Global PCB Manufacturers: Navigating the Top Players in 2024
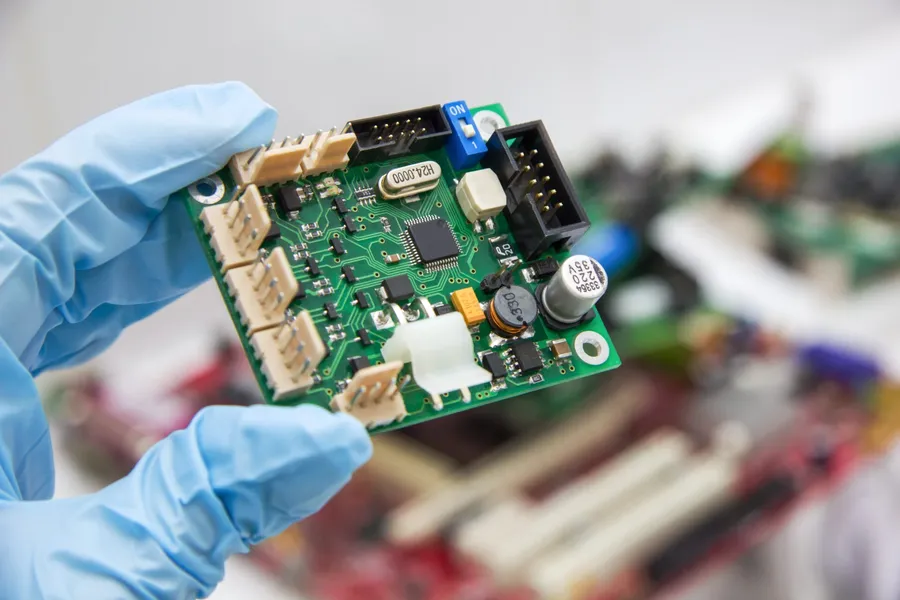
The printed circuit board (PCB) is the backbone of modern electronics, powering everything from smartphones to sophisticated medical devices. As technology advances, the demand for high-quality PCBs grows, driving the growth of global pcb manufacturers. This article delves into the key players in this industry, offering insights into their strengths and specializations and providing readers with knowledge about the global PCB manufacturing landscape.
Top PCB Manufacturers by Revenue: A Comparative Overview
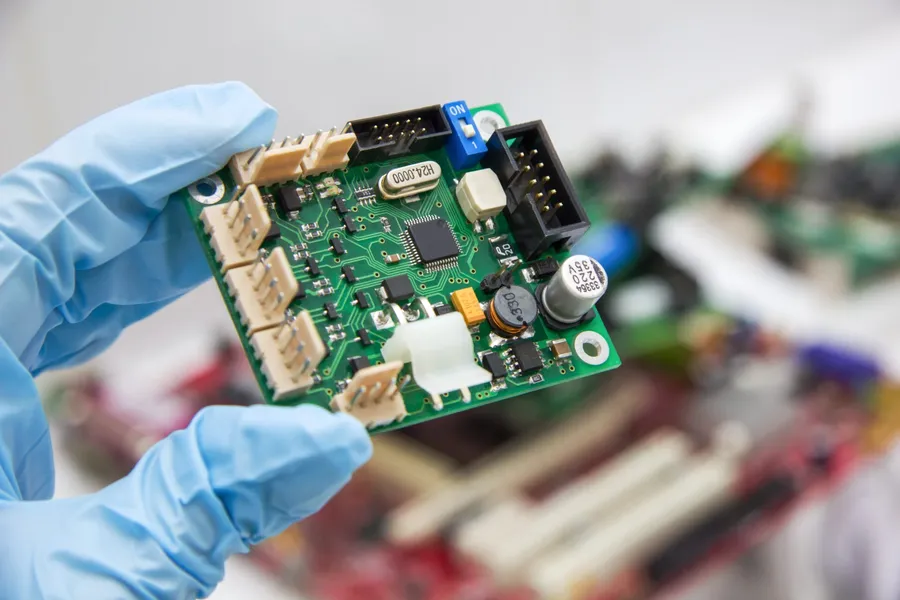
The global printed circuit board (PCB) manufacturing landscape is dominated by a select group of companies that generate substantial revenue, reflecting their market share and technological prowess. This section provides an overview of these top players, examining their financial performance and impact on the industry.
