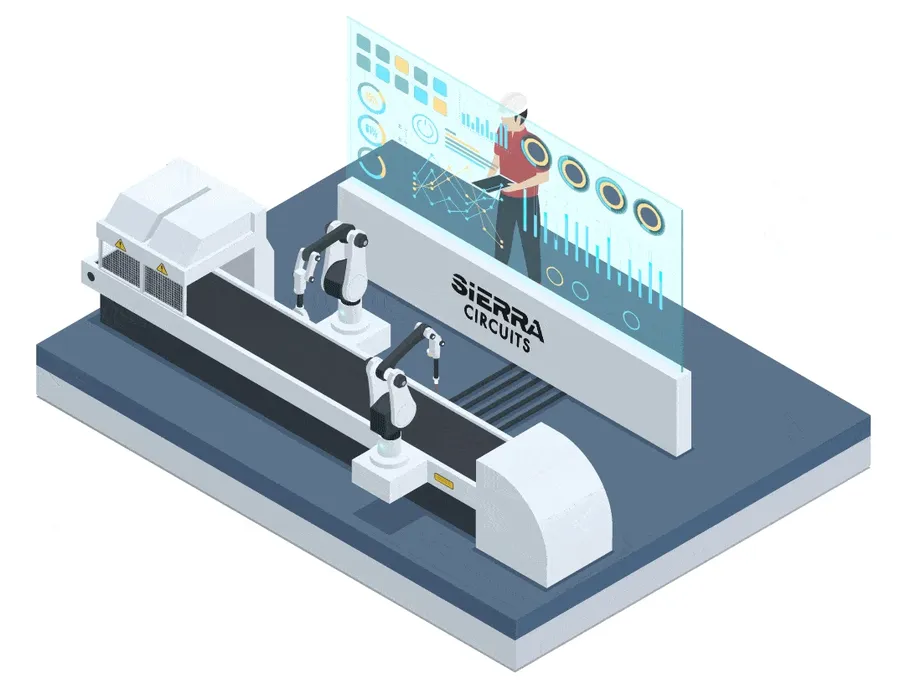
Selecting the appropriate OEM PCB manufacturer is critical for ensuring the quality, reliability, and cost-effectiveness of your printed circuit boards. This decision requires a comprehensive assessment of several key factors that directly impact the manufacturing process and final product.
- Manufacturing Capabilities
Evaluate the manufacturer's capacity to handle your specific PCB requirements, including complexity, layer count, and board size. Ensure they possess the necessary equipment and expertise for your designs. - Material Expertise
Confirm the OEM's proficiency in working with various materials, such as FR-4, flex, and high-frequency laminates. Their knowledge of material properties directly impacts performance and reliability. - Quality Control Standards
Prioritize manufacturers with robust quality control systems and certifications, including ISO 9001 or IATF 16949. These certifications ensure adherence to rigorous quality benchmarks, minimizing defects. - Certifications
Verify that the manufacturer holds relevant certifications that are important in your industry. Certifications like UL or IPC standards ensure compliance with industry-specific regulations. - Communication Processes
Establish that clear communication channels are in place. Responsive support, with the ability to promptly address your questions and concerns, is essential.
Material and Technology Capabilities
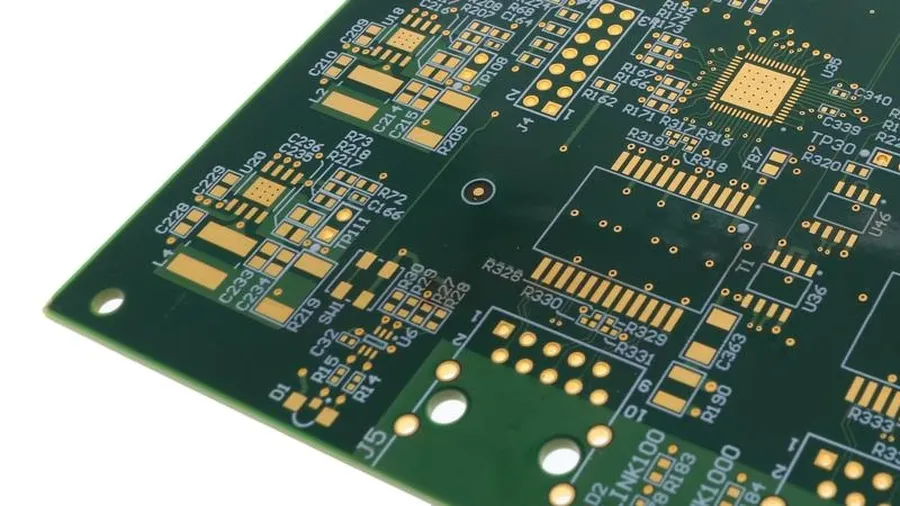
A proficient OEM PCB manufacturer demonstrates expertise in handling diverse materials and employing advanced technologies to meet varied client needs. This includes not only common substrates like FR-4 but also specialized materials such as flex PCBs and high-frequency laminates, coupled with sophisticated manufacturing techniques for producing complex boards.
