Finding Your Ideal Quality PCB Manufacturer: A Comprehensive Guide
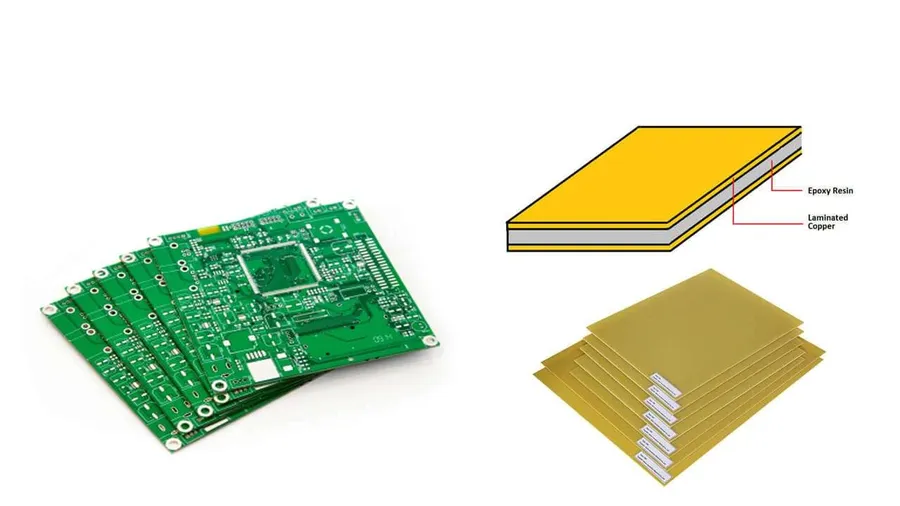
In today's fast-paced electronics industry, the quality of printed circuit boards (PCBs) is paramount. Whether you're developing a complex medical device or a simple DIY project, selecting a reliable quality PCB manufacturer is crucial to success. This article will guide you through the essential aspects of finding a manufacturer that meets your needs, ensuring high performance and reliability. We'll explore the key considerations when choosing a quality PCB manufacturer and how to make informed decisions.
Understanding Your PCB Needs
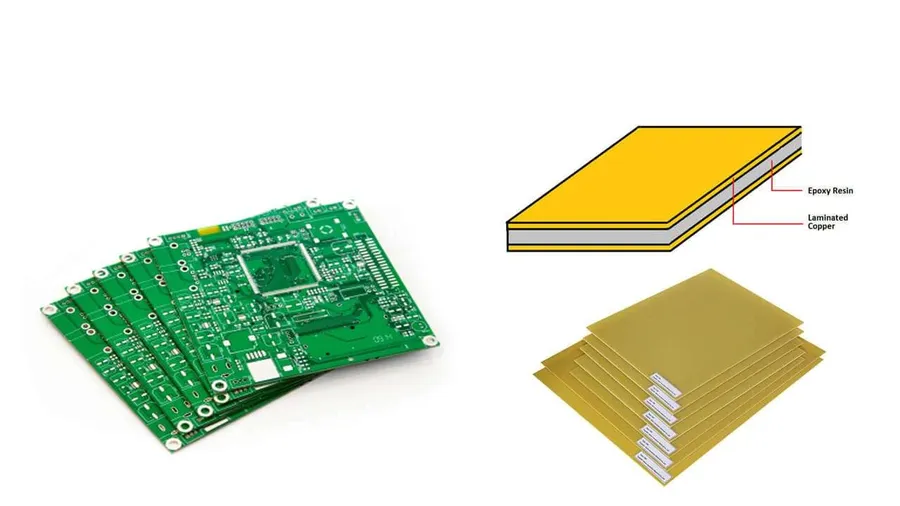
Before engaging a PCB manufacturer, a precise understanding of your project's requirements is paramount. This upfront clarity ensures that the chosen manufacturer possesses the requisite capabilities and expertise. A detailed specification, encompassing PCB type, layer count, materials, tolerances, and specialized processes, lays the groundwork for a successful manufacturing partnership and avoids costly miscommunications or redesigns down the line.