The PCB market is a critical component of the electronics industry, underpinning the functionality of almost all electronic devices, from smartphones to sophisticated aerospace equipment. Market size is in the hundreds of billions of dollars annually, and the leading manufacturers are constantly pushing the boundaries of technology, influencing both market trends and the pace of innovation.
While specific revenue figures fluctuate annually, several companies consistently appear at the top of the list. These market leaders are distinguished by their substantial production capacities, diverse product portfolios, and advanced manufacturing capabilities. Their financial success is a clear indicator of their influence and the benchmarks they set for the industry.
Key factors contributing to these manufacturers' leading positions include strategic investments in research and development, long-standing customer relationships, efficient supply chain management, and the capacity to rapidly adapt to changing market demands. These leading PCB manufacturers not only shape the industry but also drive technological advancements and set the standards for quality and reliability.
Geographic Distribution of Key PCB Manufacturers
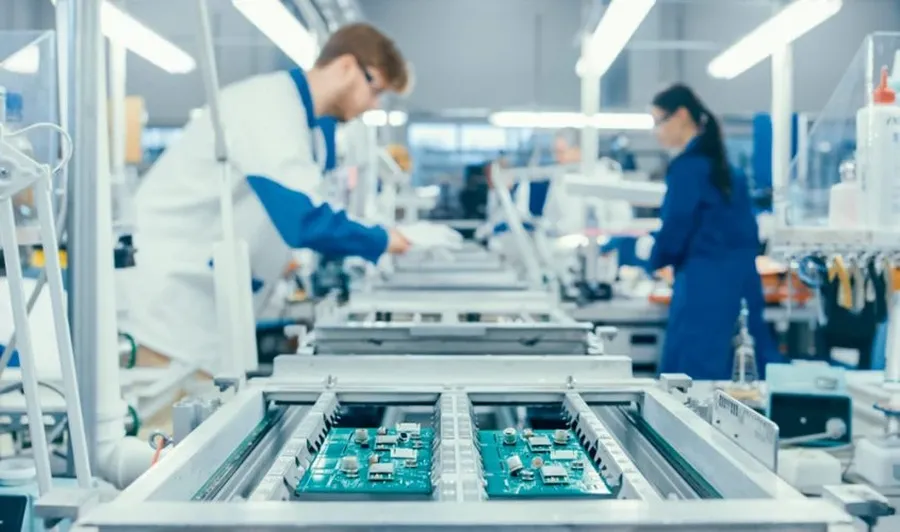
The global PCB manufacturing landscape is not uniform, with significant concentrations in specific geographic regions. This distribution is driven by a combination of factors, including historical development, technological infrastructure, labor costs, and government policies. Understanding this distribution is crucial for businesses involved in electronics manufacturing and supply chain management.
Asia Pacific is the dominant region in PCB production, accounting for a substantial majority of the global market share. This concentration is primarily due to China, Taiwan, South Korea, and Japan, each playing a unique role in the manufacturing ecosystem. These countries boast well-established electronics manufacturing infrastructures, skilled labor forces, and strong government support for the industry.
China stands out as the world's largest producer of PCBs, leveraging its vast manufacturing capacity and competitive labor costs. Taiwan, while smaller in land area, is another key player with advanced manufacturing technologies and a high concentration of leading PCB companies. South Korea is renowned for its high-end PCB production and strong focus on technology, particularly for the consumer electronics sector. Japan, with its rich history in electronics, focuses on precision and high-reliability PCB manufacturing.
While the Asia Pacific region dominates, other regions also participate in PCB production. North America and Europe have established PCB manufacturing bases focusing on high-reliability and specialized applications, often catering to aerospace, defense, and medical sectors. These regions are characterized by higher manufacturing costs but also by higher value-added products and processes.
The geographic distribution is not static; it evolves due to technological advancements, market demands, and economic factors. The shift towards advanced technologies and materials might see a shift in manufacturing hubs over time. Understanding these trends is essential for anticipating changes in the global supply chain.