Material Type | Description | Typical Applications |
---|---|---|
FR-4 | A common glass-reinforced epoxy laminate material known for its good balance of mechanical and electrical properties. | Most standard PCBs, consumer electronics, general-purpose circuits. |
Flex PCB | A flexible polyimide substrate allowing for bending and shaping, ideal for compact and dynamic applications. | Wearable devices, automotive electronics, medical equipment, any application requiring flexing. |
High-Frequency Materials | Specialized materials with low dielectric loss and stable electrical characteristics at high frequencies. | RF communication, radar systems, high-speed digital circuits, and aerospace applications |
Metal Core PCBs | A PCB with a metal base(often Aluminum or Copper) to improve heat dissipation. | LED lighting, Power supplies and Automotive electronics |
Technological capabilities are equally critical, encompassing multilayer PCB production, where multiple layers of circuitry are stacked to increase complexity and density. Advanced surface finishes are also important for solderability and reliability. Furthermore, the ability to handle fine pitch technology, which involves extremely small distances between components, showcases the manufacturer's precision and expertise in producing complex boards.
- Multilayer PCB Production
The ability to manufacture boards with multiple conductive layers, increasing circuit density and complexity. - Advanced Surface Finishes
Offers various surface finish options such as ENIG (Electroless Nickel Immersion Gold), HASL (Hot Air Solder Leveling), and OSP (Organic Solderability Preservative) to improve solderability and prevent corrosion. - Fine Pitch Technology
Proficiency in handling components with very small distances between pins, enabling more complex and compact designs.
Quality Control and Certifications
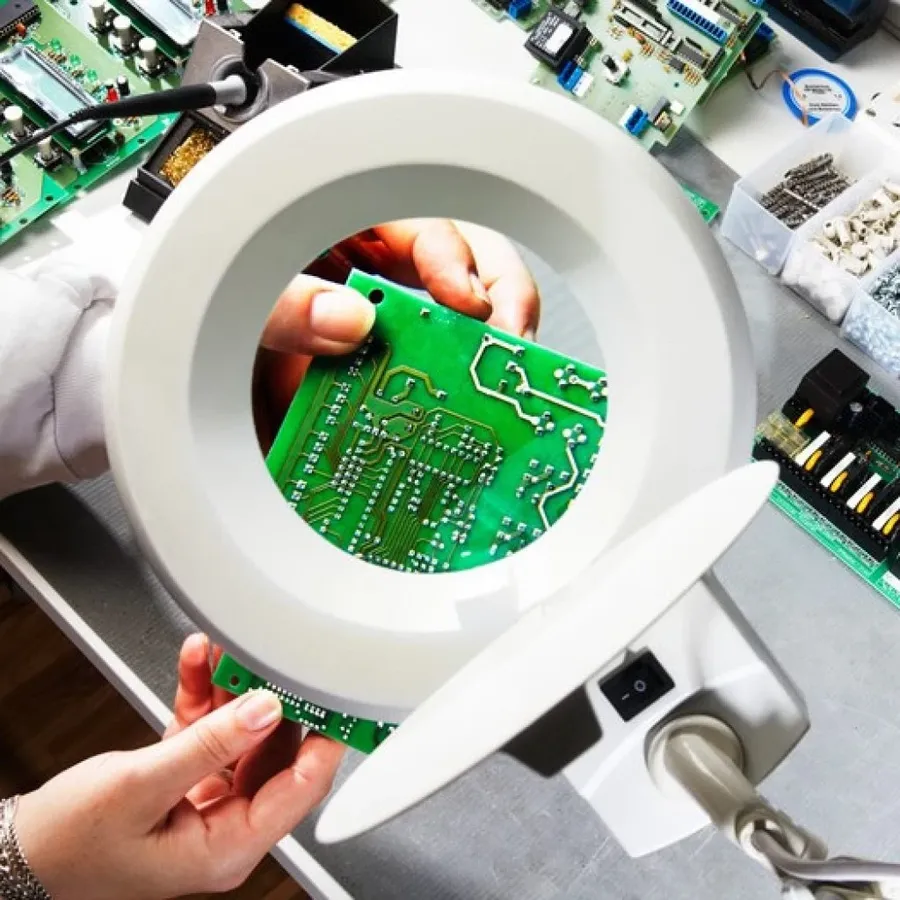
Rigorous quality control and relevant certifications are paramount when selecting an OEM PCB manufacturer. These elements ensure adherence to established standards, reducing the risk of defects and guaranteeing the reliability of the final product. A manufacturer's commitment to quality directly impacts the performance and longevity of the PCBs.