- PCB Type
Determine if you need single-sided, double-sided, multilayer, rigid, flexible, or rigid-flex PCBs. The choice depends on the complexity of your circuit and the application's requirements. - Layer Count
Specify the necessary number of conductive layers. This is crucial for routing complexity and signal integrity, and directly impacts PCB cost and manufacturing difficulty. - Material Requirements
Choose the appropriate substrate material (e.g., FR-4, Rogers, aluminum) based on the electrical, thermal, and mechanical requirements of your application. This choice impacts performance, durability, and price. - Tolerances
Define the allowable variations in dimensions and feature sizes. Tighter tolerances typically increase manufacturing costs but are crucial for high-precision applications. - Specialized Processes
Identify any unique processes required, such as impedance control, blind/buried vias, heavy copper, or specific surface finishes. These processes can significantly affect the choice of manufacturer. - Expected volume
Decide if you need prototype quantities, small batch production or large scale mass production. This can help identify the manufacturer that can fulfill your needs.
Key Factors to Evaluate When Choosing a Quality PCB Manufacturer
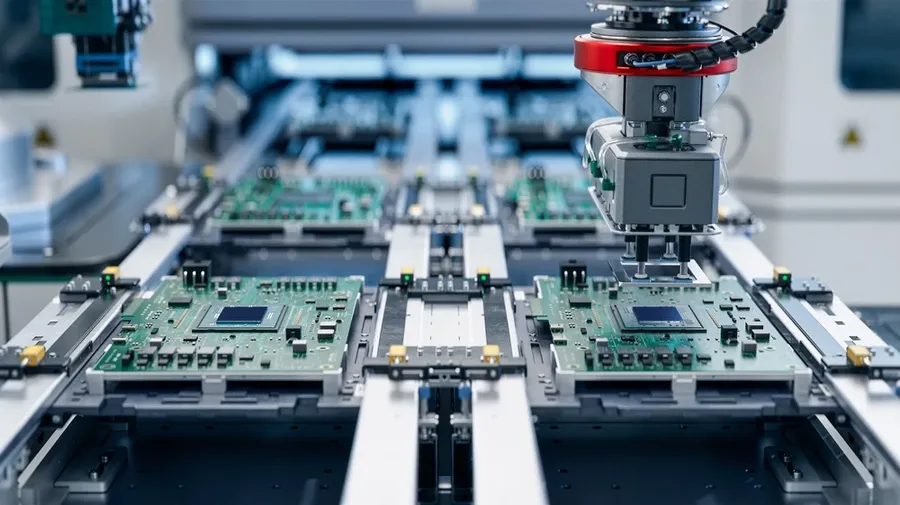
Selecting a high-quality PCB manufacturer is paramount for ensuring the reliability and performance of electronic products. Several factors significantly impact the final product, demanding careful evaluation of a manufacturer's capabilities and processes. These critical factors range from material selection to stringent quality control measures.