Key Technologies and Specializations Among Global PCB Manufacturers
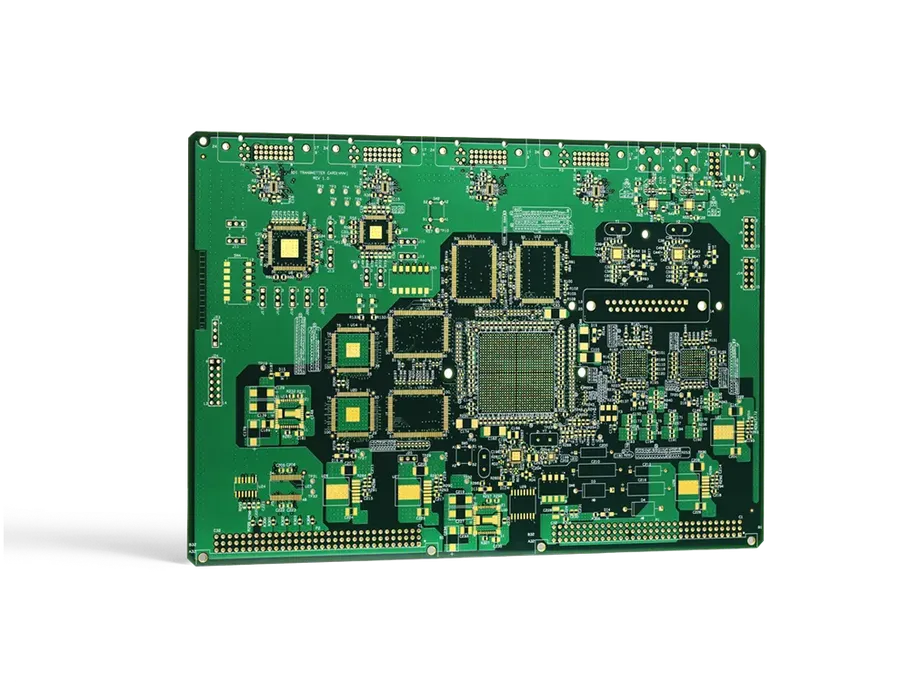
The global PCB manufacturing landscape is characterized by a diverse range of technologies and specializations, with manufacturers focusing on specific areas to gain a competitive edge. These specializations not only reflect the advancements in the electronics industry but also cater to the specific needs of various sectors. This section explores the key technologies and specializations that define the capabilities of leading global PCB manufacturers, encompassing rigid, flexible, and HDI PCBs, among others.
- Rigid PCBs
These are the most common type of PCBs, characterized by their solid and inflexible structure. They are typically made from materials like FR-4, which is a fiberglass composite. Many manufacturers have deep expertise in producing high-volume, reliable rigid PCBs for a wide array of applications. Key technologies include multi-layer design and advanced drilling techniques. - Flexible PCBs (FPCBs)
FPCBs are designed to bend and flex, allowing for complex shapes and integration into compact electronic devices. Their production requires specialized materials and processes, such as polyimide films. Specialized techniques include laser micro-via drilling and precise lamination. FPCB manufacturers often possess expertise in thin materials handling and complex circuit designs. - HDI PCBs
High-Density Interconnect (HDI) PCBs feature finer lines and spaces, enabling higher component density and increased functionality in smaller footprints. HDI manufacturing involves sophisticated technologies such as laser direct imaging, microvia fabrication, and sequential lamination. Manufacturers excelling in this area often provide solutions for high-performance devices like smartphones and medical electronics. - RF and Microwave PCBs
These PCBs are designed for high-frequency applications, requiring materials with low dielectric loss and tight impedance control. Specialized processes include precision etching and careful material selection. Manufacturers in this niche have expertise in signal integrity and high-frequency material characterization. - Metal Core PCBs (MCPCBs)
MCPCBs utilize a metal substrate, typically aluminum or copper, for improved heat dissipation, making them suitable for high-power LED lighting and power electronics. Specialized techniques include advanced thermal management solutions. Manufacturers focusing on MCPCBs possess expertise in thermal analysis and heat transfer. - Advanced Substrate Technologies
Some manufacturers specialize in advanced substrate technologies, such as system-in-package (SiP) substrates and embedded component PCBs. These technologies enable increased miniaturization and integration of multiple functionalities into a single module. The production requires high precision fabrication techniques and advanced material handling processes.