Certifications such as ISO 9001 and IATF 16949 are not merely badges of honor; they are indicators of a manufacturer's dedication to process control and continuous improvement. ISO 9001, a widely recognized standard, focuses on quality management systems, while IATF 16949, specific to the automotive industry, demands more stringent quality requirements. These certifications mean that the manufacturer has demonstrated the ability to consistently provide products that meet customer requirements and applicable statutory and regulatory requirements.
Certification | Focus | Implication for OEM PCB Manufacturing |
---|---|---|
ISO 9001 | Quality management systems | Ensures consistent quality through process control, documentation and continuous improvement |
IATF 16949 | Automotive industry quality management system | Guarantees high-quality, reliable PCB's designed for automotive applications. |
Beyond specific certifications, a comprehensive quality control system should cover aspects such as incoming material inspection, in-process checks, and final testing. Look for manufacturers who use advanced testing equipment and methodologies, such as automated optical inspection (AOI) and in-circuit testing (ICT), to identify defects and verify performance. Traceability of materials and processes is also critical to pinpoint the source of any issues.
Turnaround Time and Supply Chain Management
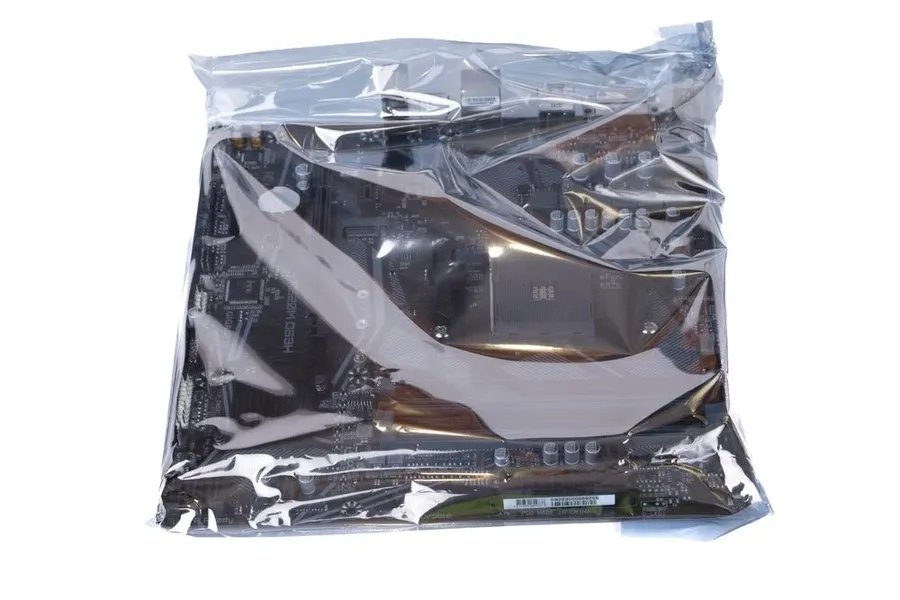
Effective turnaround time and robust supply chain management are paramount for any OEM PCB manufacturer. A manufacturer's ability to handle both rapid prototyping and large-scale production efficiently directly impacts a customer's time-to-market and overall project success.