Factor | Description | Importance |
---|---|---|
Material Quality | The quality of the base materials (e.g., FR-4, Rogers, aluminum) and laminates used directly impacts the performance, durability, and reliability of the PCB. | Critical, as poor materials can lead to premature failure and performance issues. |
Manufacturing Standards | Adherence to industry standards such as IPC-A-600 for acceptability of printed boards and IPC-6012 for rigid boards demonstrates the manufacturer's commitment to quality. | Essential for ensuring consistency and meeting industry benchmarks. |
Testing Procedures | Rigorous testing at various stages of the manufacturing process, including electrical tests, visual inspections, and functional tests ensures that the PCB meets specified requirements. | Vital to identify and rectify defects before PCBs reach end products. |
Quality Certifications | Certifications such as ISO 9001, UL, and IPC demonstrate the manufacturer's adherence to high quality standards and are indicators of the company's commitment to continuous quality improvement. | Provides assurance of consistent and reliable manufacturing processes. |
Technology and Equipment | The technology and equipment used by the manufacturer plays a critical role in achieving high-precision PCBs. | Necessary for creating high-density circuits and ensuring accuracy. |
Layer Count Capability | The ability of the manufacturer to handle the number of layers in the design to support complex circuit requirements. | Crucial for complex designs requiring multiple signal layers. |
Surface Finish Options | The availability of various surface finishes such as HASL, ENIG, and OSP to match the design requirements and intended usage. | Relevant for solderability and environmental protection. |
Turnaround Time | The time it takes for a manufacturer to complete a production batch and deliver the PCBs. | Essential for project timelines and maintaining schedule efficiency |
Communication and Support | Responsive and effective communication and support between the manufacturer and the client will ensure issues can be addressed efficiently and ensure the project progresses smoothly | Important for resolving any issues and keeping projects on track |
Manufacturing Capabilities
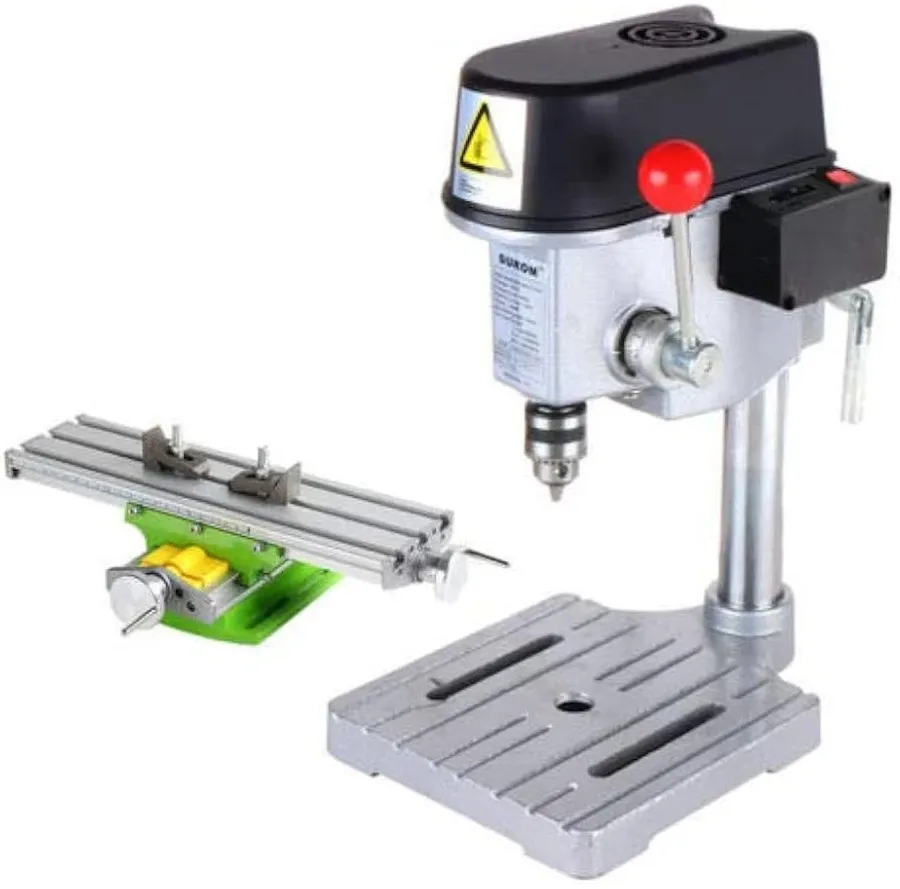
A quality PCB manufacturer must possess a comprehensive suite of manufacturing capabilities to meet diverse project needs, including prototyping, fabrication, and assembly services. Evaluating a manufacturer's equipment, technical expertise, and service range is crucial for ensuring they can fulfill all the necessary requirements of your PCB design.