Material Innovations in PCB Manufacturing
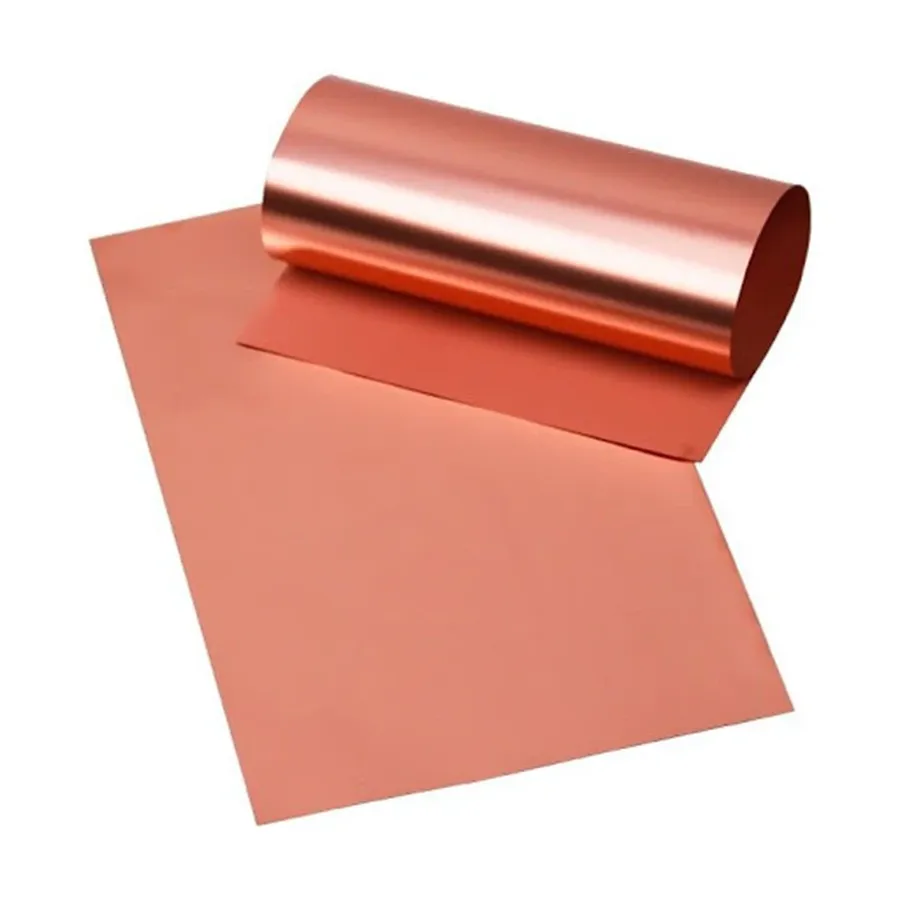
The relentless pursuit of enhanced performance, reliability, and sustainability is driving significant innovations in the materials used for PCB manufacturing. These advancements directly impact the capabilities and environmental footprint of electronic devices, shaping the future landscape of global PCB manufacturing.
Traditional materials such as FR-4 (Flame Retardant type 4) still dominate the market due to their cost-effectiveness and acceptable performance for many applications. However, the demand for miniaturized, high-speed, and high-frequency electronics is pushing manufacturers to explore and adopt advanced material alternatives.
- High-Performance Laminates
Beyond FR-4, materials like polyimide, PTFE (Teflon), and cyanate ester offer superior electrical and thermal properties. These materials are crucial for high-speed digital and RF applications, demonstrating lower dielectric loss and better thermal stability, enabling more efficient signal transmission and heat dissipation. - Metal Core PCBs (MCPCBs)
MCPCBs utilize a metal base, typically aluminum or copper, for enhanced heat dissipation. This design is essential in high-power applications, like LED lighting and power electronics, where thermal management is critical to maintain optimal performance and longevity. These base metals facilitate efficient heat transfer away from sensitive components. - Flexible Substrates
Materials like polyimide and liquid crystal polymer (LCP) are used for flexible PCBs (FPCs), enabling circuitry to conform to non-planar shapes. FPCs play a crucial role in compact electronic devices, automotive applications, and wearables, allowing for innovative design and integration where space is limited. - Advanced Fillers and Resins
Researchers are constantly developing new fillers and resin systems to improve the mechanical, thermal, and electrical properties of PCB materials. Nanomaterials, for example, are being incorporated to enhance thermal conductivity and mechanical strength of PCB substrates. These additives also enhance the ability to withstand high temperatures and harsh environments. - Environmentally Friendly Materials
The focus on sustainability is driving the industry towards eco-friendly options, including bio-based resins and halogen-free materials. These materials minimize the environmental impact of PCB production, aligning with growing sustainability trends and regulations, making PCBs more recyclable and less toxic.