OEM PCB manufacturers should demonstrate competence in these areas by:
- Quick Turn Prototyping
The ability to rapidly produce prototype PCBs allows for quick design iterations and validation, reducing time-to-market and development costs. Look for manufacturers who can turn around prototypes in days, rather than weeks. - Scalability for Mass Production
A capable OEM should seamlessly transition from prototype to large-scale production while maintaining consistent quality and adherence to specifications. The infrastructure, processes, and systems should be designed for efficient ramp-up. - Efficient Logistics and Distribution
From component procurement to finished product delivery, the supply chain must be streamlined and managed effectively to reduce lead times and ensure on-time delivery. This also includes efficient handling of international shipments for global clients. - Component Procurement
A reliable supply chain requires strong relationships with component distributors, ensuring the availability of necessary parts at competitive prices and with stable lead times, mitigating the risk of component shortages impacting production schedules.
Supply Chain Aspect | Key Considerations | Impact on Customer |
---|---|---|
Lead Time | Average time from order placement to delivery; evaluate for both prototype and mass production. | Directly impacts time-to-market and project timelines. |
Component Sourcing | Manufacturer's network of suppliers and their ability to secure consistent component supply. | Influences production stability and cost. |
Logistics | Efficiency in transportation and handling of PCBs. | Ensures timely delivery and minimizes potential damage. |
Inventory Management | The ability to manage raw materials and finished goods efficiently. | Reduces storage costs and prevents delays. |
Cost Structure and Pricing
A detailed understanding of cost structures and pricing is essential when selecting an OEM PCB manufacturer. While cost is a significant consideration, it should not be the sole determinant. The ideal partnership balances competitive pricing with exceptional quality and service. A transparent pricing model from an OEM manufacturer provides a clear breakdown of all expenses, allowing you to make informed decisions based on value, not just the lowest price.
Cost Component | Description | Impact on Overall Price |
---|---|---|
Material Costs | Raw materials used in PCB manufacturing (e.g., FR-4, copper, solder mask) | Significant, depending on material type and quantity |
Manufacturing Costs | Expenses associated with PCB fabrication processes (e.g., etching, drilling, plating) | Moderate to high, varies with complexity |
Tooling Costs | Expenses for creating custom tools for specific PCB designs | One-time cost, can be significant for complex designs |
Labor Costs | Wages for personnel involved in manufacturing, quality control, and other processes | Moderate, impacts cost based on location and skill level |
Testing Costs | Expenses related to testing and inspection of the PCBs | Moderate, ensures reliability and quality |
Shipping and Logistics Costs | Expenses associated with packaging, transportation, and delivery of PCBs | Moderate to high, impacts cost based on distance and method |
Other Potential Costs | Additional expenses such as customs fees or expedited services | Variable, depending on specific requirements |
When evaluating an OEM's pricing, consider the following:
- Quotation Transparency
A detailed breakdown of costs should be provided, without hidden charges. Request a comprehensive quote that includes all elements of the project. - Cost Drivers
Understand the factors that influence the cost, such as material type, board complexity, production volume, and lead time. This allows for better cost management in your design and supply chain. - Negotiation
Explore opportunities for price negotiations, especially for long-term partnerships or large-volume orders. Understand that value extends beyond pure price, including reliability and reduced failure rates. - Total Cost of Ownership
Consider the long-term implications of the chosen OEM. Lower upfront costs can sometimes lead to increased total costs of ownership if quality issues result in higher failure rates. Evaluate the cost of returns, lost sales, and potential damage to brand reputation.
By carefully examining the cost structure and pricing model of a potential OEM, you can select a partner that not only fits your budget but also delivers reliable PCBs with exceptional value.
Communication and Customer Support for OEM PCB Manufacturing
Effective communication and robust customer support are paramount for a successful partnership with an OEM PCB manufacturer. This ensures clarity, responsiveness, and the smooth progression of your projects, ultimately leading to high-quality products delivered on time.
- Responsive Customer Service
A reliable OEM should provide prompt responses to inquiries, technical questions, and any concerns you may have. Look for manufacturers with dedicated account managers or technical support teams. - Clear Communication Channels
The manufacturer should have established communication channels (e.g., email, phone, project management platforms) and use clear, concise language. Misunderstandings due to poor communication can lead to significant delays and costly errors. - Proactive Project Updates
Regular project updates are essential for transparency and timely intervention if any issues arise. This includes updates on manufacturing progress, any changes in the schedule or specifications, and tracking details. - Technical Support Availability
The OEM should possess a team of technical experts capable of handling technical inquiries, troubleshooting, and providing support throughout the entire manufacturing process. This includes design for manufacturability (DFM) feedback and material selection guidance. - Multilingual Support
If your team operates in multiple languages, consider an OEM that can accommodate your communication needs in a variety of languages to ensure clarity across all channels.