Capability | Description | Importance |
---|---|---|
PCB Prototyping | Quick turnaround for testing and design validation before full production. | Essential for verifying design functionality and making necessary adjustments. |
PCB Fabrication | Manufacturing the bare PCB, including drilling, etching, and plating. | Core process for creating the physical board with precise specifications. |
PCB Assembly | Mounting electronic components onto the fabricated PCB. | Critical step to integrate components and achieve the complete circuit. |
Surface Mount Technology (SMT) | Automated process of mounting surface mount components. | Enables high-density and high-precision component placement. |
Through-Hole Technology (THT) | Mounting components with leads inserted through holes in the PCB. | Suitable for larger components requiring strong mechanical connections. |
Testing Services | Electrical tests to verify PCB functionality. | Ensures proper electrical continuity and performance. |
Specialized Processes | Options such as HDI, flexible PCBs, and advanced materials. | Important for specialized applications or design requirements. |
Equipment | Modern and well-maintained equipment ensures high quality manufacturing. | State-of-the-art machinery is a pre-requisite for complex designs. |
Technical Expertise | Experienced engineers and technicians who can handle complex PCB designs. | Highly knowledgeable staff guarantee quality and process optimisation. |
Geographical Considerations: Local vs. Overseas PCB Manufacturers
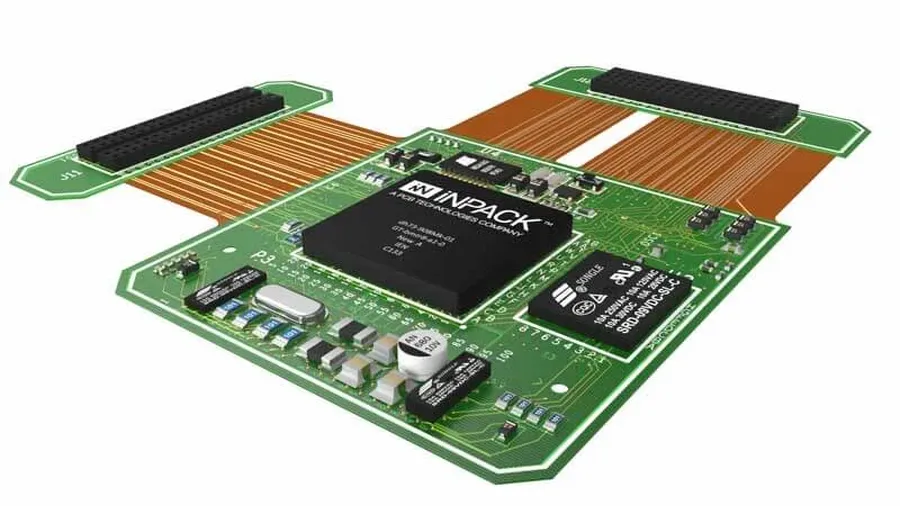
The decision between a local and an overseas PCB manufacturer is a pivotal one, directly impacting project costs, lead times, communication efficiency, and ultimately, the overall success of your product. This section will delve into the nuanced considerations of choosing between these options.
Factor | Local PCB Manufacturer | Overseas PCB Manufacturer |
---|---|---|
Cost | Generally higher due to labor and overhead | Potentially lower due to lower labor costs and economies of scale |
Lead Time | Shorter lead times due to proximity and reduced shipping | Longer lead times due to shipping and potential customs delays |
Communication | Easier communication due to time zone alignment and language | Potential for communication barriers and time zone differences |
Quality Control | Easier to audit and monitor production processes | Potentially harder to verify and enforce quality standards |
Shipping and Logistics | Simplified logistics, lower shipping costs, and less risk of damage | Increased shipping costs, potential delays, and more complex logistics |
Minimum Order Quantity | Often more flexible with smaller order quantities | May require larger minimum order quantities to achieve cost efficiencies |
Intellectual Property Protection | Potentially higher protection due to local laws and regulations | IP protection concerns may exist based on the overseas location |
Choosing between a local and an overseas manufacturer depends on the priority of your specific project needs. If rapid prototyping, tight quality control, and seamless communication are paramount, a local manufacturer may be preferable despite the potentially higher costs. However, if cost reduction is the primary objective, and you can manage longer lead times and potential communication challenges, then an overseas manufacturer may be a suitable option.