The adoption of these innovative materials is not just about improving performance metrics; it’s also about aligning with global trends towards miniaturization, higher integration, and environmental consciousness. Global PCB manufacturers must continuously evaluate and integrate these material innovations to remain competitive and meet the ever-evolving demands of the electronics industry.
Comparative Analysis: Top PCB Manufacturers
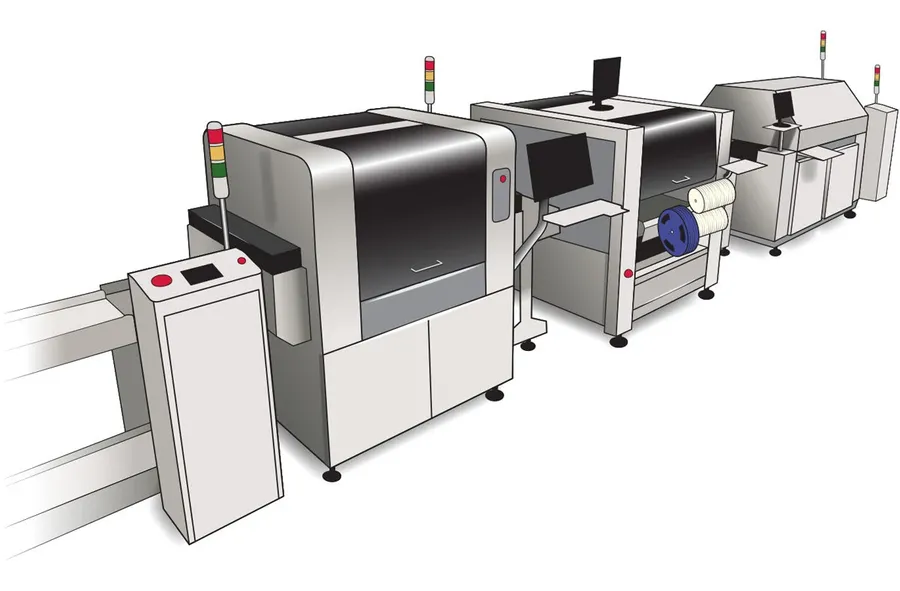
This section provides a detailed, side-by-side comparison of leading global PCB manufacturers. It highlights their strengths, technological focus, and core capabilities. The analysis incorporates critical parameters including manufacturing capacity, technological specialization, relevant certifications, and their primary customer base, enabling a thorough evaluation of each manufacturer’s position in the market.
Manufacturer | Manufacturing Capacity | Technology Focus | Key Certifications | Customer Base | Geographic Strengths |
---|---|---|---|---|---|
TTM Technologies | High volume; multi-site global manufacturing. | High-layer count PCBs, HDI, RF/microwave. | ISO 9001, AS9100, IATF 16949. | Aerospace, defense, automotive, medical. | North America, Asia |
Nippon Mektron | Significant capacity for flexible PCBs. | Flexible PCBs, rigid-flex PCBs, high-density interconnect. | ISO 9001, ISO 14001. | Consumer electronics, automotive, industrial. | Asia, Europe |
Unimicron | Very large global capacity across various PCB types. | HDI, multilayer PCBs, IC substrates. | ISO 9001, ISO 14001, TL 9000. | Mobile devices, IT infrastructure, automotive. | Asia, North America, Europe |
Compeq | Large-scale production of rigid PCBs and HDI boards. | Rigid PCBs, HDI PCBs, high-layer count. | ISO 9001, ISO 14001, IATF 16949. | Mobile devices, computers, consumer electronics. | Asia |
AT&S | High-end PCBs including embedded components. | HDI, IC substrates, advanced packaging. | ISO 9001, ISO 14001, IATF 16949. | Automotive, industrial, medical. | Europe, Asia, North America |
Kinwong Electronic | Large volume production capacity in China. | Multilayer PCBs, HDI, flexible PCBs. | ISO 9001, ISO 14001. | Consumer electronics, automotive, telecommunications. | Asia |
Shennan Circuits | Rapidly growing capacity focusing on advanced PCB technologies. | HDI PCBs, IC substrates, rigid-flex PCBs. | ISO 9001, IATF 16949. | Telecommunications, data centers, medical. | Asia, Global expansion |