Frequently Asked Questions About OEM PCB Manufacturers
This section addresses common inquiries regarding OEM PCB manufacturers, offering insights into what to look for in a suitable partner. Understanding these factors will guide you in selecting an OEM that aligns with your quality, cost, and production needs.
- What exactly is an OEM PCB Manufacturer?
An OEM (Original Equipment Manufacturer) PCB manufacturer produces printed circuit boards based on the specifications provided by another company. They are primarily focused on manufacturing and typically do not handle the design or the end-user sales. Their expertise lies in efficiently producing PCBs to meet their clients' requirements. - Who is the best PCB manufacturer?
The 'best' PCB manufacturer is subjective and depends heavily on specific needs, such as volume, material requirements, and turnaround time. Factors like the manufacturer's capabilities, certifications, communication, cost structure, and supply chain management should align with your project's demands to determine the best fit. - What are the advantages of using an OEM PCB manufacturer over internal manufacturing?
OEM PCB manufacturers offer several advantages over internal manufacturing, such as scalability of production, optimized cost structures due to mass production efficiencies, and specialized equipment and expertise. Outsourcing allows companies to focus on core competencies, such as product design and marketing, rather than the complexities of PCB manufacturing. OEM partners are typically adept at managing supply chains and adhering to stringent quality controls, providing reliable results that internal manufacturing may not readily achieve. - What factors should be considered when selecting an OEM PCB manufacturer?
When selecting an OEM PCB manufacturer, key factors include their manufacturing capabilities (e.g., layer count, material handling), material expertise (FR-4, flex, high-frequency), quality control standards (ISO certifications), turnaround time, and supply chain management. The ability to manage quick turn prototypes and large-scale production, transparency in cost structure, and effective communication channels are also critical considerations. - Who are some of the leading PCB manufacturers in the USA?
Identifying the 'largest' or 'top' PCB manufacturers in the USA depends on criteria such as revenue, production volume, and customer base. Some well-regarded U.S.-based manufacturers include Epec, among others, but the best choice hinges on specific project requirements and the specialization of the manufacturer. - How can I ensure the quality of PCBs from an OEM manufacturer?
To ensure PCB quality, prioritize OEM manufacturers with recognized certifications like ISO 9001 or IATF 16949. Request process data, and if possible, conduct site audits. Seek transparent documentation of their testing procedures and quality control measures. Furthermore, start with small trial runs before proceeding with large-scale production to assess consistency and reliability. A robust quality management system that includes inspections, testing, and corrective action processes is essential.
Choosing the correct OEM PCB manufacturer is a critical step in bringing your electronic products to life. By carefully evaluating their capabilities, certifications, and track record, you can establish a partnership that ensures quality, reliability, and cost-effectiveness. As an integral part of the electronics manufacturing process, leveraging the expertise of a capable OEM PCB manufacturer can streamline your operations and ensure the production of high-quality PCBs for your innovative solutions.
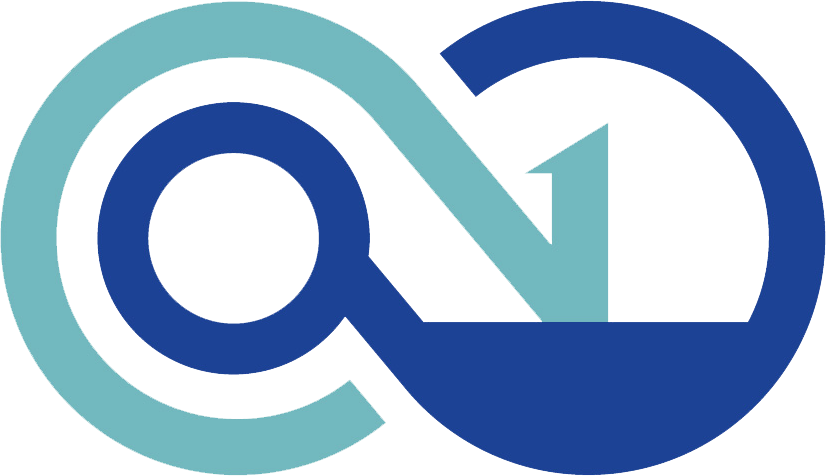