Quality Control and Certifications
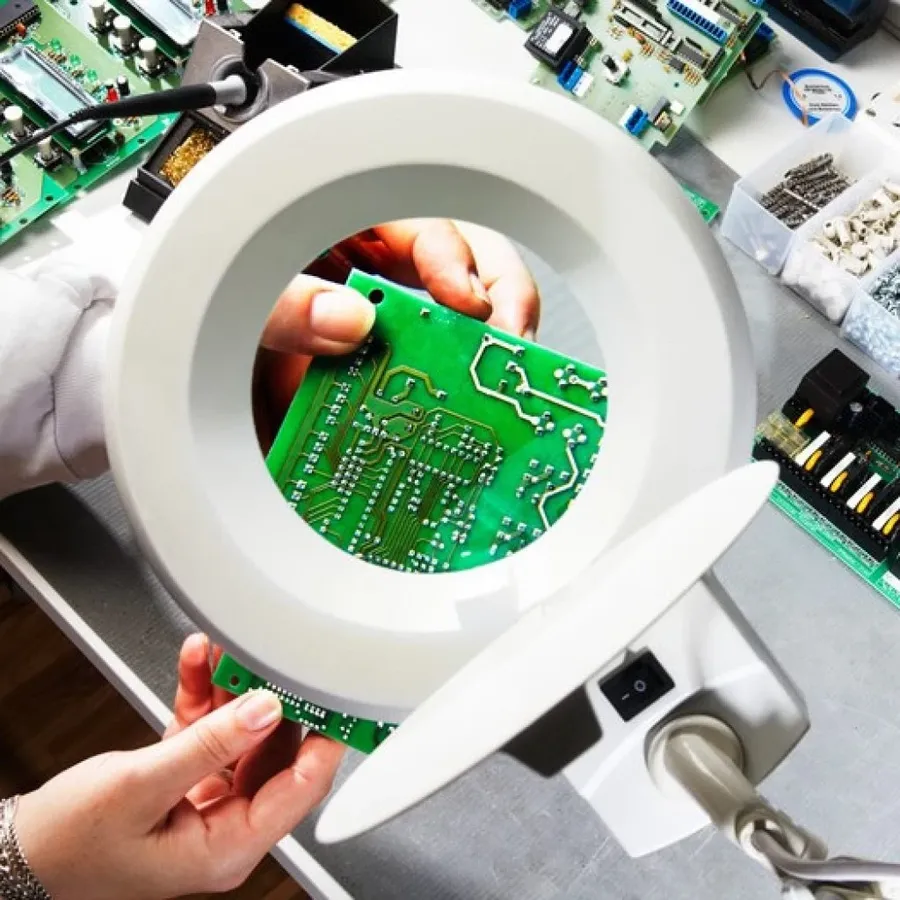
Rigorous quality control and adherence to industry certifications are paramount when selecting a PCB manufacturer. These certifications provide assurance that the manufacturer's processes and products meet established quality and environmental standards, reducing the risk of defects and ensuring reliable performance of your printed circuit boards.
Certification | Description | Significance for PCBs |
---|---|---|
ISO 9001 | International standard for quality management systems. | Indicates a structured approach to quality control throughout the manufacturing process, from design to delivery. |
UL Certification | Safety certification by Underwriters Laboratories. | Confirms the PCB manufacturer's compliance with specific safety standards for electrical products. |
IPC Standards (e.g., IPC-A-600, IPC-6012) | Standards developed by the Association Connecting Electronics Industries. | Provides guidelines for acceptable quality of printed circuit boards, covering aspects such as design, fabrication, and performance. |
ISO 14001 | International standard for environmental management systems. | Ensures that a PCB manufacturer adopts environmentally sustainable practices during the manufacturing process. |
RoHS Compliance | Restriction of Hazardous Substances directive. | Verifies that the manufacturer eliminates the use of hazardous substances, ensuring the environmental safety of PCBs. |
Beyond these key certifications, assess the manufacturer's commitment to quality throughout the entire production process. This includes: detailed inspection procedures, usage of high-precision testing equipment, and a robust system for tracking and resolving defects. These practices minimize the likelihood of flaws in the final PCB and reduce long-term costs associated with faulty circuits.