The Impact of Global Supply Chains on PCB Production
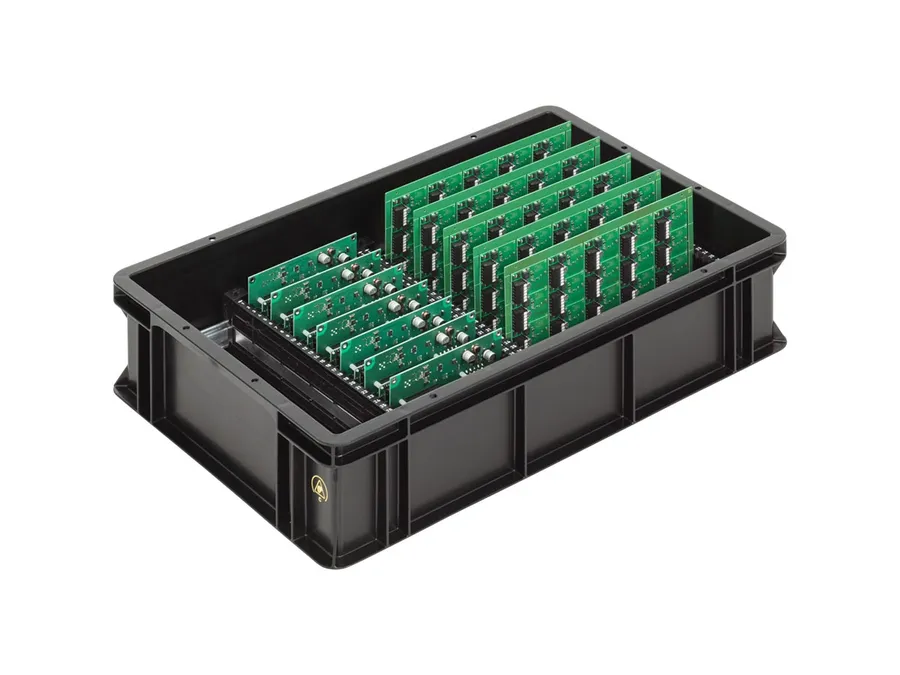
The global printed circuit board (PCB) industry is heavily reliant on complex international supply chains. These chains encompass the sourcing of raw materials, manufacturing processes, logistics, and the influence of geopolitical factors, all of which significantly impact PCB production.
Understanding these dynamics is crucial for mitigating risks and ensuring a steady supply of PCBs, which are fundamental components in virtually all electronic devices. Disruptions at any point in the supply chain can cascade into significant delays and cost increases, highlighting the need for robust supply chain management strategies.
- Sourcing of Raw Materials
Key materials for PCB manufacturing include copper, glass fiber, resins, and various metals. These materials are often sourced from different regions, leading to potential dependencies and vulnerabilities. For example, certain specialized resins might come from specific manufacturers that could be impacted by regional instability or trade policies. - Manufacturing Locations
PCB manufacturing is largely concentrated in Asia, particularly in China, Taiwan, South Korea, and Japan. This geographic concentration creates both advantages in terms of scale and efficiency, but also significant risks from potential supply disruptions due to geopolitical tensions or natural disasters in these regions. Diversification of manufacturing locations is a key strategy in mitigating such risks. - Logistics and Transportation
Efficient and reliable transportation networks are vital for moving PCBs and their components across the globe. Delays due to shipping congestion, port closures, or customs issues can severely impact delivery times. Furthermore, the increasing demand for PCBs and ongoing challenges within the global logistics infrastructure underscore the need for enhanced supply chain resilience. - Geopolitical Factors
Geopolitical events such as trade disputes, tariffs, and political instability in key manufacturing regions can have immediate and substantial effects on the cost and availability of PCBs. These factors necessitate careful monitoring and adaptive supply chain strategies that can accommodate geopolitical unpredictability.