Frequently Asked Questions About Quality PCB Manufacturers
Selecting the right PCB manufacturer is crucial for the success of your electronic projects. This section addresses some of the most frequently asked questions to guide you in making an informed decision. Understanding these key points can help ensure you partner with a manufacturer that aligns with your quality and project requirements.
- Who is considered the best PCB manufacturer?
Determining the 'best' PCB manufacturer is subjective and depends on specific project needs, including complexity, volume, and budget. There isn't a universally acknowledged 'best' manufacturer; rather, leading companies excel in different niches, such as high-reliability PCBs, rapid prototyping, or large-volume production. It is best to evaluate manufacturers based on their capabilities and alignment with your unique requirements rather than relying on broad rankings. It is recommended to assess factors like technology, quality certifications, and customer reviews. - Which company's PCBs are known for their high quality?
Several companies have established a reputation for producing high-quality PCBs. These manufacturers often invest in advanced technology, stringent quality control processes, and possess relevant certifications. The quality can vary based on the specific type of PCB being produced and also the individual application. It's advisable to research individual companies and view any specific project requirements to gauge overall fit. Some high quality indicators include low defect rate and high reliability. - Who are the largest PCB manufacturers in the USA?
The landscape of PCB manufacturing in the USA is dynamic, with several large-scale manufacturers playing a significant role. While market positions can shift, companies with broad capabilities, advanced technology, and large production capacities generally lead the market. When you need to select a manufacturer, it is essential to evaluate their experience and technical capability as well as their financial stability. - What types of companies manufacture PCBs?
PCB manufacturers range from large, vertically integrated global companies to smaller, specialized shops. Some focus on high-volume production, while others cater to prototype and low-volume orders. The type of manufacturer you choose should depend on your project specifications. Some manufacturers specialize in areas such as flexible PCBs, high-frequency boards, or high-layer count boards. - How can I verify the quality of a PCB manufacturer before placing an order?
Verifying a PCB manufacturer's quality involves several steps. Check for relevant certifications like ISO 9001, UL, and IPC standards. Examine their testing procedures and ask for sample boards. Review customer testimonials and case studies. It is also advisable to request a detailed technical audit to ensure they can meet your specified needs. - What are the key factors to consider when selecting a PCB manufacturer?
When selecting a PCB manufacturer, consider factors such as their manufacturing capabilities, material quality, technological expertise, testing procedures, quality control processes, certifications, pricing, lead times, and customer service. Ensure they have a good track record and can provide the necessary support for your project. You should not just focus on price, you must focus on overall value.
Reading Reviews and Seeking Recommendations for Quality PCB Manufacturers
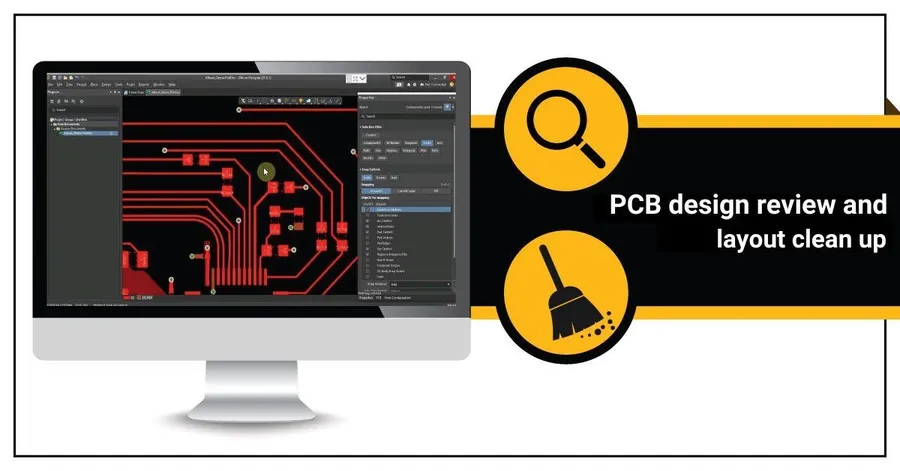
Gauging a PCB manufacturer's suitability extends beyond stated capabilities; it necessitates examining real-world performance. Customer reviews, case studies, and industry recommendations offer invaluable insights into a manufacturer’s strengths, weaknesses, and overall reliability. This provides a pragmatic view, supplementing technical specifications with user experience.