Frequently Asked Questions About Global PCB Manufacturers
This section addresses common questions regarding PCB manufacturers, providing clear and concise answers to help you better understand the industry landscape and make informed decisions. We'll explore the nuances of selecting the right manufacturer, geographical manufacturing hubs, and other key aspects.
- Who is considered the 'best' PCB manufacturer?
Determining the 'best' PCB manufacturer is subjective and depends heavily on specific project requirements, such as volume, complexity, and required certifications. There isn't a single best manufacturer globally; rather, it's about finding the right fit for your needs. Factors to consider include technological expertise, manufacturing capacity, quality standards (ISO certifications), and the types of PCBs they specialize in (e.g., rigid, flexible, HDI). - Which country is the largest manufacturer of PCBs?
China currently holds the position as the largest manufacturer of PCBs globally, with a significant portion of the world's PCB production concentrated there. This is due to a combination of factors, including lower production costs, a robust manufacturing infrastructure, and government support. However, other countries like Taiwan, South Korea, and Japan also possess strong PCB manufacturing capabilities. - Which company's PCBs are considered the 'best' in terms of quality and reliability?
Several companies are recognized for their high-quality PCBs, but it's crucial to assess your specific needs. Companies known for high quality include those that focus on advanced technology and stringent quality control, many of which are publicly traded. It is important to review certifications and testing data, as well as evaluate manufacturing standards before selection. - Who are the major players manufacturing PCBs?
The PCB manufacturing industry is comprised of a mix of publicly traded and privately held companies. Key players are based in Asia, North America, and Europe. These companies vary in size, manufacturing capabilities, and technological specializations. Researching and comparing manufacturers based on their areas of focus, production volume, and geographic availability is highly recommended to choose the best partner for your manufacturing needs. - What factors should I consider when choosing a PCB manufacturer?
Key factors include the manufacturer's experience with your specific type of PCB (e.g., rigid, flexible, HDI), their manufacturing capacity to meet your volume requirements, their quality certifications (such as ISO 9001 and others), their technology expertise (e.g., via filling, impedance control), their location and logistics, their pricing structure, and their customer support. It's also beneficial to assess their lead times and any additional services they offer, like design support or assembly. - How do global supply chains affect PCB manufacturing?
Global supply chains significantly impact PCB manufacturing by influencing the availability of raw materials, logistics, and production costs. Geopolitical factors and trade regulations can lead to disruptions. Diversifying sourcing and establishing robust supply chain management practices are essential for mitigating risks associated with global supply chains. Moreover, the type of materials sourced and production techniques used have a direct impact on costs and delivery times.
Future Trends and Innovations in PCB Manufacturing
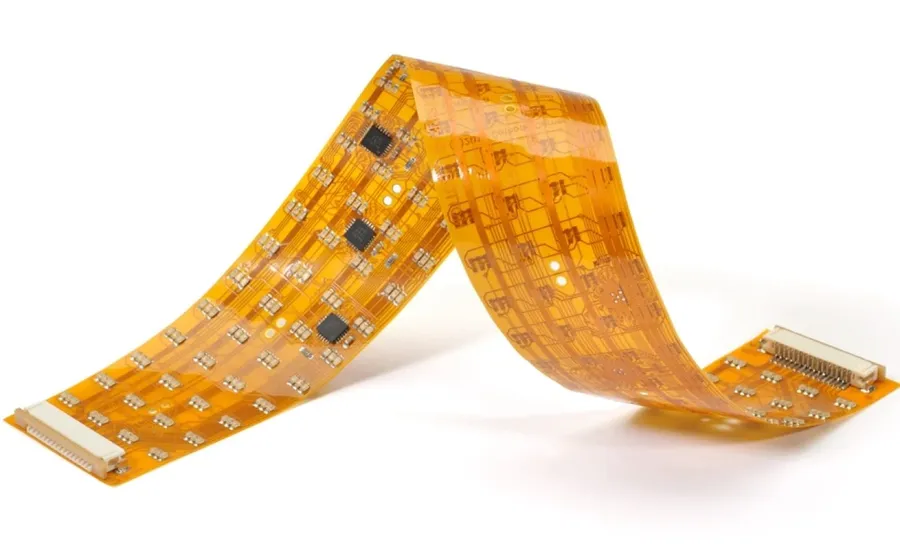
The printed circuit board (PCB) manufacturing industry is on the cusp of significant transformation, driven by technological advancements and evolving market demands. These changes are not just incremental improvements but represent fundamental shifts in how PCBs are designed, produced, and integrated into electronic devices. Global PCB manufacturers are actively adapting to these trends to stay competitive and meet the requirements of increasingly complex and sophisticated products.
One of the primary drivers of change is the move towards miniaturization, higher performance, and greater functionality. This has spurred innovation in several key areas:
- Embedded Electronics
Embedding electronic components within the PCB layers themselves is emerging as a key technology. This approach allows for smaller, lighter, and more robust designs by eliminating the need for discrete surface-mounted components. It also offers improved electrical performance due to shorter signal paths and reduced parasitic effects. Future PCBs will integrate more active and passive components within their structures, leading to more compact and efficient electronic systems. - 3D Printing of PCBs
Additive manufacturing, or 3D printing, is poised to revolutionize PCB fabrication. Unlike traditional subtractive methods, 3D printing allows for the creation of complex geometries, intricate internal structures, and on-demand customization. This technology enables rapid prototyping, flexible production runs, and potentially a shift towards decentralized manufacturing. Direct writing of conductive inks and materials onto substrates offers new possibilities for integrating antennas, sensors, and other functional elements directly into the PCB. - Advanced Materials
Ongoing research is focused on developing new materials for PCB manufacturing with enhanced properties. These include materials with higher thermal conductivity, lower dielectric constants, and greater mechanical strength. Additionally, environmentally friendly and sustainable materials are gaining importance, driven by increasing regulatory pressures and environmental consciousness. The use of nano-materials is also under exploration for their potential to improve the electrical and thermal performance of PCBs. - Flexible and Stretchable Electronics
The demand for wearable electronics and flexible displays is driving the development of flexible and stretchable PCBs. These require specialized materials and manufacturing processes that allow for bending, folding, and even stretching without compromising electrical functionality. This trend is opening new possibilities for innovative electronic products. - Artificial Intelligence in PCB Design and Manufacturing
AI is being used to optimize PCB design by reducing design time and enhancing performance. Machine learning can predict potential manufacturing defects and enhance the quality of the process. The technology is helping global PCB manufacturers to enhance efficiency and reduce errors in all the processes.
Global PCB manufacturers must adapt to these changes by investing in new technologies, research, and training, and by creating strategic alliances to navigate this evolving landscape. The future of PCB manufacturing will be shaped by these advancements, leading to more powerful, versatile, and environmentally sustainable electronics.
The landscape of global pcb manufacturers is dynamic and competitive, driven by technological advancements and the ever-increasing demand for electronic devices. The leading pcb manufacturers are not only creating the crucial components of our electronic world, but also shaping the future of electronics. Staying informed about these key players and their innovations is essential for anyone involved in the electronics industry. These global pcb manufacturers will continue to innovate, pushing the boundaries of technology and shaping the future of the electronics industry.
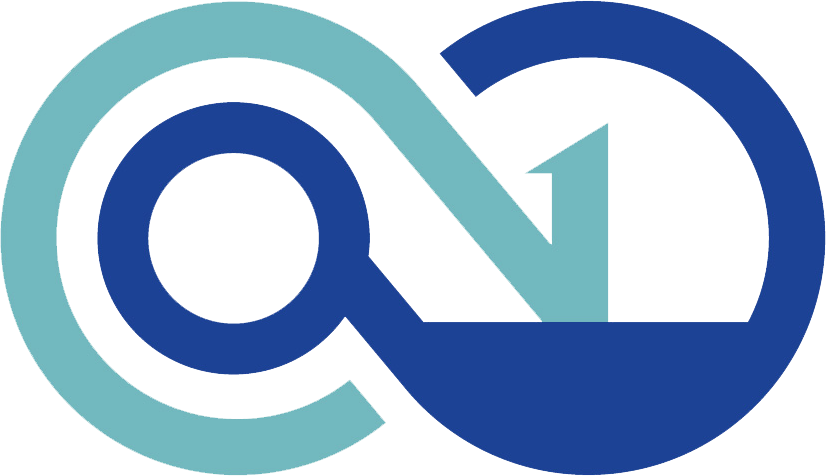