When considering these resources, prioritize the following:
- Consistency of Quality
Look for patterns in reviews regarding the consistency of the PCB quality delivered. A reputable manufacturer will exhibit uniform results across multiple orders. - Responsiveness and Communication
Assess how manufacturers respond to queries and issues. Effective communication is vital for avoiding delays and ensuring a smooth production process. - Adherence to Specifications
Evaluate if the manufacturer consistently delivers PCBs that meet the specified technical requirements and tolerances. Non-compliance can lead to costly rework and project delays. - Handling Complex Designs
If your designs are intricate, examine how the manufacturer performs with complex PCBs. Check for expertise in specialized techniques and if they have experience in specific industries, such as medical or aerospace. - Cost Transparency and Unexpected Costs
Look for reviews that speak to a manufacturer’s cost transparency. Hidden or unexpected costs, including extra charges for testing or revisions, can impact the budget. Be alert to reports of these practices. - Delivery Time and Reliability
Assess delivery lead times and their consistency, which is crucial for project timelines. Manufacturers who can deliver reliably, without delays, are preferred.
Utilize the following resources to gather information:
- Independent Review Platforms
Websites like Trustpilot, Google Reviews, and industry-specific forums often host candid reviews from users. Cross-reference information across these platforms to obtain a balanced viewpoint. Seek out detailed reviews that are specific to similar types of PCB projects. - Industry Forums and Communities
Participate in industry forums or online communities where other engineers and designers share their experiences and recommendations. This can provide direct, pertinent feedback from professionals facing similar challenges. - Case Studies from the Manufacturer
Review detailed case studies presented by the manufacturers themselves. While potentially selective, case studies can showcase the manufacturer's expertise in specific areas and capabilities. Critically analyze how these case studies align with your particular needs. - Direct Recommendations from Peers
Seek recommendations directly from colleagues or industry peers who have previously used PCB manufacturers. These firsthand accounts provide more tailored insight and can offer information not readily available through other sources.
Cost Analysis and Budgeting
Cost is a pivotal consideration when selecting a PCB manufacturer, yet it should not be the sole determinant. A balanced approach that weighs both cost and quality is essential for long-term project success. A comprehensive cost analysis extends beyond the unit price of the PCBs and includes a thorough evaluation of tooling, testing, and potential rework expenses to fully grasp the financial implications.
Cost Factor | Description | Impact on Overall Cost |
---|---|---|
Unit Cost | The price per PCB, influenced by material, complexity, and volume. | Directly impacts the total cost, especially at high volumes. |
Tooling Costs | Fees for creating necessary tools and fixtures for PCB production. | Significant initial cost, potentially amortized over larger production runs. |
Testing Costs | Expenses related to electrical testing, functional testing, and other quality assurance procedures. | Essential for ensuring reliability, but adds to the total cost. |
Shipping Costs | The cost of transporting PCBs from the manufacturer to your location. | Can vary significantly based on distance and shipping method. |
Rework Costs | Expenses associated with rectifying issues and defects on PCBs. | Can be substantial if quality control is inadequate. |
NRE Costs | Non-recurring engineering costs. | One-time expenses associated with the set-up of manufacturing process. |
- Volume Pricing
Understand how price per unit changes with volume. Most manufacturers provide tiered pricing, where larger orders result in lower per-unit costs. It is important to consider your project's expected volume when comparing quotes. - Material Costs
The type of material (FR-4, Aluminum, Rogers, etc) used will greatly influence the PCB's cost. High-performance and specialized materials will command higher prices, but may be essential for some projects. - Complexity Factor
The number of layers, the presence of microvias or buried vias, and other design complexities have a direct impact on production costs. Consider if design simplification is possible to optimize your budget. - Testing Requirements
Basic electrical testing is standard, but additional testing like flying probe or functional testing will add to the overall expense, ensure that you have the required test requirements for your project requirements. - Hidden Costs
Be wary of hidden costs such as NRE costs, handling fees, additional charges for rush orders, etc., include these in your initial costing assessments to avoid surprises during the project's execution. - Payment Terms
Negotiate the best possible payment terms to manage cash flow and optimize your financial planning. Some manufacturers may offer discounts for up-front payments or flexible payment options for regular collaborations.
Building a Long-Term Partnership with a Quality PCB Manufacturer
Establishing a long-term partnership with a quality PCB manufacturer is a strategic decision that yields consistent quality, streamlined processes, and reduced lead times, crucial for sustained project success. This goes beyond individual transactions, fostering a relationship built on mutual understanding, consistent communication, and shared goals.
- Consistent Quality
A long-term relationship allows the manufacturer to deeply understand your specific requirements and preferences, leading to more consistent quality across multiple production runs, reducing defects and waste. - Streamlined Processes
Repeated collaborations streamline communication, documentation, and logistical processes, minimizing delays and improving overall efficiency. This also enables quicker adaptation to changes in specifications or material needs. - Reduced Lead Times
Manufacturers familiar with your products can often offer priority scheduling and optimized production cycles, significantly decreasing lead times compared to engaging new manufacturers for each project. This is particularly beneficial for projects with tight deadlines. - Cost Efficiencies
Long term collaborations can lead to preferential pricing and discounts from manufacturers seeking to retain a reliable client, making overall production costs more competitive. Additionally, reduced rework and waste contribute to significant cost savings. - Enhanced Communication
Over time, a strong relationship with your PCB manufacturer fosters open communication channels and a shared understanding of design nuances and production requirements. This translates into quicker issue resolution and minimized errors. - Proactive Collaboration
A long-term partner is more likely to proactively offer design recommendations, material alternatives, or process optimizations based on their in-depth knowledge of your needs, contributing to continuous improvement and superior outcomes. - Mutual Growth and Innovation
Working closely over time can spur opportunities for mutual learning and innovation. Sharing knowledge and jointly seeking better solutions can lead to improved designs, lower costs, and the development of new technologies.
Selecting the right quality PCB manufacturer is an essential step in ensuring the success of your electronic project. By carefully considering all aspects from material quality to certifications, and by aligning with a manufacturer that offers the right capabilities, you can secure high-quality PCBs that will meet all your needs. Whether you're seeking a local partner or looking at an international quality PCB manufacturer, due diligence and a thorough understanding of your needs will guarantee long-term success. A quality PCB manufacturer is more than just a supplier; they’re a crucial partner in your electronics journey, ensuring your projects are built to your high standards.
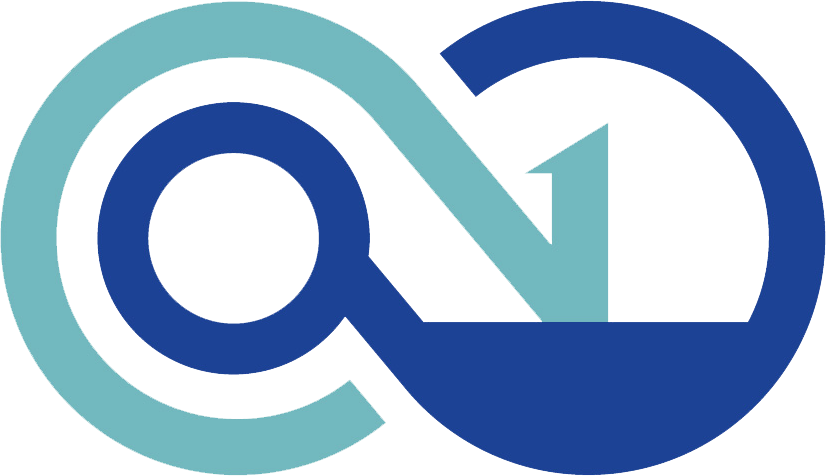